Реферат за темою випускної роботи
Зміст
- вступ
- 1. Організація і структура ремонтного виробництва на підприємствах чорної металургії
- 2. Технологія і конструкції верстатів плазмового різання
- 2.1 короткий опис процесу плазмового різання
- 2.2 загальний пристрій і принцип роботи плазмореза
- 2.3 огляд пристроїв для плазмового різання
- 3. Опис конструкції моделі переносного верстата плазмового різання з чпу
- 4. Програмна настройка плазмореза
- висновки
- Список джерел
вступ
Невід'ємною складовою надійності обладнання є ремонтопридатність, показники якої (тривалість, трудомісткість, вартість відновлення) впливають на економічну ефективність виробництва. Для металургійних машин, що характеризуються унікально-стю конструкцій, великими габаритними розмірами і масами, одиничним і дрібносерійним виготовленням елементів, питання вдосконалення технології проведення ремонтно-відновлювальних робіт залишаються актуальними. Одним з напрямків розвитку є організація ремонту і відновлення елементів обладнання безпосередньо на місці експлуатації, без транспортування в спеціальні ремонтні цехи, використовуючи переносні металообробні верстати та комплекси. Металургійні, енергетичні, Гірничі машини, що характеризуються тривалими термінами роботи і мають зношені корпусні або несучі деталі, - найбільш перспективні об'єкти для використання переносних верстатів.[1]
В даний час відзначається розширення парку переносних (мобіль-них) верстатів і комплексів, що випускаються зарубіжними і вітчизняними виробниками, серед яких можна виділити: Токарні; розточувальні і розточувально-наплавочні; фрезерні; свердлильні; для планування (торцювання). Окрему групу складають верстати для газового та плазмового різання металу. В ході практики виконано пошук інформації про технології плазмового різання, конструкціях верстатів, а також розрахунок параметрів для моделі переносного плазмореза пропонованої конструкції.
1. Організація і структура ремонтного виробництва на підприємствах чорної металургії
Завдання ремонтного виробництва металургійного заводу зводиться до забезпечення безперебійної, надійної і високопродуктивної роботи обладнання при мінімальних витратах коштів. В останні роки проведена значна робота по поліпшенню утримання та ремонту обладнання металургійних заводів. До складу ремонтного виробництва металургійного заводу входять цехи з ремонту обладнання (доменного, електросталеплавильного, прокатного), з виготовлення ремонтно-експлуатаційного металу (ливарні, ковальські, металоконструкцій, механічні та ін.), склад запасних частин, склад напівфабрикатів. Структура управління ремонтним виробництвом визначається масштабом заводу і існуючими методами організації ремонту. У виробничих цехах підтриманням працездатності обладнання займається ремонтна служба очолює ремонтну службу цеху помічник начальника цеху з Механічного обладнання (механік цеху). У безпосередньому підпорядкуванні Механіка цеху знаходь.[2-6]
2. Технологія і конструкції верстатів плазмового різання
Плазма-це високотемпературний іонізований газ, що володіє високою електропровідністю. Процес плазмового різання заснований на використанні повітряно-плазмової дуги постійного струму прямого дії (електрод - катод, що розрізається метал – анод). Для збудження робочої дуги (електрод - метал, що розрізається), за допомогою осцилятора запалюється допоміжна дуга між електродом і соплом - так звана чергова дуга, яка видувається з сопла пусковим повітрям у вигляді факела довжиною 20-40 мм Застосування способу плазмового різання, при якому в якості плазмообразующего газу використовується стиснений повітря, відкриває широкі можливості при розкрої низьковуглецевих і легованих сталей, а також кольорових металів та їх сплавів.
Верстат для плазмового різання (плазморез) складається з декількох компонентів Малюнок 1:
- Джерело живлення;
- Плазмовий різак;
- Повітряний компресор;
- Кабель-шлангового пакета
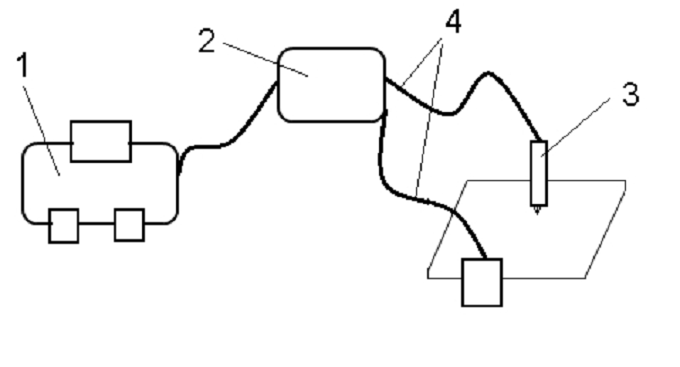
Малюнок 1-Загальний пристрій плазморезу
2.1 Короткий опис процесу плазмового різання
Для збудження робочої дуги (електрод - метал, що розрізається), за допомогою осцилятора запалюється допоміжна дуга між електродом і соплом-так звана чергова дуга, яка видувається з сопла пусковим повітрям у вигляді факела довжиною 20-40 мм малюнок 2.
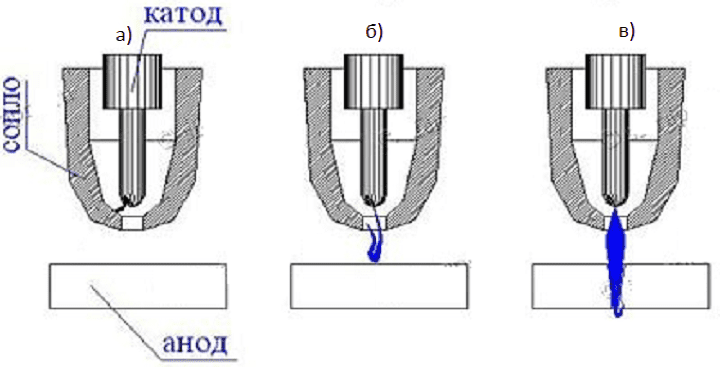
Малюнок 2-фази утворення робочої дуги:
а) зародження чергової дуги;
б) видування чергової дуги до торкання з поверхнею металу, що розрізається;
в) поява робочої (ріжучої) дуги і проникнення через рез металу
Струм чергової дуги дорівнює 25 або 40 ... 60 а, в залежності від джерела плазмової дуги. При торканні факела чергової дуги металу виникає ріжуча дуга-рабо-чаю, і включається підвищена витрата повітря; чергова дуга при цьому авто-матично відключається.
Переваги повітряно-плазмового різання в порівнянні з механізиро-ванною кисневої і плазмової різкою в інертних газах наступні:
- Простота процесу різання;
- Застосування недорогого плазмообразующего газу-повітря;
- Висока чистота різу (при обробці вуглецевих і низьколегованих сталей);
- Знижена ступінь деформації;
- Більш стійкий процес, ніж різання в водневмісних сумішах.
2.2 Загальний пристрій і принцип роботи плазмореза
Головним елементом верстата є плазмовий різак або плазмотрон, який складається з сопла, електрода, охолоджувача (ізолятора) між ними і каналу для подачі стисненого повітря малюнок 3.
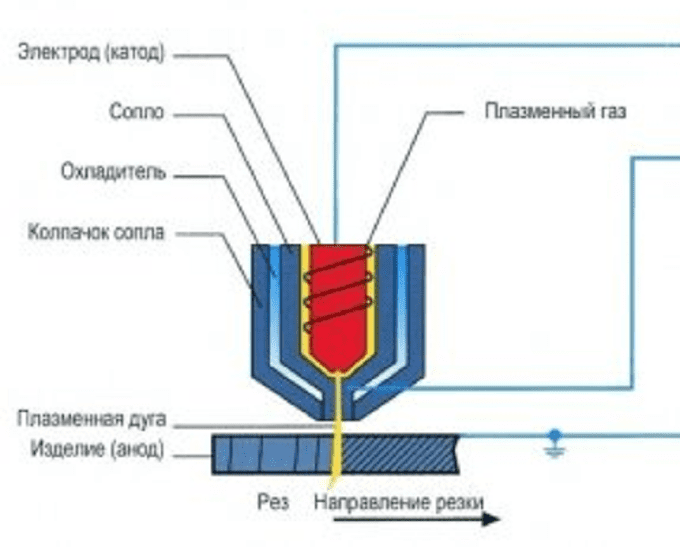
Малюнок 3-Принципова схема плазмореза.
Усередині корпусу плазмотрона знаходиться електрод, який служить для збудження електричної дуги. Сопло плазмотрона обжимає і формує плазмову струмінь, яка виривається з вихідного каналу і розрізає заготовку. Компресор забезпечує подачу повітря. Технологія плазмового різання має на увазі використання газів: плазмообразующих і захисних.
Кабель-шланговий пакет з'єднує джерело живлення, компресор і плазмотрон. По електричному кабелю подається струм від трансформатора або інвертора для збудження електричної дуги, а по шлангу йде стиснене повітря, який необхідний для утворення плазми всередині плазмотрона.
Принцип роботи плазмореза наступний. При включенні джерела Пі-Танія (інвертора) 2 на плазмотрон надходить струм високої частоти. В результаті всередині плазмотрона виникає чергова електрична дуга, температура якої 6000 – 8000 °С. Чергова дуга запалюється між електродом і наконечником сопла на увазі того, що утворення дуги між електродом і оброблюваної заготівлею відразу важко. Стовп чергової дуги заповнює весь канал сопла.
Після виникнення чергової дуги в камеру сопла починає надходити стиснене повітря. Звужене до низу сопло плазмотрона стискає повітряний струмінь і формує потік, який зі швидкістю 2-3 м/з виривається з сопла. Температу-ра повітря в цей момент може досягати 25000 – 30000 °С. Саме цей високотемпературний іонізоване повітря і є в даному слу-чаї плазмою.
Її електропровідність приблизно дорівнює електропровідності металу, який обробляється. У той момент, коли плазма виривається з сопла і стикається з по-верхностью оброблюваного металу, запалюється ріжуча дуга, а чергова дуга гасне. Ріжуча (робоча) дуга розігріває оброблювану заготовку локально в місці різу. Метал плавиться, з'являється рез
2.3 Огляд пристроїв для плазмового різання
Пристроїв для плазмового різання можна розділити на дві групи: ручні плазморізи і апарати машинного різання (верстати). Ручні плазморізи використовуються в побуті, на маленьких виробництвах і в приватних майстернях для виготовлення і обробки деталей. При цьому способі рез виходить рівним, але не ідеальним; производи-ність виконуваних операцій не висока.
На машинобудівних підприємствах для виготовлення деталей або обробки заготовок застосовуються верстати (машини) плазмового різання, сучасні конструкції яких мають ЧПУ (числове програмне управління). Верстат з ЧПУ працює за заданою програмою з мінімальною участю оператора, що максимально виключає людський фактор на виробництві і значно збільшує продуктивність.
Якість різу машинним апаратом ідеально, не потрібна додаткова обробка кромок. Також забезпечується виконання фігурних різів. Тривалість включення верстата може досягати 100 %. Ціна на верстат плазмового різання в залежності від складності і розмірів становить 3000...20000 у.о. можна виділити машини важкого, середнього і малого класу. До машин малого класу відносяться і переносні верстати.
3. Опис конструкції моделі переносного верстата плазмового різання з чпу
Головним завданням проекту є детальне опрацювання конструкції малогабаритного переносного верстата плазмового різання з ЧПУ. З цією метою в системі автоматизованого проектування КОМПАС була створена трьох-мірна модель плазмореза малюнок 4. Масштаб комп'ютерної моделі відповідав натуральним розмірам.
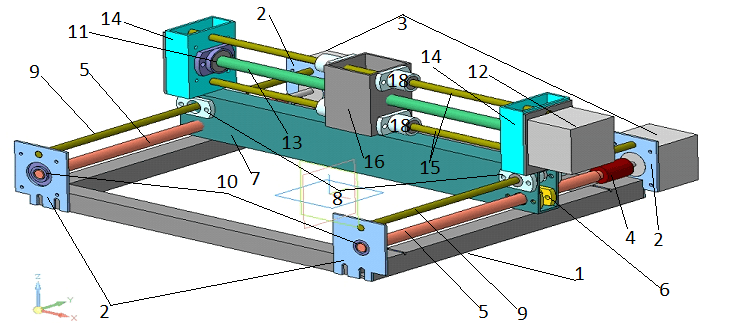
Малюнок 4-тривимірна модель розробленого переносного плазмореза.
Підстава верстата 1 являє собою зварену раму, виконану з профільної труби квадратного поперечного перерізу. На рамі розміщуються механізми переміщення різака по осях Х і Y. на бічних поверхнях рами з чотирьох сторін закріплені опорні пластини 2, до двох з яких кріпляться крокові двигуни 3 механізму переміщення по осі Y. Вали двигунів за допомогою гнучких муфт 4 з'єднуються з гвинтами 5, які спільно з гайками 6 утворюють гвинтові передачі механізму переміщення по осі Y. Гайки 6 змонтовані всередині траверси 7, виготовленої з профільної труби прямокутного перетину. На траверсі закріплені лінійні підшипники 8 для напрямних 9. По два підшипника на кожну направляючу. Напрямні 9 являють собою циліндричні стрижні, що спираються на пластини 2. Крім того на пластинах 2 закріплені корпусу 10 підшипників кочення 11, які є опорами гвинтів 5. Гвинтові передачі 5-6 перетворюють обертання валів двигунів 3 в поступальний рух травер
На траверсі 7 змонтований механізм переміщення різака по осі х. до складу механізму входить кроковий двигун 12, який через гнучку муфту з'єднується з гвинтом 13. Гвинт спирається на підшипники кочення 11, Корпуси 10 яких закріплені на стійках 14, встановлених на краях траверси 7. Стійки 14 виступаю також як опори напрямних 15. Уздовж напрямних 15 і гвинта 13 переміщається каретка 16 із закріпленим на ній плазмотроном 17. Гайка, що забезпечує переміщення каретки, розташована всередині каретки 16. Корпуси 17 лінійних підшипників 18 напрямних 17 закріплені на каретці 17 із зовнішніх сторін.
4. Програмна настройка плазмореза
Для того щоб вирізати деталь на плазморезе з ЧПУ необхідно спочатку написати програму управління для контролера верстата. Нижче наведена послідовність виконуваних дій. 1. Створення креслення деталі. Для цього відкрити програму "КОМПАС-3D" і в файлі типу фрагмент Малюнок 1 створити зображення деталі малюнок 2.
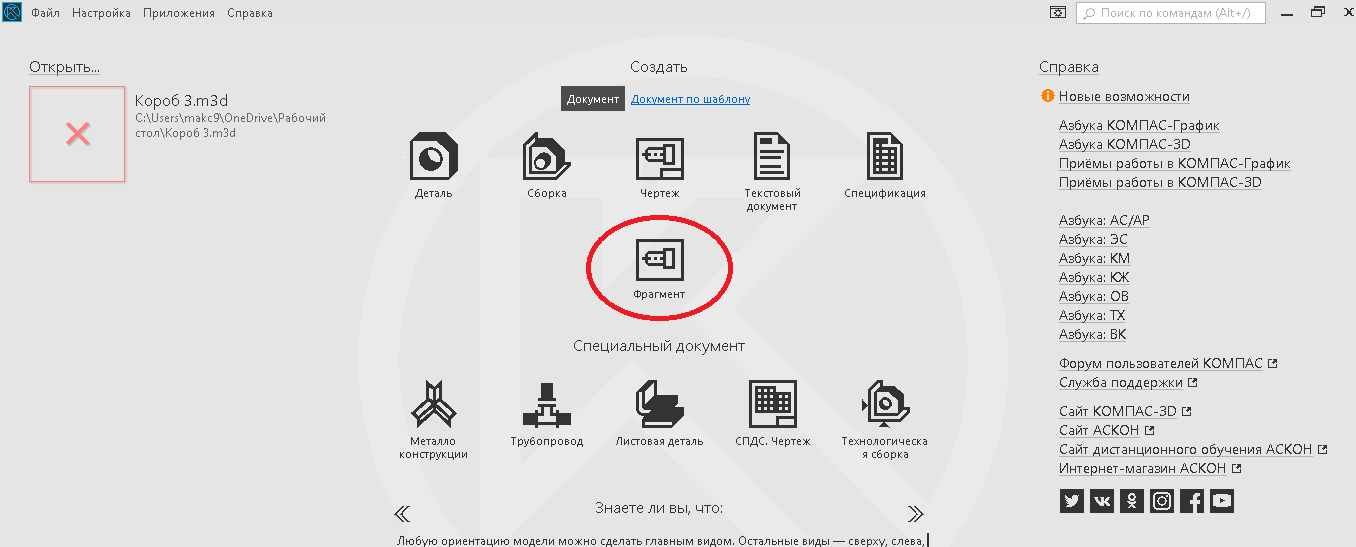
Малюнок 1-Вибір файлу типу фрагмент в системі КОМПАС
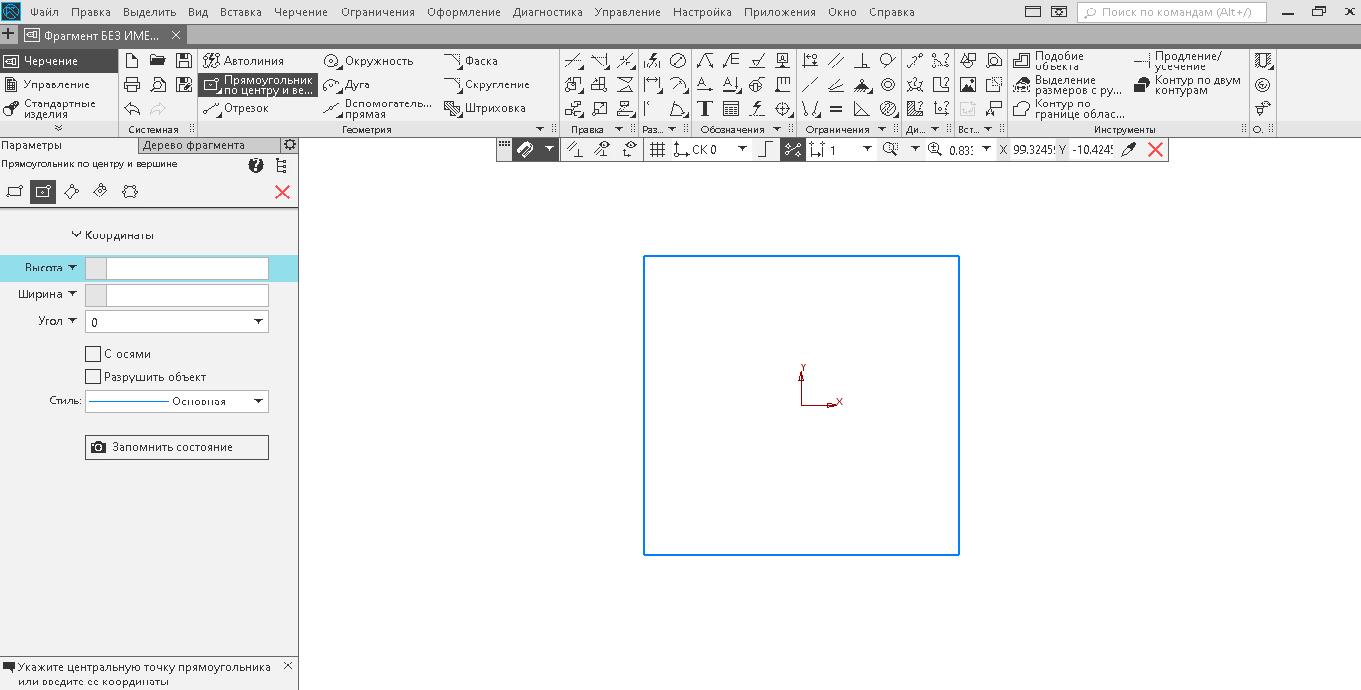
Малюнок 2-Збереження зображення деталі
2. Зберегти зображення деталі в форматі PNG в масштабі 1: 1 малюнок 3.
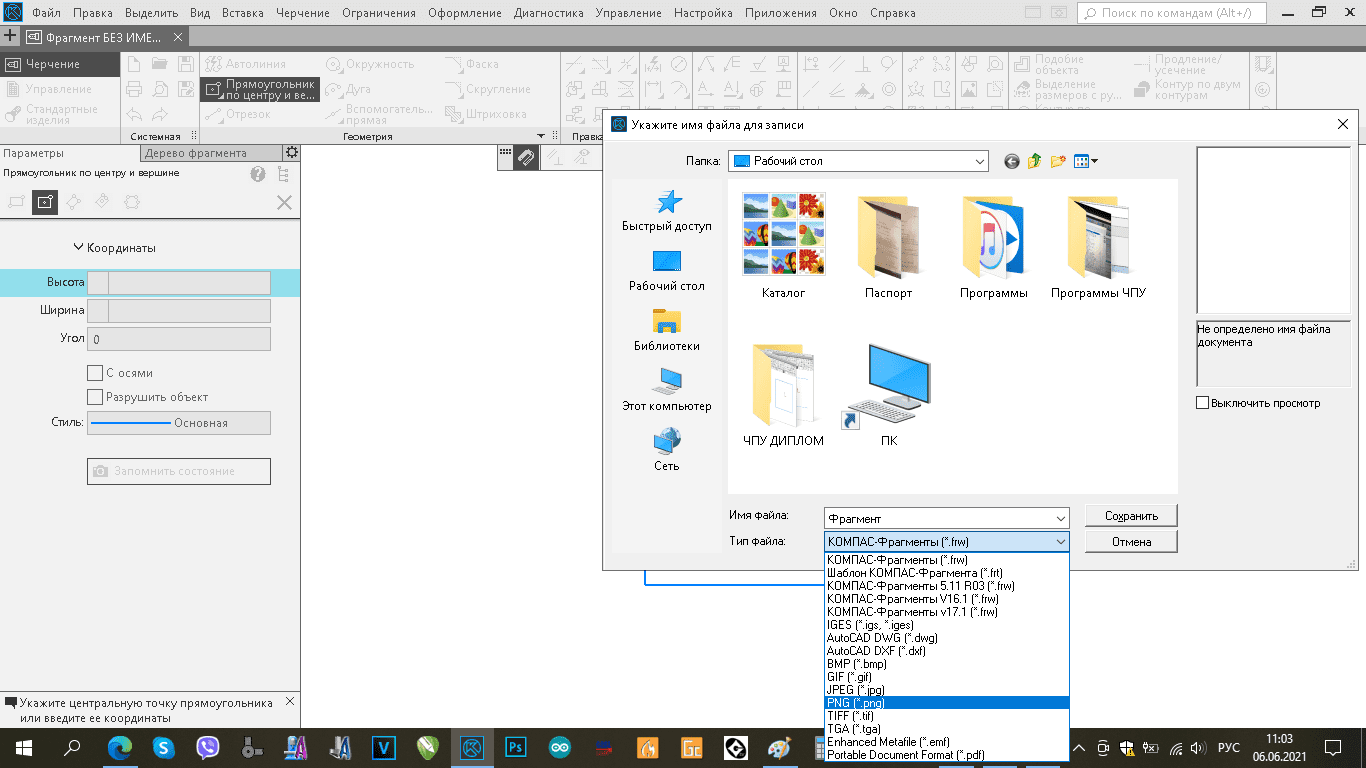
Малюнок 3-креслення зображення деталі
3. Завдання налаштувань різання для файлу деталі. 3.1. Запустити програму LaserGRBL малюнок 4 і вибрати збережений файл малюнок 5.
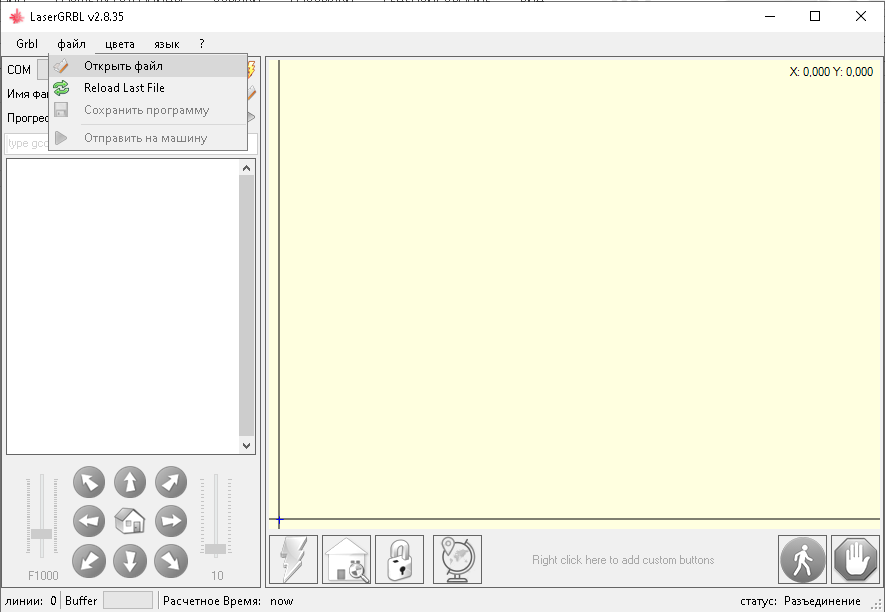
Малюнок 4-Інтерфейс програми LaserGRBL
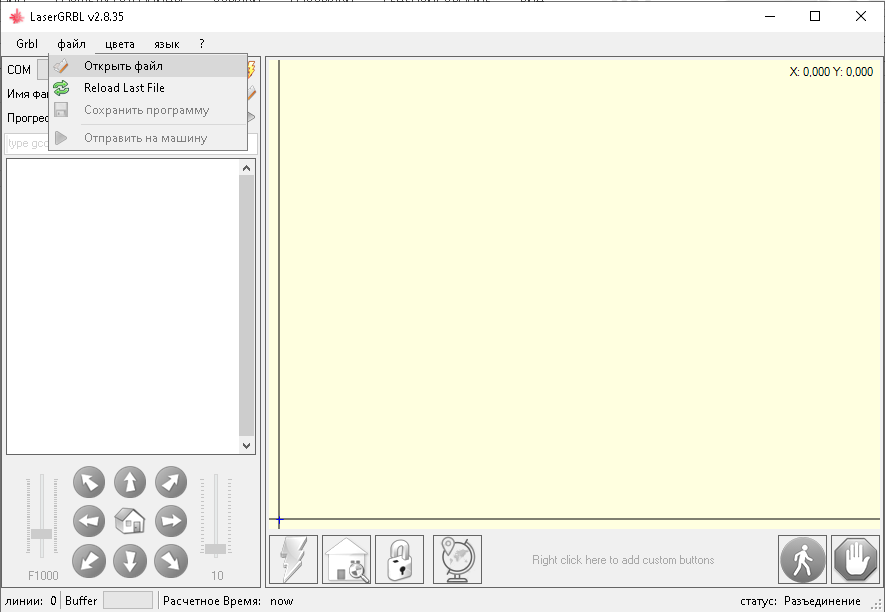
Малюнок 5-Вибір файлу в програмі LaserGRBL
3.2. У вікні задати налаштування параметрів різання.
1. Вибрати параметр» Векторизувати " малюнок 6. Натиснути кнопку "Так-леї".
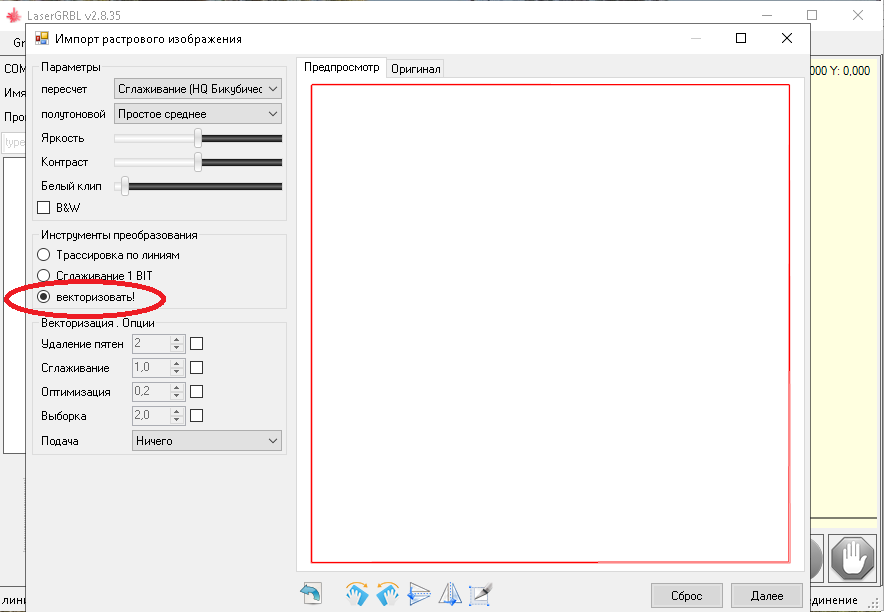
Малюнок 6-Налаштування векторизації
2. У вікні виставити габаритні розміри деталі-ширину W і висоту H (мм) малюнок 7.
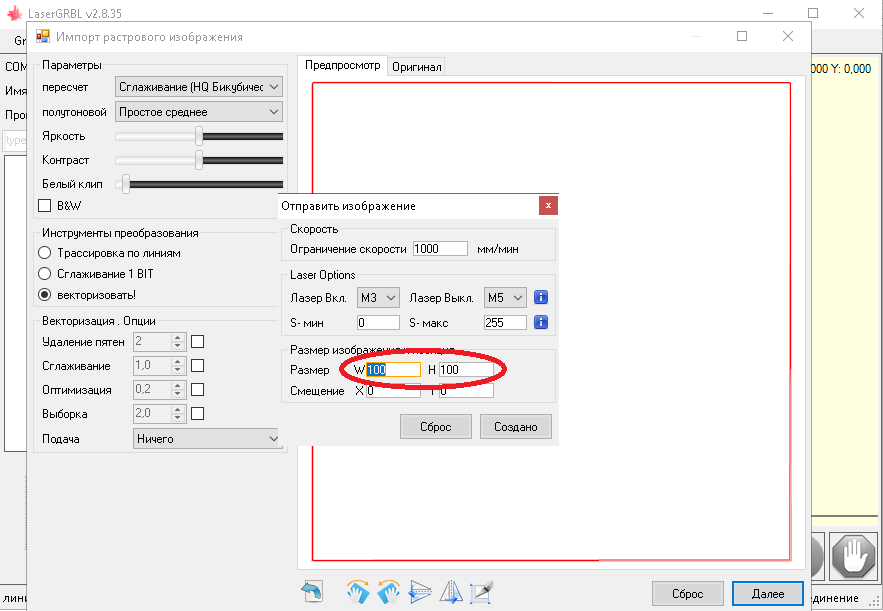
Малюнок 7-Установка габаритних розмірів деталі
3. Задати мінімальне і максимальне значення потужності робочого органу Малюнок 8.
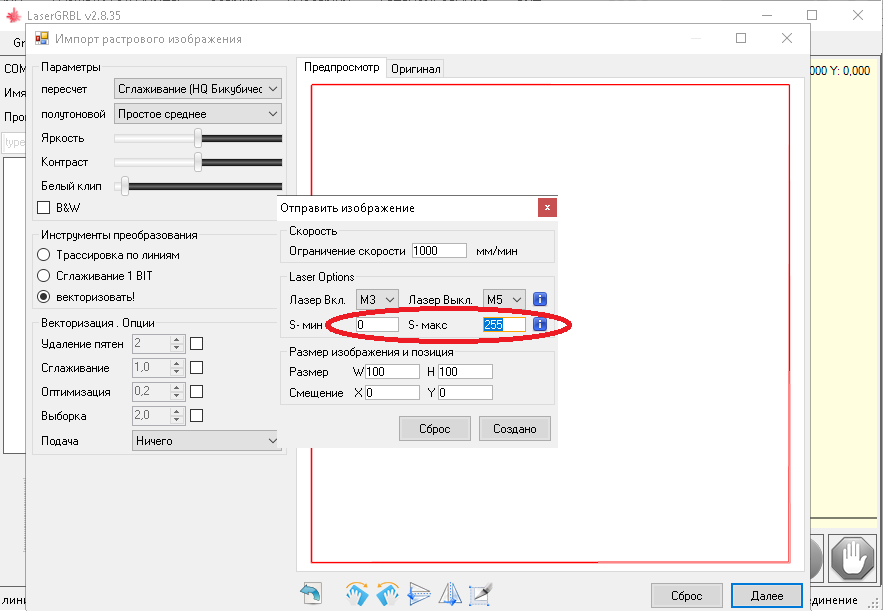
Малюнок 8 - завдання потужності
4. Задати обмеження по швидкості різання (мм/хв.) малюнок 9.
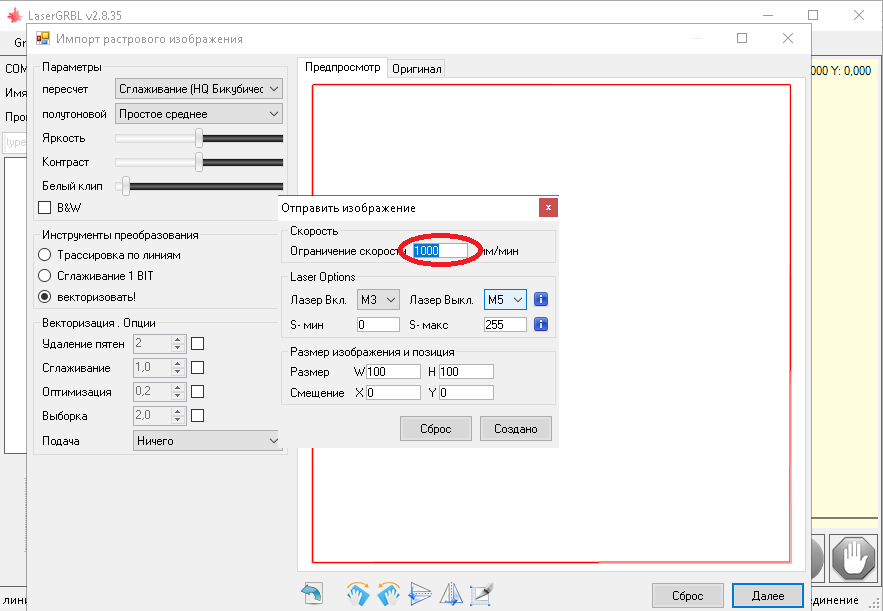
Малюнок 9-настоянка обмеження швидкості різання
5. Натиснути кнопку»створено".
3.3. Підключення порту контролера верстата до програми: 1. В поле "COM порт «вибрати порт COM3 малюнок 10 і натиснути на кнопку»Підключити".
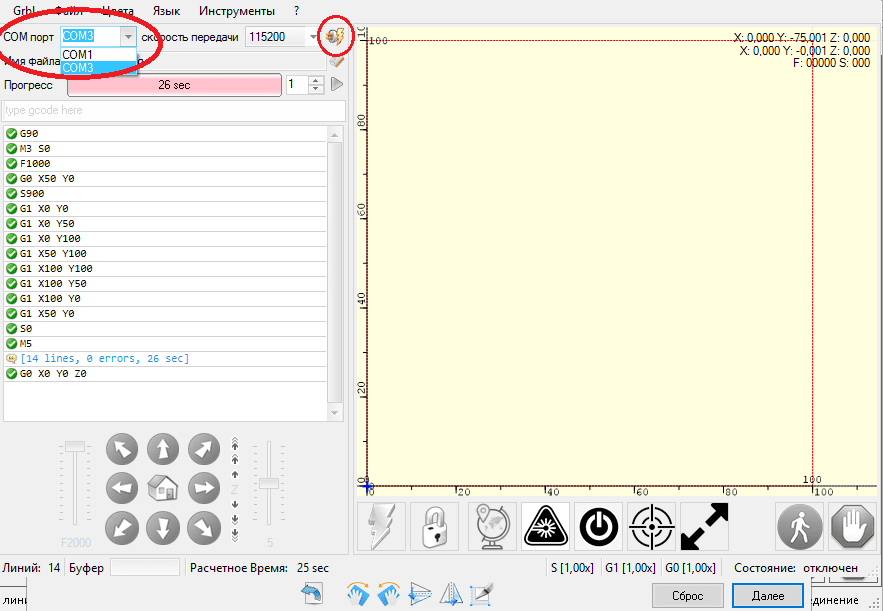
Малюнок 10-Вибір порту підключення
В поле» Розрахунковий час " буде вказано приблизний час для виконання завдання з урахуванням заданих налаштувань малюнок 11.
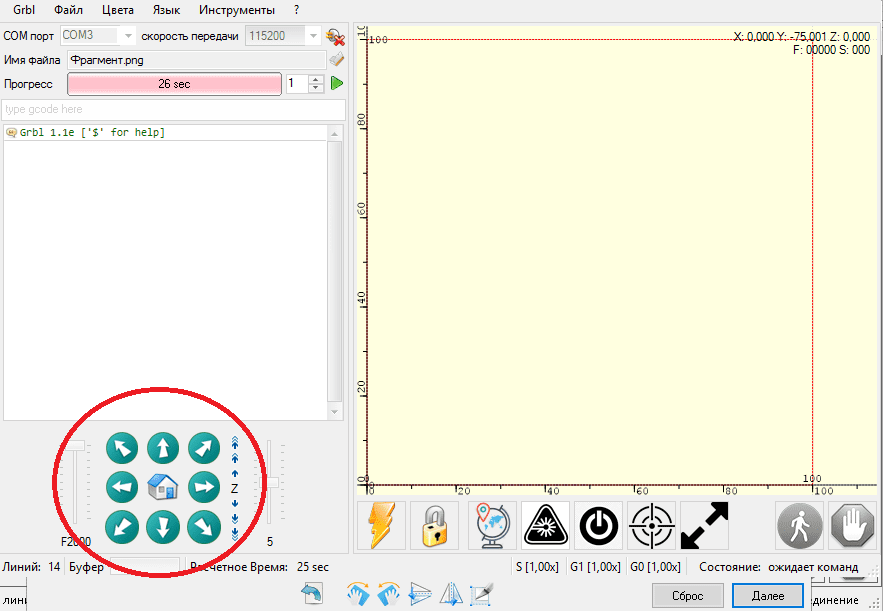
Малюнок 11-оцінка необхідного часу роботи верстата
2.Виконати переміщення осей. Стрілки-клавіші відповідають за переме-щення осей верстата, повзунок зліва налаштовує швидкість переміщення всіх осей в мм/хв., повзунок праворуч регулює відстань переміщення осей в мм, центральна кнопка повертає різак в «нульову точку» малюнок 12.
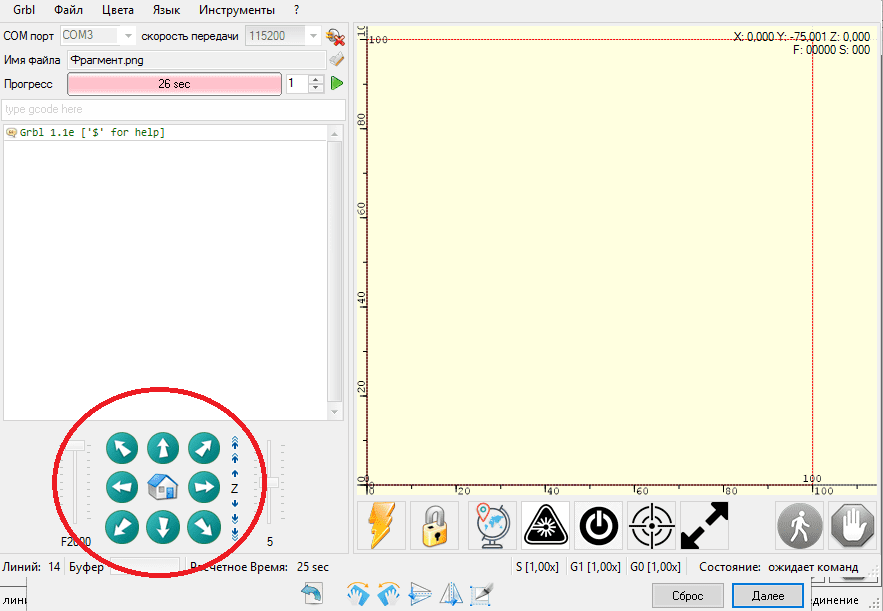
Малюнок 12-Кнопки управління переміщенням осей верстата
3. Встановити "нульову точку" переміщаємо осі верстата в потрібне положення на заготівлі і натиснути на кнопку "Глобус" малюнок 13, тепер програма буде розуміти, від якої точки їй починати рух, і курсор різака на робочому полі програми зміститися в крайнє праве положення на позначку 0 малюнок 14.
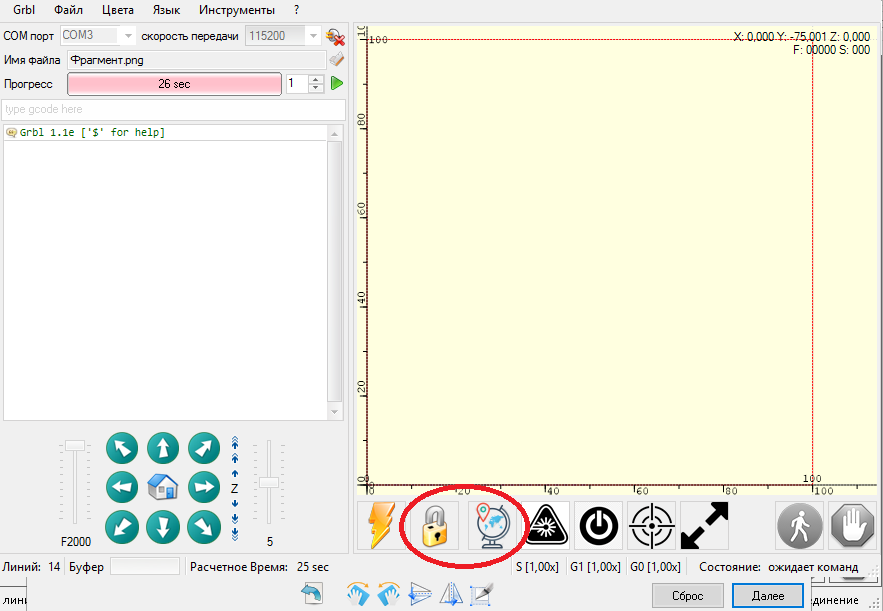
Малюнок 13-Установка різака в початок відліку « "нульова точка"»
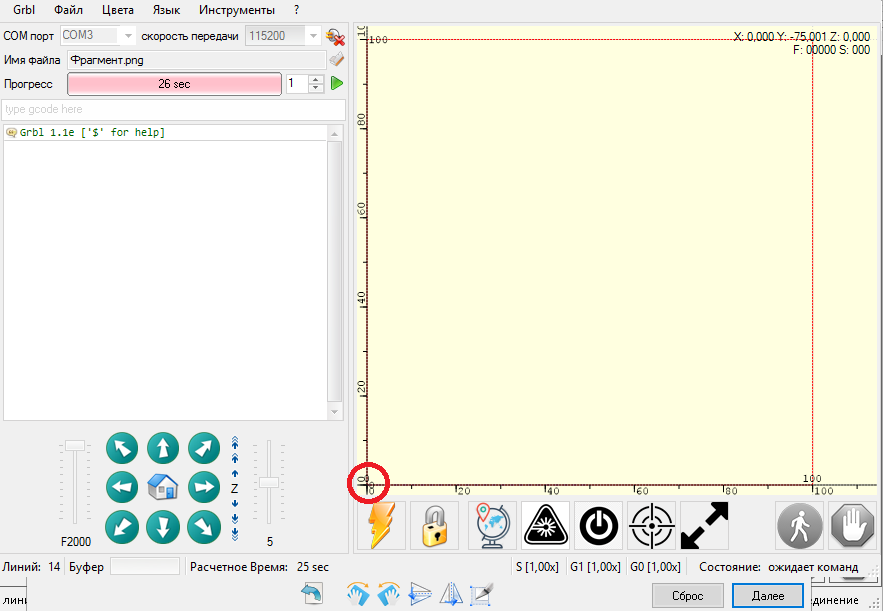
Малюнок 14-Результат установки в нульову точку
4. Запуск програми і верстата на виконання завдання. Для цього необхідно натиснути зелену кнопку «PLAY» малюнок 15.
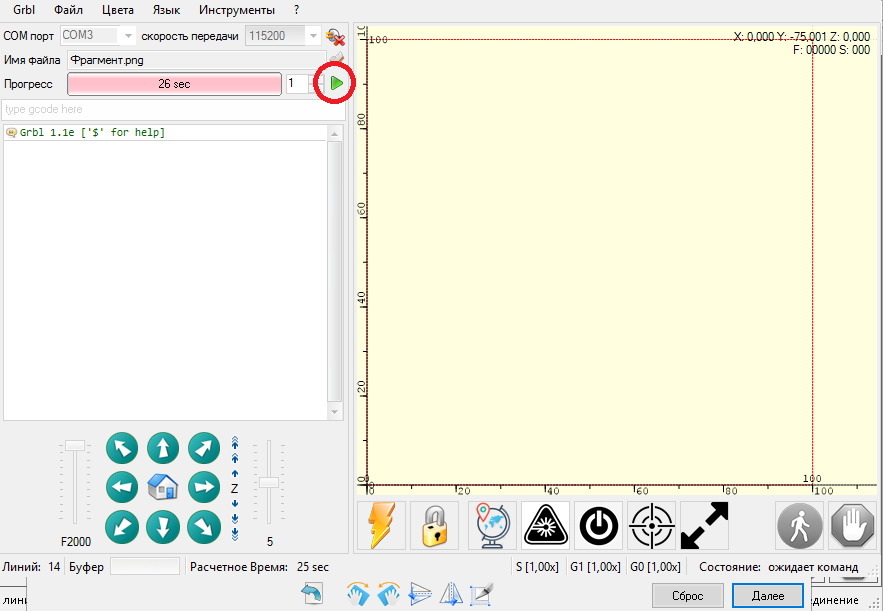
Малюнок 15-Запуск програми на виконання
Після натискання курсор різака почне рух уздовж лінії деталі, а на шкалі «прогрес» відображається кількість відпрацьованого програмою часу малюнок 16.
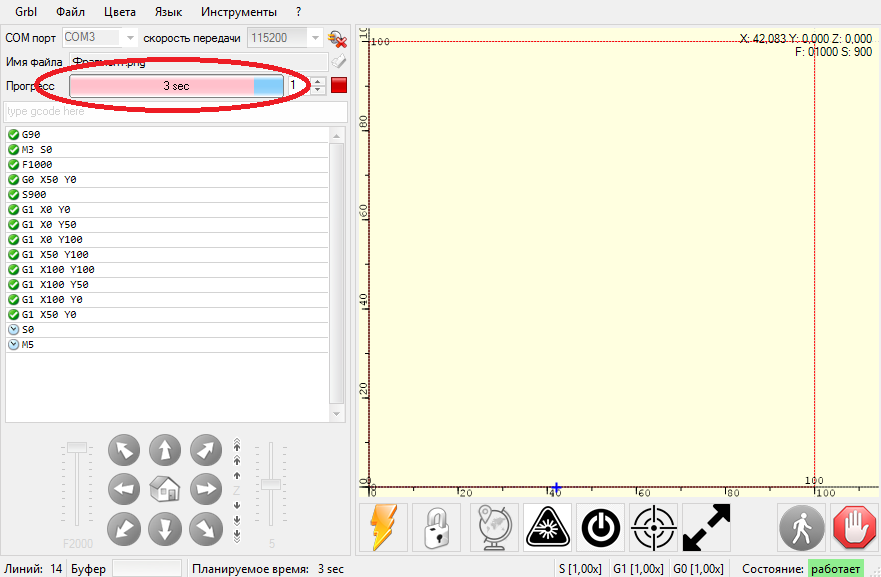
Малюнок 16-відображення відпрацьованого часу
По закінченню роботи різак повернеться в нульову точку.
Висновок
У випускній кваліфікаційній роботі бакалавра Виконано проект натурної моделі переносного плазмореза з ЧПУ. Представлений аналіз інформації про переносних верстатах; короткі відомості про технології плазмового різання, розглянуті види верстатів для плазмового різання, наведені їх характеристики. Запропонована конструкція переносного плазмореза, в системі автоматизованого проектування КОМПАС створена тривимірна модель верстата. Виконані розрахунки по визначенню енергосилових параметрів механізмів переміщення різака по осі Х і по осі Y, обрані крокові двигуни, муфти, підшипники кочення і лінійні підшипники напрямних. Проведено перевірочні розрахунки міцності гвинтових передач. Дано рекомендації по змащенню вузлів тертя і розроблений лінійний графік складання верстата. Складено кошторис витрат. Розглянуто питання охорони праці персоналу, що працює на плазморезі.
Список джерел
- Єременко ю.і. та ін експертна система технічного обслуговування ма-шин. - Старий Оскол: СОФ місіс, 1999. - 306 с.
- Сайт https://ingeneryi.info.
- Анур'єв А.а. довідник конструктора. Т.1. - М.: Машинобудування, 2000. - 586 с.
- Іванов А.С. конструюємо машини. Крок за кроком. У 2-х частинах. - Ч.1. - М.: Вид-в МГТУ ім. Н. Е Баумана, 2000. - 328 с.
- Іванов А.С. конструюємо машини. Крок за кроком. У 2-х частинах. - Ч.2. - М.: Вид-в МГТУ ім. Н. Е Баумана, 2003. - 392 с.
- Перель Л.Я. підшипники кочення: Розрахунок, проектування і обслужи-вання опор: довідник. - М.: Машинобудування, 1983. - 543 с.
- Бельков, В. Н.основи розрахунку і конструювання гвинтових механізмів: учеб. посібник / В. Н. Більків. – Омськ: Изд-во ОмГТУ, 2008. – 160 с
- Седуш В.Я. надійність, ремонт і монтаж металургійних машин: Учеб-Нік. - К.: УМК ВО, 1992. - 368 с.
- Гедик П.К., Калашникова м. і. мастило металургійного обладнання. - М.: Металургія, 1971. - 376 с.
- Рибанов в.м. зварювання та різання металів. - М.: Вища школа, 1979. - 214 с.