ЗМІСТ
    Вступ
          1. Технологічний процес пневмопостачання шахти як об'єкт автоматизації.
          2. Мета проектування та вимоги до системи автоматизації турбокомпресорної станції пневмопостачання шахти.
          3. Пристрої автоматизації.
          4. Розробка пристрою автоматичного протипомпажного захисту турбокомпресора.
          5. Розрахунок надійності.
          Висновки
    Перелік посилань
ВСТУП
Витрати на пневмопостачання гірничих робіт шахти дуже великі (зокрема, витрата електроенергії досягає 60% від всієї енергії, споживаної шахтою) [5]. При автоматизації процесу пневмопостачання істотно важливим є рішення питань доцільного і ефективного використання стислого повітря і зниження витрат на його виробництво. Слідством цього є підвищені вимоги до точності регулювання режиму роботи компресорної станції, необхідність обліку взаємозв'язків між окремими елементами (компресорні машини, електроприводи, допоміжні механізми, пристрої управління, контролю і регулювання, пневмоспоживачі і ін.) і характеристиками (тиск стислого повітря і продуктивність компресорів і пневмоспоживачів, витоки стислого повітря, енергетичні показники, температурні та інші параметри режиму агрегатів) процесу пневмопостачання.
На рисунку 1 показана структурна схема процесу пневмопостачання, який здійснюється компресорною станцією, магістральними і дільничними пневмомережею і пневмоспоживачами (машини і механізми, що приводяться в рух пневмоенергією). У конкретних випадках конфігурація пневмомережі відрізняється кількістю відгалужень приймачів. На рисунку 1 позначено: 1 - компресорний агрегат (станція); 2 – споживачі; 3 – регулюючі органи; 4 – вузли трубопроводів; 5 – дільнична магістраль; 6 – головна магістраль. На гірничих підприємствах як правило використовуються центробіжні компресори – турбокомпресори. У турбокомпресорних машинах передача енергії до газу відбувається безперервно в робочому колесі, що обертається, забезпеченому лопатками. При обтіканні потоком газу решітки з профілів лопаток колеса, що обертається, виникає підйомна сила, що викликає прискорення потоку, збільшення його швидкості і тиску. Надалі в нерухомих елементах відбувається додаткове збільшення тиску за рахунок перетворення кінетичної енергії газу [6,9].
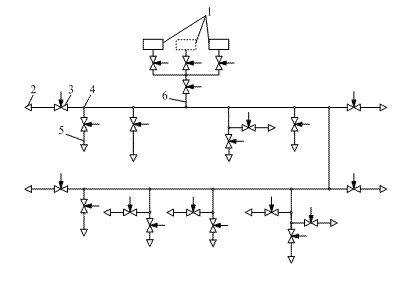
Рисунок 1 – Структурна схема процесу пневмопостачання
Параметри стислого повітря, визначальні техніко-економічні показники роботи приймачів пневмоенергії, залежать від умов постачання і споживання стислого повітря, тобто від роботи компресорної станції, пневмомережі, вигляду і кількості споживачів.
1. Технологічний процес пневмопостачання шахти як об'єкт автоматизації
Устаткування турбокомпресорної станції
Повітряний тракт. Для забезпечення нормальної експлуатації, збільшення терміну служби і підвищення надійності компресорних агрегатів необхідно, щоб всмоктуване компресором атмосферне повітря було очищене від пилу і інших механічних домішок, концентрація яких залежить від пори року, метеорологічних умов і т.д. Для цієї мети на всмоктуючому тракті компресора встановлюються фільтри, що розташовуються в спеціальних ка мерах.
Система водяного охолоджування. Тепло, еквівалентне роботі стиснення і переміщення повітря в компресорі, а також що виділяється при терті деталей механізму руху і роботі електродвигуна, відводиться за допомогою охолоджуючої води. У зв'язку з великою витратою води для охолоджування па копальневих компресорних станціях, як правило, застосовується циркуляційна система водопостачання, що містить насосну станцію, пристрій для охолоджування води і проміжні споруди (басейни, водоводи, пристрою для очищення води і ін.).Одним із завдань автоматизації компресорних станцій є управління за заданою програмою і контроль за роботою насосів, вентиляторів градирні, засувок на магістралі водяного охолоджування, управління системою обробки води, а також контроль наявності потоку і тиску води і виключення роботи компресорного агрегату при несправностях в системі водяного охолоджування.
Система маслопостачання. Маслосистема турбокомпресорного агрегату (компресор – редуктор – електродвигун) – примусова, циркуляційна. Масло всмоктується з бака через фільтри головним шестерним насосом, розташованим на валу редуктора, і нагнітається в систему під тиском 5 кгс/см2. Такий тиск масла необхідний для нормальної роботи реле осьового зрушення опорно-наполегливого підшипника і покажчика рівня в маслобаку, а також для системи гідравлічного регулювання і противопомпажного захисту. Для пониження тиску масла, що йде на мастило підшипників двигуна і компресора, сполучних муфт і редуктора, до 0,5—0,9 кгс/см2 в маслопроводі встановлюється спеціальний редукційний клапан. До місць мастила масло проходить через маслоохолоджувачі трубчастого типа, де віддає своє тепло циркулюючій по трубах воді. Регулювання кількості масла, що подається до окремих точок змащування, здійснюється установкою в маслопроводі дросельних шайб. Відпрацьоване в системі мастила масло самоплив зливається в масляний бак.
Система регулювання продуктивності. Система регулювання продуктивності компресорних агрегатів, як правило, загальна. Введення компресорів під навантаження здійснюється після заданого технологічним режимом роботи прогрівання на холостому ході.
Основним завданням регулювання режиму роботи рудникових турбокомпресорних агрегатів є підтримка в пневматичній мережі постійного заданого тиску стислого повітря шляхом зміни продуктивності турбокомпресорів при змінній витраті, яка може коливатися в широких межах і при значній частоті. Основними вимогами, що пред'являються до системи регулювання турбокомпресорів, є забезпечення заданого характеру зміни продуктивності і економічності роботи установки, простота пристрою, надійність в роботі, компактність, зручність обслуговування і ін.
Режими роботи турбокомпресорної станції
  На рис.2 зображені робочі характеристики турбокомпресора. Робоча точка компресора визначається точкою перетину А характеристики компресора 1 і характеристики повітропроводу 2. Крапка К відповідає критичній продуктивності Qк компресора, при якій він розвиває максимальний тиск Рк. Якщо витрата повітря в пневмомережі стане менший Qк, то тиск, що розвивається компресором, виявиться меншим за Рк і, отже, менше, ніж в пневмомережі, з якої повітря спрямується до компресора і закриє зворотний клапан в повітропроводі. Робочий режим компресора переміститься в крапку Б, відповідну холостому ходу. У міру витрачання повітря, з пневмосети його тиск знизиться до величини, відповідній крапці А, зворотний клапан відкриється і компресор почне подавати в пневмомережу повітря в кількості, визначуваній крапкою В. Якщо витрата повітря залишиться меншим Qк, все повторюється в тому ж порядку. Це явище відоме під назвою помпажа і відбувається при експлуатації компресора на ділянці робочої характеристики, розташованої ліворуч критичної крапки К.
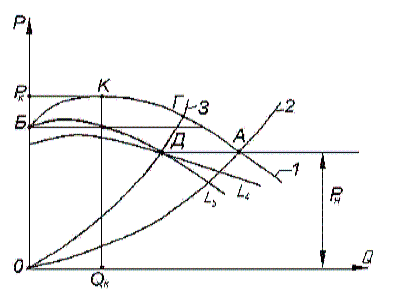
Рисунок 2 – Напірні характеристики турбокомпресора
Стійка робота компресора можлива на ділянці характеристики, розташо-ваній правіше за точку К. Для забезпечення нормальної роботи компресора, при змінній витраті повітря в пневмомережі, його забезпечують противопомпажним захистом, який забезпечується спеціальним регулятором, що сполучає противопомпажной заслінкою нагнітальний повітропровід компресора з атмосферою, коли споживання повітря пневмомережою стає нижчим Qк і, таким чином, утримує режим роботи компресора на стійкій гілці робочої характеристики. Ступінь відкриття противопомпажної заслінки визначається різницею між Qк і дійсним споживанням повітря пневмомережі.
2. Мета проектування та вимоги до системи автоматизації турбокомпресорної станції пневмопостачання шахти
Метою автоматизації турбокомпресорної станції є:
- забезпечення ефективної (у перспективі – оптимальної) роботи компресорних агрегатів відносно економічності і безпеки експлуатації;
- запобігання аварійним режимам, порушення роботи або виходу з ладу окремих елементів, вузлів і компресорних агрегатів в цілому;
- збільшення міжремонтних термінів роботи компресорного агрегату і зниження витрат на ремонт, технічне обслуговування і експлуатацію;
- вибір економічно доцільного поєднання працюючих агрегатів;
- часткове або повне вивільнення постійного обслуговуючого персоналу компресорної станції;
- поліпшення умов і підвищення культури праці і безпеки персоналу, що залишається;
- підвищення ефективності використання пневмоенергії.
Вимоги до системи автоматизації турбокомпресорної станції
Система автоматизації турбокомпресорної станції повинна забезпечувати роботу компресорних агрегатів в нормальних технологічних режимах, їх захист, видачу необхідної інформації в систему управління гірничим виробництвом і виконання команд, що поступають від неї. Зокрема:
1. Наступні режими управління компресорною станцією:
- автоматичне програмне управління, при якому первинний імпульс на пуск і останов окремих агрегатів і всієї станції подається або від ЕОМ або оператором (диспетчером) з пульта, встановленого поза машинним залом компресорної станції, або з машинного залу;
- місцеве – роздільне управління всіма механізмами при їх випробуванні під час налагоджувальних і ремонтних робіт.
При автоматичному управлінні повинна дотримуватися задана технологічна послідовність управління основним і допоміжним устаткуванням станції. Можливість одночасної роботи агрегатів в двох режимах повинна бути виключена .
2. Контроль роботи, сигналізацію про нормальний і аварійний режими роботи, а також необхідні автоматичні блокування і захисту, зокрема від помпажа.
3. Автоматична підтримка заданого тиску стислого повітря у вихідному колекторі компресорної станції регулюванням режиму роботи окремих агрегатів.
У зв'язку з тим, що приміщення компресорних станцій знаходяться на поверхні шахти і відповідно до ГОСТ 15150–69 відносяться до категорії 4, комплект апаратури повинен мати нормальне загальнопромислове виконання.
Система автоматизації повинна мати два пульти управління і індикації, що розміщуються – один в приміщенні компресорної станції, другий у диспетчера шахти на пульті управління, наприклад КОД.1М.
3. Пристрої автоматизації
Для автоматизації компресорної установки існує пристрій УКАС-М, який призначений для автоматичного керування роботою компресорних станцій, оснащених поршневими і турбо- компресорами (у кількості до шести) продуктивністю 100-500 м3/хв з електроприводом від синхронних високовольтних двигунів з тиристорною системою збудження [10.13].
Пристрій УКАС-М складається з комплексів УКАС-АМ і УКС-СМ (дивись рис. 3). Комплект УКАС-М поставляється у виді шаф центрального автомата (ШЦА) і контрольно-вимірювальних приладів (КВП). Шафи ШЦА служать для автоматичного керування, регулювання, сигналізації і захисту компресора. Прилади шаф КВП виконують функції технологічного контролю ряду технологічних параметрів і керування допоміжними приводами компресора. Комплект УКАС-АМ поставляється з кожним компресором, а УКАС-СМ – один на всю станцію для організації енергопостачання допоміжних агрегатів.
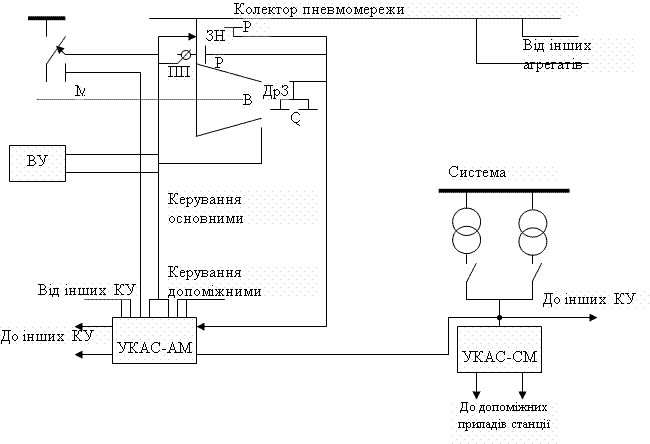
Рисунок 3 – Структурна схема комплектного пристрою УКАС-М
Апаратура автоматизації забезпечує: керування компресорами з подачею керуючого імпульсу оператором з наступним автоматичним виконанням програми пуску (зупину), а також місцеве керування окремими механізмами установки; регулювання подачі компресора і компресорної станції в цілому; контроль технологічних параметрів (температури стиснутого повітря, тиску в системі охолодження та ін.); захист компресорів; сигналізацію про нормальну роботу, попереджувальну й аварійну сигналізацію.
Недолік пристрою – не виконує регулювання продуктивністю компресору і не здійснює протипомпажний захист.
4. Розробка пристрою автоматичного протипомпажного захисту турбокомпресора
Прийнято наступний принцип автоматичного контролю і захисту турбокомпресору від помпажу. При збільшенні опору пневматичної мережі компресора, його робоча крапка наближається до межі помпажа. При цьому починає обертаючий зрив газу з поверхні лопаток робочих коліс турбомашини, виникають коливання струму статора приводного електродвигуна, пропорційні коливанню значення витрати. Як джерело сигналу для пристрою захисту від помпажа може бути використаний датчик струму (трансформатор струму, первинна обмотка якого включена послідовно в обмотку статора приводного електродвигуна компресора). На виході датчика струму з'являються коливання сигналу, пропорційні відповідно коливанням струм статора. Вихідним сигналом вхідного пристрою є сигнал напруги змінного струму частотою 50 Гц, промодульований предпомпажными коливаннями низької частоти 0,2-3,5 Гц. Поява коливань струму статора не залежить від умов всмоктування, охолоджування і технічного стану турбокомпресора, що свідчить про значну перевагу використанні їх для побудови пристрою протипомпажного захисту (ППЗ) .
Розроблено схему принципову електричну пристрою ППЗ. Схема включає: активний випрямляч, фільтр нижніх частот, фільтр верхніх частот, функціональний перетворювач, інтегратор, компаратори, тригер Шмитта.
При швидкому порушенні помпажних коливань сигнал з виходу ФНЧ через діод VD4 надходить на не інвертує вхід DA3.2 (другого компаратора). На вхід, що інвертує, цей сигнал надходить через аттенюатор R26 і блок затримки R27,C10. При цьому на виході DA3.2 з'являється прямокутний імпульс, що надходить на другий вхід транзисторного елемента “ИЛИ” (VT1, VD16,R47). При цьому спрацьовує реле KV1, своїми контактами замикає ланцюг сервопривода противопомпажного клапана. Індикація спрацьовування реле КV1 здійснюється світлодіодом HL3, а компаратора – світлодіодом HL2.
5. Розрахунок надійності
Для оцінки спроможності розробленим пристроєм автоматичного захисту турбокомпресора зберігати в установлених межах значення всіх параметрів, які характеризують здатність виконувати пристроєм функції, що вимагаються, здійснено розрахунок надійності уточненим методом.
Критерієм відмов пристрою прийнято невиконання ним будь-якої з основних його функцій.
Відповідно до принципової електричної схеми пристрою складена структурно-логічна схема розрахунку безвідмовності, яка подана на рисунку 4.
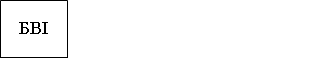
Рисунок 4 – Структурно-логічна схема розрахунку безвідмовності пристрою ППЗ (gif_animator)
На рисунку 4 позначено: БВІ – блок вводу інформації, ЕБ – електроний, БІ – блок індикації.
При розрахунках приймаються такі допущення:
- час безвідмовної роботи пристрою є випадковою величиною, яка розподілена за показниковим законом;.
- потік відмов є найпростішим;
- величина інтенсивності відмов однотипних елементів однакова, а комплек-туючі вироби працюють у основний період експлуатації, де інтенсивність відмов є постійною величиною;
- враховуються тільки елементи, що впливають на працездатність пристрою.
У результаті розрахунків інтенсивність відмовлень проектованого пристрою складає 9,83 х 10-6. Середній наробіток до відмовлення пристрою для показового закону розподілу складе
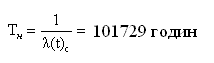
Згідно з [5] проектуємий пристрій належить до малої категорії складності, четвертого класу щодо надійності. Тому нормативне чисельне значення часу напрацювання на відмову для нього складає . Фактичне середнє напрацювання пристроя на відмову складає більше нормативного. Відкіля можна зробити висновок, що розроблений пристрій відповідає нормативним рівням безвідмовності апаратури шахтної автоматики.
ВИСНОВКИ
Виконано аналіз турбокомпресорної станції процесу пневмопостачання шахти як об’єкт автоматизації: розглянута технологічна схема компресорного агрегату, системи забезпечення його нормального функціонування, а також основні залежності, що характеризують режим роботи агрегатів. Система автоматизації турбокомпресорної станції пневмопостачання шахти складається з двох підсистем: автоматичного (дистанційного) управління пуском і остановом окремих машин і механізмів і їх комплексу; автоматичного регулювання режимів роботи компресорних агрегатів. Перша підсистема реалізується за допомогою апаратури УКАС.М. Для другої підсистеми в розроблено новий пристрій автоматичного контролю і захисту турбокомпресору від помпажних режимів. Особливість пристрою – контроль помпажу по величині струму у статорній обмотці привідного двигуна турбокомпресору, що значно підвищує ефективність контролю і захисту турбокомпресору від анормального режиму експлуатації. Виконано розрахунки надійності впровадження нових пристроїв на шахті. Результати позитивні.
Перелік посилань
1. Правила безпеки у вугільних шахтах. ДНОАП 1.1.30-1.01-00-К., 2001.- 484 с.
2. Правила технической эксплуатации электроустановок потребителей и Правила техники безопасности при эксплуатации электроустановок потребителей / Глав. Упр. Гос. Энергетического надзора Минэнерго СССР.- 4-е изд.- М.: Энергоатомиздат, 1989.- 432с
3. Дорохов Д.В. и др. Технологии подземной разработки пластовых месторождений полезных ископаемых. Донецк: ДонГТУ, 1997 .- 344 с.
4. Гетопанов В.Н., Гудилин Н.С., Чугреев Л.И.. Горные и транспортные маши-ны и комплексы, М., «Недра», 1991-455с.
5. Мелькумов Л.Г., Найман А.Е.,Травкин Е.К. Автоматизация пневматического хозяйства шахт и рудников. М.: Недра, 1977. – 271с.
6. Справочник энергетика угольной шахты: В 2 т./Под общ. Ред. Б.Н. Ванеева.- Донецк. Юго-Восток Ltd.- 2001 г. Т1- 447 с.; Т2 – 440 с.
7. Автоматизация подземных горных работ / Под ред. Проф. А.А. Иванова – К.: Вища школа, 1987 – 328с.
ДонНТУ>
Портал магістрів ДонНТУ>
Біографія
|| Бібліотека
|| Звіт про пошук
|| Посилання
||Індивідуальне завдання