The abstract of the final work theme
Сontent
1 Introductory part
Introduction
Work urgency
The purpose and work problems
2 Theoretical part
The theory of high-speed cutting
The mineral keramik cutting tool
Animation
3 Final part
Conclusions
The literature
1 Introductory part
Introduction
Principal views of high-speed cutting of metals are: high-speed cutting and internal surfaces cutting, milling, gear milling, planing and drilling.
Distinctive feature of all kinds of high-speed processing is application of tool materials different the raised durability and wear resistance. A wide circulation such tool materials as have received firm alloys and mineral keramik.
Сontent
Work urgency
Нigh-speed processing by cutting is mainly applied for cutting tempered and hard-processing materials. At the same time one of tendencies of development of modern mechanical engineering is working out and application of progressive tools on the basis of high-quality tool materials, in particular, mineral keramik. In this connection there is a question on rational use of such tool materials at processing of the constructional steels having most a wide circulation.
The purpose and work problems
The work purpose — the analysis of use of the cutting tool with mineral keramik for processing of constructional steels in the conditions of high-speed processing by cutting.
The primary goal of work: definition of the most rational modes of processing of constructional steels by the cutting tool with mineral keramik in the conditions of high-speed processing by cutting.
2 Theoretical part
Сontent
The theory of high-speed cutting
Prominent feature of high-speed processing of metals cutting is decrease in forces of cutting in some range of speeds. However the most important factor is heat redistribution in a cutting zone. At small sections of a cut, in the given range of speeds heat great bulk concentrates in a shaving, without having time to pass in preparation. It allows to conduct processing of the tempered steels without being afraid of blanket holiday. From here main principle HSC — the small section of a cut removed with high speed of cutting, and accordingly high turns of a spindle and high minute giving.
The essence of this way of processing of metals consists that with increase of speed of cutting degree of deformation of metal in process shavingeducation decreases that proves to be true, in particular, reduction compression shavings and forces of cutting at high-speed cutting. Deformation reduction in separate particles of a shaving causes reduction of quantity of the warmth formed in the course of cutting in each particle. Besides, each particle of a shaving at high speed of cutting adjoins to a forward surface of a cutter during smaller time, than at rather low speed. Thanks to it at high-speed cutting from each separate particle of a shaving in a cutter arrives less warmth, than at low speed of cutting.
At increase in speed of processing the quantity of the warmth passing from a shaving in the processed detail decreases also. Experiences well proves to be true that at high speeds of cutting the processed surface heats up only slightly.
Thus, in the conditions of high-speed cutting distribution of the formed warmth is more favorable, than at moderate speeds; in the shaving which has turned out at high speed of cutting, remains warmth more than at low speed.
The basic laws of high-speed cutting are presented in drawing 1.
Fig. 1 — Interrelation of the cutting speed and the outprocess parametres of HSC (Р — cutting forse; t — temperature in a cutting zone)
The development of high-speed cutting has caused necessity of the further increase of durability and firmness carboloy cutters.
One of the actions directed to achievement of this purpose, improvement of quality of firm alloys was. Other way - creation а new high-quality tool materials which known representative is а mineral keramik.
Besides development of high-speed cutting has caused necessity of the further increase of durability and firmness of the cutting tool, in particular mineral keramik, carboloy, with application of superfirm materials.
One of the actions directed to achievement of this purpose, improvement of quality of tool materials was. Other way of increase of durability and firmness carboloy cutters — application of a negative forward corner of a cutter.
Fig. 2 — Pressure of a chip upon a cutting tool at negative (a) and positive (b) forward corners
Chip formation at different speeds of cutting is illustrated on figures 3 and 4.
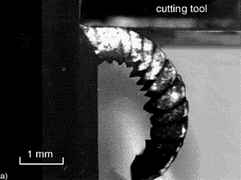 |
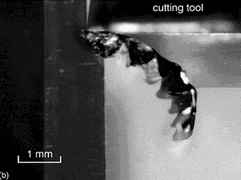 |
|
|
|
|
|
|
|
|
Fig. 3 — Chip formation at cutting speed V = 15 m/s |
Fig. 4 — Chip formation at cutting speed V = 45 m/s |
Сontent
The mineral keramik cutting tool
Providing high efficiency at processing of various materials by cutting, mineral keramik owing to specificity of its physical and mechanical properties cannot exclude necessity of application of traditional firm alloys. It only expands a range of used powder cutting materials in that area where can play an intermediate link role between firm alloys and containing diamonds and other superfirm composite materials. Cutting ceramics — valuable addition to firm alloys with good prospects of the further increase in its consumption. Mineral keramik on the basis of Al203 it is possible to divide into three groups: — Purely oxide ("white") ceramics;
— The mixed ceramics;
— oxide ("black") ceramics.
Now mineral keramik apply to semifair and fair continuous turning details from grey, malleable, high-strength, bleached cast-iron, the tempered and improved steels, some marks of nonferrous metals and alloys, and also nonmetallic materials (graphite, etc.) at high speeds of cutting (to 600 — 800 m/min) without application of a greasing-cooling liquid (GCL), for drawing by manufacture of a wire from nonferrous metals and for manufacturing of wearproof details of the cars which are exposed to intensive unaccented abrasive deterioration (snuffled, nozzles, etc.).
Animation
Fig. 5 — The high-speed cutting process scheme (animation in volume — 64 кВ, consists of 15 shots, 8 repetitions)
4 Final part
Сontent
Conclusions
So, it is possible to notice that use of the cutting tool with mineral keramik in the conditions of high-speed cutting for processing of constructional steels has the advantages, however only under certain conditions processings. Nevertheless, at creation of such favorable conditions application of the cutting tool with mineral keramik for processing of constructional steels in the conditions of high-speed cutting allows to raise considerably productivity at enough high indicators of accuracy and quality of processed surfaces of details.
References
1. Клушин М. И. Скоростное резание металлов. — М.: Государственное научно-техническое издательство машиностроительной литературы, — 1947, 124с.
2. Прейс Г.А. Скоростное резание металлов. — К. — М.: Машгиз, — 1950, 84с.
3. Скоростное резание металлов. — под. ред. Р. Д. Бейзельмана. М.: Государственное научно-техническое издательство машиностроительной и судостроительной литературы, — 1953, 164с.
4. Journal of Manufacturing Science and Engineering, 2005 by ASME. G. Sutter, A. Molinari.
5. Соловов А. Некоторые секреты высокоскоростной обработки металлов [Electronic resource] — Access mode to article:
http://www.obo-rt.ru/arhiv/3(3)/21%20Nekotorie%20sekrety.html
6. Мутылина И.Н. Технология конструкционных материалов. Обработка металлов резанием. Виды инструментальных материалов и области их применения. [Electronic resource] — Access mode to article:
http://window.edu.ru/window_catalog/pdf2txt?p_id=18616&p_page=15
7. Инструментальные материалы. Минералокерамические материалы. [Electronic resource] — Access mode to article:
http://www.info.instrumentmr.ru/instrum_material2.shtml
8. Инструментальные материалы. [Electronic resource] — Access mode to article:
http://www.bestreferat.ru/referat-57681.html 9. Твердые сплавы. Минералокерамические твердые сплавы. [Electronic resource] — Access mode to article:
http://m-met.ru/?Tverdye_splavy:Mineralokeramicheskie_tverdye_splavy 10. Высокоскоростная обработка. [Electronic resource] — Access mode to article:
http://www.delcam-ural.ru/cam/tehpodderjka
11. Теория токарной обработки. Точение с высокими скоростями. [Electronic resource] — Access mode to article:
http://tehno-line.ru/files/theory/Turning/3-2-1.htm
|