Реферат по теме выпускной работы
Содержание
- Введение
- 1. Актуальность темы
- 2. Цель и задачи исследования
- 3. Результаты исследования
- 3.1 Анализ процесса конвейерного транспорта как объекта автоматизации
- 3.2 Критический обзор известных технических решений по автоматизации процесса конвейерного транспорта
- 3.3 Обоснование и разработка системы автоматизации разветвленной конвейерной линии
- Выводы
- Список источников
Введение
В угольных шахтах и рудниках для доставки полезного ископаемого из забоя, а также для транспортирования его по сборным штрекам, бремсбергам, уклонам и наклонным стволам в настоящее время широко применяются ленточные конвейеры. Расстояние транспортирования ленточными конвейерами достигает нескольких километров, а их трасса может иметь различную схему, что позволяет приспосабливать конвейеры к условиям производства и местности [1].
На поверхности шахт и рудников полезное ископаемое транспортируется либо на обогатительную фабрику, либо к погрузочному пункту в железнодорожные вагоны, либо на склад. Для реализации таких операций, а также для внутреннего транспорта на обогатительных фабриках ленточные конвейеры также нашли широкое применение. Следует отметить, что ленточные конвейеры служат неотъемлемой частью проходческих комбайнов и погрузочных машин. Условия эксплуатации ленточных конвейеров отличаются большим разнообразием: от жаркого климата до работы на открытом воздухе при минусовых температурах [2].
1. Актуальность темы
Магистерская работа посвящена актуальной в настоящее время на шахтах Украины проблеме повышения надежности конвейерного транспорта за счет уменьшения неравномерности поступающего на магистральный конвейер грузопотока.
Основной особенностью конвейерного транспорта как объекта управления является высокая неравномерность грузопотока, вызванная тем, что конвейерная линия по своему технологическому назначению является транспортным объектом, обслуживающим очистной и подготовительный забой. А технологические паузы в работе механизмов (аварийная остановка лавы, периодические изменения скорости перемещения комбайна вдоль лавы и т.д.) являются причиной неравномерного грузопотока. Неравномерность поступления груза ведет к нерациональному использованию мощности привода (при недогрузке), а также чрезмерному износу тягового органа и снижению надежности АД (при перегрузе).
Существует два способа уменьшения неравномерности грузопотока: регулирование частоты вращения приводного электродвигателя конвейера и применение промежуточных накопительных бункеров. Однако использование частотно-регулируемого привода имеет ряд спорных моментов: диапазон регулируемой частоты для конвейеров ограничен и не приводит к экономии энергии; при уменьшении частоты вращения надо обеспечить рабочий момент на валу двигателя, к тому же длительная работа в режиме пониженных частот приведет к принудительному охлаждению, как двигателя, так и преобразователя. Помимо этого данный подход не позволяет обеспечить выравнивание грузопотока для последующих конвейеров в цепи, что требует применения регулируемых приводов на каждом конвейере.
Таким образом, с точки зрения повышения энергоэффективности, в шахте целесообразно регулировать не производительность конвейера, а поступающий на него грузопоток, приближая его к номинальному значению, тем самым предотвращая режим холостого хода и увеличивая КПД конвейерной установки. Это может быть достигнуто за счет применения аккумулирующих бункеров (бункеров-питателей), объем, и производительность которых будут определять, и выравнивать грузопоток на забункерной конвейерной линии.
2. Цель и задачи исследования
Целью исследования является повышение эффективности и надежности конвейерного транспорта за счет уменьшения неравномерности загрузки магистральных конвейеров.
Объект автоматизации представляет собой разветвленную конвейерную линию (участковые и магистральную) с аккумулирующими промежуточными бункерами-питателями.
Необходимо выделить следующие основные задачи исследования:
- Анализ процесса конвейерного транспорта как объекта автоматизации.
- Критический обзор известных технических решений по автоматизации процесса конвейерного транспорта.
- Обоснование и разработка системы автоматизации разветвленной конвейерной линии.
3. Результаты исследования
3.1 Анализ процесса конвейерного транспорта как объекта автоматизации
Конвейерный транспорт — технологический процесс перемещения горных масс с помощью конвейеров на подземных и открытых разработках месторождений полезных ископаемых. В широком смысле — комплекс, объединяющий конвейеры и вспомогательное оборудование (например, бункеры, питатели и др.), технические средства управления производством работ, а также технического обслуживания и ремонта [10].
Ленточный конвейер состоит из следующих основных элементов: собственно конвейерная лента, привод, став с роликоопорами, загрузочное и натяжное устройство. Также на конвейеры устанавливаются ловители ленты, чистящие механизмы, механизмы для взвешивания груза и т.д. [3].
Ленточный конвейер (рисунок 1) условно можно разбить на три основные части: головную, среднюю и хвостовую. В качестве несущего (транспортирующего) и тягового органа применяются резинотканевые ленты с гладкой поверхностью [1].
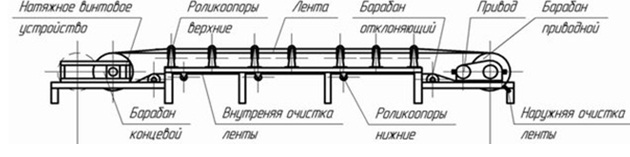
Рисунок 1 - Схема ленточного конвейера
Механизация погрузочно-разгрузочных работ – это один из важнейших резервов повышения экономической эффективности технологических операций с сыпучими грузами. Многообразие насыпных грузов, различающихся по свойствам и назначению, обуславливает применение различных бункеров, бункерных устройств, загрузочных приспособлений, стабилизаторов истечения, питателей и т.д. Все они относятся к системе транспортирующих механизмов для комплексной механизации грузопотока [4].
Бункер – это емкость для хранения и самотечной разгрузки сыпучих грузов, имеющая малую глубину по сравнению с размерами в плане (рисунок 2) [4].
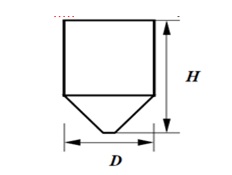
Рисунок 2 - Схема бункера
Питателями называют механизмы, при помощи которых осуществляется равномерная регулируемая подача сыпучих грузов из емкостей в технологическую линию (непосредственно или через промежуточные емкости).
Питатель кроме равномерной регулируемой подачи сыпучих грузов из емкостей может являться также запорным устройством и выполнять роль бункерного затвора, но он отличается от них возможностью более тонкого регулирования потока сыпучего груза [9].
Важнейшие требования, предъявляемые к питателям, – это равномерность подачи груза и возможность регулирования производительности устройства. В некоторых производственных процессах питатели используют как простые, надежные и дешевые объемные дозаторы небольшой точности [5].
Исходя из того, что масса единицы объема сыпучих грузов в некоторых технологических процессах может изменяться в широких пределах (иногда до 15%), в случае необходимости высокой точности дозирования, объемные питатели оснащают автоматическими устройствами и приспособлениями.
В настоящее время почти все конвейерные линии на шахтах автоматизированы. Развитие автоматизации шахтных конвейерных линий на протяжении длительного периода определялось необходимостью снижения трудоемкости управления и повышения безопасности эксплуатации конвейерного транспорта. В связи с этим широкое распространение получило автоматизированное управление конвейерной линией, техническая сущность которого заключается в централизации управления процессами пуска-останова конвейеров, а также в обеспечении автоматической защиты от развития аварии при возникновении аварийных ситуаций [10].
3.2 Критический обзор известных технических решений по автоматизации процесса конвейерного транспорта
В горной промышленности существует достаточно большое количество способов автоматизации конвейеров и конвейерных линий. Основные способы автоматизации приведены ниже:
Аппаратура САУКЛ [6] предназначена для автоматизации шахтного и рудничного конвейерного транспорта. Многолетний опыт эксплуатации подтвердил высокую надежность, удобство в эксплуатации, функциональную полноту и соответствие всем требованиям безопасности эксплуатации горношахтного оборудования, в том числе на шахтах и рудниках опасных по газу и пыли.
Система автоматизированного управления конвейерными линиями (САУКЛ) предназначена для:
- централизованного автоматизированного управления и контроля работы разветвленными и неразветвленными конвейерными линиями, состоящие из ленточных конвейеров, предназначенных для транспортирования груза и перевозки людей, с числом конвейеров управляемых через один комплект АПУ и АЛС до 60 единиц, и неограниченным числом маршрутов;
- централизованного или местного автоматизированного управления и контроля работы отдельными конвейерами, входящими или не входящими в состав конвейерной линии;
- телеуправления и контроля состояния сопутствующим вспомогательным оборудованием;
- автоматической регистрации и сохранения информации о работе конвейеров и сопутствующего оборудования, командах управления и настройках, защитных отключениях и блокировках.
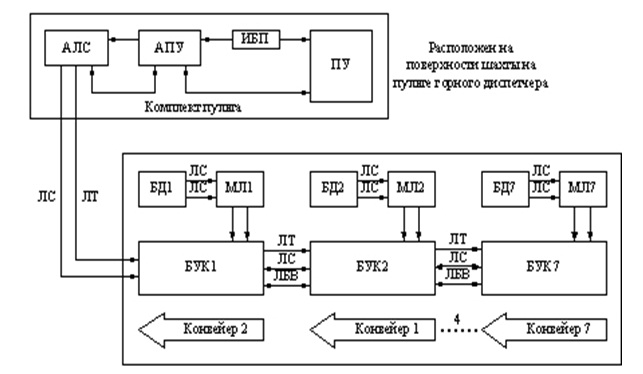
Рисунок 3 - Структурная схема системы САУКЛ
Система САУКЛ состоит из комплекта пульта управления, который располагается в диспетчерской шахты, и комплектов аппаратных средств устанавливаемых на конвейерах.
Система автоматики APD1 [7] (Чехия) предназначена для программного регулирования, управления и мониторинга хода конвейерной линии, в том числе дробилки и струга, или же других машин на шахте и на поверхности.
Она дает возможность передачи данных и разговора из шахты на поверхность, визуализации процесса отработки, громкой разговорной связи, сигнализации и передачи предупредительного тона при разгоне машин в забое или на штреках. Систему APD1 можно использовать во всех шахтных пространствах опасных взрывом метана и угольной пыли, за исключением пространств с высокой опасностью взрыва метана.
Изделие исполняет технические требования к оборудованию, предназначенному для использования в среде опасной взрывом согласно Директиве 94/9/ЕС (NV 176/1997 Свода).
Система автоматики APD1 представляет собой микропроцессорную систему управления, предназначенную для управления забоем, или же конвейерными линиями в шахтах или на поверхности. Вся система имеется в искробезопасном исполнении. Она исполняет технические требования к оборудованию, предназначенному для использования в среде опасной взрывом. Изделие можно использовать в угольных шахтах опасных по газу (метану) и угольной пыли, в соответствии с Техническим описанием и инструкцией по эксплуатации и Правилами безопасности в угольных шахтах РД 05-94-95.
Основные функции системы:
- программное управление, параметризация и управление конвейерными линиями;
- аварийный останов (блокирование) машин;
- разговорная связь вдоль линий;
- сигнализация, включая передачу предостерегающего сигнала до разгона;
- мониторинг хода конвейерных линий;
- визуализация всего процесса разработки;
- несложная диагностика всей системы и локализация отказа из поста управления на поверхности или в шахте;
- доступ из Ithernet и Internet.
Мониторинг хода конвейерной линии
Все сведения о ходе конвейера (состояние датчиков, состояние выводов, сведения о месте блокировки и ее причине и т.п.) являются доступными на каждой Станции конвейера SD1. В диагностическом режиме можно на 2-строковом буквенно-цифровом LCD дисплее Станции конвейера изобразить все важные напряжения датчиков, батарейного источника, проводов линии и т.п. Одинаковым образом можно получить информацию о состояниях других станций конвейеров, включенных в линии.
Между Станцией центральной и Станцией конвейеров проходит постоянная передача сведений, и сведения, таким образом, являются доступными также на управляющем компьютере Станции центральной (обычный компьютер стандарта IBM ПК 486 и выше). Если компьютер подключен в заводскую сеть, то эти данные являются доступными для всех других участников сети. Все рабочие изменения хранятся в файле, так что они доступны для позднейшей оценки.
Структурная схема системы автоматизации APD1 представлена на рисунке 4.
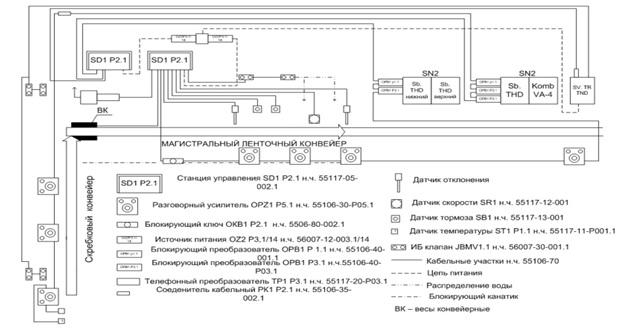
Рисунок 4 - Структурная схема системы автоматизации APD1
Комплекс автоматизированного управления конвейерами АУК.2М [8] предназначен для автоматизированного управления и контроля работы стационарных и полустационарных неразветвленных конвейерных линий с числом конвейеров до 10, а также для местного управления отдельным конвейером, входящим и не входящим в состав линии. Комплекс предназначен для эксплуатации в шахтах, в том числе опасных по газу или пыли, при температуре окружающего воздуха от минус 10 до 40°С относительная влажность до 100% при температуре 35 °С.
Комплекс обеспечивает выполнение следующих функции управления:
- автоматический последовательный запуск конвейеров, включенных в линию, в порядке, обратном направлению движения грузопотока;
- автоматизированное управление конвейерной линией с кнопок пульта управления;
- автоматизированное управление конвейерной линией с кнопок прибора-указателя;
- автоматизированное управление конвейерной линией по сигналам телемеханики;
- запуск части конвейерной линии;
- запуск конвейерной линии без остановки работающих конвейеров;
- автоматическое управление конвейерной линией по сигналам технологических датчиков приемных устройств без применения дополнительных аппаратов контроля;
- прекращение запуска конвейерной линии с любого блока управления;
- возможность работы конвейерной линии в режиме автоматического отключения ее при отсутствии грузопотока;
- управление любым конвейером в линии при отсутствии питания на пульте управления;
- управление любым конвейером линии с кнопок блока управления в ремонтно-наладочном режиме;
- управление любым конвейером линии с выносного кнопочного поста в ремонтно-наладочном режиме;
- управление концевым (подлавным) конвейером из-под лавы;
- управление одиночным конвейером без применения пульта управления;
- управление двухприводным конвейером со следующими программами работы пускателей: управление одним пускателем; работа по выбору одного из двух пускателей; управление двумя пускателями с их одновременным включением и отключением; работа двух пускателей, включение которых сдвинуто по времени, а отключение - одновременное;
- дозапуск линии ответвления с пульта управления магистральной конвейерной линии;
- выдача команды на управление вспомогательными механизмами без применения дополнительных аппаратов.
Из перечисленных способов автоматизации за основополагающую мы выбрали аппаратуру САУКЛ, т.к. данная аппаратура наилучшим образом подходит для автоматизации исследуемого объекта.
3.3 Обоснование и разработка системы автоматизации разветвленной конвейерной линии
Рассматриваемый объект автоматизации представляет собой разветвленную конвейерную линию (участковые и магистральную) с аккумулирующими промежуточными бункерами-питателями. Каждая участковая конвейерная линия состоит из одного ленточного конвейера типа 1Л-80 с протяженностью 300 м и шириной ленты 800 мм. Участковая конвейерная линия предназначена для транспортирования породы, поступающей от добычного участка, непосредственно в аккумулирующий бункер-питатель. Бункер-питатель, в свою очередь, применяется типа ШМ-50 объемом 50 м3. Магистральная конвейерная линия состоит из одного ленточного конвейера типа 1Л-100 с протяженностью 700 м и шириной ленты 1000 мм. Магистральная конвейерная линия предназначена для транспортирования породы, поступающей из бункера-питателя, непосредственно к погрузочному пункту.
На рисунке 5 приведена технологическая схема стабилизации грузопотока разветвленной конвейерной линии с помощью промежуточных емкостей бункеров-питателей.
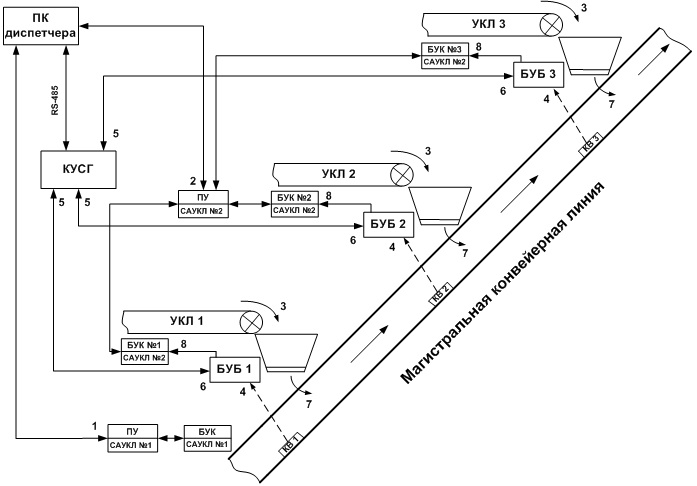
Рисунок 5 - Технологическая схема стабилизации грузопотока разветвленной конвейерной линии с помощью промежуточных емкостей бункеров-питателей
На рисунке 5 приняты следующие обозначения:
КУСГ – Координирующее устройство стабилизации грузопотока; УКЛ – Участковая конвейерная линия; САУКЛ - Система автоматизированного управления конвейерными линиями; ПУ – Пульт управления; БУК – Блок управления конвейером; БУБ – Блок управления бункером; КВ – Конвейерные весы.
Принцип работы автоматизированной системы заключается в следующем: с ПК диспетчера шахты подается сигнал 1 на пульт управления (ПУ) системы САУКЛ №1 на включение магистральной конвейерной линии. Затем аналогичным образом подается сигнал 2 на ПУ системы САУКЛ №2 на включение участковой конвейерной линии. Затем горная масса 3, поступающая от добычного участка, с помощью участковой конвейерной линии транспортируется в аккумулирующий бункер-питатель. Под опорами бункера-питателя БП устанавливают тензометрические преобразователи ВДУ, которые преобразуют силу тяжести бункера с заполняющим его материалом в электрический сигнал. Этот сигнал (информация о состоянии загрузки бункера) поступает на блок управления бункером, где данный сигнал анализируется, а также анализируется сигнал 4, поступающий с конвейерных весов забункерного магистрального конвейера о состоянии загрузки ленты; затем информация от каждого блока управления бункером 5 поступает на координирующее устройство стабилизации грузопотока, где анализируется и затем с КУСГ выдается команда 6 на блок управления соответствующим бункером на открытие/закрытие шибера Ш этого бункера. Далее стабилизированный грузопоток 7 с помощью магистральной конвейерной линии транспортируется к погрузочному пункту. Следует отметить, что в случае, если уровень угля в бункере достиг аварийного, а шибер бункера полностью открыт, то с блока управления этого бункера поступает сигнал 8 на блок управления БУК соответствующего участкового конвейера на отключение участковой конвейерной линии с последующим оповещением диспетчера шахты об аварии.
На рисунке 6 приведена анимация, благодаря которой можно наблюдать процесс стабилизации грузопотока конвейерной линии в действии.
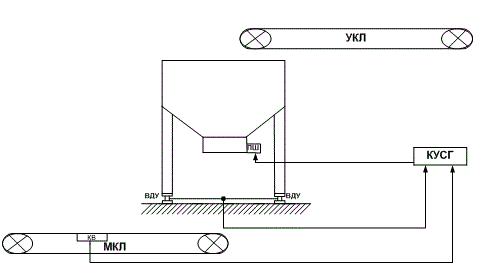
Рисунок 6 - Процесс стабилизации грузопотока конвейерной линии
(анимация: 10 кадров, 7 циклов повторения, 44 килобайта)
На рисунке 6 приняты следующие обозначения:
КУСГ – Координирующее устройство стабилизации грузопотока; УКЛ – Участковая конвейерная линия; МКЛ – Магистральная конвейерная линия; ВДУ – Весовые датчики уровня бункера; ПШ – Привод шибера бункера; КВ – Конвейерные весы.
На рисунке 7 приведена структурная схема автоматизации объекта, которая отображает взаимосвязь самого координирующего устройства стабилизации грузопотока и блоков управления бункерами.
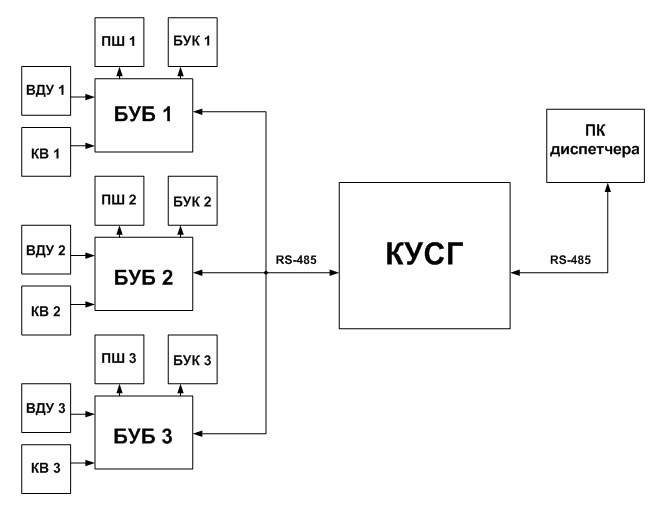
Рисунок 7 - Структурная схема автоматизации объекта
На рисунке 7 приняты следующие обозначения:
КУСГ – Координирующее устройство стабилизации грузопотока; ПК диспетчера – Персональный компьютер диспетчера шахты; БУБ – Блок управления бункером; БУК – Блок управления конвейером; ПШ – Привод шибера бункера; ВДУ – Весовые датчики уровня бункера; КВ – Конвейерные весы; RS-485 – Интерфейс.
Выводы
В результате исследования произведен анализ технологического процесса конвейерного транспорта как объекта автоматизации, сформулирована цель и задачи исследования. Сделан критический обзор известных технических решений по автоматизации процесса конвейерного транспорта, обосновано дальнейшее направление автоматизации исследуемого процесса. Произведено обоснование и разработка системы автоматизации разветвленной конвейерной линии, а именно: разработана технологическая схема стабилизации грузопотока разветвленной конвейерной линии с помощью промежуточных емкостей бункеров-питателей, разработана структурная схема автоматизации объекта, которая отображает взаимосвязь самого координирующего устройства стабилизации грузопотока и блоков управления бункерами.
Так как с точки зрения повышения энергоэффективности в шахте целесообразно регулировать не производительность конвейера, а поступающий на него грузопоток, приближая его к номинальному значению, тем самым предотвращая режим холостого хода и увеличивая КПД конвейерной установки, применяются аккумулирующие бункеры (бункеры-питатели), объем, и производительность которых определяют, и выравнивают грузопоток на забункерной конвейерной линии. И, в связи с этим, разработав данное координирующее устройство стабилизации грузопотока, мы наилучшим образом сможем добиться повышения вышеуказанной энергоэффективности.
Таким образом, за счет применения разрабатываемого устройства, можно достичь не только высокого экономического эффекта, но и существенно улучшить условия труда рабочих, повысить безопасность, а самое главное – повышаются технико-экономические показатели предприятия в целом, что приводит к повышению уровня жизни работников этого предприятия.
При написании данного реферата магистерская работа еще не завершена. Окончательное завершение: декабрь 2013 года. Полный текст работы и материалы по теме могут быть получены у автора или его руководителя после указанной даты.
Список источников
- Конвейер ленточный [Электронный ресурс]. – Режим доступа: http://emmkursk.ru/transportnoe-oborudovanie/konvejer-lentochnyj.
- Малиновский А.К. Автоматизированный электропривод машин и установок шахт и рудников / А.К. Малиновский. – М.: Недра, 1987. – 280 с.
- Толпежников Л.И. Автоматическое управление процессами шахт и рудников / Л.И. Толпежников. – М.: Недра, 1985. – 352 с.
- Гаврилов П.Д., Гимельштейн Л.Я., Медведев А.Е. Автоматизация производственных процессов: Учебник для ВУЗов / П.Д. Гаврилов, Л.Я. Гимельштейн, А.Е. Медведев. – М.: Недра, 1985. – 216 c.
- Батицкий В.А., Куроедов В.И., Рыжков А.А. Автоматизация производственных процессов и АСУ ТП в горной промышленности: Учебник для техникумов / В.А. Батицкий, В.И. Куроедов, А.А. Рыжков. – 2-е изд., перераб. и доп. – М.: Недра, 1991. – 303 c.
- Кузнецов Б.А., Ренгевич А.А., Шорин В.Г. Транспорт на горных предприятиях / Б.А. Кузнецов, А.А. Ренгевич, В.Г. Шорин. – 2-е изд., перераб. и доп. – М.: Недра, 1976. – 552 c.
- Мельникова А.П. Исследование и разработка системы автоматического управления разветвленной конвейерной линией / А.П. Мельникова // Автореф. магистерской работы [Электронный ресурс]. – Режим доступа: Портал магистров ДонНТУ, Факультет ФЭМА, 2009 г.
- Авласенко Ю.Г., Ковалевский М.М. Автоматизация шахтных установок / Ю.Г. Авласенко, М.М. Ковалевский // Государственное издательство технической литературы УССР. – Киев, 1958. – 296 c.
- Рачков Е.В. Совершенствование системы пуска ленточного конвейера с грузом / Е.В. Рачков // Речной транспорт. – 2011. – № 5 (53). – С. 63.
- Гливанский А.А. Методы управления шахтным подземным конвейерным транспортом / А.А. Гливанский, И.П. Коновалова, В.М. Ротенберг, Е.К. Травкин // Средства и аппаратура горной автоматики для угольных предприятий, Труды института № 29. – Москва, 1978. – С. 77-95.