Реферат по теме выпускной работы
Содержание
- Введение
- 1. Актуальность темы
- 2. Цель и задачи исследования, планируемые результаты
- 3. Обзор исследований и разработок
- 3.1 Технологический выплавки стали в электродугосталеплавильной печи как объект автоматизации
- 3.2 Разработка алгоритма работы и схемных решений системы автоматического управления технологическим режимом электродугосталеплавильной печи
- Выводы
- Список источников
Введение
На сегодняшний день электродуговые печи считаются самыми распространенными и экологически чистыми агрегатами для выплавки стали. Возможность сосредоточенного ввода значительного количества тепловой энергии в сочетании с простотой управления подводимой электрической мощностью является неоспоримым преимуществом дуговых сталеплавильных печей по сравнению с другими агрегатами для производства стали.
1. Актуальность темы
Снижение расходов на обслуживание и продление межремонтного срока, а также упрощение диагностики неполадок в совокупности с повышением надежности и экономичности, позволяет говорить о значительном экономическом эффекте, который связан с применением предлагаемых в работе методов и средств автоматизации в сравнении с традиционно применяемыми на рассматриваемом технологическом объекте – электродугосталеплавильной печи.
Именно поэтому исследование и проектирование системы автоматизации процессов выплавки стали в электродугосталеплавильной печи является актуальной темой в настоящее время.
2. Цель и задачи исследования, планируемые результаты
Цель исследования – повышение эффективности функционирования электродугосталеплавильной печи за счет разработки системы автоматического управления, что позволит улучшить качество производимой продукции при экономии материальных и энергетических ресурсов.
Основные задачи исследования:
- Анализ технологического процесса выплавки стали в электродугосталеплавильной печи как объекта автоматизации.
- Разработка структурной и функциональной схем системы автоматизации.
- Разработка алгоритма управления технологическим режимом электродугосталеплавильной печи.
3. Обзор исследований и разработок
3.1 Технологический выплавки стали в электродугосталеплавильной печи как объект автоматизации
Главной целью управления процессом плавки в электродугосталеплавильной печи является получение металла заданного состава и заданной температуры при высокопроизводительной и экономичной работе агрегата. Эта цель может быть достигнута при успешном решении системой управления следующих задач:
- согласованного изменения параметров плавильного процесса, т.е. температуры и состава металла и шлака с обеспечением заданных конечных значений параметров на выпуске;
- поддержания рационального и экономичного электрического режима печи;
- предотвращения перегрева и разрушения футеровки и других конструктивных элементов печи.
Повысить эффективности процесса выплавки стали в электродугосталеплавильной печи можно путем создания современной системы автоматического управления, обновлением аппаратного обеспечения. Основными задачами автоматического управления процессом плавки в электродугосталеплавильной печи являются:
- Централизованный контроль технологического процесса и работы печи с выдачей оперативной информации обслуживающему печь персоналу с регистрацией и сигнализацией отклонений от заданных значений основных параметров.
- Управление технологическим процессом – расчет оптимального состава шихты; управление загрузкой шихты в соответствии с рассчитанным составом; расчет количества кислорода, легирующих и шлакообразующих материалов, обеспечивающих получение металла заданного состава и качества и экономию материалов; управление подачей легирующих и шлакообразующих материалов; управление подачей кислорода в ванну; прогнозирование момента окончания технологических периодов плавки.
- Управление энергетическим режимом, обеспечивающее максимальное использование мощности печи, минимальный расход электроэнергии и нормальную эксплуатацию печи и ее электрического оборудования – управление тепловым режимом, управление электрическим режимом, управление газокислородными горелками, управление отводом отходящих из печи газов.
- Управление вспомогательными операциями – отбором проб металла, замером температуры металла и др.
- Сбор и отборка информации с выдачей необходимой документации – учет и регистрация расходов шихтовых материалов, легирующих, электроэнергии, кислорода; печатание протоколов плавки и др.
- Контроль за работой оборудования с сигнализацией и регистрацией неисправностей.
Современные АСУ ТП стали разрабатываются на основе классической трехуровневой модели построения архитектуры системы:
- нижний – полевой уровень (датчики);
- средний – уровень базовой автоматизации процессов производства (управляющие контроллеры);
- верхний – уровень управления технологией.
На нижнем уровне находится полевое оборудование: датчики, исполнительные механизмы и их вторичные приборы, щиты станций управления. В задачи оборудования этого уровня входит измерение физических параметров и их преобразование в стандартные типы электрических сигналов, получение управляющих сигналов от оборудования среднего уровня (контроллеры) и непосредственное управление технологическим оборудованием в соответствии с этими сигналами.
Уровень управления создается с применением высокопроизводительных программируемых логических контроллеров с распределенной системой ввода-вывода.
Первые два уровня проектируются с использованием современных программно-технических средств от ведущих зарубежных и отечественных производителей компонентов АСУ ТП (Siemens, Schneider Electric, Bernecker&Rainer, ABB, Omron и др.), системы контроля и диспетчерского управления (SCADA-системы) разрабатываются на основе программных продуктов Siemens WinCC, Schneider Vijeo Citect, WonderWare InTouch, Bernecker&Rainer и др.
Для автоматизации ДСП-150 конструкции фирмы Siemens VAI (Германия) использовалась системная платформа ПЛК для управления технологическими процессами всего сталеплавильного цеха в целом - SIEMENS SIMATIC S7 (рис. 3.1).

Рисунок 3.1 – Структурная схема автоматизации ДСП-150
Уровень системы автоматизации способен управлять оборудованием без какой-либо другой системы более высокого уровня. АСУ ТП включает следующие компоненты по мере того, насколько они указаны в спецификации объема поставки:
- человеко-машинный интерфейс (ЧМИ);
- программируемые логические контроллеры (ПЛК);
- весоизмерительное оборудование;
- специальные узлы на базе микропроцессорной техники;
- пульт и/или панели в посту (постах) управления
Система уровня 1 покрывает все необходимые функции для управления оборудованием в ручном и/или автоматическом режиме. Передача данных между системой уровня 1 и системами более высоких уровней обеспечивается либо через систему шин, либо через стандартные последовательные каналы связи.
Ручное управление отдельными агрегатами или группами агрегатов (старт/стоп) или ручная настройка клапанов, дроссельных заслонок, исполнительных органов и т.д. производится с пультов или панелей управления в посту (постах) управления. В этом режиме работы функционируют только основные блокировочные функции для предупреждения опасности для эксплуатационного персонала и механического оборудования.
Автоматический режим предусматривается функции управления без обратной связи и/или с обратной связью и управление оборудованием со всеми блокировками через ЧМИ (например, ручная настройка уставок) и традиционные элементы управления по мере необходимости для управления оборудованием.
Цель функционирования дуговой сталеплавильной печи – получение металла температурой 1620оС ±20оС с необходимым составом и требуемого качества [1,3].
Выплавка стали в ДСП включает в себя следующие технологические операции [1,3,4]: подготовка печи к завалке; завалка; расплавление; доводка; выпуск плавки.
В шихтовом пролете ЭСПЦ осуществляется загрузка металлической шихты в корзины (бадьи) и с помощью мостового крана доставляется в печной пролет ЭСПЦ, где производится ее завалка в дуговую сталеплавильную печь. Выплавка стали начинается с завалки металлической шихты на «болото», оставшейся от предыдущей плавки части жидкого металла в количестве 15 т. На дно загрузочной бадьи укладывают легковесный лом, затем размещается тяжеловесный лом. Ближе к стенкам бадьи загружаются шлакообразующие добавки. Кокс укладывают поверх слоя тяжеловесного лома и извести для предотвращения поломок электродов при контакте с токонепроводящими материалами. Затем на средний лом кладут слой легковесного лома для быстрого проплавления колодцев. Плотная укладка металлической шихты обеспечивает её хорошую проводимость. В случае невозможности загрузки кокса или шлакообразующих в бадью их засыпку в ДСП производят во время расплавления завалки.
Выплавка стали осуществляется в автоматическом режиме, при влиянии теплового воздействия. Преобразование электрической энергии в тепловую происходит при возникновении электрической дуги, которая представляет собой один из видов дугового разряда, возникающего между графитированными электродами. Именно величина тока дуги и расстояние между электродами определяют скорость плавки металла. После окончания завалки и установки свода ДСП в рабочее положение, электроды опускают почти до касания с шихтой и включают печь. Между электродами и шихтой загораются электрические дуги, под воздействием излучения которых, металлическая шихта начинает плавиться под электродами и жидкий металл стекает вниз. Для ускорения плавления лома в холодных местах рабочего пространства и получения активной по всей поверхности шлаковой ванны, используют дополнительную энергию газокислородных горелок, расход газа и кислорода на горелку принимают в соотношении 1:2. Горелки включают сразу после завалки, при работе стеновых газокислородных горелок, также осуществляют донную продувку аргоном для повышения качества металла.
Расход электроэнергии в период плавления равен 370 кВт·ч/т. При работе ДСП необходимо поддерживать постоянную электрическую дугу. Для этого необходимо организовать надлежащую проводимость между электродом и шихтой. Достигается необходимый уровень проводимости за счет изменения положения (перемещения) электродов по вертикали, либо изменением напряжения на них, для поддержания дуги подается напряжение от 100 до 600 В и ток 50-100 кА. Электроды постепенно перемещаются и опускаются в образующиеся под ними в шихте «колодцы». В процессе плавления контролируется температура воды на панелях свода.
В момент интенсивного шлакообразования и сходу шлака из печи температура металла должна быть 1550оС, что позволяет получить наилучшие условия дефосфорации металла. Для схода шлака корпус ДСП наклоняют в сторону рабочей площадки материалов приблизительно на 5о. Удаление шлака осуществляется через рабочее окно ДСП. С целью недопущения переокисления ванны во время работы кислородных фурм и продувке ванны кислородом, подача углесодержащего материала является обязательным. В момент полного расплавления металлической шихты термопарой измеряют температуру металла и осуществляют отбор проб погружным пробоотборником. Получив предварительную информацию о химическом составе металла, продолжают окисление примесей в металле продувкой ванны ДСП кислородом через кислородную фурму.
Процесс плавки стали в ДСП, а также предшествующие и последующие за ним стадии данного технологического процесса, сопровождаются существенными выделениями пыли. Удаление печных газов из ДСП осуществляется через водоохлождаемый газоход и систему газоочистки с рукавными фильтрами. Выпуск готового металла осуществляется через сливной желоб. Весь процесс управления дуговой сталеплавильной печью и ее элементами, подразделяется на управление технологическим режимом и управление тепловым режимом [5,6]. Поскольку в электросталеплавильном технологическом процессе в ДСП основная часть тепла получается в результате преобразования электрической энергии, то возникает необходимость управлять количеством поступающего тепла, т.е. электрическим режимом, а если точнее – электрической мощностью ДСП [6,7].
Выполненный выше анализ особенностей процесса выплавки стали позволил составить структурную схему материальных потоков ДСП, которая приведена на рис. 3.2.
Как следует из схемы материальных потоков ДСП (рис.3.2) и выполненного выше анализа технологических процессов, протекающих в ней, электросталеплавильная печь является сложным, многомерным, многосвязным объектом управления, состоящим из большого количества технологических элементов. Первым и основным технологическим элементом и процессом, без нормального функционирования которого невозможно представить работу ДСП в принципе, является процесс получения тепловой энергии из электрической за счет требуемого поддержания длины электрической дуги на различных этапах процесса плавки. Как было описано выше, это является основным процессом при управлении ДСП – управление тепловым режимом ДСП, который сводится к управлению электрическим режимом, а точнее – электрической мощностью ДСП, как правило, за счет изменения длины дуги [6,7].
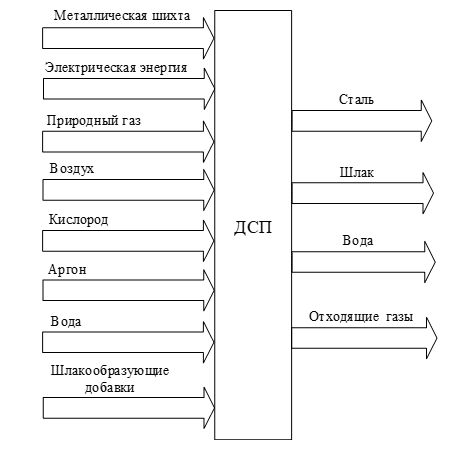
Рисунок 3.2 – Структурная схема материальных потоков ДСП
Следующим технологическим элементом ДСП, определяющим эффективность и экономичность, процесса выплавки стали является кислородная фурма. Нормальное функционирование кислородной фурмы определяется поддержанием требуемых параметров процесса подачи кислорода и процесса ее охлаждения. Процесс подачи кислорода в рабочее пространство ДСП характеризуется необходимым расходом кислорода на продувку при поддержании требуемого его давления. Отклонение расхода и давления кислорода от требуемых значений приводит к повышению эксплуатационных затрат на процесс производства стали в ДСП или к ухудшению качества получаемой стали. При охлаждении фурмы необходимо изменять расход охлаждающей воды для поддержания требуемой разности температуры на выходе и входе кислородной фурме, что при относительно постоянной температуре охлаждающей воды сводится к поддержанию заданной температуры охлаждающей воды на выходе из кислородной фурмы [7,8].
Таким образом, на основании схемы материальных потоков ДСП (рис.3.2) и рассмотренных выше особенностей процесса перемещения электродов, процесса охлаждения кислородной фурмы, а также процесса подачи кислорода, получена схема дуговой сталеплавильной печи для перечисленных элементов как объекта автоматического управления, которая приведена на рис. 3.3.
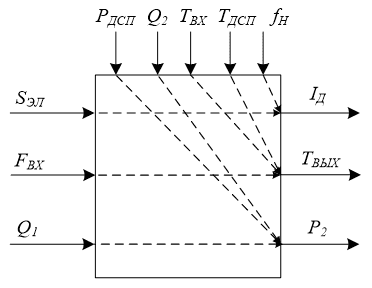
Рисунок 3.3 – ДСП как объект автоматического управления
Управляемыми переменными, характеризующими функционирование основных технологических элементов и процессов, при выплавке стали в ДСП, являются (рис. 3.3):
- при управлении мощностью ДСП – электрический ток дуги IД;
- при управлении охлаждением кислородной фурмы – температура охлаждающей воды на выходе фурмы ТВЫХ;
- при управлении подачей кислорода в фурму – давление на входе в кислородную фурму (на выходе подающего кислород трубопровода) Р2;
Управляющими воздействиями, позволяющими требуемым образом влиять на перечисленные управляемые переменные, являются (рис. 3.3):
- при управлении мощностью ДСП – перемещение электрода SЭЛ;
- при управлении охлаждением кислородной фурмы – расход охлаждающей воды на входе в кислородную фурму FВХ;
- при управлении подачей кислорода в фурму – расход кислорода на выходе управляемой задвижки (на входе подающего трубопровода) Q1;
Возмущающими воздействиями для рассматриваемых элементов ДСП, выступают (рис. 3.3):
- при управлении мощностью ДСП – неконтролируемые возмущения электрического режима, изменяющие расстояние между электродом и металлической шихтой fH (возмущения электрического режима возникают при обвалах металлической шихты в процессе плавления; при кипении металла; при обгорании электродов; при подъеме уровня металла по мере его плавления);
- при управлении охлаждением кислородной фурмы – температура охлаждающей воды на входе в кислородную фурму ТВХ и температура в рабочей зоне ДСП ТДСП;
- при управлении подачей кислорода в фурму – расход кислорода, потребляемый кислородной фурмой (на выходе подающего кислород трубопровода) Q1 и давление в рабочей зоне ДСП РДСП;
Анализ технологической схемы, технических особенностей, режимов работы, средств и систем автоматизации технологических элементов и процессов ДСП позволяет сформулировать цель – повышение эффективности функционирования электродугосталеплавильной печи за счет разработки системы автоматического управления, что позволит улучшить качество производимой продукции при экономии материальных и энергетических ресурсов.
Cформулируем требования к системе управления технологическим режимом электродугосталеплавильной печи на основании модели FURPS+, такие как: Functionality - функциональность; Usability - применимость; Reliability - надежность; Performance - производительность; Supportability - пригодность к эксплуатации.
1. Функциональность:
- сбор, первичная обработка, распределение и формирование массивов информации, получаемой от датчиков технологических и энергетических параметров электродугосталеплавильной печи в виде аналоговых, дискретных и цифровых сигналов;
- представление информации и взаимодействие пользователей с программно-техническим комплексом электродугосталеплавильной печи;
- дистанционное управление приводами оборудования и исполнительных механизмов электродугосталеплавильной печи;
- автоматическое, программное управление электродугосталеплавильной печью;
2. Безопасность.
Электротехнические изделия, используемые в системе управления электродугосталеплавильной печи, должны соответствовать ГОСТ 12.2.007-75, а средства вычислительной техники – по ГОСТ 25861-83, и имеют класс 1 защиты человека от поражения электрическим током. Все внешние элементы технических системы управления, находящиеся под напряжением, защищаются от случайного прикосновения;
3. Применимость.
Рабочее место оператора системы управления электродугосталеплавильной печью должно содержать несколько рабочих станций, которые предназначены для:
- представления, хранения и обработки технологической информации;
- выполнение функция и задач расчетного характера;
- реализация общесистемных функций;
4. Надежность.
Программно-технический комплекс электродугосталеплавильной печи в части требований по надежности должен соответствовать ГОСТ 4.148-85, ГОСТ 24.701-86 и ГОСТ 27.003-90.
5. Производительность.
Показатели быстродействия, времени отклика, точности и достоверности информации должны быть не хуже существующих аналогов.
6. Пригодность к эксплуатации.
Пригодность к эксплуатации характеризуется:
- рабочая температура окружающей среды 5-50°С;
- предельная температура 0-100°С;
- относительная влажность воздуха 30-75% при температуре 25°С;
7. Требования по массе, габаритам и степени защищенности корпуса.
Узлы САУ должны являться изделиями заводского изготовления с типовыми или проектно-компонуемыми тактико-техническими, метрологическими и массогабаритными характеристиками.
По степени защиты от воздействия окружающей среды:
- приборные шкафы КП ТМ – не ниже IP55(IP65);
- пульт управления – не ниже IP21;
- шкаф серверного оборудования – не ниже IP21;
3.2 Разработка алгоритма работы и схемных решений системы автоматического управления технологическим режимом электродугосталеплавильной печи.
Управление электрическим режимом печи электродугосталеплавильной печи разделяют на несколько стадий (рис. 3.4):
- Заглубление электродов в шихту.
- Проплавление колодцев.
- Плавка металла.
Рисунок 3.4 – Блок-схема алгоритма управления технологическими режимами электродугосталеплавильной печи
Перед стадией заглубления электродов в шихту, происходит зажигания дуг печи. Дифференциальный способ регулирования обеспечивает автоматическое зажигание дуг. После включения печи при отсутствии тока электрод опускается вниз, до момента касания с металлом. При появлении на датчике тока сигнала, первый электрод останавливается. Начинает опускаться второй электрод, при касании металлом вторым электродом оба электрода поднимаются вверх, зажигая дуги. А третий электрод опускается вниз до касания с металлом, после появления в нем тока, начнет подниматься, зажигая третью дугу.
Первая стадия заглубление электродов в шихту. В момент зажигания дуг фиксируется текущее положения электродов. Программно задается значение заглубления электродов, когда текущее значение заглубления электродов достигнет заданного, система управления переходит в следующий режим – проплавление колодцев.

Продолжение рисунка 3.4 - Блок-схема алгоритма управления технологическими режимами электродугосталеплавильной печи
Стадия проплавления колодцев. В этой стадии электроды проходят колодец быстро, при этом образуется жидкий металл. Для ограничения перемещения электродов в крайнее положение предусмотрены конечные выключатели. Сигнал об отсутствии движения электродов, будет свидетельствовать о завершении периода проплавления колодцев, и переходе в стадию плавки металла.
Стадия плавки металла проходит на введении максимальной мощности в печь. Завершается данная стадия в период, когда температура металла достигнет заданного программного значения.
Проектируемая система автоматизации по своей структуре представляет распределенную автоматизированную систему управления. Применяя современные принципы построения, можно определить следующую структуру системы автоматизации (рис. 3.5):
- диспетчерский уровень – отвечает за сбор, обработку данных и отображения технологического процесса;
- уровень контроллеров и модулей ввода/вывода, на данном уровне будет осуществляться сбор и обработка первичной информации с самого нижнего уровня;
- уровень датчиков и исполнительных механизмов, на этом уровне осуществляется согласование сигналов датчиков с входами устройства управления, а вырабатываемых команд с исполнительными механизмами.
Для проектируемой системы автоматизации необходимо установить первичные датчики измерения температуры футеровки и кладки днища, измерения температуры жидкого металла. Датчик измерения температуры охлаждающей воды в трубопроводе, используемой для охлаждение элементов печи, а также измерение температуры на сливе из водоохлаждаемой панели, по разности температур на входе и выходе которых, можно судить об интенсивности охладителя, и соответственно регулировать расход охлаждающей воды с помощью исполнительного механизма с заслонкой, а также датчик температуры отходящих газов.
Для системы автоматизации необходимо осуществить контроль расхода кислорода на фурму, с помощью датчиков давления и расхода, а также осуществить управление расходом на фурму посредством исполнительного механизма и установить отсечной клапан, с целью предотвращения аварийных ситуаций.
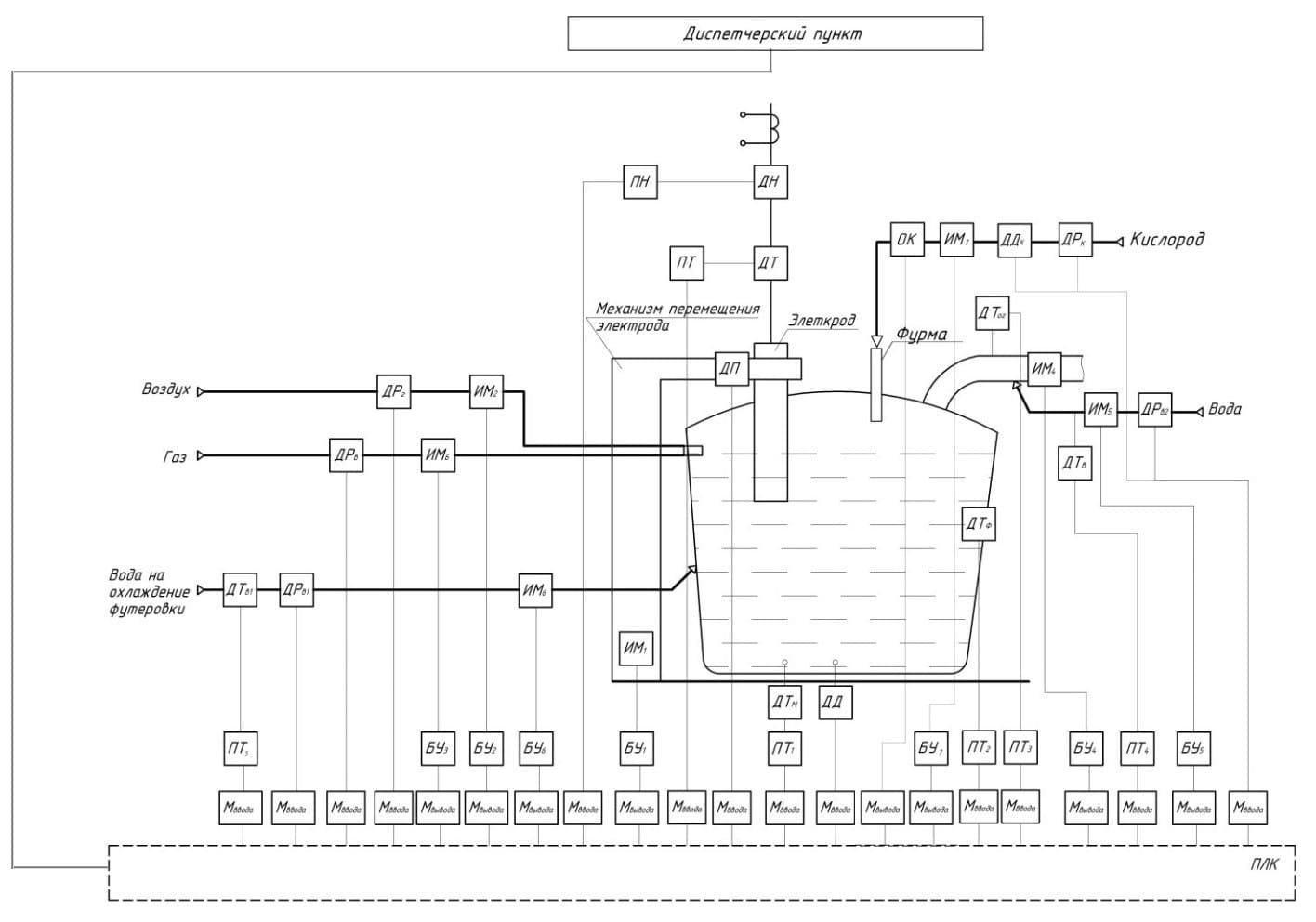
Рисунок 3.5 – Структурная схема системы автоматического управления ДСП
Величина рабочего тока в каждой фазе при выбранной ступени напряжения питания зависит от длины дуги. Управление величиной рабочего тока осуществляется путем перемещения электрода, контроль над которым устанавливается датчиком положения, а также необходимо снимать показания с первичных устройств датчика тока и напряжения.
Вся информация, собранная с первичных устройств (датчиков), направляется на контроллерный уровень, представленная аналоговыми унифицированными токовыми сигналами 4-20мА. Для управления исполнительными механизмами следует использовать аналоговый унифицированный сигнал 4-20 мА. Для связи ПЛК с верхним (диспетчерским) уровнем используются витые пары Ethernet.
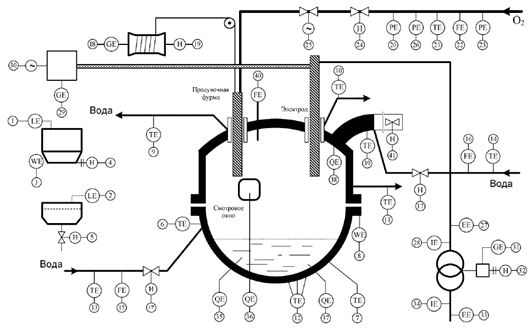
Рисунок 3.6 – Функциональная схема системы автоматизации ДСП
Выводы
Был рассмотрен технологический процесс выплавки стали в электродугосталеплавильной печи как объект автоматизации. Разработана структурная и функциональная схемы системы автоматизации, а также алгоритм управления технологическим режимом электродугосталеплавильной печи.
При написании данного реферата магистерская работа еще не завершена. Окончательное завершение: июнь 2023 года. Полный текст работы и материалы по теме могут быть получены у автора или его руководителя после указанной даты.
Список литературы
- Сведчанский, А.Д. Электрические промышленные печи: Дуговые печи и установки специального нагрева: учебник для вузов. / А.Д. Сведчанский, И.Т. Жердев, А.М. Кручинин – 2-е изд., перераб. и доп. – М.: Энергоиздат, 1981. – 296 с.: ил., табл.
- Поволоцкий, Д.Я. Электрометаллургия стали и ферросплавов. / Д.Я. Поволоцкий – М.: «Металлургия», 1978. – 550с.
- Окороков, Н. В. Электроплавильные печи черной металлургии. / Н.В.Окороков – М.: Металлургия, 2005. – 220 с.
- Марков, Н.А. Электрические печи и режимы дуговых электропечных установок. / Н.А. Марков. – М.: Энергия, 2003. – 204 с.
- Пирожников, В.Е. Автоматизация контроля и управления электросталеплавильными установками / В.Е. Пирожников, А.Ф. Каблуковский – М.: «Металлургия», 1974. – 208 с.: ил., табл.
- Лапшин, И.В. Автоматизация дуговых печей. / И.В. Лапшин – Москва, 2004. – 166 с.
- Глинков, Г.М. АСУ ТП в черной металлургии: учебник для вузов. / Г.М. Глинков, В.А. Маковский – 2-е изд., перераб. и доп. – М.: «Металлургия», 1999. – 310 с.
- Глинков, Г.М. АСУ технологическими процессами в агломерационных и сталеплавильных цехах: учебник для вузов. / Г.М. Глинков, В.А. Маковский – М.: «Металлургия», 1981. –360 с.: ил., табл.
- Кисаримов, Р.А. Электропривод: справочник. / Р.А. Кисаримов, Москва, ИП РадиоСофт, 2008.- 391 с.
- Терехов, В.М. Системы управления электроприводов: учебник для студ. высш. учеб. заведений / В.М. Терехов, О.И. Осипов; под ред. В.М. Терехова. - 2-е изд., стер. - М.: Издательский центр «Академия», 2006. - 304 с.