Abstract
The content
- Introduction
- 1. Theme urgency
- 2. Goal and tasks of the research
- 3. A brief review of the master's work
- 3.1 Analysis of the degassing of the mine network
- 3.2 Analysis of the vacuum – pumping stations
- 3.3 Analysis of systematic violations technology of work
- 3.4 Analysis of the prospects decontamination of mine
- Conclusions
- List of sources
Introduction
The increase in coal production and the pace of mining accompanied by a complication of mining – geological and mining conditions, mining of coal seams associated with the increase in gas release and gas – dynamic phenomena (ГДЯ) in the mines. In this regard, particular importance is the problem of reducing gas dangerous mines using degasification of coal developed strata during mining operations.
1. Theme urgency
With the development of coal deposits are inextricably linked selection methane. In mining operations, released accumulated in mountain range, methane, creating a risk of explosion in underground mines mine.
The problem of methane in the modern mining industry
considered in three ways: as a problem of
safety and economic efficiency of high – coal mining, the
problem
of industrial use of methane in the energy and
other industries, as well as environmental problem associated with
receipt of methane in underground coal seams in the
atmosphere. In underground coal mining methane problem is especially
important
in terms of mine safety and increase their
economic efficiency. In recent years in the coal
Ukrainian industry have reached a critical value of the frequency and
size
accidents and disasters in underground coal mines. Most
significant of these relate to the explosions of methane emitted from
coal seams [1].
Next, consider the situation at the mine
Krasnoarmeyskaya - Western
Number 1
(fig. 1).
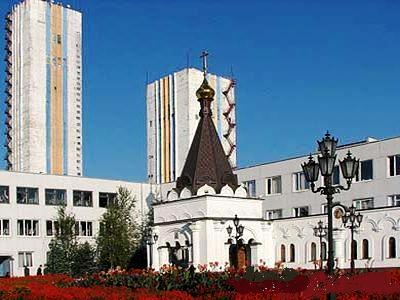
Figure 1. Mine "Krasnoarmeyskaya – Zapadnaya number 1"
2.
Goal and tasks of the research
The aim of this study is to increase the coefficient of degassing ensuring safe conditions of working, an increase of captured methane – air mixture and to provide a cogeneration plant workers gas. Also considered is the organization of drainage in the long term development information field which is the analysis of the required parameters underground drainage excavation sites and analysis of surface degassing. This analysis allows you to organize and review complex drainage system of the mine. To ensure that the coefficient degassing Kdvo least 0.7 proposed drainage scheme, separately for layers of medium and low power, described the scheme of degassing developed layer, shielding scheme of drainage wells and gob degasification wells flank. Considered to use the scheme of degassing reservoir nadrabatyvaemogo d3. For operational management of the system considered the use of decontamination automatic flow control of gas – air mixture. Completed brief analysis of the drainage holes of the program from the surface.
Main objectives of the study:
- Analysis of underground degassing of mines and the establishment of the causes of inefficiency the system.
- Systematic analysis disturbances in the system and their impact on the safety of the mine check
- Coefficient effectiveness of decontamination.
- Improving the quality of captured methane – air mixture.
- Research and development measures to improve the degassing system of the mine (Increased rate of degassing).
- Analysis of the prospects degassing of the mine.
object
of
study: mine Krasnoarmeyskaya
– Zapadnaya
,
the system
degassing.
subject of study: improving the degassing system and improve safety.
As part of master's thesis will receive the actual scientific results in the following areas:- Development of recommendations for improvement of drainage system for the reduction of accidents.
- Achieving the highest economic effect of the use of methane.
3. A brief review
of
the
master's work
3.1 Analysis of the
degassing of the mine network
Mine degasification scheme is a network of pipelines located in the mountain workings, which is conventionally divided into three branches – is branch of the horizon, 593 m, 708 m and horizon horizon 815 m (fig. 2). The branches of the horizons 593 m and 708 m through the hole out on the surface of the main industrial area and connected to the SPC number 1, and a branch of the horizon through the skip shaft 815 m ventilation shaft to the surface of the industrial site UPU–2 and connected to the VNS number 2. The length of the branches g. 593–5500 m, is transportation of gas – air mixture from the areas:
— two northern lava block 3;
— goaf 5 northern lava "encore" incline block 5;
— a goaf North "encore" lava block 2.
The length of the branches g. 708–13300m on it is transportation of gas – air mixture from the areas:
— four north central lava 8 of the unit;
— five southern lava of the central panel unit 8;
— six southern lava of the central panel unit 8;
— a northern lava unit 10;
— goaf 4 South "encore" lava unit 10.
The length of the branches g. 815–6000 m, it is to transport gas mixture of:— a southern lava unit 10;
— two southern lava unit 10.
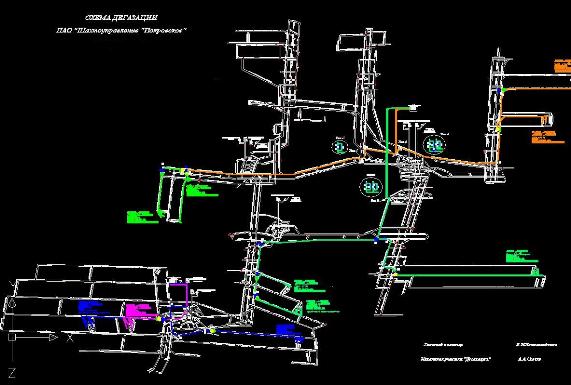
Pokrovskoye
Currently decontamination network of mines, made after the reconstruction, which lasted from 2005 and continued in 2011. (Replacement of pipelines with 325 mm to 426 mm, and for the block 10–530 mm, the transition to Precinct pipes not less than 426 mm, the new refurbishment of the mine advanced drilling technology, which allows to drill diameter less than 114–132mm, putting in the work of modern vacuum – pumping station on the VPS–2, the reconstruction of the vacuum – pumping station the main industrial site with conclusion of the work on the worn – out pipelines skip shaft), has the required capacity and the necessary capacity to ensure high degassing excavation sites of mine to to create safe working conditions [7].
3.2 Analysis of the
vacuum pumping stations
Currently, there are two in the vacuum surface – Pumping Station: ANS number 1 (the main industrial site) and VNS number 2 (industrial site CHD-2).
On the main production site modernized ANS number 1 with the replacement of the four vacuum – Pump VVN2–150 for four vacuum – compressor VVK2–150. Produced by design and construction of new towers, which provided opportunity to supply fuel gas for the cogeneration plant (Provision of gas pressure in the discharge line to 450mbar).
To ensure a stable feed methane – air mixture from the vacuum – pumping station VNS N 1 to finish third and fourth stages of the reconstruction of the SPC number 1 (The first stage of the transition from the trunk pipelines in four wells drilled from the surface, with the installation of culverts and connecting underground part – is made, the second phase of construction and start- work of the new cooling tower water recycling – made): the third phase – installation of a second pipeline issue methane mixture on the territory of the vacuum – pumping station with the construction extension; the fourth stage – the replacement of valves and tools dehumidified (Separator).
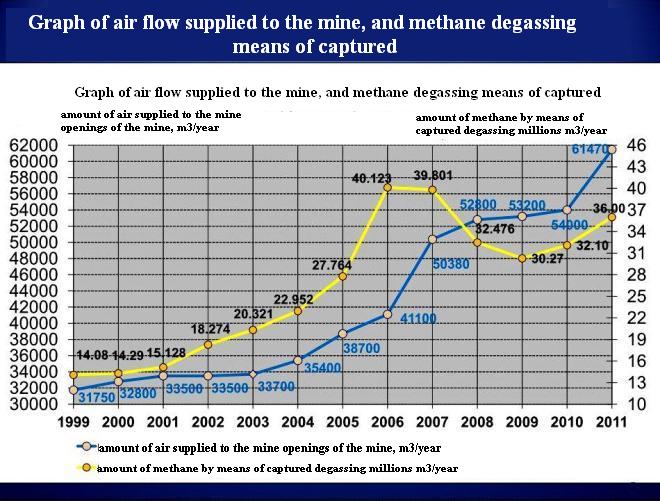
3.3 Analysis of the
systematic
violations of the technology of work
After the examination, excavation of the mine sites have been identified following systematic violations [7]:
Two northern lava block 3 – Concentration of the gas mixture at the output of 25 %, the drilling wells are drilling machine GBH1/89/12 over 75 bars, Drill 114 mm. Drilling rig in a satisfactory condition, that allows you to drill at least 30–35 m per shift, the work is a bush Well, two in reserve. Wells are drilled according to the length and diameter passport, the further operation of wells does not meet the standards. Sealing holes produced by 2–3 m without connecting couplings, when the wells go into mined-out space of the mouth is not increase bolting for their preservation or install roof supports unsatisfactory. Without casing wellhead and enhance the well destroyed immediately after the passage of lava, and as a consequence are in several days depending on the size of destruction. None metering and control devices on wells. State degassing pipe satisfactorily.
Four northern central lava 8 of the unit – the concentration of gas – air mixture at the outlet 28 % drilling is drilling unit UBC–1M (with electric engine) in the presence of 60 bars, chisels 93 mm. Drilling rig in the satisfactory condition, which allows decontamination drill wells at a rate of up to 15–20 m/smenu, behind a bush on the lava degasification wells is 50m. Length and diameter of the holes under the Passport options with the distance between the bushes, 20 m, and the angle of rotation recovery wells are not always observed because of the presence of anchors gain and pick – up. Sealing wells at 2–3 m, so work Well short – lived. There is no metering and control devices on wells. Degassing pipes in good condition.
Six southern lava of the central panel Unit 8 – the concentration of gas-air mixture at the output 30 % drilling well drilling rig is available GBH1/89/12 80 rods, Drill 114 mm. Drilling rig in a satisfactory condition, that allows you to drill at least 30–35 m per shift, lagging behind the lava bush degasification wells is 30 m. Wells drilled in accordance with Passport options with the distance between the bushes 10–13 m. Sealing wells at 2–3 m, so the work is short–lived wells. Length diameter Well according to the passport, and the rotation angle and lift wells are not always observed due to the availability of the gain and pick – up anchors, and also because of the unsatisfactory state of generation after passage of lava. There is no metering and control devices on wells.
Five southern lava of the central panel Unit 8 – the concentration of gas–air mixture at the outlet 7 % drilling well drilling rig is UBC–1m in the presence of 45 bars, chisels 76 mm. Sealing wells at 2–3 m, so work well short–lived. Length and diameter of the holes are not met, and angle of rotation and rise in the wells is not always observed due to the loss of project section of development. There is no metering and control devices on wells.
Two southern lava unit 10 – the concentration of methane in the gas mixture at the output 18 % drilling is drilling machine GBH1/89/12 in the presence of 100 bars, chisels 114 mm. Drilling rig in a satisfactory condition, that allows you to drill at least 30–35 m per shift, lagging behind the lava bush degasification wells is 50 m. Wells drilled in accordance with Passport options with the distance between the bushes 10 m. The length and diameter Well according to the passport, and the rotation angle and lift wells are not always observed due to the availability of the gain and anchors pickup. Sealing wells at 2–3 m, so work well short–lived.
A southern lava unit 10 – the concentration of methane in the gas mixture at the output 30 % drilling drilling rig is available in 80 GBH1/89/12 bars, chisels 114 mm. Drilling rig in a satisfactory condition, that allows you to drill at least 30–35 m per shift. Wells are drilled according to Passport options with the distance between the bushes 10 m. The length and diameter Well according to the passport. Sealing of wells in 2–3 m, so work Well short – lived.
A northern lava unit 10 – the concentration of methane in the gas mixture Output 30 %, well drilling is drilling machine GBH1/89/12 in the presence of 80 bars, chisels 114 mm. Drilling rig in a satisfactory a state that allows drilling at least 30–35 m per shift, lag from Lava bush degasification wells is 30 m. Wells are drilled according to the parameters of the passport with the distance between the bushes 10 m. Sealing wells at 2–3 m, so work well short–lived. Wells drilled in the area of increased inflow of water from the decontamination boreholes and wells installed dehumidifiers in a timely manner.
3.4 Analysis of the
Prospects
development of the degassing system of the mine
Combined degassing scheme
On the analysis of methane heavy–working areas of the mine is set strict dependence of the methane, which is 10 m3/min 100% methane for every 1,000 tons daily average production. At the moment, means of ventilation kaptiruetsya largest proportion of methane – is due to the lack of effectiveness of decontamination, which at once–through ventilation schemes should be impounded 60–70 % total methane. Given the limited bandwidth the ability of the ventilation openings due to sewage network section of excavation systems and regulated air velocity SDS, maximum possible flow of fresh air to ventilate excavation site can range from 3000 to 3500 m3/min. According to amount of air can be diluted to safe concentrations of 1 % 30–35 m3/min pure methane (converted to 4000 t/sut raw coal). The result is that in the case of exceeding the working areas of concentration maximum allowable methane concentration and significantly overstated air flow rate in the treatment workings.
The use of direct – flow scheme ventilation can almost rule out the presence of hazardous concentrations of methane-air mixture in the conjugation of lava from the drifts, however, in the ventilation drift outside of lava at 30–40 meters formed local accumulations of methane in place contact strip and the rigid guard roof (fig. 4).
In order to increase the load on the gas – oil ratio and the creation of safe working conditions in coal mining with the load must be used to 8000–15000t/sut combined drainage scheme, which provides for degassing reservoir – satellite host rocks, further developed space motion stope and nadbermovoy of ventilatory output. For this targets for the development of the outgoing air stream are laid two degassing pipeline, in addition to capturing the methane from the drilled degasification wells behind the working face (line number 1 – Degassing) provides additional degassing gob and ventilation of the production nadbermovoy (Line number 2-out space), to reduce background methane in the outgoing stream of the excavation site.
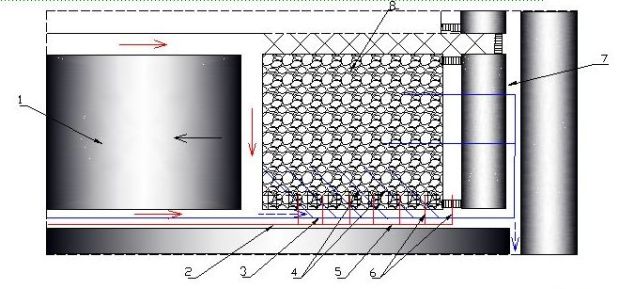
Figure 4. A combined scheme of degassing
As seen from the figure:
- Developed layer;
- Generation of outgoing stream of air;
- Degassing becoming;
- Degassing wells;
- Becoming degassing goaf;
- Barrier wells;
- Development, supported by of lava;
- Goaf.
To provide the required used well casing leak sealer decontamination with foam collar (89 mm GDPM. and 95 mm.). Wells drilled Kustov way (two – three wells in the bush). The distance between the bushes of 10–20 m.
Surface decontamination degassing developed
Spaces of moving longwall faces with holes drilled with surface [4]. This method of degassing is used as an additional way to gob degasification with degassing of the underground workings. Since 2005, the mine produced construction boreholes from the surface to reduce gassing at the excavation areas (fig. 5). Gassing of these wells began approaching stope. The maximum rate observed during their underworking and ranges from 5 to 10 m3/min. In the active period of operation of such well of them stands out from 800 to 1500 thousand m3 of methane. Content methane in the gas mixture seems to 90–98 %. It was established experimentally that the efficiency of drainage excavation area can be further increased to 20 %, which implies increased load on the gas factor. The application of this measure in combined with a degassing wells drilled from the workings eliminates restrictions on the gas factor loadings on the working face.
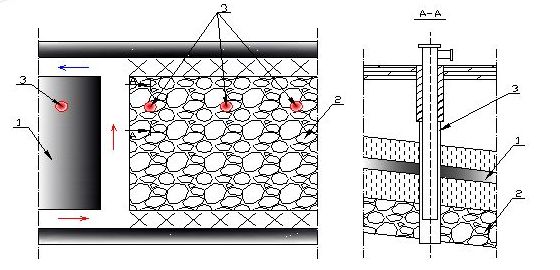
Figure 5. The scheme of surface degassing
Where:
- Developed layer;
- Goaf;
- Degasification wells;
- Undermined strata.
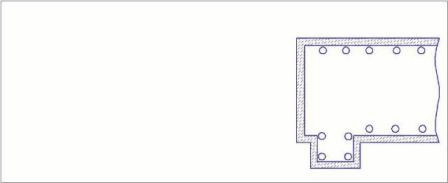
Figure 6. The scheme of degassing of coal during the generation of the array (number of frames – 6 cycles – 7, size 127 KB)
Conclusions
Methane is a gas, which, according to experts, create a greenhouse effect, holding heat in the Earth's atmosphere. The degree to which one or the other greenhouse dioxide at trapping heat, measured relative to the thermal effect of carbon dioxide. It is believed that the ability to retain heat in the atmosphere over a hundred years Methane is 21 times greater than carbon dioxide carbon. Methane and other greenhouse gases are emitted into the atmosphere as as a result of natural processes, and as a result of human activities, such as coal mining [6].
Extraction and utilization of methane from coal deposits in Ukraine will significantly reduce the amount of greenhouse gas emitted to the atmosphere of coal mines.
Based on the findings will be developed by a complex of measures on the use of methane industry and the economy.
results can be
successfully used as a mine Krasnoarmeyskaya
–
Zapadnaya
,
and
other companies in the sector.
In writing this essay Master's work is not yet complete. Final completion: December In 2012. The full text of the and materials on the topic can be obtained from the author or his head after that date.
List
of sources
- Дегазация угольных шахт. Требования к способам и схемам дегазации СОУ 10.00174088–2004.
- Руководство по дегазации угольных шахт. – М.:Недра.1975, 189 с.
- Дегазация угольных пластов и вмещающих пород при проведении горных выработок. Временное руководство и типовой проект. – М.:ГОСГОРТЕХИЗДАТ. 1962 г., С.38–40.
- Дегазация выработанных пространств (Обзор). – М. 1976, 56 с.
- Инструкция по расчету количества воздуха необходимого для проветривания действующих угольных шахт. – М.:Недра, 1975 г.
- Ушаков
К.З., Бурчаков А.С.,
Пучков Л.А.,Медведев И.И.
Аэрология горных предприятий
: Учебник для ВУЗов, – М.: Недра, 1987.–421 с. - Порцевский А.К. Безопасность жизнедеятельности при горных и горноразведочных работах. Часть 1. – М. 2005, 80 с.