Реферат за темою випускної роботи
Зміст
- Вступ
- 1. Актуальність теми
- 2. Мета і задачі дослідження та заплановані результати
- 3. Огляд досліджень та розробок
- 3.1 Аналіз технологічного процесу завантаження доменної печі як об'єкта автоматизації
- 3.2 Доменної печі як об'єкт автоматичного управління
- 3.3 Аналіз існуючих розробок по автоматизації завантаження доменної печі
- 3.4 Обґрунтування напрямку автоматизації завантаження доменної печі
- 3.5 Алгоритмізація роботи і схемних рішень системи автоматичного контролю завантаження доменної печі
- Висновки
- Перелік посилань
Вступ
Системи контролю і управління роботою доменних печей поступово ускладнювалися - від найпростіших систем стабілізації окремих параметрів до локальних систем управління окремими режимами роботи печі і нарешті, до комплексних систем управління всім доменним процесом.
Для вирішення даної проблеми необхідно забезпечити своєчасне інформування про тиск доменного гада в колошниковой системі перед завантаженням завантаженням доменної печі. Повноцінне рішення задачі ефективного скидання тиску стало можливим з масовим розподілом високонадійних програмованих логічних контролерів.
1. Актуальність теми
Впровадження автоматичного системи управління завантаження колошникового пристрою доменної печі на базі ПЛК дозволило збільшити реальну продуктивність при одночасному зниженні собівартості, так як автоматична система може функціонувати безперервно в режимі реального часу.
2. Мета і задачі дослідження та заплановані результати
Мета дослідження-підвищення ефективності функціонування колошникового пристрою доменної печі за рахунок розробки системи автоматичного управління, що дозволяє поліпшити якість завантаження шихтових матеріалів при економії матеріалів і енергетичних ресурсів.
Основні завдання дослідження:
- Аналіз технологічного процесу завантаження доменної печі як об'єкта автоматизації.
- Розробка структурної та функціональної схем системи автоматизації.
- Розробка алгоритму управління технологічним режимом завантаження доменної печі.
3. Огляд досліджень та розробок
3.1 Аналіз технологічного процесу завантаження доменної печі як об'єкта автоматизації
Колошниковое пристрій являє собою багатоповерхову металеву конструкцію, що служить для підтримки комплексу механізмів, призначених для завантаження шихти в доменну печі (засипний апарат та ін), відведення газів (газовідводи) і для монтажу обладнання.
Газовідводи. Для відводу доменного газу в куполі печі є отвори і йдуть від них вгору газовідводи. Зазвичай число газовідводів дорівнює чотирьом, їх з'єднують спочатку симетрично попарно, а потім в один газохід, що йде вниз до пиловловлювачів, розташованим на нульовій позначці (на печах об'ємом 5000-5500 М3 є вісім газовідводів і по два низхідних газоходу). Від верхніх точок газовідводів відходять вер-тикальні свічки (труби), що закінчуються атмосферним клапаном, який відкривається, випускаючи газ в атмосферу при перевищенні тиску в печі понад допустимий. Число свічок з клапанами коливається від двох до чотирьох, вони служать також для випуску газу при зупинках печі.
засипний апарат. Він призначений для завантаження шихти, необхідного її розподілу по перетину колошника, тобто печі і для забезпечення герметичності печі в процесі завантаження, тобто для запобігання потрапляння в піч повітря, що веде до можливості вибуху, і запобігання виділення пічного газу в атмосферу.
велика частина доменних печей обладнана двоконусними засипними апаратами, а нові печі споруджують з засипними апаратами нової конструкції - безконусними. Двоконусний засипний апарат показаний на малюнку 1. Його основними елементами є: великий конус 1 з лійкою (чашею) 2; обертовий розподільник шихти, що складається з малого конуса 4 і воронки 10; приймальна воронка 6. Великий і малий конуси можуть переміщатися вгору-вниз; у верхньому положенні великий конус притиснутий до воронки 2, а малий до воронки 10, ізолюючи робочий простір печі від атмосфери; по-ложеніе конусів в опущеному стані показано пунктиром. Малий конус підвішений на порожнистої трубчастої штанзі 5, великий - на штанзі 3, що проходить всередині порожнистої штанги 5, завдяки чому конуси можуть опускатися і підніматися незалежно один від одного. Воронка 10 пов'язана з приводом, що забезпечує її обертання разом з малим конусом.
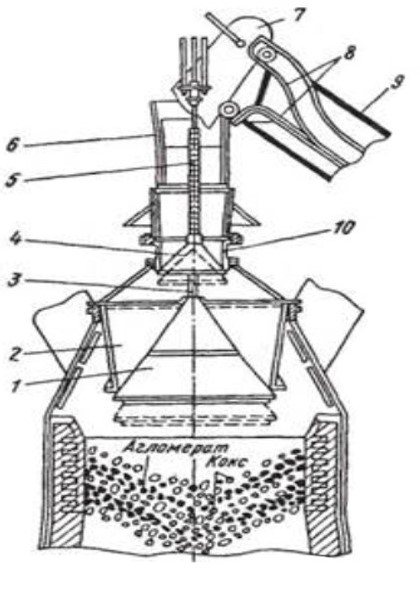
Малюнок 1-засипний апарат двоконусний
Шихтові матеріали доставляють на колошник двома скіпами (візками), що рухаються по рейках 8 похилого моста 9; в крайньому верхньому положенні Скіп 7 перекидається, оскільки його передні колеса котяться по рейках, загнутим вниз, а задні — по інших рейках, загнутим вгору і піднімає задню частину скіпа При цьому порція шихти висипається через приймальну воронку на поверхню малого конуса, після чого він опускається і матеріал прокидається вниз на поверхню великого конуса, а малий. Подібним чином на поверхню великого конуса завантажують два—шість скіпів (набирають подачу). Потім при піднятому малому конусі опускають великий конус, і матеріал подачі прокидається в піч, після чого великий конус піднімається.
Далі на великий конус набирають нову подачу (два—шість скіпів), але перед кожним опусканням малого конуса він з лійкою 10 повертається на 60°. Завантаживши цю подачу в піч шляхом опускання і підйому великого конуса, на нього набирають наступну подачу; при цьому перед кожним опусканням малого конуса він з лійкою повертається на 120° від вихідного положення. При наборі після-дме подачі кут повороту становить 180° і т. д. Завдяки такому обертанню розподільника подачі потрапляють не в одне місце під похилим мостом 9, а порівняно рівномірно розподіляються по периферії колошника.
У процесі завантаження конуси працюють по черзі: коли один опущений, інший піднятий (закритий), що забезпечує герметичність печі.
Після опускання малого конуса в межконусном просторі створюється тиск, відповідне атмосферному, а великий конус знаходиться під тиском газів в печі, що перешкоджає його опускання. Після ж опускання великого конуса, в межконусном просторі створюється тиск, рівний тиску газів в печі, що перешкоджає відкриттю малого конуса. Для вирівнювання тиску в міжконусному просторі і печі подають чистий газ в міжконусний простір під тиском, близьким до тиску газів в печі. Це роблять перед опусканням великого конуса за допомогою зрівняльних клапанів, а при опусканні малого конуса скидає клапан випускає газ з межконусного простору в атмосферу. Робота зрівняльних клапанів автоматизована і зблокована з роботою конусів засипного апарату.
слабким місцем апарату є стики конусів з відповідними воронками. Тут у зв'язку з підвищеним тиском в печі просочується доменний газ, і що міститься в ньому пил викликає абразивний знос металу. Тому стійкість конусів низька, малий; конус замінюють майже через кожні півроку, а великий через 1,5-2,5 р.
3.2 Доменної печі як об'єкт автоматичного управління
Мета проектування, розробка системи автоматичного контролю завантаження доменної печі, за рахунок сучасно апаратури автоматизації на базі ПЛК – програмованого логічного контролера, а саме ПЛК63. Який дозволяє збільшити працездатність, надійність. Заміна призведе до кращого функціонування системи в цілому.
Вимоги до пристрою автоматичного контролю завантаження доменної печі без участі обслуговуваного персоналу:
- регулювання вела шихтового матеріалу 4-8 т;
- регулювання об'єму шихтового матеріалу 7300 м^3;
- дистанційне керування оператором з пульта;
- можливість передачі технологічної інформації по протоколу RS 485, а також передачі інформації стану протікання процесу іншим ПЛК;
- клас точності ПЛК 0,5 / 0,25;
- замінність апаратури;
- світлова та звукова інформація на пульті оператора;
- відображення стану технологічного процесу та обладнання на пульті оператора;
- відображення регулювання на пульті оператора;
- Оперативна зміна налаштувань регулювання;
- швидкий вихід з аварійної ситуації;
- підвищення надійності та безпеки;
- корпус щитового кріплення;
- габаритні розміри (ВхШхГ), (168х137х55) мм;
- пластиковий корпус, зі ступенем захисту IP55;
Вимоги до показників надійності системи встановлюються в відповідно до ГОСТ 24. 701-86. Показники надійності системи повинні бути не нижче наступних значень:
- для функцій управлінь-30000 годин напрацювання на відмову;
- для функцій контролю-30000 годин напрацювання на відмову;
- для інформаційних функцій-15000 ч.
Середній термін служби технічних засобів повинен бути не менше 10 років.
3.3 Аналіз існуючих розробок з автоматизації завантаження доменної печі
Відкрита архітектура – важлива характеристика системи при інтеграції АСУ в існуючі на доменних печах системи управління і засоби контролю. Широка номенклатура промислових контролерів вітчизняного та зарубіжного виробництва, що застосовується в даний час при створенні автоматизованих систем управління, зокрема, доменних печей, визначає важливість цієї характеристики АСУ.
Підсистема верхнього рівня (АРМ оператора-технолога) розроблена на базі SCADA-системи TRACE MODE 5.09 з використанням персонального комп'ютера промислового виконання. Підсистема середнього рівня (базовий рівень автоматизації) виконана на базі ПЛК Modicon TCX Quantum з використанням розподіленого введення/виводу. Розподілені вузли вводу / виводу (DIO) об'єднані в локальну мережу з використанням мережевої технології Modbus Plus. Нижній рівень-технічні засоби управління електроприводами і датчики КВП.
Зв'язок по мережі Modbus Plus контролера Modicon з комп'ютером станції оператора – технолога здійснена через ОРС Factory Server фірми "Schneider Electric" з використанням адаптера мережі, встановленого на комп'ютері станції оператора-технолога. Частотно-регульований привід розроблений на базі частотних перетворювачів Altivar 66 фірми "Schneider Electric"
Особливістю технічної структури АСУ є умовне її розбиття на постійну і змінну частини:
- постійна частина-технічні засоби і датчики КВП, що забезпечують управління власне роторним розподільником, КК і контроль стану механізмів РЗУ; є невід'ємною частиною АСУ;
– змінна частина-технічні засоби, що забезпечують синхронізацію роботи АСУ з верхньою системою завантаження доменної печі і виконує, при необхідності, частину функцій цієї системи.
Для вирішення завдання визначення ваги матеріалу, що розподіляється на колошник доменної печі, що використовує ваговимірювальні датчики. Алгоритм побудований на контролі витрат енергії при розподілі матеріалу, а також на контролі зміни запасу кінетичної енергії при його вивантаженні. Результати впровадження АСУ на об'єкті підтвердили задовільну точність цього методу при реалізації різних режимів розподілу матеріалу відповідно до заданої програми завантаження. Адаптація коефіцієнтів рівнянь алгоритму розподілу проводиться від подачі до подачі, що виключає ефект накопичення помилок в його розрахункової частини.
АРМ АСУ надає можливість оператору, використовуючи функціональну клавіатуру, по ходу технологічного процесу Дистанційно викликати функції управління, включаючи зміну завдань на поточні параметри процесу, а також відображає технологічний процес завантаження у вигляді мнемосхем технологічних вузлів і механізмів, графіків зміни параметрів і їх налаштувань для здійснення зв'язку оператора–технолога з процесом завантаження. Розроблений пакет візуалізації процесу забезпечує оперативне і представницьке зчитування інформації з екранів монітора АРМ.
Інструментальна система Trace Mode, як відомо, включає в себе два редактори:
- редактор бази каналів;
- редактор подання даних.
У редакторі бази каналів описується конфігурація операторської станції, використовуваної в АСУ, налаштовуються канали зв'язку з підключеним до них ПЛК, задаються змінні і способи їх обробки, створюються меню для виклику інформації та управління, формуються звіти, перелік змінних і т.д. операторська станція (ОС) АРМ підтримує роботу через мережу Modbus Plus з ПЛК середнього рівня – Modicon TCX Quantum.
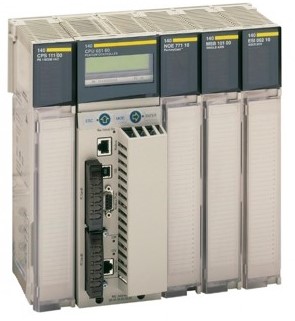
Малюнок 2 - Зовнішній вигляд програмного контролера Modicon TCX Quantum
Вузол АРМ з використанням інструментальної системи на 1024 канали без автопобудування і два об'єкти. Один з об'єктів є сукупністю каналів, що визначають кількість технологічних змінних (аналогових і дискретних), що використовуються в АСУ, інший – включає канали, що використовуються для реалізації власних функцій інтерфейсу оператора-технолога, включаючи рівень візуалізації.
В каналах передбачена первинна і вихідна обробка даних. Всі інші завдання з обробки даних і управління розробляються у вигляді окремих програм. Для цього передбачені дві мови програмування в стандарті МЕК-61131: Техно FBD і Техно IL. Програми, створені на мові FBD, можуть викликатися з процедур каналів.
Кількість вхідних/вихідних сигналів АСУ досягає 160.
Насправді в системі Кількість каналів, використовуваних для технологічних змінних і реалізації власних функцій інтерфейсу оператора значно більше, ніж заявлено інструментальною системою, тобто 1024. Використання глобальних змінних, визначених в Trace Modе, дозволило ефективно вирішити задачу проектування підсистеми верхнього рівня на базі інструментальної системи на 1024 вх/виходу.
Використання глобальних змінних особливо ефективно проявилося в режимі off-line роботи системи при формуванні циклів завантаження доменної печі. При цьому загальний цикл завантаження задається оператором на двадцять подач (максимально), кожна з яких складається з шести скіпів різного матеріалу.
Всього в проекті створено близько 1250 каналів, з них 310 - пов'язані з ОРС-сервером. В АСУ використовується OPC Factory Server розробки фірми Schneider Electric c локальним доступом. У цьому застосуванні ОРС-клієнт і ОРС-сервер встановлюються на одній станції, тобто на комп'ютері АРМ.
Необхідно відзначити ефективність програмування деяких завдань на мові FBD, який був використаний для створення додаткових елементів управління і візуалізації і, головне, для поліпшення динаміки відображення повідомлень на технологічних екранах інтерфейсу оператора-технолога. Як відомо, в TRACE MODE формування повідомлень здійснюється кодуванням слів станів без використання символьних змінних. При наявності великої кількості повідомлень з урахуванням затримки обробки і перетворення сигналів каналом ОРС запізнювання виведення на технологічний екран повідомлення стає неприпустимо великим, що може привести до візуальної втрати важливої технологічної інформації.
В АСУ для зниження часу запізнювання виведення на екран повідомлень на FBD блоках розроблена програма обробки слів станів з використанням блоку логарифмування слова стану. При цьому попередньо здійснюється перевірка зміни слова стану щодо попереднього циклу його зчитування. Такий підхід дозволив істотно знизити час запізнювання виведення повідомлень на технологічні екрани по ходу технологічного процесу завантаження.
Основною вимогою до організації структури рівня візуалізації при роботі РЗУ була оперативність переходу на викликаний технологічний екран. Засоби TRACE MODE дозволили створити зручну систему технологічних екранів, які попередньо об'єднуються у функціональні групи, всередині яких формуються підгрупи, організовані в Допоміжні екрани.
Вихід на будь-яку функціональну групу здійснюється через основний екран "МНЕМОСХЕМА" рисунок 3. Далі за допомогою відповідних кнопок здійснюється вихід на допоміжні екрани.
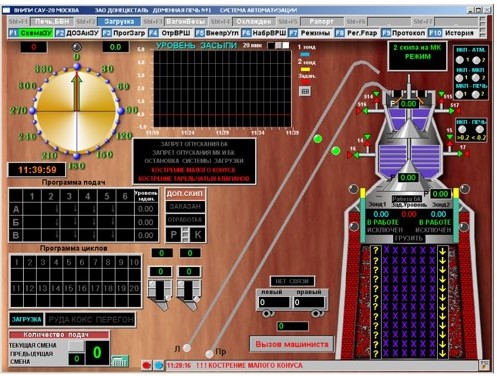
Малюнок 3 - Екранна форма мнемосхеми завантаження
Передбачений оперативний вихід на основні екрани за допомогою "гарячих" клавіш клавіатури. Технологічний екран ділиться на робочу та інформаційні зони. Інформаційна зона розташовується у верхній частині екрану і містить:
- найменування екрану;
- дату і час включення системи;
- рядок повідомлень, в якому вказується технологічний стан змінної, тип механізму і режим його роботи;
- дата і час формування повідомлення по даній змінній;
- кнопку переходу на перегляд звіту тривог;
- кнопку перегляду графічного відображення змінної.
Режим "Робота" – режим роботи, при якому здійснюються функції контролю і управління АСУ в реальному масштабі часу. При цьому система здійснює: < / p>
- "стеження" за станом механізмів верхнього завантаження доменної печі з урахуванням необхідної послідовності роботи механізмів.
- обробляє інформацію і формує керуючі сигнали на підставі даних, отриманих від датчиків технологічного процесу і технічного стану основних вузлів РЗУ; < / p>
- проводить розрахунок і передачу сигналів управління на Електропривод роторного розподільника відповідно до заданого алгоритму розподілу шихтового матеріалу на колошнику доменної печі.
В процесі вивантаження шихтового матеріалу підсистема середнього рівня виробляє Розрахунок кількості матеріалу, що надходить на колошник в одиницю часу.
В режимі "робота" здійснюється архівування і формування протоколів. Тут повністю використовуються можливості TRACE MODE з архівування та створення звіту тривог. Оновлення даних в архіві здійснюється циклічно. Дані в звіті тривог заносяться у вигляді окремих рядків, кожна з яких містить час і дату її формування. Додатково в кожному рядку вказується тип повідомлень: аварійний, технологічний, попереджувальний або системний, що визначає стан КТС АСУ.
В АСУ передбачено "гаряче" резервування модуля центрального процесора (ЦПУ) 140 CPU 213 04 керуючого контролера. Модулі ЦПУ (основний і резервний) розміщуються в шафі контролера на окремих слотах і пов'язані з модулями вузлів системи локальною мережею Modbus Plus (MB+). Програмне забезпечення основного і резервного ЦПУ практично ідентичні і відрізняються лише програмними модулями MAIN і RESERV, що визначають статус ЦПУ: основний – MAIN, резервний – RESERV. Статус ЦПУ визначається при конфігурації системи.
при реалізації резервування використовується особливість локальної мережі МВ+, що представляє собою однорангову мережу з послідовною передачею маркера мережі до віддалених вузлів системи і можливість використання Active X додатків в TRACE MODE.
"Резервний "ЦПУ постійно знаходиться в процесі зчитування інформації про стан модулів введення/виведення системи при" захопленні " маркера мережі, тобто працює також як і основний ЦПУ, і також формує Керуючі вихідні сигнали. Однак при роботі" основного "ЦПУ керуючі сигнали "резервного" відключені від ліній зв'язку, як від ОС, так і від вузлів розподіленого введення/виводу. При виявленні несправності" основного " ЦПУ "резервний" ЦПУ має повну інформацію про стан технологічного процесу і автоматично підключається до процесу управління, відключаючи при цьому несправний ЦПУ. Час перемикання становить не більше 2с, що для технологічного процесу завантаження доменної печі є цілком прийнятним.
3.4 Обґрунтування напрямку автоматизації завантаження доменної печі
Основна проблема, яка існує на Донецькому металургицькому заводі це використання застарілої апаратури. ПЛК Schneider Electric, Siemens т.д. використання несе ризик про поступовий вихід з ладу, неможливість знайти аналогічну заміну. Тому для побудови системи автоматизації потрібен ПЛК, який без проблем можна знайти на ринку і для можливості покупки резерву для швидкого перемикання між ними. Також вибір ПЛК як блок управління грунтується на великій кількості параметрів і модульності, вузли контролю і регулювання ПЛК заснований на центральному процесорі має потрібну обчислювальну потужність і впоратися з системною автоматизацією.
Параметр, який відповідає за завантаження доменної печі який можна автоматизувати є регулювання витрати шихтового матеріалу.
Засипний апарат складається з двох конусів: великого і малого. При опусканні матеріалів з малого конуса в межконусное простір потрапляє повітря.
Перед опусканням малого конуса проводитися завмер рівня шихти з допомогою рівнеміра.
Для підвищення надійності системи застосовують здвоєні Сигналізатори рівняномір, константи яких включають послідовно. Таке ускладнення обумовлено можливістю вигину штанг конусів.
3.5 Алгоритмізація роботи і схемних рішень системи автоматичного контролю завантаження доменної печі
Система автоматичного контролю завантаження доменної печі включає програмований логічний контролер ПЛК63 від компанії ОВЕН, який взаємодіє з датчиками, отримує інформацію від об'єкта управління, обробляє її відповідно до закладеним алгоритмом і видає управління впливом на виконавчі пристрої.
застосування мікропроцесорних засобів для реалізації підсистеми технологічних зашитий і захисних блокувань дає стежили переваги:
- можливості безперервного контролю достовірності всієї вхідної інформації з сигналізацією і реєстрацією несправності окремих датчиків або каналів зв'язку;
- реструктуризація алгоритмів при виявленні несправностей;
- контроль виконання команд за фактом і часом;
- санкціонований контроль будь-якого датчика і алгоритму;
- внесення оперативних та неоперативних змін при санкціонованому доступі до змін одночасної автоматичної реєстрації факту доступу та внесення змін;
- фіксація часу виникнення реєстраційних подій;
- автоматична підготовка звітної документації;
- висока ремонтопридатність технічних засобів;
- зменшення габаритних розмірів технічних засобів;
ОВЕН ПЛК63 – контролер з HMI для локальних засобів автоматизації в шитовому виконанні. Сам ПЛК зображений на малюнку 4 має 8 аналогових входів для підключення датчиків і 6 вихідних. кількість дискретних виходів становить 8. Напруга живлення дискретного виходу 24±3 в.програмується через програму CODESYS V2 через інтерфейс КС1, RS-485, RS-232. До переваг можна віднести можливість розширення шляхом підключення модулів введення/виведення. Збільшення дискретних виходів шляхом підключення модуля ОВЕН МР1. Корпус має зручне кріплення на DIN-рейку. Вбудований джерело вторинного живлення вихідна напруга 24±3 В струм не більше 180 мА, дозволяє пропрацювати деякий час при перебоях живлення, а також виконанні програми на переведення вихідних елементів в безпечний стан.
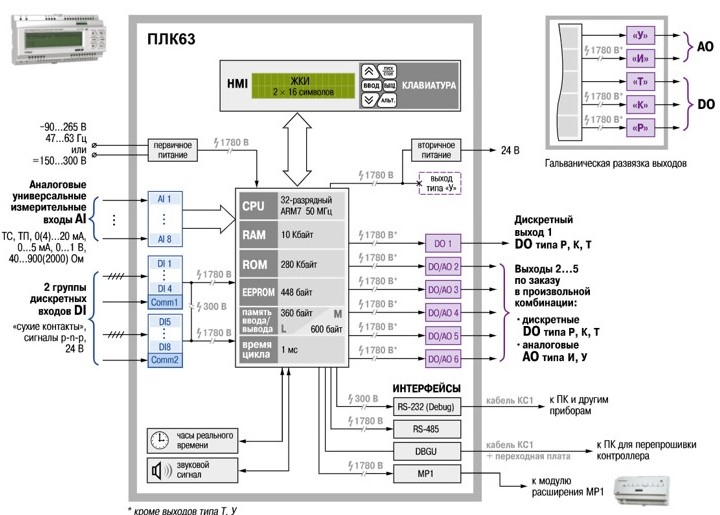
Малюнок 4 - Функціональна схема ПЛК63
Взаємодія з датчиками і виконавчими пристроями визначається відповідними протоколами обміну, що враховують особливості функціонування системи в цілому і вимоги програмно-апаратної і схематичної сумісності з іншими пристроями і системами.
На структурній схемі зображені всі основні функціональні частини виробу (елементи, пристрої і функціональні групи) і основні взаємозв'язки між ними. Графічна побудова схеми забезпечує найкраще уявлення про послідовність взаємодії функціональних частин в системі. На лінії взаємозв'язків стрілками позначені напрямок ходу процесів, що відбуваються в пристрої.
Дана система включає стежили блоки:
- Д1-об'єм шихти над малим конусом;
- Д2-об'єм шихти над великим конусом;
- БП1-блок живлення; < / p>
- ПЛК;
- ПБР-пускач безконтактний Реверсивний;
- МЕВ-виконавчий електричний однооборотний механізм;
- УП-Покажчик Положення;
- RS-485-стандарт промислової мережі;
- ПК-персональний комп'ютер; < / p>
- ДП - диспетчерський пункт.
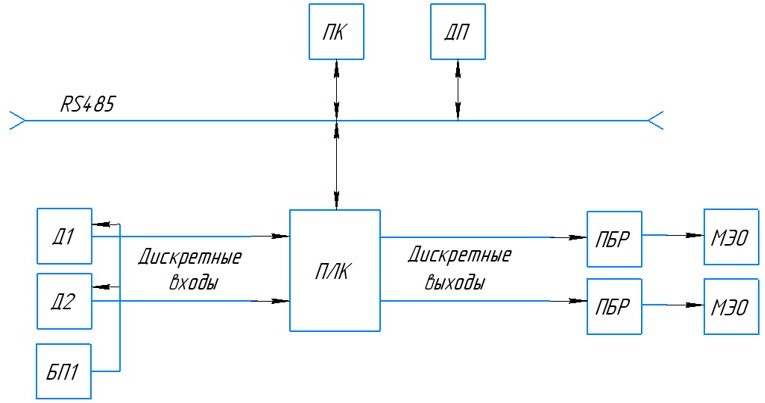
Малюнок 5 - Структурна схема контролю завантаження доменної печі
Головний принцип системи автоматичного контролю завантаження – це використання обчислювальної потужності ПЛК. Що дозволить раціонально управляти обсяг шихти в пристрої.
Попереднім етапом сигнал надходить з датчика УЛМ-11а1, який сигналізує про об'єм шихти в колошниковому просторі над малим конусом. Параметри обсягу шихти обчислюватися ПЛК і порівнюватися між двома датчиками.
У процесі завантаження конуси працюють по черзі: коли один опущений, інший піднятий (закритий), що забезпечує герметичність печі.
Після опускання малого конуса в межконусном просторі створюється тиск, відповідне атмосферному, а великий конус знаходиться під тиском газів в печі, що перешкоджає його опускання. Після ж опускання великого конуса, в межконусном просторі створюється тиск, рівний тиску газів в печі, що перешкоджає відкриттю малого конуса.
Слабким місцем апарату є стики конусів з відповідними воронками. Тут у зв'язку з підвищеним тиском в печі просочується доменний газ, і що міститься в ньому пил викликає абразивний знос металу. Тому стійкість конусів низька, малий; конус замінюють майже через кожні півроку, а великий через 1,5-2,5 м для відкривання і закривання конусів на доменних печах служать виконавчий електричний механізм МЕВ-1600.
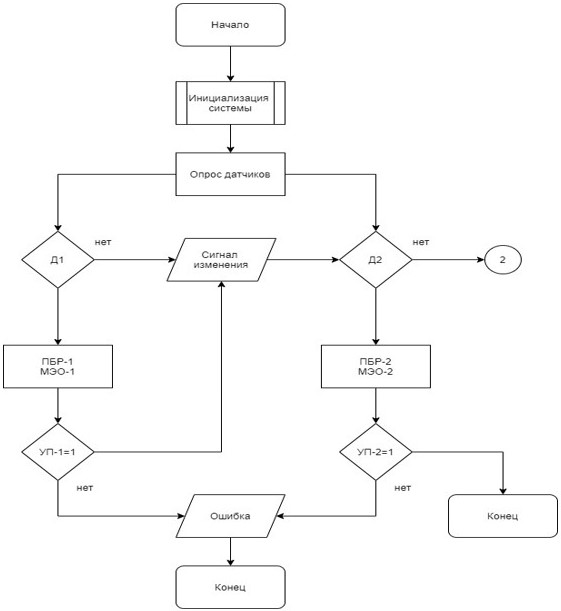
Малюнок 6 - Блок-схема алгоритму роботи системи автоматичного контролю завантаження доменної печі
Принципова електрична схема автоматизації служить для зображення взаємного електричного зв'язку апаратів і пристроїв, дії яких забезпечує вирішення завдань автоматичного контролю, сигналізації та контролю технологічним процесом. Принципова електрична схема автоматичного управління, регулювання, сигналізації та живлення повинні бути виконані розгорнутим способом відповідно до вимог стандартів ЕСКД (єдиною системою конструкторської документації) за правилами виконання схем, умовним графічним позначенням, маркування ланцюгів і буквено-цифровими позначеннями елементів схем згідно відповідних ГОСТ 21404 – 85 та ін.
розроблена електрична схема системи автоматичного контролю завантаження доменної печі розгорнутим способом, де зображено на аркуші 3 графічної частини дипломного проекту.
Контроль завантаження шихти виконується рівнеміром УЛМ-11а1 працює за принципом ЛЧМ (FMCW) - радіолокатора. Це один з класичних методів безконтактного вимірювання відстані, що дозволяє мінімізувати вплив паразитних перешкод і перешкод, пов'язаних з нерівностями (хвилюваннями) поверхні вимірюваного продукту. Виникнення сигналу по імпульсних лініях надходить на датчик типу "УЛМ-11а1" (поз. 5P1, 5P2) з мікропроцесором обробкою.
безконтактний радарний рівнемір УЛМ-11а1 орієнтований на вирішення загальнотехнологічних завдань вимірювання рівня в різних резервуарах з рідкими продуктами і сипучими матеріалами.
в роботі датчиків рівнемір УЛМ-11а1 використовують мікропроцесори, тому датчики є інтелектуальними. Мікропроцесори дають датчикам ряд переваг: конфігурація і зміна діапазону вимірювання, регулярна компенсація впливу навколишнього середовища, поліпшена робота, дистанційне керування датчиком, отримання Дистанційно інформації про діагностику. Ці переваги швидко окупають витрати.
Датчики тиску УЛМ-11а1 мають 0.50%, 0.25%, 0.15% і 1.5% класи точності.
живлення датчиків тиску УЛМ-11а1 здійснюється від блоку живлення Карат-22 (поз. Б1) напруги 24В постійного струму. Вихідний струм сигналу УЛМ-11а1 4-20мА, пропорційно для контролю рівня шихтового матеріалу, сигнал надходить на відповідні виходи програмного контролера ПЛК63 від фірми ОВЕН (поз. А1). Живлення програмного контролера здійснюється від мережі змінного струму 220В.
вихідні струмові сигнали 4 - 20 Ма, пропорційно витраті доменного надходять на відповідні входи програмованого контролера типу ПЛК63 від фірми ОВЕН (поз. Al). З датчики УЛМ-11а1 для вимірювання витрати шихти (поз. 5р1) виводять два аналогових сигналу (Р-7, Р-8) йдуть на вхід ПЛК, а саме (AI1, AI2). Датчики УЛМ-11а1 для вимірювання витрати шихти в колошнику (поз. 5Р2) виводять два аналогових сигналу (Р-9, Р-10) йдуть на вхід ПЛК, а саме (ai3, ai4). Живлення програмованого контролера типу ПЛК63 здійснюється від мережі змінного струму напругою 220 В.
У даній системі застосовуємо пряме цифрове управління на базі контролера ПЛК63 від фірми ОВЕН. Це програмований логічний контролер вищого класу, призначений для вирішення складних завдань автоматизації технологічних процесів, і може застосовуватися практично у всіх галузях промисловості. Контролер має 8 аналогових входів з позначенням (AII, AI2, AI3, ai4, IFS, ai6. I7. AI8) і точно така ж кількість дискретних (DI1, DI2, DI3, DI4, DI5, DI6, DI7, DI8). Кількість виходів всередині контролера 6. Кількість дискретних виходів 1 (DO1). Кількість аналогових виходів 4 (АО1, АО2, АО3, AO4, ao45) центральний процесор 32-розрядний, RISC 50 МГц на базі ядра ARM7. Розмір Retain-пам'яті (EEPROM) 448 байт. Об'єм оперативної пам'яті для зберігання змінних програм 10 кб. обсяг пам'яті зберігання програм 280 кб. Обсяг пам'яті введення-виведення 600 байт.
на корпусі присутні елементи людино-машинного інтерфейсу, дисплей текстовий монохромний РКІ з підсвічуванням кількість знакомест (символів) 2 x 16. Кнопки управління на лицьовій панелі 6 штук: "Пуск/стоп", "вихід", "Альт", "введення", "вгору", "Вниз". Контролер має наступні найважливіші функції і характеристики:
- дуже висока швидкодія;
- мультипроцесорний режим роботи; < / p>
- функції діагностування та діагностичний буфер:
- вбудовані функції для відображення (управління);
- програмне параметризоване модулів;
- можлива робота без примусової вентиляції;
- висока стійкість до вібрації; < / p>
- функції годинника, лічильник часу роботи, копіювання даних;
- обробка помилок;
- вбудований інтерфейс, придатний для простих мережевих рішень.
ПЛК63 програмний логічний контролер вищого класу якості для вирішення складних завдань автоматизації технічних процесів. Основні області застосування ОВЕН ПЛК63-ЖКГ, ЦТП, ІТП, котельні, невеликі установки.
Для зміни рівня шихтового матеріалу в контролері відповідно до алгоритму, відбувається обчислення керували впливів для закону регулювання. Керуючі впливу модуля виведення дискретних сигналів МР1 (поз. А2) до контролера через пускач безконтактний Реверсивний типу ПБР-3а (поз. 2Р7, 3Р7, 4Р7, 5Р7).
Вхідним сигналом пускачів є напруга негативної полярності, що подається щодо контакту 8 на вхід "М" (контакт 7) або вхід "Б" (контакт 9). Позначення " М "(менше) або" Б " (більше) прийняті умовно.
Для здійснення управління пускачем за допомогою ключів в пускачі є джерело напруги, позитивний потенціал якого виведений на клему 8, негативний – на клему 10.
За допомогою ключів контакт 10 підключається до входу "М" або "б".
У вихідному стані (вхідні сигнали відсутні) напруга на емітері V17 менше напруги включення за рахунок малої величини опору резисторів R7, R20, що зменшують напругу на емітері через позитивний висновок діодного моста v33...V36.
У зв'язку з цим транзистори V13 і V14 закриті, керуючих імпульсів на трансформаторах Т2 і Т3 немає. Тріаки V4 ... V7 закриті. Напруга на виході відсутня.
Ури подачі керуючої напруги на клеми 8-7 (8-9) відбувається заряд конденсаторів С1 (С2) і С3, що виконують функції фільтрів і елементів схеми затримки на реверсі. Протікання струму через резистори R7, R20, негативний висновок діодного моста V33...V36 і діод V10 (V11) призводить до збільшення падіння напруги на резисторах r7 і R20 і відкриття діода негативного висновку діодного моста v33...V36. В результаті цього на базі транзистора V13 (V14) напруга зменшується, відбувається заряд конденсаторів С3 і С7 і збільшення напруги на базі транзистора v14 (V13) і емітер транзистора V17 щодо бази 1 транзистора v17.
Ури досягненні напругою на емітері транзистора V17 напруги включення транзистор відкривається, і конденсатор С7 розряджається по ланцюгу: резистор R10, перехід база-емітер транзистора V14 (V13), діод V16 (V15), перехід емітер-база транзистора v17 і негативний висновок діодного моста v33...V36.
Струм розряду конденсатора, що протікає через базу транзистора V14 (V13), посилюється їм і в трансформаторі Т2 (Т3) формується імпульс, що відмикає тріаки V4 (V5) і v7 (v6). Процес заряд-розряд конденсатора С7 повторюється періодично і припиняється тільки після зняття вхідного сигналу. Тріаки V4 (V5) і V7 (V6) також відкриті до зняття вхідної напруги. Тріаки силового ланцюга служать для подачі напруги на електродвигун.
Конденсатор С4 і резистори R8, R9 призначені для поліпшення умов комутації тріаків.
Пускач захищений від одночасного відмикання всіх тріаків, викликаного подачею напруги на обидва входи, або швидким реверсом напруги управління.
Пускач містить варистори R32...R35 для захисту тріаків від перенапруги при комутації синхронних електродвигунів.
Пускачі ПБР-3а містять схему захисту електродвигуна від перевантаження. Схема захисту забезпечує відключення електродвигуна механізму при виході вихідного органу механізму на упор або при заклинювання його в проміжному положенні.
Вхідний сигнал схеми захисту – струм електродвигуна.
Вихідна напруга трансформаторів струму Т4 і Т5 через діоди V41...V44, резистор R22 подається на конденсатор С11. Якщо конденсатор зарядиться до напруги відмикання транзистора V25, транзистор відкриється, зменшиться потенціал емітера транзистора v22 (при практично постійній напрузі на базі цього транзистора).
Транзистор V22 відкриється і зашунтирует ланцюг харчування емітера транзистора V17, формування імпульсів припиниться. У такому положенні схема залишається до зняття вхідної напруги з входу пускача.
Пускач розрахований на підключення електродвигунів різної потужності, тому передбачено зміну струму спрацьовування захисту зміною положення движка потенціометра R29, розташованого на передній панелі пускача.
Виконавчі механізми електричні однооборотні типу МЕВ-1600 складається з наступних основних частин: редуктор, трифазний електродвигун, блоків струмових датчиків, електромагнітне гальмо. Принцип роботи механізмів заснований на припиненні електричного сигналу, що надходив від пускачів, в обертальне перемеження.
Редуктор є основним вузлом механізму, на якому встановлюються складові частини механізму.
Редуктор складається з корпусу, циліндричних прямозубих ступенів, ручного приводу, гальма.
Ручний привід служить для переміщення вихідного валу (регулюючого органу) при монтажі та налаштуванні механізмів, а також в аварійних ситуаціях (відсутності напруги живлення).
Переміщення вихідного валу механізмів здійснюється обертанням маховика ручного приводу. Наявність планетарної передачі в редукторі механізмів дозволяє використовувати ручний привід незалежно від включення або виключення електродвигуна.
На механізмах встановлені електродвигуни асинхронні трифазні. У виконавчому механізмі застосовується блок струмових датчиків типу БСПТ-10, вихідний сигнал з якого 4-20мА надходить на покажчики положення цифровий типу МТМ-310 (поз. 2Р9, 3р9, 4Р9, 5р9) на вихід ПЛК (поз. Р11, Р12, р13, Р14) тим самим сигналізує на скільки зараз відкритий конус. У механізмі застосовується блоки датчиків БСПТ-10, які складаються з двох струмових датчиків переміщення, профільного кулачка, чотирьох мікровимикачів, чотирьох кулачків мікровимикачів вала. Всі елементи закріплені на корпусі боки датчиків
Для обмеження величини вибігу вихідного валу і запобігання переміщення його від зусилля регулюючого органу при відсутності напруги на електродвигуні в механізмі передбачений механічний гальмо.
Виконавчий механізм управління закриттям конусом поки не стане рівним заданого значення.
Дія цифрового покажчика положення заснований на аналого-цифровому перетворенні значення, зазначених на цифровому індикаторі людиною, відповідно значення вихідного струму.
Живлення цифрового покажчика здійснюється від напруги 24В постійного струму з допомогою групового блоку живлення МТМ-140 (поз. Б2).
Висновок
Магістерська робота присвячена актуальній науковій задачі є підвищення ефективності якісного технологічного процесу завантаження колошникового пристрою доменної печі шляхом розробки системи автоматичного управління, а також контролю і регулювання основних технологічних параметрів даного об'єкта управління. В рамках проведених досліджень виконано:
- Аналіз технологічного процесу завантаження колошникового пристрою доменної печі як об'єкта автоматизації;
- Розглянуто доменну піч як об'єкт автоматичного керування;
- Аналіз існуючих розробок по автоматизації доменної печі;
- Обґрунтовано напрямки автоматизації доменної печі;
- Розроблено структурну схему управління, функціональну схему автоматизації, а також алгоритми технологічного процесу доменної печі.
При написанні даного реферату магістерська робота ще не завершена. Остаточне завершення: Червень 2023 року. Повний текст роботи і матеріали по темі можуть бути отримані у автора або його керівника після зазначеної дати.
Список джерел
- Автоматизація основних металургійних процесів. Липухин Ю.В., Булатов Ю. І., Бок Г., Кнорр М. М.: Металургія, 1990. 280 с.
- Харахнін К. А., Булатов ю. і., Мочлаін В. Н. Автоматизація доменного виробництва: Учеб. Посібник. - Череповець: ГОУ ВПО ЧГУ, 2015. - 70с.
- Електричне обладнання доменних цехів. АГРОНІК С.Г., Влатт М. Ю., Скрильников С. В., Москва «Металургія», 1966. 196 с.
- Котов К.і., Шершевер М. А. засоби вимірювання, контролю та автоматизації технологічних процесів. - М.: Металургія, 1987. - 496 с.
- Громаков є.і. проектування автоматизованих систем: навчально – методичний посібник. - Томськ: Томський політехнічний університет, 2010. - 173 с.
- Глинков, г.м. АСУ ТП в чорній металургії: Підручник для вузів. / Г.м. Глинков, В. А. Маковський – 2-е вид., перераб. і дод. - м. « "Металургія", 1999. - 310 с.
- Офіційний сайт Донецького металургійного заводу [Електронний ресурс]: Режим доступ: http://dmz.donetsksteel.com/ru/company (Дата обвалення 25.05.2021)
- Доменне виробництво [Електронний ресурс]: Режим доступ: https://metalspace.ru/education-career/osnovy-metallurgii/domennaya-pech/810-domennoe-proizvodstvo.html (Дата обвалення 25.05.2021).
- Кісарімов, Р.А. Електропривод: довідник. / Р.А. Кісарімов, Москва, ІП Радіософт, 2008.- 391 с.
- Вейкерлі Д.проектування цифрових пристроїв / Д. Вейкерлі. - М.: Постмаркет, 2002. – Том 2. - 528 с.