Реферат по теме выпускной работы
Содержание
- Введение
- 1. Анализ публикаций
- 2. Постановка проблемы исследования
- 3. Изложение материала и результаты
- Выводы
- Список источников
Введение
Среди продуктов, получаемых при помощи химического синтеза, значительная доля приходится на метанол. Метанол является хорошей заменой для топлив и сырьем для многих производств органического синтеза. К перспективным направлениям использования метанола относятся: производство уксусной кислоты, очистка сточных вод, производство синтетического протеина, синтез углеводородов с целью получения топлива.
Важной задачей является снижение себестоимости производства метанола и повышение экологической безопасности за счет реализации современных подходов. Для эффективного использования передового мирового опыта в этой области необходима разработка в рамках отечественной науки решений для изучения, оптимизации и управления современным оборудованием и процессами.
1. Анализ публикаций
Принципиально технологический процесс получения метанола включает ряд операций, которые обязательны для любой технологической схемы синтеза [1, 2]:
- получение синтез-газа (газа, основными компонентами которого являются H2 и CO, содержащиеся в заданной пропорции);
- очистка синтез-газа от карбинола железа и сернистых соединений;
- подогрев газа до температуры начала реакции;
- работа газа в реакторе синтеза метанола;
- выделение из потока газов, покидающих реактор, метанола за счет охлаждения;
- сжатие оставшегося газа до давления синтеза и возврат в процесс.
Классическая технология синтеза метанола предполагает использование в качестве реакторов колонн синтеза (рисунок 1). При этом равновесная степень превращения метанола за один проход, как правило, не превышает 20%.
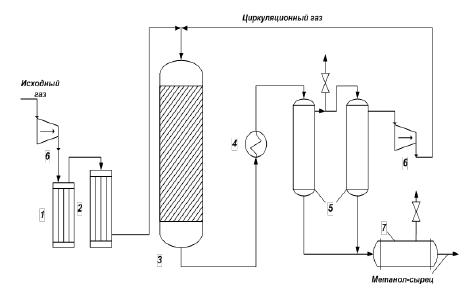
Рисунок 1 – Схема синтеза метанола
(1 – масляный фильтр; 2 – угольный фильтр; 3 – колонна синтеза; 4 – холодильник-конденсатор; 5 – сепараторы; 6 – компрессоры; 7 – сборник)
Несколько десятилетий назад компанией Лурги были разработаны трубчатые реакторы, в которых тепло реакций передается кипящей воде.
Водоохлаждаемый реактор синтеза метанола представляет собой вертикальную шахту с трубчатым теплообменником и фиксированными трубными решетками. Катализатор расположен в трубках и лежит на подстилке из инертного материала. Кипящая вода заполняет межтрубное пространство. Паро-водяная смесь, полученная благодаря теплу реакций, отводится из-под верхней трубной решетки. Контроль давления пара позволяет управлять температурой реакции. Этот изотермический реактор позволяет достичь высокой производительности при низкой доле возврата и минимизирует производство попутных продуктов.
В последнее время компанией Лурги разработана двойная система реакторов, в рамках которой изотермический водоохлажадемый реактор комбинируется с газоохлаждаемым реактором. Также известен целый ряд работ, предлагающих высокоэффективные реакторы синтеза метанола, в которых в той или иной мере используются изложенные выше подходы [3].
Таким образом, освоение водоохлаждаемых реакторов и двойных систем реакторов является актуальной задачей для отечественной химической промышленности, так как при этом производственный комплекс становится более компактным, уменьшаются капитальные затраты на его сооружение и расход энергии на производство единицы продукции.
2. Постановка проблемы исследования
В данной работе решается задача создания концептуальных и алгоритмических основ систем диагностики тепловой работы водоохлаждаемых реакторов синтеза метанола. Задача решается за счет разработки методики составления теплового баланса реактора и ее использования для определения важных технологических параметров на стадии проектирования (максимальные и номинальные расходы пара и питательной воды) и создания алгоритма для оперативной диагностики тепловой работы реактора путем определения доли расходования монооксида углерода в реакциях синтеза и соответственно вынесения суждения об истощении каталитической способности катализатора.
3. Изложение материала и результаты
Схема водоохлаждаемого реактора синтеза метанола с предложенным набором элементов КИП и АСУ ТП для диагностики тепловой работы представлена на рисунке 2.
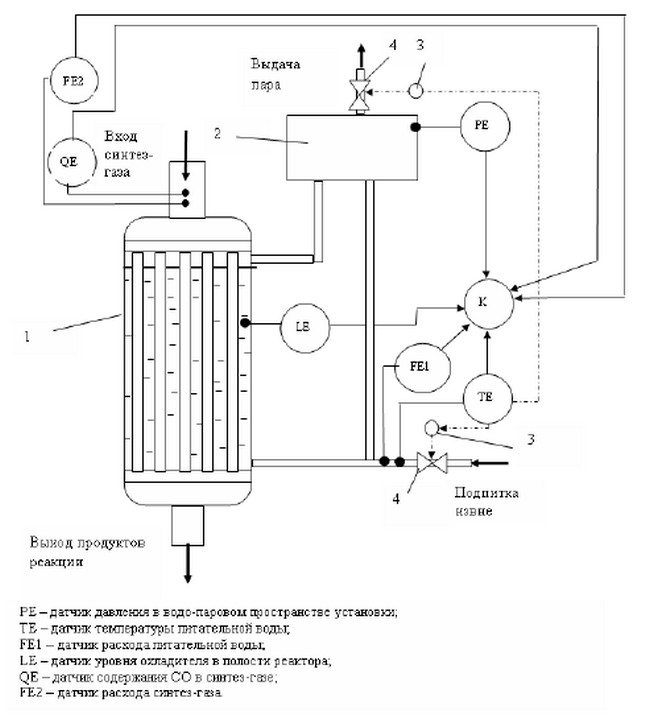
Рисунок 2 – Системы диагностики тепловой работы реактора синтеза метанола
(1 – водоохлаждаемый реактор, 2 – сепаратор, 3 – исполнительные механизмы, 4 – регулирующие органы)
Постоянная температура в полости реактора поддерживается за счет установки давления пара при помощи соответствующих регулирующих органов. Пароводяная смесь, образующаяся при кипении воды в межтрубном пространстве, поднимается в сепаратор, в котором отделяется и выводится сухой насыщенный пар. Восполнение массы охладителя реализуется за счет подвода свежей питательной воды. Расход подпиточной воды определяется из условия поддержания заданного уровня охладителя в межтрубном пространстве реактора или заданной массы охладителя в реакторе. В первом случае необходимо использование датчика уровня, во втором взвешивание реактора при помощи тензодатчиков. По мнению авторов, из-за малой доли испаряемой жидкости по сравнению с ее общей массой в реакторе, верхний уровень жидкости в реакторе будет иметь хотя несколько колеблющуюся однако достаточно четкую границу, что позволяет использовать, например, емкостные датчики уровня.
Составление теплового баланса водоохлаждаемого реактора необходимо как на стадии его проектировании, так и для создания алгоритма управления и мониторинга.
На стадии проектирования сепаратора необходимо знать номинальный и максимальный расходы пара, которые будут образовываться в реакторе.
Эти величины могут быть определены при помощи следующего комплекса зависимостей:
Qp= ξ · | CO | · | V | · | 1 | · QM , | (1) |
100 | 3600 | 22,4 |
где Qp – тепловыделение в реакторе синтеза метанола, Вт;
ξ – доля расходования монооксида углерода в реакциях синтеза;
СО – процентное содержание монооксида углерода в синтез-газе, %;
V – объемный расход синтез-газа, м3/ч;
Qм – тепловой эффект образования метанола, Дж/кмоль.
Gпар=  | Qp | , | (2) |
iнп − iпв |
где Gпар – расход пара из сепаратора, кг/с;
iнп, iпв – энтальпия насыщенного пара на выходе из реактора и питательной воды соответственно, Дж/кг.
Энтальпия питательной воды выбирается в зависимости от ее давления и температуры, а насыщенного пара – в зависимости от заданного уровня давления в водо-паровом пространстве из термодинамических таблиц, описывающих свойства воды и водяного пара, [4] или соответствующих интерполяционных зависимостей.
Давление в водо-паровом пространстве выбирается исходя из условия обеспечения заданной температуры кипения воды, что и определяет стабилизированное значение температуры в реакционном пространстве. Для определения максимально возможного выхода пара в качестве аргументов для зависимостей (1) и (2) используются максимально возможные по технологии расход синтез-газа и произведение содержания синтез газа на долю его усвоения в реакции. Для определения номинального значения этой величины аргументы устанавливаются на проектном уровне.
Для проектирования системы снабжения реакторов питательной водой должны быть определены номинальное и максимальное значения этой величины. Для каждого из характерных режимов работы реактора массовый расчетный расход питательной воды равен соответствующему расчетному выходу пара.
Пример использования предложенных зависимостей для определения расхода питательной воды представлен на рисунке 3. При этом были использованы следующие исходные данные:
Содержание СО в синтез-газе, % ……………………………….….21,5
Энтальпия насыщенного пара при давлении 43 атм , кДж/кг…....2799
Энтальпия питательной воды (43 атм, 50oС), кДж/кг ……………..213
Тепловой эффект реакции образования метанола, МДж/кмоль ...110,8
Диагностику протекания реакций и анализ истощения реакционной способности катализатора предложено вести на основании анализа величины расходования монооксида углерода в реакциях синтеза, рассчитанной в зависимости от текущего расхода питательной воды:
ξ = | Gв · (iнп − iпв) · 100 · 3600 · 22,4 | . |
CO · V · Qм |
Использование предложенной зависимости представлено на рисунке 4. При этом были взяты те же исходные данные, что и при построении рисунка 3.
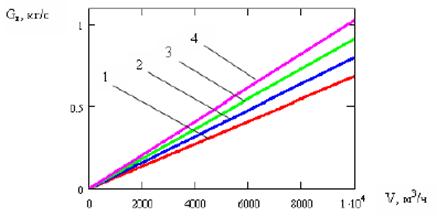
Рисунок 3 – Зависимость расхода питательной воды от расхода синтез-газа через аппарат
(1 – для доли использования монооксида углерода 60%, 2 – 70%, 3 – 80%, 4 – 90%)
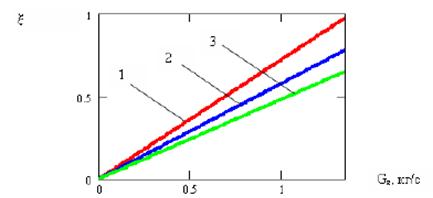
Рисунок 4 – Зависимость доли прореагировавшего монооксида углерода от расхода питательной воды
(1 – для расхода синтез-газа 10000 м3/ч, 2 – 15000 м3/ч, 3 – 18000 м3/ч)
Представленная на рисунке 4 информация показывает, как для заданных параметров работы реактора в зависимости от расхода питательной воды может быть однозначно определена величина расходования монооксида углерода в реакциях синтеза, что позволяет в реальном времени получать информацию об интенсивности протекания реакций и выносить суждение об истощении реакционной способности катализатора.
Наличие такой информации необходимо для принятия решения о приостановке процесса для замены или регенерации катализатора. Накопление этой информации и ее анализ совместно со статистикой изменения других важных производственных факторов позволяют углубить представления о процессе и подобрать условия, позволяющие расширить временные рамки использования катализаторов.
Создание предпосылок для рационального использования современного оборудования синтеза метанола повышает экологическую безопасность за счет сокращения объемов перерабатываемого исходного сырья, снижения объемов вредных выбросов в атмосферу и уменьшения площадей занимаемых соответствующими предприятиями.
Выводы
Обоснована целесообразность разработки систем диагностики тепловой работы водоохлаждаемых реакторов синтеза метанола, позволяющих на основании непрерывного анализа теплового баланса выносить суждение об истощении реакционной способности катализатора.
Предложена конкретная схема диагностики тепловой работы водоохлаждаемых реакторов синтеза метанола и алгоритм ее использования в рамках систем АСУ ТП участка синтеза метанола.
Список источников
- Химическая технология ТГИ / Под ред. Г.Н. Макарова, Г.Д. Харламповича. – М.: Химия, 1986. – 496 с.
- Печуро Н.С. Химия и технология синтетического жидкого топлива и газа / Н.С. Печуро, В.Д. Капкин, О.Ю. Песин. – М.: Химия, 1986. – 352 с.
- Мещеряков Г.В. Химическая технология неорганических и органических веществ, теоретические основы / Г.В. Мещеряков // Химия и химическая технология .– 2009.– №6.– 86-88
- Ривкин С.Л. Термодинамические свойства воды и водяного пара. Справочник. - 2-е изд., перераб., и доп. / С.Л. Ривкин, А.А. Александров – М.: Энергоатомиздат, 1984. – 80 с.
- Теплотехника термической переработки твердых топлив: Учебное пособие/ Кравцов В.В., Бирюков А.Б., Дробышевская И.П. - Донецк: Издательство «Ноулидж», 2011. – 170с.
- Промышленные печи. Справочное руководство для расчетов и проектирования. 2-е издание, дополненное и переработанное. Казанцев Е.И. М., "Металлургия", 1975. 368 с.
- Бондалетова Л.И., Бондалетов В.Г. Процессы переработки сырья и рациональное использование природных ресурсов: Учебное пособие. – Томск: Изд-во ТПУ, 2006. – 160 с.