Abstract
Сontent
- Introduction
- 1. Relevance of the topic
- 2. The purpose and objectives
- 3. Review of research and development
- 4. Heat and mass transfer regimes and resource-furnace treatment of metal-cored wire
- Findings
- References
Introduction
The question of improving the quality of metall is an important issue in modern metallurgy. The question of continuous casting of steel deoxidized by aluminum, originated in the early 80s. Filling glasses delayed due to deoxidation by aluminum. This problem has hampered the use of continuous casting in steel production. To prevent the overgrowth of glasses needed to change the nature of alumina inclusions, provide them with the liquid state at temperatures of casting. This can be achieved controlled entry of calcium into the liquid steel.
The search for ways of introducing regulated calcium in steel led to a flux-cored wire for the steel industry - a thin-walled metal shell filled with compacted powder material.
Ladle treatment of steel-cored wire is the most efficient and modern method of deoxidation of liquid steel. Steel deoxidized with aluminum in modern metallurgy. But the deoxidation product - Alumina Al2O3 causes a sharp decrease in fluidity. After this delayed channels filling glasses. It is the main reason limiting the use of alumina for deoxidation of steel critical applications. The practice proved that the processing of steel, deoxidized Al and Ca addition makes it possible to eliminate this undesirable effect. His entry into the melt to reduce the oxygen content in very low values (up to ten-thousandths of %).
1. Relevance of the topic
Analysis of heat and mass transfer aspects of the technology-furnace treatment of steel with flux cored wire enables them to develop energy-saving modes. This contributes to the solution of pressing problems of energy saving in Ukraine. The analysis showed that the introduction of powder calcium alumino wire in the casting ladle is the most effective and economical way to deoxidation of liquid steel. (The scheme of the movement of metal during continuous casting of steel is shown in Figure 1).
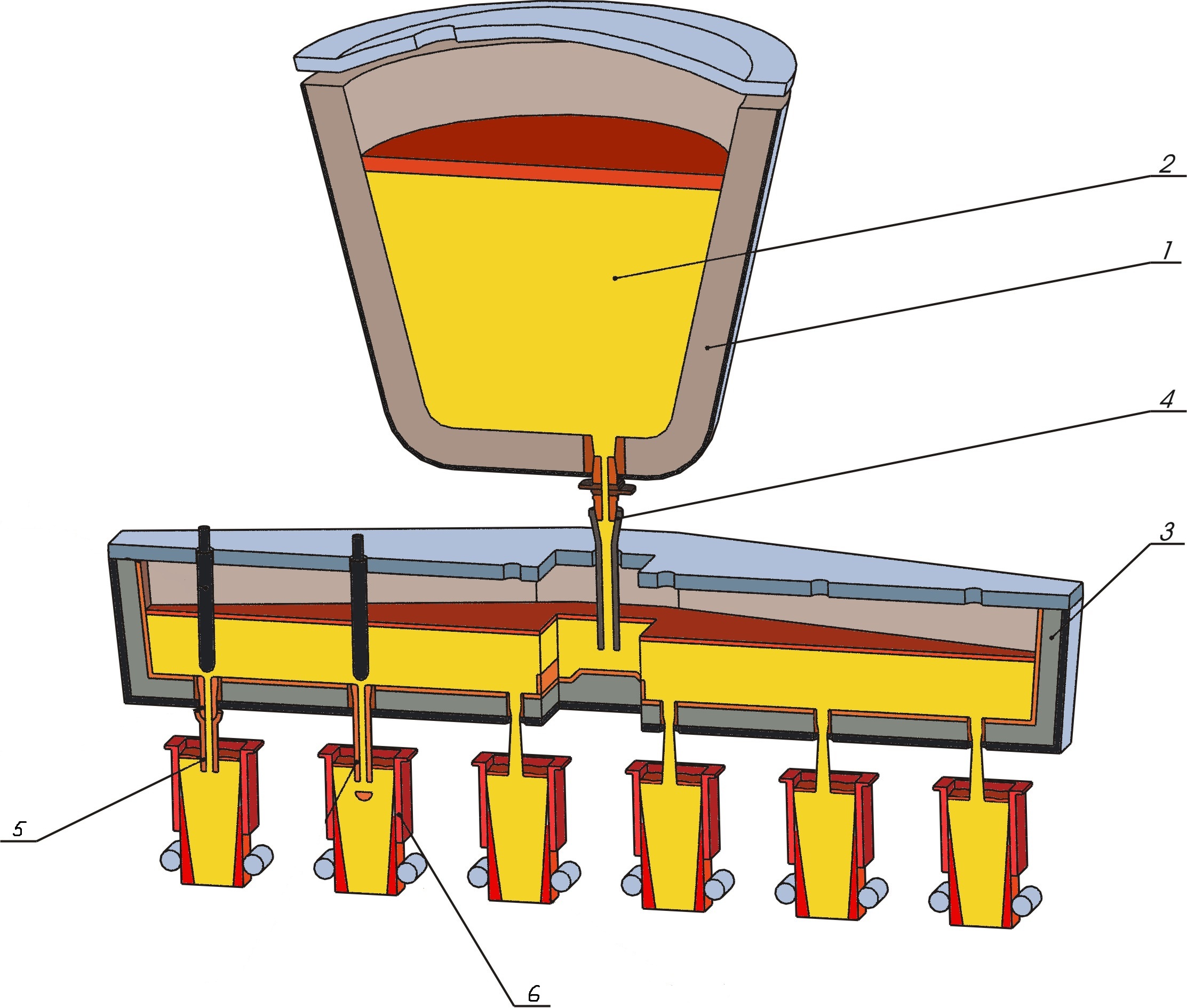
Figure 1 – The scheme of the movement of metal during continuous casting of steel
(1 – casting ladle, 2 – liquid metal, 3 – intermediate ladle, 4 – glass casting,
5 – dip cup, 6 – crystallizer)
Urgent is the development of energy efficient modes of technology based on the analysis of heat and mass transfer aspects, in particular, the development of semiempirical formula for the optimal (energy saving) the rate of supply of powder calcium alumino wire in molten steel to its deoxidation.
2. The purpose and objectives
The purpose of the work is to develop energy-saving modes furnace deoxidation of liquid steel powder calcium alumino wire, which is based on the analysis of heat and mass transfer aspects of the technology.
Objectives of work:
a) a review of the literature on the current state of the question;
b) the statement of objectives of the study;
c) familiarity with the finite difference method for calculating the heat equation;
d) investigation of heat energy and mass transfer aspects of the technology based on computer modeling;
e) development of energy-saving modes;
e) calculation of the expected economic effect;
g) study of environmental issues and safety.
3. Review of research and development
There is a need to develop the design and organization of production equipment for the processing technology were cored wires and putting them into the melt. Such equipment in the Soviet Union was carried out. Foreign wire feeder pricey and its characteristics are not consistent with the terms of steelworks (high dust, high temperature, etc.).
The work on the use of cored wire in Ukraine began in the early 1990s at the "Universal equipment" Technological line for production of cored wires include a set of standard and specially designed by the devices. This technology has had a large number of deficiencies. Therefore, priorities have been identified to improve technology-cored wires of various sizes. To solve this problem have been reviewed with all applicable calibration work rolls. Since 1992, the transition was made to manufacture wires only castle execution.
For different sizes of wire used symmetric and asymmetric calibration, providing a different relative position of the castle and the compensator. This approach is in contrast to the known solutions [1, 2] simplifies the configuration of the caliber and provides the stable introduction of a given quantity of powder filler.
To determine the optimal speed [14] entering cored wire, depending on the type of filler needed formulation and solution of the heat problem on the level (depth) of the melt. This is especially important when using flux-cored wire containing calcium and aluminum [3].
The effectiveness of the input flux-cored wire filled with calcium alumino greatly exceeds the SCAT-injection process and silicone calcium powder in a stream of argon through a lance. This method has an advantage even in comparison with the processing of steel powder silicone calcium wire and is characterized by the degree of absorption of calcium from the filler wire to be 29%.
In [4] identified the main parameters affecting the absorption of the input wire. The authors identified in a bath of liquid metal with the introduction of three levels of calcium powder in the bucket (levels of H1, H2, H3).
The most difficult problem of mathematical modeling of heat and mass transfer in the furnace metal processing is the problem of modeling of thermal processes in systems with moving boundaries of phase transition [11-13]. The question of a joint review processes in liquid and solid phases has been put in the work of Academician A. Lykov [5]. The method of calculation of the conjugate heat transfer problem is described in [6, 15]. An approximate solution of the boundary layer are presented in [7].
The authors [8] proposed analytical method for the heat equation for systems with moving boundaries. But there are many more efficient finite-difference methods using а personal computers. [9, 10].
4. Heat and mass transfer regimes and resource-furnace treatment of metal - cored wire
The mechanism of deoxidation are thought to be composed of the following sequence of steps: dissolving in a liquid bath powder filler wire, the formation and growth of oxide inclusions.
Before dissolving the powder filler wire, it should melt steel shell.
A mathematical model of heat transfer calcium alumino cored wire with molten metal includes the initial and boundary conditions.
The initial conditions:
а) T1 ≡ T3 ≡ T0 , б) R1 (0) = R2 (0) = R, в) R3 (0) = R + σ,
where T0 - Ambient temperature, ° C;
R - initial radius of boundary separating element, which is entered from the steel shell of wire;
σ - its thickness when τ = 0.
Consider the range of variation of the radial coordinate r in each of the regions (i = 1,2,3).
i=1: 0 ≤ r ≤ R1 (τ) = R + ΔR1 (τ) , ΔR1 < 0;
i=2: R1 (τ) ≤ r ≤ R2 (τ) ≡ R;
i=3: R ≤ r ≤ R3 (τ) = R+ΔR3 (τ), ΔR3 (0) = σ,
where the R1 - the boundary of the solid phase of the powder element that is introduced;
R2 - the limit of its liquid phase;
R3 - the outer limit of the steel shell.
The latter includes both the primary shell, and frozen on her solid steel crust. It is obvious that R3 > R3 > R1. In this case Δ R1 < 0, Δ R2 = 0.
Boundary conditions include the movement of phase boundaries in the process of melting the filler and the steel shell.
The complexity of the mathematical model consists in moving the boundaries of the phase transition and heat transfer processes in them. Therefore, the challenge is to develop a method of conjugate heat transfer problems. For this task, it was decided use the method of finite differences. Relations are derived for each of the zones of the phase transition.
Computer simulation of the interaction of flux-cored wire with a liquid bath revealed a decreasing dependence of the entering wire to the melt steel Uопт on its diameter. At this speed the effect of deoxidation is maximal. This made it possible to derive the empirical formula:

where k - coefficient characterizing the scatter of the experimental data, 1 / s, H - depth of the bath liquid, m; γ - coefficient of adjustment of the semiempirical formula to the real technology; Θ - temperature of the steel; δ, d - thickness of the shell and the diameter of the flux-cored wire, m;
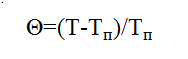
where T, Tп¬ temperature of steel in the ladle and liquidus, respectively, ° C.
It is known that the concept of using mathematical models of mixed type (in particular, semiempirical formulas) for the development of resource-saving modes of modern metallurgical technology is most promising. Reducing k to level Uопт saves material flux-cored wire.
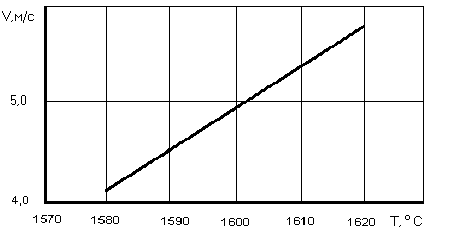
Figure 2 - Optimal speed of the input flux-cored wire in the steel shell in the ladle findings
Findings
Furnace treatment of liquid steel calcium alumino cored wire is one of the most modern and effective methods of steel deoxidation. Analysis of heat and mass transfer processes, this technology makes it possible to develop energy-saving modes. These modes make it possible to solve the urgent problem of energy saving in Ukraine.
As part of studies has been developed semiempirical formula for the optimal input speed calcium alumino cored wire in the molten steel for its deoxidation.
This master's work is not completed yet. Final completion: December 2011. The full text of the work and materials on the topic can be obtained from the author or his head after this date.
References
- Дюдкин Д.А., Гринберг С.Е., Маринцев С.Н. Совершенствование технологии производства стали// Производство стали в XXI веке: прогноз, процессы, технологии, экологии. Международная н/т конф. - К.: 2000. - С. 144-147.
- Обработка жидкой стали порошковой проволокой/ В.А. Вихлевшук,В.М.Черногрицкий, В.А.Поляков и др.// Металлургическая и горнорудная промышленность. - 1991. - №4. - С.31-32.
- Технология обработки стали порошковой проволокой в сталеразливочном ковше/ В.А.Вихлевщук, В.М.Черногрицкий, Г.Г.Подопригора и др.// Черная металлургия - 1991. - №12. - С.39-40.
- Лю Д. Ж., Айронс Д.А., Лю В.К. Исследование кинетики ввода кальцийсодержащей проволоки в сталь// Обработка стали кальцием. Международный симпозиум. - К..: ИЭС им. Е.О.Патона. - 1985. - С.59-74.
- Лыков А.В. Тепломассообмен. - М.: Энергия. - 1978. - 480 с.
- Моделирование теплофизических процессов внепечной дегазации металла/ Н.И.Захаров, Д.А.Дюдкин, А.И.Троцан и др. - Донецк: Юго-Восток, -1999.-140с.
- Захаров Н.И., Полозюк О.Е. Исследование процессов теплообмена при обработке жидкой стали порошковой проволокой// Приднепр. научн. вестник. - Дн. - 1997. - № 17. - С.22-26.
- Полозюк О.Е., Захаров Н.И. Математическое моделирование плавления порошковой проволоки при внепечной обработке стали// IV региональная н/т конф. - Мариуполь. - 1997. - С.6.
- Самарский А.А. Теория разностных схем. - М.: Наука. - 1977. - 656 с.
- Берковский Б.М., Ноготов Н.Ф. Разностные методы исследования задач теплообмена. - Минск: Наука и техника. - 1976. - 112.
- Захаров Н.И., Троцан А.И., Недопекин Ф.В. Оптимизация раскисления стали в ковше порошковой проволокой // Тезисы международной научно-технической конференции «Университетская наука – 2007» - Мариуполь, 2007. - С. 119-120.(0,13 п.л.).
- Захаров Н.И., Троцан А.И., Дюдкин Д.А., Недопекин Ф.В., Туяхов А.И. Массообменные процессы внепечной дегазации стали: монография. Донецк: НОРД-ПРЕСС, 2009. – 160 с. (9,3 п.л.)
- Захаров Н.И. Интенсификация массообмена процессов внепечной дегазации стали // Процессы литья. – 2010. №4. – С.8-12. (0,33 п.л.).
- Захаров Н.И., Троцан А.И., Чупика К.Н. О скорости ввода порошковой проволоки в расплав стали // Тезисы докладов международной научно-технической конференции «Университетская наука – 2011» - Мариуполь, 2011. – С. 78-79 (п.л. 0,14: Захаров Н.И.-0,126п.л.(0,9), Троцан А.И.-0,014п.л.(0,1)).
- Захаров М.І., Троцан А.І. Математичні методи розрахунку та комп`ютерне моделювання металургійних процесів. Учебное пособие с грифом 1/11 – 32 от 05.01.11 Министерства образования и науки, молодежи и спорта Украины – Донецк, 2011. – 99 с. (п.л. 5,82: Захаров М.І.-5,238п.л.(0,9), Троцан А.І.-0,582п.л.(0,1)).