Реферат по теме выпускной работы
Содержание
- Введение
- 1. Актуальность темы
- 2. Цель и задачи исследования, планируемые результаты
- 3. Обзор исследований и разработок
- 3.1 Технологический процесс производства теплоносителя теплоэнергоцентрали металлургического завода как объекта автоматизации
- 3.2 Обзор известных технических решений по автоматизации котельных установок
- 3.3 Структурная схема разработанной системы автоматизации
- Выводы
- Список источников
Введение
Современная котельная установка является сложным сооружением, включающим в себя различное оборудование, связанное в единое целое общей технологической схемой, основным элементом которой является котельный агрегат. Именно котельный агрегат предназначен для производства требуемого количества конечного продукта пара или горячей воды с заданными потребителем показателями качества.
Источником энергии для котельных установок различного назначения являются природные и искусственные топлива в твердом, жидком и газообразном состояниях, теплота исходящих газов технологических установок, теплота экзотермических превращений, выделяющаяся в отдельных технологических процессах и т.п. В данной работе рассматривается паровой барабанный котел, оснащенный газовой топкой. Эффективность работы топок всех типов в первую очередь определяется эффективностью процесса горения. Эффективность процесса горения, в свою очередь, обеспечивается путем поддержания на требуемом уровне отношения «топливо-воздух». Тем самым предопределяется та первостепенная роль, которую играют в системе управления топочным устройством системы автоматического регулирования подачи топлива и давления дутьевого воздуха.
К одной из существенных проблем энергетики Донецкого металлургического завода относится недостаточно эффективное использование попутного топлива (доменного газа), получаемого при производстве чугуна в доменных печах. Неравномерность хода металлургических процессов обусловлена нестабильностью режима производства и потребления доменного газа, что приводит к значительным колебаниям давления в газопроводах, к увеличению прямых потерь через сбросные свечи, ухудшению режимов работы основных металлургических агрегатов: нагревательных колодцев, печей прокатных станов и т.д.
Основным потребителем доменного топлива являются котлы ТЭЦ-ПВС, в большинстве случаев они не в состоянии обеспечить его полное потребление и стабилизацию давления в магистральных газопроводах. Одна из основных причин - недостаточный уровень автоматизации средств по управлению подачи топлива в топку котла. Для решения данной проблемы необходимо обеспечить своевременное информирование о калорийности и давлении доменного газа перед подачей его в топку. Для поддержания на требуемом уровне отношения «топливо-воздух» необходимо измерять количество кислорода в отходящих газах, для чего используется стационарный газоанализатор. К этому следует добавить, что эффективность работы котлоагрегата в целом определяется показателями качества конечного продукта, каковым в данном случае является пар.
Теплоотдача топки является управляющим воздействием для системы парогенерации. Следовательно, для поддержания давления пара на заданном уровне необходимо соответствующим образом корректировать уставки регулятора подачи топлива. На необходимость такой связи указывается во многих литературных источниках. Однако в силу особенностей изготовления и монтажа котлоагрегата такой связи практически нигде нет. Каждая из указанных систем управления функционирует самостоятельно, реагируя только на внешние и внутренние факторы. Связь же между ними осуществляется только через процесс нагрева, причем односторонне – от топки к барабану. Понятно, что это приводит к существенному снижению эффективности основных технологических параметров парогенерирующей системы [1].
С учетом сказанного, целью данной работы является обеспечение эффективности, надежности и безопасности работы парового котлоагрегата путем автоматического регулирования основных технологических параметров газового топочного устройства это приведет к увеличению реальной производительности ТЭЦ при одновременном снижении себестоимости отпускаемого пара, электроэнергии и тепла, так как автоматизированная система может функционировать непрерывно в режиме реального времени обеспечивающего эффективность процесса горения и учитывающего режимы работы и динамические свойства парогенерирующей системы в виде соответствующих корректирующих связей.
1. Актуальность темы
Повышение эффективности использования вторичных энергоресурсов может быть достигнуто путем совершенствования эксплуатирующегося основного и вспомогательного оборудования теплоэлектростанции (ТЭЦ-ПВС), их тепловых и пусковых схем, автоматизированных систем технологических процессов (АСУ ТП) и технологии эксплуатации, а также внедрением нового замещающего оборудования. Технико-экономические показатели ТЭЦ-ПВС зависят от характеристик основного оборудования и вида сжигаемого топлива, особенно при сжигании различных углей, а также от технологической схемы отпуска тепла. Важнейшее значение при этом имеет эффективность котлов и теплофикационных паротурбинных установок. Поэтому разработки, направленные на повышение эффективности технологии использования вторичных энергоресурсов таких как (доменный газ), получаемого при производстве чугуна в доменных печах являются актуальными. Особенно это важно для проведения реконструкции и технического перевооружения АСУТП ТЭЦ-ПВС, оборудование которых исчерпало ресурс.
К основным элементам котельной относятся:
Котел – это теплообменное устройство, в котором теплота от горячих продуктов сгорания топлива передается воде. В результате этого в паровых котлах вода превращается в пар, а в водогрейных котлах нагревается до требуемой температуры. Топочное устройство служит для сжигания топлива и превращение его химической энергии в теплоту нагретых газов. Питательные устройства (насосы, инжекторы) предназначены для подачи воды в котел. Без перечисленных элементов не может работать даже самая простая котельная установка.
К вспомогательным элементам котельной относят:
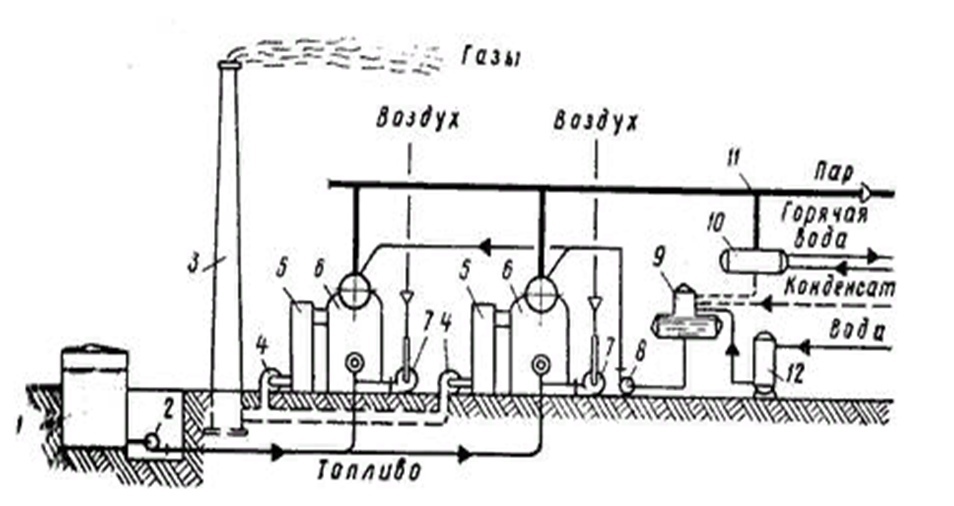
Рисунок 1 – Схема котельной установки: 1 – топливохранилище; 2 - топливный насос; 3 – дымовая труба; 4 – дымососы; 5 – водяные экономайзеры; 6 – паровые котлы; 7 – дутьевые вентиляторы; 8 – питательные насосы; 9 – деаэратор; 10 – водоподогреватель; 11 – паропровод; 12 – водоподготовительная установок.
2. Цель и задачи исследования, планируемые результаты
Производство тепла всегда является очень важной проблемой современной жизни, а модернизация и улучшение этого процесса всегда актуальны. На данный момент котельные установоки остро нуждаются в модернизации, поскольку они практически не автоматизированы и большинством процессов управляет человек вручную, допуская ошибки. Как правило, на многих котельных, большинство систем регулирования параметров котла все еще работают в ручном режиме, что приводит к серьезным экологическим загрязнениям и неэффективному использованию топлива в режимах избытка или недостатка воздуха для горения.
Целью данной работы является анализ технологических параметров газового топочного устройства для последующей его автоматизации котрая обеспечить своевременное информирование о калорийности и давлении доменного газа перед подачей его в топку. Полноценное решение задачи эффективного сжиганиякоксодоменной смеси на котлах путем создания всережимных регуляторов стало возможным только с массовым распространением высоконадежных программируемый логических контроллеров.
Основные задачи исследования:
- анализ котельная установки как объекта автоматизации;
- анализ существующих разработок по автоматизации производства теплоносителя теплоэнергоцентрали;
- разработка математической модели производство теплоносителя теплоэнергоцентрали металлургического завода;
- разработка схемных решений. Структурная, функциональная схема устройства автоматизации, алгоритм работы;
- практическая реализация системы автоматизированного управления котельная установки. Разработка мнемосхемы управления производством теплоносителя теплоэнергоцентрали металлургического завода;
- разработка мероприятий по безопасной и безаварийной эксплуатации разработанного устройства.
Объект исследования: котельная установка.
Предмет исследования: автоматическая система управления производством теплоносителя теплоэнергоцентрали металлургического завода.
3. Обзор исследований и разработок
3.1 Технологический процесс производства теплоносителя теплоэнергоцентрали металлургического завода как объекта автоматизации
Объектом автоматизации является котел типа БК3-75-39ФБ - однобарабанный, П-образной компоновки, вертикально-водотрубный, с естественной циркуляцией. Котел состоит из: топочной камеры и горелочных устройств, пароперегревателя, водяного экономайзера, трубчатого воздухоподогревателя. Технологическая схема устройства и работы котельной на базе котла типа БК3-75-39ФБ приведена на рисунке 2.
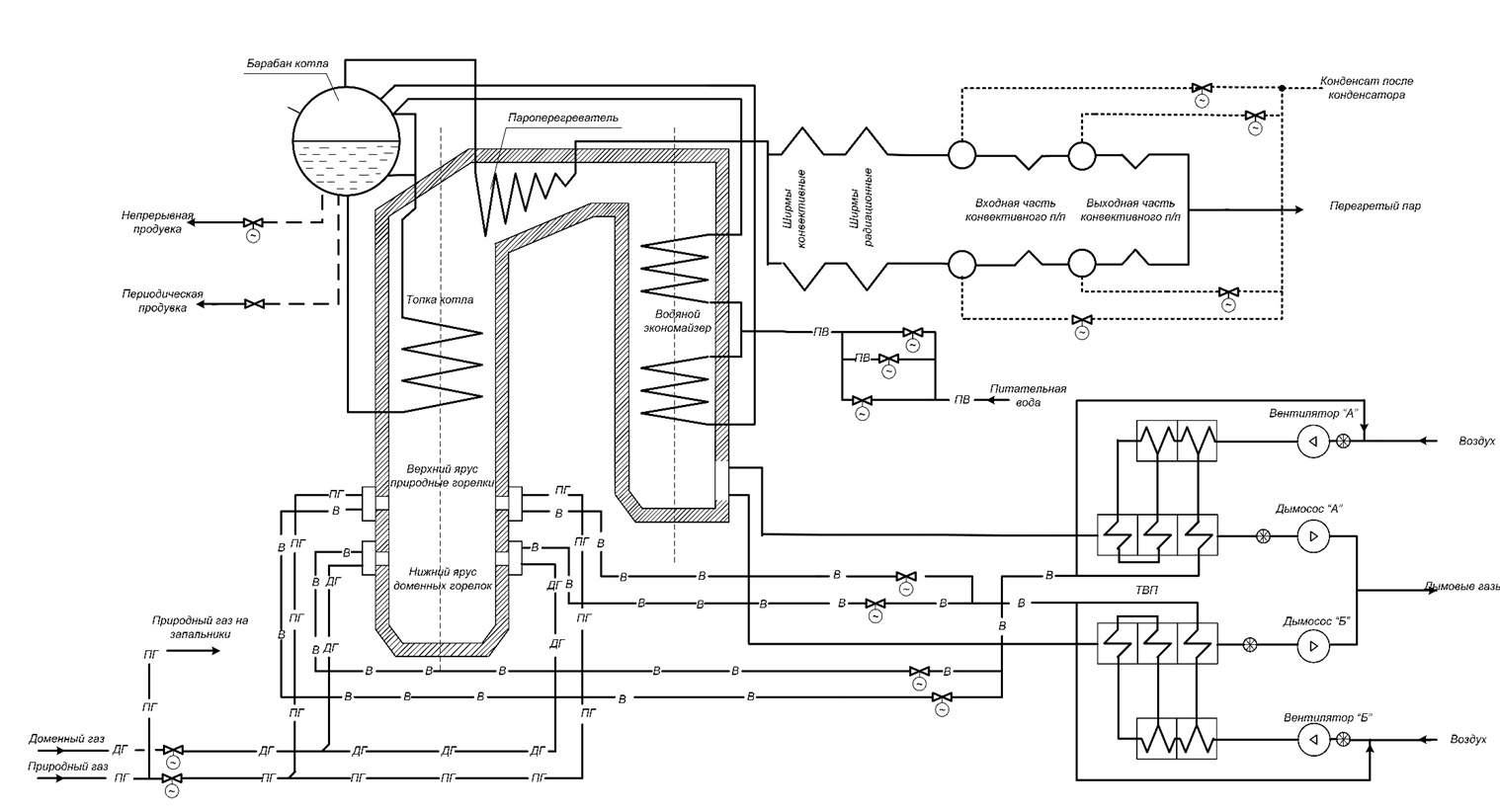
Рисунок 2 – Технологическая схема устройства и работы котла типа БК3-75-39ФБ
Объем топочной камеры - 454 м3, стены топки полностью экранированы трубами диаметром (60x3) мм, выполненные из стали Ст. 20. Экранные поверхности нагрева разбиты на 12 самостоятельных циркуляционных контуров по числу монтажных блоков.
Количество труб:
В качестве топлива используется природный, а также доменный газ - искусственный вид топлива, получаемый как побочный продукт при производстве чугуна. В качестве теплоносителя выступает пар. Основными цехами, тесно связанными по технологии, являются котельно-турбинный и химической водоочистки. Для получения пара нормального качества в котле применена схема трехступенчатого испарения. Первая ступень испарения (чистый отсек) и вторая ступень (солевые отсеки) расположены непосредственно в барабане котла. Выносные циклоны являются третьей ступенью испарения.
В первую ступень испарения включена центральная часть барабана котла с блоками фронтового, заднего и переднего блоков боковых экранов. Во вторую ступень выделены торцевые части барабана, отделенные от центральной части перегородками. В циркуляционный контур второй ступени включены средние блоки боковых экранов. В третью ступень испарения включены выносные циклоны диаметром (377x18) мм, а в циркуляционный контур третьей ступени включены задние блоки боковых экранов. Питание выносных циклонов осуществляется необогреваемыми трубами диаметром (83x3,5) мм из солевых отсеков барабана. Сепарационные устройства первой ступени испарения состоят из утопленного перфорированного пароприемного потолка. [4]
Во второй ступени испарения установлены (в каждом торце барабана) по два внутри барабанных циклона и пароперепускные короба, изменяющие направление движения пара. В третьей ступени испарения элементами сепарации являются: сама улитка выносного циклона и перфорированный пароприемный потолок.
Питательная вода из водяного экономайзера поступает в барабан котла по 10 трубам диаметром (60x3) мм и через раздаточный короб направляется на промывочные (дырчатые) щиты, протекает по ним и сливается в водяной объем барабана. Средний рабочий уровень воды в Чистом отсеке на 50 мм ниже оси барабана. В солевые отсеки котловая вода поступает из чистого отсека через трубы, смонтированные в нижних частях перегородок. Пароводяная смесь из выходных коллекторов третьей ступени испарения поступает в улитки выносных циклонов, а отсепарированный пар из выносных циклонов по трубам диаметром (83x3,5) мм поступает в соответствующий солевой отсек барабана.
Пароводяная смесь из экранных контуров второй ступени поступает во внутрь барабанных циклонов, установленные в солевых отсеках. Вода, отсепарированная в циклонах, сливается в водяной объем солевого отсека, а пар проходит через жалюзийные сепараторы, расположенные над циклонами, смешивается с паром третьей ступени и по коробам направляется в паровое пространство чистого отсека барабана. Пароводяная смесь из экранной системы первой ступени поступает под дырчатые листы, погруженные в воду на 50 мм ниже низшего уровня воды в барабане. Пар проходит через них, смешивается с паром, поступающим из соевых отсеков, и, пройдя жалюзийный пакет и пароприемный дырчатый потолок, направляется в пароперегреватель. Циркуляционная схема котла предусматривает глубокое секционирование экранов, что повышает надежность циркуляции пароводяной смеси в экранах котла.
На котле установлен конвективный пароперегреватель, расположенный за четырехрядным фестоном в переходном горизонтальном газоходе. Пароперегреватель выполнен двухступенчатым, площадь поверхности нагрева каждой ступени - 220 м2. Схема включения пароперегревателя относительно направления движения уходящих газов - смешанная. Пар из барабана по 72 трубам диаметром (38x3) мм проходит первую ступень пароперегревателя и поступает в выходной коллектор диаметром (273x25) мм. Из выходного коллектора первой ступени пар 10 трубами диаметром (83x5) мм (перекрестным потоком по 5 трубам с левой и правой стороны коллектора) отводится в два коллектора диаметром (325x25) мм. Далее пар по 36 трубам диаметром (38x3) мм проходит вторую ступень пароперегревателя и поступает в промежуточный коллектор диаметром (273x25) мм. Из боковых частей промежуточного коллектора пар поступает в среднюю часть и далее по 72 змеевикам диаметром (38x3) мм проходит среднюю часть второй ступени пароперегревателя, а затем поступает в выходной коллектор пароперегревателя диаметром (273x25) мм и далее в паропровод.
Водяной экономайзер и воздухоподогреватель расположены в опускном газоходе в рассечку. Водяной экономайзер кипящего типа, змеевиковый, двухступенчатый, поверхность нагрева первой ступени 700 м2, второй ступени - 240 м2. Первая ступень водяного экономайзера состоит из 41 змеевика диаметром (32x3) мм из стали 20, вторая ступень водяного экономайзера состоит из 48 змеевиков такого же диаметра и материала. После блока питания вода трубой диаметром (108x10) мм подводится к входному коллектору первой ступени водяного экономайзера. Расчетная температура питательной воды 150 °С. Пройдя змеевики первой ступени, вода из выходного коллектора 6 трубами диаметром (66x3) мм перекрестным потоком поступает во входной коллектор второй ступени. Пройдя вторую ступень, питательная вода через два выходных коллектора, расположенных на боковых стенках, 10 трубами диаметром (60x3) мм (по 5 трубам с каждого коллектора) отводится в барабан котла. Все пять коллекторов водяного экономайзера выполнены из труб диаметром (219x16) мм. Воздухоподогреватель котла - трубчатый, однопоточный по газам и четырехходовой по воздуху, состоит из стальных труб диаметром (40x1,5) мм Поверхность нагрева первой (холодной) ступени - 2600 м2, второй (горячей) ступени - 1600 м2
Тягодутьевая установка котла состоит из одного дутьевого вентилятора типа ВД-18 и одного дымососа типа Д 20x2. Воздух с температурой от 30 °C до 50 оС всасывается вентилятором из помещения котельной и, пройдя через воздухоподогреватель, по воздухопроводам подается к газовым горелкам. Дымовые газы отсасываются дымососом и выбрасываются в дымовую трубу. Сопротивление котлоагрегата по дымовым газам в зависимости от вида топлива составляет от 116 до 148 мм вод. ст. Воздушное сопротивление от 73 до 87 мм вод. ст.
Котел рассчитан на работу с уравновешенной тягой (подача воздуха на горение осуществляется дутьевым вентилятором, а удаление продуктов сгорания - дымососом). Регулирование подачи и напора дымососа и вентилятора осуществляется направляющими аппаратами, установленными на стороне всасывания.
Основным параметром, отвечающим за управление производством теплоносителя в теплоэнергоцентрали металлургического завода, который можно автоматизировать - является регулирование подачи топлива в топку котла. В топке котла сжигается совместно или раздельно доменный и природный газ. Для сжигания этих топлив топка котла оборудована двумя плоско факельными горелками, горелка состоит из двух газовоздушных сопел, наклоненных под углом 60° друг к другу. Верхнее сопло состоит из соосно расположенных коробов прямоугольного сечения для доменного газа и воздуха. Доменный газ подается по центральному коробу, внутренние размеры которого равны (0,39x0,74) м. По наружному коробу верхнего газовоздушного сопла поступает горячий воздух для горения. Размеры последнего (0,6x0,9) м. Нижнее газовоздушное сопло представляет собой горелку природного газа и состоит из воздушного короба размером (0,5x0,5) м, внутри которого расположены в два ряда по вертикали десять газораздающих труб диаметром (42x3) мм. Между верхним и нижним газовоздушными соплами устанавливается труба для зашитно-запального устройства и труба для датчика основного факела. Техническая характеристика комбинированной плоскофакельной горелки приведена ниже:
Производительность горелки по:
Сопротивление горелки по:
Максимальное сопротивление по воздуху:
Принцип действия плоскофакельной горелки основан на использовании эффекта соударения двух струй воздуха, направленных под углом друг к другу. Между этими потоками образуется «треугольник», в который с боковых сторон эжектируются раскаленные продукты сгорания, осуществляющие прогрев и зажигание топлива. Соударение двух потоков приводит к образованию плоской струи, имеющей большую степень турбулизации и сильно развитую поверхность, что способствует интенсивному сгоранию топлива в объеме топки. При работе на доменном газе газовоздушный импульс верхнего сопла мощнее импульса нижнего сопла. Поэтому факел смещается к поду топки. Тепловосприятие нижней части топки увеличивается, что приводит к понижению температуры газов на выходе из топки. Это позволяет повысить производительность котла на доменном газе.
При работе котла на высококалорийном природном газе, газовоздушный импульс нижнего сопла выше, чем верхнего. Факел смещается вверх, температура газов на выходе из топки повышается и увеличивается температура перегретого пара. При работе на смеси топлив факел в топке занимает промежуточное положение. Таким образом, обеспечивается саморегулирование температуры перегретого пара. Характеристика сжигаемых топлив. Доменный газ - искусственный вид топлива, получаемый как побочный продукт при производстве чугуна. Средний состав доменного газа:
- углекислый газ СО2 - 16,2 %;
- метан CH, - 0,2 %;
- кислород O2, - 0,1 %;
- водород Н2 - 4,8 %;
- окись углерода СО - 22,8 %;
- азот N2 - 56,0 %;
- теплота сгорания Q - 772 ккал/м3;
- плотность р - 1,298 кт/м
Определение содержания природного газа производится по содержанию в нем метана CH4. Состав природного газа:
- CH4, - 94,565 %;
- Cm Hn, - 2,34 %;
- CO2 - 0,019 %;
- N2 - 3,076 %;
- низшая теплота сгорания - 7918 ккал/м3;
- плотность р - 0,70 кг/м3.
Таким образом, предлагаемая автоматизация системы управления заключается в модернизации существующей системы управления производством теплоносителя за счет использования современных средств автоматизации, которые в свою очередь заменят устаревавшую аппаратуру. Данная система автоматического управления производством теплоносителя на базе котла типа БК3-75-39ФБ, с учетом специфики управления, обеспечит снижение потребления природного газа за счет, смешанного режимов работы на двух топливах, в идеальных условия будет использоваться только доменный газ, что позволит увеличить производительности агрегата, при этом возрастет экономичность в использовании природного газа.
3.2 Обзор известных технических решений по автоматизации котельных установок
В качестве существующей системы автоматизации приведена система управления котлом БКЗ-75-39ГМА выполнена на базе программируемого контроллера C200HG фирмы «OMRON». Паровой котел является объектом повышенной опасности с точки зрения безопасности работы производственного оборудования. Функционирование котла характеризуется информацией, поступающей от аналоговых и дискретных датчиков состояния теплотехнических параметров, датчиков положения ИМ и датчиков состояния (включено/отключено) электродвигателей. Оперативное управление котлом производится с промышленного терминала NT620C. В качестве модуля управления применяется промышленный терминал NT620C. Терминал NT620C имеет широкие возможности.
Применение такого терминала позволит:
- отображать состояние оборудования и системы управления;
- вводить необходимую информацию;
- отображать в виде мнемосхем ход технологического процесса;
- осуществлять ручное управление оборудованием и контуров контроля;
- отказаться от большого числа сигнальных ламп и кнопок управления.
В основу построения унифицированной системы управления положен принцип конфигурирования систем из типовых модулей и блоков, позволяющих решать все многообразие задач контроля и управления технологическими процессами. Все модули связаны между собой высокоскоростной сетью и могут составлять любую конфигурацию.
- осуществляет обмен командами и данными с модулем управления;
- осуществляет включение и выключение дискретных выходов;
- возможность непрерывного контроля достоверности всей или определенного класса входной информации с сигнализацией и регистрацией неисправности отдельных датчиков или каналов связи;
- возможность реструктуризации алгоритмов при выявлении неисправности;
- возможность контроля выполнения команд по факту и во времени;
- самодиагностика технических средств с сигнализацией и регистрацией отказов на уровне типового элемента замены;
- возможность санкционированного контроля состояния любого датчика или алгоритма;
- упрощение процедуры внесения оперативных и неоперативных изменений при санкционированном доступе к таким изменениям с одновременной автоматической регистрацией факта доступа и внесенных изменений;
- возможность фиксации времени возникновения всех регистрируемых событий;
- автоматическая подготовка отчетной документации;
- упрощение процедуры опробования защит;
- более высокая ремонтопригодность технических средств;
- значительное уменьшение габаритных размеров технических средств, реализующих подсистему, при расширении выполняемых функций;
- возможность полного резервирования технических средств при минимальном усложнении системы.
- Теоретические основы разработки и моделирования систем автоматизации: Учебное пособие / А.М. Афонин, Ю.Н. Царегородцев, А.М. Петрова и др. - М.: Форум: НИЦ ИНФРА-М, 2014. - 192 с.
- Глинков, Г.М. АСУ ТП в черной металлургии: учебник для вузов. / Г.М. Глинков, В.А. Маковский – 2-е изд., перераб. и доп. – М.: «Металлургия», 1999. – 310 с.
- Лысенко, В. Г. Топливо. Рациональное сжигание, управление и технологическое использование: Справочное издание. В 3 книгах / В. Г. Лысенко, Я. М. Щелоков, М. Г.Ладыгичев. – Теплотехник, 2004. – 608 с.
- Гусев Ю. М. Основы проектирования котельных установок / Ю. М. Гусев. – [изд. 2-е, перераб. и доп.] – М.: Стройиздат, 1973. – 248 с.
- Справочник эксплуатационника газовых котельных / [под ред. Е. Б. Столпнера]. – Л.: Недра, 1976. – 608 с.
- Липов Ю. М. Котельные установки и парогенераторы / Ю. М. Липов, Ю. М. Третьяков. – Москва-Ижевск: НИЦ «Регулярная и хаотическая динамика», 2003. – 592 с.
- Официальный сайт Донецкого металлургического завода [Электронный ресурс]: Режим доступ: http://dmz.donetsksteel.com/ru/company
- Официальный сайт компании ОВЕН, ПЛК73 контроллер [Электронный ресурс]: Режим доступ: https://owen.ru/product/plk73
В процессе работы модуль выполняет следующие задачи:
Все модули обладают развитой системой самодиагностики. Осуществляется проверка исправности прохождения сигналов (проверка на наличие “1” при наличии входного сигнала, проверка на наличие “0”- при отсутствии сигнала), проверка на отсутствие влияния входов друг на друга. Модули имеют индикаторы исправной работы. Зеленый светодиод информирует об исправном функционировании модуля. В случае неисправности загорается красный светодиод, и информация о характере неисправности становится доступной модулю управления
В данном случае автоматизация процесса управления разряжением в топке котла выполнена с помощью датчика «Метран – 45 ДИВ», контроллера фирмы «Омрон» С200НG, пускателя бесконтактного реверсивного ПБР – 3А, исполнительного механизма электрического однооборотного МЭО – 630/25 –0,25–87–Р и дымососа ДН-18. Технические характеристики каждого из элементов АСР и выполняемые ими функции приведены ниже на рисунке 3.
Датчик давления – разряжения «Метран – 45 ДИВ» с токовым унифицированным сигналом 4 - 20 мА, с пределом допускаемой основной погрешности = 0,5%. Верхний предел измерений +3,15 кПа. Нижний предел измерений +0,03 кПа. Диапазон температур измеряемой среды –40 - +80?С. Степень защиты от пыли и воды IP65. Взрывозащищенность Ех. Пускатель бесконтактный реверсивный ПБР – 3А. Завод – изготовитель г. Челябинск, «Завод электроники и механики». Механизм электрический однооборотный, номинальный крутящий момент на выходном валу 630 Нм, время полного хода выходного вала 25 с, полный ход выходного вала 0,25 оборота, датчик обратной связи токовый с сигналом 4 - 20 мА. Комплект с блоком питания БП – 10. Дымосос ДН-18, производительность 143000 куб. м/ч, напор 236 мм вод. ст., 730 об/мин, мощность 250кВт.
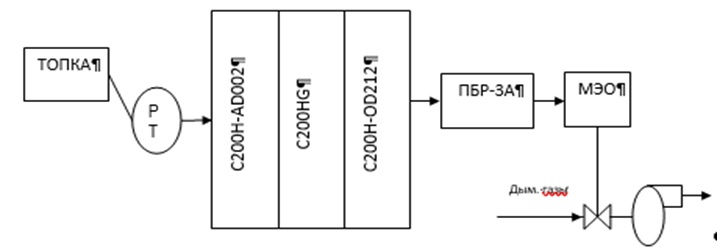
Рисунок 3 – Структурная схема одноконтурной автоматической системы расхода разряжения в топке котла
Таким образом, данная система автоматизации построена на базе программируемого контроллера C200HG фирмы «OMRON» но, у нее есть определенные недостатки принцип конфигурирования системы состоит из использования типовых модулей и блоков расширения от фирмы Sysmac. В случае выхода из строя (неисправности) блоков входящих в единую систему управления возникают определенные сложности с заменой аппаратуры так как, в основу построения унифицированной системы управления положен принцип конфигурирования систем из типовых модулей и блоков. Это приводи к тому, что универсальность и взаимозаменяемость становится невозможной при данном технологическом решении. Для любого предприятия простои связаны с финансовыми убытками, нарушением сроков сдачи готового продукта, потерей имиджа компании. Внеплановые остановки – это упущенная прибыль завода.
Альтернативным методом модернизации автоматической системы управления является взаимозаменяемость и универсальность использования программируемых контроллеров. За базовую аппаратуру автоматизации примем широко применяемый в современных котельных установка, а именно ПЛК от компании ОВЕН.
3.3 Структурная схема разработанной системы автоматизации
Для системы автоматического управления производством теплоносителя теплоэнергоцентрали металлургического завода принят программируемый логический контроллер ПЛК73 от компании ОВЕН который, взаимодействуя с датчиками, получает информацию от объекта управления, обрабатывает ее в соответствии с заложенным алгоритмом и выдает управляющие воздействия на исполнительные устройства. Применение микропроцессорных средств для реализации подсистемы технологических защит и защитных блокировок дает следующие преимущества по сравнению с традиционными средствами:
Взаимодействие с датчиками и исполнительными устройствами определяется соответствующими протоколами обмена, учитывающими особенности функционирования системы в целом и требований программно-аппаратной и схемотехнической совместимости с другими устройствами и системами. На структурной схеме изображены все основные функциональные части системы (элементы, устройства и функциональные группы) и основные взаимосвязи между ними. Графическое построение схемы на рисунке 4 обеспечивает наилучшее представление о последовательности взаимодействия функциональных частей в системе. На линиях взаимосвязей стрелками обозначены направление хода процессов, происходящих в устройстве.
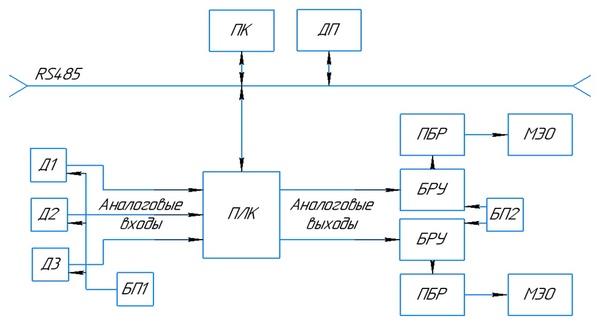
Рисунок 4 – Структурная схема управления производством теплоносителя: 1 - расход доменного газа Д1; 2 - давление доменного газа Д2; 3 - расход природного газа Д3; 4 - блок питания БП1; 5 - блок ручного управления БРУ; 6 - пускатели бесконтактные реверсивные ПБР; 7 - исполнительный электрический однооборотный механизм МЭО; 8 - блок питания logo power БП2; 9 - указатель положения УП; 10 - стандарт промышленных сетей RS485; 11 - персональный компьютер ПК; 12 - диспетчерский пункт ДП.
Выводы
В результате выполнения дипломного проекта, был проанализирован технологический процесс производства теплоносителя теплоэнергоцентрали металлургического завода. Исходя из проведенного анализа была составлена cтруктурная схема управления производством теплоносителя.
На основании проведенных исследований можно перейти к разработке принципиальных схем, и программного обеспечения, системы автоматического управления производством теплоносителя теплоэнергоцентрали металлургического завода.
При написании данного реферата магистерская работа еще не завершена. Окончательное завершение: декабрь 2023 года. Полный текст работы и материалы по теме могут быть получены у автора или его руководителя после указанной даты.