Реферат по теме выпускной работы
Содержание
- Введение
- 1. Актуальность темы
- 2. Цель и задачи исследования, планируемые результаты
- 3. Обзор исследований и разработок
- 3.1 Анализ технологического процесса загрузки доменной печи как объекта автоматизации
- 3.2 Доменной печи как объект автомаматического управления
- 3.3 Анализ существующих разработок по автоматизации загрузки доменной печи
- 3.4 Обоснование направления автоматизации загрузки доменной печи
- 3.5 Алгоритмизация работы и схемных решений системы автоматического контроля загрузки доменной печи
- Выводы
- Список источников
Введение
Системы контроля и управления работой доменных печей постепенно усложнялись - от простейших систем стабилизации отдельных параметров до локальных систем управления отдельными режимами работы печи и наконец, до комплексных систем управления всем доменным процессом.
Для решения данной проблемы необходимо обеспечить своевременное информирование о давлении доменного гада в колошниковой системе перед загрузкой загрузкой доменной печи. Полноценное решение задачи эффективного сброса давления стало возможным с массовым распределение высоконадежных программируемых логических контроллеров.
1. Актуальность темы
Внедрение автоматического системы управления загрузки колошникового устройства доменной печи на базе ПЛК позволило увеличить реальную производительность при одновременном снижении себестоимости, так как автоматическая система может функционировать непрерывно в режиме реального времени.
2. Цель и задачи исследования, планируемые результаты
Цель исследования – повышение эффективности функционирования колошникового устройства доменной печи за счет разработки системы автоматического управления, что позволяет улучшить качество загрузки шихтовых материалов при экономии материалов и энергетических ресурсов.
Основные задачи исследования:
- Анализ технологического процесса загрузки доменной печи как объекта автоматизации.
- Разработка структурной и функциональной схем системы автоматизации.
- Разработка алгоритма управления технологическим режимом загрузки доменной печи.
3. Обзор исследований и разработок
3.1 Анализ технологического процесса загрузки доменной печи как объекта автоматизации
Колошниковое устройство представляет собой многоэтажную металлическую конструкцию, служащую для поддержания комплекса механизмов, предназначенных для загрузки шихты в доменную печи (засыпной аппарат и др.), отвода газов (газоотводы) и для монтажа оборудования.
Газоотводы. Для отвода доменного газа в куполе печи имеются отверстия и идущие от них вверх газоотводы. Обычно число газоотводов равно четырем, их соединяют вначале симметрично попарно, а затем в один газоход, идущий вниз к пылеуловителям, расположенным на нулевой отметке (на печах объемом 5000—5500 м3 имеется восемь газоотводов и по два нисходящих газохода). От верхних точек газоотводов отходят вер-тикальные свечи (трубы), заканчивающиеся атмосферным клапаном, который открывается, выпуская газ в атмосферу при превышении давления в печи сверх допустимого. Число свечей с клапанами колеблется от двух до четырех, они служат также для выпуска газа при остановках печи.
Засыпной аппарат. Он предназначен для загрузки шихты, необходимого ее распределения по сечению колошника, т.е. печи и для обеспечения герметичности печи в процессе загрузки, т.е. для предотвращения попадания в печь воздуха, ведущего к возможности взрыва, и предотвращения выделения печного газа в атмосферу.
Большая часть доменных печей оборудована двухконусными засыпными аппаратами, а новые печи сооружают с засыпными аппаратами новой конструкции - бесконусными. Двухконусный засыпной аппарат показан на рисунке 1. Его основными элементами являются: большой конус 1 с воронкой (чашей) 2; вращающийся распределитель шихты, состоящий из малого конуса 4 и воронки 10; приемная воронка 6. Большой и малый конусы могут перемещаться вверх—вниз; в верхнем положении большой конус прижат к воронке 2, а малый к воронке 10, изолируя рабочее пространство печи от атмосферы; по-ложение конусов в опущенном состоянии показано пунктиром. Малый конус подвешен на полой трубчатой штанге 5, большой - на штанге 3, проходящей внутри полой штанги 5, благодаря чему конусы могут опускаться и подниматься независимо друг от друга. Воронка 10 связана с приводом, обеспечивающим ее вращение вместе с малым конусом.
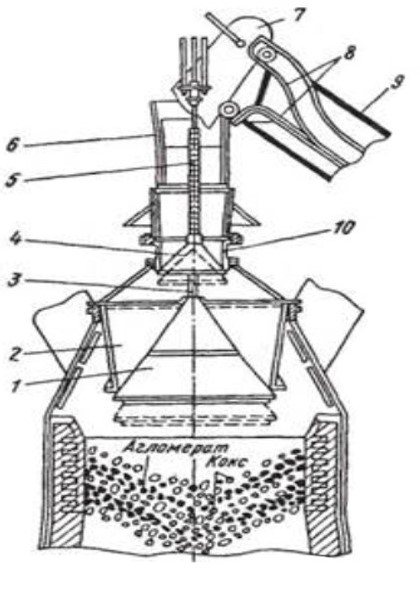
Рисунок 1 – Засыпной аппарат двухконусный
Шихтовые материалы доставляют на колошник двумя скипами (тележками), движущимися по рельсам 8 наклонного моста 9; в крайнем верхнем положении скип 7 опрокидывается, поскольку его передние колеса катятся по рельсам, загнутым вниз, а задние — по другим рельсам, загнутым вверх и поднимающим заднюю часть скипа При этом порция шихты высыпается через приемную воронку на поверхность малого конуса, после чего он опускается и материал просыпается вниз на поверхность большого конуса, а малый конус сразу же поднимается. Подобным образом на поверхность большого конуса загружают два—шесть скипов (набирают подачу). Затем при поднятом малом конусе опускают большой конус, и материал подачи просыпается в печь, после чего большой конус поднимается.
Далее на большой конус набирают новую подачу (два—шесть скипов), но перед каждым опусканием малого конуса он с воронкой 10 поворачивается на 60°. Загрузив эту подачу в печь путем опускания и подъема большого конуса, на него набирают следующую подачу; при этом перед каждым опусканием малого конуса он с воронкой поворачивается на 120° от исходного положения. При наборе после-дующей подачи угол поворота составляет 180° и т.д. Благодаря такому вращению распределителя подачи попадают не в одно место под наклонным мостом 9, а сравнительно равномерно распределяются по периферии колошника.
В процессе загрузки конусы работают поочередно: когда один опущен, другой поднят (закрыт), что обеспечивает герметичность печи.
После опускания малого конуса в межконусном пространстве создается давление, соответствующее атмосферному, а большой конус находится под давлением газов в печи, что препятствует его опусканию. После же опускания большого конуса, в межконусном пространстве создается давление, равное давлению газов в печи, что препятствует открытию малого конуса. Для выравнивания давления в межконусном пространстве и печи подают чистый газ в межконусное пространство под давлением, близким к давлению газов в печи. Это делают перед опусканием большого конуса при помощи уравнительных клапанов, а при опускании малого конуса сбрасывающий клапан выпускает газ из межконусного пространства в атмосферу. Работа уравнительных клапанов автоматизирована и сблокирована с работой конусов засыпного аппарата.
Слабым местом аппарата являются стыки конусов с соот-ветствующими воронками. Здесь в связи с повышенным давлением в печи просачивается доменный газ, и содержащаяся в нем пыль вызывает абразивный износ металла. Поэтому стойкость конусов низкая, малый; конус заменяют почти через каждые полгода, а большой через 1,5-2,5 г.
3.2 Доменной печи как объект автомаматического управления
Цель проектирования, разработка системы автоматического контроля загрузки доменной печи, за счет современно аппаратуры автоматизации на базе ПЛК – программируемого логического контроллера, а именно ПЛК63. Который позволяет увеличить работоспособность, надежность. Замена приведет к лучшему функционированию системы в целом.
Требования к устройству автоматического контроля загрузки доменной печи без участия обслуживаемого персонала:
- регулирование вела шихтового материала 4-8 т;
- регулирование объёма шихтового материала 7300 м^3;
- дистанционное управление оператором с пульта;
- возможность передачи технологической информации по протоколу RS485, а также передачи информации состояния протекания процесса другим ПЛК;
- класс точности ПЛК 0,5/0,25;
- заменимость аппаратуры;
- световая и звуковая информация на пульте оператора;
- отображение состояния технологического процесса и оборудования на пульте оператора;
- отображения регулирования на пульте оператора;
- оперативное изменение настроек регулирования;
- быстрый выход из аварийной ситуации;
- повышение надежности и безопасности;
- корпус щитового крепления;
- габаритные размеры (ВхШхГ), (168х137х55) мм;
- пластиковый корпус, с степенью зашиты IP55;
Требования к показателям надёжности системы устанавливаются в соответствии с ГОСТ 24. 701-86. Показатели надежности системы должны быть не ниже следующих значений:
- для функций управлений - 30000 часов наработки на отказ;
- для функций контроля - 30000 часов наработки на отказ;
- для информационных функций - 15000 ч.
Средний срок службы технических средств должен быть не менее 10 лет.
3.3 Анализ существующих разработок по автоматизации загрузки доменной печи
Открытая архитектура – важная характеристика системы при интеграции АСУ в существующие на доменных печах системы управления и средства контроля. Широкая номенклатура промышленных контроллеров отечественного и зарубежного производства, применяемая в настоящее время при создании автоматизированных систем управления, в частности, доменных печей, определяет важность этой характеристики АСУ.
Подсистема верхнего уровня (АРМ оператора-технолога) разработана на базе SCADA-системы TRACE MODE 5.09 с использованием персонального компьютера промышленного исполнения. Подсистема среднего уровня (базовый уровень автоматизации) выполнена на базе ПЛК Modicon TCX Quantum с использованием распределенного ввода/вывода. Распределенные узлы ввода/вывода (DIO) объединены в локальную сеть с использованием сетевой технологии Modbus Plus. Нижний уровень – технические средства управления электроприводами и датчики КИП.
Связь по сети Modbus Plus контроллера Modicon с компьютером станции оператора – технолога осуществлена через ОРС Factory Server фирмы "Schneider Electric" с использованием адаптера сети, установленного на компьютере станции оператора-технолога. Частотно-регулируемый привод разработан на базе частотных преобразователей Altivar 66 фирмы "Schneider Electric"
Особенностью технической структуры АСУ является условное ее разбиение на постоянную и переменную части:
- постоянная часть – технические средства и датчики КИПиА, обеспечивающие управление собственно роторным распределителем, КК и контроль состояния механизмов РЗУ; является неотъемлемой частью АСУ;
- переменная часть – технические средства, обеспечивающие синхронизацию работы АСУ с верхней системой загрузки доменной печи и выполняющая, при необходимости, часть функций этой системы.
Для решения задачи определения веса материала, распределяемого на колошник доменной печи, использующий весоизмерительные датчики. Алгоритм построен на контроле затрат энергии при распределении материала, а также на контроле изменения запаса кинетической энергии при его выгрузке. Результаты внедрения АСУ на объекте подтвердили удовлетворительную точность этого метода при реализации различных режимов распределения материала в соответствии с заданной программой загрузки. Адаптация коэффициентов уравнений алгоритма распределения производится от подачи к подаче, что исключает эффект накопления ошибок в его расчетной части.
АРМ АСУ предоставляет возможность оператору, используя функциональную клавиатуру, по ходу технологического процесса дистанционно вызывать функции управления, включая изменение заданий на текущие параметры процесса, а также отображает технологический процесс загрузки в виде мнемосхем технологических узлов и механизмов, графиков изменения параметров и их настроек для осуществления связи оператора–технолога с процессом загрузки. Разработанный пакет визуализации процесса обеспечивает оперативное и представительное считывание информации с экранов монитора АРМ.
Инструментальная система Trace Mode, как известно, включает в себя два редактора:
- редактор базы каналов;
- редактор представления данных.
В редакторе базы каналов описывается конфигурация операторской станции, используемой в АСУ, настраиваются каналы связи с подключенным к ним ПЛК, задаются переменные и способы их обработки, создаются меню для вызова информации и управления, формируются отчеты, перечень переменных и т.д. Операторская станция (ОС) АРМ поддерживает работу через сеть Modbus Plus с ПЛК среднего уровня – Modicon TCX Quantum.
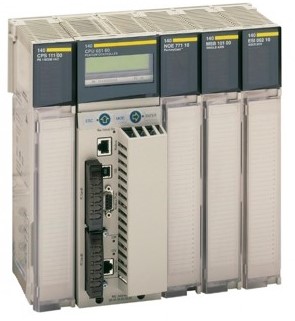
Рисунок 2 – Внешний вид программного контроллера Modicon TCX Quantum
Узел АРМ с использованием инструментальной системы на 1024 канала без автопостроения и два объекта. Один из объектов является совокупностью каналов, определяющих количество технологических переменных (аналоговых и дискретных), используемых в АСУ, другой – включает каналы, используемые для реализации собственных функций интерфейса оператора-технолога, включая уровень визуализации.
В каналах предусмотрена первичная и выходная обработка данных. Все остальные задачи по обработке данных и управлению разрабатываются в виде отдельных программ. Для этого предусмотрены два языка программирования в стандарте МЭК-61131: Техно FBD и Техно IL. Программы, созданные на языке FBD, могут вызываться из процедур каналов.
Количество входных/выходных сигналов АСУ достигает 160.
В действительности в системе количество каналов, используемых для технологических переменных и реализации собственных функций интерфейса оператора значительно больше, чем заявлено инструментальной системой, т.е. 1024. Использование глобальных переменных, определенных в Trace Modе, позволило эффективно решить задачу проектирования подсистемы верхнего уровня на базе инструментальной системы на 1024 вх/выхода.
Использование глобальных переменных особенно эффективно проявилось в режиме off-line работы системы при формировании циклов загрузки доменной печи. При этом общий цикл загрузки задается оператором на двадцать подач (максимально), каждая из которых состоит из шести скипов различного материала.
Всего в проекте создано около 1250 каналов, из них 310 - связаны с ОРС-сервером. В АСУ используется OPC Factory Server разработки фирмы Schneider Electric c локальным доступом. В этом применении ОРС-клиент и ОРС-сервер устанавливаются на одной станции, т.е. на компьютере АРМ.
Необходимо отметить эффективность программирования некоторых задач на языке FBD, который был использован для создания дополнительных элементов управления и визуализации и, главное, для улучшения динамики отображения сообщений на технологических экранах интерфейса оператора-технолога. Как известно, в TRACE MODE формирование сообщений осуществляется кодированием слов состояний без использования символьных переменных. При наличии большого количества сообщений с учетом задержки обработки и преобразования сигналов каналом ОРС запаздывание вывода на технологический экран сообщения становится недопустимо большим, что может привести к визуальной потере важной технологической информации.
В АСУ для снижения времени запаздывания вывода на экран сообщений на FBD блоках разработана программа обработки слов состояний с использованием блока логарифмирования слова состояния. При этом предварительно осуществляется проверка изменения слова состояния относительно предыдущего цикла его считывания. Такой подход позволил существенно снизить время запаздывания вывода сообщений на технологические экраны по ходу технологического процесса загрузки.
Основным требованием к организации структуры уровня визуализации при работе РЗУ являлась оперативность перехода на вызываемый технологический экран. Средства TRACE MODE позволили создать удобную систему технологических экранов, которые предварительно объединяются в функциональные группы, внутри которых формируются подгруппы, организованные во вспомогательные экраны.
Выход на любую функциональную группу осуществляется через основной экран "МНЕМОСХЕМА" рисунок 3. Далее с помощью соответствующих кнопок осуществляется выход на вспомогательные экраны.
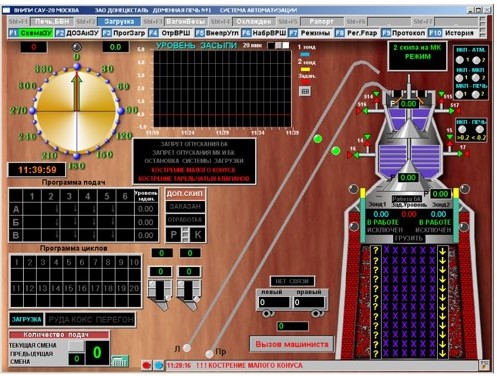
Рисунок 3 – Экранная форма мнемосхемы загрузки
Предусмотрен оперативный выход на основные экраны с помощью "горячих" клавиш клавиатуры. Технологический экран делится на рабочую и информационные зоны. Информационная зона располагается в верхней части экрана и содержит:
- наименование экрана;
- дату и время включения системы;
- строку сообщений, в которой указывается технологическое состояние переменной, тип механизма и режим его работы;
- дата и время формирования сообщения по данной переменной;
- кнопку перехода на просмотр отчета тревог;
- кнопку просмотра графического отображения переменной.
Режим "Работа" – режим работы, при котором осуществляются функции контроля и управления АСУ в реальном масштабе времени. При этом система осуществляет:
- "слежение" за состоянием механизмов верхней загрузки доменной печи с учетом необходимой последовательности работы механизмов.
- обрабатывает информацию и формирует управляющие сигналы на основании данных, полученных от датчиков технологического процесса и технического состояния основных узлов РЗУ;
- производит расчет и передачу сигналов управления на электропривод роторного распределителя в соответствии с заданным алгоритмом распределения шихтового материала на колошнике доменной печи.
В процессе выгрузки шихтового материала подсистема среднего уровня производит расчет количества материала, поступающего на колошник в единицу времени.
В режиме "Работа" осуществляется архивирование и формирование протоколов. Здесь полностью используются возможности TRACE MODE по архивированию и создания отчета тревог. Обновление данных в архиве осуществляется циклически. Данные в отчете тревог заносятся в виде отдельных строк, каждая из которых содержит время и дату ее формирования. Дополнительно в каждой строке указывается тип сообщений: аварийный, технологический, предупредительный либо системный, определяющий состояние КТС АСУ.
В АСУ предусмотрено "горячее" резервирование модуля центрального процессора (ЦПУ) 140 CPU 213 04 управляющего контроллера. Модули ЦПУ (основной и резервный) размещаются в шкафу контроллера на отдельных слотах и связаны с модулями узлов системы локальной сетью Modbus Plus (MB+). Программное обеспечение основного и резервного ЦПУ практически идентичны и отличаются лишь программными модулями MAIN и RESERV, определяющими статус ЦПУ: основной – MAIN, резервный – RESERV. Статус ЦПУ определяется при конфигурации системы.
При реализации резервирования используется особенность локальной сети МВ+, представляющей собой одноранговую сеть с последовательной передачей маркера сети к удаленным узлам системы и возможность использования Active X приложений в TRACE MODE.
"Резервный" ЦПУ постоянно находится в процессе считывания информации о состоянии модулей ввода/вывода системы при "захвате" маркера сети, т.е. работает также как и основной ЦПУ, и также формирует управляющие выходные сигналы. Однако при работе "основного" ЦПУ управляющие сигналы "резервного" отключены от линий связи, как от ОС, так и от узлов распределенного ввода/вывода. При обнаружении неисправности "основного" ЦПУ "резервный" ЦПУ имеет полную информацию о состоянии технологического процесса и автоматически подключается к процессу управления, отключая при этом неисправный ЦПУ. Время переключения составляет не более 2с, что для технологического процесса загрузки доменной печи является вполне приемлемым.
3.4 Обоснование направления автоматизации загрузки доменной печи
Основная проблема, которая существует на донецком металургичском заводе это использование устаревшей аппаратуры. ПЛК Schneider Electric, Siemens т.д. Использование несет риск о постепенном выходе из строя, невозможность найти аналогичную замену. Поэтому для построения системы автоматизации нужен ПЛК, который без проблем можно найти на рынке и для возможности покупки резерва для быстрого переключения между ними. Также выбор ПЛК как блок управления основывается на большом количестве параметров и модульности, узлы контроля и регулирования ПЛК основанный на центральном процессоре имеет нужную вычислительную мощность и справиться с системной автоматизацией.
Параметр, который отвечает за загрузку доменной печи который можно автоматизировать является регулирование расхода шихтового материала.
Засыпной аппарат состоит из двух конусов: большого и малого. При опускании материалов с малого конуса в межконусное пространство попадает воздух.
Перед опусканием малого конуса производиться замер уровня шихты с помочью уровнемера.
Для повышения надежности системы применяют сдвоенные сигнализаторы уравномер, константы которых включают последовательно. Такое усложнение обусловлено возможностью изгиба штанг конусов.
3.5 Алгоритмизация работы и схемных решений системы автоматического контроля загрузки доменной печи
Система автоматического контроля загрузки доменной печи включает программируемый логический контроллер ПЛК63 от компании ОВЕН, который взаимодействует с датчиками, получает информацию от объекта управления, обрабатывает ее в соответствии с заложенным алгоритмом и выдает управление воздействием на исполнительные устройства.
Применение микропроцессорных средств для реализации подсистемы технологических зашит и защитных блокировок дает следившие преимущества:
- возможности непрерывного контроля достоверности всей входной информации с сигнализацией и регистрацией неисправности отдельных датчиков или каналов связи;
- реструктуризация алгоритмов при выявлении неисправностей;
- контроль выполнения команд по факту и времени;
- санкционированный контроль любого датчика и алгоритма;
- украшение внесения оперативных и неоперативных изменений при санкционированном доступе к изменениям одновременной автоматической регистрации факта доступа и внесения изменений;
- фиксация времени возникновения регистрационных событий;
- автоматическая подготовка отчетной документации;
- высокая ремонтопригодность технических средств;
- уменьшение габаритных размеров технических средств;
ОВЕН ПЛК63 – контроллер с HMI для локальных средств автоматизации в шитовом исполнении. Сам ПЛК изображён на рисунке 4 имеет 8 аналоговых входов для подключения датчиков и 6 выходных. количество дискретных выходов составляет 8. Напряжение питания дискретного выхода 24±3 В. Программируется через программу CODESYS V2 через интерфейс КС1, RS-485, RS-232. К преимуществам можно отнести возможность расширения путем подключения модулей ввода/вывода. Увеличение дискретных выходов путем подключения модуля ОВЕН МР1. Корпус имеет удобное крепление на DIN-рейку. Встроенный источник вторичного питания выходное напряжение 24±3 В ток не более 180 мА, позволяет проработать некоторое время при перебоях питания, а также выполнении программы на перевод выходных элементов в безопасное состояние.
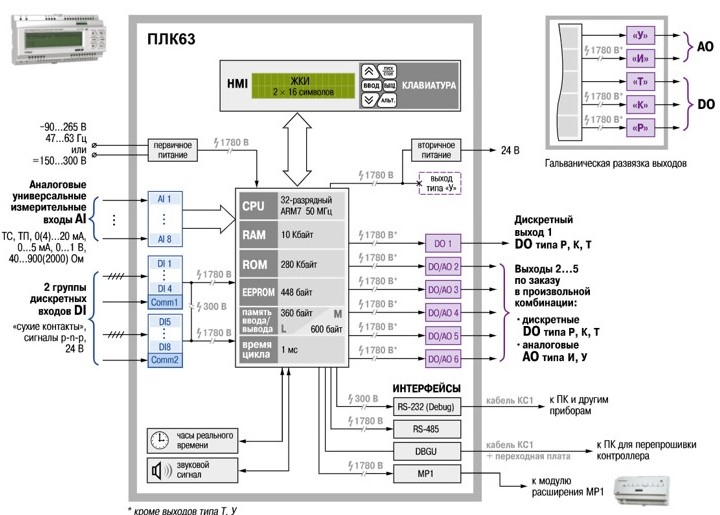
Рисунок 4 – Функциональная схема ПЛК63
Взаимодействие с датчиками и исполнительными устройствами определяется соответствующими протоколами обмена, учитывающие особенности функционирования системы в целом и требования программно-аппаратной и схематической совместимости с другими устройствами и системами.
На структурной схеме изображены все основные функциональные части изделия (элементы, устройства и функциональные группы) и основные взаимосвязи между ними. Графическое построение схемы обеспечивает наилучшее представление о последовательности взаимодействия функциональных частей в системе. На линии взаимосвязей стрелками обозначены направление хода процессов, происходящих в устройстве.
Данная система включает следившие блоки:
- Д1 – объём шихты над малым конусом;
- Д2 - объём шихты над большим конусом;
- БП1 - блок питания;
- ПЛК;
- ПБР - пускатель бесконтактный реверсивный;
- МЭО - исполнительный электрический однооборотный механизм;
- УП - указатель положения;
- RS-485 - стандарт промышленной сети;
- ПК - персональный компьютер;
- ДП - диспетчерский пункт.
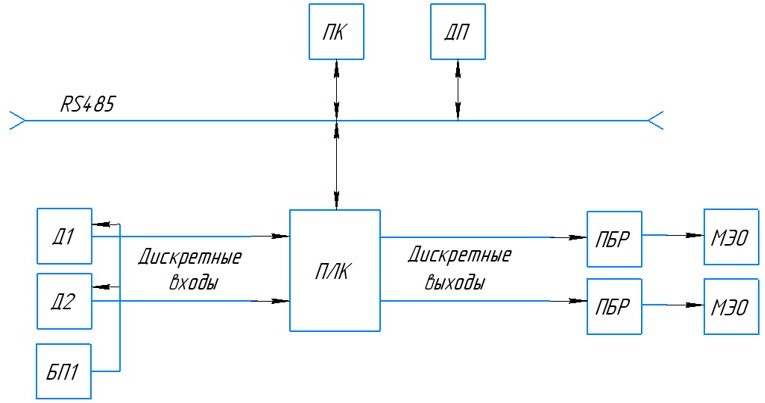
Рисунок 5 – Структурная схема контроля загрузки доменной печи
Главный принцип системы автоматического контроля загрузки – это использование вычислительной мощности ПЛК. Что позволит рационально управлять объём шихты в устройстве.
Предварительным этапом сигнал поступает с датчика УЛМ-11А1, который сигнализирует об объёме шихты в колошниковом пространстве над малым конусом. Параметры объёме шихты вычисляться ПЛК и сравниваться между двумя датчиками.
В процессе загрузки конусы работают поочередно: когда один опущен, другой поднят (закрыт), что обеспечивает герметичность печи.
После опускания малого конуса в межконусном простран¬стве создается давление, соответствующее атмосферному, а большой конус находится под давлением газов в печи, что препятствует его опусканию. После же опускания большого конуса, в межконусном пространстве создается давление, равное давлению газов в печи, что препятствует открытию малого конуса.
Слабым местом аппарата являются стыки конусов с соот-ветствующими воронками. Здесь в связи с повышенным давле¬нием в печи просачивается доменный газ, и содержащаяся в нем пыль вызывает абразивный износ металла. Поэтому стой¬кость конусов низкая, малый; конус заменяют почти через каждые полгода, а большой через 1,5-2,5 г. Для открывания и закрывания конусов на доменных печах служат исполнительный электрический механизм МЭО-1600.
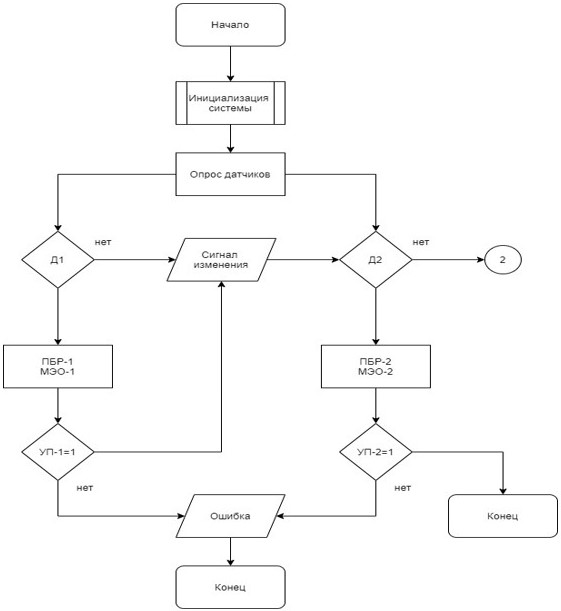
Рисунок 6 – Блок-схема алгоритма работы системы автоматического контроля загрузки доменной печи
Принципиальная электрическая схема автоматизации служит для изображения взаимной электрической связи аппаратов и устройств, действия которых обеспечивает решение задач автоматического контроля, сигнализации и контроля технологическим процессом. Принципиальная электрическая схема автоматического управления, регулирования, сигнализации и питания должны быть выполнены развернутым способом в соответствии с требованиями стандартов ЕСКД (единой системой конструкторской документации) по правилам выполнения схем, условным графическим обозначением, маркировке цепей и буквенно-цифровыми обозначениям элементов схем согласно соответствующих ГОСТ 21404 – 85 и др.
Разработана электрическая схема системы автоматического контроля загрузки доменной печи развернутым способом, где изображено на листе 3 графической части дипломного проекта.
Контроль загрузки шихты выполняется уровнемером УЛМ-11А1 работающий по принципу ЛЧМ (FMCW) - радиолокатора. Это один из классических методов бесконтактного измерения расстояния, позволяющий минимизировать влияние паразитных помех и помех, связанных с неровностями (волнениями) поверхности измеряемого продукта. Возникновение сигнала по импульсным линиям поступает на датчик типа «УЛМ-11А1» (поз. 5P1, 5P2) с микропроцессором обработкой.
Бесконтактный радарный уровнемер УЛМ-11А1 ориентирован на решение общетехнологических задач измерения уровня в различных резервуарах с жидкими продуктами и сыпучими материалами.
В работе датчиков уровнемер УЛМ-11А1 используют микропроцессоры, поэтому датчики являются интеллектуальными. Микропроцессоры дают датчикам ряд преимуществ: конфигурация и изменение диапазона измерения, регулярная компенсация влияния окружающей среды, улучшенная работа, дистанционное управление датчиком, получение дистанционно информации о диагностике. Эти преимущества быстро окупают затраты.
Датчики давления УЛМ-11А1 имеют 0.50%, 0.25%, 0.15% и 1.5% классы точности.
Питание датчиков давления УЛМ-11А1 осуществляется от блока питания Карат-22 (поз. Б1) напряжения 24В постоянного тока. Выходной ток сигнала УЛМ-11А1 4-20мА, пропорционально для контроля уровня шихтового материала, сигнал поступает на соответствующие выходы программного контроллера ПЛК63 от фирмы ОВЕН (поз. А1). Питание программного контроллера осуществляется от сети переменного тока 220В.
Выходные токовые сигналы 4 - 20 Ма, пропорционально расходу доменного поступают на соответствующие входы программируемого контроллера типа ПЛК63 от фирмы ОВЕН (поз. Al). С датчики УЛМ-11А1 для измерения расхода шихты (поз. 5Р1) выводят два аналоговых сигнала (Р-7, Р-8) идущие на вход ПЛК, а именно (AI1, AI2). Датчики УЛМ-11А1 для измерения расхода шихты в колошнике (поз. 5Р2) выводят два аналоговых сигнала (Р-9, Р-10) идущие на вход ПЛК, а именно (AI3, AI4). Питание программируемого контроллера типа ПЛК63 осуществляется от сети переменного тока напряжением 220 В.
В данной системе применяем прямое цифровое управления на базе контроллера ПЛК63 от фирмы ОВЕН. Это программируемый логический контроллер высшего класса, предназначенный для решения сложных задач автоматизации технологических процессов, и может применяться практически во всех отраслях промышленности. Контроллер имеет 8 аналоговых входов с обозначением (AII, AI2, AI3, AI4, IFS, AI6. I7. AI8) и точно такое же количество дискретных (DI1, DI2, DI3, DI4, DI5, DI6, DI7, DI8). Количество выходов внутри контроллера 6. Количество дискретных выходов 1 (DO1). Количество Аналоговых выходов 4 (АО1, АО2, АО3, AO4, AO45) центральный процессор 32-разрядный, RISC 50 МГц на базе ядра ARM7. Размер Retain-памяти (EEPROM) 448 байт. Объем оперативной памяти для хранения переменных программ 10 кб. объем памяти хранения программ 280 кб. Объем памяти ввода-вывода 600 байт.
На корпусе присутствует элементы человеко-машинного интерфейса, дисплей текстовый монохромный ЖКИ с подсветкой количество знакомест (символов) 2 x 16. Кнопки управления на лицевой панели 6 штук: "Пуск/стоп", "Выход", "Альт", "Ввод", "Вверх", "Вниз". Контроллер имеет следующие важнейшие функции и характеристики:
- очень высокое быстродействие;
- мультипроцессорный режим работы;
- функции диагностирования и диагностический буфер:
- встроенные функции для отображения (управление);
- программное параметризованное модулей;
- возможна работа без принудительной вентиляции;
- высокая устойчивость к вибрации;
- функции часов, счетчик времени работы, копирование данных;
- обработка ошибок;
- встроенный интерфейс, пригодный для простых сетевых решений.
ПЛК63 программный логический контроллер высшего класса качества для решения сложных задач автоматизации технических процессов. Основные области применения ОВЕН ПЛК63 – ЖКХ, ЦТП, ИТП, котельные, небольшие установки.
Для изменения уровня шихтового материала в контроллере в соответствии с алгоритмом, происходит вычисление управлявших воздействий для закона регулирования. Управляющие воздействия модуля вывода дискретных сигналов МР1 (поз. А2) к контроллеру через пускатель бесконтактный реверсивный типа ПБР-3А (поз. 2Р7, 3Р7, 4Р7, 5Р7).
Входным сигналом пускателей является напряжение отрицательной полярности, подаваемого относительно контакта 8 на вход "М" (контакт 7) или вход "Б" (контакт 9). Обозначение "М" (меньше) или "Б" (больше) приняты условно.
Для осуществления управления пускателем с помощью ключей в пускателе имеется источник напряжения, положительный потенциал которого выведен на клемму 8, отрицательный – на клемму 10.
С помощью ключей контакт 10 подключается к входу "М" или "Б".
В исходном состоянии (входные сигналы отсутствуют) напряжение на эмиттере V17 меньше напряжения включения за счет малой величины сопротивления резисторов R7, R20, уменьшающих напряжение на эмиттере через положительный вывод диодного моста V33…V36.
В связи с этим транзисторы V13 и V14 закрыты, управляющих импульсов на трансформаторах Т2 и Т3 нет. Триаки V4…V7 закрыты. Напряжение на выходе отсутствует.
При подаче управляющего напряжения на клеммы 8-7 (8-9) происходит заряд конденсаторов С1 (С2) и С3, выполняющих функции фильтров и элементов схемы задержки на реверсе. Протекание тока через резисторы R7, R20, отрицательный вывод диодного моста V33…V36 и диод V10 (V11) приводит к увеличению падения напряжения на резисторах R7 и R20 и открытию диода отрицательного вывода диодного моста V33…V36. В результате этого на базе транзистора V13 (V14) напряжение уменьшается, происходит заряд конденсаторов С3 и С7 и увеличение напряжения на базе транзистора V14 (V13) и эмиттере транзистора V17 относительно базы 1 транзистора V17.
При достижении напряжением на эмиттере транзистора V17 напряжения включения транзистор открывается, и конденсатор С7 разряжается по цепи: резистор R10, переход база-эмиттер транзистора V14 (V13), диод V16 (V15), переход эмиттер-база транзистора V17 и отрицательный вывод диодного моста V33…V36.
Ток разряда конденсатора, протекающий через базу транзистора V14 (V13), усиливается им и в трансформаторе Т2 (Т3) формируется импульс, отпирающий триаки V4 (V5) и V7 (V6). Процесс заряд-разряд конденсатора С7 повторяется периодически и прекращается только после снятия входного сигнала. Триаки V4 (V5) и V7 (V6) также открыты до снятия входного напряжения. Триаки силовой цепи служат для подачи напряжения на электродвигатель.
Конденсатор С4 и резисторы R8, R9 предназначены для улучшения условий коммутации триаков.
Пускатель защищен от одновременного отпирания всех триаков, вызванного подачей напряжения на оба входа, или быстром реверсом напряжения управления.
Пускатель содержит варисторы R32...R35 для защиты триаков от перенапряжения при коммутации синхронных электродвигателей.
Пускатели ПБР-3А содержат схему защиты электродвигателя от перегрузки. Схема защиты обеспечивает отключение электродвигателя механизма при выходе выходного органа механизма на упор либо при заклинивании его в промежуточном положении.
Входной сигнал схемы защиты – ток электродвигателя.
Выходное напряжение трансформаторов тока Т4 и Т5 через диоды V41…V44, резистор R22 подается на конденсатор С11. Если конденсатор зарядится до напряжения отпирания транзистора V25, транзистор откроется, уменьшится потенциал эмиттера транзистора V22 (при практически постоянном напряжении на базе этого транзистора).
Транзистор V22 откроется и зашунтирует цепь питания эмиттера транзистора V17, формирование импульсов прекратится. В таком положении схема остается до снятия входного напряжения с входа пускателя.
Пускатель рассчитан на подключение электродвигателей различной мощности, поэтому предусмотрено изменение тока срабатывания защиты изменением положения движка потенциометра R29, расположенного на передней панели пускателя.
Исполнительные механизмы электрические однооборотные типа МЭО-1600 состоит из следующих основных частей: редуктор, трехфазный электродвигатель, блоков токовых датчиков, электромагнитный тормоз. Принцип работы механизмов основан на прекращении электрического сигнала, поступавшего от пускателей, во вращательное перемежение.
Редуктор является основным узлом механизма, на котором устанавливаются составные части механизма.
Редуктор состоит из корпуса, цилиндрических прямозубых ступеней, ручного привода, тормоза.
Ручной привод служит для перемещения выходного вала (регулирующего органа) при монтаже и настройке механизмов, а также в аварийных ситуациях (отсутствии напряжения питания).
Перемещение выходного вала механизмов осуществляется вращением маховика ручного привода. Наличие планетарной передачи в редукторе механизмов позволяет использовать ручной привод независимо от включения или выключения электродвигателя.
На механизмах установлены электродвигатели асинхронные трехфазные. В исполнительном механизме применяется блок токовых датчиков типа БСПТ-10, выходной сигнал с которого 4-20мА поступает на указатели положения цифровой типа МТМ-310 (поз. 2Р9, 3Р9, 4Р9, 5Р9) на выход ПЛК (поз. Р11, Р12, Р13, Р14) тем самым сигнализирует на сколько сейчас открыт конус. В механизме применяется блоки датчиков БСПТ-10, которые состоят из двух токовых датчиков перемещения, профильного кулачка, четырех микровыключателей, четырех кулачков микровыключателей вала. Все элементы закреплены на корпусе бока датчиков
Для ограничения величины выбега выходного вала и предотвращения перемещения его от усилия регулирующего органа при отсутствии напряжения на электродвигателе в механизме предусмотрен механический тормоз.
Исполнительный механизм управления закрытием конусом пока не станет равным заданного значения.
Действие цифрового указателя положения основан на аналого-цифровом преобразовании значения, указанных на цифровом индикаторе человеком, в соответствии значения выходного тока.
Питание цифрового указателя осуществляется от напряжения 24В постоянного тока с помочью группового блока питания МТМ-140 (поз. Б2).
Выводы
Магистерская работа посвящена актуальной научной задаче является повышение эффективности качественного технологического процесса загрузки колошникового устройства доменной печи путем разработки системы автоматического управления, а также контроля и регулирования основных технологических параметров данного объекта управления. В рамках проведенных исследований выполнен:
- Анализ технологического процесса загрузки колошникового устройства доменной печи как объекта автоматизации;
- Рассмотрена доменная печь как объект автоматического управления;
- Анализ существующих разработок по автоматизации доменной печи;
- Обоснованы направления автоматизации доменной печи;
- Разработаны структурная схема управления, функциональная схема автоматизации, а также алгоритмы технологического процесса доменной печи.
При написании данного реферата магистерская работа еще не завершена. Окончательное завершение: июнь 2023 года. Полный текст работы и материалы по теме могут быть получены у автора или его руководителя после указанной даты.
Список источников
- Автоматизация основных металлургических процессов. Липухин Ю.В., Булатов Ю.И., Бок Г., Кнорр М.М.: Металлургия, 1990. 280 с.
- Харахнин К.А., Булатов Ю.И., Мочлаин В.Н. Автоматизация доменного производства: Учеб. Пособие. – Череповец: ГОУ ВПО ЧГУ, 2015. – 70с.
- Электрическое оборудование доменных цехов. Агроник С.Г., Влатт М.Ю., Скрыльников С.В., Москва «Металлургия», 1966. 196 с.
- Котов К. И., Шершевер М. А. Средства измерения, контроля и автоматизации технологических процессов. – М.: Металлургия, 1987. – 496 с.
- Громаков Е. И. Проектирование автоматизированных систем: учебно – методическое пособие. – Томск: Томский политехнический университет, 2010. – 173 с.
- Глинков, Г.М. АСУ ТП в черной металлургии: учебник для вузов. / Г.М. Глинков, В.А. Маковский – 2-е изд., перераб. и доп. – М.: «Металлургия», 1999. – 310 с.
- Официальный сайт Донецкого металлургического завода [Электронный ресурс]: Режим доступ: http://dmz.donetsksteel.com/ru/company (Дата обрушения 25.05.2021)
- Доменное производство [Электронный ресурс]: Режим доступ: https://metalspace.ru/education-career/osnovy-metallurgii/domennaya-pech/810-domennoe-proizvodstvo.html (Дата обрушения 25.05.2021).
- Кисаримов, Р.А. Электропривод: справочник. / Р.А. Кисаримов, Москва, ИП РадиоСофт, 2008.- 391 с.
- Уэйкерли Д. Проектирование цифровых устройств / Д. Уэйкерли. – М.: Постмаркет, 2002. – Том 2. – 528 с.