Abstract
The content of the abstract
- Introduction
- 1. Theme urgency
- 2. Goal and tasks of the research
- 3. Results of the study
- Conclusion
- References
Introduction
In the coal mines for the delivery of minerals from the slaughtering, as well as for the transportation of his on precast drift, apex, slopes and inclined trunks are now widely used belt conveyors. Distance transport of belt conveyors up to several kilometers, and the route can have a different scheme, which allows to adapt to the conditions of production and terrain [1].
Mineral resources are transported to the processing plant or to a loading points in the railroad cars, or a warehouse. To implement these operations, as well as inland transport conveyors concentrators are also widely used. It should be noted that the belt conveyors are an integral part of the tunneling machines and loaders. Operating conditions of belt conveyors are very diverse: from hot climates to work outdoors in sub-zero temperatures [2].
1. Theme urgency
Master's thesis is devoted to the urgent now in Ukrainian mines problem of increasing the reliability of conveyor transport by reducing the non-uniformity of the incoming cargo on the main conveyor.
The main feature of the conveyor transport as a control object is a high non-uniformity of cargo caused by the fact that the conveyor line at its technological purpose is the transport facilities serving the cleaning and preparation slaughtering. A technological break in work arrangements (emergency stop lava, periodic changes in the rate of movement along the longwall shearer, etc.) are the cause of uneven traffic. The uneven load leads to a waste of drive power (at min power) as well as excessive wear on the pulling unit and reduce the decrease the reliability of the engine (when reloading).
There are two ways to reduce the non-uniformity of cargo: speed control of the conveyor drive motor and the application of interim storage bins. However, the use of variable frequency drive has a number of controversial issues: the range of adjustable frequency drives for conveyors is limited and does not lead to energy savings, with decreasing speed is necessary to provide the operating torque of the motor shaft to the same long-term work in the low-frequency mode will force cooling a motor and inverter. In addition, this approach does not allows for the alignment of freight for the next the chain conveyor, which requires controlled drives for each conveyor.
Thus, from the point of view of energy efficiency in the mine preferably to regulate the incoming flow of cargo on the conveyor, bringing it closer to the nominal value, thereby preventing idling and increasing the efficiency of the conveyor system. This can be achieved through the use of accumulating hoppers (silos, feeders), volume, and performance that will define and align the flow of cargo to after bunker conveyor line.
2. Goal and tasks of the research
The aim of the study is to improve the efficiency and reliability of conveyor transport by reducing the load imbalance of main conveyors.
Automation object is a branched conveyor line (district and main) with bins intermediate-batchers.
Be sure to highlight the following key objectives of the study:
1. Analysis of the process of conveyor transport as an automation object.
2. A review well-known technical solutions for automation process of conveyor transport.
3. Rationale and development of automation systems branched conveyor line.
3. Results of the study
Conveying – a technological process of moving rock masses with using conveyors in underground and open-pit mining. In a broad sense – the complex, which includes conveyors with ancillary equipment (such as bunkers, feeders, etc.), technical means of production management activities, as well as maintenance and repair [10].
A belt conveyor consists of the following main elements: the actual conveyor belts, drive, standing up with the rollers, the loading and tensioning device. Also on the conveyor belt mounted catcher, cleaning mechanisms, mechanisms for weighing cargo, etc [3].
The mechanization of loading and unloading - is one of the most important reserves for increasing the economic efficiency of manufacturing operations with bulk materials. The diversity bulk goods, which differ in properties and function, causes the use of different bins, hopper devices, boot devices, stabilizers expiration, feeders, etc. All of them belong to the system of the transport mechanism for the comprehensive mechanization of cargo [4].
Automation object is a branched conveyor line (district and main) with bins intermediate-batchers. Each district conveyor line consists of a conveyor belt type 1L-80 with a length of 300 m and a width of 800 mm tape. District conveyor line is designed for the transportation of rocks coming from the mining site directly into the feed hopper of accumulating. Intermediate-batcher, in turn, applies the type of MM-50 50 m3. Main conveyor line consists of a conveyor belt type 1L-100 with a length of 700 m and a width of 1000 mm tape. Main conveyor line is designed for the transportation of rocks coming out of the hopper-feeder directly to the loading point.
In Figure 1 shows the process flow diagram stabilize cargo branched conveyor line with bins intermediate-batchers.
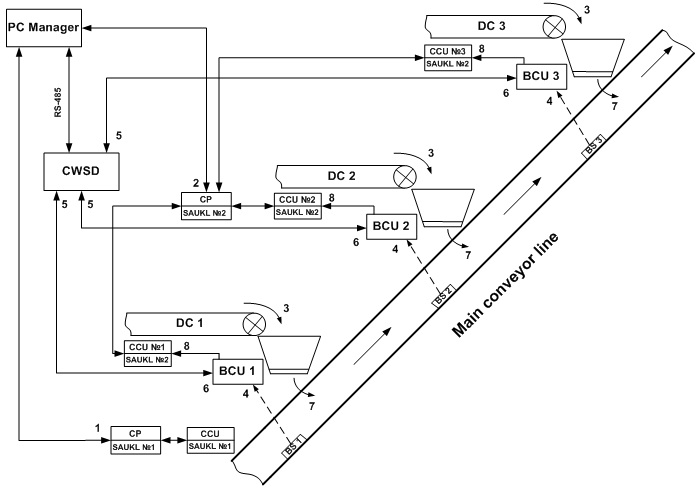
Figure 1 - Flow diagram stabilize cargo branched conveyor line with bins intermediate-batchers
In Figure 1, the following designations:
CWSD – Coordinating the work of the stabilization device;
DC – District conveyor line;
SAUKL – Automated control system of conveyor belts;
CP – Control panel;
CCU – Conveyor control unit;
BCU – Bunker control unit;
BS – belt scales.
In Figure 2 shows the animation, through which you can observe the process of stabilizing the cargo conveyor line in action.
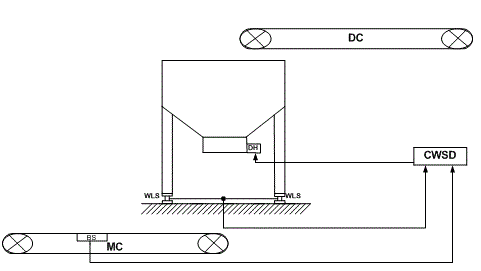
Figure 2 - Process of stabilizing the cargo conveyor line
(animation: 10 frames, 7 cycles of repeating, 41 kilobytes)
In Figure 2, the following designations:
CWSD – Coordinating the work of the stabilization device;
DC – District conveyor line;
MC – Main conveyor line;
WLS – Weighing hopper level sensors;
DH – Drive gate hopper;
BS – belt scales.
In Figure 3 shows the structural scheme of automation object which shows the interrelation of a coordinating device of stabilization the cargo and buncer control unit.
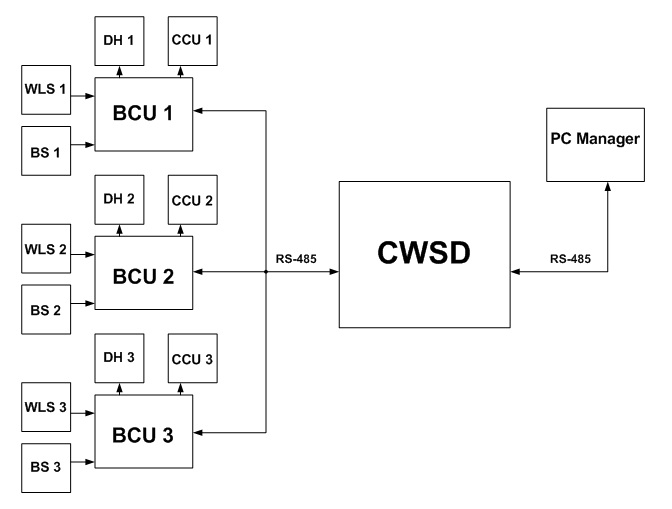
Figure 3 - Structural scheme of automation object
In Figure 3, the following designations:
CWSD – Coordinating the work of the stabilization device;
PC Manager – PC Manager of the mine;
BCU – Bunker control unit;
CCU – Conveyor control unit;
DH – Drive gate hopper;
WLS – Weighing hopper level sensors;
BS – belt scales;
RS-485 – Interface.
Conclusion
The study analyzed the process of conveyor transport as an automation object, formulated goal and objectives of the study. Produced substantiation and development of system automation branched conveyor line, namely designed technological scheme of stabilization cargo conveyor lines branched with bins intermediate-batchers, developed structural scheme of automation object which shows the interrelation of a coordinating device of stabilization the cargo and buncer control unit.
Thus, from the point of view of energy efficiency in the mine preferably to regulate the incoming flow of cargo on the conveyor, bringing it closer to the nominal value, thereby preventing idling and increasing the efficiency of the conveyor system. This can be achieved through the use of accumulating hoppers (silos, feeders), volume, and performance that will define and align the flow of cargo to after bunker conveyor line. And, in this regard, having developed this coordinating device of stabilization the cargo, we can achieve the above-mentioned increase of energy efficiency.
Thus, through the application of the developed device, you can achieve not only high economic impact, but also significantly improve the working conditions, increase security, and most importantly – the increase of technical and economic performance of the enterprise as a whole, which leads to an increase in the standard of living of workers of this enterprise.
In writing this essay master's work is not yet complete. Final completion: December 2013. Full text of the work and materials on the topic can be obtained from the author or his manager after that date.
References
- Конвейер ленточный [Электронный ресурс]. – Режим доступа: http://emmkursk.ru/transportnoe-oborudovanie/konvejer-lentochnyj.
- Малиновский А.К. Автоматизированный электропривод машин и установок шахт и рудников / А.К. Малиновский. – М.: Недра, 1987. – 280 с.
- Толпежников Л.И. Автоматическое управление процессами шахт и рудников / Л.И. Толпежников. – М.: Недра, 1985. – 352 с.
- Гаврилов П.Д., Гимельштейн Л.Я., Медведев А.Е. Автоматизация производственных процессов: Учебник для ВУЗов / П.Д. Гаврилов, Л.Я. Гимельштейн, А.Е. Медведев. – М.: Недра, 1985. – 216 c.
- Батицкий В.А., Куроедов В.И., Рыжков А.А. Автоматизация производственных процессов и АСУ ТП в горной промышленности: Учебник для техникумов / В.А. Батицкий, В.И. Куроедов, А.А. Рыжков. – 2-е изд., перераб. и доп. – М.: Недра, 1991. – 303 c.
- Кузнецов Б.А., Ренгевич А.А., Шорин В.Г. Транспорт на горных предприятиях / Б.А. Кузнецов, А.А. Ренгевич, В.Г. Шорин. – 2-е изд., перераб. и доп. – М.: Недра, 1976. – 552 c.
- Мельникова А.П. Исследование и разработка системы автоматического управления разветвленной конвейерной линией / А.П. Мельникова // Автореф. магистерской работы [Электронный ресурс]. – Режим доступа: Портал магистров ДонНТУ, Факультет ФЭМА, 2009 г.
- Авласенко Ю.Г., Ковалевский М.М. Автоматизация шахтных установок / Ю.Г. Авласенко, М.М. Ковалевский // Государственное издательство технической литературы УССР. – Киев, 1958. – 296 c.
- Рачков Е.В. Совершенствование системы пуска ленточного конвейера с грузом / Е.В. Рачков // Речной транспорт. – 2011. – № 5 (53). – С. 63.
- Гливанский А.А. Методы управления шахтным подземным конвейерным транспортом / А.А. Гливанский, И.П. Коновалова, В.М. Ротенберг, Е.К. Травкин // Средства и аппаратура горной автоматики для угольных предприятий, Труды института № 29. – Москва, 1978. – С. 77-95.