Реферат по теме выпускной работы
Содержание
- Введение
- 1. Агломерационное производство
- 2. Анализ существующих конструкций
- 3. Описание предложенной конструкции одновалковой зубчатой дробилки
- 4. Моделирование процесса дробления
- Выводы
- Список источников
Введение
Агломерационное производство является одним из начальных этапов металлургического цикла. Результатом этого производства является спекаемый агломерат, который представляет собой шихту, в состав которой входят: железная руда, коксовая мелочь (крупность не более 3 мм), антрацитовый штыб (до 3 мм), тощий уголь (до 3 мм), известняк (до 3 мм), известь и возврат (бракованный мелкий агломерат размерами до 5 мм, возвращаемый в шихту для повторного спекания) [1].
Спекание агломерата осуществляется в специальных агломашинах, которые выдают агломерат в виде пирога. Очевидно, что дальнейшее использование агломерата в таком виде невозможно. С этой целью, непосредственно за агломашинами, устанавливают дробильное оборудование, которое измельчает пирог агломерата до необходимых размеров. В большинстве случаев эту функцию осуществляют дробилки, которые позволяют получить высокую однородность по размеру выходных частиц. Дробилки могут иметь различные конструкции и реализовывать различные способы дробления агломерата. В данной работе будет приведен обзор агломерационного производства, выполнен анализ существующих конструкций дробилок, а также подробно изучены конструктивные особенности одновалковой зубчатой дробилки.
1. Агломерационное производство
Агломерационные фабрики обычно располагают непосредственно на металлургических заводах. Это связано с необходимостью использования при производстве агломерата большого объема побочных продуктов и отходов металлургического производства, а также со сложностью транспортировки готового агломерата.
В агломерационном процессе используют колошниковую пыль, являющуюся отходом доменного производства, окалину, образующуюся в нагревательных и термических печах и при прокатке слитков, а также мелкий кокс, получаемый при сортировке кокса в доменных и коксохимических цехах. При расположении аглофабрики на металлургическом заводе отпадает необходимость в транспортировке этих материалов. Кроме этого, в качестве топлива для спекания агломерационной шихты используются доменный и коксовый газы.
Агломерат, особенно офлюсованный, при перевозке на большие расстояния и перегрузках разрушается, в результате чего образуется значительное количество некондиционной мелочи. Расположение аглофабрики около доменного цеха позволяет транспортировать агломерат ленточными конвейерами.
Агломерационные фабрики представляют собой сложные производственные комплексы. Состав и структура комплексов определяются технологией окускования агломерационной шихты. В состав агломерационной фабрики обычно входят следующие основные сооружения: отделение вагоноопрокидывателей и приемных бункеров шихтовых материалов, корпус дробления и измельчения топлива, корпус дробления и сортировки флюсов (известняка), отделение шихтовых бункеров, корпус смешивания и окомкования шихты, корпуса спекания, охлаждения, дробления и сортировки агломерата, газоочистные сооружения и корпус нагнетателей (эксгаустеров).
Транспортировка шихтовых материалов по технологической цепи агломерационных фабрик осуществляется системой ленточных транспортеров, в состав которой входят перегрузочные узлы.
На рисунке 1 изображена схема цепи аппаратов агломерационной фабрики с конвейерной машиной и прямолинейным охладителем агломерата.
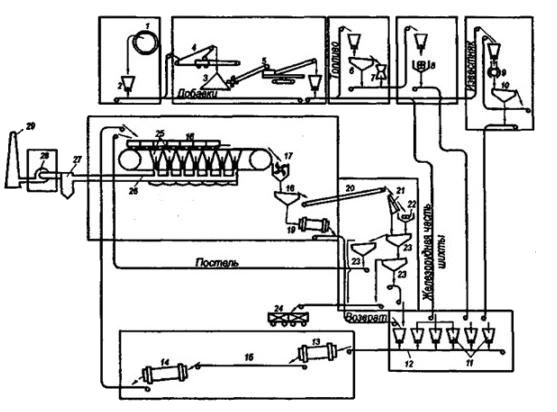
Рисунок 1 – Схема расположения оборудования на агломерационной фабрике
Шихтовые материалы, поступающие на аглофабрику в железнодорожных вагонах, роторными вагоноопрокидывателями 1 разгружаются в приемные бункера 2. Перед вагоноопрокидывателями установлены железнодорожные весы для взвешивания поступающего сырья. При дальних перевозках аглоруда и концентраты, имеющие естественную влажность, в зимнее время смерзаются. Это приводит к усложнению разгрузочных работ и дополнительным расходам на строительство и эксплуатацию гаражей размораживания.
Материалы из приемных бункеров выдаются пластинчатыми или электровибрационными питателями, проходят через перегрузочные узлы и ленточными конвейерами подаются в отделение распределения, передающее материалы на устреднительные склады и обратно со складов на смешивание и окомкование.
На усреднительных складах материалы укладываются в штабели 3, непрерывное послойное формирование которых осуществляется ленточными конвейерами 4, саморазгружающимися тележками или штабелеукладчиками.
Из штабелей сырье различными способами, например роторными экскаваторами 5, загружается на отводящие ленточные конвейеры и транспортируется в отделение шихтовых бункеров. Системы конвейерной загрузки штабелей, существующие на отечественных аглофабриках, не позволяют получать требуемую однородность состава сырья. Крупные склады шихтовых материалов новых отечественных аглофабрик оснащаются современным усреднительным оборудованием, обеспечивающим максимальную степень усреднения, таким, как штабелеукладчики двухконсольный Ш2К-750 и одноконсольный Ш1КП-1000, двухроторный усреднитель-заборщик У2Р-600, универсальная погрузочно-загрузочная машина МПЗУ-1250/750. Топливо и известняк со складов направляются ленточными конвейерами на дробление и измельчение. Для измельчения известняка используют молотковые дробилки 9 типа ДМРИЭ, работающие в замкнутом цикле с грохотами 10. Иногда известняк измельчают в две стадии: в молотковых дробилках до крупности 8-0 мм и в шаровых мельницах до крупности менее 3 мм [6].
Топливо (кокс) в зависимости от исходной крупности измельчают в одну или две стадии. В последнем случае на первой стадии дробления до крупности 15-0 мм применяют конусные дробилки 7 типа КМД-1750 и КМД-220. Кокс перед дробилкой попадает на инерционный грохот 6, где отсеивается мелкая фракция, а затем после дробления вместе с отсеянной мелочью подается в четырех валковую дробилку 8 на вторую стадию измельчения. При одностадийном измельчении используются только валковые дробилки.
Все шихтовые материалы, подготовленные по гранулометрическому составу, поступают в отделение шихтовых бункеров. Бункеры 11 вместимостью 70-100 м3 располагают рядами, число рядов соответствует числу агломашин на фабрике. Число бункеров для различных компонентов определяется составом спекаемой шихты. Для железорудных концентратов и аглоруды используют обычно восемь-девять бункеров, для флюсов – четыре-пять, для топлива – три-четыре. Имеются бункеры для возврата, окалины, колошниковой пыли и других компонентов шихты. Иногда бункера возврата располагают в отделении первичного смешивания, куда направляется возврат с аглолент и из доменного цеха (отсев в скиповой яме). При этом устанавливают один общий для всех агломашин бункер емкостью 350 м3.
Загрузка шихтовых бункеров ведется ленточными конвейерами, оборудованными барабанными сбрасывающими тележками или передвижными конвейерами. Компоненты агломерационной шихты из бункеров выгружаются тарельчатыми или электровибрационными питателями, проходят через систему автоматического взвешивания и дозирования, укладываются на сбороный ленточный конвейер 12 и направляются в корпус первичного смешивания.
В агломерационном процессе для смешивания шихты применяют смесители барабанного типа. Отечественной промышленностью выпускаются смесители СБ-2,8х6 и СБ-2,8х8 для агломашин рабочей площадью 50 и 75 м2, СБ-3,2Х8 и СБ-3,2х12,5 для агломашин площадью 200-400 м2.
Смешанная шихта транспортируется в отделение агломерации и ленточными реверсивными конвейерами загружается в промежуточные бункера, из которых подается на вторичное смешивание (аглофабрики с машинами 75 м2) или на окомкование в барабанные окомкователи типа ОБ-3,2х 12,5 (аглофабрики с машинами 200-400 м2).
Возможно смешивание и окомкование в одном агрегате – смесителе-окомкователе. При загрузке в промежуточные бункера имеет место сегрегация шихты, ухудшающая достигнутую однородность по крупности. Учитывая это, на современных крупных аглофабриках стремятся исключить промежуточные бункера и шихту из барабанного смесителя 13 в окомкователь 14 передавать ленточным транспортером 15.
Подготовленная шихта из окомкователя или вторичного смесителя загружается на челноковый ленточный распределитель, которым равномерно укладывается в бункер барабанного питателя шихты агломерационной машины 16. Перед загрузкой шихты на колосники движущихся спекательных тележек укладывается защитный слой постели – агломерат крупностью 12-25 мм. Загруженные тележки поступают под зажигательный горн, где происходит воспламенение твердого топлива верхнего слоя шихты. При дальнейшем продвижении тележек по агломашине через слой шихты просасывается воздух и горение топлива из верхних слоев постепенно перемещается в нижние. После спекания готовый агломерат в хвостовой части агломашины сходит со спекательных тележек и поступает в одновалковую зубчатую дробилку 17, а оттуда на самобалансный грохот 18, где выделяется горячий возврат (мелочь 6-0 мм); надрешетный продукт подается на охладитель 20. Горячий возврат направляется на сборный конвейер шихтовых бункеров и используется для подогрева других компонентов шихты или охлаждается водой в охладителях барабанного типа 19 и загружается в бункера шихтового отделения. Выделение из горячего агломерата мелких фракций повышает эффективность работы охладителей. Однако затраты на изготовление и обслуживание самобалансных грохотов горячего агломерата и барабанных охладителей возврата весьма высокие. В связи с этим на ряде крупных зарубежных установок вынуждены были отказаться от выделения горячего возврата и весь агломерат после дробления направлять на охлаждение.
На аглофабриках для охлаждения агломерата применяются три типа охладителей: прямолинейные, кольцевые и чашевые, на которых продувом или прососом воздуха агломерат охлаждают до температуры 100o С. При дальнейшей переработке агломерата с такой температурой, улучшаются условия работы оборудования и обслуживающего персонала.
На некоторых отечественных и зарубежных аглофабриках агломерат частично или полностью охлаждают непосредственно на ленте агломашины. Охлажденный агломерат проходит многостадийное грохочение для разделения на годный продукт и возврат.
Для первой стадии грохочения перед вторичным дроблением широко применяются стационарные грохоты 21, разделяющие агломерат на два класса. Надрешетный продукт подвергается измельчению в двухвалковых дробилках 22. При последующих стадиях грохочения на грохотах самобалансного типа 23 агломерат разделяется на годный продукт и возврат, а также выделяется агломерат для подстилочного слоя, подаваемого на колосники спекательных тележек.
После сортировки кондиционный агломерат транспортерами направляется в доменный цех или грузится в специальные железнодорожные вагоны 24.
Горячие газы, получающиеся при спекании агломерата, отсасываются нагнетателем (эксгаустером) 28 через вакуум-камеры 25, газовый коллектор 26, систему пылеочистки 27 и выбрасываются в дымовую трубу 29 [2].
2. Анализ существующих конструкций дробилок
Как было отмечено ранее, одной из важных технологических операций процесса производства агломерата является его дробление после схода с тележки спекательной машины. Эту операцию выполняют с помощью специальных дробилок.
Самыми распространенными видами дробилок являются:
–конусные;
–щековые дробилки;
–валковые;
–молотковые.
Устройство дробилок показано на рис. 2. Разрушение кусков руды в них происходит в результате раздавливающих, раскалывающих, истирающих усилий и ударов. В щековой дробилке блэка материал, вводимый в дробилку сверху, раздавливается качающейся 2 и неподвижной 1 щеками, а в конусной дробилке мак-кули – неподвижным 12 и вращающимся внутренним 13 конусами. вал конуса 13 входит во вращающийся эксцентрик 18. В щековой дробилке только один ход подвижной щеки является рабочим, во время обратного хода щеки часть дробленого материала успевает выйти из рабочего пространства дробилки через нижнюю выпускную щель.
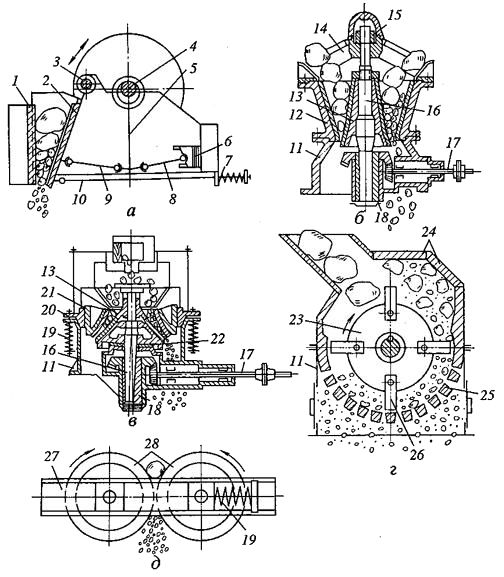
Рисунок 2 – Конструктивные схемы дробилок
а – щековая; б – конусная; в – грибовидная; г – молотковая; д – валковая;
1 – неподвижная щека с осью вращения; 2 – подвижная щека; 3, 4 – эксцентриковый вал; 5 – шатун; 6 – шарнирная опора задней распорной щеки; 7 – пружина; 8, 9 – механизм регулировки ширины разгрузочной щели; 10 – тяга замыкающего устройства; 11 – станина; 12 – неподвижный конус; 13 – подвижный конус; 14 – траверса; 15 – шарнир подвески подвижного конуса; 16 – вал конуса; 17 – приводной вал; 18 – эксцентрик; 19 – амортизационная пружина; 20 – опорное кольцо; 21 – регулирующее кольцо; 22 – подпятник конуса; 23 – ротор; 24 – отбойные плиты; 25 – колосниковая решетка; 26 – молоток; 27 – основная рама; 28 – дробящие валки.
Производительность наиболее крупных щековых дробилок не превышает 450—500 т/ч. Характерными для щековых дробилок являются случаи запрессовки рабочего пространства при дроблении влажных глинистых руд. Кроме того, щековые дробилки не должны применяться для дробления руд, имеющих плитчатое сланцевое строение куска, так как отдельные плитки в случае ориентации их длинной оси вдоль оси щели выдачи дробленого материала могут проходить через рабочее пространство дробилки не разрушаясь.
Питание щековых дробилок материалом должно быть равномерным, для чего пластинчатый питатель устанавливают со стороны неподвижной щеки дробилки. Обычно щековые дробилки применяют для дробления крупных кусков руды (i=3-8). Расход электроэнергии на дробление 1 т железной руды в этих установках может колебаться от 0,3 до 1,3 кВт•ч.
В конусной дробилке ось вращения внутреннего конуса не совпадает с геометрической осью неподвижного конуса, т. е. в любой момент дробление руды происходит в зоне приближения поверхностей внутреннего и наружного неподвижного конусов. При этом в остальных зонах происходит выдача дробленого продукта через кольцевую щель между конусами. Таким образом дробление руды в конусной дробилке осуществляется непрерывно. Достигаемая производительность составляет 3500-4000 т/ч (i=3-8) при расходе электроэнергии на дробление 1 т руды 0,1-1,3 кВт•ч.
Конусные дробилки с успехом можно применять для руд любого типа, в том числе со слоистым (плитчатым) строением куска, а также для глинистых руд. Конусные дробилки не нуждаются в питателях и могут работать под завалом
, т. е. с рабочим пространством, полностью заполняемым рудой, поступающей из расположенного выше бункера.
Короткоконусная грибовидная дробилка Саймонса отличается от обычной конусной дробилки удлиненной зоной выдачи дробленого продукта, обеспечивающей полное дробление материала до заданного размера кусков.
В молотковых дробилках дробление руды осуществляется главным образом под действием ударов по ним стальных молотков, закрепленных на быстровращающемся валу. На металлургических заводах в таких дробилках измельчают известняк, используемый затем в агломерационных цехах. Хрупкие материалы (например, кокс) могут быть измельчены в валковых дробилках.
После первичного дробления богатая малосернистая руда фракции более 8 мм может использоваться доменными цехами, фракция меньше 8 мм, называемая аглорудой
, подвергается окускованию на агломерационных фабриках. Загрузка мелких фракций руды в доменные печи резко ухудшает технико-экономические показатели доменной плавки. В большом количестве мелочь выносится из печи восходящим потоком доменного газа и оседает в пылеулавливателях. Затем ее направляют на аглофабрику.
Часть мелких фракций все же усваивается печью, резко ухудшая газопроницаемость столба шихты, так как мелкие частицы заполняют пространство между более крупными кусками. Необходимо помнить, что отделение мелочи от доменной шихты во всех случаях дает значительный технико-экономический эффект, улучшая ход процесса, стабилизируя вынос пыли на постоянном минимальном уровне, что в свою очередь способствует постоянству нагрева печи и снижению расхода кокса.
Богатые сернистые руды дробят до крупности меньше 8 мм и подвергают агломерации, в ходе которой удаляется из руд 98% сульфидной серы. Бедные руды измельчают до крупности меньше 74 мкм, чтобы разрушить сростки рудного минерала с пустой породой, и направляют на обогащение [3].
Валковые дробилки устанавливают непосредственно за разгрузочной частью агломашины. Устройство, снимающее пирог агломерата с тележек машины, может быть стационарным или подвижным. Эффективнее подвижное исполнение, обеспечивающее регулирование зазора между колосниками спекательных тележек и сменными зубьями отсеивающего устройства. Регулирование выполняется при монтаже, ремонтах и по мере износа зубьев.
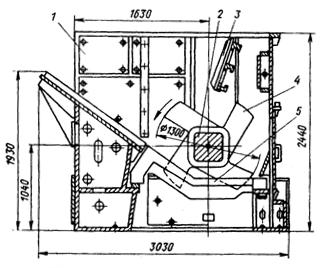
Рисунок 3 – Типовая конструкция одновалковой зубчатой дробилки:
1–корпус; 2–вал ротора; 3–износостойкая плита; 4–зубчатая звездочка ротора; 5–колосниковая решетка.
Дробилка, кроме выполнения основной задачи дробления, является одновременно питателем для установленного за ней грохота горячего агломерата, защищая грохот также от ударов тяжелых кусков агломерата.
Конструкции дробилок, выпускаемых ПО Волгоцеммаш
, построены на более прогрессивном принципе дробления – зубья звездочек проходят между колосниками, обеспечивая лучшее дробление.
Дробилка состоит из зубчатого валка и колосниковой решетки, шарнирно подвешенной в верхней части рамы. Нижний конец колосниковой решетки притянут пружиной к регулируемому упору, что позволяет изменять зазор между зубьями и колосниковой решеткой, и предохраняет дробилку от поломок при попадании недробимых предметов.
Для дробления агломерата в ряде случаев длиннозубчатые валки устанавливают непосредственно над колосниковой решеткой, по которой движутся пласты агломерата, причем зубья валка проходят в зазоры между колосниками. Дробилки предназначены для дробления горячего агломерата, имеющего температуру 600-850o С. Для отвода тепла вал выполнен полым и охлаждается водой. Станина сварная из листового проката, в ее нижней части расположены сменные колосники, стенки облицованы износостойкими плитами. Вал ротора установлен в подшипниках качения. На него насажены звездочки и дистанционные втулки.
При работе дробилки ротор захватывает звездочками поступающий в дробилку пирог агломерата, дробит его на куски и продавливает в зазоры колосниковой решетки. Звездочки выполняют составными, зубья, предварительно изготовленные методом литья из стали 80М14Х16Т, устанавливают в форму ступицы, которую заливают сталью 25. Из стали 80М14Х16Т отливают колосники.
Наиболее изнашиваемыми являются зубья звездочки, поэтому существуют варианты, где они выполняются сменными. Применение таких зубьев, вместо прямоугольных, позволяет уменьшить фракцию раздробления агломерата (менее 100 мм) и уменьшить колличество мелочи. Обычно зубья отливают из стали 70ХЛ и подвергают закалке на твердость 350 НВ. Иногда рабочую поверхность зубьев наплавляют.
Недостатком в работе одновалковых зубчатых дробилок является низкое качество готового агломерата, обусловленное наличием крупных кусков до 25% с размерами 200 мм и более, высокий износ зубьев звездочек и колосников, значительное колличество пылевидных фракций в агломерате, загружаемом непосредственно в доменную печь, что приводит к снижению эффективности ее работы. При уменьшении расстояний между колосниками неоправданно снижается износостойкость рабочих органов дробилки, что увеличивает время простоев аглофабрики из – за ремонтов.
Технические решения (рис. 4), направленные на уменьшение щели между колосниками, заложены в конструкции двухвалковой зубчатой дробилки с зубчатыми валками. Максимальный размер дробленых кусков достигает 40 мм. Кроме того, двухвалковая дробилка имеет преимущество – возможность регулировать размер разгрузочной щели за счет перемещения подвижного валка, крутящий момент которому передается с помощью универсального шпинделя.
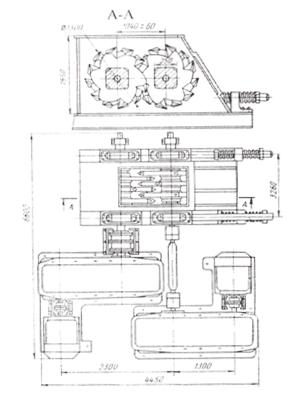
Рисунок 4 – Двухвалковая зубчатая дробилка
Двухвалковая дробилка с индивидуальными приводами валков обладает повышенной надежностью. Работоспособность сохраняется при заклинивании подшипников одного из валков, поскольку зубья неподвижного валка играют роль колосников. Из – за отсутствия неподвижных колосников снижается износ рабочих органов. Недостатком является сложность конструции и повышенная металлоемкость. В ОАО Северсталь
(Россия) применяется одновалковая зубчатая дробилка (рис. 5).
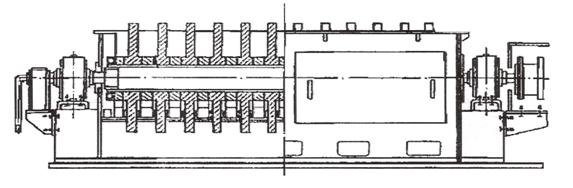
а
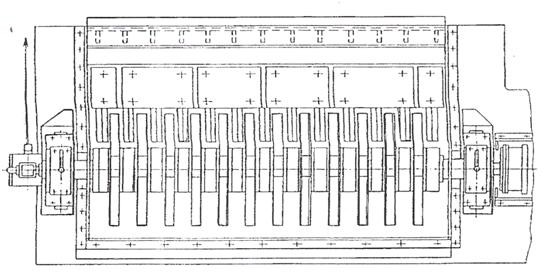
б
Рисунок 5 – Дробилка конструкцииСеверсталь
а–вид спереди, б–вид сверху.
Колосники опираются на балку коробчатого типа, размещенную параллельно валку с зубьями, и зафиксированы на балке с заданным шагом посредством П – образных пластин и упоров на задней стенке корпуса. Длина рабочих поверхностей колосников, находящихся под валком с зубьями, уменьшена до минимально возможного значения, что резко уменьшает температурные деформации колосников при дроблении нагретых материалов. При износе одной рабочей части колосников их переворачивают и используют повторно. Для захвата колосников стропами при переворачивании и замене, каждый из них имеет два паза. Пластины П – образной формы, расположенные между колосниками, формируют шаг между колосниками и закрывают щели между ними для исключения попадания дробимого материала в зону, расположенную за колосниками.
Недостатками данной конструкции является низкое качество дробленого агломерата из – за большого расстояния между колосниками [4].
3. Описание предложенной конструкци одновалковой зубчатой дробилки
Из результатов обзора конструкции дробилок следует, что двухвалковые дробилки при дроблении агломерата на металлургических предприятиях практически не используются, а их внедрение сопряжено с существенными дополнительными затратами. В щековых дробилках эффективного разрушения пирога агломерата добиться невозможно из – за повышенной температуры, при этом теряется энергия на упругое деформирование агломерата.
В связи с этим одновалковые зубчатые дробилки представляются более перспективными, так как получили большое распространение, а разрушение аглоспека в них происходит преимущественно путем продавливания (среза) через колосниковую решетку, что является менее энергозатратным по сравнению с раздавливанием в щековых дробилках. Поэтому совершенствование конструкции одновалковых зубчатых дробилок с целью устранения недостатков является важной практической задачей, стоящей перед специалистами проектных организаций [4].
На рисунке 6 представлена предложенная кинематическая схема одновалковой зубчатой дробилки, в которой применена дополнительная колосниковая решетка, что позволило реализовать двухстадийный процесс дробления, обеспечивающий более высокую однородность кускового состава получаемого агломерата.
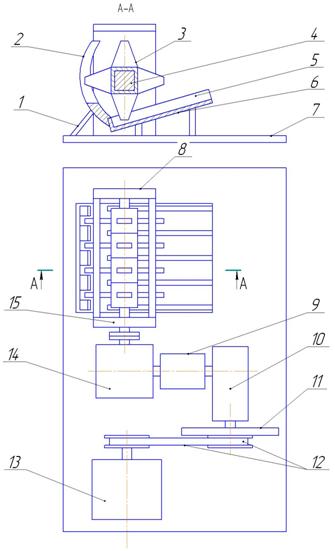
Рисунок 6 – Кинематическая схема одновалковой зубчатой дробилки:
1 – опора вертикальной колосниковой решетки; 2 – колосниковая решетка второй ступени дробления; 3 – звездочка; 4 – ротор; 5,6 – колосниковая решетка первой ступени дробления; 7 – фундамент дробилки; 8 – опорный узел (подшипник скольжения); 9 – тензорезисторный датчик; 10 – цилиндрический двухступенчатый редуктор; 11 – маховик; 12 – ременная передача; 13 – электродвигатель; 14 – червячный редуктор; 15 – муфта упругая втулочно-пальцевая.
Кроме того, в привод добавлена ременная передача, которая сможет предотвратить выход его из строя в случае заклинивания зубчатого валка.
На валу электродвигателя 13 жестко закреплен ведущий шкив ременной передачи 12. Так как диаметры шкивов одинаковы, то передаточное число ременной передачи ip=1. Второй шкив с помощью зубчатой муфты соединен с входным валом быстроходного коническо-цилиндрического редуктора 10 (i1=7,5). Между двумя редукторами расположен тензорезисторный преобразователь 9, который позволяет контролировать крутящий момент, передаваемый тихоходному редуктору 14 (i2=11). Выходной вал этого редуктора соединен с ротором дробилки 4 упругой втулочно-пальцевой муфтой 15. Дробление пирога агломерата осуществляется на колосниковых решетках 2 и 5, которые имеют разные зазоры между колосниками.
На рисунке 7 представлен чертеж общего вида одновалковой зубчатой дробилки (вид сверху)
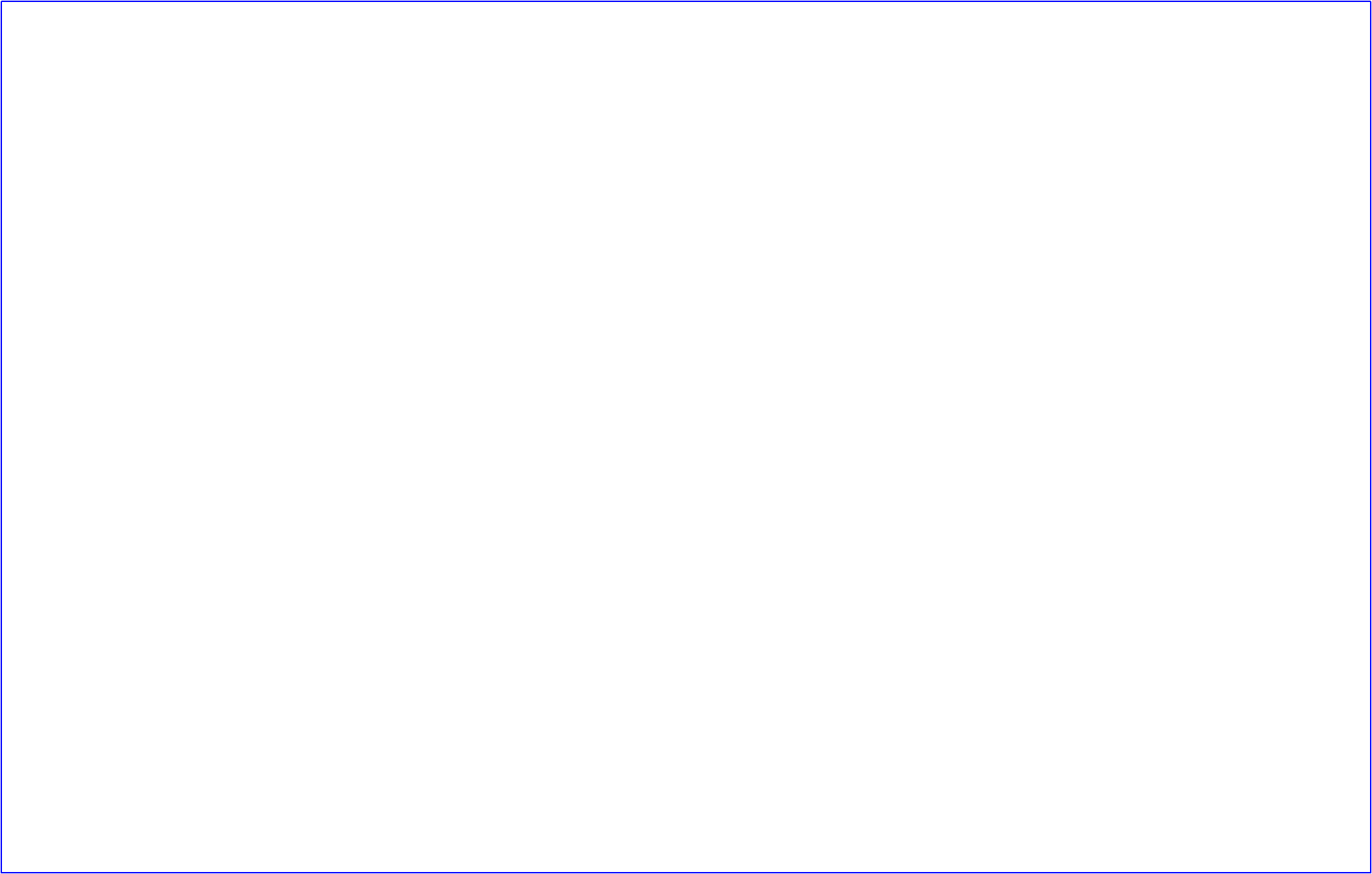
Рисунок 7 – Чертеж общего вида одновалковой зубчатой дробилки (вид сверху)
4. Моделирование процесса дробления
По предложенной кинематической схеме была сконструирована физическая модель одновалковой зубчатой дробилки в масштабе 1:10 (рисунок 8). На данной модели были проведены эксперименты по измельчению материала, в ходе которых были определены данные, которые позволяют охарактеризовать реальный режим работы дробилки.
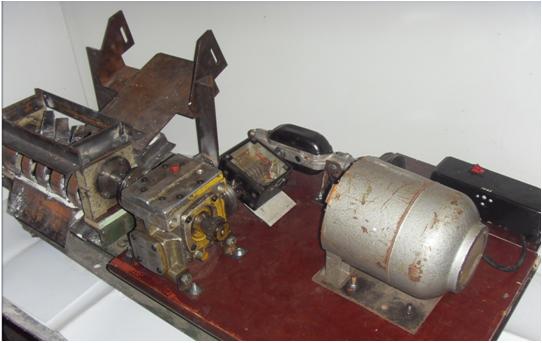
Рисунок 8 – Модель одновалковой зубчатой дробилки
Процесс измельчения материала на физической модели исследуемой дробилки протекает в две стадии. Вначале массив материала зубья вращающихся звездочек 3 раскалывают на крупные фрагменты, попадающие на поддон 6 наклонной колосниковой решетки 5 и выталкиваемые из него в зону расположения цилиндрической решетки 2. Затем образовавшиеся фрагменты продавливаются через узкие прорези этой решетки, в результате чего образуются куски заданного размера, которые по наклонному склизу 1 ссыпаются в приемный короб.
В качестве материала, имитирующего агломерат при моделировании процесса его дробления, было решено использовать пенобетон и пенопласт, т.к. по комплексу свойств они в наибольшей мере соответствуют условиям эксперимента. В ходе экспериментальных исследований процесса измельчения материала контролировалось изменение суммарного момента сопротивления вращению ротора дробилки. В процессе функционирования модели дробилки электрический сигнал, поступавший с преобразователя, после усиления и преобразования в цифровой код на компьютере под управлением специализированного программного обеспечения.
На рисунке 9 показаны характерные виды сигналов, регистрировавшихся при измельчении пенобетона во время контроля крутящего момента, передаваемого муфтой, которая связывала соответствующие валы быстроходного и тихоходного редукторов привода.
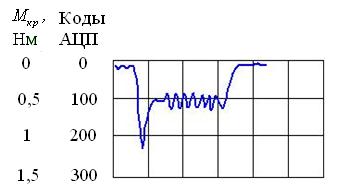
а
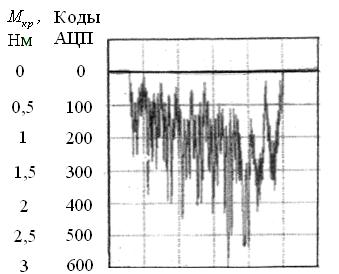
б
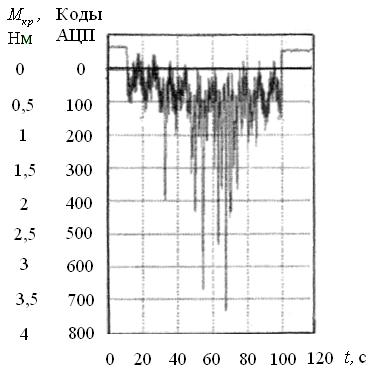
в
Рисунок 9 – Характерный вид регистрировавшихся сигналов при контроле крутящего момента, развиваемого приводом модели дробилки во время холостого хода (а), при разрушении кусков на одной (б) и одновременно на двух (в) решетках.
Как видно из приведенных графиков, привод модели дробилки подвергается действию пиковых нагрузок, вызванных кратковременными, чередующимися во времени реактивными силами, возникающими в зоне контакта головок зубьев звездочек с пластиной материала в момент ее разрушения на крупные фрагменты и последующего их дробления на куски требуемого размера. Указанный характер изменения технологических нагрузок проявлялся для обоих видов материала, использовавшегося в качестве имитатора измельчаемого агломерата. При этом момент холостого хода и моменты сопротивления вращению ротора со звездочками, обусловленные дроблением материала на первой и второй колосниковой решетках, составляли соответственно 10, 12; 60, 65 и 23, 30 % от суммарного значения крутящего момента, развиваемого приводом модели дробилки [5].
Таким образом, на основании полученных результатов моделирования работы предложенной дробилки, можно сделать вывод про ее работоспособность и возможность ее внедрения в производство.
Выводы
Эффективность работы доменных печей в значительной мере зависит от качества агломерата, регламентируемого, прежде всего, содержанием железа с фракционным составом в пределах 5...50 мм. Наличие больших кусков (>50 мм) и пылевидных включений (меньше 5 мм) в товарном агломерате, производимом в Украине, обусловлено несовершенством эксплуатируемого на фабриках дробильного оборудования (щековых, одно- и двухвалковых зубчатых дробилок). Предложенная конструкция дробилки позволит избавиться от этого недостатка, так как она обеспечивает повышение в шихте доли агломерата, фракционный состав которого находится в оптимальных пределах.
На данный момент магистерская работа находится в стадии написания. с рефератом в полном объеме можно будет ознакомиться после 31.01.2013 г.
Список источников
- Вегман Е.Ф. Теория технология агломерации. М.– 1974
- Каталог производственного оборудования
Tehnoinfo.ru
[электронный источник]Tehnoinfo.ru
- Воскобойников В.Г. и др. Общая металлургия – 6-изд., перераб. и доп.– М.: ИКЦ
Академкнига
, 2005– 768 с. - Левченко О.А. Повышение эффективности дробления агломерата путем усовершенствования конструктивных параметров одновалковой зубчатой дробилки: дис.канд. техн. наук: 05.05.08 Левченко Оксана Александровна; Донбасс. гос. техн. ун-т.–Алчевск, 2009.– 176 с.
- Еронько С.П. Удинцев Р.А. Левченко О.А. Моделирование процесса измельчения материала на одновалковой зубчатой дробилке.– Металлургические процессы и оборудование.– 2012.– №1– с. 17-25.
- Патковский А.Б. Агломерационные фабрики черной металлургии. М.– 1954.
- Алтухов В.Н. Пути повышения эффективности дробления агломерата в одновалковой зубчатой дробилке / В.Н. Алтухов, О.А. Левченко // Разработка рудных месторождений : научно-технический сборник / КТУ.– Кривой Рог : КТУ, 2005.– Вып. 89.– С.151-154.