Розвиток сучасного машинобудування пов’язаний з розробкою та впровадженням нових матеріалів і прогресивних технологічних процесів їх обробки. До таких матеріалів повністю обґрунтовано відносяться крихкі неметалеві матеріали (КНМ), в тому числі, технічні стекла, ситали, кераміка, тощо. Не зважаючи на те, що матеріали цього класу відрізняє підвищена крихкість, вони мають ряд таких позитивних характеристик як високий опір стиску, жорсткість при відносно низькій питомій вазі, радіопрозорість і термостійкість, стійкість відносно дії агресивних середовищ. Найбільш перспективним є використання названих матеріалів при виготовленні елементів приладів, оболонкових систем різної форми та габаритів, що працюють в умовах підвищеного зовнішнього тиску та жорстких температурних навантажень.
Специфіка експлуатації виробів із КНМ передбачає підвищені вимоги щодо їх міцності, точності та якості поверхні, що формується (шорсткість не більша, ніж R
a=0,08 – 0,04 мкм і практична повна відсутність дефектного шару, що сформувався при обробці). Технологічні процеси (ТП) обробки виробів включають операції шліфування, на яких відбувається їх формоутворення, фінішні операції доводки або полірування, що забезпечують необхідний рівень шорсткості та мінімальну дефектність поверхневого шару деталі. У комбіновано-дефектних ситалах і стеклах дефектний шар, що залишився після обробки, вилучають на операції комбінованого зміцнення, до якої входять хімічне травлення обробленої поверхні та зміцнення її іонним обміном.
Аналіз ТП механічної обробки виробів із КНМ [1, 2] свідчить про значний обсяг напівчистових і чистових операцій – шліфування, полірування, алмазної доводки. Тривалість фінішних операцій визначається глибиною та структурою дефектного шару, який створюється на попередніх технологічних переходах. Причиною цього є підвищені вимоги до якості оброблюваної поверхні, бо експлуатаційні характеристики виробів із цих матеріалів безпосередньо залежать від дефектності сформованого при обробці поверхневого шару деталей. Таким чином, ефективність процесів механічної обробки КНМ пов’язана з підвищенням продуктивності чорнових операцій при умовах забезпечення дефектного шару такої глибини та структури, які гарантують мінімальну тривалість фінішних операцій. Однак на цей час немає достатньо обгрунтованих технологічних принципів проектування ТП обробки виробів із КНМ, особливо конструкцій із цих матеріалів. Більшість проведених досліджень і виданих рекомендацій в основному відносяться до обробки виробів із оптичних стекол, ситалів і кристалів, які застосовуються у приладобудуванні, не належать до категорії конструкційних і не експлуатуються в умовах екстремальних і силових навантажень. На відміну від конструкцій, ці вироби мають невеликі розміри, достатньо прості геометричні форми, що спрощує одержання точних заготовок для них і знижує величину припуску на механічну обробку. Тому спрямованість більшості досліджень пов'язана з вивченням процесів напівчистового, чистового шліфування, полірування або доводки. Відмітною особливістю процесів абразивної обробки в цих умовах є достатньо прості з точки зору кінематики схеми взаємодії інструменту і деталі, легкі режими різання, використання абразивних порошків або інструментів дрібної зернистості з більш низькими характеристиками міцності ріжучих зерен. Усе це стримує розвиток дефектного шару під час різання.
Розглянуті умови не співпадають із тими, в яких ведеться обробка великогабаритних виробів із технічних стекол і ситалів, які являють собою конструкції складної просторової форми. Одержання високої якості поверхні і точності в цьому випадку вкрай ускладнене через низьку оброблюваність матеріалів і відрізняється значною трудоємкістю (необхідністю вилучення великих припусків, наприклад, до 10 мм при обробці крупно габаритних виробів оболонкової форми із технічних ситалів), великими непродуктивними витратами енергії та інструменту. Причиною цього є: недостатня повнота знань про механізми руйнування припуску під час різання матеріалів, які розглядаються, у напружених умовах; відсутність наукового системного обґрунтування залежності дефектності поверхневого шару виробів від вхідних технологічних параметрів процесу обробки і властивостей оброблюваних матеріалів, які визначають рівень силового впливу на поверхню, що формується; низька ефективність прийнятих способів обробки та організації ТП одержання виробів. Особливо це відноситься до операцій формоутворення виробів, тобто операцій чорнового та напівчистового шліфування, які можна віднести до категорії операцій глибинного шліфування (глибина різання більше 0,1 мм).
Результати теоретичних та експериментальних досліджень [3] свідчать про те, що враховуючи особливості механізмів диспергування КНМ при абразивній обробці, такі параметри дефектності оброблюваної поверхні як розміри, щільність, глибина проникнення дефектів, в значній мірі визначаються рівнем та спрямованістю силової дії на матеріал при різанні. В свою чергу, силові характеристики процесу шліфування залежать від двох категорій факторів, що змінюють їх рівень:
– фізико-механічних властивостей оброблюваного матеріалу (його міцності, твердості, крихкості, поверхневої енергії, вхідної дефектності, виду та особливостей попередньої обробки);
– технологічних параметрів процесу обробки – схеми різання, яка визначає рівень та напрямок складових зусиль різання; режиму різання; технологічних та експлуатаційних характеристик застосовуваних інструментів і методів відновлення їх ріжучих властивостей, а також від рівня поверхневої активності та типу використовуваних технологічних середовищ (ТС).
Однак із цієї точки зору проблема досліджена не достатньо. Відсутні достовірні відомості про глибину та структуру порушеного обробкою шару і вплив на параметри дефектності технологічних факторів процесів механічної обробки. Виходячи з цього, ціллю цієї статті є узагальнення результатів комплексних наукових досліджень щодо вибору раціональних умов обробки, завдяки яким забезпечується мінімальний рівень силового впливу на поверхню, що формується, та зменшення рівня напружено-деформованого стану оброблюваного матеріалу, з урахуванням технологічної спадковості. Наведені далі результати стосуються підвищення ефективності обробки виробів із технічних ситалів, які є одними з найбільш важкооброблюваних конструкційних матеріалів із групи КНМ.
Для дослідження глибини та структури порушеного обробкою шару матеріалу використовувався метод капілярної люмінесцентної дефектоскопії в поєднанні з пошаровим хімічним травленням зразків із ситалів до рівня, який гарантує повну відсутність дефектів, що викликані обробкою [4]. Розроблений спеціальний апаратно-програмний комплекс дозволяє на мікрофотографіях дефектної поверхні оброблюваних зразків, одержаних на різних рівнях глибини відносно оброблюваної поверхні, автоматично виділити області дефектів і розрахувати їх усереднені та інтегральні характеристики, встановити математичні залежності параметрів дефектності від змінюваних технологічних характеристик процесу обробки. Методика, що пропонується, дозволяє отримати дійсну картину порушеного шару на різних рівнях заглиблення, виявляючи дефекти довжиною від 0,1 мм до 1 мкм.
Для підвищення продуктивності процесу шліфування доцільно інтенсифікувати параметри режиму різання, в тому числі, глибину різання t і подачу s. Однак при цьому збільшуються складові сили шліфування – радіальна P
y і тангенціальна P
z. Так при роботі правленим кругом 1А1-200х6х3х76 АС 20 250/200-4-М2-01 за схемою плоского урізного шліфування ситалу АС-418 залежності складових сили шліфування від режимів різання мають вигляд
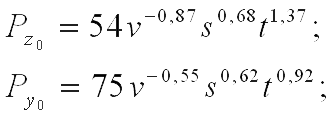
де P
z0, P
y0 – відповідно тангенціальна та радіальна складові сили шліфування при роботі не затупленим кругом, Н; v – швидкість різання, м/с; s – подовжня подача, мм/хвил; t – глибина різання, мм.
Аналіз одержаних залежностей сил різання від кінематичних параметрів режиму показує, що найбільший вплив на зміну величини сил виявляють подовжня подача та глибина різання, найменший – швидкість різання. Таким чином, експериментально підтверджений вплив параметрів режиму шліфування на силові характеристики процесу обробки – в першу чергу на нормальну складову зусилля різання, і, як наслідок, на структуру дефектного шару та ступінь його розвитку. При цьому співвідношення між нормальною і тангенціальною складовими зусиль різання знаходиться в діапазоні P
y0/P
z0 ≈ 4...10. Поза залежністю від схеми обробки збільшення подачі та глибини різання негативно відбивається на дефектності поверхні, що формується. Так, при зміні подачі від s =14, 5 мм/хв до s =27, 0 мм/хв (схема круглого внутрішнього шліфування) на рівні травлення h
тр=100 – 140 мкм розмір дефектів, внесених обробкою, збільшується в 3,5 рази і досягає 300 мкм і більше. Наслідком підвищеної дефектності поверхневого шару виробу є зниження його міцності. Зміна подачі від s =4,0 мм/хв до s =27,0 мм/хв призводить до дворазового зниження міцності виробів на згин.
Одним із факторів, які суттєво змінюють ситуацію в зоні різання, є стан робочої поверхні алмазних кругів і їх ріжуча спроможність, яка постійно змінюється під час обробки КНМ. Так, наприклад, при чорновому шліфуванні ситалів [5] алмазні круги через 5 – 10 хвилин експлуатації повністю втрачають свої ріжучі властивості. Стан робочої поверхні алмазних кругів визначається геометричною формою верхівок зерен і щільністю розподілу зерен по глибині робочого шару інструменту. Вихідними даними для визначення початкового стану є характеристики інструменту та умови його правки. Однак у літературі відсутній системний підхід до встановлення взаємозв’язків між характеристиками алмазного інструменту, його зносом при різних умовах шліфування, силами різання, способами відновлення ріжучих властивостей інструменту та їх впливом на дефектність поверхневого шару виробів.
Експериментально встановлена залежність зміни складових сили шліфування від ступеня затупленості круга, яке пов’язано зі збільшенням об'єму сошліфованого матеріалу. Ця залежність враховує параметри режиму шліфування і має вигляд [5]
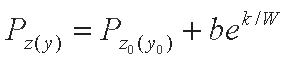
де P
z0(y0) – значення відповідних складових сили шліфування при W=0; W – питомий об'єм сошліфованого матеріалу, мм, який визначається як відношення об'єму сошліфованого матеріалу до площі робочої поверхні круга; k – коефіцієнт, який характеризує швидкість наростання сили в залежності вид затуплення інструменту; b – коефіцієнт приросту сили шліфування при збільшенні W. В свою чергу, коефіцієнти k і b є функціями параметрів режиму шліфування.
Затуплення інструменту супроводжується значним зростанням сил різання (особливо радіальної складової – в 2 – 4 рази) у порівнянні з роботою гострим кругом. Особливо чітко це просліджується при роботі кругами з більш дрібною зернистістю та меншою міцністю алмазів (рис. 1). Зниження дефектності простежується практично на всіх рівнях травлення і, що особливо важливо на значній глибині, при h
тр >300 км.
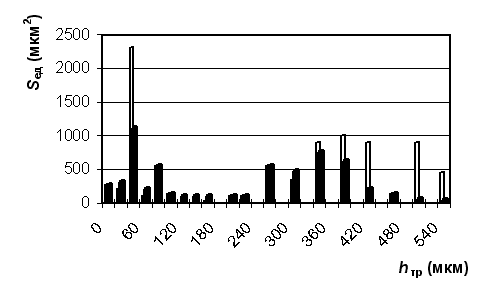
Рисунок 1. Діаграма залежності площі одиничного максимального мікродефекту S
од від глибини травлення. Шліфування ситала АС-418 за схемою круглого внутрішнього шліфування кругом 1А1 200х6х3х76 АС6-100/80-4М201 у стані: ♦ – вихідному; ◊ – затупленому (W = 28 мм)
Технологічні характеристики застосованих алмазів (зернистість, конфігурація, міцність) впливають на ступінь зносу кругів, що призводить до змін величини сил різання та дефектності поверхні, що формується. Встановлено, що застосування кругів більш дрібної зернистості (100/80 проти 250/200) забезпечує зменшення розмірів внесених дефектів практично на всіх рівнях травлення, знижуючи глибину проникнення дефектного шару вдвічі. Застосування інструменту з більш міцними алмазними зернами (АС 20 у порівнянні з АС 6) призводить під час обробки ситалів до значного (до 12 разів) підвищення дефектності обробленої поверхні.
Одним із ефективних методів впливу на процеси різання КНМ є застосування поверхнево-активних середовищ направленої дії [6], які змінюють характеристики міцності оброблюваного матеріалу і зменшують енергетичні витрати на його диспергування. Так для технічних стекол і ситалів, речовин дуже крихких, сила різання на відміну від обробки пластичних матеріалів визначається опором матеріалу сколюванню (крихкому зсуву) у площині максимальних напружень зсуву. Сила, що здійснює зсув матеріалу під час різання, визначає рівень як тангенціальної, так і нормальної складових сили різання, впливаючи як на енергоємність процесу різання (відповідальна P
z), так і на силовий вплив на оброблювану поверхню, який призводить до розвитку дефектного шару (відповідальна P
y ).
При інших рівних умовах ці параметри залежать від значення питомої поверхневої енергії твердого тіла або від величини його вільної поверхневої енергії при утворенні нових поверхонь. Введення в зону диспергування твердих тіл поверхнево-активних ТС супроводжується зниженням їх вільної поверхневої енергії за рахунок адсорбційних взаємодій атомів середовища і тіла, що деформується, які відбуваються на поверхні, що формується, тобто, до відповідної зміни його міцності. Для крихких матеріалів це насамперед призводить до пропорційного зменшення їх мікротвердості. Описані явища пов'язані з проявом адсорбційного ефекту зниження міцності твердих тіл.
Розроблені комп'ютерно-математичні моделі дефектності поверхні, що формується [7], дозволяють досліджувати вплив ТС різного ступеня активності на енергоємність процесів диспергування КНМ під час різання і прогнозувати розвиток дефектного шару. Це дає можливість на етапі попереднього проектування ТП виробництва виробів формулювати вимоги до властивостей ТС, що використовуються на різних операціях обробки.
Враховуючи результати теоретичних досліджень, запропоновані ТС для операцій лезової обробки (а. с. № 1331053), шліфування та полірування технічних стекол і кришталю (а.с. № 1654319), алмазного шліфування технічних ситалів. Середовища являють собою водні розчини синтетичних миючих засобів, які є активними ПАВ, що забезпечує їх підвищений вплив на матеріал припуску, знижує енергоємність процесу різання, покращує якість обробки. Названі середовища відрізняє простота виготовлення, гігієнічність, низька вартість.
Запропоновані ТС порівняно з кращими складами, які рекомендуються в літературі (наприклад, емульсоли ЕМУС, НГЛ-205 та ін.) дозволяють на операціях попереднього формоутворення виробів із технічних стекол і ситалів (точіння, чорнове шліфування) знизити енергоємність процесу різання до 40%, сприятливо змінивши глибину і структуру дефектного шару, який виникає в результаті обробки. Загальна глибина проникнення дефектів під час обробки технічних ситалів зниження розмірів дефектів досягає 4 – 10 разів. Знеміцнюючи ОМ, поверхнево-активні ТС поліпшують умови роботи для абразивного інструменту, зменшуючи його знос. Застосування під час шліфування рекомендованої ТС у порівнянні з використанням води дозволяє скоротити число правок та об’ємний знос кругів до 1,5 разу.
Враховуючи технологічну спадковість робочої дії інструменту і маючи одержані експериментально-теоретичним шляхом відомості про глибину та структуру порушеного обробкою шару, можливе проектування раціональних ТП, характерною рисою яких будуть обґрунтовані міжопераційні припуски на обробку, що дозволить, у цілому, знизити собівартість одержання виробів за рахунок зміни глибини і структури порушеного обробкою шару на різних етапах їх виробництва.
Виходячи з особливостей фізико-механічних характеристик оброблюваного матеріалу в поєднанні зі способами одержання заготовок із них, встановлено, що в поверхневому шарі заготовки практично буде відсутній зруйнований шар (H
pш). Це дозволило при розрахунку міжопераційних припусків умовно вважати, що H
pш≈ 0. Тоді знаходження значень міжопераційних припусків зводиться до вирішення завдання раціонального перерозподілу сумарного припуску на обробку, що визначається як різниця розмірів заготовки та готової деталі, між операціями механічної обробки та зміцнення виробу.
Існуюча методика розрахунку раціональних значень міжопераційних припусків, що створювалась здебільшого для обробки металів, уточнена за рахунок наступних положень. При обробці матеріалів типу ситалів на проміжній стадії формоутворення відсутня необхідність повного вилучення порушеного шару, що залишився в оброблюваному матеріалі після попередньої обробки, тому що при певній глибині шліфування розміри дефектів, які вносяться працюючим інструментом в оброблювану поверхню, стають рівними, а при подальшому заглибленні і більшими, ніж ті, що залишені на цьому рівні в результаті виконання попередньої операції. Тому величину припуску , пов'язану з глибиною дефектного шару, який залишився в матеріалі після попередньої обробки і знімається на даному переході, доцільно призначати, виходячи з рівності розмірів дефекту, що вноситься, і вже внесеного в матеріал на попередній операції. Це дозволить істотно зменшити величину припусків на заключних стадіях обробки, скоротити час і зменшити технологічну собівартість операцій обробки виробів.
На рис. 2 подана запропонована схема розрахунку припусків, де: A і Б – поверхні заготовки та виробу, що остаточно сформувався; H
p1 – пошкоджений шар, що залишився після чорнового шліфування; H
p2, H
p3 – пошкоджені шари, що залишилися відповідно після чистового шліфування та доводки, з накладанням дефектів від попередніх операцій обробки; Z
1 – припуск, що знімається при чорновому шліфуванні; Z
2', Z
3', Z
хим' – припуски, що знімаються відповідно при чистовому шліфуванні, доводці, хімічному травленні і включають порушені шари, що залишилися після попередніх операцій обробки.
Виконаними теоретичними та експериментальними дослідженнями [8] підтверджена залежність інтенсивності розвитку дефектного шару при обробці технічних ситалів від рівня напружено-деформованого стану зони різання, який визначається ступеню силової дії на оброблюваний матеріал при різанні, що в значній мірі залежить від схеми шліфування. З метою забезпечення мінімального розвитку дефектного шару в процесі різання і підвищення за рахунок цього експлуатаційних характеристик виробу, потрібно вибір схеми обробки здійснювати, виходячи з критерію мінімального силового впливу на оброблювану поверхню. Для цього треба забезпечити розворот сумарної сили різання в напрямку припуску, що видаляється, при зменшенні її значення.
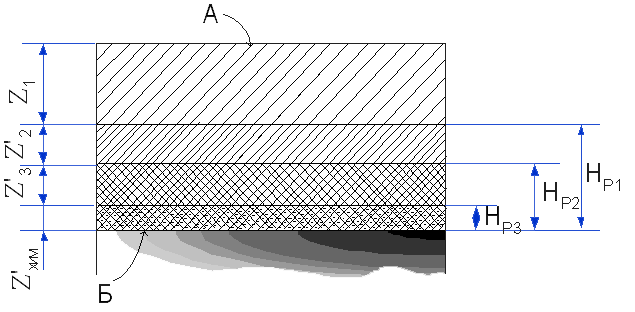
Рисунок 2. Запропонована схема розрахунку мінімальних асиметричних припусків на обробку КНМ
Правомірність наведених вище положень була апробована в умовах обробки виробів типу дисків із ситалу, які використовуються в якості елементів приладів в електронній техніці. Диски мають вигляд пластин круглої форми діаметром 18...40 мм і товщиною 12...28 мм. Відхилення від товщини пластини не повинно перебільшувати ± 8 мкм. Експлуатаційні характеристики виробів потребують забезпечення високих вимог до якості робочої (виконавчої) поверхні пластин (шорсткість R
a=0,32 мкм і відсутність дефектного шару, який виникає при обробці).
Технологія одержання заготовок визначає припуск на обробку пластин, який перевищує необхідний розмір не менш ніж на 2,0...2,5 мм. Тому подальша обробка включає плоске шліфування неробочої поверхні пластини з метою забезпечення базової площини, а потім – шліфування робочої поверхні для одержання потрібних якості та розмірів деталі. На заключній стадії обробки здійснюється хімічне травлення дефектного шару матеріалу, що виник під час шліфування, з наступним іонним зміцненням робочої поверхні пластини. Технологічна собівартість обробки пластин залежить від раціональності поопераційного розподілення загального припуску на обробку з урахуванням призначених вхідних параметрів технологічного процесу.
В умовах конкретного виробництва шліфування робочої поверхні пластин може бути здійснено при реалізації схем плоского торцевого шліфування за пружною схемою (шліфування торцем чашкового круга) та плоского торцевого шліфування з примусовою поперечною подачею круга (урізне шліфування периферією чашкового круга). За першою схемою зусилля різання спрямовані безпосередньо в оброблювану поверхню проти спрямування зусиль різання в припуск, який видаляється, за другою схемою, що повинно позитивно сказатися на розвитку дефектного шару при реалізації схеми урізного шліфування.
Це положення було підтверджено експериментально. Було встановлено, що урізне шліфування забезпечує більш високу якість пластин у порівнянні з торцевим шліфуванням за пружною схемою, що видно з результатів їх обробки кругами зернистості 80/63, які використовувалися на заключній стадії шліфування.
Аналогічні дані були одержані і авторами роботи [9] при шліфуванні пластин кремнію.
Технологічний процес обробки пластин проектувався, виходячи з використання схеми плоского торцевого урізного шліфування робочої поверхні пластин. При цьому здійснювалось шліфування кругами 12А2 125х50х20х2,5 АС6-4-М2-01 з різною зернистістю в залежності від операцій: чорнового шліфування – 125/100, напівчистового – 100/80, чистового – 80/63. Швидкість шліфування v= 30 м/с. Робоча подача супорту верстата з закріпленим на ньому пластинами в напрямку круга здійснюється зі швидкістю v
в= 10...200 мм/хвил, зменшуючись при переході від чорнових операцій до чистових. Глибина різання відповідає розрахунковому значенню припуску для кожної операції. Максимальна швидкість видалення матеріалу досягає для кругів зернистістю 125/100, 100/80, 80/63 відповідно 140, 105 і 80 мкм/хвил при обробці з використанням у якості ТС води.
        Розрахунковий припуск на складові операції Z'
imin визначається відповідно з рівнянням [10]

де R
zi-1, h'
di-1, ρ
i-1 – відповідно висота мікро нерівностей, глибина дефектного шару та сумарні значення просторових відхилень поверхні, які одержані на попередньому переході; ε
yi – похибка установки деталі на переході, що виконується.
В конкретному випадку ε
yi=0, тому що всі операції шліфування здійснюються без переустанови заготовок. Величина ρ
i-1 визначалась відповідно до рекомендацій, пов’язаних із технологією одержання заготовок. Для розрахунку Z'
imin експериментально вимірювались шорсткість оброблюваної поверхні; глибина та структура дефектного шару ситалу після обробки; розміри вихідних дефектів, які виникають на оброблюваній поверхні при кожному виді обробки. Величину припуску h'
di-1, яка пов’язана з глибиною дефектного шару, що залишився в матеріалі після попередньої обробки і знімається на даному переході, призначали, виходячи з рівності розмірів дефекту, що вноситься і вже внесеного в матеріал на попередньої операції.
В табл. 1 наведені результати розрахунків міжопераційних припусків з урахуванням того, що загальний мінімальний припуск на пластину складає 2,0 мм і повинен бути раціонально розподіленим між операціями обробки робочої плоскості пластини.
Таблиця 1. Характеристики якості оброблюваної поверхні пластин і міжопераційні припуски, що призначені для видалення
Технологічна операція, або перехід |
Шліфування кругами зернистості: |
Хімічне травлення |
125/100 (чорнове) |
100/80 (напівчистове) |
80/63 (чистове) |
Параметр, який визначається |
        |
        |
        |
        |
Просторові відхилення поверхні ρi-1, мкм |
55 |
        |
        |
        |
Шорсткість Rzi-1, мкм |
5.6 |
3.0 |
1.45p |
0.025 |
Дефектний шар hd, мкм |
280.0 |
220.0 |
150.0 |
        |
Порушений шар Hp , мкм |
286.0 |
223.0 |
152.0 |
0.025 |
Розмір вихідного дефекту dd , мкм |
30.0 |
20.0 |
15.0 |
        |
Дефектний шар h'di-1, який належить вилучити, мкм |
130.0 |
90.0 |
80.0 |
        |
Раціональний мінімальний припуск на операцію Z'imin, мм |
1.624 |
0.191 |
0.093 |
0.092 |
Мінімальний припуск на операцію Zimin , мм за базовою методикою |
1.221 |
0.341 |
0.286 |
0.152 |
При відомих значеннях максимальної швидкості видалення матеріалу на операціях шліфування, орієнтуючись на значення міжопераційних припусків, можна визначити трудомісткість операцій механічної обробки для двох варіантів технологічних процесів, які відрізняються методикою розрахунку припусків – той, що пропонується, і традиційний, коли на кожній наступній операції видаляється весь дефектний шар, що сформований на попередній операції. Результати розрахунків наведені в табл. 2.
Таблиця 2. Дані щодо трудомісткості операцій механічної обробки пластин
Варіант обробки |
Час обробки виробів на операціях шліфування, хвил: |
Сумарний час обробки, хвил. |
        |
чорнового |
напівчистового |
чистового |
        |
Варіант, що пропонується |
10.15 |
1.82 |
0.80 |
12.3 |
Базовий варіант |
7.27 |
3.25 |
3.60 |
14.1 |
Аналіз результатів, що наведені в табл. 1 і 2, свідчить про те, що запропонований варіант перерозподілу міжопераційних припусків, дозволяє скоротити тривалість механічної обробки пластин на 18-20% і в 1,6 рази зменшити глибину дефектного шару, який повинен бути видаленим на операції хімічного травлення, що дозволить у стільки ж разів знизити трудомісткість і технологічну собівартість операції зміцнення виробів.
На основі результатів проведених досліджень можна зробити висновки щодо організації ефективних ТП обробки виробів із технічних стекол і ситалів, основними положеннями яких є: вибір схеми обробки, виходячи з критерію мінімального силового впливу на оброблювану поверхню; багатостадійність процесу механічної обробки з тенденцією зменшення напружено-деформованого стану в зоні різання та інтенсивності процесу диспергування оброблюваного матеріалу на заключних операціях за рахунок призначення певних режимів, вибору ТС, характеристик ріжучого інструменту, способів підтримання його ріжучої здатності з метою забезпечення підвищеної якості поверхні, що формується, перед операцією зміцнення. Визначені підходи до вирішення завдання підвищення ефективності механічної обробки можуть бути поширені і на обробку виробів із інших КНМ, наприклад, технічної кераміки.
1. Калафатова Л.П. Резание стекломатериалов // Машиностроение. Энциклопедия. – М.: Машиностроение, 2000. – Т. III3 «Технология изготовления деталей машин». – С. 142-145.
2. Хрульков В.А., Тародей В.А. Механическая обработка деталей из керамики и ситаллов. – Саратов: Изд-во Сарат. ун-та, 1975. – 185 с.
3. Калафатова Л.П. Влияние технологической наследственности на эффективность процессов механической обработки стекломатериалов // Справочник. Инженерный журнал. – М.: Машиностроение. – 1997. - № 9. – С. 7-11.
4. Калафатова Л.П. Диагностика дефектности обработанной поверхности технических ситаллов // Прогрессивные технологии и системы машиностроения: Междунар. сб. научн. трудов. – Донецк: ДонГТУ. – 1997. – Вып.4. – С. 66-75.
5. Белов С.Г., Калафатова Л.П. Правка шлифовальных кругов как способ повышения эффективности абразивной обработки // Надійність інструменту та оптимізація технологічних систем. Зб.наук.праць. – Краматорськ-Київ: ДДМА, вип. №15, 2004, – С.78-85.
6. Калафатова Л.П. Технологические среды как фактор повышения эффективности обработки хрупких неметаллических материалов // Резание и инструмент в технологических системах: Междунар. научн. -техн. сборник. – Харьков: НТУ «ХПИ». – 2003. – Вып. 64. – С. 119-126.
7. Калафатова Л.П. Изменение напряженно-деформированного состояния зоны обработки при алмазном шлифовании ситалла за сет использования технологических сред // Практика и перспективы развития институционного партнерства. Известия ДонНТУ-ТРТУ: Междунар. Сб. научн. трудов. – Донецк: ДонНТУ. – 2003. – Т. 2. – С. 188-194.
8. Калафатова Л.П. Моделирование взаимодействия алмазного инструмента с обрабатываемыми образцами из технических ситаллов // Прогрессивные технологии и системы машиностроения: Межд. сб. научн. трудов. – Донецк: ДонГТУ. – 2003. – Вып. 24. – С. 78-82.
9. Готра З.Ю. Технология микроэлектронных устройств: Справочник. – М.: Радио и связь, 1991. – 528 с.
10. Калафатова Л.П. Особенности методики расчета рациональных межоперационных припусков при обработке изделий из материалов на основе стекла // Підвищення надійності відновлюємих деталей машин. Фізичні та комп’ютерні технології: Вісник Харківського державного технічного університету сільського господарства. – Харків: ХДТУСГ. – 2002. – Вип. 10. – С. 372-378.