Реферат по теме выпускной работы
Содержание
- Введение
- 1. Актуальность темы.
- 2. Цель и задачи исследования.
- 3. Анализ высокотемпературной камерной печи как объекта автоматизации.
- 4. Критический обзор известных технических решений по автоматизации высокотемпературной камерной печи.
- 5. Разработка алгоритма работы и схемных решений устройства автоматического управления высокотемпературной камерной печи.
- Выводы
- Список источников
Введение
Промышленные предприятия выпускают множество изделий из металла. Важной составляющей технологического процесса является термическая обработка деталей. Химические и физические процессы, протекающие при термообработке, обуславливают состав и характеристику образующихся фаз, их соотношение, размер, форму и взаимное расположение структурных элементов, изменение массы и объема тела. Тем самым эти процессы определяют весь комплекс физических, механических и химических свойств, а также получение изделий заданных размеров и форм.
Для предельно точной работы, камерные печи оснащены закалочными секциями, микропроцессорными регуляторами и программаторами.
Виды камерных печей можно разбить по:
Камерные или статистические печи состоят из стен, внутри которых расположены лабиринтообразные полости с уплотнениями для термоизоляции. В качестве изолянта используются огнеупорный кирпич и термостойкие плиты, а также из специальных матов и плиток, которые полностью подходят для использования при высоких температурах. Что касается подвесного свода, то он также включает в свой состав огнеупорные плиты в количестве нескольких штук, между которыми расположены прослойки из термостойких матов разной площади и специальными панелями обладающими характеристиками для использования обрабатывающим оборудованием. На внутренних стенках камерной печи располагаются нагреватели, которые обеспечивают, разогрев обрабатываемых изделий и материалов. На одной из боковых стенок расположены специальные вентиляторы, которые обеспечивают вытяжку испарений из продуктов, которые проходят обработку в камерной печи, и вывод этих вредных газов за пределы оборудования. Этот же вентилятор выполняет функцию охлаждения камеры после завершения процесса обработки изделия, так как способен производить отток горячего воздуха, что существенно понижает температуру в камере.
Нарушения температурного режима могут привести к несоответствию механических свойств изделий, заявленных изготовителем, что, в свою очередь, может повлечь аварии на производстве. Использование автоматизированных систем управления при термической обработке повышает качество продукции и облегчает труд обслуживающего персонала.
Целью автоматизации высокотемпературной камерной электропечи является поддержание постоянной температуры, так как это влияет напрямую на качество изделия и минимизирует фактор человеческого труда или полностью устраняет его участие в процессе поддержания температуры.
1. Актуальность темы
Актуальность темы состоит из большого спектра назначения. Основные назначение камерной печи – равномерный нагрев заготовок из различных материалов. Это необходимо для дальнейшей обработки образцов (ковки и проката, обжига и прочей термообработки). Оборудование состоит из кожуха теплоизоляции с нагревателями и дверцы, закрывающей загрузочный проем. Камерная печь используется в различных отраслях промышленности. Техника может иметь разнообразные конструктивные особенности.
Автоматизируя камерную печь, нужно учитывать много факторов, что и является сложностью:
2. Цель и задачи исследования, планируемые результаты
Обоснование направления автоматизации высокотемпературной камерной электрической печи.
Высокотемпературная камерная электропечь широко распространена на металлургических заводах. В данной печи происходит отжиг металла, для избавления лишних примесей в деталях. Температурный режим печи достаточно сложный и производится по технологическим заданиям и температурной карте. Точное управление температурной вручную очень сложное и не точное, человеческий фактор играет свою роль, недосмотрев за температурой будет происходить брак деталей. Так же постоянное включение и выключение печей будет приводить к износу деталей печи. Для того чтобы не было брака и лишних финансовых затрат мы должны разработать систему автоматизации. Поскольку главным фактором играет температурный режим, то для его регулирования можно выбрать контроллер ПЛК-154 который выполняет такие задания:
Рисунок – 2.1 Высокотемпературная камерная печь
3. Анализ высокотемпературной камерной печи как объекта автоматизации.
Камерные печи периодического действия являются самой простой и универсальной конструкцией термических печей. Их применяют при единичном и серийном производстве, когда приходится нагревать детали, разнообразные по форме, размерам, марке стали и режимам термической обработки. Температура в камерной печи постоянна, но может меняться во времени при нагреве и охлаждении деталей, посадке новой партии и т. п. Конструкции камерных печей рассматриваются согласно принятой классификации по способу загрузки деталей и устройству рабочей камеры. Для термической обработки деталей широко применяют электрические камерные печи.
Принцип действия электропечи следующий. При достижении в рабочем пространстве электропечи заданной температуры нагреватели отключаются, затем открывается заслонка. Изделия загружаются в электропечь, после чего закрывается заслонка. Включаются нагреватели, и происходит термообработка садки по технологическому режиму. По окончании термообработки нагреватели отключаются, заслонка открывается, садка выгружается из электропечи, цикл повторяется. Конструкция механизма подъема заслонки обеспечивает открытие загрузочного проема и надежный прижим заслонки к кожуху электропечи.
Задача управления процессом нагрева в камерных печах периодического действия заключается в обеспечении режима работы, необходимого для получения металла заданной температуры, равномерно прогретого по сечению, и проведения соответствующей термообработки
Измерение и регулирование температуры производится автоматически терморегулятором.

Рисунок 3.2 – График режима отжига быстрорежущей стали Р6М5.
Термическая программа - это желаемая зависимость температуры объекта от времени. Часть программы, имеющая постоянную скорость изменения температуры, называется участком. Каждый участок характеризуется двумя параметрами - конечной температурой и временем. На рисунке 3.1 изображено три участка: 1 - нагрев, 2 - выдержка, 3 - охлаждение. Регулятор выполняет программу последовательно, участок за участком, пока не обнаружит участок конец программы, после чего прекращает выполнение программы и переходит в дежурный режим. В дежурном режиме термическая программа не выполняется основные идополнительные выходы разомкнуты, тока в нагрузке нет. Здесь можно контролировать температуру объекта и вводить необходимые параметры, а при автоматическом режиме изменение заданных параметров невозможно.
При смене участка, обрыве термопары и перегреве печи программный регулятор вырабатывает звуковые сигналы. Аварийную температуру, при которой происходит срабатывание аварийного выхода и переход регулятора в дежурный режим обычно устанавливают на 20...50 .С больше максимальной температуры термической программы, но не больше предельно-допустимой температуры для данного объекта. Регулятор в автоматическом режиме работы при пропадании сетевого напряжения сохраняет в памяти текущие параметры процесса и после появления питания продолжает выполнение термической программы с прерванного места.
4. Критический обзор известных технических решений по автоматизации высокотемпературной камерной печи.
Использование АСУ при термической обработке повышает качество продукции и облегчает труд обслуживающего персонала. Современное оборудование и новые методы автоматического управления позволяют снизить затраты на ремонт и обслуживание оборудования, получить экономический эффект от рационального использования энергоресурсов вследствие оптимального управления технологическим процессом. Рассмотрим два проектных решения модернизации системы управления электропечами с учетом таких технологических потребностей, как точное регулирование температуры, возможности быстрой смены режимов при обработке различных видов изделий.
Системы регулирования температуры в электропечах на основе ОВЕН.

Рисунок 4.3 – Преобразователь интерфейса ОВЕН.
В качестве регулирующего устройства в системе управления электропечью используется двухканальный программный ПИД-регулятор ОВЕН ТРМ151, два канала которого регулируют температуру на нагревательных элементах. Исполнительным устройством служит блок управления симисторами и тиристорами ОВЕН БУСТ, который обеспечивает точность автоматической регулировки мощности на нагревательных элементах печи методом фазового управления. Для расширения входов и получения дополнительной возможности измерения температуры в самом изделии или в муфеле печи применяется модуль ввода ОВЕН МВА8. Обмен данными между регуляторами и модулем аналогового ввода осуществляется при помощи компьютера, для согласования интерфейсов RS-485/RS-232 используется преобразователь интерфейса ОВЕН АС3-М.
Разработанная система позволяет выполнять режим отжига любой степени сложности. Программы технолога создаются на компьютере верхнего уровня и заносятся в каждый прибор ТРМ151.
Для более сложных систем с управлением тремя и более нагревательными зонами, а также работой вентиляторов и других исполнительных механизмов наиболее приемлемой станет система с управляющим устройством в виде программируемого логического контроллера, например, ОВЕН ПЛК. Примером такого типа установок может служить самый распространённый в промышленности тип печей – камерная электрическая печь сопротивления, либо колпаковая электропечь. В этих печах, в зависимости от конструкции, могут быть три зоны нагрева. Для оптимального регулирования температуры в них необходимо иметь три независимых контура управления. Система регулирует температуру в каждой зоне нагрева: в первой, во второй и в третьей зонах используя, соответственно, первый, второй и третий каналы регулирования. Все контуры подчиняются главному контуру управления температуры в муфеле. Контуры подчинённого регулирования идентичны и состоят из регулятора температуры, программно реализованного в контроллере (ОВЕН ПЛК154), исполнительного устройства (ОВЕН БУСТ и симисторов) и объекта управления (нагревательных элементов). Регулятор главного контура регулирования так же как и регуляторы подчинённых контуров, программно реализован в контроллере ПЛК154.
Данные с каждого канала поступают сначала на контроллер, а затем на компьютер, где обрабатываются и хранятся при помощи SCADA-системы, приспособленной для работы с данным технологическим процессом и выбранным контроллером. В разработанной системе помимо автоматического регулирования температуры возможно регулирование с помощью резисторов ручного управления. Ручное управление используется во время наладки или аварийной ситуации.
Основными управляющими и контролирующими элементами СУ камерной печи являются:
Отличительной особенностью проекта с использованием ПЛК является возможность визуализации на компьютере процесса регулирования температуры в выбранной электропечи.
5. Разработка алгоритма работы и схемных решений устройства автоматического управления высокотемпературной камерной печи.
Термическая обработка – это обработка материалов, связанная с их охлаждением или нагреванием и направленная на изменение свойств материалов. Термической и термоциклической обработке подвергаются металлы и сплавы, а также неметаллические материалы для улучшения кристаллической структуры, например, для получения мелкозернистой структуры материала основы биметаллических композиций, получаемых методом совместного нагрева, или для увеличения прочности адгезионной связи слоев биметалла В данной статье рассматривается автоматизированный технологический процесс термической обработки керамических изделий в камерной печи, целью которого является удаление вредных примесей, изменение химических и физических свойств материала или придание изделию необходимых качеств (механической прочности, химической стойкости, жаростойкости, огнеупорности и др.). Металлокерамические композиции используются, например, в авиастроении, где требуется соблюдение высокой точности технологического режима при изготовлении изделия.
Технологический процесс термической обработки керамических стержней состоит из последовательности шагов нагрева, охлаждения или выдержки. Для успешного завершения процесса обработки изделия необходимо в течение продолжительного (5-6 ч.) времени контролировать текущую температуру нагревательного устройства (в данном случае камерной печи), переключение режимов работы устройства. Для повышения уровня контроля качества изделий рекомендуется использовать систему сбора и учета данных для анализа производственного цикла каждого из изделий. С этой целью в производственную структуру внедряется полная АСУ ТП со всеми необходимыми компонентами. Термообработка заготовки изделия производится по определенному алгоритму. Этот алгоритм представляет из себя последовательность шагов нагрева (увеличение температуры в печи),охлаждения (уменьшение температуры) или выдержки (удержание определенного значения температуры в течение заданного времени). У каждого из шагов есть соответствующие ему параметры: скорость нагрева, температура при завершении шага (то есть, температура, до которой нужно нагреть или охладить изделие на данном этапе алгоритма).
Алгоритм работы печи состоит в том, что обрабатываемая деталь выкладывается на под, открывается дверь, затем под перемещается внутрь печи. После окончания термообработки действия повторяются в обратном порядке, после чего полный цикл обработки закончен. Управление нагревом осуществляется за счет программного регулятора. В системе используется импульсное управление – программа контроллера выдает ширину управляемого импульса, то есть мощность, с которой печь должна нагреваться (или охлаждаться).
ПЛК в свою очередь для получения условного значения мощности на своем выходе оперирует 2-мя значениями температуры: текущей (получаемой с термопары, установленной внутри печи) и желаемой (той, которая должна быть в печи по алгоритму термообработки). Для того, чтобы получать необходимую ширину импульса, удобно применять ПИД-регулирование. Таким образом, ПЛК, осуществляющий управление, должен поддерживать возможность такого вида регулирования.
Реализуемую систему управления с точки зрения архитектуры программы можно представить в виде конечных автоматов. Система может принимать определенное количество состояний, переход между которыми происходит за счет обработки системой возникающих в ней событий.
Начальное состояние - состояние, в котором находится ПЛК при старте: при этом осуществляется первоначальная настройка (инициализация), загрузка данных из памяти, сброс входов. Ожидание – состояние, в котором находится ПЛК, когда ожидает команды для перехода в другие состояния. Выполнение – исполнение программного кода, запускающего выполнение конкретной выбранной последовательности. Редактирование последовательности – состояние, когда осуществляется редактирование, удаление или добавление новой последовательности в память для последующего выполнения. В виде конечного автомата реализована также и логика состояния «Выполнение», где имеется еще 3 состояния: нагрев, охлаждение и выдержка. Для реализации автоматизированной системы для контроля данным технологическим процессом предлагается контроллер российской компании «ОВЕН», предназначенный для построения систем автоматизации низкой и средней степени сложности.
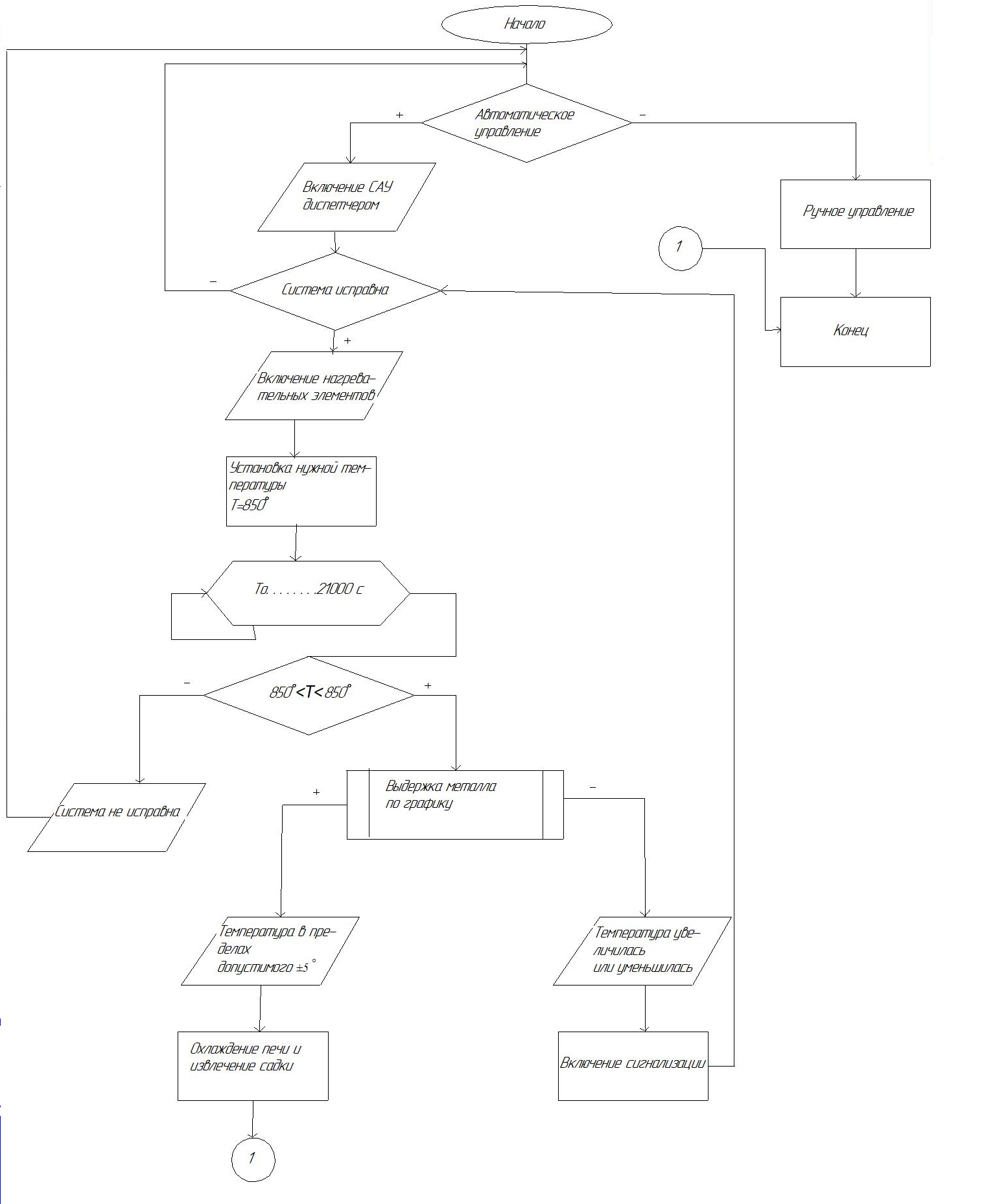
Рисунок 5.3 – Алгоритм управления тепловым режимом
В автоматических процессах (объектах) достаточно часто необходимо изменять или поддерживать постоянными какие-либо физические величины, называемыми регулируемыми переменными, в данном случае поддержание температуры.
Для этого используют автоматические регуляторы или управляющие устройства (УУ) различной сложности.
Автоматический регулятор и УУ на основании измерения регулируемых переменных и задающих воздействий формирует управляющее воздействие на объект регулирования.
На рисунке 5.4 приведена структурная схема управления электропечи для отжига заготовок с регулируемой величиной y(t) - температурой. Данная система предназначена для подержания необходимого режима, т.е. изменения температуры y(t) в электропечи по заданному закону.
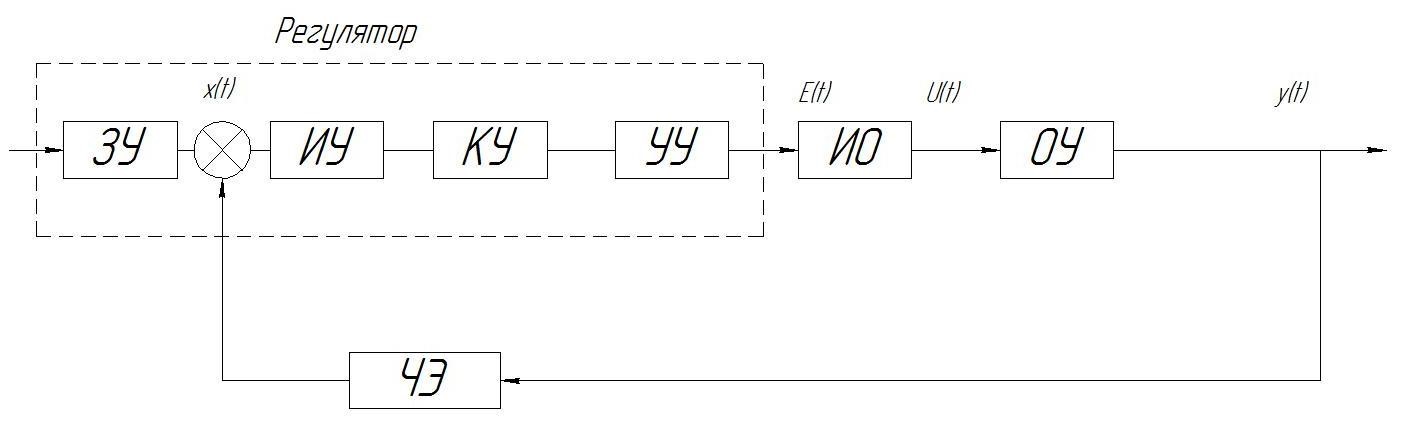
Рисунок – 5.4 Структурная схема управления.
Схема состоит из объекта управления и устройства управления. Объект управления (ОУ) - это основной элемент системы, то есть электропечь, заданный режим работы которых должен поддерживаться устройством управления (программным терморегулятором) при помощи управляющих (регулирующих) органов. Под управляющим подразумевается устройство, обеспечивающие процесс управления, т.е. целенаправленное действие, приводящие к желаемому изменению управляемой переменной(температурой нагрева, выдержки, охлаждения). Для уменьшения ошибки регулирования в систему вводят обратную связь. Задающие устройство (ЗУ) оказывает управляющее воздействие Uз(t) на вход системы, формируя программу изменения регулируемой величины. ЗУ подает сигнал исполнительному механизму (ИМ) - трансформатору, который непосредственно является корректирующим звеном системы. Управляющие воздействие корректируется в зависимости от выходной величины y(t).чувствительный элемент (ЧЭ) преобразует управляемую величину в пропорциональную ей и удобную для использования в САУ. В качестве данного элемента используется термопара , на выходе которой формируется напряжение, пропорциональное температуре в печи. Затем этот сигнал подается измерительное устройство. Выявления соответствий требуемого и полученного значения выполняет сравнивающие устройство. Если значение y(t) отклоняется от заданного, то происходит корректировка сигнала через усилительное устройство (УсУ) и корректирующее устройство. Сигнал об изменении температуры подается термопарой на терморегулирующее устройство ПЛК-154, где в задающем устройстве происходит сравнение, с заданной оператором температурой, и выдается команда на включение или выключение нагрузки.
Выводы
Был проанализирован технологический процесс обжига деталей в высокотемпературной камерной печи как объекта автоматизации и сформированы требования к системе управления. Для её безаварийной работы требуется постоянный контроль таких параметров, как температура внутрикамерного пространства. В результате был • Обоснован выбор оптимального универсального легкого в применении современного устройства управления, в соответствии с выходными сигналами датчиков температуры, а также выбор вспомогательных элементов управления. Алгоритм позволяет производить автоматический непрерывный контроль температуры внутри печи, и автоматически отключать электроэнергию при аварийном повышении температуры.
При написании данного реферата магистерская работа еще не завершена. Окончательное завершение: май 2023 года. Полный текст работы и материалы по теме могут быть получены у автора или его руководителя после указанной даты.
Список источников
- Campos I.B., Aguirrezabala N.N.,Valdes L.D. Ezenarro B.E., Arantzamendi H.G. Energy efficiency and line productivity improvements for a continuous heat treatment process. – Industrial Summer Study on Industrial Efficiency: Leading the Low-Carbon Transition, Kalkscheune, Berlin, Germany, 2018. P. 431 – 441.
- Гринчук П.С., Торопов В.В. Ознобишин А.Н., Кияшко М.В., Дмитриев С.И., Замедленное остывания металла в современных энергоэффективных печах // Известия национальной академии наук Беларуси. Серия физико-технических наук. –2013. – №1. – С. 82 – 88.
- Гурьев А. М., Иванов С. Г., Гурьев М. А., Бердыченко А. А., Черных Е. В. Влияние режимов термической обработки на структуру и физико-механические свойства быстрорежущей стали // Фундаментальные проблемы современного материаловедения.– 2018.– №1.– С. 103– 108.
- Ишимбаев А.В., Матюхин В.И. Совершенствование конструкции камерной нагревательной печи с изменяющейся рабочей температурой // Теплотехника и информатика в образовании, науке и производстве: сб. науч. тр. Екатеринбург, 2021. – С. 62 –64.
- Кабишов С.М., Ратников П.Э., Трусова И.А., Менделеев Д.В. Оценка влияния конструкции футеровки на величину тепловых потерь при работе камерной печи // Литье и Металлургия. –2015. – №4(81). – С. 108 – 115.
- Панферов В.И., Панферов С.В. К решению задачи об управляемости нагрева металла в промышленных печах // Вестник Южно-Уральского государственного университета. Серия: Металлургия. –2019. – №2. – С. 79 – 85.
- Панферов В.И., Панферов С.В. К решению задачи об управляемости нагрева металла в промышленных печах // Вестник Южно-Уральского государственного университета. Серия: Металлургия. –2019. – №2. – С. 79 – 85.
- Погребисский М.Я., Усачев Р.А. Выбор схемы размещения нагревателей в камерной печи сопротивления на температуру 1200-1250°С // Электромеханика, электротехнологии, электротехнические материалы и компоненты. – Алушта, 2016. – С. 236 –237.
- Скоробогатова И. В. Синтез системы автоматического управления энергосберегающими режимами камерной печи // Сборник научных работ Донецкого института железного транспорта. –2014. – №37. – С. 53 – 59.
- Н. В. Пасечник, Энциклопедия. Т.4-5 Машины и агрегаты металлургического производства / Н. В. Пасечник В. М. Синицкий, В. Г. Дрозд и др. — Под общ. ред. В. М. Синицкого, Н. В. Пасечника. — М.: Машиностроение, 2000. — 912 с.
- Слащев М.Н. Автоматизированная система управления тепловым режимом камерной печи для термообработки металлопроката // Конкурс научно-исследовательских работ студентов Волгоградского государственного технического университета. –2020. С. 41.