Content
- Introduction
- 1. Analysis of factors that have a negative impact on the environment in the conditions of operation of arc furnaces foundries
- 1.1 Gas and dust emissions from steel production in electric arc furnaces of small capacity
- 1.2 Methods of evacuation of gas and dust emissions from the working area of low-tonnage electric arc furnaces and evaluation of the effectiveness of their functioning
- 1.3 Development of measures aimed at improving the efficiency of emission removal systems from arc furnaces operated in foundries
- 1.4 The purpose and objectives of the research
- 2. Improvement of the design and justification of the parameters of the umbrella rotation mechanism of the gas exhaust system of a low-tonnage electric arc furnace
- 2.1 Description of the advanced gas pump system
- 2.2 Design features of the proposed mechanism for turning the arc furnace umbrella arc furnace umbrella
- 2.3 Calculation of energy-power parameters of the upgraded drive of the umbrella rotation mechanism
- 3. Experimental verification of the correctness of technical solutions embedded in the design of the improved umbrella rotation mechanism
- 3.1 Design and manufacture of a working model of a low-tonnage arc furnace for laboratory research
- 3.2 Methodology of model experiments and analysis of the results obtained
- Conclusions
- List of sources
Introduction
Electric furnaces for steel smelting in the conditions of foundry production are the most common technological units. A wide range of foundry steels are smelted in them , designed to produce castings of different weights. At the same time, as is known, gases saturated with dust are formed, which have a negative impact on the environmental situation and working conditions in industrial premises.
The main amount of gas exits through the gaps between the openings of the vault and the electrodes, as well as the working window. Gases are released from electric furnaces not only in the process melting, but also during loading the furnace and draining the finished steel into the bucket. Due to the tightening of environmental safety requirements regarding the amount of emissions of harmful substances into the atmosphere, in recent years there has been a need to improve existing gas extraction and gas purification systems in order to increase the efficiency of their operation in the foundry.
Of particular relevance is the task associated with the development of gas extraction systems for electric arc furnaces of small tonnage (up to 10 tons) operated in foundries of machine -building enterprises. We are talking about furnaces equipped with outdated gas extraction and gas purification systems. Therefore, the topic of baklavr work related to the development of measures aimed at modernization gas extraction systems of low-tonnage electric arc furnaces in order to increase the efficiency of their operation is of great practical importance.[1]
1.1 Gas and dust emissions from steel production in electric arc furnaces of small capacity
In the process of steel smelting in electric arc furnaces, the temperature of the metal can reach 2500 - 3000 ° C, which entails the burnout of the electrodes and the evaporation of iron, silica, alumina, manganese and other elements contained in the metal melt.
According to the literature data, the composition of gases includes 5-70% CO, 5-15% C02, 0.5 - 5% H2, 3 - 10% O2, the rest is N2. The dust content of the gas, depending on the quality of the charge, can be from 2 to 10 g/ m3 (n) without purging the bath with oxygen and from 14 to 100 g/ m3 when it is used.
The dispersed composition of dust is as follows: Particle size, microns <5 5-10 10-20 20-44 >44 Content, % (by weight) 71,9-67,9 8,3-6,8 9,8-6 9-7,5 6,5-6,3 The dust dispersion increases dramatically in the case of oxygen application. At the same time, the content of sublimations reaches 85-95% [2]. The above information indicates the urgent need to install evacuation and purification systems for exhaust furnace gases on electric arc furnaces.
1.2 Methods of evacuation of gas and dust emissions from the working area of low-tonnage electric arc furnaces and evaluation of the effectiveness of their functioning
Steel smelting in electric furnaces proceeds due to the heat of an electric arc excited between the electrodes.
The following devices have been widely used to capture and remove gas released from electric furnaces [3]. Installation of a special umbrella over the electric furnace Figure 1, completely overlapping in terms of the furnace vault.[2]
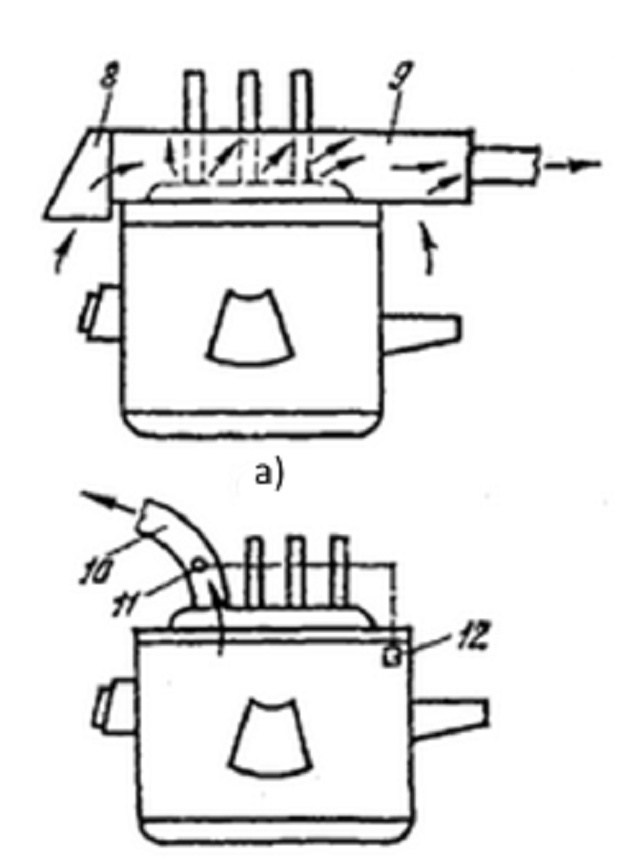
Figure 1 – Gas removal system from electric furnaces using an umbrella
Sectional suction figure 2 is an improved shelter.
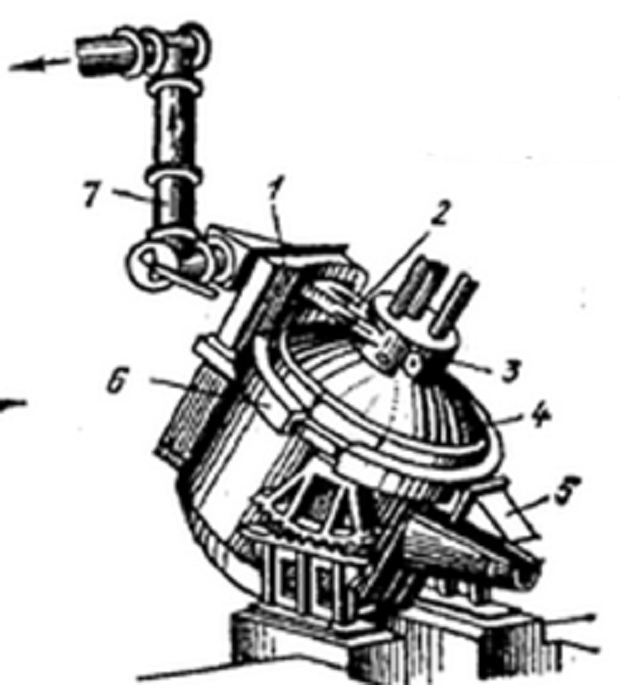
Figure 2 – Sectional gas pump system
Gas removal directly from the furnace vault Figure 3. In the vault of the furnace, a special hole is made through which, with the help of a water-cooled the pipe 10, connected pivotally to the gas outlet gas pipeline, sucks off the gas formed during the melting of steel.
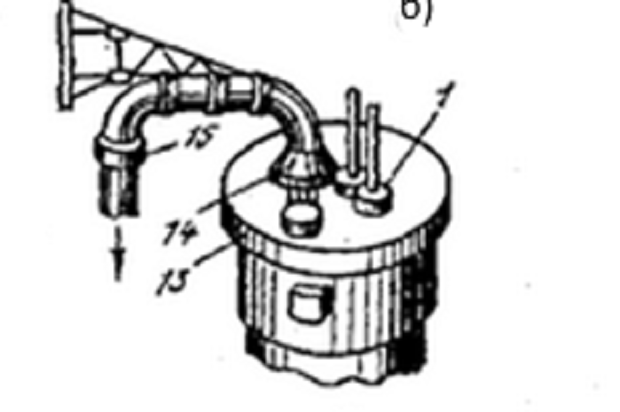
Figure 3 – Method of gas removal from the arch of an electric arc furnace
1.3 Development of measures aimed at improving the efficiency of emission removal systems from arc furnaces operated in foundries
Purification of gases discharged from electric arc is carried out with the help of special dust collectors, electric filters, fabric filters and other hardware.
When using high-speed dust collectors, the gas after afterburning is sent to a hollow scrubber, where it is cooled and roughly cleaned from dust.
A wet electrofilter is used after afterburning the gas in the afterburning chamber and cooling in a hollow scrubber at a temperature of ~ 250 ° C. When gas is sucked through the furnace vault, the capacity and pressure of the extractor are usually adjusted, since during the melting process the amount of gas emissions from the furnace changes.[4-9]
To increase the degree of purification of emissions from the furnace, several types of dual purification systems are used in practice, providing for the installation of cleaning equipment both on the furnace itself and after the umbrella installed under the lantern on the roof of the production building figure 4.
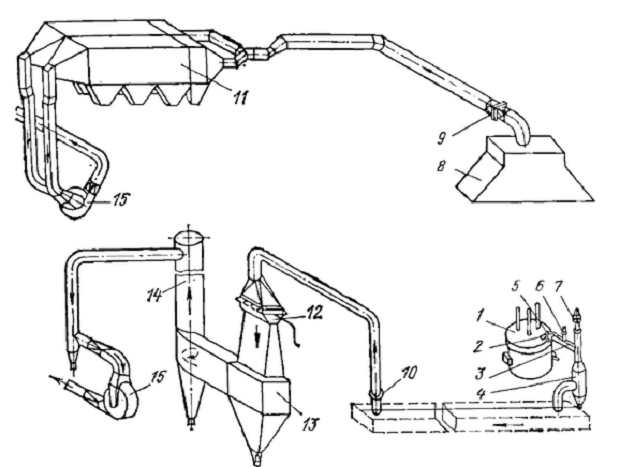
Figure 4 – Scheme of combined purification of gases discharged from the electric furnace and through an umbrella under the shop lamp
The experience of operating such installations has shown that the most time-consuming operations are the replacement of flexible hoses, which have to be performed due to their breaks in the lower fastening (30%) and along the seam (30-35%), as well as as a result of clogging with an unshaken dust layer (35-40%).
1.4 The purpose and objectives of the research
The purpose of the study is to improve the design and substantiation of the parameters of the gas exhaust system of a low–tonnage electric arc furnace foundry.
To achieve this goal, it is necessary to solve the following tasks:
- To propose a rational technical solution to improve the gas exhaust system of the electric arc furnace of the foundry in order to eliminate bottlenecks
- To substantiate the energy-power parameters of the improved rotation mechanism of the catching umbrella of the arc furnace.
- Check the correctness of the technical decisions made on the current model of the furnace umbrella rotation mechanism.
- To evaluate the technical and economic efficiency of the implementation of the modernized gas exhaust system of the electric arc furnace of the foundry.
2.1 Description of the advanced gas pump system
The proposed system of suction (evacuation) of gas and dust generated in the electric arc furnaces of the foundry during steel smelting includes an umbrella located on the working site of the melting unit and equipped with an upgraded mechanism for its rotation, as well as by means of a discharge a circular section path connected to the inlet of the bag filter.[11]
The system provides for the installation of two identical DN 12.5 smoke pumps, one of which is a working one, and the second is a backup one. The smoke pumps can operate separately and simultaneously, for which they are equipped with gate valves, each of which is switched to the closed position if the corresponding smoke pump is placed in reserve. [13]
2.2. Design features of the proposed mechanism for turning the arc furnace umbrella arc furnace umbrella
Taking into account the results of a comparative analysis of the performance of existing low-tonnage gas extraction systems arc furnaces have developed an improved design of the mechanism of rotation of the catching umbrella.
2.3.Calculation of energy-power parameters of the upgraded drive of the umbrella rotation mechanism
To calculate the energy-power parameters of the umbrella rotation mechanism drive, we will use the methodology proposed by the staff of the Department of the Moscow State Technical University and published in the work.
The moment of resistance to rotation of the exhaust umbrella consists of static moments of friction in the centering and support rollers, as well as resistance in the sand gate:
Ms = (Msc+Mso)kz,
where Mcc is the moment of resistance from friction in centering rollers;
Mso – the moment of resistance from friction in the support rollers;
kz is a coefficient that takes into account the friction in the sand gate.
During the start-up of the drive, the MD dynamic segment additionally acts on it, so the total moment of resistance:
Mo = Ms + MD.
The dynamic moment of resistance is determined by the well - known formula
where I is the moment of inertia of the exhaust umbrella relative to the axis of its rotation;
- angular velocity of the umbrella;
tp ? the start-up time of the drive, which is taken according to
according to the recommendations of VNIIPTmash, tp = 1c.
3.1 Design and manufacture of a working model of a low-tonnage arc furnace for laboratory research
In order to verify the correctness of itechnical solutions embedded in the design of the upgraded umbrella rotation mechanism of the gas pump system A 5-ton arc furnace was manufactured with its current model, made on a scale of 1:10.
This model of the furnace, equipped with a gas pump system, made it possible to accurately simulate the operation of a full-scale sample of the furnace and check the dynamics of the functioning of its gas pump system.
3.2 Methodology of model experiments and analysis of the results obtained
To measure the force transmitted by the lever of the model of the mechanism of rotation of the catching umbrella, a control and measuring complex was used, which included a strain gauge converter, an AC amplifier, an analog-to-digital converter and a computer with a printing device.
The strain gauge converter included two working foil sensors glued to the surface of the lever along the axis of symmetry and two compensation sensors that were located perpendicular to the workers.
The calibration of the strain-resistor converter for sequential loading of the suspended lever with weights with a known mass and fixing the corresponding signal amplitudes in ADC codes was previously performed.
Based on the results obtained, a calibration dependence graph was constructed (Fig. 3.5) and the measurement accuracy provided was estimated.
In accordance with the experimental plan, it was supposed to study the nature of changes in the loads acting on the elements of the model of the mechanism of rotation of the catching umbrella when it was transferred from one extreme position to another, as well as determining the fraction of the moment of resistance to the rotation of the umbrella associated with friction in the nodes of the sand shutter.
Model studies of the operation of the proposed mechanism for turning the trapping umbrella of an electric arc furnace were carried out according to the methodology recommended in the works.
The obtained data were processed using a calibration dependence graph.
The results of processing experimental data indicate that the total resistance force caused by friction in the lower and upper sand gates when transferring the catching umbrella from one extreme position to another reaches 25% of the total technological load acting on the actuator.[10]
Conclusions
1. Based on the results of the analysis of the state of the issue related to the problem of evacuation of gas and dust emissions from the working space of electric arc furnaces of small tonnage operated in foundries of machine -building plants, it was found that the main factor negatively affecting the efficiency of gas extraction systems is the ingress of fine dust and gases into the surrounding space in the joints of movable joints.
2. To ensure reliable operation of the gas pump system, it is proposed to provide the umbrella rotation mechanism with sand gates.
3. The constructive and energy-power parameters of the umbrella rotation mechanism are theoretically substantiated. As a result of the calculation of the energy-power parameters of the exhaust umbrella rotation drive, it was found that the greatest moment of resistance on the output shaft of the gear motor occurs when the umbrella is rotated 18? from the initial position and is MSrmah = 792.4 N • m; the maximum thrust force occurs at the beginning of the umbrella rotation from the initial position and is Fmax = 1956.5 N; estimated drive power Np = 557 watts.
4. Нand the current physical model of a 5-ton arc, manufactured at a scale of 1:10, was checked for the correctness of the technical decisions made and the validity of the calculated dependencies obtained to determine the operating parameters of the improved gas extraction system proposed for use in the conditions of the foundry of the Yasinovatsky Machine-building Plant.
5. The results of processing experimental data indicate that the total resistance force caused by friction in the lower and upper sand gates when transferring the catching umbrella from one extreme position to another reaches 25% of the total technological load acting on the actuator. The information obtained by calculation when determining the components of the total moment of resistance to rotation of the hollow console carrying the catching umbrella indicates that the total share of moments caused by friction in both sand gates reaches 23% of the total moment. Thus, we can talk about a fairly good convergence of the calculated and experimental data.
6. Total economic costs for the implementation of the completed development will amount to ...... rubles.
7. The introduction into production of an upgraded mechanism for turning the exhaust umbrella of the gas extraction system of a small-tonnage electric arc furnace will significantly reduce the amount of gas and dust emissions emitted into the surrounding space, which will improve the working conditions of foundry workers and the eclogical situation near them.
List of sources
- Kiselev, A.D. Improving the efficiency of gas removal of arc steelmaking furnaces / A.D. Kiselev, Yu.N. Tuluyevsky, I.Yu. Zinurov .- M.: Metallurgy, 1992. 112 p.
- Osipenko, V.D. Removal and dedusting of gases of arc steelmaking furnaces / V.D. Osipenko, A.P. Egorychev, B.N. Maksimov . - M.: Metallurgy, 1985. - 104 p.
- Aliyev, G.M. The technique of dust extraction and purification of industrial gases. Reference ed. M.: Metallurgy, 1986. – 544 p.
- Stark, S.B. Gas cleaning devices and installations in metallurgical production: Textbook for universities. 2nd edition, reprint. and additional M.: Metallurgy, 1990. -400 p.
- Bukach, B.F. Rational system of gas removal from large-tonnage chipboard / B.F. Bukach, A.G. Notych // Development of new high-power electric furnaces: Temat. Sb. nauchn. Tr. MCHM USSR. (NIIM). -M.: Metallurgy, 1982. pp. 20-23.
- Rakhmetova, E.R. Development of a system for cleaning waste gases from electric arc furnaces of the foundry and measures to improve environmental production // All-Russian Forum of Scientific Youth "Wealth of Russia": Collection of reports. - Moscow: Bauman Moscow State Technical University, 2018.- pp. 275 – 276.
- Pavlovich, L.B. Assessment of environmental risk from emissions of foundry production into the atmosphere / L.B. Pavlovich. V.V. Sadikhova, D.A. Shuldishova // Bulletin of the Siberian State Industrial University.- 2014.- № 4 (10).- Pp. 52-55.
- Rechkalov A.V. Basic requirements for arc furnaces smelting metal for casting production / A.V. Rechkalov [et al.] // Electrometallurgy.- 2014.- No. 11.- p. 2-5.
- Krutyansky, M.M. Calculation of gas emissions from DC and AC arc furnaces in the foundry / M.M. Krutyansky, S.M. Nehamim, E.M. Rebikov // Electrometallurgy.- 2016.- No. 7.- pp. 27-34.
- Solovyov, V.P. Design of new and reconstruction of existing foundries: A textbook. / V.P. Solovyov, S.A. Gladyshev, V.I. Vorontsov.- M.: MISIS, 2004.- 227 p.
- Drobitko, M.Yu. Systems for cleaning waste gases of smelting and their use in foundry production / M.Yu. Drobitko [et al.].-M.: Mashinostroenie, 2004.- 198 p.
- Calculations of lifting and transporting machines / F.K. Ivanchenko [et al.].-K.:Higher School, 1978. - 576s.
- Stalinsky, D.V. Gas purification of low-tonnage electric steelmaking furnaces in the foundry shop // D.V. Stalinsky [et al.] // Metallurgical and mining industry.- 2016.- No. 6.- p.100 – 105.
- Yeronko, S.P. Improvement of the design and model studies of the operation of the gas exhaust system of the electric arc furnace of the foundry shop / S.P. Yeronko [et al.] // Izvestiya vuzov. Ferrous metallurgy.- 2019.- No. 1.- p. 34 – 41.
- Eron’ko S.P.Improving the Gas-Exhaust System at Foundry Electrofurnaces / S.P. Eron’ko [e.a.] // ISSN 0967-0912, Steel in Translation, 2019, Vol. 49, № 1, pp. 7 – 12.
- Innovative integrated solutions for the treatment of waste gases in the ferrous metallurgy. Technical solutions for the purification of high-temperature gas flows / B.L. Krasny [et al.] // Ferrous metallurgy: Byul. in-ta "Chermetinformatsiya" 2021.- Vol. 77. No. 2.- p.200 – 208.