Abstract
of
the Master's Qualification
Work
“Research and
Development of
Automatic Control System of the Load and Velocity Submission Clearing
Combine
with Frequency-Controlled Drive”
Content
3.1. The
work purpose
3.2. Idea of
work
3.3. The
main objectives of the development (research)
3.4. The
subject of the development (of the research)
3.5. The
object of the development (of the research)
3.6.
Methodology and methods of researches
7.1. At the local level
7.2. At the national level
7.3. At the
global level
Introduction
Excavation
machines are the main tools for mining, which requires considerable
attention with regard to their automation and continuous improvement of
their quality characteristics.
Clearing
Combine – a combined mining machinery, both of the demolition
of coal and its loading on conveyer [1].
The
need to
combine automation equipment stipulated by various regulatory
documents. These tools and systems are: remote control equipment and
motors combine the pipeline, as well as an automatic feeder, apparatus
warning lights before starting the combine, the beginning of the
machine, safety winch apparatus speakerphone working in the pit among
themselves and with staff at the roadway, the automatic controller
load, ensuring the maintenance of the desired mode of operation, remote
control position of cutting bodies, protection of electric apparatus of
the rollover and abortive launch, excluding longer find the drive in
the inhibited state, automatic control equipment Lining[2].
A
theme urgency
The effectiveness of the mine depends
on the effective use of mining equipment.
Working with a small strata
of power at large depths, as well as the
need for more precise location, implies an increase in the velocity
response of various elements of automation and improve the high level
of protection to ensure safe operation of maintenance personnel and
protect the equipment from various negative factors of the working
process. In connection with these problems of automation the process of
automatization has received considerable attention.
One of the urgent tasks in the sphere of automation winning machines
(Clearing Combines) is an objective improvement of regulatory burden on
the drive. Existing systems are designed for work with volume hydraulic
drive, can not be used for working with modern combines with with
Frequency-Controlled Drive, so the task of the Research and Development
of Automatic Control System of the Load and Velocity Submission
Clearing Combine with Frequency-Controlled Drive is relevant today.
Communication
of work with scientific programs, plans, themes
Master's
qualification work is executed during 2009-2010 agrees with a
scientific direction of the department "Mining Electrical Engineering
and Automation after R. M. Leibov” of Donetsk National
Technical
University.
The
purpose and problems of the development (of the research)
Objective
- increase the efficiency of the technological process of coal mining
through the development of automation systems including load management
device.
The idea of work
is to develop and study the regulator load Clearing combine with a
Frequency-Controlled Drive application based on microprocessor
technology and modern element base.
The main objectives of the development
(research):
Since the main task of the mining industry is the increase in coal
production and reduce the risks associated with its prey apply
automated control methods combine in order to remove any person to a
safe distance from the place of work.
In the graduation project the following tasks will be discribed :
• Modeling of the work of the Clearing Combine;
• Modeling of system management of the Load and
Velocity Submission Clearing Combine with Frequency-Controlled Drive;
• improving the efficiency, reliability, reducing maintenance
costs and replacement of major components of the equipment process of
coal mining.
The subject of the development
(research) is a direct regulator of the Load and Velocity
Submission Clearing Combine with Frequency-Controlled Drive filing.
The object of
automation is the technological process of coal mining.
Methodology
and methods of researches
The complexity of research,
and often the correctness of the modeling
results are largely determined by the chosen method of research. First
of all, it regards the choice of the method of structural
identification of the object. There are three main approaches to the
development of the mathematical model:
a) The formation of the model equations through
the application of
physical laws that describe the behavior or condition of the object.
The method requires a detailed acquaintance with the physical essence
of the phenomenon.
b) obtaining a mathematical description of the
object on
the basis of the theory of linear graphs. It allows significantly
simplify the process of identification through the formalized
representation of system components in the form-ports and structure of
the object (system) in the form of so-called graph. The method makes it
possible to adapt the model for its implementation by means of
computers.
c) Structural identification of the
object based on the systematic application of variational principles in
the same way as the previous method allows to some extent formalize the
process of drafting a model. This approach requires knowledge of the
researcher bases the calculus of variations and, in particular, the
main variational principles (the principle of Lagrange, Fermat's
principle, etc.), as well as their application.
In this
case, after analyzing the above described
methods of structural identification, to simulate the load of the
combine’s cutting body with the variable resistance of the
coal
cutting choose the first method, based on the application of physical
laws describing the behavior of the object, as well as statistical laws
describing stochastic processes as all other methods are not
appreciated.
Prospective
scientific novelty of the received results
To
develop a reliable mode of operation requires numerous experimental
studies on the existing Clearing Combines. However, the experimental
study of load on the Clearing Combine is very difficult. Under these
conditions mathematical modeling is applied, requires two
prerequisites: the availability of the possibility of constructing an
accurate mathematical model of the mandatory strict adaptation of the
model in an efficient Combine. Modeling of automatic control system for
electric load Clearing Combine is a part of an overall problem of
building Clearing Combines management system. System modeling of
Clearing Combines, as well as mathematical models for regulating the
load will significantly reduce the amount of experimental work carried
out directly on the site, but ultimately does not exclude or replace
them.
Practical
value of the received results
This work will use data
derived from
mathematical analysis. In his ochenred these results are of great
importance in the development of the current model controller workload
mining combine.
Approbation
of the work results
The results
reported at conferences and published in the respective collections.
• X
International Scientific-Technical Conference of graduate and
undergraduate students.Automation of technological objects and
processes. Young Search. (19/05/2010);
• XI International Scientific Youth Conference "Severgeoekotek
– 2010";
At the local level
Such research and development were observed by the students DonNTU:
- Astapov A. "Automation of Рrocess of Regulation
of Speed of Submission
of a Clearing Combine"
- Savitsky A. "Creating a Thyristor Frequency Converter on
IGBT-Modules Made
by Filing a
coal Clearing
Combine"
- Meznikov D. "Variable-Frequency Electric Drive of Submission
of a Clearing Combine"
- Alexeyev R. "Thermal processes research in the
asynchronous motor which feeds with frequency thyristor converter"
At the national level
In
2002, PC "Avtomatgormash
them V.A. Antipov"
has developed a set of technical tools KS500CH.UHL5 for managing
combines 1KDK500, 2KDK500, KDK700, KDK400 with variable speed drive
application, located on Clearing Combine by Production Company
"Gorlovsky machine builder". In the feeding system applied inverter
PCHE – 120M production of "ELMIS" (Kyiv), located directly on
the
combine. KS500CH complex, you can perform a combine in underground
mines, hazardous gas or dust, including the excavation of coal in the
outburst, or threaten the emission layers.
At present the complex is produced in six versions, together with
equipment CMD: KS500CH.02.UHL5 – for Management combines
1KDK500,
2KDK500; KS500CH.04.UHL5 – for KDK700; KS500CH.05.UHL5
–
for KDK400; KS500CH.06.UHL5 – for 1KDK500 and 2KDK500 (with
hardware DCD); KS500CH.07.UHL5 – for 1KDK500, 2KDK500
(without
remote control); KS500CH.08.UHL5 – for KDK400 (without remote
control).
Complexes KS500CH.07,
KS500CH.08 provide management of "local" mode
with the remotes, located at the combine, but complexes KS500CH.02,
KS500CH.04, KS500CH.05, KS500CH.06 – in such regimes: "local"
– with remote management Clearing Combines, "Radio"
–
remotely in the zone of combine visibility with a worn remote radio
wirelessly, "drift" – remotely out of sight from the gate-end
remote in accordance with safety requirements for work on the outburst
and threatened reservoirs.
Complex KS500CH performs the following functions:
- Activation and deactivation
of the Combine
and conveyor together with the equipment installed on the roadway or
CMD DCD (depending on performance);
- Blocking the unauthorized
inclusion of the Combine;
- Control with frequency
converter in the supply system;
- Control of combine actuators;
- Diagnosis and protection of
the basic combine units;
- Management of a combine in a
local mode or
in one of three ("Local", "Radio", "drift") depending on the
modification;
- Emergency shutdown of
mechanisms operating in the coal-face;
- Mapping of the technology
and diagnostic information.
The
system comprises KS500CH: central control panels (built in
elektroblok combine PB 3B Eeyore), Left, Right (RO Ia IR54) and radio
(RO Ia IR54) terminal box (PO Eeyore IR54), temperature sensors and
water flow, oil temperature, of the combine in the lava (RO Ia IR54);
current sensors engines, the availability of water (built in
elektroblok combine PB pollutants Ia) transformers (built in
elektroblok combine PB pollutants Ia); PSU 36/25I (in elektroblok
combine PB pollutants Ia); remote gate-end control (RO Eeyore IR54);
three-channel power 127/12I (PB pollutants Ia).
Functionally
complex KS500CH a local network, which consists of a
series of modules and 1-7000 tCON with attached thereto controls,
sensors and actuators; block indicating the central control console,
controller, remote gate-end control VisiGRAF. Communicationis carried
out over the network using the standard RS-485 interface. A separate
channel is used for its connection with the frequency converter. Each
module has its own strictly defined address, which is assigned
programmatically. The central module of the complex is the controller
1-7188, located in the central control unit. The work of the complex is
stored in accordance with a program in the memory controller,
I-7188.
In case of
emergency: overheating motors, overloading, exceeding the
permissible concentration of methane in the slaughter, the lack of
water in the cooling system of engines overheating of oil in the gear
cutting bodies; violation insulation of power cables, inverter and
engine supply, the disappearance channel at radio, the Combine is off .
Stop of the combine (the feed rate is reset to
0) occurs in the absence of oil pressure in the hydraulic brakes and
water in the cooling system of the frequency converter, in excess of
the permissible temperature of the converter.
Information about the state of the Compex and Combine and is displayed
on the indicating the block, located in the central control unit, in 13
windows: "The reason is off"; "Found faults"; "Remote Central"; "Remote
Left", "Remote Rights"; "Dashboard Radio", "Remote gate-end"; "terminal
box"; "control unit"; "converter of Frequency," "Submission,"
"Engines", "Contactor". Window – is 8 lines of information
that
is visible on the display unit at the current time.
In the versions KS500CH.02, KS500CH.04,
KS500CH.05, KS500CH.06 information about the state of the complex and
the combine is also displayed on the screen controller VisiGRAF,
located in the remote gate-end control. Designed for remote gate-end
control program is recorded on the flash drive controller VisiGRAF,
which interrogates the local network of the complex, monitors and
displays the work of the combine.
Testing complex KS500CH was
held at four mines: Bazhanov, "Butovskaya",
"Yuzhnodonbasskaya" #3, "Novodonetsk". Currently in operation there are
two combines with complex KDK500 KS500CH – in the Bazhanov
mines
and "Yuzhnodonbasskaya" #3. As a result of industrial tests inherent
technical solutions for the management of frequency-controlled drive
source were confirmed. Apparatus and Clearin Combine are accepted for
mass production [4].
At the
global level
Joy
Global Inc. is a world
leader in making high-performance mining. Thanks to its leading
companies – P&H Mining
Equipment and the Joy Mining Machinery –
the company produces and sells original equipment, spare parts and
provides a range of services for underground and surface mining.
Traction System OPTIDRIVE
Clearing Combine JOY 12HM31-B MkII features a new control
system of
submission OPTIDRIVE, which uses a variable voltage to frequency
controlled electric 2 60 kW (80 hp) (VFD). AC electric motors deliver
improved reliability and lower operating maintenance than DC
motors.OPTIDRIVE system offers improved traction effort, which helps to
use more cutting power.OPTIDRIVE –
a system that enhances control and combine maneuverability over speed
control, and allows you to work the motor in generator mode, giving
some power back to the network.
JOY
12HM31-B MkII fitted with the latest JOY management system, which
provides advanced diagnostic, reporting on the performance and status
information for the combine at the surface, remotely and locally,
directly on the vehicle board. Using microprocessor technology and
compact block execution helps greatly to improve the quality and ease
maintenance [5].
Clearing Combines are the main tools for mining, which leads
to much
attention paid to their automation and continuous improvement of their
characteristics.
Since
the main objective of the mining industry is the increase in coal
production, and reduce the risk associated with its prey apply
automated control methods combine to remove any person to a safe
distance from the place of work
[6].
Operation of
longwall machines, systems and components associated with
considerable difficulties resulting from their continuous movement, a
variety of mining and geological conditions, mine dust and gas regime,
its microclimate and other factors [7].
Automation of mining machines must meet certain
requirements to
the specification of mine working conditions, and general requirements
for control systems. They should meet safety regulations to be reliable
in work, to provide automatic control of feed rate and position combine
executive bodies in the profile of the reservoir to avoid processing
incisors enclosing wall rocks [8].
Automation of Clearing Combines have provide the automatic
shutdown of
the combine: bottomhole assembly line at a stop, leaving the combine
from the section of lining at a distance of more than a given, there
are obstacles on the road machine, exceeded the permissible
concentration of methane emanating from the lava stream in place of the
combine, the termination of water supply in the irrigation device
Combine reaches the starting position at the ends of the lava [9].
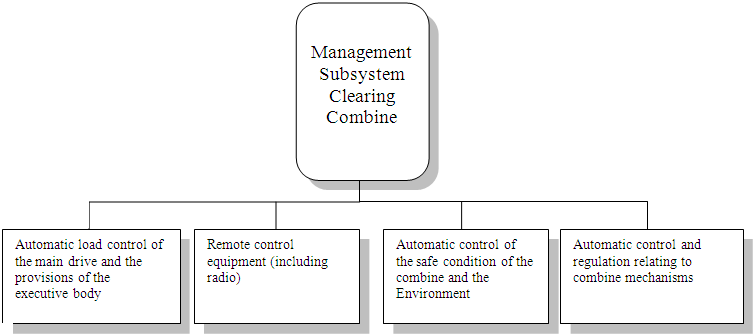
Figure 1 –
Structure of Management Subsystem Clearing
Combine
Management subsystem of
mining machine performs the functions of local and remote control
combine, for the automatic management mode, automatic control of
movement of the Combine taking into account power changing and
hypsometry formation [10].
The problem of automatic regulation of the
load of the main Clearing Combine is relevant today.
Regulation of the load carried out by means of pressure regulator,
which is a complex system of regulation.
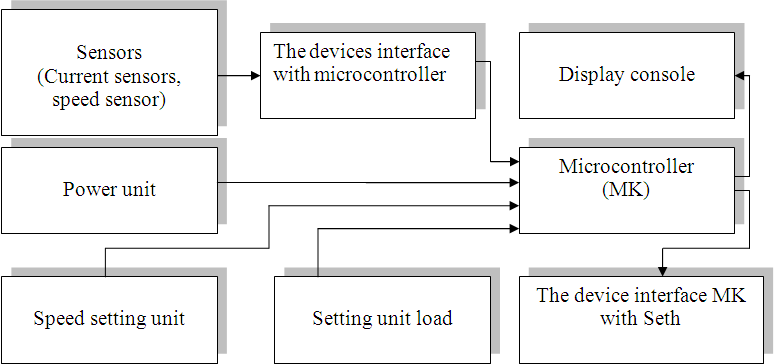
Figure 2 –
Block Diagram of the Controller Workload
Work
of the control is this:
the sensing elements are presented in the form of current sensors and
speed sensor, through the interface attached to the microcontroller.
Power is supplied via a voltage rectifier on the MC. Setting unit joins
the input of the MC-based software algorithm will be comparing the
current value of the load electric current through the sensors and the
speed with a given value. The output of the MC will join the device
pairing with Sifu, for supplying control pulses. The presence of the
block display allows you visually to control the serviceability of the
regulator.
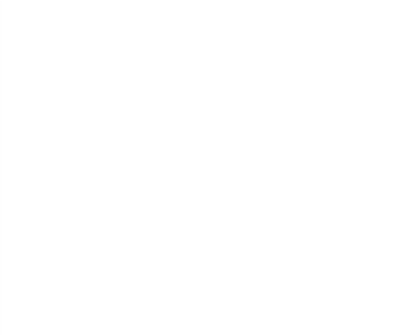
Figure
3 – Functional Diagram of
the Controller Workload Clearing Combine
(Animation:
volume – 40,1
KB; size – 398x355;
number of shots – 5; delay between
shots – 200
ms; delay between the last and first shots – 2000 ms; number
of repetition cycles – infinity)
TA1,
TA2,
TA3 –
current transducers
A1, A2, A3 –
operational amplifiers
Z1, Z2, Z3 –
low-pass filter
RP –
voltage divider
STU –
Stabilizer
HA –
current collector, a rolling pin (setting unit)
VU –
transistor optocouplers
HL –
LED
BV –
speed sensor
Conclusions
The final result
of the work will be
developed Automatic Control System of the Load and Velocity Submission
Clearing Combine with Frequency-Controlled Drive, will also be a number
of studies on this topic. The solution will allow automation of
longwall machines:
•
Increase the productivity of the machines through better capacity
utilization of electric motors;
•
Improve the quality of mined coal and reduce its cost;
•
To improve the dynamic properties of machines, their reliability and
extend service life;
•
Turn down hole machine subsystem ACS "Stopes"
Therefore,
the issue of
control is important in the study, there is need for better
controls load Clearing combines and improvement of existing ones,
designed to work with frequency-controlled drive source.
Bibliography
1.
Батицкий В.А., Куроедов В.И., Рыжков А.А. Автоматизация
производственных процессов и АСУ ТП в горной промышленности: Учебник
для техникумов.-2-е изд., перераб. и доп. – М.: Недра,
1991.-303
с.
2.
Автоматизация процессов подземных горных работ / Под ред. проф.
А.А.Иванова. – К.; Донецк: Вища школа. Головное изд-во, 1987.
– 328 с.
3.
Автоматизация и автоматизированные системы управления в
угольной
промышленности / Под ред. Б.Ф.Братченко – М.: Недра, 1976.
– 383с.
4.
В.
Н. Сирченко, С. Н. Андрусенко, А. В. Мезников, инженеры, В. В. Синенко,
канд. техн. наук. Уголь Украины. №9, 2006г. стр. 34-35.
5.
Doheny T. Mining. Perspectives for Both Worlds [Electronic
resource] / T. Doheny. / –
Access mode to article: http://www.joy.com/jmm/perspectives/Vol12No1.pdf
6.
Электрослесарю добычного и проходческого оборудования:
Справочник
/ Под. общ. ред. В.А. Антипова - Донецк: Донбасс, 1989 - 159 с.
7.
Автоматизация
производственных процессов угольных шахт /Н.Г.Попович, Г.И.Данильчук,
В.С.Лисовский, Г.М. Янчук.-К.: Вища школа, 1978.-336с.
8. Гаврилов П.Д.,
Гимельшейн Л.Я., Медведев А.Е. Автоматизация
производственных процессов. Учебник для вузов.- М.:
Недра, 1985 - 215с.
9. Крюков І.В., Пономарев А.К.
Рудникова автоматика: Навч. Посібник. – К. Вища шк..., 1994.
– 266с.
10. Автоматизация
технологических процессов угольных
шахт /Л.Г.Мелькумов, Н.Я.Лазукин, Б.Х.Богопольский, Р.Л.Розенберг. -М.:
Недра,1973.-352
с.
Note
When writing this abstract
the master’s qualification work is not completed. Date of final completion of work:
December, 1, 2010. Full text of the work and materials on a work theme can be received
from the author or his scientific supervisor after that date.
Copyright
© 2010,
DonNTU, Bogdan Yunevich
|