Анализ существующих технологических процессов механической обработки изделий из хрупких неметаллических материалов (ХНМ), в частности, технических стекол, ситаллов, керамик, хрусталя [1, 2] показал значительную трудоемкость получистовых и чистовых операций шлифования, полирования и алмазной доводки, что вызвано повышенными требованиями к качеству обработанной поверхности по критерию минимума шероховатости и дефектности поверхностного слоя изделий. Продолжительность доводочных операций определяется глубиной и структурой дефектного слоя, образующегося на предшествующих технологических переходах. Следовательно, эффективность процессов механической обработки из ХНМ связана с повышением производительности черновых операций при условии получения дефектного слоя такой глубины и структуры, при котором бы обеспечивалась минимальная продолжительность финишных операций.
        Результаты теоретических и экспериментальных исследований [3] позволяют заключить, что исходя из особенностей механизмов диспергирования хрупких материалов при абразивной обработке, степень дефектности формируемого поверхностного слоя определяется напряженным состоянием зоны резания, характеризуемым уровнем силового воздействия на обрабатываемую поверхность (то есть энергоемкостью процесса резания), и зависит от двух категорий факторов, изменяющих уровень этого воздействия:
        – физико-механических свойств обрабатываемого материала (его прочности, твердости, хрупкости, поверхностной энергии, исходной дефектности и т.д.);
      – технологических параметров (факторов) процесса обработки: схемы резания, определяющей величину и направленность составляющих усилий резания; режима резания; технологических и эксплуатационных характеристик применяемых инструмента и методов ее восстановления.
        Одним из факторов, существенно изменяющих ситуацию в зоне резания, являются смазочно-охлаждающие технологические среды (СОТС), использование которых обязательно при абразивной обработке ХНМ. Даже при оптимизации всех остальных параметров, определяющих состояние технологической системы при обработке, использование СОТС с направленными свойствами позволит дополнительно повысить эффективность процессов резания за счет изменения условий протекания процессов диспергирования обрабатываемого материала в зоне резания [4, 5]. Под силовым воздействием инструмента и влиянием СОТС изменяются прочностные, теплофизические характеристики, химические и физико-механические свойства обрабатываемого материала. Кроме того, и свойства самого инструмента претерпевают изменения в процессе резания. В совокупности это приводит к изменению уровня выходных параметров процесса (параметров функционирования системы резания), к которым относятся, в частности, производительность, качество и точность обработки.
        Однако в настоящее время в недостаточной степени изучены механизмы влияния технологических сред на процессы диспергирования ХНМ на различных этапах их обработки абразивным инструментом, что не позволяет четко сформулировать требования к свойствам и составам СОТС. Так, например, ассортимент специальных СОТС для абразивной обработки стекла (наиболее изученного представителя ХНМ) ограничивается эмульсолами марок «Эдоксом» и «Эмус» [6], которые отличают нестабильность смеси, неэффективность использования при черновых и получистовых операциях обработки, малый срок службы, плохие экологические показатели их применения.
        Учитывая сказанное, настоящая работа посвящена теоретическому обоснованию механизмов воздействия технологических сред различной природы на процессы абразивной обработки материалов на основе стекла с целью выдачи обоснованных рекомендаций о составах ТС и области их рационального применения.
      Рассмотрим теоретическую возможность повышения эффективности процесса формообразования за счет уменьшения энергетических затрат на диспергирование при использовании поверхностно-активных СОТС с направленными свойствами, изменяющих прочностные характеристики обрабатываемого материала. Приняв положение работы [7], согласно которому между отдельными процессами резания не имеется принципиальной разницы, так как процесс стружкообразования на режущих элементах различных инструментов протекает идентично, независимо от их конструктивного оформления, рассмотрим процесс резания как процесс, происходящий при взаимодействии режущего клина с обрабатываемым материалом. В этом случае энергия формообразования определяется, в основном, величиной тангенциальной составляющей силы резания. При обработке хрупких материалов типа стекол и ситаллов в условиях, обеспечивающих интенсивное разрушение припуска, преобладает хрупкое разрушение [2]. Поэтому все теоретические положения, выдвинутые, например, Корчаком С.Н. и другим авторами при расчете усилий резания и базирующиеся на адекватности процессов резания металлов процессам пластического сжатия, в этом случае являются неправомерными. При шлифовании хрупких материалов процесс резания может моделироваться как процесс трещинообразования, в котором напряженное состояние материала при расклинивании определяется особенностями возникновения и движения трещины разрушения [8]. Поэтому составляющие усилия резания должны рассчитываться с позиций теории трещинообразования.
      Учитывая сказанное, тангенциальная составляющая силы резания может быть определена по методике, предложенной в работе [9] для обработки хрупких металлов. Предполагается, что сила резания определяется сопротивлением материала скалыванию (хрупкому сдвигу) в плоскости максимальных напряжений сдвига. В отличие от случая резания пластичного металла, когда напряжение в зоне сдвига является функцией степени пластической деформации, а в большинстве случаев и интенсивности деформаций и температуры, при резании хрупких материалов сопротивление сдвигу в плоскости максимальных касательных напряжений должно являться постоянным для данного обрабатываемого материала. В основу вывода уравнения силы при резании хрупкого материала заложено условие постоянства максимального касательного напряжения и независимости его от геометрии инструмента, размеров срезаемого слоя и скорости резания.
        В условиях рассмотрения схемы свободного прямоугольного резания сила, производящая сдвиг при резании P
τ, выражается уравнением
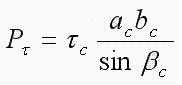
        где τ
c – максимальное касательное напряжение в материале, приводящее к сдвигу; α
τ, b
τ – соответственно толщина и ширина срезаемого слоя; β
с – угол, образуемый плоскостью сдвига с горизонталью.
        Анализ механизма отделения объема материала при разрушении хрупких материалов на основе стекла [2, 8] позволяет следующим образом описать этот процесс при резании. В начальный момент контакта передней поверхности инструмента (зерна) с обрабатываемым образцом прилегающий к режущей кромке объем материала подвергается деформациям сдвига. Увеличение нагрузки в сочетании с неоднородностями сдвигообразования, вызванными наличием микродефектов в структуре материала, приводят к резким локальным концентрациям напряжений и зарождению магистральной трещины разрушения. Дальнейшее увеличение нагрузки сопровождается ростом трещины и при достижении ею критической величины, происходит скол элемента твердого тела путем хрупкого отрыва под действием растягивающих напряжений, нормальных поверхности трещины. Скол элемента стружки сопровождается резким падением напряжений в материале. Затем цикл повторяется. Тангенциальная составляющая силы резания, отражающая энергетический уровень процессов разрушения в обрабатываемом материале, также имеет периодический, пульсирующий характер изменения. По данным ряда авторов [10] время цикла составляет 10-310-5 c. Таким образом, процесс стружкообразования хрупких материалов определяется явлениями хрупкого отрыва, обусловленными периодическим развитием опережающей трещины.
        Значение скалывающих напряжений τ
c, приводящих к разрушению объема материала по плоскости скалывания, равно
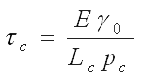
        где E и y
0 – соответственно модуль Юнга и удельная свободная поверхностная энергия обрабатываемого материала; L
c – длина сечения скола; p
c – опасное напряжение, нормальное к плоскости трещины.
        Для хрупких тел величина p
c совпадает с пределом прочности материала при растяжении. Тогда
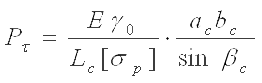
        Сила P
τ определяет уровень как тангенциальной, так и нормальной составляющих силы резания, влияя как на энергоемкость процесса резания (ответственна P
z), так и на силовое воздействие на обрабатываемую поверхность, приводящее к развитию дефектного слоя (ответственна P
y). При прочих равных условиях эти параметры зависят от значения удельной поверхностной энергии твердого тела или от величины его свободной поверхностной энергии при образовании новых поверхностей [11].
        При хрупком разрушении свободная поверхностная энергия определяет работу A
д, затрачиваемую на диспергирование материала [112], то есть A
д=A
д(y
m). Причем резкому уменьшению его поверхностной энергии отвечает еще более резкое падение работы образования свободной поверхности. Согласно соотношению Гриффитса связь между прочностью p
c и работой на диспергирование A
д аппроксимируется зависимостью p
c≈A
д½. Так как A
д может быть отождествлена с y
m, то p
c≈(y
m)
½. Как известно [12], введение в зону диспергирования твердых тел поверхностно-активных сред (ПАС) приводит к снижению их удельной свободной поверхностной энергии за счет адсорбционных взаимодействий атомов среды и деформируемого тела, происходящих на формируемой поверхности, то есть, к соответствующему изменению его прочностных свойств. Облегчение развития новых поверхностей, сопровождающее процессы деформации и разрушения твердых тел в присутствии поверхностно-активных СОТС, связано с проявлением адсорбционного эффекта понижения прочности твердых тел (эффект Ребиндера). Это позволяет уменьшить энергоемкость процесса резания и интенсифицировать режимы обработки, повысив тем самым ее производительность.
        Однако известно [12], что этот эффект проявляется при соблюдении ряда условий, основными из которых являются: родственность химического состава и строения тела и СОТС; особенности реальной структуры твердого тела (его дефектность); условия деформирования. Химический состав твердого тела определяет характер взаимодействия между атомами (ионами, молекулами) на межфазной границе, от которого зависит принципиальная возможность влияния среды на прочность твердого тела. При этом характер межатомных взаимодействий проявляется в большем или меньшем изменении поверхностной энергии на межфазной границе, что возможно при определенном «родстве» граничащих фаз. Для материалов на основе стекла, веществ хрупких с типично гидрофильной поверхностью (то есть, ярко выраженной полярностью) наибольшее понижение поверхностной энергии, а, следовательно, и прочности, происходит при контакте с наиболее полярной жидкостью – водой или водными растворами ПАВ, обладающими высокой полярностью.
        Исходя из положений теории П.А. Ребиндера, можно сформулировать требования к физико-механическим свойствам сред, применяемых с целью интенсификации процессов механической обработки материалов на основе стекла. СОТС должны: быть полярными; обладать высокой скоростью растекания, соизмеримой со скоростью образования микросколов при резании, для чего они должны иметь низкое поверхностное натяжение, высокое значение движущей силы растекания и малую вязкость. Теоретический анализ основ разрушения хрупких материалов показал, что наиболее важным функциональным свойством ТС, положительно влияющим на выходные параметры технологического процесса их обработки, является повышенная диспергирующая способность сред.
        Учитывая результаты теоретических исследований, предложены составы СОТС для операций лезвийной обработки (а.с. 1331053), шлифования и полирования технических стекол, ситаллов и хрусталя – СОТС П2 (а.с. 997446), полирования стекла и хрусталя (а.с. 1654319). Среды представляют собой водные растворы синтетических моющих средств, являющихся активными ПАВ, что обеспечивает их повышенное воздействие на материал удаляемого припуска, снижает энергоемкость процесса резания, улучшает качество обработки. Названные среды отличает простота изготовления, гигиеничность, дешевизна.
        Предлагаемые СОТС по сравнению с лучшими рекомендуемыми в литературе составами (в частности, эмульсолы ЭМУС, НГЛ-205 и др.) позволяют на операциях предварительного формообразования изделий из технических стекол, ситаллов и хрусталя (точение, черновое шлифование) снизить энергоемкость процесса резания до 40%, благоприятно изменив глубину и структуру возникающего в результате обработки дефектного слоя. Общая глубина проникновения дефектов (обработка стекол и хрусталя) уменьшается практически вдвое при снижении средних размеров единичных дефектов в 1,6 – 2,2 раза (рис. 1). При обработке технических ситаллов снижение размеров дефектов достигает 4 – 10 раз.
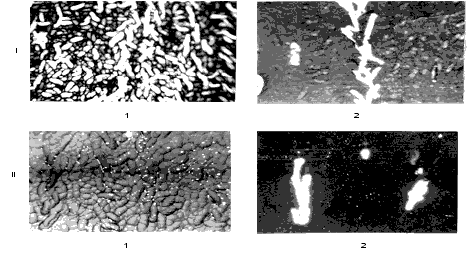
        Рис. 1. Микрофотографии дефектности образцов технического стекла на глубине залегания I – 60 мкм; II – 120 мкм. Обработка по схеме упругого торцового шлифования кругом АС6 зернистости 125/100 при давлении р = 0,4 МПа в испытуемых средах: 1 – СОТС П2; 2 – воды. Увеличение в 75 раз.
        Применение разработанных ПАС в условиях черновой и получистовой обработки позволяет расширить диапазон режимов шлифования без ухудшения качества формируемой поверхности. Об этом свидетельствуют результаты эксперимента, выполненного при внутреннем круглом шлифовании изделий из ситаллов кругами А 400/315 со связкой М2-01 100% концентрации с режимами: скорость вращения круга v = 30 м/с, частота вращения детали n = 60 – 100 об/мин, глубина резания t = 1 – 2 мм.
        Эффективность влияния сред (воды и СОТС П2) на процесс резания оценивалась величиной предельных подач шлифования S
пр, допустимых из условия отсутствия горения материала в зоне шлифования, а также удельной мощностью шлифования N
уд, определявшейся как отношение мощности шлифования N, отнесенной к величине предельной подачи. Было установлено, что предельное значение эффективной мощности шлифования Nэф(max), определяемое в момент возникновения плавления материала изделия в зоне контакта деталь-инструмент, зависит от физико-механических свойств обрабатываемого материала. Для ситалла при доверительной вероятности 90% величина N
эф(max) с погрешностью 15% составляет 2,5 Квт. Применяемые технологические среды, режимы обработки не влияют на значение N
эф(max). Однако от свойств технологических сред существенно зависит изменение границ предельных подач и удельной мощности шлифования (рис. 2).
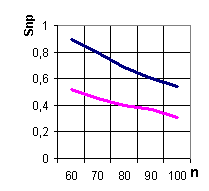
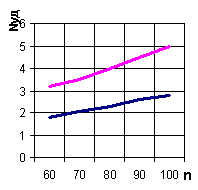
                                                                                          а)                                                 б)
        Рис. 2. Зависимость предельной подачи (а) и удельной мощности шлифования ситалла (б) от скорости вращения детали и используемых сред: 1 – вода; 2 – СОТС П2
        Результаты эксперимента показали, что применение поверхностно-активной среды СОТС П2 более рационально при напряженных условиях резания, зависящих, в частности, от глубины шлифования. Так, если при t = 1 мм значения S
пр и N
уд для обеих сред практически одинаковы, то при t = 2 мм (см. рис. 2) использование СОТС П2 позволяет вести процесс шлифования ситалла с предельными подачами, вдвое превышающими соответствующие значения S
пр, полученные при обработке в среде воды, и при пропорциональном уменьшении удельной мощности шлифования.
        Это позволило рекомендовать применение разработанной среды на черновой и получистовой операциях шлифования изделий из технических ситаллов, стекол и хрусталя при увеличении рабочих подач на 20-30% по сравнению с принятыми на производстве при использовании воды. Необходимо также отметить, что снижение энергоемкости процесса резания в присутствии ПАС способствует благоприятному изменению глубины и структуры возникающего в результате обработки дефектного слоя. Поверхностно-активная среда, обеспечивая развитую трещиноватость в приповерхностном объеме обрабатываемого материала в сочетании с мелкодефектной структурой более глубоких слоев, позволяет существенно снизить время обработки на последующих чистовых операциях, что благоприятно скажется на общей трудоемкости производства изделий.
        1. Калафатова Л.П. Резание стекломатериалов // Машиностроение. Энциклопедия. – М.: Машиностроение, 2000. – Т. III3 «Технология изготовления деталей машин». – С. 142-145.
        2. Хрульков В.А., Тародей В.А. Механическая обработка деталей из керамики и ситаллов. – Саратов: Изд-во Сарат. ун-та, 1975. – 185 с.
        3. Калафатова Л.П. Влияние технологической наследственности на эффективность процессов механической обработки стекломатериалов // Справочник. Инженерный журнал. – М.: Машиностроение. – 1997. – № 9. – С. 7-11.
        4. Технологические свойства новых СОЖ для обработки резанием / М.И. Клушин, В.М. Тихонов, Д.И. Симкин и др. / Под ред. М.И. Клушина. – М.: Машиностроение, 1979. - 192 с.
       5. Латышев В.Н., Курочкин А.Е., Новиков В.В. Исследование эффективности действия водорастворимы присадок поверхностно-активных веществ (ПАВ) при абразивной обработке стекла // Справочник. Инженерный журнал. – М.: Машиностроение. – 2003. - № 1. – С. 22 – 26.
        6. Смазочно-охлаждающие технологические средства для обработки металлов резанием: Справочник / Под общей ред. С.Г. Энтелиса, Э.М. Берлинера. – М.: Машиностроение, 1995. – 469 с.
        7. Маслов Е.Н. Теория шлифования материалов. – М.: Машиностроение, 1974. – 319 с.
        8. Апанасенко В.И. Выбор режимов шлифования твердых и хрупких материалов, исходя из требуемой чистоты поверхности: Дис.... канд. техн. наук: 05.02.08. – Орджоникидзе, 1972. – 212 с.
        9. Розенберг А.М., Еремин А.И. Элементы теории процесса резания металлов. – М.: Машиностроение, 1956. – 319 с.
        10. Ардамацкий А.Л. Алмазная обработка оптических деталей. – Л.: Машиностроение, Ленингр. отд-ние, 1978. – 232 с.
        11. Калафатова Л.П. Энергетический подход к повышению качества обработки хрупких неметаллических материалов // Труды Междунар. конф. «Машиностроение и техносфера на рубеже ХХI века». – Том 2. – Донецк: ДонГТУ. – 1998. – С. 27-30.
        12. Ребиндер П.А. Физико-химическая механика. – М.: Наука, 1979. – 124 с.