Реферат по теме выпускной работы
Содержание
1 Вступительная часть
Введение
Актуальность работы
Цель и задачи работы
2 Теоретическая часть
Основные положения теории высокоскоростной обработки резанием
Особенности оборудования и режущего инструмента
Минералокерамический режущий инструмент
3 Практическая часть
Описание хода эксперимента
Анимация
4 Заключительная часть
Выводы
Литература
1 Вступительная часть
Введение
В современных условиях повсеместного стремления к повышению производительности труда и наращивании объёмов производства актуальной становится разработка и внедрение новых и прогрессивных методов обработки. Такие методы должны позволять осуществлять обработку заготовок получаемых по новейшим технологиям, основной тенденцией развития которых является уменьшение припусков на механическую обработку. В технологии машиностроения одним из наиболее крупных и принципиальных достижений в области разработки описанных выше методов на протяжении уже длительного периода времени явилась обработка металлов с весьма высокими скоростями резания, получившая название скоростной обработки резанием.
Резание металлов на больших скоростях (скоростное резание), возникшее в СССР в 50-х годах прошлого столетия, к настоящему времени получило теоретическое обоснование и применяется на металлорежущих станках. Это достигнуто объединенными усилиями ученых, инженеров-производственников (А. В. Кривоухова, А. И. Исаева, П. П. Грудова и др.) и токарей-новаторов (Г. С. Борткевича, П. Б. Быкова, В. М. Бирюкова, В. Н. Трутнева, В. Я. Карасева, В. К. Семинского, Д. И. Рыжкова, В. А. Колесова и многих других).
Возможность скоростного резания металлов стала результатом, как усовершенствования твёрдых сплавов, так и развития новых принципов конструирования и эксплуатации режущих инструментов.
Основными видами скоростного резания металлов являются: скоростное точение и растачивание, фрезерование, зубофрезерование, строгание и сверление.
Отличительной особенностью всех видов высокоскоростной обработки является применение инструментальных материалов отличающихся повышенной прочностью и износостойкостью. Широкое распространение получили такие инструментальные материалы как твердые сплавы и минералокерамика.
Минералокерамические материалы для изготовления режущих инструментов стали применять сравнительно недавно. Наиболее широкое распространение получил минералокерамический материал марки ЦМ332, состоящий в основном из окиси алюминия Al203 с небольшой добавкой окиси магния МgО. Минералокерамика, не содержащая дорогостоящих и дефицитных элементов, имеет следующие основные преимущества: повышенную производительность и качество обработки, стабильность цен и практически неограниченные сырьевые ресурсы исходных материалов.
Основываясь на результатах исследований, можно сделать вывод о том, что скоростное резание позволяет обеспечить повышение производительности лезвийной обработки при высоком качестве обработанной поверхности. Появление новых инструментальных материалов позволяет значительно повысить скорости резания, однако требует проведения дополнительных исследований для изучения закономерностей высокоскоростного резания.
Содержание
Актуальность работы
Высокоскоростное резание за последние годы совершило революционный переворот в методах механообработки. Решающий фактор в оценке процесса высокоскоростной обработки металлов резанием — производительность станков, которые определяют стоимость производства и, таким образом, амортизацию инвестиций. Технология высокоскоростной обработки резанием относится к числу наиболее прогрессивных и быстро развивающихся. Однако, несмотря на более чем полувековую историю своего развития, эта технология не везде получила широкое применение. Этот вид обработки резанием является относительно новым технологическим процессом, и опыт его применения в нашей стране весьма ограничен. В большинстве случаев это связано с несовершенством технической базы отечественного производства, а также со специфическими требованиями, предъявляемыми к станкам, системам с ЧПУ, режущему инструменту, вспомогательному инструменту с системой закрепления инструмента, средствам технического оснащения, системам программирования, квалификации технолога программиста и оператора станка с ЧПУ. Пренебрежение одним из этих составляющих может свести к нулю все предыдущие усилия.
Кроме этого следует отметить, что скоростная обработка резанием преимущественно применяется для точения закалённых и труднообрабатываемых материалов. В то же время одной из тенденций развития современного машиностроения является разработка и применение прогрессивных инструментов на основе высококачественных инструментальных материалов, в частности, минералокерамики. В связи с этим возникает вопрос о рациональном использовании таких инструментальных материалов при обработке конструкционных сталей, имеющих наиболее широкое распространение.
Цель и задачи работы
Цель работы — анализ возможности использования режущего инструмента с минералокерамикой для обработки конструкционных сталей в условиях высокоскоростного точения.
Основная задача работы: определение наиболее рациональных режимов обработки конструкционных сталей режущим инструментом с минералокерамикой в условиях высокоскоростного точения.
2 Теоретическая часть
Содержание
Основные положения теории высокоскоростной обработки резанием
Характерной особенностью высокоскоростной обработки металлов резанием является снижение сил резания в некотором диапазоне скоростей. Однако наиболее важным фактором является перераспределение тепла в зоне резания. При небольших сечениях среза, в данном диапазоне скоростей основная масса тепла концентрируется в стружке, не успевая переходить в заготовку. Именно это позволяет вести обработку закаленных сталей не опасаясь отпуска поверхностного слоя. Отсюда основной принцип ВСО — малое сечение среза, снимаемое с высокой скоростью резания, и соответственно высокие обороты шпинделя и высокая минутная подача.
Сущность этого способа обработки металлов заключается в том, что с повышением скорости резания уменьшается степень деформации металла в процессе стружкообразования, что подтверждается, в частности, уменьшением усадки стружки и силы резания при скоростном точении. Уменьшение деформации в отдельных частицах стружки обусловливает уменьшение количества теплоты, образующейся в процессе резания в каждой частице. Кроме того, каждая частица стружки при высокой скорости резания соприкасается с передней поверхностью резца в течение меньшего времени, чем при сравнительно низкой скорости. Благодаря этому при скоростном точении из каждой отдельной частицы стружки в резец поступает меньше теплоты, чем при низкой скорости резания.
При увеличении скорости обработки уменьшается и количество теплоты, переходящей из стружки в обрабатываемую деталь. Опытами многих исследователей, занимавшихся этим предметом (А. В. Кривоухов, В. К. Семинский, В. А. Колесов и другие), хорошо подтверждается, что при высоких скоростях резания обработанная поверхность нагревается лишь незначительно.
Таким образом, в условиях высокоскоростного точения распределение образовавшейся теплоты благоприятнее, чем при умеренных скоростях; в стружке, получившейся при высокой скорости резания, остается теплоты больше, чем при низкой скорости.
Основные закономерности, характерные для процесса высокоскоростной обработки резанием представлены на рисунке 1.
Рисунок 1 — Взаимосвязь скорости резания с выходными параметрами процесса ВСО (Р — сила резания; t — температура в зоне резания)
Несмотря на положительное значение повышения скорости обработки, условия работы режущей кромки резца при скоростном точении тяжелее, чем при менее высоких скоростях. Хотя количество теплоты, поступающей в резец из каждой частицы стружки, при скоростном резании меньше, чем при умеренных скоростях резания, общее количество теплоты, которое поступит в резец за одно и то же время его работы, будет больше при высокой скорости обработки, чем при низкой. Это объясняется тем, что в первом случае резец получит теплоту из большего количества частиц стружки, чем за такое же время при невысокой скорости.
В результате при скоростном резании резец нагревается значительно больше, чем при работе с умеренной скоростью резания. Поэтому развитие скоростного резания обусловило необходимость дальнейшего повышения прочности и стойкости твердосплавных резцов.
Одним из мероприятий, направленных к достижению этой цели, явилось улучшение качества твердых сплавов. Другое направление — создание новых высококачественных инструментальных материалов, известным представителем которых является минералокерамика.
Содержание
Особенности оборудования и режущего инструмента
Развитие скоростного резания предъявило новые требования к станкостроению и абразивной промышленности.
Современные станки должны характеризоваться:
— достаточной мощностью, жесткостью и виброустойчивостью;
— широким диапазоном скоростей шпинделя, предпочтительно с электронным управлением, допускающим плавное регулирование;
— более широким применением гидравлических и электрических приборов;
— хорошо смазывающимися и хорошо сбалансированными шпинделями;
— наличием конвейерной уборки стружки;
— надёжным обильным охлаждением режущих инструментов;
— эффективными способами подачи изделия к станку и от станка;
— пневмоприспособлениями для зажима.
Основное требование к абразивной промышленности — производство широкой номенклатуры алмазных кругов, крайне необходимых для качественной заточки современных твёрдых сплавов.
Кроме этого развитие скоростного резания обусловило необходимость дальнейшего повышения прочности и стойкости режущего инструмента, в частности минералокерамического, твёрдосплавного, с применением сверхтвёрдых материалов.
Одним из мероприятий, направленных на достижение этой цели, явилось улучшение качества инструментальных материалов. Другой способ повышения прочности и стойкости твердосплавных резцов — применение отрицательного переднего угла резца. Режущая способность твердосплавных резцов с положительным углом ограничивается склонностью твердосплавных пластинок к выкрашиванию. Это особенно заметно при обтачивании очень твердых или закаленных сталей и при работе с ударной нагрузкой (прерывистое точение, точение с неравномерным припуском и т. д.).
Рисунок 2 — Давление стружки на резец при отрицательном (а) и положительном (б) переднем углах
При отрицательном переднем угле выкрашивания пластинки, как правило, не происходит, что объясняется следующими факторами:
1) при точении резцами с отрицательным передним углом (- ) направление действующей силы Р обусловливает сжатие (рис. 2, а) и обеспечивает более благоприятные условия работы пластинки твердого сплава в сравнении с условиями работы резца с положительным (+ ) передним углом (рис. 2, б);
2) при отрицательном переднем угле и положительном угле наклона режущей кромки вершина резца предохранена от ударов при обтачивании прерывистых поверхностей.
Все сказанное выше относится главным образом к обработке стали. Резание чугуна и цветных металлов требует значительно меньших затрат; преимущества отрицательных углов в данном случае сказываются слабее. Вследствие этого при обработке указанных материалов резцы с отрицательными передними углами применяются реже.
Наряду с достоинствами резцы с отрицательным передним углом имеют ряд существенных недостатков.
1) При точении резцами с отрицательным передним углом возрастает сила трения стружки о резец, вследствие чего увеличивается и потребная мощность. Поэтому при работе на недостаточно мощных станках приходится уменьшать скорость резания или подачу, а вместе с тем и производительность.
2) При работе рассматриваемыми резцами возрастает радиальная сила Ру, что приводит к искажению формы обрабатываемой детали (при ее недостаточной жесткости), вибрациям и т. д.. Ввиду этого резцы с отрицательным передним углом применяются лишь для обработки стали с повышенной и высокой прочностью (бв = 800 МПа и больше), при резании с ударной нагрузкой и при обработке заготовок с очень твердым поверхностным слоем. В последнее время стремятся и в таких случаях пользоваться резцами с положительным передним углом.
Наблюдение за внешним видом стальной стружки, снимаемой резцами с положительными и отрицательными передними углами (+ 20°; + 10°; 0°; - 20°) показывает, что во всех случаях увеличение скорости резания приводит к увеличению радиуса завитков стружки. При снимаемом сечении стружки t х s= 3,0 х 0,1 мм2 и работе резцами с положительными передними углами на небольших скоростях резания (порядка 20 м/мин) стружка имеет вид туго закрученных архимедовых спиралей. По мере же увеличения скорости резания она приобретает форму сплошной спиральной ленты, диаметр завитка которой вырастает от 15 до 20 мм. при скоростях порядка 100 м/мин и до 50 см при скоростях 300 м/мин. Одновременно с этим происходит и изменение цвета стружки от светлого (стального) до синего. При работе резцами с отрицательными передними углами на небольших скоростях резания (порядка 20 м/мин) стружка сходит завитками, длиной не более одного завитка; при больших скоростях резания стружка имеет форму сплошной спиральной ленты, радиус завитков, которой растет значительно быстрее, чем для резцов с положительными передними углами. Так, при отрицательном переднем угле = - 10° на скоростях резания более 200 м/мин стружка сходит в виде прямой (неспиральной) ленты. При угле = - 20° и скорости резании V = 60 м/мин стружка ломается на отрезке в 2 — 4 завитка, и уже при скорости резания более 75 м/мин она сходит в виде прямой (неспиральной) ленты.
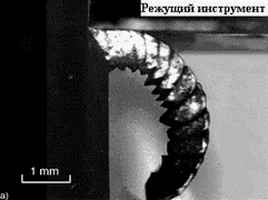 |
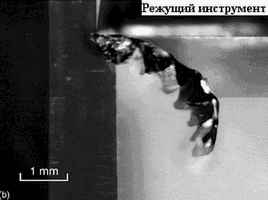 |
|
|
Рисунок 3 — Формирование стружки при скорости резания V = 15 м/сек |
Рисунок 4 — Формирование стружки при скорости резания V = 45 м/сек |
Цвет стружки изменяется так же, как и при положительных передних углах.
На стружках, снятых резцом с отрицательным передним углом = - 20° заметны весьма сильные сдвиги отдельных элементов (наружная поверхность стружки пилообразна) даже при подаче s = 0,l мм/об. При больших скоростях резания эти сдвиги становятся менее заметными и при скоростях, превышающих 200 м/мин, стружки, снятые резцом = - 20° почти не отличаются по виду от стружек, снятых резцом с положительным передним углом. При подачах (толщинах стружки) больших, чем 0,1 — 0,3 мм/об, и невысоких скоростях резания (V = 40 — 50 м/мин) стружка, снимаемая инструментами с отрицательными передними углами, разделена на отдельные элементы, т. е. представляет типичную стружку скалывания.
Можно сделать вывод, что усадка стружки в пределах скоростей резания до 40 м/мин, в особенности при работе с отрицательными передними углами, имеет несомненную тенденцию к увеличению. При увеличении же скорости резания выше 40 м/мин происходит уменьшение усадки стружки, причем особенно интенсивно при работе с отрицательными передними углами.
Большой интерес представляет изучение влияния скорости резания на изменение тангенциальных усилий при работе резцами с положительными и отрицательными углами. Американские ученые, производившие измерение тангенциальных усилий при резании сталей резцами с положительными и отрицательными передними углами в широком диапазоне изменения скоростей резания (от 30 до 350 м/мин), установили, что при больших скоростях резания тангенциальное усилие с увеличением скорости резания возрастает в случае положительных передних углов и, наоборот, уменьшается в случае отрицательных передних углов.
По данным этих исследований величина тангенциального усилия для обоих случаев будет одинаковой, и далее, по мере увеличения скорости резания, усилие резания при отрицательных передних углах будет меньше, чем при положительных.
Опыты проводились по стали 50 и чугуну Нв = 143 в условиях свободного резания резцами с углами = + 20°; + 10°; 0°, - 10° и - 20° при заднем угле 3°, при подаче s = 0,1 мм; резцами с углами = + 10° и - 10° и задним углом 3°, при подачах 0,2 мм; резцами с углами = + 10° и - 10° и задним углом 8° при подаче 0,05 мм.
Результаты опытов позволяют сделать следующие выводы.
А. При резании сталей:
1) увеличение скорости резания при работе резцами с положительными передними углами вызывает увеличение тангенциального усилия резания;
2) при резании резцами с нулевым передним углом скорость резания в диапазоне от 50 до 350 м/мин на величину тангенциального усилия резания не влияет;
3) увеличение скорости резания в диапазоне 50 — 400 м/мин при работе резцами с отрицательными передними углами вызывает уменьшение тангенциального усилия резания;
4) значение скорости резания, при которой усилия резания становятся одинаковыми для резцов с отрицательными и положительными передними углами, при обработке стали 50 достигает приблизительно 400 м/мин.
5) в диапазоне скоростей резания от 10 до 40 — 50 м/мин при работе инструментами с нулевым и отрицательным передним углом наблюдается большой разброс экспериментальных данных при общей тенденции к росту усилий с увеличением скорости резания, т. е. имеют место явления, повторяющие изменение усадки стружки в этом диапазоне.
Естественным объяснением такого явления представляется влияние на процесс резания нароста, образование которого в указанном диапазоне скоростей резания протекает наиболее интенсивно.
Б. По чугуну:
1) при работе резцами как с отрицательными, так и с положительными передними углами тангенциальные усилия резания по мере увеличения скорости резания сначала падают, а затем остаются неизменными;
2) при невысоких скоростях резания усилия резания для резцов с отрицательными передними углами больше, чем для резцов с положительными передними углами;
3) при достаточно высоких скоростях резания (более 100 м/мин) усилия резания при работе инструментами с отрицательным передним углом ( = - 10°) оказываются меньшими, чем при работе с положительным передним углом ( = + 10°).
Содержание
Минералокерамический режущий инструмент
Промышленное производство режущей оксидной керамики из Al203 началось более 45 лет тому назад, а в 50-е годы прошлого века были созданы сплав ЦМ332 (Al203 и до 1 % оксидов других металлов) в нашей стране, керамический материал «кермет» (2 — 10 % Мо или Сг, остальное Al203) и оксидно-карбидная керамика (20 — 40 % простых или сложных карбидов переходных металлов IV — VI групп Периодической системы Д.И.Менделеева - титана, молибдена, вольфрама и др., остальное Al203) за рубежом. К середине 70-х годов доля режущей керамики в металлообработке в целом составила 2 % (в ФРГ 6 %, в США 5 %), причем на нее приходилось 4 % объема стружки, снимаемой инструментальными материалами.
Исходным материалом для производства практически всех выпускаемых в разных странах марок режущей минералокерамики служит технический глинозем (V — Al203) чистотой 98,5 — 99,5% (основные примеси — оксиды кремния, железа, кальция, натрия и калия от сотых до десятых долей процента каждого), полученный обработкой боксита с применением соды или кислоты. Такой глинозем обжигают при 1400 — 1600°С, превращая его из v-модификации в а-модификацию (корунд). Обожженный глинозем размалывают до зернистости 1 — 3 мкм (например, в шаровой мельнице); измельчение до крупности частиц меньше 1 мкм нежелательно из-за возможного увеличения хрупкости готового изделия. Размолотый корунд подвергают обработке кислотами для отмывки железа, натертого в процессе размола, промывают водой и высушивают. После этого подготовленный порошок формуют, прессуют, а затем спекают при температуре 1750 — 1900°С. Пластинки можно получить также литьем под давлением.
Высокая твердость минералокерамики, теплостойкость до 1200°C, химическая инертность к металлу, сопротивление окислению во многом превосходят эти же параметры твердых сплавов. Однако минералокерамика уступает этим сплавам по теплопроводности, имеет более низкий предел прочности на изгиб. Твердость минералокерамики составляет 90 HRA, значения
при изгибе 295 МПа (значения
при изгибе твердых сплавов до 1700 МПа).
Минералокерамику на основе Al203 можно разделить на три группы:
— чисто оксидная («белая») керамика, основу которой составляет Al203 (до 99,7 %) с незначительными добавками MgO, ZnO2 и др.;
— смешанная керамика, представляющая собой Al203 с добавлением тугоплавких металлов (Ti, Nb и др.);
— оксидная («черная») керамика — Al203 с добавлением карбидов тугоплавких металлов (Ti, W, Mo) для повышения ее прочностных свойств и твердости.
Пластины из «белой» керамики получают холодным прессованием с последующим спеканием. Процесс экономичен, стоимость таких пластин минимальна. Основной недостаток этих пластин относительно небольшая прочность, но твердость (91 HRA — Россия, 93 — Япония, США) и красностойкость их велики. Представители этой керамики, например, ЦМ332 (Al203 + 1 % MgO) и ВО (более 99 % Al203) — Россия и зарубежные: СХЗ (Япония), V34 — США.
«Белая» керамика применяется для чистовой и получистовой обработки не обработанных термически сталей, серых чугунов.
Пластины из «смешанной» и «черной» керамики получают горячим прессованием, процесс более трудоемок. Отечественная керамика — ВОК (Al203
60 %, TiC 40 % и др.), К090 (Al203 + TiC) — США и др.
«Черная» керамика применяется для чистовой, получистовой обработки ковких, высокопрочных и отбеленных чугунов, закаленных сталей, для обработки цветных металлов на основе меди; нитридная керамика — для получистовой обработки чугунов.
Наряду с материалами на основе оксида алюминия выпускается материал на основе нитрида кремния Si3N4 — силинит (метод получения — горячее прессование) и кортинит ОНТ с добавками Al203+TiC. Значения твердости для силинита — 94 НRA, а
при изгибе — 500 МПа. Новым инструментальным материалом, созданным на основе нитрида кремния, является силинит-Р. Он используется при чистовом точении сталей, чугуна, алюминиевых сплавов.
Минералокерамические материалы изготовляются в виде неперетачиваемых пластин, что существенно облегчает условия их эксплуатации. Эти пластинки присоединяются к корпусам инструментов механическим путем, приклеиванием или припаиванием.
Расширение потребления режущих керамических материалов связано с нарастающим дефицитом вольфрама, стимулирующим производство безвольфрамовых инструментальных материалов созданием новых эффективных марок режущей керамики и развитием применения инструмента с механическим креплением МНП, увеличением в металлообработке доли финишных и чистовых операций при одновременном повышении твердости поверхности обрабатываемы деталей.
В настоящее время минералокерамику применяют для получистовой и чистовой непрерывной обточки, а также расточки деталей из серых, ковких, высокопрочных, отбеленных чугунов, закаленных и улучшенных сталей, некоторых марок цветных металлов и сплавов, а также неметаллических материалов (графита и др.) при высоких скоростях резания (до 600 — 800 м/мин) без применения смазочно-охлаждающей жидкости (СОЖ), для волочения при производстве проволоки из цветных металлов и для изготовления износостойких деталей машин, подвергающихся интенсивному безударному абразивному износу (сопел, насадок и т.п.).
Минералокерамические инструменты целесообразно применять только на станках повышенной жесткости, характеризующихся безвибрационной работой.
С целью улучшения свойств минералокерамики проводятся работы по созданию керметов, состоящих из минералокерамики и металлических добавок в виде карбидов вольфрама, молибдена и др.
Существенным недостатком минералокерамики является ее крайне низкое сопротивление циклическому изменению температуры. Вследствие этого даже при небольшом числе перерывов в работе на контактных поверхностях инструмента появляются микротрещины, которые приводят к его разрушению даже при небольших усилиях резания. Это обстоятельство ограничивает практическое применение минералокерамического инструмента.
Обеспечивая высокую производительность при обработке различных материалов резанием, минералокерамика в силу специфичности ее физических и механических свойств не может исключить необходимость применения традиционных твердых сплавов. Она лишь расширяет диапазон используемых порошковых режущих материалов в той области, где может играть роль промежуточного звена между твердыми сплавами и алмазосодержащими и другими сверхтвердыми композиционными материалами. Режущая керамика — ценное дополнение к твердым сплавам с хорошими перспективами дальнейшего увеличения ее потребления.
3 Практическая часть
Содержание
Описание хода эксперимента
Одной из основополагающих частей магистерской работы является практическая часть, которая предполагает проведение эксперимента. При выполнении практической части своей магистерской работы мне предстоит оценить влияние подачи и глубины резания при скоростном точении на шероховатость обрабатываемой поверхности.
Для этого предварительно выполняется планирование эксперимента, которое предполагает определение следующих исходных данных:
1) Предстоит провести 3-х факторный эксперимент;
2) В качестве независимых переменных факторов принимаются скорость резания (изменяется в диапазоне от 178,4 до 780 м/мин), подача (0,05 — 0,2 мм/об) и глубина резания (0,15 — 0,5 мм);
3) Критерием оптимизации является шероховатость обрабатываемой поверхности заготовки Ra, мкм;
4) В ходе эксперимента проводится 15 опытов при различных сочетаниях режимов резания и каждый опыт выполняется трижды с целью получения результатов высокого уровня достоверности.
Эксперимент, который я и мой руководитель планируем провести заключается в следующем:
1) На токарном станке с ЧПУ модели 16К20Ф3 провести обработку одинаковых заготовок при различных сочетаниях режимов обработки;
2) Провести статистическую и аналитическую обработку полученных экспериментальных данных;
3) Сделать выводы о том какие режимы являются наиболее рациональными при обработке конструкционных сталей режущим инструментом с минералокерамикой в условиях высокоскоростной обработки резанием.
Анимация
Рисунок 4 — Схема высокоскоростной обработки заготовки (анимация объемом — 64 кВ, состоит из 15 кадров, 8 повторений)
4 Заключительная часть
Содержание
Выводы
По данным различных исследований можно судить о том, что применение режущего инструмента с использованием минералокерамики наиболее рационально для точения закалённых и труднообрабатываемых материалов. Однако целью настоящей работы является изучение возможности использования режущего инструмента с минералокерамикой в условиях высокоскоростного точения для обработки конструкционных сталей, имеющих наиболее широкое распространение. И по этому поводу можно отметить, что применять режущий инструмент с использованием минералокерамики наиболее целесообразно при высоких скоростях резания порядка 600 — 800 м/мин, однако малых подачах (0,05 — 0,1 мм/об) и глубинах резания (0,15 — 0,25 мм). Наименее благоприятные условия обработки конструкционных сталей режущим инструментом с минералокерамикой в условиях высокоскоростного точения при скоростях до 300 м/мин, подачах свыше 0,15 мм/об и величине снимаемого припуска более 0,3 мм. При этом величина шероховатости обрабатываемой поверхности заготовки имеет достаточно большую величину. Такой результат можно объяснить следующим образом.
Из физики процесса резания металлов известно, что режущий материал должен обладать большей твердостью, чем обрабатываемый. Однако следует отметить, что если такая разница чрезмерна, то это неизбежно повлечёт за собой снижение качества обработки. В нашем случае разница в твёрдости режущего материала, минералокерамики (90 HRA) и материала заготовки, незакалённой стали 40Х () достаточно существенна, поэтому можно сказать, что именно это и привело к получению низкого качества поверхности заготовки в ходе проведения эксперимента при низких скоростях резания. В процессе обработки твёрдая минералокерамика, не столько режет более мягкую и вязкую сталь 40Х, сколько, в буквальном смысле, обдирает поверхностный слой заготовки, вырывая из него отдельные частицы. Это также усугубляется большими подачей и глубиной резания.
При увеличении скорости точения и уменьшении величины подачи и снимаемого припуска качество поверхности повышается, что, в свою очередь, объясняется уменьшением времени контакта режущего инструмента и заготовки.
Помимо этого следует отметить преимущества применения режущего инструмента с использованием минералокерамики. Как было отмечено ранее, в условиях высокоскоростного точения тепло в зоне резания распределяется таким образом, что большая его часть остаётся в стружке и поступает в резец. В этом отношении режущий инструмент с использованием минералокерамики лучше твёрдосплавного, так как обладает большей теплостойкостью (до 1200°С) и износостойкостью.
Таким образом, в заключение можно отметить, что использование режущего инструмента с минералокерамикой в условиях высокоскоростного точения для обработки конструкционных сталей имеет свои преимущества, однако только при определённых условиях обработки. Тем не менее, при создании такого рода благоприятных условий применение режущего инструмента с минералокерамикой для обработки конструкционных сталей в условиях высокоскоростного точения позволяет значительно повысить производительность при достаточно высоких показателях точности и качества обрабатываемых поверхностей деталей.
Литература
1. Клушин М. И. Скоростное резание металлов. — М.: Государственное научно-техническое издательство машиностроительной литературы, — 1947, 124с.
2. Прейс Г.А. Скоростное резание металлов. — К. — М.: Машгиз, — 1950, 84с.
3. Скоростное резание металлов. — под. ред. Р. Д. Бейзельмана. М.: Государственное научно-техническое издательство машиностроительной и судостроительной литературы, — 1953, 164с.
4. Journal of Manufacturing Science and Engineering, 2005 by ASME. G. Sutter, A. Molinari.
5. Соловов А. Некоторые секреты высокоскоростной обработки металлов [Электронный ресурс] — Режим доступа к статье:
http://www.obo-rt.ru/arhiv/3(3)/21%20Nekotorie%20sekrety.html
6. Мутылина И.Н. Технология конструкционных материалов. Обработка металлов резанием. Виды инструментальных материалов и области их применения. [Электронный ресурс] — Режим доступа к статье:
http://window.edu.ru/window_catalog/pdf2txt?p_id=18616&p_page=15
7. Инструментальные материалы. Минералокерамические материалы. [Электронный ресурс] — Режим доступа к статье:
http://www.info.instrumentmr.ru/instrum_material2.shtml
8. Инструментальные материалы. [Электронный ресурс] — Режим доступа к статье:
http://www.bestreferat.ru/referat-57681.html 9. Твердые сплавы. Минералокерамические твердые сплавы. [Электронный ресурс] — Режим доступа к статье:
http://m-met.ru/?Tverdye_splavy:Mineralokeramicheskie_tverdye_splavy 10. Высокоскоростная обработка. [Электронный ресурс] — Режим доступа к статье:
http://www.delcam-ural.ru/cam/tehpodderjka
11. Теория токарной обработки. Точение с высокими скоростями. [Электронный ресурс] — Режим доступа к статье:
http://tehno-line.ru/files/theory/Turning/3-2-1.htm
|