Автореферат
квалификационной работы магистра
«Исследование и
разработка автоматической системы
регулирования нагрузки и скорости подачи добычного комбайна с
частотно-регулируемым приводом»
Содержание
Введение
1. Актуальность
темы
2.
Связь
работы с научными программами, планами,
темами
3. Цель и задачи разработки
(исследования)
3.1. Цель
работы
3.2. Идея
работы
3.3. Основные
задачи разработки (исследования)
3.4. Предмет
разработки (исследования)
3.5. Объект
разработки (исследования)
3.6. Методология
и методы исследований
4. Предлагаемая
научная новизна полученных результатов
5. Практическое
значение полученных результатов
6. Апробация результатов работы
7. Обзор разработок и
исследований по теме
7.1.
На
локальном уровне
7.2. На
национальном уровне
7.3. На
глобальном уровне
8. Описание
полученных и планируемых результатов работы
Выводы
Список
использованной литературы
Примечание
Введение
Выемочные
машины являются главным средствам для добычи полезного ископаемого, что
требует
значительного внимания в отношении их автоматизации и постоянному
улучшению их
качественных характеристик.
Очистной комбайн
– комбинированная
горная машина, одновременно выполняющая операции по разрушению угля и
его
погрузке на конвейер [1].
Необходимость оснащения
комбайнов средствами автоматизации
оговорена различными нормативными документами. Такими средствами и
системами
являются: аппаратура дистанционного управления двигателями комбайна и
конвейера, а так же фидерным автоматом; аппаратура предупредительной
сигнализации
перед пуском комбайна, началом движения машины, предохранительные
лебедки,
аппаратура громкоговорящей связи рабочих в лаве между собой и с
персоналом на
штреке, автоматический регулятор нагрузки, обеспечивающий поддержание
требуемого режима работы, система дистанционного управления положением
режущих
органов, аппарат защиты электродвигателей при опрокидывании и
несостоявшемся
пуске, исключающий длительное нахождение привода в заторможенном
состоянии,
аппаратура автоматического управления крепью [2].
Актуальность
темы
Эффективность работы шахты напрямую зависит
от эффективного использования добывающего оборудования.
Работа с более малыми по
мощности пластами на
больших горизонтах, а также необходимостью более точного определения
местоположения, предполагает увеличение скорости срабатывания различных
элементов автоматики и повышения надежной защиты, для обеспечения
безопасной
работы обслуживающего персонала и предохранения оборудования от
различных
негативных факторов рабочего процесса. В связи с этим проблемам
автоматики и
автоматизации уделяется значительное внимание.
Одной из актуальных задач в
области автоматизации добычных
комбайнов являтся задача усовершенствование средств регулирования
нагрузки на
привод. Существующие системы рассчитаны на работу с объемным
гидроприводом, не
могут быть использованы для работы с современными комбайнами с
частотно-регулируемым приводом подачи, поэтому задача исследования и
разработки
автоматической системы регулирования нагрузки и скорости подачи
добычного
комбайна с частотно-регулируемым приводом актуальна на сегодняшний день.
Связь
работы с научными программами, планами, темами
Квалификационная работа магистра выполнена на
протяжении 2009-2010 г.г. согласно с научным направлением кафедры
«Горная электротехника
и автоматика имени Р.М. Лейбова» Донецкого национального
технического
университета.
Цель
и задачи разработки (исследования)
Цель работы
–
повышение эффективности работы технологического процесса добычи угля,
путем
разработки системы автоматизации включающей устройство регулирования
нагрузки.
Идея работы
состоит в создании и исследовании
регулятора нагрузки добычного комбайна с частотно управляемым приводом
подачи
на основе микропроцессорной техники и современной элементной базе.
Основные задачи
разработки (исследования): Поскольку
основной задачей горнодобывающей промышленности является увеличение
объемов
добычи угля, и уменьшение опасности связанной с его добычей
применяются
автоматизированные способы управления комбайном, с целью удаления
человека на
безопасное расстояние от места ведения работы.
В квалификационной работе магистра будут раскрыты
следующие задачи:
· моделирование
работы очистного комбайна;
· моделирование системы
регулирования
нагрузки электропривода добычного комбайна;
· повышения эффективности, надежности,
уменьшение затрат на обслуживание и замену основных составляющих частей
оборудования технологического процесса добычи угля.
Предметом разработки (исследования) является непосредственно регулятор нагрузки
добычного комбайна с частотно-регулируемым приводом подачи.
Объектом автоматизации является
технологический процесс добычи угля.
Методология
и методы исследований
Трудоемкость разработки, а часто и корректность
результатов моделирования во многом определяются выбранной методикой
исследований. Прежде всего, касается выбора метода структурной
идентификации
исследуемого объекта. Известны три основных подхода к разработке
математической
модели:
а) формирование уравнений модели на
основе применения
физических законов, описывающих поведение или состояние объекта. Метод
требует
детального знакомства с физической сущностью явления.
б) получение математического описания
объекта на основе
использования теории линейных графов. Позволяет существенно упростить
процесс
идентификации за счет формализованного представления компонентов
системы в виде
двухполюсников, а структуры объекта (системы)-в виде так называемого
графа.
Метод позволяет существенно адаптировать модель для ее реализации
средствами
вычислительной техники.
в) структурная идентификация объекта на основе
систематического
применения вариационных принципов так же, как и предыдущий метод
позволяет в
некоторой степени формализовать процесс составления модели. Применение
данного
подхода требует знания исследователем основ вариационного исчисления и,
в
частности, главных вариационных принципов (принцип Лагранжа, принцип
Ферма и
т.п.), а также области их применения.
В данном случае, проанализировав выше изложенные методы структурной
идентификации, для моделирования нагрузки режущего органа комбайна при
переменной сопротивляемости угля резанию выбираем первый метод,
основанный на
применении физических законов, описывающих поведение объекта, а также
статистических
закономерностей описывающих стохастические процессы так как остальные
методы не
применимы.
Предлагаемая
научная новизна полученных результатов
Для выработки надежного режима работы необходимы
многочисленные экспериментальные исследования на действующих добычных
комбайнах. Однако, экспериментальное исследование нагрузки на приводе
добычного
комбайна весьма затруднительно. В таких условиях применяется
математическое
моделирование, требующее выполнения двух непременных условий: наличия
возможности построения точной математической модели процесса в
обязательной
строгой адаптации модели на действующем комбайне. Моделирование системы
автоматического управления нагрузкой на электродвигатель добычного
комбайна
является составной частью общей задачи построения системы управления
добычным
комбайном. Применение модели добычного комбайна, а также математической
модели
регулирования нагрузки позволит значительно сократить объем
экспериментальных
работ, проводимых непосредственно на объекте, но, в конечном итоге не
исключает
и не заменяет их.
Практическое
значение полученных результатов
Данная работа позволит использовать данные
полученные в результате математического анализа. В свою
оченредь эти
результаты представляют большую значимость при разработки действующей
модели
регулятора нагрузки добычного комбайна.
Апробация
результатов работы
Результаты
работы докладывались на конференциях и опубликованы в соответствующих
сборниках:
· X
Международная научно-техническая конференция
аспирантов и студентов. Автоматизация технологических объектов и
процессов.
Поиск молодых. (19.05.2010);
· XI международная молодежная
научная конференция «Севергеоэкотек – 2010»;
Обзор
разработок и исследований по теме
На
локальном уровне
Подобные разработки и исследования велись
студентами ДонНТУ:
- Астапов А.С.
«Автоматизация процесса регулирования скорости подачи
очистного комбайна»
- Савицкий А.В.
«Создание тиристорного частотного преобразователя
на IGBT-модулях вынесенной подачи угольного
очистного комбайна»
- Мезников Д.А.
«Частотно-регулируемый электропривод подачи очистного
комбайна»
- Алексеев
Р.В. «Исследование тепловых процессов в асинхронном
двигателе при питании от тиристорного преобразователя частоты»
На
национальном уровне
В 2002 г. в ОАО «Автоматгормаш
им. В. А.
Антипова» разработан комплекс технических средств
КС500Ч.УХЛ5, предназначенный
для управления комбайнами 1КДК500, 2КДК500, КДК700, КДК400 с частотным
приводом
подачи, находящимся на очистном комбайне производства ЗАО
«Горловский
машиностроитель». В системе подачи применен преобразователь
частоты ПЧЭ-120М
производства ОАО «ЭЛМИС» (г. Киев), расположенный
непосредственно на комбайне.
Комплекс КС500Ч позволяет осуществлять управление комбайном в условиях
подземных выработок шахт, опасных по газу или пыли, в том числе при
выемке угля
на выбросоопасных или угрожающих по выбросам пластах.
В настоящее время комплекс изготавливается в
шести модификациях
совместно с аппаратурой УМК: КС500Ч.02.УХЛ5 – для управления комбайнами
1КДК500, 2КДК500; КС500Ч.04.УХЛ5 – для КДК700; КС500Ч.05.УХЛ5 – для
КДК400;
КС500Ч.06.УХЛ5 – для 1КДК500 и 2КДК500 (с аппаратурой
КДУ);КС500Ч.07.УХЛ5 – для
1КДК500, 2КДК500 (без дистанционного управления);
КС500Ч.08.УХЛ5 – для
КДК400
(без дистанционного управления).
Комплексы КС500Ч.07,
КС500Ч.08 обеспечивают управление
в «местном» режиме с пультов,
расположенных на комбайне, а комплексы
КС500Ч.02, КС500Ч.04, КС500Ч.05, КС500Ч.06 – в таких
режимах: «местном» –
с пультов управления на очистном
комбайне; «Радио» – дистанционно в зоне
видимости комбайна с носимого пульта радиоуправления по беспроводному
каналу
связи; «Штрек» – дистанционно вне зоны
видимости с пульта штрекового в
соответствии с требованиями безопасности для работы на выбросоопасных и
угрожающих пластах.
Комплекс КС500Ч выполняет следующие функции:
- включение и отключение комбайна
и конвейера совместно с установленной на штреке аппаратурой
УМК или
КДУ (в
зависимости от исполнения);
-
блокирование
несанкционированного включения комбайна;
-
управление с
преобразователем частоты в системе подачи;
-
управление
исполнительными механизмами комбайна;
-
диагностирование и
защита основных узлов комбайна;
- управление комбайном в местном
режиме или в одном из трех
(«Местное», «Радио», «Штрек»)
в
зависимости от модификации;
-
аварийное отключение
механизмов, работающих в забое;
-
отображение
технологической и диагностической информации.
Состав комплекса КС500Ч: пульты управления
центральный (встраивается в электроблок комбайна РВ 3В Иа), левый,
правый (РО
Иа IР54) и радиоуправления (РО Иа IР54); коробка клеммная (РО Иа IР54);
датчики
температуры и расхода воды, температуры масла, положения комбайна в
лаве (РО Иа
IР54); датчики тока двигателей, наличия воды (встраиваются в
электроблок
комбайна РВ ЗВ Иа); трансформаторы (встраиваются в электроблок комбайна
РВ ЗВ
Иа); блок питания 36/25И (в электроблок комбайна РВ ЗВ Иа); пульт
управления
штрековый (РО Иа IР54); источник питания трехканальный 127/12И (РВ ЗВ
Иа).
Функционально комплекс КС500Ч
представляет собой локальную
сеть, которая состоит из модулей серии 1-7000 и tCON с присоединенными
к ним
органами управления, датчиками и исполнительными устройствами; блока
индикации
пульта управления центрального; контроллера VisiGRAF пульта управления
штрекового. Связь по сети осуществляется с помощью стандартного
интерфейса
RS-485. Отдельный его канал используется для связи с преобразователем
частоты.
Каждый модуль имеет свой строго определенный адрес, который назначается
программным путем. Центральным модулем комплекса является контроллер
1-7188,
расположенный в пульте управления центральном. Работа комплекса
осуществляется
в соответствии с программой, записанной в памяти контроллера I-7188.
При возникновении аварийных
ситуаций: перегрев
электродвигателей; перегрузка; превышение допустимой концентрации
метана в
забое; отсутствие воды в системе охлаждения двигателей; перегрев масла
в
редукторах режущих органов; нарушение изоляции силовых кабелей,
преобразователя
частоты и двигателей подачи; исчезновение радиоканала при
радиоуправлении,
происходит отключение комбайна.
Остановка комбайна (скорость
подачи сбрасывается до
0) происходит при отсутствии давления масла в гидросистеме тормоза и
воды в
системе охлаждения преобразователя частоты; при превышении допустимой
температуры преобразователя.
Информация о состоянии
комплекса и комбайна отображается на
дисплее блока индикации, расположенного в пульте управления
центральном, в 13
окнах: «Причина
выключ.»; «Найденные
неиспр.»; «Пульт
центральн.»; «Пульт
левый»; «Пульт
правый»; «Пульт
радио»; «Пульт
штрековый»; «Коробка
клеммная»; «Блок
управления»; «Преобраз.
частоты»; «Подача»; «Двигатели»; «Контакторы».
Окно – это 8
строк информации, видимой на дисплее блока индикации в текущий момент.
В исполнениях КС500Ч.02,
КС500Ч.04,
КС500Ч.05,КС500Ч.06 информация о состоянии комплекса и комбайна также
отображается на экране дисплея контроллера VisiGRAF, расположенного в
пульте
управления штрековом. Разработанная для пульта управления штрекового
программа
записывается на флеш-диск контроллера VisiGRAF, который опрашивает
локальную
сеть комплекса, отслеживает и отображает работу комбайна.
Испытания комплекса КС500Ч проходили на четырех
шахтах: им.
Бажанова, «Бутовская», «Южнодонбасская»
№3, «Новодонецкая». В
настоящее время в эксплуатации находятся два комбайна КДК500 с
комплексом
КС500Ч - на шахтах им. Бажанова
и «Южнодонбасская» №3. В результате
промышленных испытаний подтверждены заложенные технические решения по
управлению частотно-регулируемым приводом подачи. Аппаратура и очистной
комбайн
приняты к серийному производству [4].
На глобальном уровне
Joy Global Inc. является мировым лидером в области
решений высокой производительности добычи полезных ископаемых.
Благодаря своим
ведущим предприятиями – P&H Mining Equipment и Joy Mining Machinery –
компания производит и продает оригинальное оборудование, запчасти и
предоставляет комплекс услуг для подземной и надземной
горнодобывающей
промышленности.
Система курсовой устойчивости OPTIDRIVE
Очистной комбайн JOY 12HM31-B MkII
оснащен
новой системой управления подачи OPTIDRIVE, которая использует
переменное
напряжение для частотного управления электроприводом 260 кВт (80 л.с.) (VFD).
Электродвигатели переменного тока обеспечивают
повышенную надежность и требуют меньшего эксплуатационного ухода по
сравнению с
двигателями постоянного тока. Система OPTIDRIVE предлагает
улучшенные тяговые усилия, которая помогает в
использовании дополнительной силы резания. OPTIDRIVE –
система, которая
улучшает контроль и маневренность комбайна через регулятор скорости, а
также
позволяет работать электродвигателю в генераторном режиме, отдавая
часть
электричества обратно в сеть.
JOY 12HM31-B MkII
оснащен новейшей JOY системой управления, которая
обеспечивает расширенную диагностику отчетности по производительности и
информации о состоянии комбайна на поверхности, в удаленном режиме и в
местном,
непосредственно на борту машины. Использование микропроцессорной
техники и
компактное блочное исполнение помогают во многом повысить качество и
простоту
технического обслуживания [5].
Описание
полученных и планируемых результатов работы
Выемочные машины являются главным средствам для
добычи полезного ископаемого, что обуславливает большое внимание
уделяемое их
автоматизации и постоянному улучшению их характеристик.
Поскольку
основной задачей горнодобывающей
промышленности является увеличение объемов добычи угля, и уменьшение
опасности связанной с его добычей применяются
автоматизированные способы
управления комбайном, с целью удаления человека на безопасное
расстояние от
места ведения работы [6].
Эксплуатация забойных машин, комплексов и
агрегатов
связана со значительными трудностями, обусловленными их непрерывном
перемещением, разнообразными горно-геологическими условиями,
пылегазовым
режимом шахты, ее микроклиматом и другим факторами [7].
Системы автоматизации
горных машин должны удовлетворять
ряду требований, связанных со спецификацией шахтных условий работы, и
общих
требований, предъявляемых к системам управления. Они должны
удовлетворять
правилам безопасности, быть надежными в работе, обеспечивать
автоматическое
регулирование скорости подачи комбайна и положения исполнительных
органов в
профиле пласта с целью исключения обработки резцами вмещающих боковых
пород [8].
Системы
автоматизации выемочных машин должны обеспечивать
автоматическое отключение комбайна: при остановке забойного конвейера,
уходе
комбайна от передвинутой секции крепи на расстояние более заданного,
наличии
препятствий на машинной дороге, превышении допустимой концентрации
метана на
исходящей из лавы струе и в месте работы комбайна, прекращении подачи
воды в
оросительное устройство комбайна по достижении им исходного положения
по концам
лавы [9].
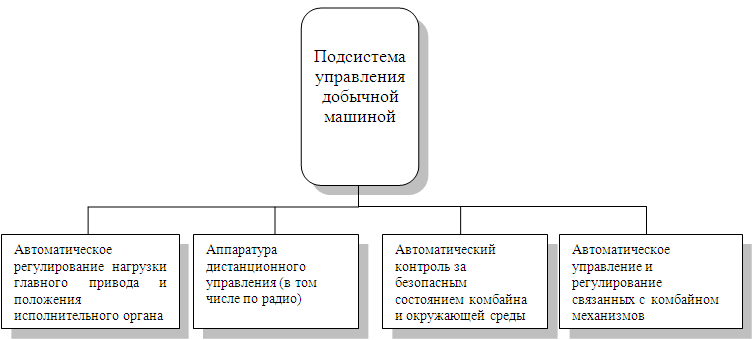
Рисунок 1 –
Структура подсистемы
управления добычной машиной
Подсистема
управления добычной машиной выполняет функции обеспечения местного и
дистанционного управления комбайном, автоматического поддержания
рационального
режима работы, автоматического управления перемещением комбайна вдоль
забоя с
учётом изменения мощности и гипсометрии пласта. Проблема
автоматического
регулирования нагрузки главного привода добычного комбайна является
актуальной
и сегодня [10].
Регулирование нагрузки
осуществляется по средствам
регулятора нагрузки, который представляет собой сложную систему
регулирования .
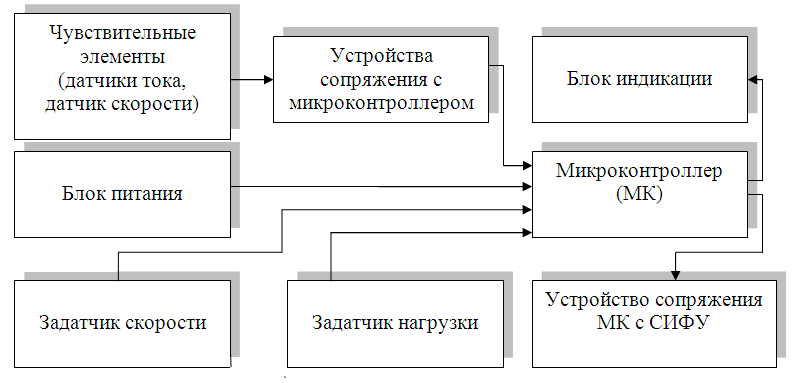
Рисунок 2 - Структурная
схема регулятора нагрузки
Работа регулятора заключается в
следующем.
Чувствительные элементы представлены в виде датчиков тока и датчика
скорости,
через устройства сопряжения присоединяются с микроконтроллером. Питание
подается через выпрямитель напряжения на МК.
Задатчики
присоединяется на вход МК, на основе программного алгоритма будет
происходить
сравнение текущего значения нагрузки электродвигателя через датчики
тока и
скорости, с заданным значением (уставочным). На выходе МК присоединятся
устройство сопряжение с СИФУ, для подачи управляющих импульсов. Наличие
блока
индикации позволяет визуально контролировать исправность
регулятора.
.
Рисунок 3 - Функциональная
схема
регулятора нагрузки добычного комбайна
(анимация: объем – 40,1 КБ; размер – 398x355;
количество кадров – 5; задержка между кадрами – 200 мс; задержка между
последним и первым кадром – 2000 мс, циклов повторения – бесконечное)
ТА1, ТА2, ТА3 – датчики тока
А1, А2, А3 – операционные усилители
Z1, Z2, Z3 – фильтры низких частот
RP – делитель напряжения
STU – стабилизатор
ХА – токосъемник, скользящий контакт (задатчик)
VU – транзисторная оптопара
HL – светодиодный индикатор
BV – датчик скорости
Выводы
Окончательным результатом работы будет являться
разработанная автоматическая система регулирования нагрузки и скорости
подачи
добычного комбайна с частотно-регулируемым приводом, также будет
проведен ряд
исследований на эту тему. Решение задачи автоматизации забойных машин
позволит:
· Повысить
производительность машин путем более полного использования мощности их
электродвигателей;
· Повысить
качество добытого
угля и снизить его себестоимость;
· Улучшить динамические
качества машин,
их надежность и удлинить срок службы;
· Включить
забойные машины в
подсистему АСУ «Очистные забои»
Таким образом, вопрос регулирования важен в
изучении. Необходимость создания более качественных
регуляторов нагрузки
добычного комбайна и усовершенствования существующих, предназначенных
для
работы с частотно-управляемым приводом подачи, это не только важно, но
и
необходимо.
Список
использованной литературы
1.
Батицкий В.А., Куроедов В.И., Рыжков
А.А. Автоматизация производственных процессов и АСУ ТП в горной
промышленности:
Учебник для техникумов.-2-е изд., перераб. и доп. – М.:
Недра, 1991.–
303 с.
2.
Автоматизация процессов подземных
горных работ / Под ред. проф. А.А.Иванова. – К.; Донецк: Вища
школа. Головное
изд-во, 1987. – 328 с.
3.
Автоматизация и автоматизированные
системы управления в угольной промышленности / Под ред. Б.Ф.Братченко
– М.:
Недра, 1976. – 383с.
4. В. Н.
Сирченко, С. Н. Андрусенко, А.
В. Мезников, инженеры, В. В. Синенко, канд. техн. наук. Уголь Украины.
№9,
2006г. стр. 34-35.
5. Doheny T. Mining. Perspectives for Both Worlds [Электронный
ресурс] / T. Doheny.
/ – Режим доступа к статье: http://www.joy.com/jmm/perspectives/Vol12No1.pdf
6.
Электрослесарю добычного и
проходческого оборудования: Справочник / Под. общ. ред. В.А.
Антипова –
Донецк:
Донбасс, 1989 - 159 с.
7.
Автоматизация производственных
процессов угольных шахт /Н.Г.Попович,
Г.И.Данильчук, В.С.Лисовский,
Г.М. Янчук.–
К.: Вища
школа, 1978.-336с.
8. Гаврилов П.Д., Гимельшейн Л.Я.,
Медведев А.Е. Автоматизация
производственных процессов. Учебник для вузов.- М.:
Недра, 1985 - 215с.
9. Крюков І.В., Пономарев А.К.
Рудникова автоматика: Навч. Посібник. – К. Вища шк..., 1994.
– 266с.
10.
Автоматизация
технологических процессов угольных
шахт /Л.Г.Мелькумов, Н.Я.Лазукин, Б.Х.Богопольский, Р.Л.Розенберг. -М.:
Недра,1973.-352
с.
Примечание
При написании данного автореферата квалификационная
работа магистра еще не завершена. Дата окончательного завершения
работы: 1
декабря 2010г. Полный текст работы и материалы по теме работы могут
быть
получены у автора или его научного руководителя после указанной даты.
Copyright © 2010,
ДонНТУ, Юневич Богдан Анатольевич
|