Реферат по теме выпускной работы
Содержание
- Введение
- 1. Организация и структура ремонтного производства на предприятиях черной металлургии
- 2. Технология и конструкции станков плазменной резки
- 2.1 Краткое описание процесса плазменной резки
- 2.2 Общее устройство и принцип работы плазмореза
- 2.3 Обзор устройств для плазменной резки
- 3. Описание конструкции модели переносного станка плазменной резки с чпу
- 4. Программная настройка плазмореза
- Выводы
- Список источников
Введение
Неотъемлемой составляющей надежности оборудования является ремонтопригодность, показатели которой (длительность, трудоемкость, стоимость восстановления) влияют на экономическую эффективность производства. Для металлургических машин, характеризующихся уникально-стью конструкций, большими габаритными размерами и массами, единичным и мелкосерийным изготовлением элементов, вопросы совершенствования технологии проведения ремонтно-восстановительных работ остаются актуальными. Одним из направлений развития является организация ремонта и восстановления элементов оборудования непосредственно на месте эксплуатации, без транспортировки в специальные ремонтные цеха, используя переносные металлообрабатывающие станки и комплексы.[1] Металлургические, энергетические, горные машины, характеризующиеся длительными сроками работы и имеющие изношенные корпусные или несущие детали, – наиболее перспективные объекты для использования переносных станков.
В настоящее время отмечается расширение парка переносных (мобиль-ных) станков и комплексов, выпускаемых зарубежными и отечественными производителями, среди которых можно выделить: токарные; расточные и расточно-наплавочные; фрезерные; сверлильные; для планирования (торцевания). Отдельную группу составляют станки для газовой и плазменной резки металла. В ходе практики выполнен поиск информации о технологии плазменной резки, конструкциях станков, а также расчет параметров для модели переносного плазмореза предлагаемой конструкции.
1. Организация и структура ремонтного производства на предприятиях черной металлургии
Задача ремонтного производства металлургического завода сводится к обеспечению бесперебойной, надежной и высокопроизводительной работы оборудования при минимальных затратах средств. В последние годы проведена значительная работа по улучшению содержания и ремонта оборудования металлургических заводов. В состав ремонтного производства металлургического завода входят цехи по ремонту оборудования (доменного, электросталеплавильного, прокатного), по изготовлению ремонтно-эксплуатационного металла (литейные, кузнечные, металлоконструкций, механические и др.), склад запасных частей, склад полуфабрикатов. [2-6]Структура управления ремонтным производством определяется масштабом завода и существующими методами организации ремонта. В производственных цехах поддержанием- работоспособности оборудования занимается ремонтная служба Возглавляет ремонтную службу цеха помощник начальника цеха по механическому оборудованию (механик цеха). В непосредственном подчинении механика цеха находится технический отдел (бюро) цеха, задачей которого является подготовка, техническое и материальное обеспе¬чение ремонтов. Назначение ремонтного производства, представляющего собой совокупность материально-технических средств и ремонтного персонала, заключается в изготовлении и замене изношенных деталей, частичном или полном обновлении металлургического оборудования на базе новой техники. В зависимости от принятой системы управления различают децентрализованную, нейтрализованную и смешанную формы организации ремонтного производства. При децентрализованной форме ремонтный персонал сосредоточен в производственных цехах, а материально-технические средства - в отделе главного механика. Централизованная форма характеризуется тем, что материально-технические средства и ремонтный персонал объединены в отделе главного механика. В настоящее время на большинстве заводов принята смешанная форма организации ремонтного производства, при которой каждый производственный цех имеет небольшие мастерские для изготовления быстроизнашивающихся деталей и необходимый штат рабочих для выполнения ремонтов.[7]
2. Технология и конструкции станков плазменной резки
Плазма – это высокотемпературный ионизированный газ, обладающий высокой электропроводностью. Процесс плазменной резки основан на использовании воздушно-плазменной дуги постоянного тока прямого действия (электрод - катод, разрезаемый металл – анод). Для возбуждения рабочей дуги (электрод - разрезаемый металл), с помощью осциллятора зажигается вспомогательная дуга между электродом и соплом - так называемая дежурная дуга, которая выдувается из сопла пусковым воздухом в виде факела длиной 20-40 мм Применение способа плазменной резки, при котором в качестве плазмообразующего газа используется сжатый воздух, открывает широкие возможности при раскрое низкоуглеродистых и легированных сталей, а также цветных металлов и их сплавов.[8]
Станок для плазменной резки (плазморез) состоит из нескольких компонентов рисунок 1:
- Источника питания;
- Плазменного резака;
- Воздушного компрессора;
- Кабель-шлангового пакета
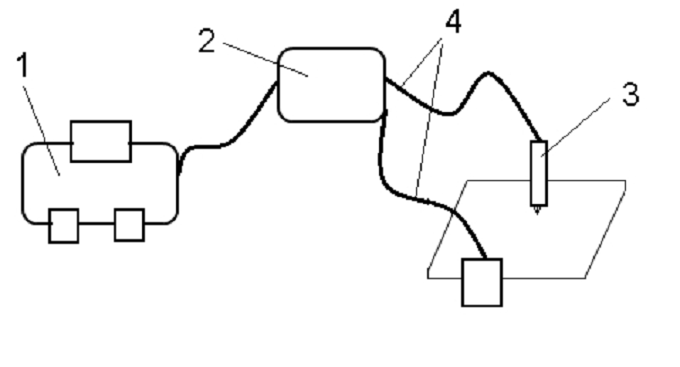
Рисунок 1 – Общее устройство плазмореза
2.1 Краткое описание процесса плазменной резки
Для возбуждения рабочей дуги (электрод - разрезаемый металл), с помощью осциллятора зажигается вспомогательная дуга между электродом и соплом - так называемая дежурная дуга, которая выдувается из сопла пусковым воздухом в виде факела длиной 20-40 мм рисунок 2.
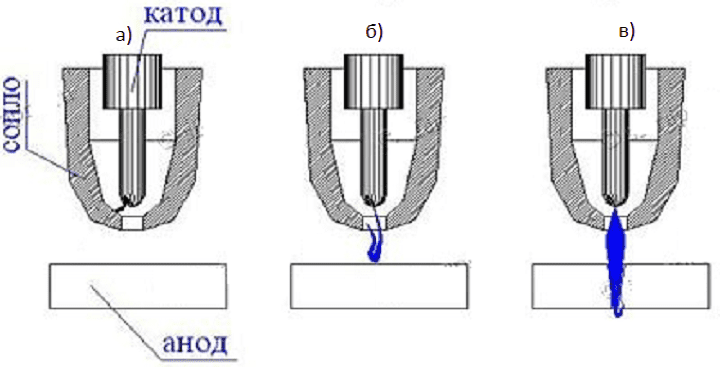
Рисунок 2 – Фазы образования рабочей дуги:
а) зарождение дежурной дуги;
б) выдувание дежурной дуги до касания с поверхностью разрезаемого металла;
в) появление рабочей (режущей) дуги и проникновение через рез металла
Ток дежурной дуги равен 25 или 40…60 А, в зависимости от источника плазменной дуги. При касании факела дежурной дуги металла возникает режущая дуга - рабо-чая, и включается повышенный расход воздуха; дежурная дуга при этом авто-матически отключается.
Преимущества воздушно-плазменной резки по сравнению с механизиро-ванной кислородной и плазменной резкой в инертных газах следующие:
- Простота процесса резки;
- Применение недорогого плазмообразующего газа - воздуха;
- Высокая чистота реза (при обработке углеродистых и низколегированных сталей);
- Пониженная степень деформации;
- Более устойчивый процесс, чем резка в водородосодержащих смесях.
2.2 Общее устройство и принцип работы плазмореза
Главным элементом станка является плазменный резак или плазмотрон, который состоит из сопла, электрода, охладителя (изолятора) между ними и канала для подачи сжатого воздуха рисунок 3.
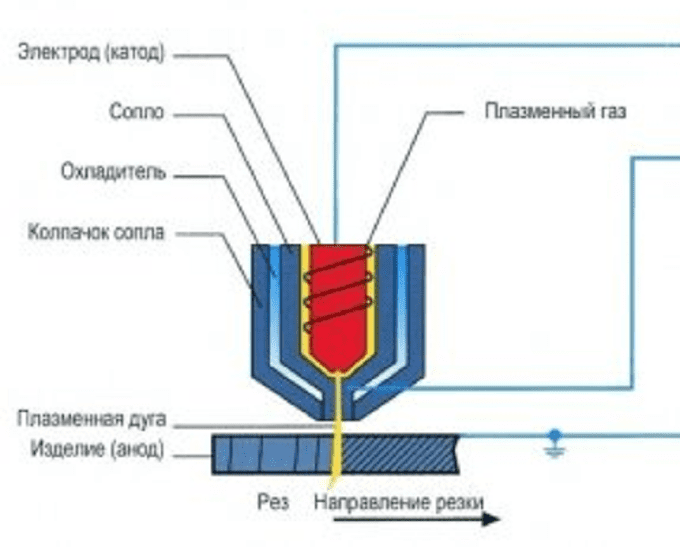
Рисунок 3 – Принципиальная схема плазмореза.
Внутри корпуса плазмотрона находится электрод, который служит для возбуждения электрической дуги. Сопло плазмотрона обжимает и формирует плазменную струю, которая вырывается из выходного канала и разрезает заготовку. Компрессор обеспечивает подачу воздуха. Технология плазменной резки подразумевает использование газов: плазмообразующих и защитных.
Кабель-шланговый пакет соединяет источник питания, компрессор и плазмотрон. По электрическому кабелю подается ток от трансформатора или инвертора для возбуждения электрической дуги, а по шлангу идет сжатый воздух, который необходим для образования плазмы внутри плазмотрона.
Принцип работы плазмореза следующий. При включении источника пи-тания (инвертора) 2 на плазмотрон поступает ток высокой частоты. В результате внутри плазмотрона возникает дежурная электрическая дуга, температура которой 6000 – 8000 °С. Дежурная дуга зажигается между электродом и наконечником сопла в виду того, что образование дуги между электродом и обрабатываемой заготовкой сразу затруднительно. Столб дежурной дуги заполняет весь канал сопла.[9]
После возникновения дежурной дуги в камеру сопла начинает поступать сжатый воздух. Суженное к низу сопло плазмотрона сжимает воздушную струю и фор-мирует поток, который со скоростью 2–3 м/с вырывается из сопла. Температу-ра воздуха в этот момент может достигать 25000 – 30000 °С. Именно этот высокотемпературный ионизированный воздух и является в данном слу-чае плазмой.
Ее электропроводимость примерно равна электропроводимости металла, который обрабатывается. В тот момент, когда плазма вырывается из сопла и соприкасается с по-верхностью обрабатываемого металла, зажигается режущая дуга, а дежурная дуга гаснет. Режущая (рабочая) дуга разогревает обрабатываемую заготовку локально в месте реза. Металл плавится, появляется рез
2.3 Обзор устройств для плазменной резки
Устройств для плазменной резки можно разделить на две группы: ручные плазморезы и аппараты машинной резки (станки). Ручные плазморезы используются в быту, на маленьких производствах и в частных мастерских для изготовления и обработки деталей. При этом способе рез получается ровным, но не идеальным; производи-тельность выполняемых операций не высокая.
На машиностроительных предприятиях для изготовления деталей или обработки заготовок применяются станки (машины) плазменной резки, современные конструкции которых имеют ЧПУ (числовое программное управление). Станок с ЧПУ работает по заданной программе с минимальным участием оператора, что максимально исключает человеческий фактор на производстве и значительно увеличивает производительность.
Качество реза машинным аппаратом идеально, не требуется дополнительная обработка кромок.[10] Также обеспечивается выполнение фигурных резов. Продолжительность включения станка может достигать 100 %. Цена на станок плазменной резки в зависимости от сложности и размеров составляет 3000…20000 у.е. Можно выделить машины тяжелого, среднего и малого класса. К машинам малого класса относятся и переносные станки.
3. Описание конструкции модели переносного станка плазменной резки с чпу
Главной задачей проекта является детальная проработка конструкции малогабаритного переносного станка плазменной резки с ЧПУ. С этой целью в системе автоматизированного проектирования КОМПАС была создана трех-мерная модель плазмореза рисунок 4. Масштаб компьютерной модели отвечал натуральным размерам.
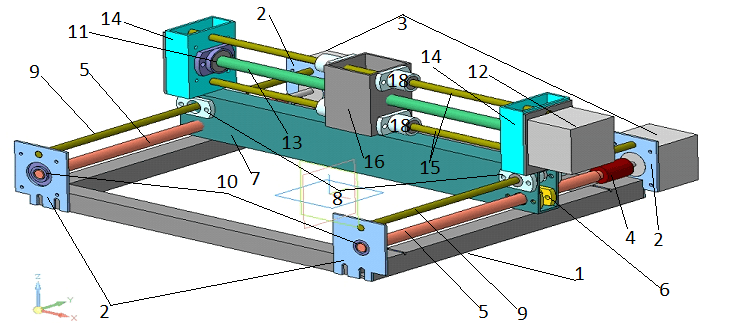
Рисунок 4 – Трехмерная модель разработанного переносного плазмореза.
Основание станка 1 представляет собой сварную раму, выполненную из профильной трубы квадратного поперечного сечения. На раме размещаются механизмы перемещения резака по осям Х и Y. На боковых поверхностях рамы с четырех сторон закреплены опорные пластины 2, к двум из которых крепятся шаговые двигатели 3 механизма перемещения по оси Y. Валы двигателей с помощью гибких муфт 4 соединяются с винтами 5, которые совместно с гайками 6 образуют винтовые передачи механизма перемещения по оси Y. Гайки 6 смонтированы внутри траверсы 7, изготовленной из профильной трубы прямоугольного сечения. На траверсе закреплены линейные подшипники 8 для направляющих 9. По два подшипника на каждую направляющую. Направляющие 9 представляют собой цилиндрические стержни, опирающиеся на пластины 2. Кроме того на пластинах 2 закреплены корпуса 10 подшипников качения 11, являющихся опорами винтов 5. Винтовые передачи 5-6 преобразуют вращение валов двигателей 3 в поступательное движение траверсы 7 вдоль направляющих 9.
На траверсе 7 смонтирован механизм перемещения резака по оси Х. В состав механизма входит шаговый двигатель 12, который через гибкую муфту соединяется с винтом 13. Винт опирается на подшипники качения 11, корпуса 10 которых закреплены на стойках 14, установленных на краях траверсы 7. Стойки 14 выступаю также как опоры направляющих 15. Вдоль направляющих 15 и винта 13 перемещается каретка 16 с закрепленным на ней плазмотроном 17. Гайка, обеспечивающая перемещение каретки, расположена внутри каретки 16. Корпуса 17 линейных подшипников 18 направляющих 17 закреплены на каретке 17 с внешних сторон.
4. Программная настройка плазмореза
Для того чтобы вырезать деталь на плазморезе с ЧПУ необходимо сначала написать программу управления для контролера станка. Ниже приведена последовательность выполняемых действий. 1. Создание чертежа детали. Для этого открыть программу «КОМПАС-3D» и в файле типа фрагмент рисунок 1 создать изображение детали рисунок 2.
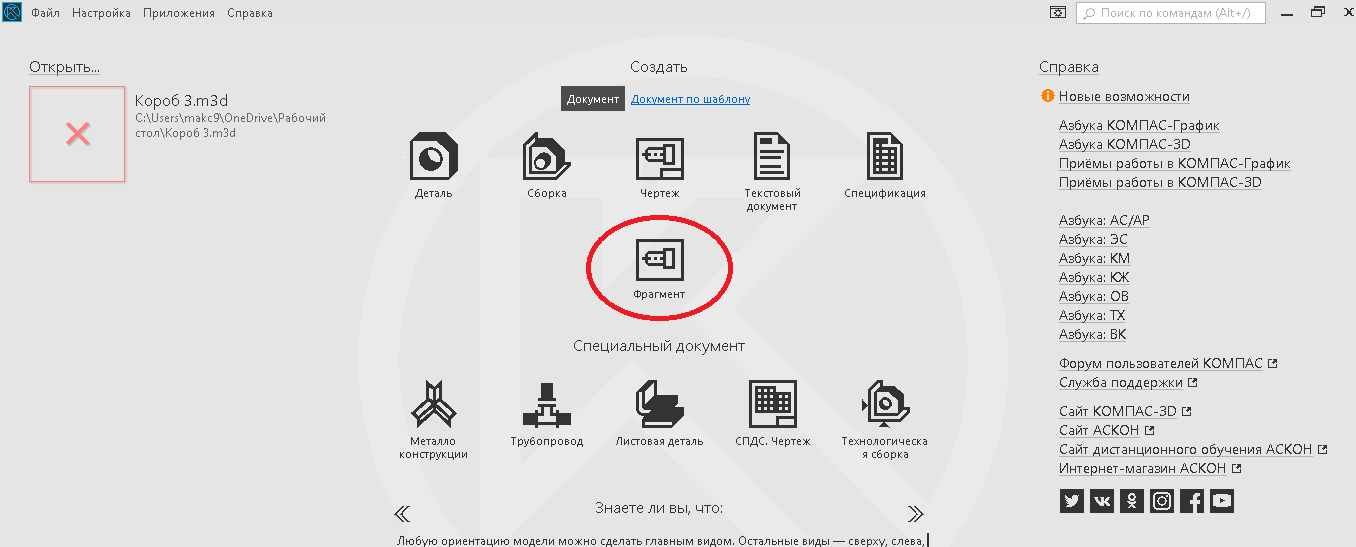
Рисунок 1 – Выбор файла типа фрагмент в системе КОМПАС
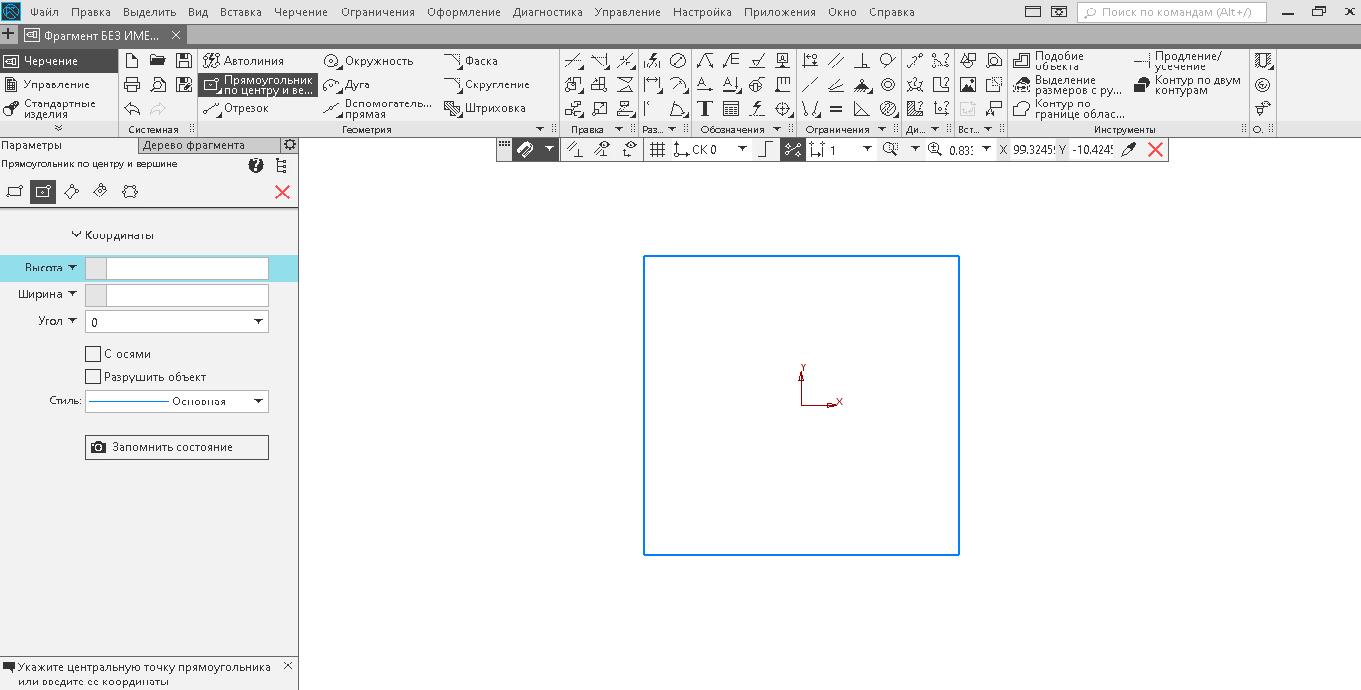
Рисунок 2 – Сохранение изображение детали
2. Сохранить изображение детали в формате PNG в масштабе 1:1 рисунок 3.
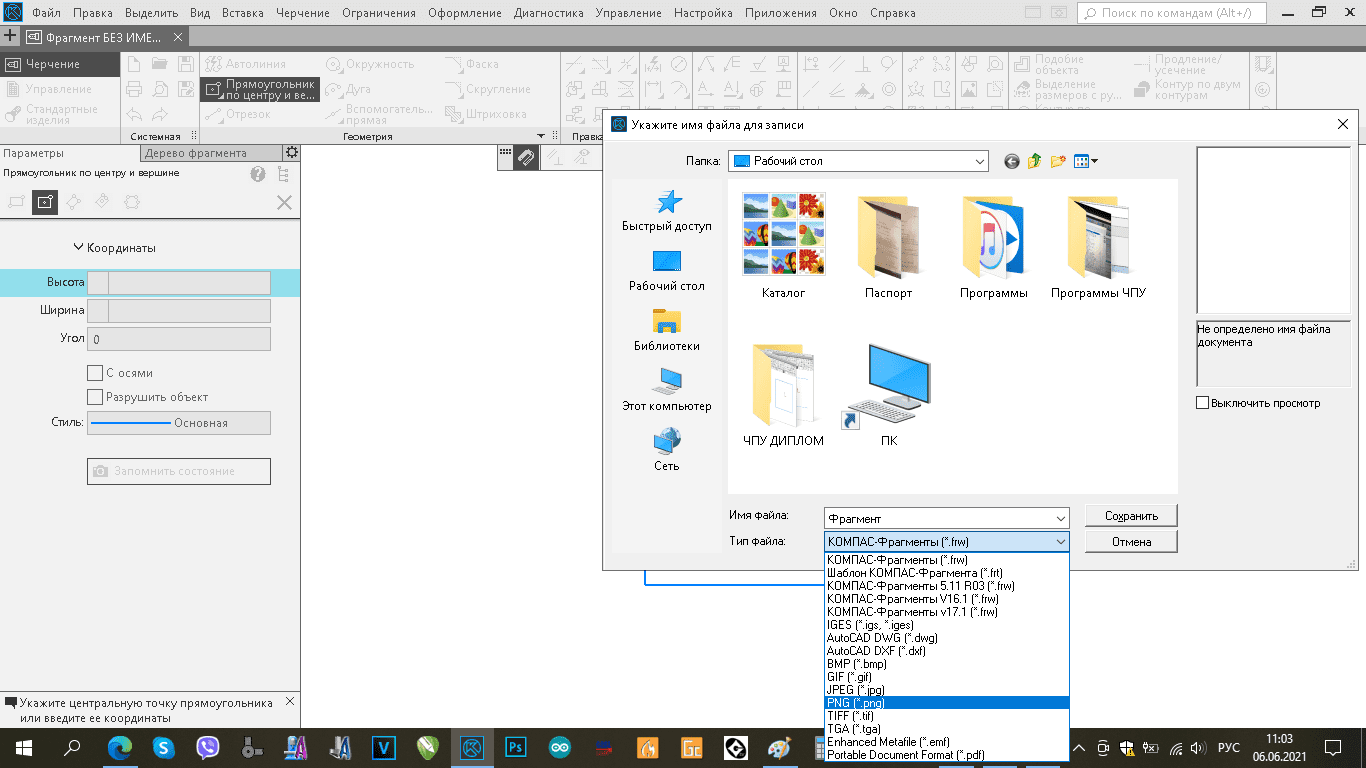
Рисунок 3 – Вычерчивание изображения детали
3. Задание настроек резания для файла детали. 3.1. Запустить программу LaserGRBL рисунок 4 и выбрать сохраненный файл рисунок 5.
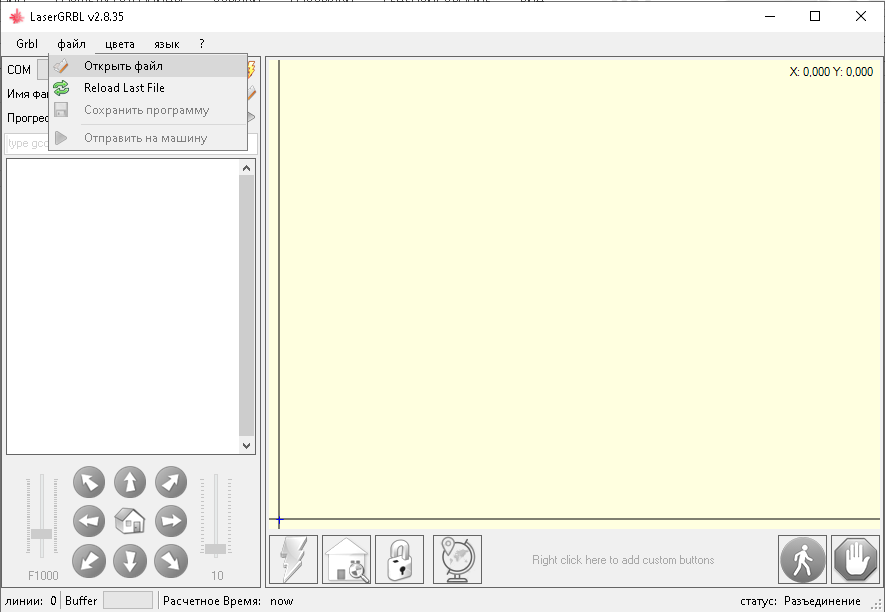
Рисунок 4 – Интерфейс программы LaserGRBL
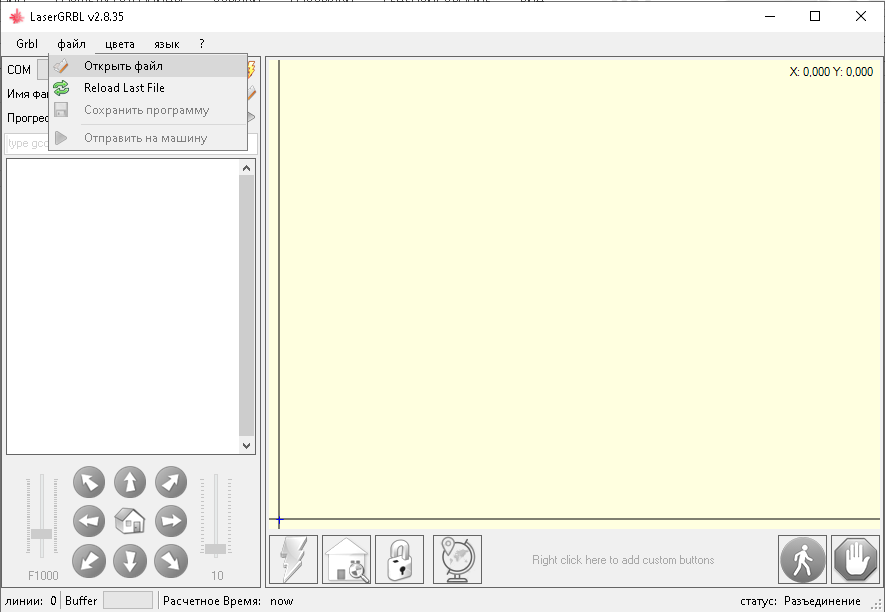
Рисунок 5 – Выбор файла в программе LaserGRBL
3.2. В открывшимся окне задать настройки параметров резки.
1. Выбрать параметр «Векторизовать» рисунок 6. Нажать кнопку «Да-лее».
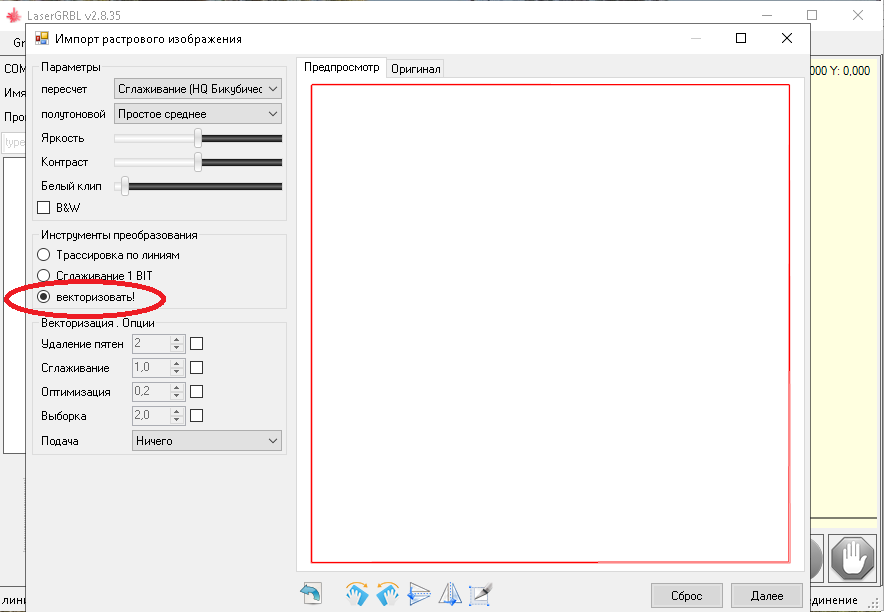
Рисунок 6 – Настройка векторизации
2. В открывшимся окне выставить габаритные размеры детали – ширину W и высоту H (мм) рисунок 7.
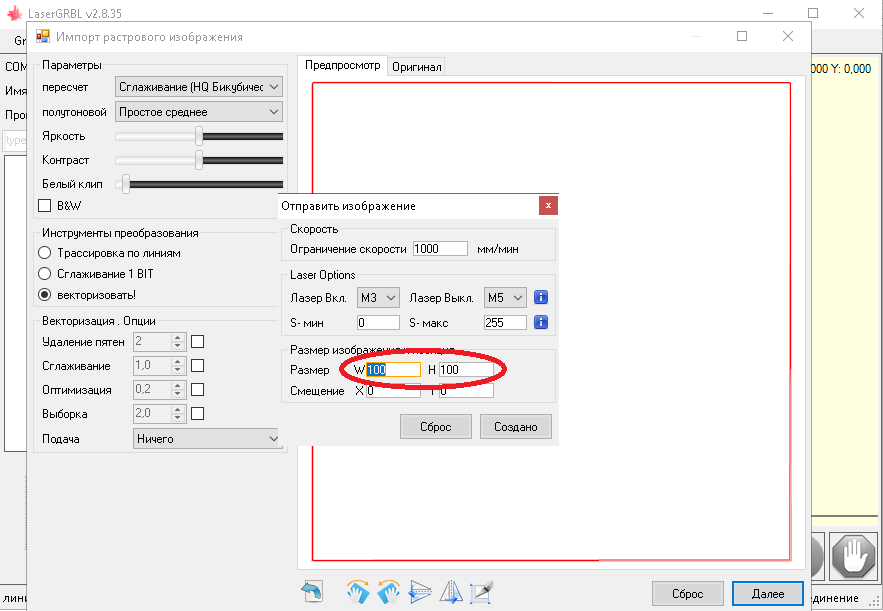
Рисунок 7 – Установка габаритных размеров детали
3. Задать минимальное и максимальное значение мощности рабочего органа рисунок 8.
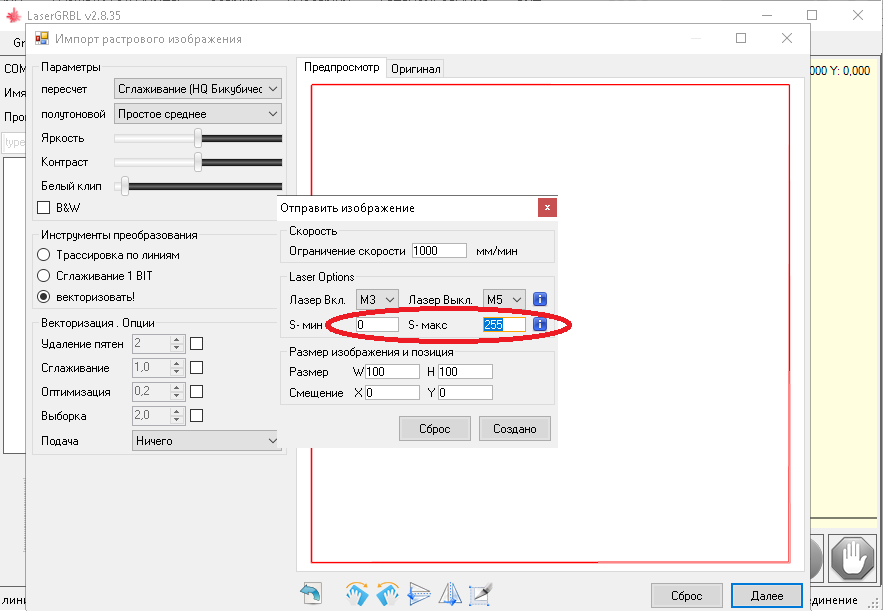
Рисунок 8 – Задание мощности
4. Задать ограничение по скорости резания (мм/мин.) рисунок 9.
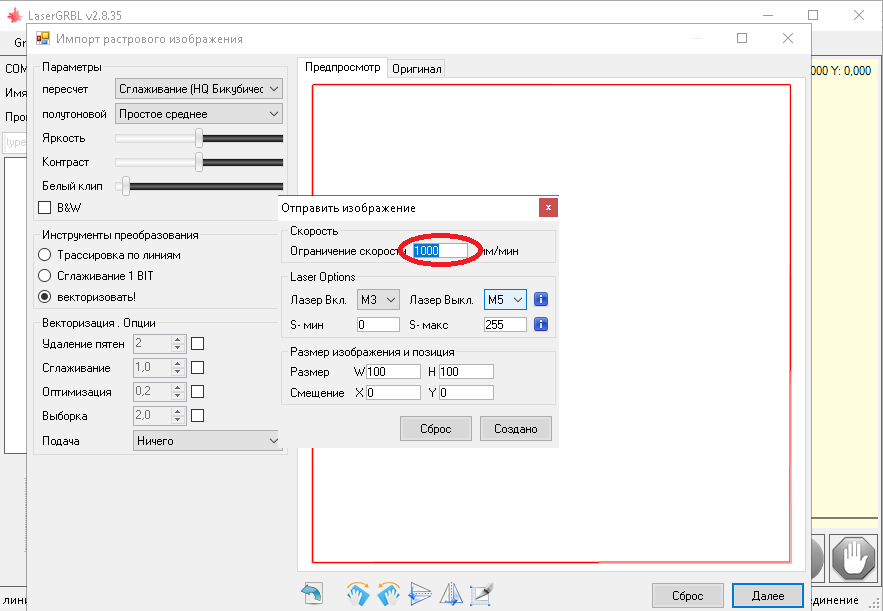
Рисунок 9 – Настойка ограничения скорости резания
5. Нажать кнопку «Создано».
3.3. Подключение порта контролера станка к программе: 1. В поле «COM порт» выбрать порт COM3 рисунок 10 и нажать на кнопку «Подключить».
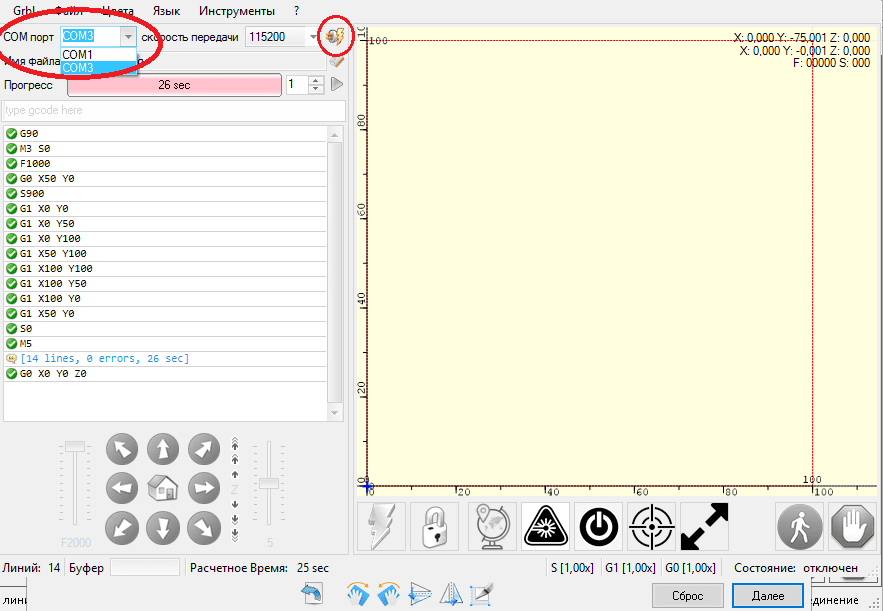
Рисунок 10 – Выбор порта подключения
В поле «Расчетное Время» будет указано приблизительное время для выполнения задания с учетом заданных настроек рисунок 11.
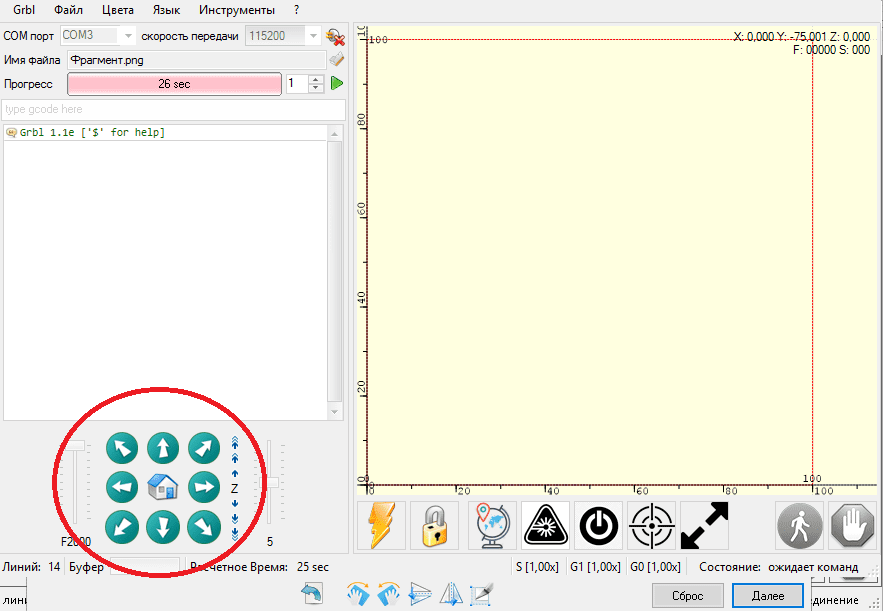
Рисунок 11 – Оценка необходимого времени работы станка
2. Выполнить перемещение осей. Стрелки-клавиши отвечают за переме-щение осей станка, ползунок слева настраивает скорость перемещение всех осей в мм/мин., ползунок справа регулирует расстояние перемещения осей в мм, центральная кнопка возвращает резак в «нулевую точку» рисунок 12.
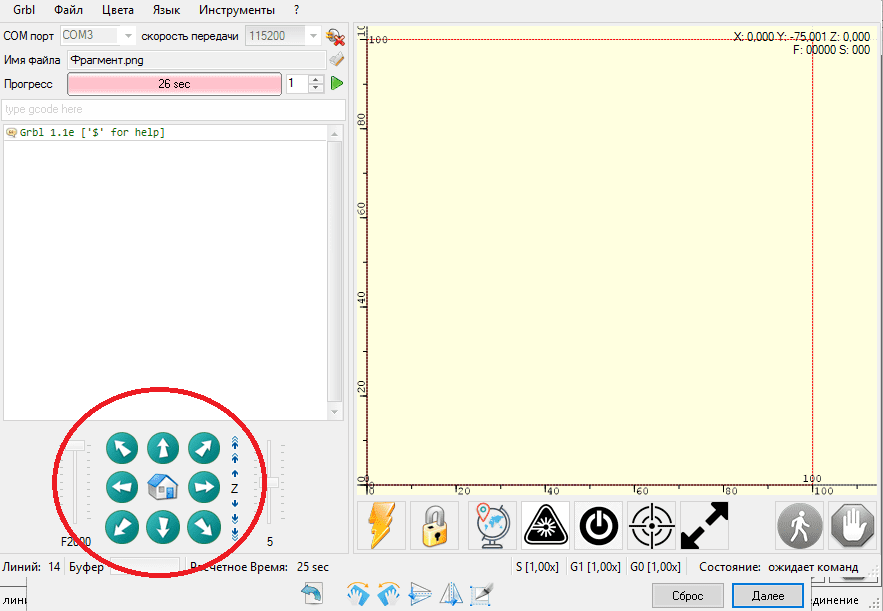
Рисунок 12 – Кнопки управления перемещением осей станка
3. Установить «Нулевую точку» перемещаем оси станка в нужное поло-жение на заготовке и нажать на кнопку «Глобус» рисунок 13, теперь программа будет понимать, от какой точки ей начинать движение, и курсор резака на рабочем поле программы сместиться в крайнее правое положение на отметку 0 рисунок 14.
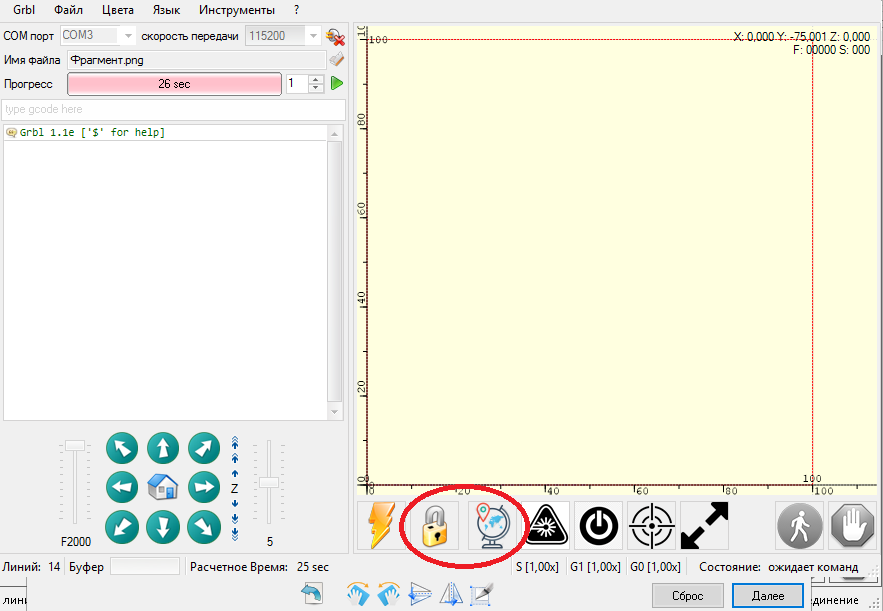
Рисунок 13 – Установка резака в начало отсчета («нулевая точка»)
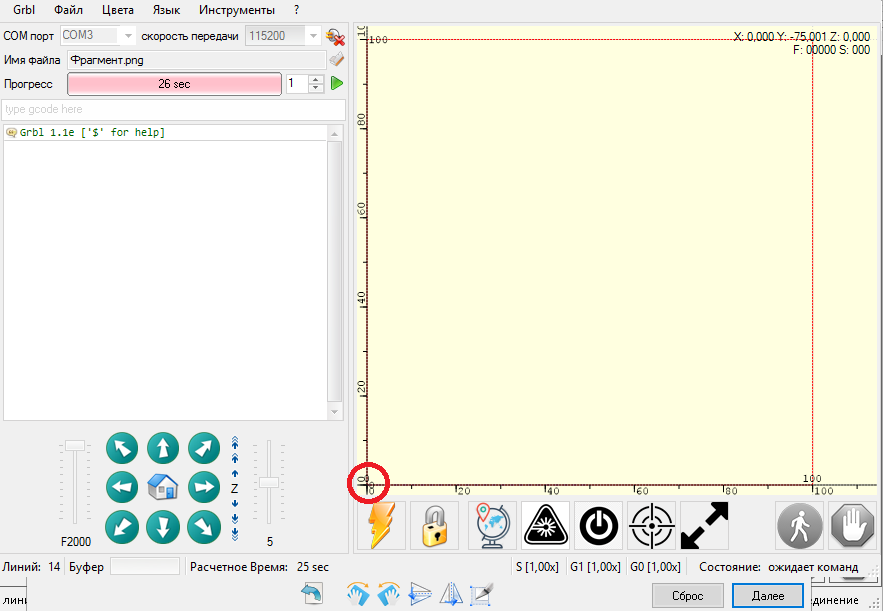
Рисунок 14 – Результат установки в нулевую точку
4. Запуск программы и станка на исполнение задания. Для этого необходимо нажать зеленую кнопку «PLAY» рисунок 15.
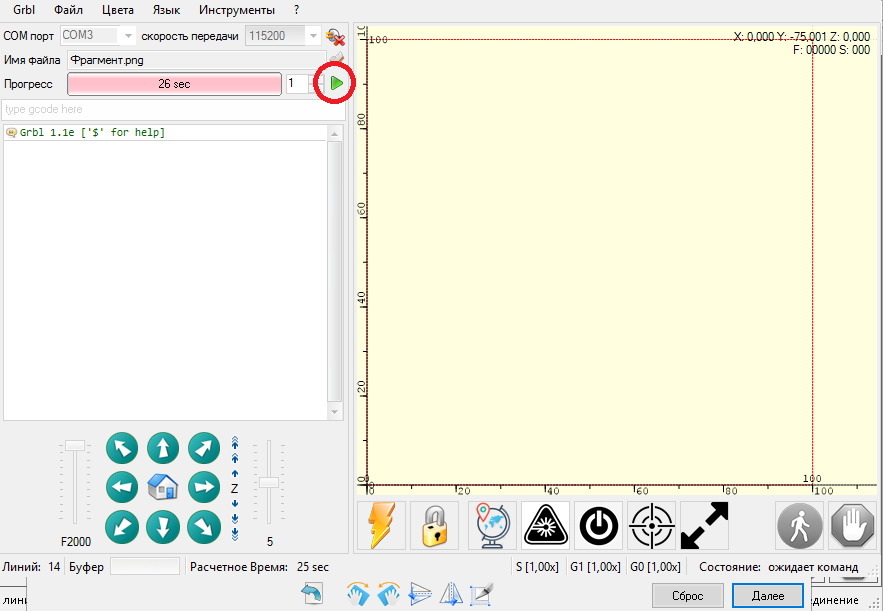
Рисунок 15 – Запуск программы на выполнение
После нажатия курсор резака начнет движение вдоль линии детали, а на шкале «Прогресс» отображается количество отработанного программой времени рисунок 16.
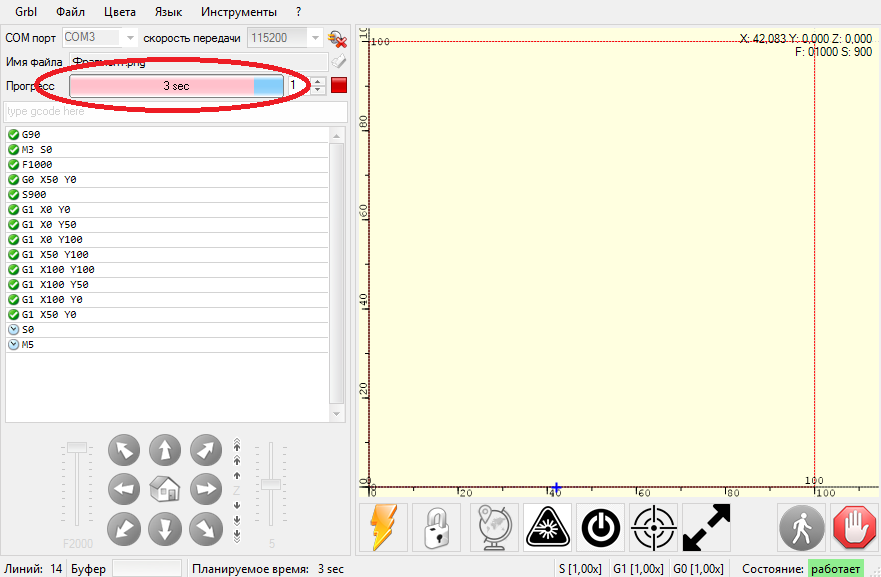
Рисунок 16 – Отображение отработанного времени
По окончанию работы резак вернется в нулевую точку.
Выводы
В выпускной квалификационной работе бакалавра выполнен проект натурной модели переносного плазмореза с ЧПУ. Представлен анализ информации о переносных станках; краткие сведения о технологии плазменной резки, рассмотрены виды станков для плазменной резки, приведены их характеристики. Предложена конструкция переносного плазмореза, в системе автоматизированного проектирования КОМПАС создана трехмерная модель станка. Выполнены расчеты по определению энергосиловых параметров механизмов перемещения резака по оси Х и по оси Y, выбраны шаговые двигатели, муфты, подшипники качения и линейные подшипники направляющих. Проведены проверочные прочностные расчеты винтовых передач. Даны рекомендации по смазке узлов трения и разработан линейный график сборки станка. Составлена смета затрат. Рассмотрены вопросы охраны труда персонала, работающего на плазморезе.
Список источников
- Ерёменко Ю.И. и др. Экспертная система технического обслуживания ма-шин. – Старый Оскол: СОФ МИСиС, 1999. – 306 с.
- Принцип работы плазмореза [Электронный рессурс]. - Режим доступа: https://ingeneryi.info.
- Анурьев А.А. Справочник конструктора. Т.1. – М.: Машиностроение, 2000. – 586 с.
- Иванов А.С. Конструируем машины. Шаг за шагом. В 2-х частях. – Ч.1. – М.: Изд-во МГТУ им. Н.Э Баумана, 2000. – 328 с.
- Иванов А.С. Конструируем машины. Шаг за шагом. В 2-х частях. – Ч.2. – М.: Изд-во МГТУ им. Н.Э Баумана, 2003. – 392 с.
- Перель Л.Я. Подшипники качения: Расчет, проектирование и обслужи-вание опор: Справочник. – М.: Машиностроение, 1983. – 543 с.
- Бельков, В.Н. Основы расчёта и конструирования винтовых механизмов: учеб. пособие / В. Н. Бельков. – Омск: Изд-во ОмГТУ, 2008. – 160 с
- Седуш В.Я. Надежность, ремонт и монтаж металлургических машин: Учеб-ник. - К.: УМК ВО, 1992. - 368 с.
- Гедык П.К., Калашникова М.И. Смазка металлургического оборудования. –М.: Металлургия, 1971. - 376 с.
- Рыбанов В.М. Сварка и резка металлов. – М.: Высшая школа, 1979. – 214 с.