Реферат за темою випускної роботи
Зміст
- Вступ
- 1. Актуальність теми
- 2. Мета і задачі дослідження та заплановані результати
- 3. Огляд досліджень та розробок
- 3.1 технологічний виплавки сталі в електро дугосталеплавильної печі як об'єкт автоматизації
- 3.2 Розробка алгоритму роботи і схемних рішень системи автоматичного управління технологічним режимом електродугосталеплавильної печі
- Висновки
- Перелік посилань
Вступ
На сьогоднішній день електродугові печі вважаються найпоширенішими і екологічно чистими агрегатами для виплавки сталі. Можливість зосередженого введення значної кількості теплової енергії в поєднанні з простотою управління підводиться електричною потужністю є незаперечною перевагою дугових сталеплавильних печей в порівнянні з іншими агрегатами для виробництва сталі.
1. Актуальність теми
Зниження витрат на обслуговування і продовження міжремонтного терміну, а також спрощення діагностики неполадок в сукупності з підвищенням надійності і економічності, дозволяє говорити про значний економічний ефект, який пов'язаний із застосуванням пропонованих в роботі методів і засобів автоматизації в порівнянні з традиційно застосовуваними на розглянутому технологічному об'єкті – електродугосталеплавильної печі.
Саме тому дослідження і проектування системи автоматизації процесів виплавки сталі в електродугосталеплавильної печі є актуальною темою в даний час.
2. Мета і задачі дослідження та заплановані результати
Мета дослідження-підвищення ефективності функціонування електродугосталеплавильної печі за рахунок розробки системи автоматичного управління, що дозволить поліпшити якість виробленої продукції при економії матеріальних і енергетичних ресурсів.
Основні завдання дослідження:
- Аналіз технологічного процесу виплавки сталі в електросталеплавильній печі як об'єкта автоматизації.
- Розробка структурної та функціональної схем системи автоматизації.
- Розробка алгоритму управління технологічним режимом електро дугосталеплавильної печі.
3. Огляд досліджень та розробок
3.1 технологічний виплавки сталі в електро дугосталеплавильної печі як об'єкт автоматизації
Головною метою управління процесом плавки в електродугосталеплавильної печі є отримання металу заданого складу і заданої температури при високопродуктивній і економічній роботі агрегату. Ця мета може бути досягнута при успішному вирішенні системою управління наступних завдань:
- узгодженої зміни параметрів плавильного процесу, тобто температури і складу металу і шлаку із забезпеченням заданих кінцевих значень параметрів на випуску;
- підтримки раціонального і економічного електричного режиму печі;
- запобігання перегріву і руйнування футеровки та інших конструктивних елементів печі.
Підвищити ефективності процесу виплавки сталі в електродугосталеплавильної печі можна шляхом створення сучасної системи автоматичного управління, оновленням апаратного забезпечення. Основними завданнями автоматичного управління процесом плавки в електродугосталеплавильної печі є:
- Централізований контроль технологічного процесу і роботи печі з видачею оперативної інформації обслуговуючому піч персоналу з реєстрацією і сигналізацією відхилень від заданих значень основних параметрів.
- Управління технологічним процесом-розрахунок оптимального складу шихти; управління завантаженням шихти відповідно до розрахованим складом; Розрахунок кількості кисню, легуючих і шлакоутворюючих матеріалів, що забезпечують отримання металу заданого складу і якості та економію матеріалів; управління подачею легуючих і шлакоутворюючих матеріалів; управління подачею кисню в ванну; прогнозування моменту закінчення технологічних періодів плавки.
- Управління енергетичним режимом, що забезпечує максимальне використання потужності печі, мінімальний витрата електроенергії і нормальну експлуатацію печі та її електричного обладнання – управління тепловим режимом, управління електричним режимом, управління газокисневими пальниками, управління відведенням газів, що відходять з печі.
- Управління допоміжними операціями-відбором проб металу, виміром температури металу та ін.
- Збір і відбирання інформації з видачею необхідної документації – облік і реєстрація витрат шихтових матеріалів, легуючих, електроенергії, кисню; друкування протоколів плавки та ін.
- Контроль за роботою обладнання з сигналізацією і реєстрацією несправностей.
Сучасні АСУ ТП стали розробляються на основі класичної трирівневої моделі побудови архітектури системи:
- нижній-польовий рівень (датчики);
- середній-рівень базової автоматизації процесів виробництва (Керуючі контролери);
- верхній-рівень управління технологією.
На нижньому рівні знаходиться Польове обладнання: датчики, виконавчі механізми та їх вторинні прилади, щити станцій управління. У завдання обладнання цього рівня входить вимірювання фізичних параметрів і їх перетворення в стандартні типи електричних сигналів, отримання керуючих сигналів від обладнання середнього рівня (контролери) і безпосереднє управління технологічним обладнанням відповідно до цих сигналів.
Рівень управління створюється із застосуванням високопродуктивних програмованих логічних контролерів з розподіленою системою введення-виведення.
Перші два рівня проектуються з використанням сучасних програмно-технічних засобів від провідних зарубіжних і вітчизняних виробників компонентів АСУ ТП (Siemens, Schneider Electric, Bernecker&Rainer, ABB, Omron і ін.), системи контролю і диспетчерського управління (SCADA-системи) розробляються на основі програмних продуктів Siemens WinCC, Schneider Vijeo Citect, WonderWare InTouch, Bernecker&Rainer і ін.
Для автоматизації ДСП - 150 конструкції фірми Siemens VAI (Німеччина) використовувалася системна платформа ПЛК для управління технологічними процесами всього сталеплавильного цеху в цілому-SIEMENS SIMATIC S7 (рис. 3.1).
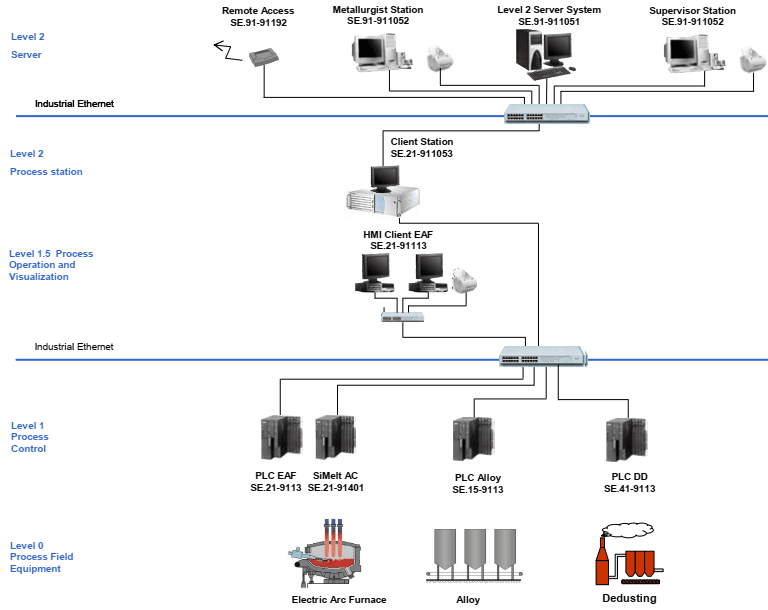
Малюнок 3.1 - Структурна схема автоматизації ДСП-150
Рівень системи автоматизації здатний керувати обладнанням без будь-якої іншої системи вищого рівня. АСУ ТП включає наступні компоненти в міру того, наскільки вони вказані в специфікації обсягу поставки:
- людино-машинний інтерфейс (ЧМІ);
- програмовані логічні контролери (ПЛК);
- ваговимірювальне обладнання;
- спеціальні вузли на базі мікропроцесорної техніки;
- пульт і / або панелі в посту (постах) управління
Система рівня 1 охоплює всі необхідні функції для керування обладнанням у ручному та/або автоматичному режимі. Передача даних між системою рівня 1 і системами більш високих рівнів забезпечується або через систему шин, або через стандартні послідовні канали зв'язку.
Ручне управління окремими агрегатами або групами агрегатів (старт/стоп) або ручна настройка клапанів, дросельних заслінок, виконавчих органів і т.д. проводиться з пультів або панелей управління в посту (постах) управління. У цьому режимі роботи функціонують тільки основні блокувальні функції для попередження небезпеки для експлуатаційного персоналу і механічного обладнання.
Автоматичний режим передбачається функції управління без зворотного зв'язку та / або зі зворотним зв'язком і управління обладнанням з усіма блокуваннями через ЧМІ (наприклад, ручна настройка уставок) і традиційні елементи управління в міру необхідності для управління обладнанням.
Мета функціонування дугової сталеплавильної печі-отримання металу температурою 1620ос ±20оС з необхідним складом і необхідної якості [1,3].
Виплавка сталі в ДСП включає в себе наступні технологічні операції [1,3,4]: підготовка печі до завалки; завалка; розплавлення; доведення; випуск плавки.
У шихтовом прольоті ЕСПЦ здійснюється завантаження металевої шихти в кошики (Бадді) і за допомогою мостового крана доставляється в пічної проліт ЕСПЦ, де проводиться її завалка в дугову сталеплавильну піч. Виплавка сталі починається з завалки металевої шихти на» болото", що залишилася від попередньої плавки частини рідкого металу в кількості 15 т.на дно завантажувальної Бадді укладають легковагий лом, потім розміщується великоваговий лом. Ближче до стінок Бадді завантажуються шлакоутворюючі добавки. Кокс укладають поверх шару великовагового брухту і вапна для запобігання поломок електродів при контакті з струмопровідними матеріалами. Потім на середній лом кладуть шар легковагого брухту для швидкого проплавлення колодязів. Щільна укладання металевої шихти забезпечує її хорошу провідність. У разі неможливості завантаження коксу або шлакоутворюючих в баддю їх засипку в ДСП виробляють під час розплавлення завалки.
Виплавка сталі здійснюється в автоматичному режимі, при впливі теплового впливу. Перетворення електричної енергії в теплову відбувається при виникненні електричної дуги, яка представляє собою один з видів дугового розряду, що виникає між графітованими електродами. Саме величина струму дуги і відстань між електродами визначають швидкість плавки металу. Після закінчення завалки і установки зводу ДСП в робоче положення, електроди опускають майже до торкання з шихтою і включають піч. Між електродами і шихтою спалахують електричні дуги, під впливом випромінювання яких, металева шихта починає плавитися під електродами і рідкий метал стікає вниз. Для прискорення плавлення брухту в холодних місцях робочого простору і отримання активної по всій поверхні шлакової ванни, використовують додаткову енергію газокисневих пальників, витрата газу і кисню на пальник приймають у співвідношенні 1:2. Пальники включають відразу після завалки, при роботі стінових газокисневих пальників, також здійснюють ДонНУ продувку аргоном для підвищення якості металу.
Витрата електроенергії в період плавлення дорівнює 370 кВт·год/т.при роботі ДСП необхідно підтримувати постійну електричну дугу. Для цього необхідно організувати належну провідність між електродом і шихтою. Досягається необхідний рівень провідності за рахунок зміни положення (переміщення) електродів по вертикалі, або зміною напруги на них, для підтримки дуги подається напруга від 100 до 600 В і струм 50-100 кА. Електроди поступово переміщаються і опускаються в утворюються під ними в шихті «колодязі». У процесі плавлення контролюється температура води на панелях склепіння.
У момент інтенсивного шлакоутворення і сходу шлаку з печі температура металу повинна бути 1550ос, що дозволяє отримати найкращі умови дефосфорації металу. Для Сходу шлаку корпус ДСП нахиляють в сторону робочого майданчика матеріалів приблизно на 5о. Видалення шлаку здійснюється через робоче вікно ДСП. З метою недопущення переокислення ванни під час роботи кисневих фурм і продування ванни киснем, подача вуглевмісного матеріалу є обов'язковим. У момент повного розплавлення металевої шихти термопарою вимірюють температуру металу і здійснюють відбір проб занурювальним пробовідбірником. Отримавши попередню інформацію про хімічний склад металу, продовжують окислення домішок в металі продувкою ванни ДСП киснем через кисневу фурму.
Процес плавки сталі в ДСП, а також попередні і наступні за ним стадії даного технологічного процесу, супроводжуються істотними виділеннями пилу. Видалення пічних газів з ДСП здійснюється через водоохлождаемый газохід і систему газоочистки з рукавними фільтрами. Випуск готового металу здійснюється через зливний жолоб. Весь процес управління дугової сталеплавильної піччю і її елементами, підрозділяється на управління технологічним режимом і управління тепловим режимом [5,6]. Оскільки в електросталеплавильному технологічному процесі в ДСП основна частина тепла виходить в результаті перетворення електричної енергії, то виникає необхідність управляти кількістю надходить тепла, тобто електричним режимом, а якщо точніше – електричною потужністю ДСП [6,7].
Виконаний вище аналіз особливостей процесу виплавки сталі дозволив скласти структурну схему матеріальних потоків ДСП, яка наведена на рис. 3.2.
Як випливає зі схеми матеріальних потоків ДСП (рис.3.2) і виконаного вище аналізу технологічних процесів, що протікають в ній, електросталеплавильна піч є складним, багатовимірним, багатозв'язним об'єктом управління, що складається з великої кількості технологічних елементів. Першим і основним технологічним елементом і процесом, без нормального функціонування якого неможливо уявити роботу ДСП в принципі, є процес отримання теплової енергії з електричної за рахунок необхідного підтримки довжини електричної дуги на різних етапах процесу плавки. Як було описано вище, це є основним процесом при управлінні ДСП – управління тепловим режимом ДСП, який зводиться до управління електричним режимом, а точніше – електричною потужністю ДСП, як правило, за рахунок зміни довжини дуги [6,7].
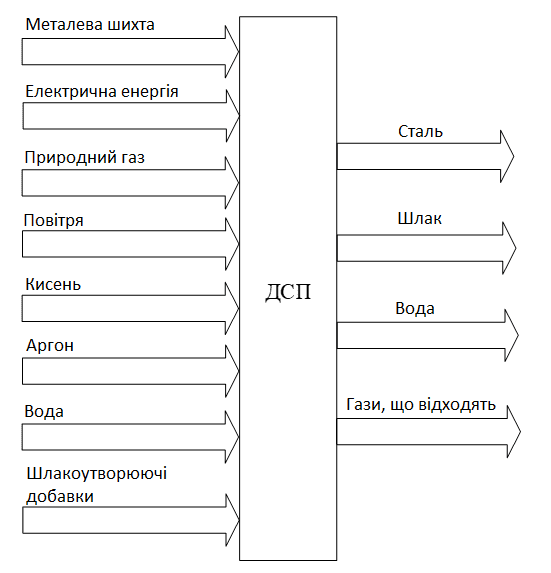
Малюнок 3.2 - Структурна схема матеріальних потоків ДСП
Наступним технологічним елементом ДСП, що визначає ефективність і економічність, процесу виплавки сталі є киснева фурма. Нормальне функціонування кисневої фурми визначається підтриманням необхідних параметрів процесу подачі кисню і процесу її охолодження. Процес подачі кисню в робочий простір ДСП характеризується необхідною витратою кисню на продування при підтримці необхідного його тиску. Відхилення витрати і тиску кисню від необхідних значень призводить до підвищення експлуатаційних витрат на процес виробництва сталі в ДСП або до погіршення якості одержуваної сталі. При охолодженні фурми необхідно змінювати витрату охолоджуючої води для підтримки необхідної різниці температури на виході і вході кисневої фурми, що при відносно постійній температурі охолоджуючої води зводиться до підтримки заданої температури охолоджуючої води на виході з кисневої фурми [7,8].
Таким чином, на підставі схеми матеріальних потоків ДСП (рис.3.2) і розглянутих вище особливостей процесу переміщення електродів, процесу охолодження кисневої фурми, а також процесу подачі кисню, отримана схема дугового сталеплавильної печі для перерахованих елементів як об'єкта автоматичного управління, яка наведена на рис. 3.3.
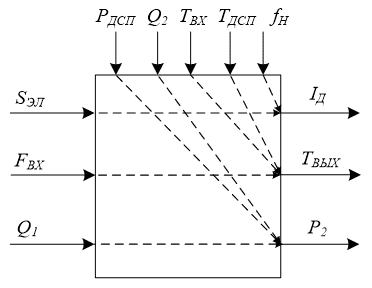
Малюнок 3.3 - ДСП як об'єкт автоматичного управління
Керованими змінними, що характеризують функціонування основних технологічних елементів і процесів, при виплавці сталі в ДСП, є (рис. 3.3):
- при управлінні потужністю ДСП-електричний струм дуги ІД;
- при управлінні охолодженням кисневої фурми-температура охолоджуючої води на виході фурми ТВИХ;
- при управлінні подачею кисню в фурму-тиск на вході в кисневу фурму (на виході подає кисень трубопроводу) Р2;
- Керуючими впливами, що дозволяють необхідним чином впливати на перераховані керовані змінні, є (рис. 3.3):
- при управлінні потужністю ДСП-переміщення електрода ЅЕЛ;
- при управлінні охолодженням кисневої фурми-витрата охолоджуючої води на вході в кисневу фурму FВХ;
- при управлінні подачею кисню в фурму-витрата кисню на виході керованої засувки (на вході подає трубопроводу) Q1;
Обурюючими впливами для розглянутих елементів ДСП, виступають (рис. 3.3):
- при управлінні потужністю ДСП – неконтрольовані збурення електричного режиму, що змінюють відстань між електродом і металевою шихтою fH (збурення електричного режиму виникають при обвалах металевої шихти в процесі плавлення; при кипінні металу; при обгоранні електродів; при підйомі рівня металу в міру його плавлення);
- при управлінні охолодженням кисневої фурми-температура охолоджуючої води на вході в кисневу фурму ТВХ і температура в робочій зоні ДСП ТДСП;
- при управлінні подачею кисню в фурму-витрата кисню, споживаний кисневою фурмою (на виході подає кисень трубопроводу) Q1 і тиск в робочій зоні ДСП РДСП;
Аналіз технологічної схеми, технічних особливостей, режимів роботи, засобів і систем автоматизації технологічних елементів і процесів ДСП дозволяє сформулювати мету – підвищення ефективності функціонування електродугосталеплавильної печі за рахунок розробки системи автоматичного управління, що дозволить поліпшити якість виробленої продукції при економії матеріальних і енергетичних ресурсів.
Сформулюємо вимоги до системи управління технологічним режимом електродугосталеплавильної печі на підставі моделі furps+, такі як: Functionality - функціональність; Usability - застосовність; Reliability - надійність; Performance - продуктивність; Supportability - придатність до експлуатації.
1. Функціональність:
- збір, первинна обробка, розподіл і формування масивів інформації, одержуваної від датчиків технологічних і енергетичних параметрів електродугосталеплавильної печі у вигляді аналогових, дискретних і цифрових сигналів;
- представлення інформації та взаємодія користувачів з програмно-технічним комплексом електродугосталеплавильної печі;
- дистанційне керування приводами обладнання та виконавчих механізмів електродугосталеплавильної печі;
- автоматичне, програмне управління електродугосталеплавильної піччю;
2. Безпека.
Електротехнічні вироби, використовувані в системі управління електродугосталеплавильної печі, повинні відповідати ГОСТ 12.2.007-75, а засоби обчислювальної техніки – по ГОСТ 25861-83, і мають клас 1 захисту людини від ураження електричним струмом. Всі зовнішні елементи ТЕХНІЧНИХ системи управління, що знаходяться під напругою, захищаються від випадкового дотику;
3. Застосовність.
Робоче місце оператора системи управління електродугосталеплавильної піччю повинно містити кілька робочих станцій, які призначені для:
- представлення, зберігання та обробки технологічної інформації;
- виконання функція і завдань розрахункового характеру;
- реалізація загальносистемних функцій;
4. Надійність.
Програмно-технічний комплекс електродугосталеплавильної печі в частині вимог по надійності повинен відповідати ГОСТ 4.148-85, ГОСТ 24.701-86 і ГОСТ 27.003-90.
5. Продуктивність
.Показники швидкодії, часу відгуку, точності і достовірності інформації повинні бути не гірше існуючих аналогів.
6. Придатність до експлуатації.
Придатність до експлуатації характеризується:
- робоча температура навколишнього середовища 5-50 ° C;
- гранична температура 0-100 ° з;
- відносна вологість повітря 30-75% при температурі 25 ° з;
7. Вимоги по масі, габаритам і ступеня захищеності корпусу.
Вузли САУ повинні бути виробами заводського виготовлення з типовими або проектно-компонованими тактико-технічними, метрологічними і масогабаритними характеристиками.
За ступенем захисту від впливу навколишнього середовища:
- приладові шафи КП ТМ - не нижче IP55 (IP65);
- пульт управління - не нижче IP21;
- шафа серверного обладнання - не нижче IP21;
3.2 Розробка алгоритму роботи і схемних рішень системи автоматичного управління технологічним режимом електродугосталеплавильної печі.
Управление электрическим режимом печи электро дугосталеплавильной печи разделяют на несколько стадий (рис. 3.4):
- Заглубление электродов в шихту.
- Проплавление колодцев.
- Плавка металла.
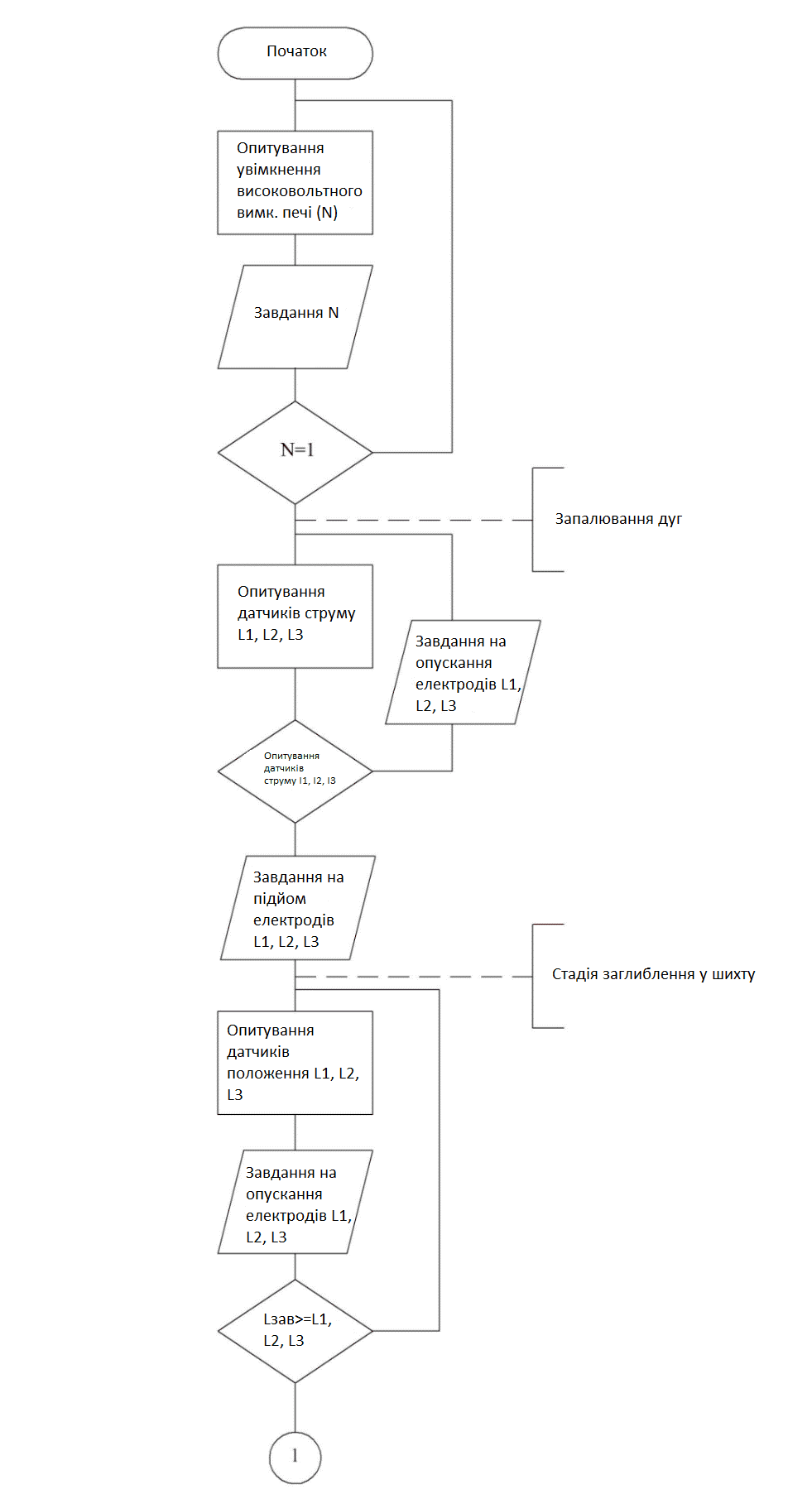
Рисунок 3.4-Блок-схема алгоритму керування технологічними режимами електродугосталеплавильної печі
Перед стадією заглиблення електродів в шихту, відбувається запалювання дуг печі. Диференційний спосіб регулювання забезпечує автоматичне запалювання дуг. Після включення печі при відсутності струму електрод опускається вниз, до моменту торкання з металом. При появі на датчику струму сигналу, перший електрод зупиняється. Починає опускатися другий електрод, при торканні металом другим електродом обидва електроди піднімаються вгору, запалюючи дуги. А третій електрод опускається вниз до торкання з металом, після появи в ньому струму, почне підніматися, запалюючи третю дугу.
Перша стадія заглиблення електродів в шихту. У момент запалювання дуги фіксується поточне положення електродів. Програмно задається значення заглиблення електродів, коли поточне значення заглиблення електродів досягне заданого, система управління переходить в наступний режим – проплавлення колодязів.
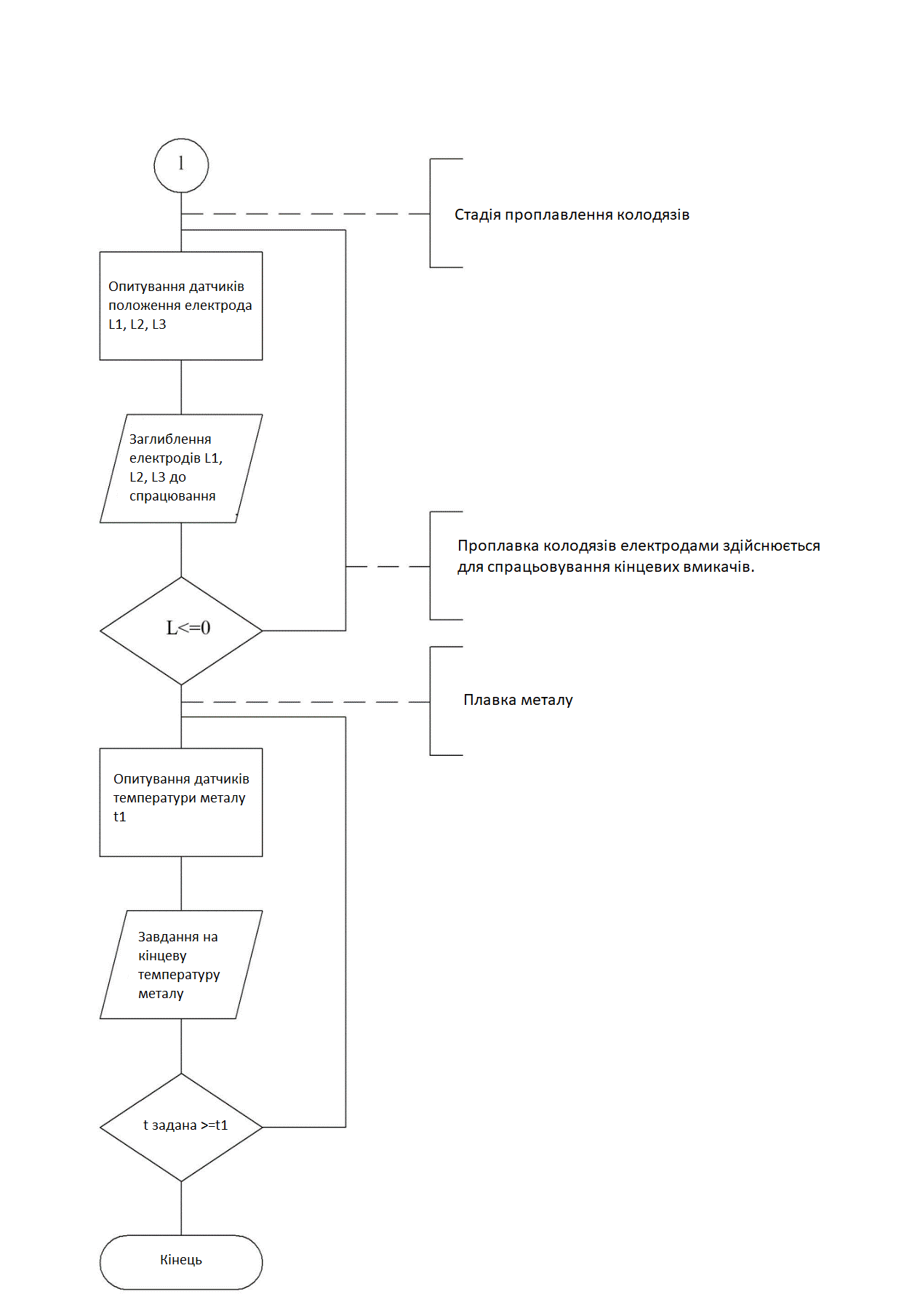
Продовження рисунка 3.4-Блок-схема алгоритму керування технологічними режимами електро дугосталеплавильної печі
Стадія проплавлення колодязів. У цій стадії електроди проходять колодязь швидко, при цьому утворюється рідкий метал. Для обмеження переміщення електродів в крайнє положення передбачені кінцеві вимикачі. Сигнал про відсутність руху електродів, буде свідчити про завершення періоду проплавлення колодязів, і переході в стадію плавки металу.
Стадія плавки металу проходить на введенні максимальної потужності в піч. Завершується дана стадія в період, коли температура металу досягає заданого програмного значення.
Проектована система автоматизації за своєю структурою представляє розподілену автоматизовану систему управління. Застосовуючи сучасні принципи побудови, можна визначити наступну структуру системи автоматизації (рис. 3.5):
- диспетчерський рівень-відповідає за збір, обробку даних і відображення технологічного процесу;
- рівень контролерів і модулів введення / виведення, на даному рівні буде здійснюватися збір і обробка первинної інформації з самого нижнього рівня;
- рівень датчиків і виконавчих механізмів, на цьому рівні здійснюється узгодження сигналів датчиків з входами пристрою управління, а виробляються команд з виконавчими механізмами.
Для проектованої системи автоматизації необхідно встановити первинні датчики вимірювання температури футеровки і кладки днища, вимірювання температури рідкого металу. Датчик вимірювання температури охолоджуючої води в трубопроводі, використовуваної для охолодження елементів печі, а також вимірювання температури на зливі з водоохлаждаемой панелі, по різниці температур на вході і виході яких, можна судити про інтенсивність охолоджувача, і відповідно регулювати витрату охолоджуючої води за допомогою виконавчого механізму з заслінкою, а також датчик температури газів, що відходять.
Для системи автоматизації необхідно здійснити контроль витрати кисню на фурму, за допомогою датчиків тиску і витрати, а також здійснити управління витратою на фурму за допомогою виконавчого механізму і встановити відсічний клапан, з метою запобігання аварійних ситуацій.
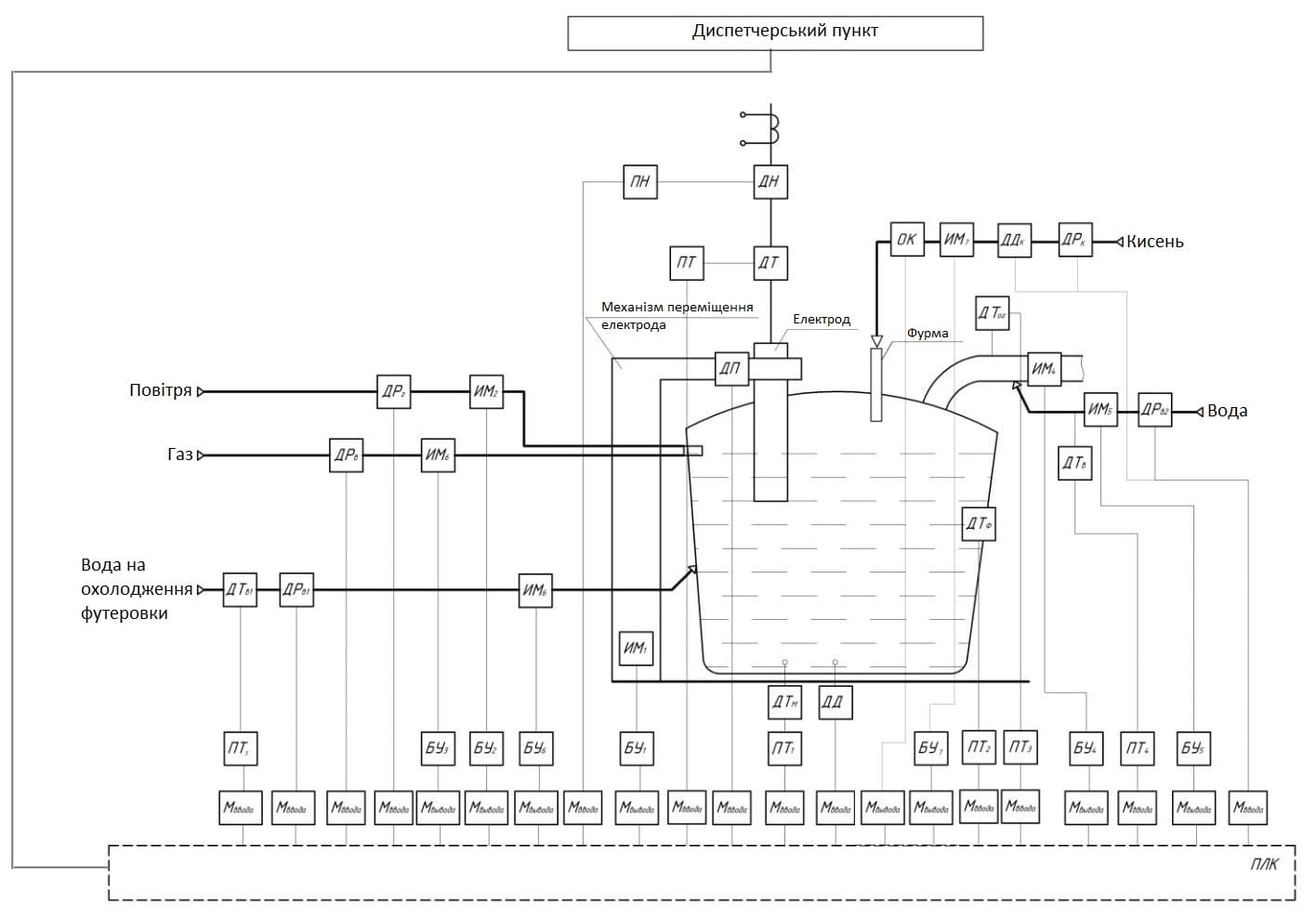
Малюнок 3.5-Структурна схема системи автоматичного управління ДСП
Величина робочого струму в кожній фазі при обраній ступені напруги живлення залежить від довжини дуги. Управління величиною робочого струму здійснюється шляхом переміщення електрода, контроль над яким встановлюється датчиком положення, а також необхідно знімати показання з первинних пристроїв датчика струму і напруги.
Вся інформація, зібрана з первинних пристроїв (датчиків), направляється на контролерний рівень, представлена аналоговими уніфікованими струмовими сигналами 4-20мА. Для управління виконавчими механізмами слід використовувати Аналоговий уніфікований сигнал 4-20 мА. Для зв'язку ПЛК з верхнім (диспетчерським) рівнем використовуються кручені пари Ethernet.
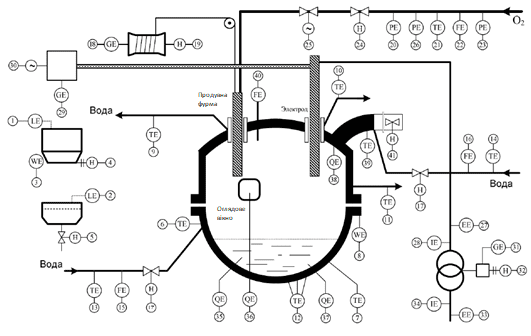
Малюнок 3.6-Функціональна схема системи автоматизації ДСП
Висновки
Було розглянуто технологічний процес виплавки сталі в електро дугосталеплавильній печі як об'єкт автоматизації. Розроблено структурну та функціональну схеми системи автоматизації, а також алгоритм управління технологічним режимом електродугосталеплавильної печі.
При написанні даного реферату магістерська робота ще не завершена. Остаточне завершення: Червень 2023 року. Повний текст роботи і матеріали по темі можуть бути отримані у автора або його керівника після зазначеної дати.
Перелік посилань
- Сведчанский, А.Д. Электрические промышленные печи: Дуговые печи и установки специального нагрева: учебник для вузов. / А.Д. Сведчанский, И.Т. Жердев, А.М. Кручинин – 2-е изд., перераб. и доп. – М.: Энергоиздат, 1981. – 296 с.: ил., табл.
- Поволоцкий, Д.Я. Электрометаллургия стали и ферросплавов. / Д.Я. Поволоцкий – М.: «Металлургия», 1978. – 550с.
- Окороков, Н. В. Электроплавильные печи черной металлургии. / Н.В.Окороков – М.: Металлургия, 2005. – 220 с.
- Марков, Н.А. Электрические печи и режимы дуговых электропечных установок. / Н.А. Марков. – М.: Энергия, 2003. – 204 с.
- Пирожников, В.Е. Автоматизация контроля и управления электросталеплавильными установками / В.Е. Пирожников, А.Ф. Каблуковский – М.: «Металлургия», 1974. – 208 с.: ил., табл.
- Лапшин, И.В. Автоматизация дуговых печей. / И.В. Лапшин – Москва, 2004. – 166 с.
- Глинков, Г.М. АСУ ТП в черной металлургии: учебник для вузов. / Г.М. Глинков, В.А. Маковский – 2-е изд., перераб. и доп. – М.: «Металлургия», 1999. – 310 с.
- Глинков, Г.М. АСУ технологическими процессами в агломерационных и сталеплавильных цехах: учебник для вузов. / Г.М. Глинков, В.А. Маковский – М.: «Металлургия», 1981. –360 с.: ил., табл.
- Кисаримов, Р.А. Электропривод: справочник. / Р.А. Кисаримов, Москва, ИП РадиоСофт, 2008.- 391 с.
- Терехов, В.М. Системы управления электроприводов: учебник для студ. высш. учеб. заведений / В.М. Терехов, О.И. Осипов; под ред. В.М. Терехова. - 2-е изд., стер. - М.: Издательский центр «Академия», 2006. - 304 с.