Реферат з теми випускної роботи
Зміст
1 Вступна частина
Вступ
Актуальність роботи
Ціль і задачи роботи
2 Теоретична частина
Основні положення теорії високошвидкісної обробки різанням
Особливості устаткування і ріжучого інструменту
Мінералокерамічний ріжучий інструмент
3 Практична частина
Опис ходу експерименту
Анімація
4 Заключна частина
Висновки
Література
1 Вступна частина
Вступ
У сучасних умовах загального прагнення до підвищення продуктивності праці і нарощуванні обсягів виробництва актуальною стає розробка і впровадження нових і прогресивних методів обробки. Такі методи повинні дозволяти здійснювати обробку заготовок отримуваних по новітніх технологіях, для яких основною тенденцією розвитку є зменшення припусків на механічну обробку. У технології машинобудування одним з найбільш значних і принципових досягнень в області розробки методів, що були описані вище впродовж вже тривалого періоду часу стала обробка металів з вельми високими швидкостями різання, що отримала назву швидкісної обробки різанням.
Різання металів на великих швидкостях (швидкісне різання), що виникло в СРСР в 50-х роках минулого сторіччя, до теперішнього часу отримало теоретичне обґрунтування і застосовується на металоріжучих верстатах. Це було досягнуто об'єднаними зусиллями учених, інженерів-виробничників (А. У. Крівоухова, А. І. Ісаєва, П. П. Грудова і ін.) і токарів-новаторів (Р. С. Борткевіча, П. Би. Бикова, В. М. Бірюкова, В. Н. Трутнева, В. Я. Карасева, В. До. Семінського, Д. І. Рижкова, В. А. Колесова і багато інших).
Швидкісне різання металів стало можливим у результаті як удосконалення твердих сплавів, так і розвитку нових принципів конструювання і експлуатації ріжучих інструментів.
Основними видами швидкісного різання металів є: швидкісне точіння і розточування, фрезерування, зубофрезеровання, стругання і свердлення.
Відмітною особливістю усіх різновидів високошвидкісної обробки є застосування інструментальних матеріалів, що відрізняються підвищеною міцністю і зносостійкістю. Широкого поширення набули такі інструментальні матеріали як тверді сплави і мінералокераміка.
Мінералокерамічні матеріали для виготовлення ріжучих інструментів почали застосовувати порівняно нещодавно. Найбільш широкого поширення набув мінералокерамічений матеріал марки ЦМ332, основнову якого складає окис алюмінію Аl2О3 з невеликим додаванням окису магнію МgО. Мінералокераміка, що не містить дорогих і дефіцитних елементів, має наступні основні переваги: підвищену продуктивність і якість обробки, стабільність цін і практично необмежені сировинні ресурси похідних матеріалів.
Грунтуючись на результатах досліджень, можна зробити висновок про те, що швидкісне різання дозволяє забезпечити підвищення продуктивності лезвійной обробки при високій якості оброблюваної поверхні. Поява нових інструментальних матеріалів дозволяє значно підвищити швидкості різання, проте вимагає проведення додаткових досліджень для вивчення закономірностей високошвидкісного різання.
Зміст
Актуальність роботи
Високошвидкісне різання за останні роки зробило революційний переворот у методах механічної обробки. Вирішальним фактором під час оцінювання процесу високошвидкісної обробки металів різанням є продуктивність верстатів, яка визначає вартість виробництва і, таким чином, амортизацію інвестицій. Технологія високошвидкісної обробки різанням відноситься до найбільш прогресивних і таких, що швидко розвиваються. Проте, не дивлячись на більш ніж півсторічну історію свого розвитку, ця технологія ще не занадто розповсюджена. Цей вид обробки різанням є відносно новим технологічним процесом, і досвід його застосування в наший країні вельми обмежений. В більшості випадків це пов'язано з недосконалістю технічної бази вітчизняного виробництва, а також із специфічними вимогами до верстатів, систем з ЧПК, ріжучого інструменту, допоміжного інструменту з системою закріплення інструменту, засобів технічного оснащення, систем програмування, кваліфікації технолога програміста і оператора верстата з ЧПК. Зневага однією з цих складових може звести до нуля всі попередні зусилля.
Окрім цього слід зазначити, що швидкісна обробка різанням переважно застосовується для точіння загартованих і важкооброблюваних матеріалів. Тим часом однієї з тенденцій розвитку сучасного машинобудування є розробка і застосування прогресивних інструментів на основі високоякісних інструментальних матеріалів, зокрема, мінералокераміки. У зв'язку з цим виникає питання про раціональне використання таких інструментальних матеріалів для обробки конструкційних сталей, що мають найбільш широке розповсюдження.
Ціль і задачи роботи
Ціль роботи — аналіз можливості використання ріжучого інструменту з мінералокерамікою для обробки конструкційних сталей в умовах високошвидкісного точіння.
Головна задача роботи: визначення найбільш раціональних режимів обробки конструкційних сталей ріжучим інструментом з мінералокерамікою в умовах високошвидкісного точіння.
2 Теоретична частина
Зміст
Основні положення теорії високошвидкісної обробки різанням
Характерною особливістю високошвидкісної обробки металів різанням є зниження сил різання в деякому діапазоні швидкостей. Проте найбільш важливим фактором є перерозподіл тепла в зоні різання. При невеликих перетинах зрізу, в даному діапазоні швидкостей основний обсяг тепла концентрується в стружці, не встигаючи переходити до заготовки. Саме це дозволяє вести обробку загартованих сталей уникаючи відпуску поверхневого шару. Звідси основний принцип високошвидкісної обробки — малий перетин зрізу, що знімається з високою швидкістю різання, і відповідно високі обороти шпінделя і висока хвилинна подача.
Суть цього способу обробки металів полягає у тому, що з підвищенням швидкості різання зменшується ступінь деформації металу в процесі стружкоутворення, що підтверджується, зокрема, зменшенням усадки стружки і сили різання при швидкісному точінні. Зменшення деформації в окремих частках стружки обумовлює зменшення кількості теплоти, що утворюється в процесі різання в кожній частинці. Крім того, кожна частка стружки при високій швидкості різання стикається з передньою поверхнею різця протягом меншого часу, ніж в умовах меншої швидкості. Завдяки цьому при швидкісному точінні з кожної окремої частки стружки в різець надходить менша кількість теплоти, ніж в умовах меншої швидкості різання.
При збільшенні швидкості обробки зменшується і кількість теплоти, що надходить до оброблюваної деталі зі стружки. Досліди багатьох дослідників, які займалися із цим питанням (А. В. Кривоухов, В. К. Семинський, В. А. Колесов та інщі), добре підтверджують, що в умовах високих швидкостей різання оброблена поверхня нагрівається незначно.
Таким чином, в умовах високошвидкісного точіння розподіл теплоти, що утворилася, більш сприятний ніж в умовах помірних швидкостей; у стружці, що виникає в умовах високих швидкостей різання, залишається більша кількість теплоти, ніж в умовах низьких швидкостей різання.
Головні залежності процесу високошвидкісної обробки різанням, які було наведено вище, проілюстровано на рисунку 1.
Рис. 1 — Взаємозв'язом швидкості різання та похідніх параметрів процесу ВШО (Р — сила різання; t — температура у зоні різання)
Несмотря Не дивлячись на позитивне значення підвищення швидкості обробки, умови роботи ріжучої кромки різця при швидкісному точінні важчі, ніж в умовах менших швидкостей. Хоча кількість теплоти, що надходить до різця з кожної частки стружки при швидкісному різанні менша за умов помірних швидкостей різання, загальна кількість теплоти, що надійде до різця протягом того ж часу його роботи, буде більша за умов високих швидкостей обробки, ніж низьких. Це пояснюється тим, що в першому випадку різець отримає теплоту з більшої кількості часток стружки, ніж за той же час в умовах невисоких швидкостей.
В результаті під час швидкісного різання різець нагрівається значно більше, ніж під час роботі з помірною швидкістю різання. Тому розвиток швидкісного різання зумовив необхідність подальшого підвищення міцності та стійкості твердосплавних різців.
Одним із заходів, спрямованих на досягнення цієї мети, є поліпшення якості твердих сплавів. Інший напрямок — створення нових високоякісних інструментальних матеріалів, серед яких відомим представником є мінералокераміка.
Зміст
Особливості устаткування і ріжучого інструменту
Розвиток швидкісного різання поставив нові вимоги до верстатобудування і абразивної промисловості.
Сучасні верстати повинні характеризуватися:
— достатньою потужністю, жорсткістю і вібростійкістю;
— широким діапазоном швидкостей шпінделя, переважно з електронним управлінням, що допускає плавне регулювання;
— ширшим застосуванням гідравлічних і електричних приладів;
— шпінделями, що добре змащуються і добре збалансовані;
— наявністю конвеєрного прибирання стружки;
— надійним рясним охолоджуванням ріжучих інструментів;
— ефективними способами подачі виробу до верстата і від верстата;
— пневмопристосуваннями для затиску.
Основна вимога до абразивної промисловості — виробництво широкої номенклатури алмазних кругів, украй необхідних для якісного заточування сучасних твердих сплавів.
Окрім цього розвиток швидкісного різання зумовив необхідність подальшого підвищення міцності і стійкості ріжучого інструменту, зокрема минералокерамического, твердосплавного, із застосуванням надтвердих матеріалів.
Одним із заходів, спрямованіх на досягнення цієї мети, стало поліпшення якості інструментальних матеріалів. Інший спосіб підвищення міцності і стійкості твердосплавних різців — застосування негативного переднього кута різця. Ріжуча здатність твердосплавних різців з позитивним кутом обмежується схильністю твердосплавних пластинок до викрошування. Це особливо помітно при точінні дуже твердих або загартованих сталей та під час роботи в умовах ударного навантаження (переривисте точіння, точіння з нерівномірним припуском, тощо).
Рис. 2 — Тиск стружки на різець при негативному (а) і позитивному (б) передньому кутах
Зазвичай при негативному передньому куті викрошування пластинки не відбувається, що пояснюється наступними факторами:
1) під час точінні різцями з негативним переднім кутом (- ) напрямок дії сили Р обумовлює стиснення (рис. 1, а) і забезпечує сприятливіші умови роботи пластинки твердого сплаву у порівнянні з умовами роботи різця з позитивним (+ ) переднім кутом (рис. 1, б);
2) при негативному передньому куті і позитивному куті нахилу ріжучої кромки вершина різця захищена від ударів при точінні переривистих поверхонь.
Усе зазначене вище відноситься головним чином до обробки стали. Різання чавуну і кольорових металів вимагає значно менших витрат, таким чином, переваги негативних кутів в даному випадку позначаються слабше. Внаслідок цього при обробці вказаних матеріалів різці з негативними передніми кутами застосовуються рідше.
Разом з перевагами різці з негативним переднім кутом мають ряд істотних недоліків:
1. При точінні різцями з негативним переднім кутом зростає сила тертя стружки об різець, унаслідок чого збільшується і потрібна потужність. Тому при роботі на недостатньо потужних верстатах доводиться зменшувати швидкість різання або подачу, а разом з тим і продуктивність.
2. При роботі даними різцями зростає радіальна сила Ру, що веде до спотворення форми оброблюваної деталі (при її недостатній жорсткості), вібрацій, тощо. Таким чином різці з негативним переднім кутом застосовуються лише для обробки стали з підвищеною і високою міцністю (бв = 800 МПа і більше), під час різанні з ударним навантаженням і при обробці заготовок з дуже твердим поверхневим шаром. Останнім часом прагнуть навіть у таких випадках користуватися різцями з позитивним переднім кутом.
Спостереження за зовнішнім виглядом сталевої стружки, що знімається різцями з позитивними і негативними передніми кутами (+ 20°; + 10°; 0°; - 20°) показує, що у всіх випадках збільшення швидкості різання приводить до збільшення радіусу завитків стружки. Під час зняття стружки з перетином t * s = 3,0 * 0,1 мм2 різцями з позитивними передніми кутами на невеликих швидкостях різання (порядка 20 м/хв) стружка має вид туго закручених архімедових спіралей. Але зі збільшенням швидкості різання вона набуває форми суцільної спіральної стрічки, діаметр завитка якої зростає від 15 до 20 мм. при швидкостях різання близко 100 м/хв і до 50 см при швидкостях 300 м/хв. Одночасно з цим відбувається і зміна кольору стружки від світлого (сталевого) до синього. Під час роботи різцями з негативними передніми кутами на невеликих швидкостях різання (близько 20 м/хв) стружка сходить завитками завдовжки не більш за один завиток; при великих швидкостях різання стружка має форму суцільної спіральної стрічки, радіус завитків якоі росте значно швидше, ніж для різців з позитивними передніми кутами. Так, при негативному передньому куті = - 10° на швидкостях різання більше 200 м/хв стружка сходить у вигляді прямої (неспіральною) стрічки. При куті = - 20° і швидкості різанні V = 60 м/хв стружка ламається на відрізку у 2 — 4 завитки, і вже при швидкості різання більше 75 м/хв вона сходить у вигляді прямої (неспіральною) стрічки.
Колір стружки змінюється так само, як і при позитивних передніх кутах.
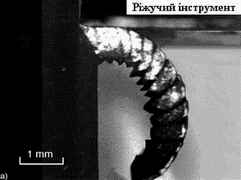 |
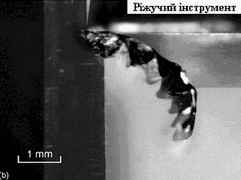 |
|
|
Рис. 3 — Формування стружки при швидкості різання V = 15 м/сек |
Рис. 4 — Формування стружки при швидкості різання V = 45 м/сек |
На стружці, яку було знято різцем з негативним переднім кутом = - 20° помітні вельми сильні зсуви окремих елементів (зовнішня поверхня стружки пилообразна) навіть за подачі s = 0,1 мм/об. При великих швидкостях різання ці зрушення стають менш помітними і за умовами швидкостей, що перевищують 200 м/хв, стружки,що зняті різцем = - 20° майже не відрізняються по вигляду від стружок,що зняті різцями з позитивним переднім кутом. При подачах (товщині стружки) більших за 0,1 — 0,3 мм/об і невисоких швидкостях різання (V = 40 — 50 м/хв) стружка, що знімається інструментами з негативними передніми кутами, розділена на окремі елементи, тобто представляє типову стружку сколювання.
Можна зробити виcновок, що усадка стружки у межах швидкостей різання до 40 м/хв, особливо при роботі з негативними передніми кутами, має безперечну тенденцію до збільшення. Але при збільшенні швидкості різання вище 40 м/хв відбувається зменшення усадки стружки. Треба зазначити, що особливо інтенсивно це відбувається під час роботи з негативними передніми кутами.
Дуже актуальним є вивчення впливу швидкості різання на зміну тангенціальних зусиль при роботі різцями з позитивними і негативними кутами. Американські вчені, що проводили вимірювання тангенціальних зусиль при різанні сталей різцями з позитивними і негативними передніми кутами в умовах широкого діапазону зміни швидкостей різання (від 30 до 350 м/хв), встановили, що при великих швидкостях різання тангенціальне зусилля із збільшенням швидкості різання зростає при використанні позитивних передніх кутів і, навпаки, зменшується при використанні негативних.
За даними цих досліджень величина тангенціального зусилля для обох випадків буде однаковою, і далі, при збільшенні швидкості різання, зусилля різання при негативних передніх кутах буде менше, ніж при позитивних.
Досліди проводилися із використанням сталі 50 і чавуну НВ = 143 в умовах вільного різання різцями з кутами = + 20°; + 10°; 0°, - 10° і - 20° при задньому куті 3°, при подачі s = 0,1 мм; різцями з кутами = + 10° і - 10° і заднім кутом 3°, при подачах 0,2 мм; різцями з кутами = + 10° і - 10° і заднім кутом 8° при подачі 0,05 мм.
Результати дослідів дозволяють зробити наступні висновки.
А. Прі різанні сталей:
1) збільшення швидкості різання при роботі різцями з позитивними передніми кутами викликає збільшення тангенціального зусилля різання;
2) при різанні різцями з нульовим переднім кутом швидкість різання в діапазоні від 50 до 350 м/хв на величину тангенціального зусилля різання не впливає;
3) збільшення швидкості різання в діапазоні 50 — 400 м/хв при роботі різцями з негативними передніми кутами викликає зменшення тангенціального зусилля різання;
4) значення швидкості різання, при якій зусилля різання стають однаковими для різців з негативними і позитивними передніми кутами, при обробці стали 50 досягає приблизно 400 м/хв.
5) у діапазоні швидкостей різання від 10 до 40 — 50 м/хв при роботі інструментами з нульовим і негативним переднім кутом спостерігається великий розкид експериментальних даних при загальній тенденції до зростання зусиль із збільшенням швидкості різання, тобто мають місце явища, що повторюють зміну усадки стружки в цьому діапазоні.
Природним поясненням такого явища представляється вплив на процес різання наросту, утворення якого у вказаному діапазоні швидкостей різання протікає найінтенсивніше.
Б. По чавуну.
1) при роботі різцями як з негативними, так і з позитивними передніми кутами тангенціальні зусилля різання у міру збільшення швидкості різання спочатку падають, а потім залишаються незмінними;
2) при невисоких швидкостях різання зусилля різання для різців з негативними передніми кутами більше, ніж для різців з позитивними передніми кутами;
3) при достатньо високих швидкостях різання (більше 100 м/хв) зусилля різання при роботі інструментами з негативним переднім кутом ( = - 10°) виявляються меншими, ніж при роботі з позитивним переднім кутом ( = + 10°).
Зміст
Мінералокерамічний ріжучий інструмент
Промислове виробництво ріжучої оксидної кераміки з Al203 почалося більше 45 років тому, а в 50-і роки минулого сторіття були створені сплав ЦМ332 (Al203 і до 1% оксидів інших металів) в нашій країні, керамічний матеріал "кермет" (2 — 10% Мо або Сг, решта Al203) і оксидно-карбідна кераміка (20 — 40% простих або складних карбідів перехідних металів IV — VI груп Періодичної системи Д.І.Менделєєва — титану, молібдену, вольфраму та ін., решта Al203) за кордоном. До середини 70-х років частка ріжучої кераміки в металообробці в цілому склала 2% (у ФРГ 6%, у США 5%), причому на неї доводилося 4% об'єму стружки, що знімається інструментальними матеріалами.
Початковим матеріалом для виробництва практично всіх марок ріжучої мінералокераміки, що випускаються в різних країнах служить технічний глинозем (V-Al203) чистотою 98,5 — 99,5% (основні домішки — оксиди кремнію, заліза, кальцію, натрію і калію від сотих до десятих відсотка кожного), отриманий обробкою бокситу із застосуванням соди або кислоти. Такий глинозем обпалюють при 1400 — 1600°С, перетворюючи його з v-модификації в а-модификацію (корунд). Обпалений глинозем розмелюють до зернистості 1 — 3 мкм (наприклад, в кульовому млині); подрібнення до великої частинок менш за 1 мкм небажано із-за можливого збільшення крихкості готового виробу. Розмолотий корунд піддають обробці кислотами для відмивання заліза, натертого в процесі помелу, промивають водою і висушують. Після цього підготовлений порошок формують, пресують, а потім спекають при температурі 1750 — 1900°С. Пластинки можна отримати також литтям під тиском.
Висока твердість мінералокераміки, теплостійкість до 1200°C, хімічна інертність до металу та опір окисленню багато в чому перевершують ці ж параметри твердих сплавів. Проте мінералокераміка поступається цим сплавам по теплопровідності, має нижчу межу міцності на вигін. Твердість мінералокераміки складає 90 HRA, значення при вигині 295 МПа (значення при вигіні твердих сплавів до 1700 МПа).
Мінералокераміку на основі Al203 можна розподілити на три групи:
— чисто оксидна («біла») кераміка, основу якої складає Al203 (до 99,7%) з незначним додаванням MgO, ZnO2 і др.;
— змішана кераміка, що представляє собою Al203 із додаванням тугоплавких металів (Ti, Nb, тощо);
— оксидна («чорна») кераміка — Al203 з додаванням карбідів тугоплавких металів (Ti, W, Мо) для підвищення її міцносних властивостей і твердості.
Пластини з «білої» кераміки отримують холодним пресуванням та подальшим спіканням. Процес економічний, вартість таких пластин мінімальна. Основний недолік цих пластин відносно невелика міцність, але їхні твердість (91 HRA — Росія, 93 — Японія, США) і червоностійкість великі. Представники цієї кераміки, наприклад, ЦМ332 (Al203 + 1% MgO) і ВО (більше 99 % Al203) — Росія і зарубіжні: СХЗ (Японія), V34 — США.
«Біла» кераміка застосовується для чистової і напівчистової обробки не оброблених термічно сталей, сірих чавунів.
Пластини зі «змішаної» і «чорної» кераміки отримують гарячим пресуванням, процес більш трудомісткий. Вітчизняна кераміка — ВОК (Al203 60 %, TiC 40%, тощо), К090 (Al203 + TiC) — США, тощо.
«Чорна» кераміка застосовується для чистової, напівчистової обробки ковких, високоміцних і відбілених чавунів, загартованих сталей, для обробки кольорових металів на основі міді; нітридная кераміка — для напівчистової обробки чавунів.
Разом з матеріалами на основі оксиду алюмінію випускається матеріал на основі нітриду кремнію Si3N4 — силініт (отримання — гаряче пресування) і кортиніт ОНТ з додаванням Al203 + TiC. Значення твердості для силініта — 94 HRA, а при вигині — 500 МПа. Новим інструментальним матеріалом, створеним на основі нітриду кремнію, є силініт-Р. Він використовується при чистовому точінні сталей, чавуну, алюмінієвих сплавів.
Мінералокерамічні матеріали виготовляються у вигляді пластин, які непереточуються, що істотно полегшує умови їх експлуатації. Ці пластинки приєднуються до корпусів інструментів механічним шляхом, приклеюванням або припаюванням.
Розширення споживання ріжучих керамічних матеріалів пов'язане з наростаючим дефіцитом вольфраму, що стимулює виробництво безвольфрамовых інструментальних матеріалів щляхом створення нових ефективних марок ріжучої кераміки і розвитком застосування інструменту з механічним кріпленням МНП, збільшенням в металообробці частки фінішних і чистових операцій при одночасному підвищенні твердості поверхні оброблюваних деталей.
В даний час мінералокераміку застосовують для напівчистового і чистового безперервного точіння, а також розточування деталей з сірих, ковких, високоміцних, відбілених чавунів, загартованих і покращуваних сталей, деяких марок кольорових металів і сплавів, а також неметалічних матеріалів (графіту, тощо) в умовах високих швидкостей різання (до 600 — 800 м/мін) без застосування змащувально-охолоджвальної рідини (СОР) для волочіння при виробництві дроту з кольорових металів і для виготовлення зносостійких деталей машин, що піддаються інтенсивному безударному абразивному зносу (сопел, насадок, тощо).
Мінералокерамічні інструменти доцільно застосовувати тільки на верстатах підвищеної жорсткості, що характеризуються роботою без вібрацій.
З метою поліпшення властивостей мінералокераміки проводяться роботи із створення керметов, що складаються з мінералокераміки і металевих домішок у вигляді карбідів вольфраму, молібдену та інш.
Істотним недоліком мінералокераміки є її вкрай низький опір циклічній зміні температури. Внаслідок цього навіть при невеликій кількості перерв в роботі на контактних поверхнях інструменту з'являються мікротріщини, які приводять до його руйнування навіть при невеликих зусиллях різання. Ця обставина обмежує практичне застосування мінералокераміческого інструменту.
Забезпечуючи високу продуктивність при обробці різних матеріалів різанням, мінералокераміка через специфічність її фізичних і механічних властивостей не може виключити необхідність застосування традиційних твердих сплавів. Вона лише розширює діапазон використовуваних порошкових ріжучих матеріалів у тій області, де може грати роль проміжної ланки між твердими сплавами та алмазомістячими і іншими надтвердими композиційними матеріалами. Ріжуча кераміка — цінне доповнення до твердих сплавів з гарними перспективами подальшого збільшення її застосування.
3 Практична частина
Зміст
Опис ходу експерименту
Однією з основних частин магістерської роботи є практична частина, яка передбачає проведення експерименту. При виконанні практичної частини своєї магістерської роботи мені належить оцінити вплив подачі і глибини різання при швидкісному точінні на шорсткість оброблюваної поверхні.
Для цього заздалегідь виконується планування експерименту, яке припускає визначення наступних початкових даних:
1) Належить провести багатофакторний експеримент;
2) У якості незалежних змінних чинників приймаються швидкість різання (змінюється в діапазоні від 178,4 до 780 м/хв), подача (0,05 — 0,2 мм/об) і глибина різання (0,15 — 0,5 мм);
3) Критерієм оптимізації є шорсткість оброблюваної поверхні заготовки Ra, мкм;
4) В ході експерименту проводиться 15 дослідів за різних поєднаннях режимів різання і кожен дослід виконується тричі з метою отримання результатів високого рівня достовірності.
Експеримент, який я та мій керівник плануємо провести полягає в наступному:
1) На токарному верстаті з ЧПК моделі 16К20Ф3 провести обробку однакових заготовок при різних поєднаннях режимів обробки;
2) Провести статистичну і аналітичну обробку отриманих експериментальних даних;
3) Зробити висновки про те які режими є найбільш раціональними при обробці конструкційних сталей ріжучим інструментом з мінералокерамікою в умовах високошвидкісної обробки різанням.
Анімація
Рис. 5 — Схема високошвидкісної обробки заготовки (анімація об'ємом — 64 кВ, складається з 15 кадрів, 8 повторень)
4 Заключна частина
Зміст
Висновки
За даними різоманітних дослідів можна судити про те, що застосування ріжучого інструменту з використанням мінералокераміки найбільш раціональне для точіння загартованих і важкооброблюваних матеріалів. Проте метою даної роботи є вивчення можливості використання ріжучого інструменту з мінералокерамікою в умовах високошвидкісного точіння для обробки конструкційних сталей, що мають найбільш широке розповсюдження. З цього приводу можна відзначити, що застосовувати ріжучий інструмент з використанням мінералокераміки доцільніше за високих швидкостей різання близько 600 — 800 м/хв, проте малих подачах (0,05 — 0,1 мм/об) і глибинах різання (0,15 — 0,25 мм). Найменш сприятливі умови обробки конструкційних сталей ріжучим інструментом з мінералокерамікою в умовах високошвидкісного точіння за швидкостей до 300 м/хв, подачах понад 0,15 мм/об і величині припуску, що знімається, більше за 0,3 мм. При цьому величина шорсткості оброблюваної поверхні заготівки має достатньо велику величину. Цей результат можна пояснити таким чином.
З фізики процесу різання металів відомо, що ріжучий матеріал повинен мати більшу твердість за оброблювальний. Проте слід зазначити, що якщо така різниця надмірна, це неминуче спричинить зниження якості обробки. У нашому випадку різниця в твердості ріжучого матеріалу, минералокерамики (90 HRA) і матеріалу заготовки, незагартованої сталі 40Х () достатньо істотна, тому можна сказати, що саме це і призвело до отримання низької якості поверхні заготовки в ході проведення експерименту за низьких швидкостях різання. В процесі обробки тверда минералокерамика, не стільки ріже м'якішу та більш в'язку сталь 40Х, скільки, в буквальному розумінні, обдирає поверхневий шар заготовки, вириваючи з нього окремі частинки. Це також посилюється великою подачею і глибиною різання.
При збільшенні швидкості точіння і зменшенні величин подачі і припуску, що знімається, якість поверхні поліпшується, що, у свою чергу, пояснюється зменшенням часу контакту ріжучого інструменту і заготовки.
Окрім цього слід зазначити переваги застосування ріжучого інструменту з використанням мінералокераміки. Як було відмічено раніше, в умовах високошвидкісного точіння тепло в зоні різання розподіляється таким чином, що велика його частина залишається в стружці і надходить до різеця. В цьому відношенні ріжучий інструмент з використанням мінералокераміки має перевагу над твердосплавним, оскільки володіє більшою теплостійкістю (до 1200°С) та зносостійкістю.
Таким чином, можна відзначити, що використання ріжучого інструменту з мінералокерамікою в умовах високошвидкісного точіння для обробки конструкційних сталей має свої переваги, але тільки за певних умов обробки. Проте, при створенні сприятливих умов такого роду застосування ріжучого інструменту з мінералокерамікою для обробки конструкційних сталей в умовах високошвидкісного точіння дозволяє значно підвищити продуктивність при достатньо високих показниках точності і якості оброблюваних поверхонь деталей.
Література
1. Клушин М. И. Скоростное резание металлов. — М.: Государственное научно-техническое издательство машиностроительной литературы, — 1947, 124с.
2. Прейс Г.А. Скоростное резание металлов. — К. — М.: Машгиз, — 1950, 84с.
3. Скоростное резание металлов. — под. ред. Р. Д. Бейзельмана. М.: Государственное научно-техническое издательство машиностроительной и судостроительной литературы, — 1953, 164с.
4. Journal of Manufacturing Science and Engineering, 2005 by ASME. G. Sutter, A. Molinari.
5. Соловов А. Некоторые секреты высокоскоростной обработки металлов [Электронний ресурс] — Режим доступу до статті:
http://www.obo-rt.ru/arhiv/3(3)/21%20Nekotorie%20sekrety.html
6. Мутылина И.Н. Технология конструкционных материалов. Обработка металлов резанием. Виды инструментальных материалов и области их применения. [Электронний ресурс] — Режим доступу до статті:
http://window.edu.ru/window_catalog/pdf2txt?p_id=18616&p_page=15
7. Инструментальные материалы. Минералокерамические материалы. [Электронний ресурс] — Режим доступу до статті:
http://www.info.instrumentmr.ru/instrum_material2.shtml
8. Инструментальные материалы. [Электронний ресурс] — Режим доступу до статті:
http://www.bestreferat.ru/referat-57681.html 9. Твердые сплавы. Минералокерамические твердые сплавы. [Электронний ресурс] — Режим доступу до статті:
http://m-met.ru/?Tverdye_splavy:Mineralokeramicheskie_tverdye_splavy 10. Высокоскоростная обработка. [Электронний ресурс] — Режим доступу до статті:
http://www.delcam-ural.ru/cam/tehpodderjka
11. Теория токарной обработки. Точение с высокими скоростями. [Электронний ресурс] — Режим доступу до статті:
http://tehno-line.ru/files/theory/Turning/3-2-1.htm
|