Реферат по темі випускної роботи
Зміст
- Введення
- 1. Актуальність теми
- 2. Мета і завдання дослідження, плановані результати
- 3. Огляд досліджень та розробок
- 3.1 Технологічний процес виробництва теплоносія теплоенергоцентралі металургійного заводу як об'єкта автоматизації
- 3.2 Огляд відомих технічних рішень по автоматизації котельних установок
- 3.3 Структурна схема розробленої системи автоматизації
- Висновок
- Список джерел
Введення
Сучасна котельня установка є складною спорудою, що включає в себе різне обладнання, пов'язане в єдине ціле загальною технологічною схемою, основним елементом якої є котельний агрегат. Саме котельний агрегат призначений для виробництва необхідної кількості кінцевого продукту пари або гарячої води із заданими споживачем показниками якості.
Джерелом енергії для котельних установок різного призначення є природні і штучні палива в твердому, рідкому і газоподібному станах, теплота вихідних газів технологічних установок, теплота екзотермічних перетворень, що виділяється в окремих технологічних процесах і т. п. В даній роботі розглядається паровий барабанний котел, оснащений газовою топкою. Ефективність роботи топок всіх типів в першу чергу визначається ефективністю процесу горіння. Ефективність процесу горіння, в свою чергу, забезпечується шляхом підтримки на необхідному рівні відносини «паливо-повітря». Тим самим зумовлюється та першорядна роль, яку грають в системі управління топковим пристроєм системи автоматичного регулювання подачі палива і тиску дуттьового повітря.
До однієї з істотних проблем енергетики Донецького металургійного заводу відноситься недостатньо ефективне використання попутного палива (доменного газу), одержуваного при виробництві чавуну в доменних печах. Нерівномірність ходу металургійних процесів обумовлена нестабільністю режиму виробництва і споживання доменного газу, що призводить до значних коливань тиску в газопроводах, до збільшення прямих втрат через скидні свічки, погіршення режимів роботи основних металургійних агрегатів: нагрівальних колодязів, печей прокатних станів і т. д.
Основним споживачем доменного палива є котли ТЕЦ-ПВС, в більшості випадків вони не в змозі забезпечити його повне споживання і стабілізацію тиску в магістральних газопроводах. Одна з основних причин - недостатній рівень автоматизації засобів з управління подачі палива в топку котла. Для вирішення даної проблеми необхідно забезпечити своєчасне інформування про калорійності і тиску доменного газу перед подачею його в топку. Для підтримки на необхідному рівні відносини "паливо-повітря" необхідно вимірювати кількість кисню в газах, що відходять, для чого використовується стаціонарний газоаналізатор. До цього слід додати, що ефективність роботи котлоагрегату в цілому визначається показниками якості кінцевого продукту, яким в даному випадку є пар.
Тепловіддача топки є керуючим впливом для системи парогенерації. Отже, для підтримки тиску пари на заданому рівні необхідно відповідним чином коригувати уставки регулятора подачі палива. На необхідність такого зв'язку вказується в багатьох літературних джерелах. Однак в силу особливостей виготовлення і монтажу котлоагрегату такого зв'язку практично ніде немає. Кожна із зазначених систем управління функціонує самостійно, реагуючи тільки на зовнішні і внутрішні фактори. Зв'язок же між ними здійснюється тільки через процес нагріву, причому односторонньо – від топки до барабану. Зрозуміло, що це призводить до істотного зниження ефективності основних технологічних параметрів парогенеруючої системи [1].
З урахуванням сказаного, метою даної роботи є забезпечення ефективності, надійності і безпеки роботи парового котлоагрегату шляхом автоматичного регулювання основних технологічних параметрів газового топкового пристрою це призведе до збільшення реальної продуктивності ТЕЦ при одночасному зниженні собівартості пари, що відпускається, електроенергії і тепла, так як автоматизована система може функціонувати безперервно в режимі реального часу забезпечує ефективність процесу горіння і враховує режими роботи і динамічні властивості парогенеруючої горіння системи у вигляді відповідних коригувальних зв'язків.
1. Актуальність теми
Підвищення ефективності використання вторинних енергоресурсів може бути досягнуто шляхом вдосконалення експлуатується основного і допоміжного обладнання теплоелектростанції (ТЕЦ-ПВС), їх теплових і пускових схем, автоматизованих систем технологічних процесів (АСУ ТП) і технології експлуатації, а також впровадженням нового заміщає обладнання. Техніко-економічні показники ТЕЦ-ПВС залежать від характеристик основного обладнання та виду палива, що спалюється, особливо при спалюванні різних вугілля, а також від технологічної схеми відпуску тепла. Найважливіше значення при цьому має ефективність котлів і теплофікаційних паротурбінних установок. Тому розробки, спрямовані на підвищення ефективності технології використання вторинних енергоресурсів таких як (доменний газ), одержуваного при виробництві чавуну в доменних печах є актуальними. Особливо це важливо для проведення реконструкції та технічного переозброєння АСУТП ТЕЦ-ПВС, обладнання яких вичерпало ресурс.
До основних елементів котельні відносяться:
Котел – це теплообмінний пристрій, в якому теплота від гарячих продуктів згоряння палива передається воді. В результаті цього у парових котлах вода перетворюється в пар, а в водогрійних котлах нагрівається до необхідної температури. Топковий пристрій служить для спалювання палива і перетворення його хімічної енергії в теплоту нагрітих газів. Живильні пристрої (насоси, інжектори) призначені для подачі води в котел. Без перерахованих елементів не може працювати навіть найпростіша котельня установка.
Кдопоміжним елементам котельні відносять:
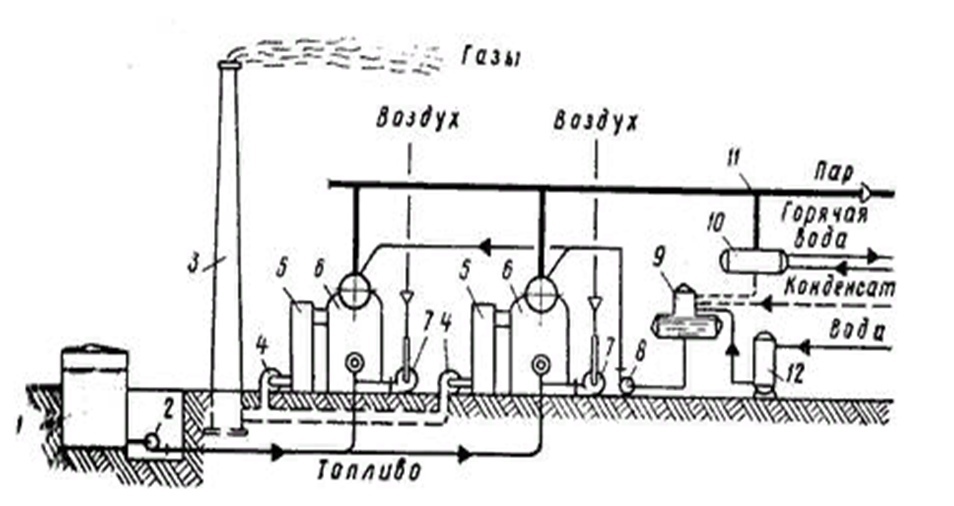
Малюнок 1-Схема котельні установки: 1-паливосховище; 2-паливний насос; 3-димова труба; 4-димососи; 5-водяні економайзери; 6-парові котли; 7-дуттьові вентилятори; 8-живильні насоси; 9-деаератор; 10-водопідігрівач; 11-паропровід; 12-водопідготовча установок.
2. Мета і завдання дослідження, плановані результати
Виробництво тепла завжди є дуже важливою проблемою сучасного життя, а модернізація і поліпшення цього процесу завжди актуальні. На даний момент котельні установоки гостро потребують модернізації, оскільки вони практично не автоматизовані і більшістю процесів управляє людина вручну, допускати помилку. Як правило, на багатьох котелень, більшість систем регулювання параметрів котла все ще працюють в ручному режимі, що призводить до серйозних екологічних забруднень і неефективному використанню палива в режимах надлишку або нестачі повітря для горіння.
Метою даної роботи є аналіз технологічних параметрів газового топкового пристрою для подальшої його автоматизації яка забезпечити своєчасне інформування про калорійність і тиск доменного газу перед подачею його в топку. Повноцінне рішення задачі ефективного сжиганиякоксодоменной суміші на котлах шляхом створення всережимних регуляторів стало можливим тільки з масовим поширенням високонадійних програмованих логічних контролерів.
Основные задачи исследования:
- аналіз котельня установки як об'єкта автоматизації;
- аналіз існуючих розробок по автоматизації виробництва теплоносія теплоенергоцентралі;
- розробка математичної моделі виробництво теплоносія теплоенергоцентралі металургійного заводу;
- Розробка схемних рішень. Структурна, функціональна схема пристрою автоматизації, алгоритм роботи;
- практична реалізація системи автоматизованого управління котельня установки. Розробка мнемосхеми управління виробництвом теплоносія теплоенергоцентралі металургійного заводу;
- Розробка заходів щодо безпечної та безаварійної експлуатації розробленого пристрою.
Об'єкт дослідження: котельня установка.
Предмет дослідження : автоматична система управління виробництвом теплоносія теплоенергоцентралі металургійного заводу.
3. Огляд досліджень та розробок
3.1 Технологічний процес виробництва теплоносія теплоенергоцентралі металургійного заводу як об'єкта автоматизації
Об'єктом автоматизації є котел типу БГ 3-75-39фб-однобарабанний, П-подібної компоновки, вертикально-водотрубний, з природною циркуляцією. Котел складається з: топкової камери і пальникових пристроїв, пароперегрівача, водяного економайзера, трубчастого воздухоподогревателя. Технологічна схема пристрої та роботи котельні на базі котла типу ПК 3-75-39фб наведена на малюнку 2.
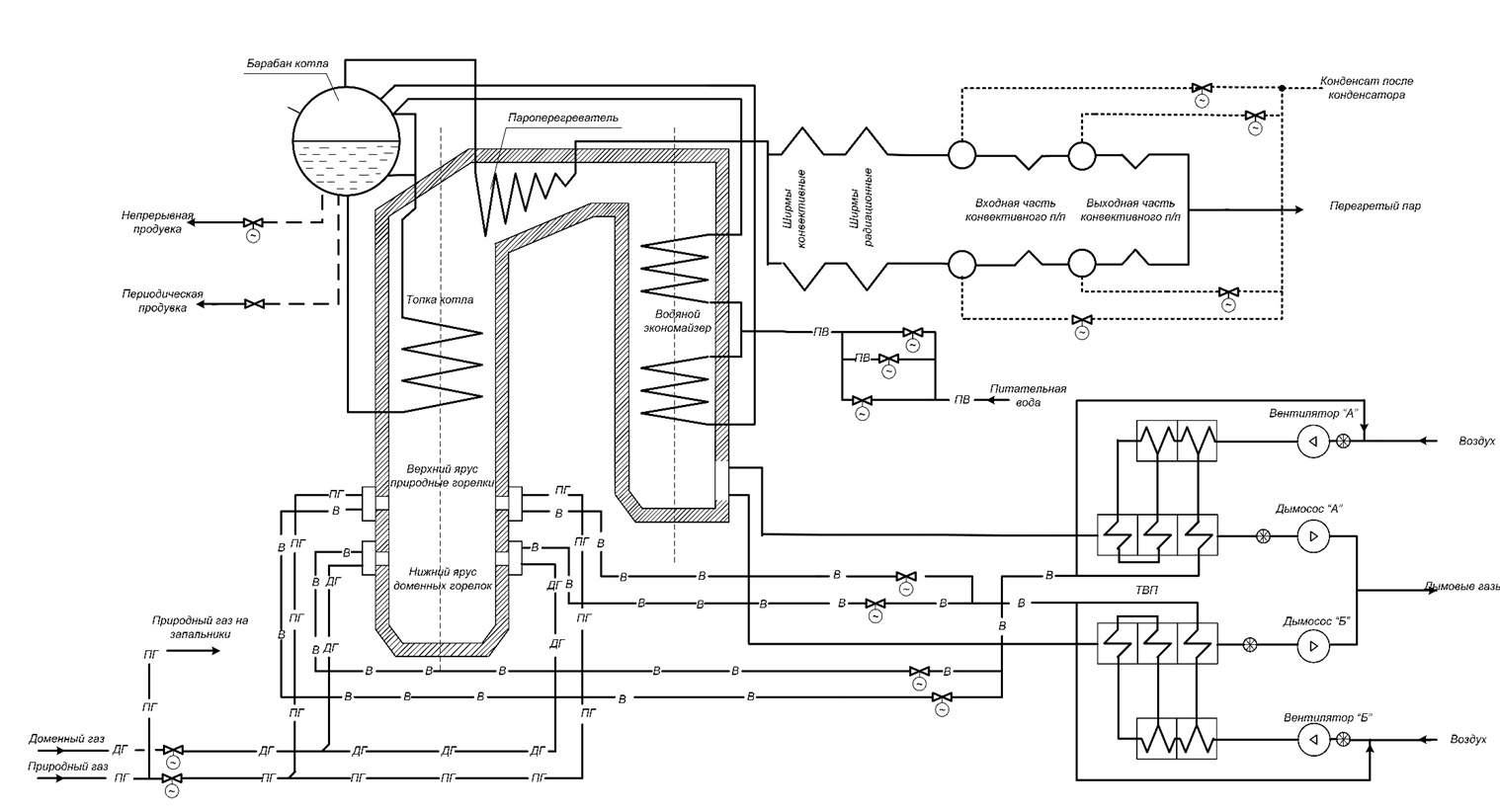
Малюнок 2 – Технологічна схема пристрою і роботи котла типу БК3-75-39ФБ
Обсяг топкової камери - 454 м3, стіни топки повністю екрановані трубами діаметром (60x3) мм, виконані зі сталі Ст. 20. Екранні поверхні нагріву розбиті на 12 самостійних циркуляційних контурів по числу монтажних блоків.
Кількість труб:
В якості палива використовується природний, а також доменний газ - штучний вид палива, одержуваний як побічний продукт при виробництві чавуну. В якості теплоносія виступає пар. Основними цехами, тісно пов'язаними за технологією, є котельно-турбінний і хімічної водоочищення. Для отримання пара нормальної якості в котлі застосована схема триступеневого випаровування. Перший ступінь випаровування (чистий відсік) і другий ступінь (сольові відсіки) розташовані безпосередньо в барабані котла. Виносні циклони є третім ступенем випаровування.
В першу ступінь випаровування включена центральна частина барабана котла з блоками фронтового, заднього і переднього блоків бічних екранів. У другу сходинку виділені торцеві частини барабана, відокремлені від центральної частини перегородками. У циркуляційний контур другого ступеня включені середні блоки бічних екранів. У третю сходинку випаровування включені виносні циклони діаметром (377x18) мм, а в циркуляційний контур третього ступеня включені задні блоки бічних екранів. Харчування виносних циклонів здійснюється необогреваемыми трубами діаметром (83x3, 5) мм з сольових відсіків барабана. Сепараційні пристрої першого ступеня випаровування складаються з утопленого перфорованого пароприймального стеля. [4]
У другому ступені випаровування встановлені (в кожному торці барабана) по два всередині барабанних циклону і пароперепускні короби, що змінюють напрямок рухи пара. У третьому ступені випаровування елементами сепарації є: сама равлик виносного циклону і перфорований паропріемний стелю.
Живильна вода з водяного економайзера надходить в барабан котла по 10 трубах діаметром (60x3) мм і через роздатковий короб направляється на промивні (дірчасті) щити, протікає по ним і зливається в водяний Обсяг барабана. Середній робочий рівень води в чистому відсіку на 50 мм нижче осі барабана. У сольові відсіки Котлова вода надходить з чистого відсіку через труби, змонтовані в нижніх частинах перегородок. Пароводяна суміш з вихідних колекторів третього ступеня випаровування надходить в равлики виносних циклонів,а отсепарированный пар з виносних циклонів по трубах діаметром (83x3, 5) мм надходить у відповідний сольовий відсік барабана.
Пароводяна суміш з екранних контурів другого ступеня надходить всередину барабанних циклонів, встановлені в сольових відсіках. Вода, отсепарированная в циклонах, зливається в водяний обсяг сольового відсіку, а пар проходить через жалюзійні сепаратори, розташовані над циклонами, змішується з парою третього ступеня і по коробах направляється в паровий простір чистого відсіку барабана. Пароводяна суміш з екранної системи першого ступеня надходить під дірчасті листи, занурені у воду на 50 мм нижче нижчого рівня води в барабані. Пара проходить через них, змішується з парою, що надходить з соєвих відсіків, і, пройшовши жалюзійний пакет і пароприймальний дірчастий стелю, направляється в пароперегрівач. Циркуляційна схема котла передбачає глибоке секціонування екранів, що підвищує надійність циркуляції пароводяної суміші в екранах котла.
На котлі встановлений конвективний пароперегрівач, розташований за чотирирядним фестоном в перехідному горизонтальному газоході. Пароперегрівач виконаний двоступеневим, площа поверхні нагріву кожного ступеня - 220 м2. Схема включення пароперегрівача щодо напрямку руху газів, що йдуть - змішана. Пар з барабана по 72 трубах діаметром (38x3) мм проходить першу сходинку пароперегрівача і надходить у вихідний колектор діаметром (273x25) мм. З вихідного колектора першого ступеня пар 10 трубами діаметром (83x5) мм (перехресним потоком по 5 трубах з лівого і правого боку колектора) відводиться в два колектора діаметром (325x25) мм. далі пар по 36 трубах діаметром (38x3) мм проходить другий ступінь пароперегрівача і надходить в проміжний колектор діаметром (273x25) мм. З бічних частин проміжного колектора пар надходить в середню частину і далі по 72 змійовиках діаметром (38x3) мм проходить середню частину другого ступеня пароперегрівача, а потім надходить у вихідний колектор пароперегрівача діаметром (273x25) мм і далі в паропровід.
Водяний економайзер і повітропідігрівач розташовані в опускному газоході в розтин. Водяний економайзер киплячого типу, змійовиковий, двоступеневий, поверхня нагріву першого ступеня 700 м2, другого ступеня - 240 м2. Перший ступінь водяного економайзера складається з 41 змійовика діаметром (32x3) мм зі сталі 20, другий ступінь водяного економайзера складається з 48 змійовиків такого ж діаметру і матеріалу. Після блоку живлення вода трубою діаметром (108x10) мм підводиться до вхідного колектора першого ступеня водяного економайзера. Розрахункова температура живильної води 150 ° С. Пройшовши змійовики першого ступеня, вода з вихідного колектора 6 трубами діаметром (66x3) мм перехресним потоком надходить у вхідний колектор другого ступеня. Пройшовши другий ступінь, живильна вода через два вихідних колектора, розташованих на бічних стінках, 10 трубами діаметром (60x3) мм (по 5 трубах з кожного колектора) відводиться в барабан котла. Всі п'ять колекторів водяного економайзера виконані з труб діаметром (219x16) мм. Повітропідігрівач котла-трубчастий, однопоточний по газах і чотирьохходовий по повітрю, складається із сталевих труб діаметром (40x1,5) мм поверхня нагріву першої (холодної) ступені - 2600 м2, другий (гарячої) ступені - 1600 м2
Тягодуттєва установка котла складається з одного дуттєвого вентилятора типу ВД-18 і одного димососа типу Д 20x2. Повітря з температурою від 30 °C до 50 оС всмоктується вентилятором з приміщення котельні і, пройшовши через повітропідігрівач, по повітропроводах подається до газових пальників. Димові гази відсмоктуються димососом і викидаються в димову трубу. Опір котлоагрегату по димових газах в залежності від виду палива становить від 116 до 148 мм вод. ст. Повітряний опір від 73 до 87 мм вод. ст.
Котел розрахований на роботу з врівноваженою тягою (подача повітря на горіння здійснюється дуттьовим вентилятором, а видалення продуктів згоряння - димососом). Регулювання подачі і напору димососа і вентилятора здійснюється направляючими апаратами, встановленими на стороні всмоктування.
Основним параметром, що відповідає за управління виробництвом теплоносія в теплоенергоцентралі металургійного заводу, який можна автоматизувати - є регулювання подачі палива в топку котла. У топці котла спалюється спільно або окремо доменний і природний газ. Для спалювання цих палив топка котла обладнана двома плоско факельними пальниками, пальник складається з двох газоповітряних сопел, нахилених під кутом 60° один до одного. Верхнє сопло складається з співвісно розташованих коробів прямокутного перерізу для доменного газу і повітря. Доменний газ подається по центральному коробу, внутрішні розміри якого дорівнюють (0, 39x0, 74) м.по зовнішньому коробу верхнього газоповітряного сопла надходить гаряче повітря для горіння. Розміри останнього (0,6x0,9) м. Нижнє газоповітряної сопло являє собою пальник природного газу і складається з повітряного короба розміром (0,5x0,5 м, всередині якого розташовані у два ряди по вертикалі десять газораздающих труб діаметром (42x3) мм. Між верхнім і нижнім газовоздушні соплами встановлюється труба для зашитно-запального пристрою і труба для датчика основного смолоскипа. Технічна характеристика комбінованої плоскофакельного пальника наведена нижче:
Продуктивність пальника по:
Опір пальника по:
Максимальний опір по повітрю:
Принцип дії плоскофакельного пальника заснований на використанні ефекту зіткнення двох струменів повітря, спрямованих під кутом один до одного. Між цими потоками утворюється "трикутник", в який з бічних сторін ежектіруются розпечені продукти згоряння, що здійснюють прогрів і запалювання палива. Зіткнення двох потоків призводить до утворення плоского струменя, що має велику ступінь турбулізації і сильно розвинену поверхню, що сприяє інтенсивному згорянню палива в обсязі топки. При роботі на доменному газі газоповітряний імпульс верхнього сопла могутніше імпульсу нижнього сопла. Тому факел зміщується до поду топки. Теплосприйняття нижньої частини топки збільшується, що призводить до зниження температури газів на виході з топки. Це дозволяє підвищити продуктивність котла на доменному газі.
При роботі котла на висококалорійному природному газі, газоповітряний імпульс нижнього сопла вище, ніж верхнього. Факел зміщується вгору, температура газів на виході з топки підвищується і збільшується температура перегрітої пари. При роботі на суміші палив факел в топці займає проміжне положення. Таким чином, забезпечується саморегулювання температури перегрітої пари. Характеристика спалюваних палив. Доменний газ-штучний вид палива, одержуваний як побічний продукт при виробництві чавуну. Середній склад доменного газу:
- вуглекислий газ СО2 - 16,2 %;
- метан CH, - 0,2 %;
- кисень O2, - 0,1 %;
- водень Н2-4,8 %;
- окис вуглецю CO-22,8 %;
- азот N2 - 56,0 %;
- теплота згоряння Q - 772 ккал / м3;
- щільність р - 1,298 кт / м
Визначення вмісту природного газу проводиться за вмістом в ньому метану CH4. Склад природного газу:
- CH4, - 94,565 %;
- Cm Hn, - 2,34 %;
- CO2 - 0,019 %;
- N2 - 3,076 %;
- нижча теплота згоряння-7918 ккал / м3;
- щільність р - 0,70 кг/м3.
Таким чином, пропонована автоматизація системи управління полягає в модернізації існуючої системи управління виробництвом теплоносія за рахунок використання сучасних засобів автоматизації, які в свою чергу замінять застарілу апаратуру. Дана система автоматичного управління виробництвом теплоносія на базі котла типу БК3-75-39фб, з урахуванням специфіки управління, забезпечить зниження споживання природного газу за рахунок, змішаного режимів роботи на двох паливах, в ідеальних умови буде використовуватися тільки доменний газ, що дозволить збільшити продуктивності агрегату, при цьому зросте економічність у використанні природного газу.
3.2 Огляд відомих технічних рішень по автоматизації котельних установок
В якості існуючої системи автоматизації приведена система управління котлом БКЗ-75-39гма виконана на базі програмованого контролера c200hg фірми «OMRON». Паровий котел є об'єктом підвищеної небезпеки з точки зору безпеки роботи виробничого обладнання. Функціонування котла характеризується інформацією, що надходить від аналогових і дискретних датчиків стану теплотехнічних параметрів, датчиків положення їм і датчиків стану (включено/відключено) електродвигунів. Оперативне управління котлом проводиться з промислового терміналу NT620C. в якості модуля управління застосовується промисловий термінал NT620C.Термінал NT620C має широкі можливості.
Застосування такого терміналу дозволить:
- відображати стан обладнання та системи управління;
- вводити необхідну інформацію;
- відображати у вигляді мнемосхем хід технологічного процесу;
- здійснювати Ручне управління обладнанням і контурів контролю;
- відмовитися від великого числа сигнальних ламп і кнопок управління.
В основу побудови уніфікованої системи управління покладено принцип конфігурації систем з типових модулів і блоків, що дозволяють вирішувати все різноманіття завдань контролю і управління технологічними процесами. Всі модулі пов'язані між собою високошвидкісною мережею і можуть складати будь-яку конфігурацію.
- здійснює обмін командами і даними з модулем управління;
- здійснює включення і виключення дискретних виходів;
- можливість безперервного контролю достовірності всієї або певного класу вхідної інформації з сигналізацією і реєстрацією несправності окремих датчиків або каналів зв'язку;
- можливість реструктуризації алгоритмів при виявленні несправності;
- можливість контролю виконання команд за фактом і в часі;
- самодіагностика технічних засобів з сигналізацією і реєстрацією відмов на рівні типового елемента заміни;
- Можливість санкціонованого контролю стану будь-якого датчика або алгоритму;
- спрощення процедури внесення оперативних та неоперативних змін при санкціонованому доступі до таких змін з одночасною автоматичною реєстрацією факту доступу та внесених змін;
- можливість фіксації часу виникнення всіх реєстрованих подій;
- автоматична підготовка звітної документації;
- спрощення процедури випробування захистів;
- більш висока ремонтопридатність технічних засобів;
- значне зменшення габаритних розмірів технічних засобів, що реалізують підсистему, при розширенні виконуваних функцій;
- можливість повного резервування технічних засобів при мінімальному ускладненні системи.
- Теоретические основы разработки и моделирования систем автоматизации: Учебное пособие / А.М. Афонин, Ю.Н. Царегородцев, А.М. Петрова и др. - М.: Форум: НИЦ ИНФРА-М, 2014. - 192 с.
- Глинков, Г.М. АСУ ТП в черной металлургии: учебник для вузов. / Г.М. Глинков, В.А. Маковский – 2-е изд., перераб. и доп. – М.: «Металлургия», 1999. – 310 с.
- Лысенко, В. Г. Топливо. Рациональное сжигание, управление и технологическое использование: Справочное издание. В 3 книгах / В. Г. Лысенко, Я. М. Щелоков, М. Г.Ладыгичев. – Теплотехник, 2004. – 608 с.
- Гусев Ю. М. Основы проектирования котельных установок / Ю. М. Гусев. – [изд. 2-е, перераб. и доп.] – М.: Стройиздат, 1973. – 248 с.
- Справочник эксплуатационника газовых котельных / [под ред. Е. Б. Столпнера]. – Л.: Недра, 1976. – 608 с.
- Липов Ю. М. Котельные установки и парогенераторы / Ю. М. Липов, Ю. М. Третьяков. – Москва-Ижевск: НИЦ «Регулярная и хаотическая динамика», 2003. – 592 с.
- Официальный сайт Донецкого металлургического завода [Электронный ресурс]: Режим доступ: http://dmz.donetsksteel.com/ru/company
- Официальный сайт компании ОВЕН, ПЛК73 контроллер [Электронный ресурс]: Режим доступ: https://owen.ru/product/plk73
У процесі роботи модуль виконує наступні завдання:
Всі модулі мають розвинену систему самодіагностики. Здійснюється перевірка справності проходження сигналів (перевірка на наявність "1" при наявності вхідного сигналу, перевірка на наявність "0"- при відсутності сигналу), перевірка на відсутність впливу входів один на одного. Модулі мають індикатори справної роботи. Зелений світлодіод інформує про справне функціонування модуля. У разі несправності загоряється червоний світлодіод, і інформація про характер несправності стає доступною модулю управління< / p>
В даному випадку автоматизація процесу управління розрядженням в топці котла виконана за допомогою датчика "Метран-45 дів", контролера фірми "Омрон" С200НG, пускача безконтактного реверсивного ПБР-3А, виконавчого механізму електричного однооборотного МЕВ– 630/25 –0,25–87–р і димососа ДН-18. Технічні характеристики кожного з елементів АСР і виконувані ними функції наведені нижче на малюнку 3.
Датчик тиску – розрядження «Метран – 45 дів» з струмовим уніфікованим сигналом 4 - 20 мА, з межею допустимої основної похибки = 0,5%. Верхня межа вимірювань + 3,15 кПа. Нижня межа вимірювань + 0,03 кПа. Діапазон температур вимірюваного середовища -40 - + 80?С. Ступінь захисту від пилу і води IP65. Вибухозахищеність Ех. Пускач безконтактний Реверсивний ПБР-3а.Завод – виробник р. Челябінськ, «Завод електроніки і механіки». Механізм електричний однооборотний, номінальний крутний момент на вихідному валу 630 Нм, час повного ходу вихідного валу 25 з, повний хід вихідного валу 0,25 обороту, датчик зворотного зв'язку струмовий з сигналом 4 - 20 мА. Комплект з блоком живлення БП-10. Димосос ДН-18, продуктивність 143000 куб.м/год, Напір 236 мм вод. ст., 730 об / хв, Потужність 250кВт.
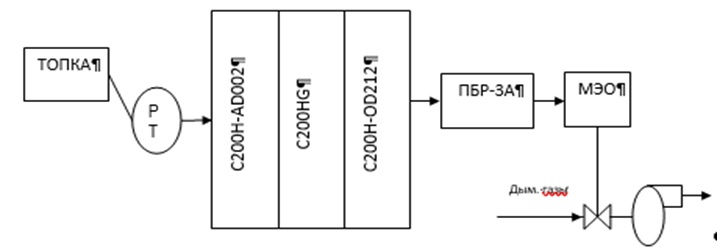
Малюнок 3 – Структурна схема одноконтурної автоматичної системи витрати розрядження в топці котла
Таким чином, дана система автоматизації побудована на базі програмованого контролера c200hg фірми «OMRON» але, у неї є певні недоліки принцип конфігурації системи складається з використання типових модулів і блоків розширення від фірми SYSMAC. У разі виходу з ладу (несправності) блоків входять в єдину систему управління виникають певні складнощі з заміною апаратури так як, в основу побудови уніфікованої системи управління покладено принцип конфігурації систем з типових модулів і блоків. Це призводь до того, що універсальність і взаємозамінність стає неможливою при даному технологічному рішенні. Для будь-якого підприємства простої пов'язані з фінансовими збитками, порушенням термінів здачі готового продукту, втратою іміджу компанії. Позапланові зупинки - це втрачений прибуток заводу.
Альтернативним методом модернізації автоматичної системи управління є взаємозамінність і універсальність використання програмованих контролерів. За базову апаратуру автоматизації приймемо широко застосовуваний в сучасних котельних установка, а саме ПЛК від компанії ОВЕН.
3.3 Структурна схема розробленої системи автоматизації
Для системи автоматичного управління виробництвом теплоносія теплоенергоцентралі металургійного заводу прийнятий програмований логічний контролер ПЛК73 від компанії ОВЕН який, взаємодіючи з датчиками, отримує інформацію від об'єкта управління, обробляє її відповідно до закладеним алгоритмом і видає керуючі впливу на виконавчі пристрої. Застосування мікропроцесорних засобів для реалізації підсистеми технологічних захистів і захисних блокувань дає наступні переваги в порівнянні з традиційними засобами:
Взаємодія з датчиками і виконавчими пристроями визначається відповідними протоколами обміну, що враховують особливості функціонування системи в цілому і вимог програмно-апаратної і схемотехнічної сумісності з іншими пристроями і системами. На структурній схемі зображені всі основні функціональні частини системи (елементи, пристрої і функціональні групи) і основні взаємозв'язки між ними. Графічне побудова схеми на малюнку 4 забезпечує найкраще уявлення про послідовність взаємодії функціональних частин в системі. На лініях взаємозв'язків стрілками позначені напрямок ходу процесів, що відбуваються в пристрої.
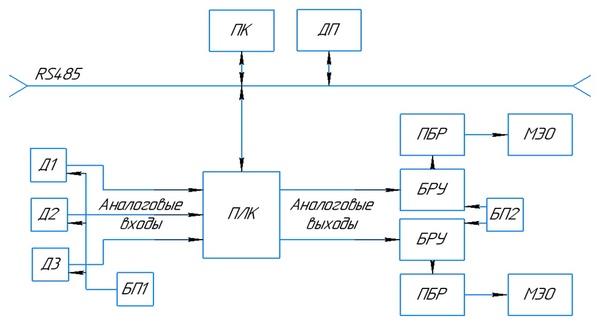
Малюнок 4 - Структурна схема управління виробництвом теплоносія: 1-витрата доменного газу Д1; 2-Тиск доменного газу Д2; 3-витрата природного газу Д3; 4-блок живлення БП1; 5-блок ручного управління БРУ; 6-пускачі безконтактні Реверсивні ПБР; 7-виконавчий електричний однооборотний механізм МЕВ; 8-блок живлення logo power БП2; 9-Покажчик Положення УП; 10-стандарт промислових мереж RS 485; 11 - персональний комп'ютер ПК; 12-диспетчерський пункт ДП.
Висновок
В результаті виконання дипломного проекту, був проаналізований технологічний процес виробництва теплоносія теплоенергоцентралі металургійного заводу. Виходячи з проведеного аналізу була складена структурна схема управління виробництвом теплоносія.
На підставі проведених досліджень можна перейти до розробки принципових схем, і програмного забезпечення, системи автоматичного управління виробництвом теплоносія теплоенергоцентралі металургійного заводу.
При написанні даного реферату магістерська робота ще не завершена. Остаточне завершення: грудень 2023 року. Повний текст роботи і матеріали по темі можуть бути отримані у автора або його керівника після зазначеної дати.