Реферат по теме выпускной работы
Содержание
- Введение
- Область применения, назначение, индексация, классификация валковых
- Конструкция и принцип работы двухвалковых дробилок
- Заключение
- Список источников
Введение
Строительные машины в настоящее время неотъемлемая часть в любой сфере косвенно или прямо связанной со строительством. Они позволяют улучшить и проконтролировать качество строительства, ускорить сроки строительства, облегчить труд человека.
В строительстве ежегодно потребляется большое количество каменных материалов: щебня, гравия и песка. Большая часть этих материалов используется на приготовление бетона. Добыча песка и гравия производится в естественных отложениях механическим или гидравлическим способом, а щебня из естественного камня путем дробления взорванных скальных пород. Добываемые каменные материалы перерабатываются на камнедробильных и промывочно-сортировочных заводах, а затем в виде готового продукта стандартного качества доставляются потребителю.
Во многих отраслях промышленности строительных материалов керамической, стекольной, цементной и других широкое распространение получили валковые дробилки, предназначенные для крупного, среднего, мелкого и тонкого измельчения материалов малой и средней прочности, удаления из глины каменистых включений и т.д.
Область применения, назначение, индексация, классификация валковых дробилок
Дробилка валковая — обогатительное дробильное оборудование, оснащённое валками с закреплёнными на них зубчатыми сегментами, имеющими форму многогранника, жестко насаженного на вал. Дробилки валковые широко применяются для тонкого, среднего и мелкого измельчения различных горных пород, пищевых продуктов и химических материалов (глинистые материалы, шамот, кварц, шпат, и пр.).
Принцип действия этих мельниц состоит в измельчении материала в основном раздавливанием, частично – истиранием, ударом или изгибом между двумя параллельными цилиндрическими валками, вращающимися навстречу друг другу с одинаковой скоростью.
Для хрупких и мягких материалов (например, уголь, соль) применяют зубчатые валковые дробилки. Они захватывают куски, которые только в 1,5-4 раза меньше диаметра валка.
Дробилки с гладкими и рифлеными валками обычно применяют для дробления материалов средней прочности (до сж = 150 МПа); дробилки с зубчатыми валками – для измельчения каменного угля и подобных материалов малой прочности (до сж = 80 МПа). Крупность продукта дробления валковой дробилки зависит как от размера выходной щели между валками, так и от типа поверхности рабочих органов. В мировой практике валковые дробилки используют, как правило, на заключительных стадиях дробления (среднее и мелкое дробление).
Существенным недостатком валковых дробилок является интенсивное и неравномерное изнашивание рабочих поверхностей валков (бандажей) при обработке прочных и абразивных горных пород. Бандаж изнашивается в основном в средней части валка, что не дает возможности поддерживать стабильный размер выходной щели по всей ее длине. Кроме того, валковые дробилки обладают сравнительно невысокой удельной производительностью.
Валковые дробилки классифицируются следующим образом.
По назначению и форм рабочей поверхности:
- для тонкого, мелкого и среднего дробления материалов – с гладкой поверхностью валков, с продольными полукруглыми выемками на одном из валков;
- для крупного дробления глинистых материалов с зубчатыми валками;
- для среднего и мелкого дробления глинистых материалов и удаления камней – с одним гладким и другим рифленым валками и с валками, имеющими винтовую поверхность.
По методу установки подшипников валков:
- с одной парой подвижных и одной парой неподвижных подшипников;
- с неподвижно установленными подшипниками;
- с подвижно установленными подшипниками у двух валков.
По количеству валков в дробилках:
- с одной;
- с двумя;
- с четырьмя.
По устройству привода:
- с редукторным приводом и карданными валами;
- с шестеренчатым приводом;
- с ременной передачей
- с редукторным приводом и ременной передачей
Конструкция и принцип работы двухвалковых дробилок
Дробилки с одним подвижным валком (рис. 1, а) наиболее распространены. Почти во всех существующих конструкциях валковых дробилок один из валков установлен в подвижных подшипниках, скользящих по направляющим. Подшипники удерживаются на месте пружинами, сжимаемыми при помощи специальных болтов. При попадании посторонних предметов пружины под увеличивающейся при этом нагрузкой дают осадку, зазор между валками увеличивается и инородное тело выпадает из дробилки. Далее, под действием пружин подшипники с валком возвращаются в исходное положение.
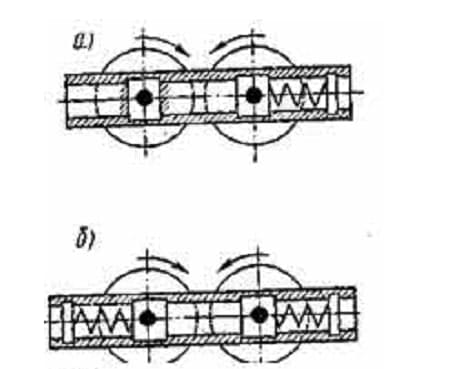
Рисунок 1. Схемы дробилок
В дробилках с подвижно установленными подшипниками (рис. 1, б) обе пары подшипников подвижные, упираются в пружины, и поэтому при попадании посторонних предметов оба валка раздвигаются и пропускают инородные тела. Так как валки, расходясь, движутся в противоположном направлении с одинаковой скоростью, а возникающие при перемещении валков силы инерции взаимно уравновешиваются, то дробилки этого типа работа относительно спокойно и их называют уравновешенными. Однако этот тип дробилок вследствие сложности конструкции и дороговизны не нашел широкого применения.
Дробилка состоит из двух валков, вращающихся навстречу друг другу и закрепленных на валах 2, опирающихся на подшипники. Одна пара подшипников 3 закреплена на раме неподвижно, а вторая 4 может передвигаться вдоль рамы. При этом корпуса этой пары подшипников постоянно прижаты к упорам пружинами 5. Между упорами и корпусами подшипников ставятся сменные стальные прокладки, регулирующие величину зазора между валками.
Привод валков осуществляется от электродвигателя (или трансмиссии) через ременную передачу. При наличии зубчатой передачи зубья второй пары делаются удлиненными по высоте, с тем чтобы можно было обеспечить зацепление при отходе подвижного валка.
Широко распространенная до последнего времени «традиционная» двухвалковая дробилка (рис. 1). Шкив 2 дробилки приводится во вращение электродвигателем, далее через одноступенчатый редуктор, закрытый кожухом 8, вращение передается первому рифленому валку 3, корпуса подшипников которого неподвижно прикреплены к раме 1 дробилки. Подшипники 7 второго гладкого валка 4 прижаты к упору амортизационными пружинами 5 и могут перемещаться, сжимая пружины, увеличивая зазор между валками и пропуская недробимый предмет. Вращение от первого (ведущего) валка передается второму (ведомому) валку с помощью шестерен с удлиненными зубьями, допускающими изменение межцентрового расстояния между валами валков. Шестерни вращаются в масляной ванне и закрыты кожухом 6.
В последнее время появились конструктивные решения, в которых каждый валок приводится от электродвигателя или через редуктор 3 и карданные валы 4.
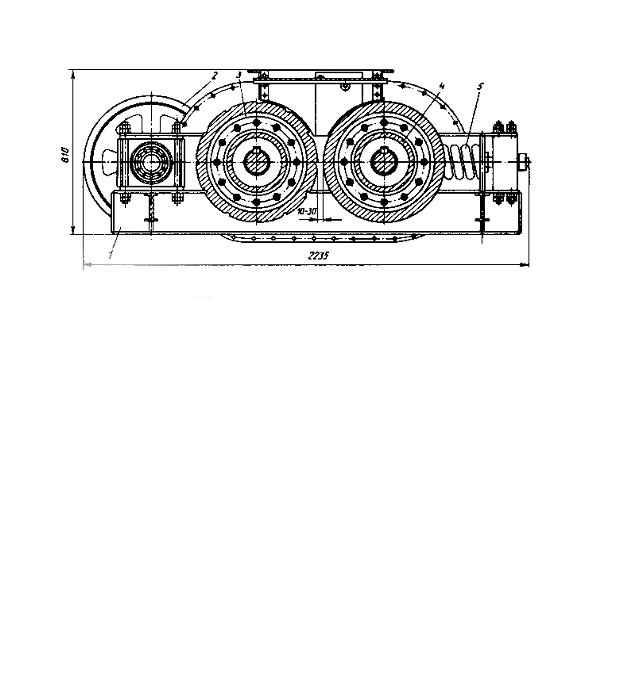
Рисунок 2. Двухвалковая дробилка с рифленым и гладким валками.
Валковая дробилка (рис. 3), имеет два валка, один из которых гладкий, другой – рифленый. Подшипники одного из валков прикреплены к корпусу 5 дробилки, подшипники другого – к подвижной раме 3, соединенной шарниром 4 с корпусом. В верхней части корпус и рама связаны между собой предохранительным механизмом 1, состоящим из системы тяг и пружин, позволяющих регулировать зазор между валками, а также допускающих расхождение валков при попадании недробимого предмета. В этом случае валок вместе с подвижной рамой и установленным на ней электродвигателем поворачивается вокруг шарнира, и зазор между валками увеличивается. После прохождения недробимого предмета пружины возвращают валок в первоначальное положение. Усилие, необходимое для дробления материала, обеспечивается предварительным поджатием пружин.
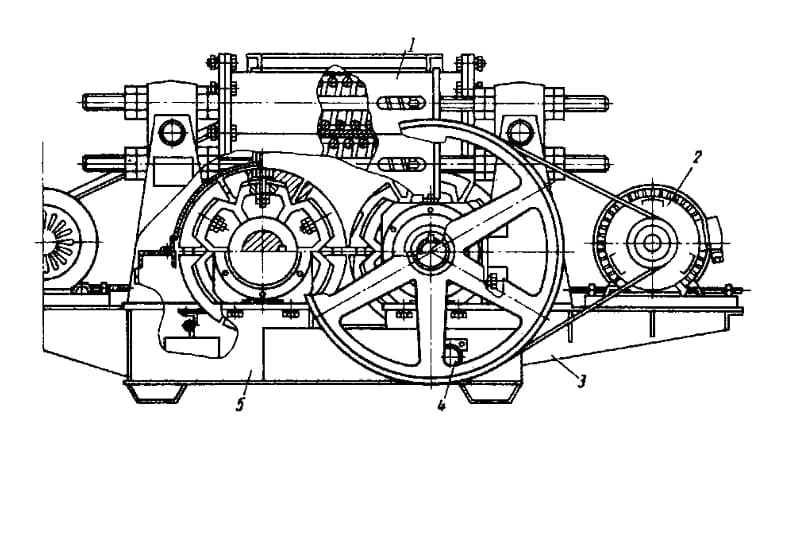
Рисунок 3. Двухвалковая дробилка с раздельным приводом валков.
Дробилка ДДЗ-6 состоит из следующих элементов (рисунок 11): 1-механизм регулировки выходной щели, 2-валки, футерованные зубчатыми бандажами, 3-приводной электродвигатель, 4,5-подшипникове опоры, 6-рама, 7-приемная воронка, 8-предохранительный механизм. Привод осуществляется клиноременной передачей от отдельно устанавливаемого электродвигателя. Вращение передается на приводной вал, а затем через синхронизатор на тихоходные валки – подвижный и неподвижный.
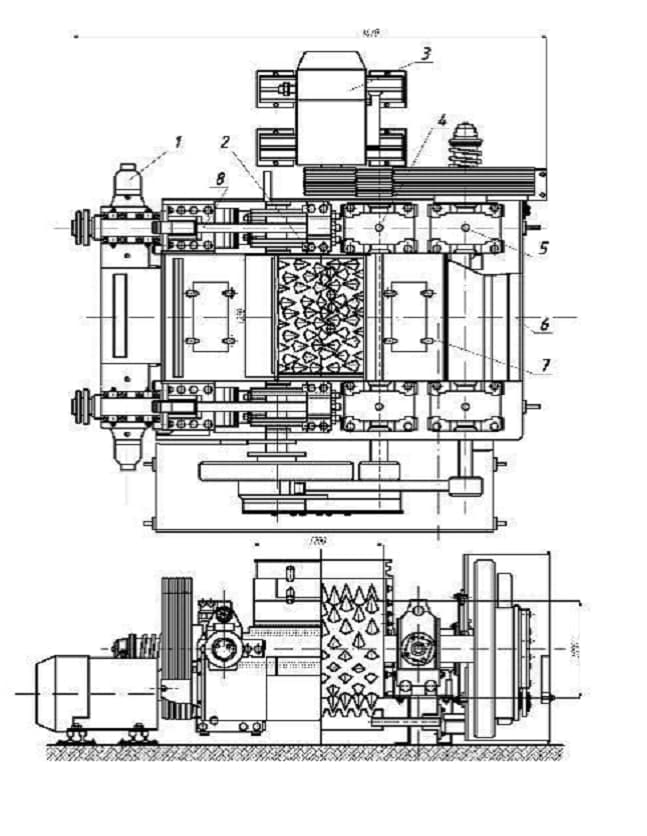
Рисунок 11 Валковая дробилка ДДЗ-6
Первоначально конструкция амортизирующего устройства двухвалковых зубчатых дробилок состояла из одной или нескольких (их число доходило до девяти в одном блоке) стальных цилиндрических пружин с каждой стороны. Однако при эксплуатации дробилок с такими амортизирующими устройствами было установлено, что при работе дробилки возможен перекос вала подвижно- го валка по причине либо неодинаковой жёсткости пружин, либо односторон- ней (не по центру) загрузки питания дробилки. Перекос вала ухудшает техно- логические показатели дробилки, повышает расход мощности и может привес- ти к поломкам.
Для избежания перекоса подвижного валка предпринималась попытка со- единить корпуса подшипников подвижного валка одним коромыслом с уста- новкой общей амортизирующей пружины. Однако этот вариант амортизирующего устройства не получил развития из-за существенного увеличения массы дробилки.
В серийно выпускаемых в 60-х годах прошлого века дробилках ДДЗ-1М, ДДЗ-2М и ДДЗ-4М (рис. 5) наибольший ход подвижного валка соответственно составлял 40, 55 и 60 мм, что было недостаточно для обеспечения надёжной ра- боты машины.
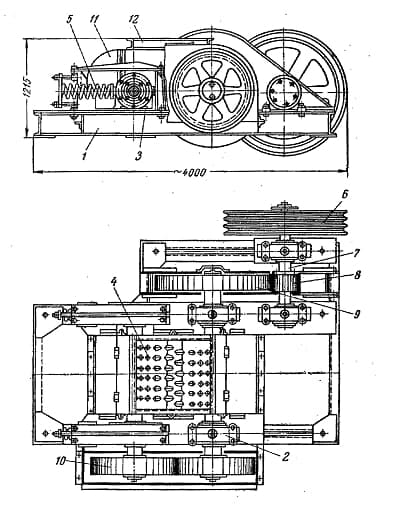
Рисунок 14 – Дробилка двухвалковая зубчатая ДДЗ-4 [2]: 1 – рама; 2, 3 – корпус подшипника; 4 – валок; 5 – пружина; 6 – шкив; 7 – вал; 8 – шестерня; 9 – колесо; 10 – синхронизатор; 11 – кожух; 12 - воронка
Основной причиной такого небольшого хода объяснялось тем, что для каждой дробилки величина хода принималась такой, чтобы при наибольшем за- зоре между валками зубчатое колесо привода вращения подвижного валка не вышло из зацепления. Вызвано это конструкцией синхронизатора вращения валков в качестве которого применялись зубчатые колёса с увеличенной длиной зуба. Поэтому, если хода было недостаточно для пропуска недробимого куска и он заклинивается между валками, то срезалась предохранительная шпилька, установленная в ступице шкива-маховика. Во избежание перегрузки пружин при заклинивании валков ход подвижных подшипников ограничен специальным упором, имеющимся в станине отжимного устройства.
В дальнейшем амортизирующие устройства двухвалковых дробилок, как и конструкции синхронизатора, непрерывно совершенствовались. На рис. 5 приведен один из вариантов амортизирующего устройства, используемый в дробилке типа ДДЗ с увеличенным ходом подвижного валка.
Цилиндрические стальные пружины использовались в амортизирующих устройствах двухвалковых дробилок типа ДДЗ или ДДЗЭ-9×9, но в ряде дроби- лок (некоторые модификации дробилок ДДЗ, ДДЗЭ-15×12 и др.) применялись тарельчатые пружины [4]. Так, в дробилках типа ДДЗ 70-х годов прошлого века амортизирующее устройство (рис. 5) [4] включало в себя две тяги 12, один конец которых устанавливался на корпусе 13 подшипника подвижного валка, а второй конец снабжался зубчатой рейкой 14, находящейся в контакт с зубчатым колесом 15, на оси которого находилась кулачковая муфта 16. В устройстве применялись тарельчатые пружины 17. Параллельное перемещение подвижного валка обеспечивалось двумя звёздочками 18 и цепью 19.
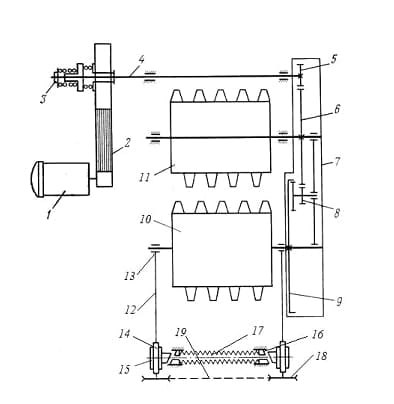
Рисунок 15 – Кинематическая схема дробилки двухвалковой зубчатой ДДЗ: 1 – электродвигатель; 2 - клиноременная передача; 3 – предохранительная муфта; 4 – вал приводной; 5 – 9 – элементы синхронизатора (передаточного механизма); 10 – валок подвижный; 11 – валок неподвижный; 12 – тяга; 13 – корпус подшипника подвижного валка; 14 - зубчатая рейка; 15 – зубчатое колесо; 16 – кулачковая муфта; 17 – пружина; 18 – звёздочка; 19 - цепь
При попадании между валками недробимого материала срабатывает амортизирующее устройство, и подвижный валок 10 отходит. Корпуса под шипников 13, скользя по круглым направляющим, передвигают рейки 14, которые вращают зубчатые колёса 15 пружинного амортизатора и сжимают пружины 17. Недробимый материал проходит между валками, и пружины 17 возвращают назад весь валок 10. Если же валок 10 отошёл более чем на 200 мм, то корпус 13 подшипника воздействует на концевой выключатель, установленный на одной из стоек, который выключает электродвигатель. Номинальная величи- на поджатия пружин 17 амортизатора должна быть 35 мм с каждой стороны. С уменьшением степени поджатия дробилка становится более чувствительной к крупным кускам угля, а также к недробимым предметам [4].
На рисунке 16 приведена современная конструкция амортизирующего уст- ройства дробилки ДДЗ [6].

Рисунок 16 – Амортизирующее устройство современных дробилок ДДЗ: 1 – винт; 2, 5 – крышка; 3 – цапфа; 4 – рычаг; 6 - планка; 7 – вал; 8 – подшипник; 9 – пружина; 10 – звёздочка; 11 – цепь; 12 - гайка
Устройство амортизирующее включает в себя винт 1, который соединён с одной стороны при помощи крышки 2, с корпусом отклоняющегося валка, с другой – с цапфой 3, установленной на рычаге 4, при помощи крышки 5. Рычаг планкой 6 крепится на валу 7, который установлен в подшипниках 8. Между подшипниками на валу при помощи шпонок закреплены кулачки, соединённые с пружинами 9. На конце винта установлена звёздочка 10, вращением которой осуществляется регулирование размера разгрузочной щели между валками. Одновременно со звёздочкой вращается винт 1, который через крышку 2 перемещает отклоняющийся валок. Параллельное перемещение отклоняющегося валка обеспечивается тем, что звёздочки 10 соединены между собой цепью 11. Предварительное поджатие пружин 9 осуществляется при помощи гаек 12.
К достоинствам пружинных амортизаторов можно отнести:
- конструктивную простоту;
- способность выдержать огромные нагрузки;
- cлабое влияние среды на работу амортизаторов.
Однако из-за больших усилий (5...10 кН на 1 см валка) пружинные блоки механических амортизирующих устройств зубчатых дробилок получаются сложными, массивными и громоздкими. Поэтому, все операции по наладке уст- ройства (затяжке пружин, изменению размера щели) становятся достаточно трудоёмкими.
Гидропневматические амортизирующие устройства позволяют быстро регулировать размер выходной щели, в большом диапазоне изменять жёсткость упругого элемента, а также обеспечивать синхронный отход корпусов подшип- ников подвижного валка при внецентренном прохождении недробимого предмета. Надежно защищая дробилку от поломок, гидропневматическая «пружи- на» практически не изнашивается.
Применение гидропневматических амортизаторов позволяет устранить большинство из недостатков механических амортизаторов, а также увеличить надёжность валковых дробилок.
Так, авторы изобретения [5], предложили гидропневматический аморти- затор (рис. 8), включающий гидроцилиндры 1 с поршнями 2, крышки 3, гидро- пневматический аккумулятор 4, дроссельный клапан 5, зубчатые рейки 7 и зуб- чатые колёса 8, установленные на валу 9. Для обеспечения быстрого и безудар- ного отхода подвижного валка 6 дробилки при попадании недробимого предме- та, поршни 2 выполнены с уступами, входящими в соответствующие им выемки крышек гидроцилиндров 1 и образующих при этом замкнутую полость. Дроссель 5 установлен на трубопроводе, соединяющем полости А гидроцилиндров 1 с атмосферой.
При попадании недробимого предмета валок 6 отходит, перемещая поршни 2, которые вытесняют жидкость из гидроцилиндров 1 в аккумулятор 4, заполненный азотом. После прохода недробимого предмета валок 6 быстро возвращается в прежнее положение под действием сжатого азота, который выдавливает жидкость в гидроцилиндры 1. При этом некоторый объём воздуха запирается и сжимается в полости Б между уступами поршней 2 и выемками крышек 3, что предотвращает удар.
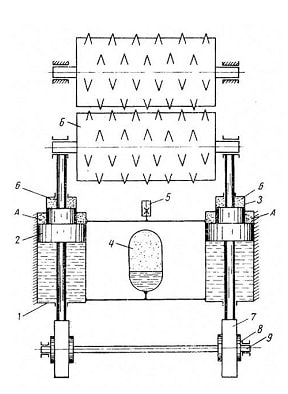
Рисунок 17 - Гидропневматический амортизатор двухвалковой дробилки [7]: 1 – гидроцилиндр; 2 – поршень; 3 – крышка; 4 – гидропневматический аккумулятор; 5 - дроссельный клапан; 6 - подвижный валок; 7 - зубчатая рейка; 8 - зубчатое колесо; 9 – вал
В конструкции амортизирующего устройства гидропневматического типа целесообразно объединить предохранительную функцию и возможность регу- лирования размера щели. На рис. 9 изображена гидравлическая схема двухвал- ковой дробилки с этими свойствами.
Насос 2 с постоянным направлением потока всасывает жидкость из бака 1 и нагнетает её в гидроцилиндр 5 через распределитель 3 и гидрозамок 4. В по- зиции А распределителя 3 жидкость поступает в левую полость гидроцилиндра 5, перемещая поршень вправо (расстояние между валками уменьшается). В по зиции В распределителя 3 напорная линия соединяется с правой полостью гид роцилиндра 5, (расстояние между валками увеличивается). В средней позиции распределителя 3 напорная линия запирается, а оба отвода А и Б соединяются с баком 1, благодаря чему гидрозамок 4 запирает полости гидроцилиндра. Амор- тизация подвижного валка осуществляется с помощью гидропневматического аккумулятора 6. В случае перегрузки системы, рабочая жидкость сливается че- рез предохранительный клапан 7.
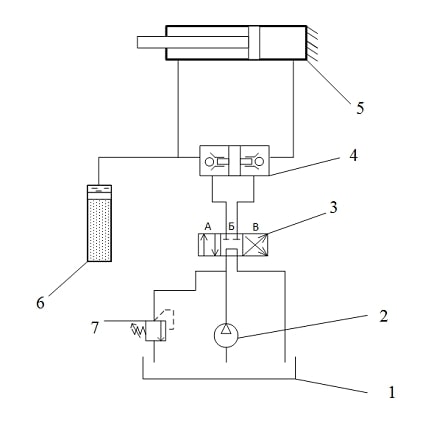
Рисунок 18 - Гидросхема амортизации и регулирования расстояния между валками двухвалковой дробилки
Рассматриваемая схема обеспечивает малошумность работы амортизи рующего устройства, установка становится менее габаритной, гидросистема одновременно выполняет амортизирующую функцию и функцию изменения расстояния между валками, сохраняет амортизационную способность.
Данное конструктивное решение значительно повысит надёжность и эф- фективность использования амортизации валковой дробилки. В то же время для правильной работы амортизаторов во избежание механических повреждений и перекосов необходимо обеспечить синхронизацию работы обеих гидроцилиндров. На рис. 10 и 11 приведены два варианта синхрони зации работы гидроцилиндров [4].
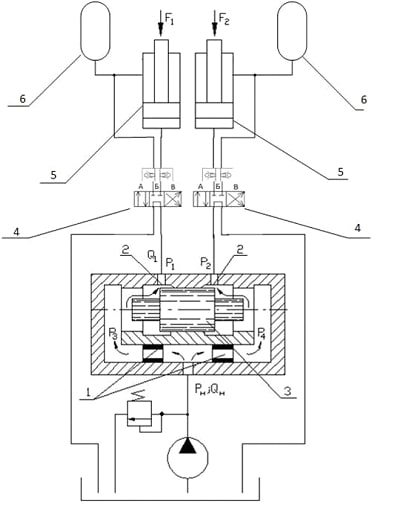
Рисунок 18 - Схема синхронизации с применением дроссельного делителя потока: 1 - балансные гидродроссели; 2 - регулируемые гидродроссели; 3 - плунжер; 4 - гидрораспределители; 5 - гидроцилиндры; 6 - аккумуляторы
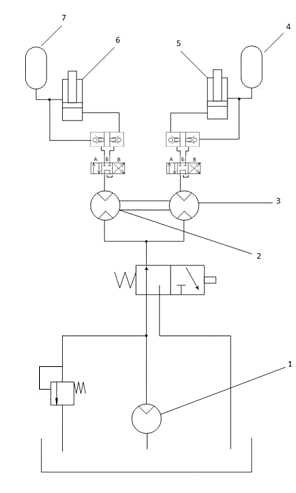
Рисунок 19 - Схема синхронизации с двумя роторными гидромашинами: 1- насос; 2, 3 – роторные гидромашины; 4, 7 – гидропневматический аккумулятор; 5, 6 –гидроцилиндры
Заключение
В работе [2] проанализированы конструкции дробилок можно и сделаны следующие выводы. Общим недостатком для всех дробилок является большая удельная металлоемкость и энергоемкость конструкций. Основная тенденция совершенствования дробилок, как видно из анализа патентных материалов и литературных источников, заключается в разработке энергосберегающих средств и технологий. Основным направлением повышения эффективности работы техники и комплексов машин являются увеличение производительности и снижение эксплуатационных затрат на поддержание их работоспособности, что может быть достигнуто на основе модернизации и создания новых машин при уменьшении их массы и габаритных размеров.
На рисунке 1 приведена схема конструкции дробилки с циклоидальным движением валков [3]. Кинематическая схема привода РО реализуется с помощью планетарного механизма Джеймса, который содержит центральное зубчатое колесо внутреннего зацепления, водило и сателлит (планетарный) внешнего зацепления, обкатывающийся внутри коронного зубчатого колеса. Водило получает вращение от приводного двигателя. Рабочий орган валковой дробилки соосно связан с сателлитом и совершает с ним планетарное движение, при этом вершины описывают ту, или иную гипоциклоиду.
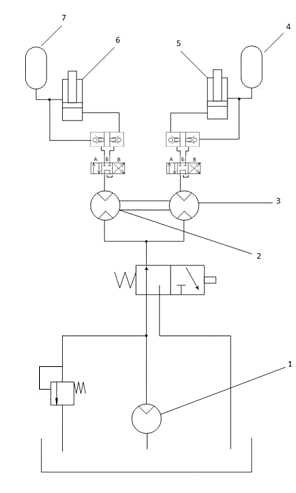
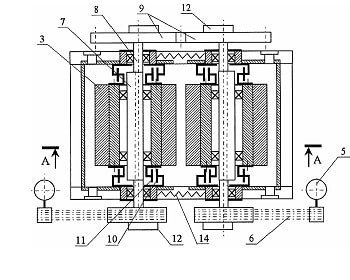
Список источников
- Богданов, В.С. Классификация валковых дробилок / В.С. Богданов, И.С. Яворская – Текст непосредственный // Энергосберегающие технологические комплексы и оборудование для производства строительных материалов. Межвузовский сборник статей. Том Выпуск XIV. Белгородский государственный технологический университет им. В.Г. Шухова; под ред. В.С. Богданова. Белгород, 2015. С. 152-154.
- Рабат, О.Ж. Выявление основных направлений в конструировании рабочих органов дробильных машин на основе анализа патентной информации / О.Ж. Рабат, А.Н. Салманова // Вестник КазАТК. – 2018. - № 1 (104). – С. 98-105.
- Рабат О.Ж., Ли С.В., Мурзахметова У.А., Нургалиева М.Р. Конструктивные особенности валковой дробилки со сложным движением рабочих органов // Транспортное, горное и строительное машиностроение: наука и производство. – 2018. – №1. – С. 38-44.
- Кондрахин, В.П. Анализ конструкций амортизирующих устройств двухвалковых зубчатых дробилок / В.П. Кондрахин, С.Л. Букин, А.А. Березин
- Пат. 93037015 РФ, МПК F03B13/12. Прибрежная силовая энергетическая установка / Гендель Е.Г. - Опубл. 1996.02.10.
- Молдаванов О.И. Метрологическое обеспечение трубопроводного строительства. М. : Недра, 1984. - 224 с. : ил.
- Остроменский П.И., Аксенов В.А., Атапин В.Г. Математическое моделирование в машиностроении: Учеб. пособие. - Новосибирск: НГТУ, 1993. - 81 с.
- Пат. 2089747 РФ, МКИ F03B13/12. Генератор электрической энергии для преобразования энергии морских волн / Миунг Шик Иим. - Опубл. 1997.09.10.