Реферат за темою випускної роботи
Зміст
- Вступ
- 1. Агломераційне виробництво
- 2. Аналіз існуючих конструкцій дробарок
- 3. Опис запропонованноі конструкції одновалкової зубчатої дробарки
- 4. Моделювання процессу подрібнення
- Висновки
- Перелік посилань
Вступ
Агломераційне виробництво є одним з початкових етапів металургійного циклу. Результатом цього виробництва є спікаємий агломерат, який представляє собою шихту, до складу якої входять: залізна руда, коксова дрібниця (крупність не більше 3 мм), антрацитовий штиб (до 3 мм), худе вугілля (до 3 мм), вапняк (до 3 мм), вапно і повернення (бракований дрібний агломерат розмірами до 5 мм, що повертається в шихту для повторного спікання) [1].
Спікання агломерату здійснюється в спеціальних агломашинах, які видають агломерат у вигляді пирога. Зрозуміло, що подальше використання агломерату у такому вигляді неможливе. З цією метою, безпосередньо за агломашинами, встановлюють спеціальне устаткування, яке подрібнює пиріг агломерату до необхідних розмірів. В більшості випадків цю функцію здійснюють дробарки, які дозволяють отримати високу однорідність за розміром вихідних часток. Дробарки можуть мати різні конструкції і реалізовувати різні способи подрібнення агломерату. У даній роботі буде наведений огляд агломераційного виробництва, виконаний аналіз існуючих конструкцій дробарок, а також детально вивчені конструктивні особливості одновалкової зубчастої дробарки.
1. Агломераційне виробництво
Агломераційні фабрики, зазвичай, розташовують безпосередньо на металургійних заводах. Це пов'язано з необхідністю використання при виробництві агломерату великого об'єму побічних продуктів і відходів металургійного виробництва, а також із складністю транспортування готового агломерату.
У агломераційному процесі використовують колошниковий пил, що є відходом доменного виробництва, окалину, що утворюється в нагрівальних і термічних печах і при плющенні злитків, а також дрібний кокс, що отримується при сортуванні коксу в доменних і коксохімічних цехах. При розташуванні аглофабріки на металургійному заводі відпадає необхідність в транспортуванні цих матеріалів. Окрім цього, як паливо для спікання агломераційної шихти використовуються доменний і коксовий гази.
Агломерат, особливо офлюсований, при перевезенні на великі відстані і перевантаженнях руйнується, внаслідок чого утворюється значна кількість некондиційної дрібниці. Розташування аглофабріки біля доменного цеху дозволяє транспортувати агломерат стрічковими конвеєрами.
Агломераційними фабриками є складні виробничі комплекси. Склад і структура комплексів визначаються технологією кускування агломераційної шихти. До складу агломераційної фабрики зазвичай входять наступні основні споруди: відділення вагоноопрокидувачів і приймальних бункерів шихтових матеріалів, корпус подрібнення палива, корпус подрібнення і сортування флюсів (вапняку), відділення шихтових бункерів, корпус змішування і грудкування шихти, корпуси спікання, охолоджування, подрібнення і сортування агломерату, газоочищувальні споруди і корпус нагнітачів (ексгаустерів).
Транспортування шихтових матеріалів по технологічному ланцюгу агломераційних фабрик здійснюється системою стрічкових транспортерів, до складу якої входять перевантажувальні вузли.
На рисунку 1 представлена схема ланцюга апаратів агломераційної фабрики з конвеєрною машиною і прямолінійним охолоджувачем агломерату.
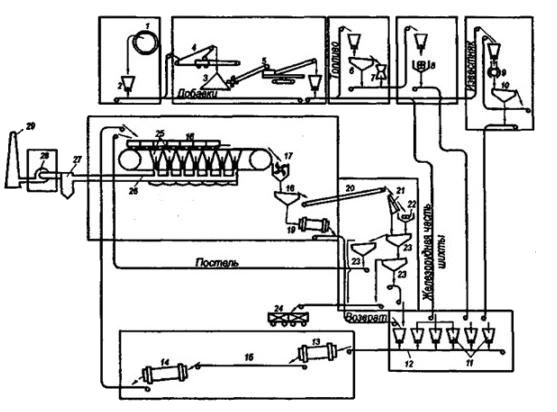
Рисунок 1 – Схема розміщення устаткування на агломераційній фабриці
Шихтові матеріали, що поступають на аглофабріку в залізничних вагонах, роторними вагоноопрокидувачами 1 розвантажуються в приймальні бункери 2. Перед вагоноопрокидувачами встановлені залізничні ваги для зважування сировини, що поступає. При далеких перевезеннях аглоруда і концентрати, що мають природну вологість, в зимовий час мерзнуть. Це приводить до ускладнення розвантажувальних робіт і додаткових витрат на будівництво і експлуатацію гаражів розморожування.
Матеріали з приймальних бункерів видаються пластинчастими або електровібраційними живильниками, проходять через перевантажувальні вузли і стрічковими конвеєрами подаються у відділення розподілу, що передає матеріали на склади і назад із складів на змішування і грудкування.
На посріднювальних складах матеріали укладаються в штабелі 3, безперервне пошарове формування яких здійснюється стрічковими конвеєрами 4,саморозвантажувальними візками або штабелеукладальниками.
З штабелів сировина різними способами, наприклад роторними екскаваторами 5, завантажується на стрічкові конвеєри, що відводять, і транспортується у відділення шихтових бункерів. Системи конвеєрного завантаження штабелів, що існують на вітчизняних аглофабріках, не дозволяють отримувати необхідну однорідність складу сировини. Крупні склади шихтових матеріалів нових вітчизняних аглофабрік оснащуються сучасним посереднювальним устаткуванням, що забезпечує максимальну міру усереднювання, таким, як штабелеукладальники двоконсольний Ш2К-750 і одноконсольний Ш1КП-1000, універсальна вантажно-завантажувальна машина МПЗУ-1250/750. Паливо і вапняк із складів спрямовують стрічковими конвеєрами на подрібнення. Для подрібнення вапняку використовують молоткові дробарки 9 типа ДМРІЕ, що працюють в замкнутому циклі з грохотами 10. Інколи вапняк подрібнюють в дві стадії: у молоткових дробарках до розмірів 8-0 мм і в кульових млинах до розмірів менше 3 мм [6].
Паливо (кокс) залежно від вихідних розмірів подрібнюють в одну або дві стадії. У останньому випадку на першій стадії дроблення до розмірів 15-0 мм застосовують конусні дробарки 7 типа КМД-1750 і КМД-220. Кокс перед дробаркою потрапляє на інерційний грохот 6, де відсіюється дрібна фракція, а потім після подрібнення разом з відсіяною дрібницею подається в чотирьох валкову дробарку 8 на другу стадію подрібнення. При одностадійному подрібненні використовуються лише валкові дробарки.
Всі шихтові матеріали, що підготовлені по гранулометричному складу, поступають у відділення шихтових бункерів. Бункери 11 місткістю 70-100 м3 мають у своєму розпорядженні ряди, число рядів відповідає числу агломашин на фабриці. Число бункерів для різних компонентів визначається складом спікаємой шихти. Для залізорудних концентратів і аглоруди використовують зазвичай вісім-дев'ять бункерів, для флюсів – чотири-п'ять, для палива – три-чотири. Є бункери для повернення, окалини, колошникового пилу і інших компонентів шихти. Інколи бункери повернення розташовують у відділенні первинного змішування, куди прямує повернення з аглолент і з доменного цеху (відсівши в скипової ямі). При цьому встановлюють один загальний для всіх агломашин бункер ємкістю 350 м3.
Завантаження шихтових бункерів ведеться стрічковими конвеєрами, які обладнані барабанними скидаючими візками або пересувними конвеєрами. Компоненти агломераційної шихти з бункерів вивантажуються тарілчастими або електровібраційними живильниками, проходять через систему автоматичного зважування і дозування, укладаються на складальний стрічковий конвеєр 12 і прямують в корпус первинного змішування.
У агломераційному процесі для змішування шихти застосовують змішувачі барабанного типа. Вітчизняною промисловістю випускаються змішувачі СБ-2,8Х6 і СБ-2,8Х8 для агломашин робочою площею 50 і 75 м2, СБ-3,2Х8 і СБ-3,2Х12,5 для агломашин площею 200-400 м2.
Змішана шихта транспортується у відділення агломерації і стрічковими реверсивними конвеєрами завантажується в проміжні бункери, з яких подається на вторичне змішування (аглофабріки з машинами 75 м2) або на грудкування в барабанні окомкувачі типу ОБ-3,2Х 12,5 (аглофабріки з машинами 200-400 м2).
Можливе змішування і грудкування в одному агрегаті – змішувачі-окомкувачі. При завантаженні в проміжні бункери має місце сегрегація шихти, яка погіршуює досягнуту однорідність по розміру. Враховуючи це, на сучасних крупних аглофабріках прагнуть виключити проміжні бункери і шихту з барабанного змішувача 13 в окомкувач 14 передавати стрічковим транспортером 15.
Підготовлена шихта з окомкувача або вторинного змішувача завантажується на челноковий стрічковий розподільник, яким рівномірно укладається в бункер барабанного живильника шихти агломераційної машини 16. Перед завантаженням шихти на колосники рухомих спікатильних візків укладається захисний шар постелі – агломерат розміром 12-25 мм. Завантажені візки поступають під запальний горн, де відбувається займання твердого палива верхнього шару шихти. При подальшому руху візків по агломашині через шар шихти просмоктується повітря і горіння палива з верхніх шарів поступово переміщається в нижні. Після спікання готовий агломерат у хвостовій частині агломашини сходить із спікатильних візків і поступає в одновалкову зубчату дробарку 17, а звідти на самобалансний грохот 18, де виділяється гаряче повернення (дрібниця 6-0 мм); надрешетний продукт подається на охолоджувач 20. Гаряче повернення прямує на збірний конвеєр шихтових бункерів і використовується для підігрівання інших компонентів шихти або охолоджується водою в охолоджувачах барабанного типа 19 і завантажується в бункери шихтового відділення. Виділення з гарячого агломерату дрібних фракцій підвищує ефективність роботи охолоджувачів. Проте витрати на виготовлення і обслуговування самобалансних грохотів гарячого агломерату і барабанних охолоджувачів возврату вельми високі. У зв'язку з цим на ряду крупних зарубіжних установок вимушені були відмовитися від виділення гарячого повернення і весь агломерат після дроблення направляти на охолоджування.
На аглофабріках для охолоджування агломерату застосовуються три типи охолоджувачів: прямолінійні, кільцеві і чашові, на яких продувкою або просмоктуванням повітря агломерат охолоджують до температури 100° С. При подальшій переробці агломерату з такою температурою покращуються умови роботи устаткування і обслуговуючого персоналу.
На деяких вітчизняних і зарубіжних аглофабриках агломерат частково або повністю охолоджують безпосередньо на стрічці агломашини. Охолоджений агломерат проходить багатостадійне грохочення для розділення на придатний продукт і повернення.
Для першої стадії грохочення перед вторинним подрібненням широко застосовуються стаціонарні грохоти 21, що розділяють агломерат на два класи. Надрешетний продукт піддається подрібненню в двовалкових дробарках 22. При подальших стадіях грохочення на грохотах самобалансного типу 23 агломерат розділяється на придатний продукт і возврат, а також виділяється агломерат для підстилкового шару, що подається на колосники спікатильних візків.
Після сортування кондиційний агломерат транспортерами прямує в доменний цех або вантажиться в спеціальні залізничні вагони 24.
Гарячі гази, що виходять при спіканні агломерату, відсасуються нагнітачем (ексгаустером) 28 через вакуум-камери 25, газовий колектор 26, систему пилеочистки 27 і викидаються в димар 29 [2].
2. Аналіз існуючих конструкцій дробарок
Як було відмічено раніше, однією з важливих технологічних операцій процесу виробництва агломерату є його подрібнення після сходу з візка спікательной машини. Цю операцію виконують за допомогою спеціальних дробарок.
Найпоширенішими видами дробарок є:
–конусні;
–щічні дробарки;
–валкові;
–молоткові.
Устрій дробарок показаний на рис. 2. Руйнування шматків руди в них відбувається в результаті роздавлюючих, розколюючих, стираючих зусиль і ударів. У щічній дробарці Блека матеріал, що вводиться в дробарку зверху, роздавлюється такою, що коливається 2 і нерухомою 1 щоками, а в конусній дробарці Мак-Кулі – нерухомим 12 і внутрішнім, що обертається, 13 конусами. Вал конуса 13 входить в ексцентрик, що обертається, 18. У щічній дробарці лише один хід рухливої щоки є робочим, під час зворотного ходу щоки частина роздробленого матеріалу встигає вийти з робочого простору дробарки через нижню випускну щілину.
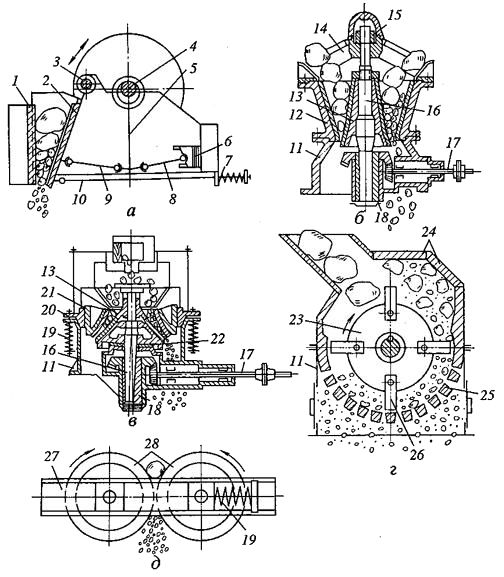
Рисунок 2 – Конструктивні схеми дробарок
а – щічна; б – конусна; в – грибоподібна; г – молоткова; д – валкова;
1 – нерухома щока з віссю обертання; 2 – рухома щока; 3,4 – ексцентриковий вал; 5 – шатун; 6 – шарнірна опора задньої розпірної щоки; 7 – пружина; 8,9 – механізм регулювання ширини розвантажувальної щілини; 10 – тяга замикаючого пристрою; 11 – станина; 12 – нерухомий конус; 13 – рухомий конус; 14 – траверса; 15 – шарнір підвіски рухомого конуса; 16 – вал конуса; 17 – привідний вал; 18 – ексцентрик; 19 – амортизаційна пружина; 20 – опорне кільце; 21 – регулювальне кільце; 22 – підп’ятник конуса; 23 – ротор; 24 – відбійні плити; 25 – колосникова решітка; 26 – молоток; 27 – основна рама; 28 – подрібнюючи валки.
Продуктивність найбільш крупних щічних дробарок не перевищує 450-500 т/ч. Характерними для щічних дробарок є випадки запресовки робочого простору при дробленні вологих глинистих руд. Крім того, щічні дробарки не повинні застосовуватися для дроблення руд, що мають плитчасту сланцеву будову шматка, оскільки окремі плитки в разі орієнтації їх довгої осі уздовж осі щілини видачі роздробленого матеріалу можуть проходити через робочий простір дробарки не руйнуючись.
Живлення щічних дробарок матеріалом має бути рівномірним, для чого пластинчастий живильник встановлюють з боку нерухомої щоки дробарки. Зазвичай щічні дробарки застосовують для подрібнення крупних шматків руди (i=3-8). Витрата електроенергії на подрібнення 1 т залізняку в цих установках може вагатися від 0,3 до 1,3 кВт•г.
У конусній дробарці вісь обертання внутрішнього конуса не збігається з геометричною віссю нерухомого конуса, тобто у будь-який момент подрібнення руди відбувається в зоні наближення поверхонь внутрішнього і зовнішнього нерухомого конусів. При цьому в останніх зонах відбувається видача роздробленого продукту через кільцеву щілину між конусами. Таким чином дроблення руди в конусній дробарці здійснюється безперервно. Продуктивність, що досягається, складає 3500-4000 т/ч (i=3-8) при витраті електроенергії на подрібнення 1т руди 0,1-1,3 кВт•г.
Конусні дробарки з успіхом можна застосовувати для руд будь-якого типу, у тому числі з шаруватою (плитчастим) будовою шматка, а також для глинистих руд. Конусні дробарки не потребують живильників і можуть працювати під завалом
, тобто з робочим простором, що повністю заповнюється рудою, що поступає з розташованого вище бункера.
Короткоконусная грибоподібна дробарка Саймонса відрізняється від звичайної конусної дробарки подовженою зоною видачі роздробленого продукту, що забезпечує повне подрібнення матеріалу до заданого розміру шматків.
У молоткових дробарках подрібнення руди здійснюється головним чином під дією ударів по ній сталевих молотків, які закріплені на швидкообертаючомуся валу. На металургійних заводах в таких дробарках подрібнюють вапняк, який використовується потім в агломераційних цехах. Крихкі матеріали (наприклад, кокс) можуть бути подрібнені у валкових дробарках.
Після первинного подрібнення багата малосірчаста руда фракції більше 8 мм може використовуватися доменними цехами, фракція менше 8 мм, звана аглорудой
, піддається кускуванню на агломераційних фабриках. Завантаження дрібних фракцій руди в доменні печі різко погіршує техніко-економічні показники доменної плавки. У великій кількості дрібниця виноситься з печі висхідним потоком доменного газу і осідає в пилеулавлювачах. Потім її направляють на аглофабріку.
Частина дрібних фракцій все ж засвоюється піччю, різко погіршуючи газопроникність стовпа шихти, оскільки дрібні частки заповнюють простір між крупнішими шматками. Необхідно пам'ятати, що відділення дрібниці від доменної шихти у всіх випадках дає значний техніко-економічний ефект, покращуючи хід процесу, стабілізуючи винесення пилу на постійному мінімальному рівні, що у свою чергу сприяє постійності нагріву печі і зниженню витрати коксу.
Багаті сірчасті руди дроблять до великої фракції менше 8 мм і піддають агломерації, в ході якої віддаляється з руд 98% сульфідної сірки. Бідні руди подрібнюють до великої фракції менше 74 мкм, щоб зруйнувати зростки рудного мінералу з порожньою породою, і направляють на збагачення [3].
Валкові дробарки встановлюють безпосередньо за розвантажувальною частиною агломашини. Пристрій, що знімає пиріг агломерату з візків машини, може бути стаціонарним або рухливим. Ефективніше рухливе виконання, що забезпечує регулювання зазору між колосниками спікатільних візків і змінними зубами відсіюючого пристрою. Регулювання виконується при монтажі, ремонтах і у міру зносу зубів.
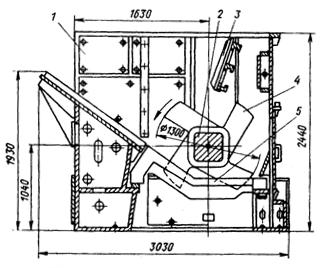
Рисунок 3 – Типова конструкція одновалкової зубчатої дробарки:
1–корпус; 2–вал ротора; 3–зносостійка плита; 4–зубчата зірочка ротора; 5–колосникова решітка.
Дробарка, окрім виконання основного завдання подрібнення, є одночасно живильником для встановленого за нею гуркоту гарячого агломерату, захищаючи грохот також від ударів важких шматків агломерату.
Конструкції дробарок, що випускаються ПО “Волгоцеммаш”, побудовані на прогресивнішому принципі дроблення – зуби зірочок проходять крізь колосники, забезпечуючи краще подрібнення.
Дробарка складається із зубчастого валка і колосникових решіток, що шарнірно підвішені у верхній частині рами. Нижній кінець колосникових решіток притягнутий пружиною до регульованого упору, що дозволяє змінювати зазор між зубами і колосниковими решітками, і оберігає дробарку від поломок при попаданні неподрібнених предметів.
Для подрібнення агломерату у ряді випадків дліннозубчаті валки встановлюють безпосередньо над колосниковими решітками, по яких рухаються пласти агломерату, причому зуби валка проходять в щілини між колосниками. Дробарки призначені для подрібнення гарячого агломерату, що має температуру 600-850° С. Для відведення тепла вал виконаний порожнистим і охолоджується водою. Станина зварна з листового прокату, в її нижній частині розташовані змінні колосники, стінки футеровані зносостійкими плитами. Вал ротора встановлений в підшипниках кочення. На нього насаджені зірочки і дистанційні втулки.
При роботі дробарки ротор захоплює зірочками пиріг агломерату, що поступає в дробарку, дробить його на шматки і продавлює в щілини колосникових решіток. Зірочки виконують складеними, зуби, заздалегідь виготовлені методом литва із сталі 80М14Х16Т, встановлюють у форму маточини, яку заливають сталлю 25. Із сталі 80М14Х16Т відливають колосники.
Найбільш зношуваними є зуби зірочки, тому існують варіанти, де вони виконуються змінними. Вживання таких зубів, замість прямокутних, дозволяє зменшити фракцію роздроблення агломерату (менше 100 мм) і зменшити кількість дрібниці. Зазвичай зуби відливають із сталі 70ХЛ і піддають гарту на твердість 350НВ. Інколи робочу поверхню зубів наплавляють.
Недоліком в роботі одновалкових зубчастих дробарок є низька якість готового агломерату, обумовлена наявністю крупних шматків до 25% з розмірами 200 мм і більш, високий знос зубів зірочок і колосників, значна кількість пилоподібних фракцій в агломераті, який завантажується безпосередньо в доменну піч, що призводить до зниження ефективності її роботи. При зменшенні відстаней між колосниками невиправдано знижується зносостійкість робочих органів дробарки, що збільшує час простоїв аглофабрики з-за ремонтів.
Технічні рішення (рис. 4), які спрямовані на зменшення щілини між колосниками, закладені в конструкції двохвалкової зубчастої дробарки із зубчастими валками. Максимальний розмір роздроблених шматків досягає 40 мм. Крім того, двовалкова дробарка має перевагу – можливість регулювати розмір розвантажувальної щілини за рахунок переміщення рухливого валка, обертальний момент якому передається за допомогою універсального шпинделя.
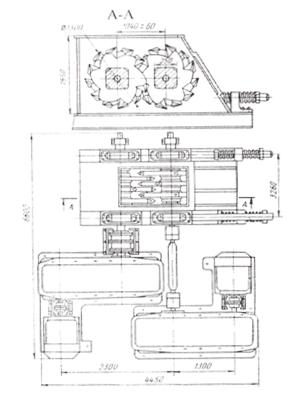
Рисунок 4 – Двохвалкова зубчата дробарка
Двохвалкова дробарка з індивідуальними приводами валків володіє підвищеною надійністю. Працездатність зберігається при заклинюванні підшипників одного з валків, оскільки зуби нерухомого валка грають роль колосників. З – за відсутності нерухомих колосників знижується знос робочих органів. Недоліком є складність конструкції і підвищена металоємність. У ОАО Северсталь
(Росія) застосовується одновалкова зубчаста дробарка (рис. 5).
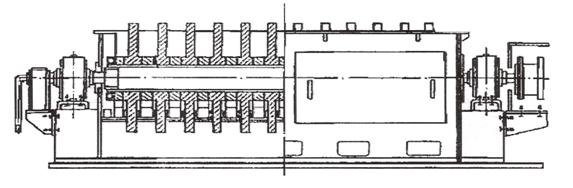
а
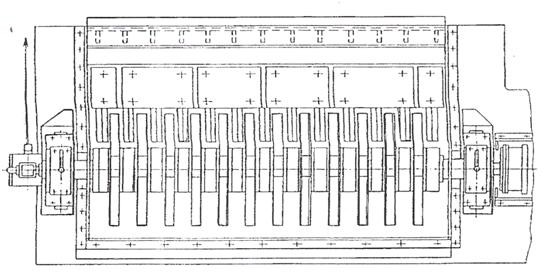
б
Рисунок 5 – Дробарка конструкції Северсталь
а–вид спереду, б–вид зверху.
Колосники спираються на балку коробчатого типу, яка розміщена паралельно валкам із зубами, і зафіксовані на балці із заданим кроком за допомогою П – образних пластин і упорів на задній стінці корпусу. Довжина робочих поверхонь колосників, які знаходяться під валком із зубами, зменшена до мінімально можливого значення, що різко зменшує температурні деформації колосників при подрібненні нагрітих матеріалів.
Недоліками даної конструкції є низька якість роздробленого агломерату з – за великої відстані між колосниками [4].
3. Опис запропонованої конструкції одновалкової зубчатої дробарки
З результатів огляду конструкції дробарок виходить, що двовалкові дробарки при подрібнені агломерату на металургійних підприємствах практично не використовуються, а їх впровадження зв'язане з істотними додатковими витратами. У щічних дробарках ефективного руйнування пирога агломерату добитися неможливо з – за підвищеної температури, при цьому втрачається енергія на пружну деформацію агломерату.
У зв'язку з цим одновалкові зубчасті дробарки представляються перспективнішими, оскільки набули великого поширення, а руйнування аглоспека в них відбувається переважно шляхом продавлювання (зрізу) крізь колосникові решітки, що є менш енерговитратним в порівнянні з розчавлюванням в щічних дробарках. Тому вдосконалення конструкції одновалкових зубчастих дробарок з метою усунення недоліків є важливим практичним завданням, що стоїть перед фахівцями проектних організацій [4].
На рисунку 6 представлена запропонована кінематична схема одновалкової зубчастої дробарки, в якій застосовані додаткові колосникові решітки, що дозволило реалізувати двохстадійний процес подрібнення, який забезпечує вищу однорідність кускового складу отримуваного агломерату.
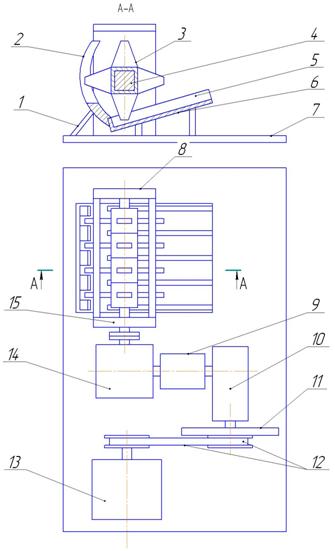
Рисунок 6 – Кінематична схема моделі одновалкової зубчатої дробарки:
1 – опора вертикальних колосникових решіток; 2 –колосникова решітка другого ступеня подрібнення; 3 – зірочка; 4 – ротор; 5,6 – колосникові решітки першого ступеня подрібнення; 7 – фундамент дробарки; 8 – опорний вузол (підшипник ковзання); 9 – тензорезісторний претворювач; 10 – циліндричний двоступінчатий редуктор; 11 – маховик; 12 – ремінна передача; 13 – електродвигун; 14 – черв'ячний редуктор; 15 – муфта пружна втулково – пальцева.
Крім того, в привід додана ремінна передача, яка дозволяє запобігти виходу його з ладу в разі заклинювання зубчатого валка.
На валу електродвигуна 13 жорстко закріплений провідний шків ремінної передачі 12. Оскільки діаметри шківів однакові, то передавальне число ремінної передачі ip=1. Другий шків за допомогою зубчастої муфти сполучений з вхідним валом швидкохідного конічо-циліндричного редуктора 10 (i1=7,5). Між двома редукторами розташований тензорезісторний перетворювач 9, який дозволяє контролювати обертальний момент, що передається тихохідному редуктору 14 (i2=11). Вихідний вал цього редуктора сполучений з ротором дробарки 4 пружньою втулково – пальцевою муфтою 15. Подрібнення пирога агломерату здійснюється на колосникових решітках 2 і 5, які мають різні зазори між колосниками.
На рисунку 7 представлене креслення загального виду одновалкової зубчатох дробарки (вид зверху)
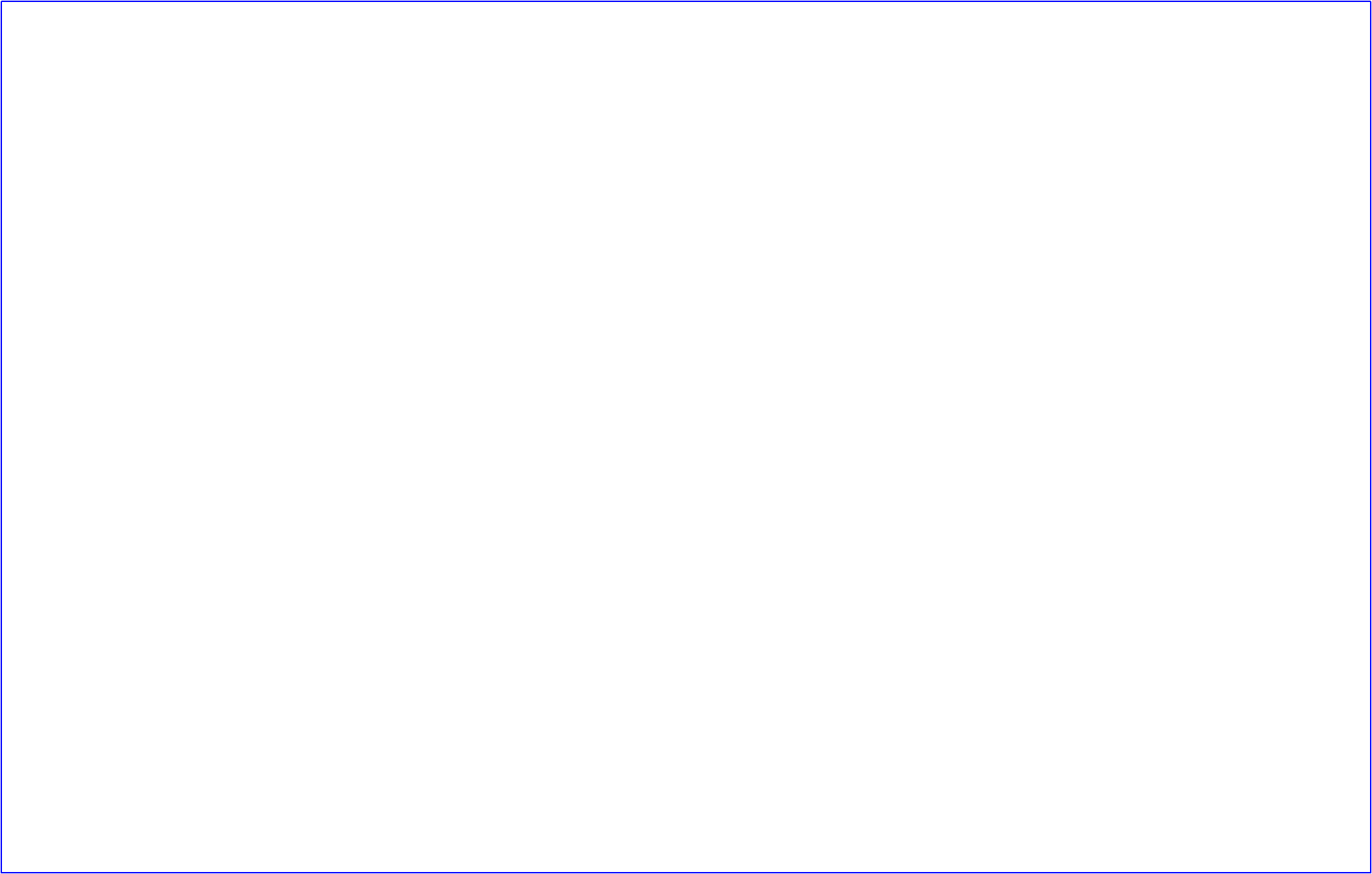
Рисунок 7 – Креслення загального виду одновалкової зубчатох дробарки (вид зверху)
4. Моделювання процесу подрібнення
За запропонованою кінематичною схемою була сконструйована фізична модель одновалкової зубчастої дробарки в масштабі 1:10 (рисунок 8). На даній моделі були проведені експерименти по подрібненню матеріалу, в ході яких були визначені дані, які дозволяють охарактеризувати реальний режим роботи дробарки.
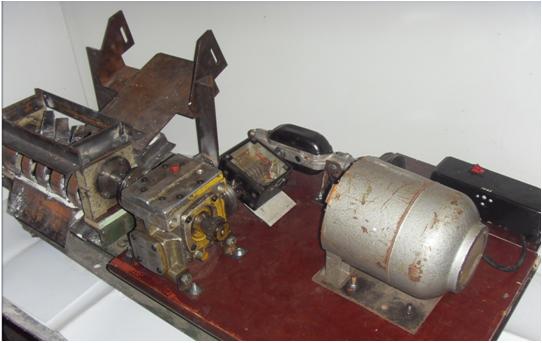
Рисунок 8 – Модель одновалкової зубчатої дробарки
Процес подрібнення матеріалу на фізичній моделі досліджуваної дробарки протікає в дві стадії. Спочатку масив матеріалу зуби зірочок, що обертаються, 3 розколюють на крупні фрагменти, які потрапляють на піддон 6 похилих колосникових решіток 5 і виштовхуються з нього в зону розташування циліндрової решітки 2. Фрагменти, які потім утворилися, продавлюються через вузькі прорізи цієї решітки, внаслідок чого утворюються шматки заданого розміру, які по похилому склізу 1 зсипаються в приймальний короб.
Як матеріал, що імітує агломерат при моделюванні процесу його дроблення, було вирішено використовувати пінобетон і пінопласт, оскільки по комплексу властивостей вони в найбільшій мірі відповідають умовам експерименту. Перед проведенням експериментальних досліджень була підготовлена партія пластин, що підлягають руйнуванню.
В ході експериментальних досліджень процесу подрібнення матеріалу контролювалася зміна сумарного моменту опору обертанню ротора дробарки. В процесі функціонування моделі дробарки електричний сигнал, що поступав з перетворювача, після посилення і перетворення в цифровий код на комп'ютері під управлінням спеціалізованого програмного забезпечення. На рисунку 9 показані характерні види сигналів, що реєструвалися при подрібненні пінобетону під час контролю обертального моменту,що передається муфтою, яка зв'язувала відповідні вали швидкохідного і тихохідного редукторів приводу.
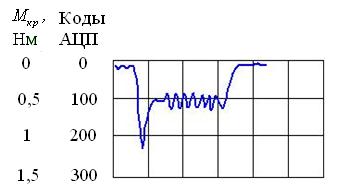
а
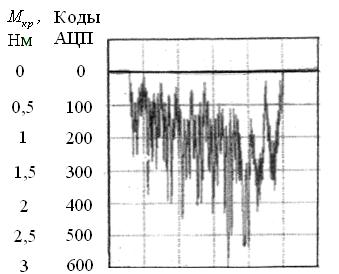
б
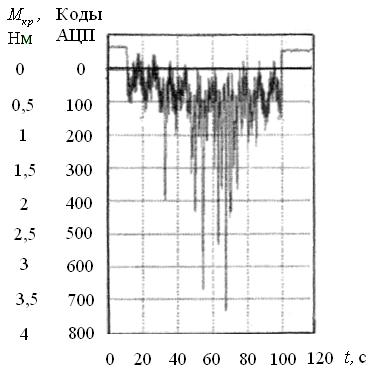
в
Рисунок 9 – Характерний вигляд сигналів, що реєструвалися, при контролі моменту, що крутить, розвивається приводом моделі дробарки під час холостого ходу (а); при руйнуванні шматків на одній (б) і одночасно на двох (в) решітках.
Як видно з приведених графіків, привід моделі дробарки піддається дії пікових навантажень, які викликані короткочасними, такими, що чергуються в часі реактивними силами, що виникають в зоні контакту голівок зубів зірочок з пластиною матеріалу у момент її руйнування на крупні фрагменти і подальшого їх подрібнення на шматки необхідного розміру. Вказаний характер зміни технологічних навантажень виявлявся для обох видів матеріалу, що використався як імітатор подрібнюваного агломерату. При цьому момент холостого ходу і моменти опору обертанню ротора із зірочками, обумовлені дробленням матеріалу на першій і другій колосниковій гратах, складали відповідно 10, 12; 60, 65 і 23, 30 % від сумарного значення обертального моменту, розвивається приводом моделі дробарки [5].
Таким чином, на підставі отриманих результатів моделювання роботи запропонованої дробарки можна зробити висновок про її працездатність і можливість її впровадження у виробництво.
Висновки
Ефективність роботи доменних печей значною мірою залежить від якості агломерату, що регламентується, перш за все, вмістом заліза з фракційним складом в межах 5...50 мм. Наявність великих шматків (>50 мм) і пилоподібних включень (менше 5 мм) в товарному агломераті, вироблюваному в Україні, обумовлена недосконалістю встановленного на фабриках дробильного устаткування (щічних, одно- і двохвалкових зубчастих дробарок). Запропонована конструкція дробарки дозволить позбавитися від цього недоліку, оскільки вона забезпечує підвищення в шихті долі агломерату, фракційний склад якого знаходиться в оптимальних межах.
На даний момент магістерська робота знаходиться в стадії оформлення, з рефератом в повному обсязі можно буде ознайомитися після 31.01.2013
Перелік посилань
- Вегман Е.Ф. Теория технология агломерации. М.– 1974
- Каталог производственного оборудования
Tehnoinfo.ru
[электронный источник]Tehnoinfo.ru
- Воскобойников В.Г. и др. Общая металлургия – 6-изд., перераб. и доп.– М.: ИКЦ
Академкнига
, 2005– 768 с. - Левченко О.А. Повышение эффективности дробления агломерата путем усовершенствования конструктивных параметров одновалковой зубчатой дробилки: дис.канд. техн. наук: 05.05.08 Левченко Оксана Александровна; Донбасс. гос. техн. ун-т.–Алчевск, 2009.– 176 с.
- Еронько С.П. Удинцев Р.А. Левченко О.А. Моделирование процесса измельчения материала на одновалковой зубчатой дробилке.– Металлургические процессы и оборудование.– 2012.– №1– с. 17-25.
- Патковский А.Б. Агломерационные фабрики черной металлургии. М.– 1954.
- Алтухов В.Н. Пути повышения эффективности дробления агломерата в одновалковой зубчатой дробилке / В.Н. Алтухов, О.А. Левченко // Разработка рудных месторождений : научно-технический сборник / КТУ.– Кривой Рог : КТУ, 2005.– Вып. 89.– С.151-154.