Реферат за темою випускної роботи
Зміст
- Вступ
- 1. Актуальність теми
- 2. Мета і завдання дослідження
- 3. Результати дослідження
- 3.1 Аналіз процесу конвеєрного транспорту як об'єкта автоматизації
- 3.2 Критичний огляд відомих технічних рішень з автоматизації процесу конвеєрного транспорту
- 3.3 Обґрунтування та розробка системи автоматизації розгалуженої конвеєрної лінії
- Висновки
- Перелік посилань
Вступ
У вугільних шахтах і рудниках для доставки корисної копалини з вибою, а також для транспортування її по збірних штреках, бремсбергами, ухилам і похилих стовбурах в даний час широко застосовуються стрічкові конвеєри. Відстань транспортування стрічковими конвеєрами досягає декількох кілометрів, а їх траса може мати різну схему, що дозволяє пристосовувати конвеєри до умов виробництва і місцевості [1].
На поверхні шахт і копалень корисна копалина транспортується або на збагачувальну фабрику, або до вантажного пункту в залізничні вагони, або на склад. Для реалізації таких операцій, а також для внутрішнього транспорту на збагачувальних фабриках стрічкові конвеєри також знайшли широке застосування. Слід зазначити, що стрічкові конвейєри служать невід'ємною частиною прохідницьких комбайнів і навантажувальних машин. Умови експлуатації стрічкових конвеєрів відрізняються великою різноманітністю: від жаркого клімату до роботи на відкритому повітрі при мінусових температурах [2].
1. Актуальність теми
Магістерська робота присвячена актуальній в даний час на шахтах України проблемі підвищення надійності конвеєрного транспорту за рахунок зменшення нерівномірності вантажопотоку, який надходить на магістральний конвеєр.
Основною особливістю конвеєрного транспорту як об'єкта управління є висока нерівномірність вантажопотоку, викликана тим, що конвеєрна лінія за своїм технологічним призначенням є транспортним об'єктом, обслуговуючим очисний і підготовчий забій. А технологічні паузи в роботі механізмів (аварійна зупинка лави, періодичні зміни швидкості переміщення комбайна вздовж лави і т.д.) є причиною нерівномірного вантажопотоку. Нерівномірність надходження вантажу веде до нераціонального використання потужності приводу (при недовантаженні), а також надмірного зносу тягового органу і зниження надійності АД (при перевантаженні).
Існує два способи зменшення нерівномірності вантажопотоку: регулювання частоти обертання приводного електродвигуна конвеєра і застосування проміжних накопичувальних бункерів. Проте використання частотно-регульованого приводу має ряд спірних моментів: діапазон регульованої частоти для конвеєрів обмежений і не призводить до економії енергії; при зменшенні частоти обертання треба забезпечити робочий момент на валу двигуна, до того ж тривала робота в режимі знижених частот призведе до примусового охолодження, як двигуна, так і перетворювача. Крім цього даний підхід не дозволяє забезпечити вирівнювання вантажопотоку для наступних конвеєрів в ланцюзі, що вимагає застосування регульованих приводів на кожному конвеєрі.
Таким чином, з точки зору підвищення енергоефективності, в шахті доцільно регулювати не продуктивність конвеєра, а вантажопотік, що надходить на нього, наближаючи його до номінального значення, тим самим запобігаючи режиму холостого ходу і збільшуючи ККД конвеєрної установки. Це може бути досягнуто за рахунок застосування акумулюючих бункерів (бункерів-живильників), обсяг і продуктивність яких будуть визначати і вирівнювати вантажопотік на забункерній конвеєрній лінії.
2. Мета і завдання дослідження
Метою дослідження є підвищення ефективності та надійності конвеєрного транспорту за рахунок зменшення нерівномірності завантаження магістральних конвеєрів.
Об'єкт автоматизації являє собою розгалужену конвеєрну лінію (дільничні та магістральну) з акумулюючими проміжними бункерами-живильниками.
Необхідно виділити наступні основні завдання дослідження:
- Аналіз процесу конвеєрного транспорту як об'єкта автоматизації.
- Критичний огляд відомих технічних рішень з автоматизації процесу конвеєрного транспорту.
- Обґрунтування та розробка системи автоматизації розгалуженої конвеєрної лінії.
3. Результати дослідження
3.1 Аналіз процесу конвеєрного транспорту як об'єкта автоматизації
Конвеєрний транспорт – технологічний процес переміщення гірничих мас за допомогою конвеєрів на підземних і відкритих розробках родовищ корисних копалин. У широкому сенсі – комплекс, який об'єднує конвеєри і допоміжне обладнання (наприклад, бункери, живильники тощо), технічні засоби управління виробництвом робіт, а також технічного обслуговування і ремонту [10].
Стрічковий конвеєр складається з наступних основних елементів: власне конвеєрна стрічка, привід, ставши з роликоопорами, завантажувальний і натяжний пристрій. Також на конвеєри встановлюються уловлювачі стрічки, чистячі механізми, механізми для зважування вантажу тощо [3].
Стрічковий конвеєр (рисунок 1) умовно можна розбити на три основні частини: головну, середню і хвостову. В якості несучого (транспортуючого) і тягового органу застосовуються гумовотканинні стрічки з гладкою поверхнею [1].
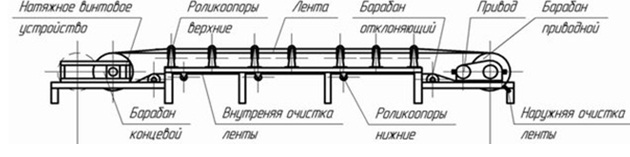
Рисунок 1 - Схема стрічкового конвеєра
Механізація навантажувально-розвантажувальних робіт – це один з найважливіших резервів підвищення економічної ефективності технологічних операцій з сипучими вантажами. Різноманіття насипних вантажів, що розрізняються за властивостями і призначенням, зумовлює застосування різних бункерів, бункерних пристроїв, завантажувальних пристроїв, стабілізаторів закінчення, живильників і т.д. Всі вони відносяться до системи транспортуючих механізмів для комплексної механізації вантажопотоку [4].
Бункер – це ємність для зберігання і самопливного розвантаження сипучих вантажів, що має малу глибину в порівнянні з розмірами в плані (рисунок 2) [4].
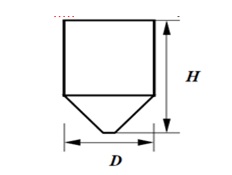
Рисунок 2 - Схема бункера
Живильниками називають механізми, за допомогою яких здійснюється рівномірна регульована подача сипучих вантажів з ємностей в технологічну лінію (безпосередньо або через проміжні ємності).
Живильник крім рівномірної регульованої подачі сипучих вантажів з ємностей може бути також запірним пристроєм і виконувати роль бункерного затвора, але він відрізняється від них можливістю більш тонкого регулювання потоку сипучого вантажу [9].
Найважливіші вимоги, пропоновані до живильників, – це рівномірність подачі вантажу і можливість регулювання продуктивності пристрою. У деяких виробничих процесах живильники використовують як прості, надійні і дешеві об'ємні дозатори слабкої точності [5].
Виходячи з того, що маса одиниці об'єму сипучих вантажів в деяких технологічних процесах може змінюватися в широких межах (іноді до 15%), у разі необхідності високої точності дозування, об'ємні живильники оснащують автоматичними пристроями і пристосуваннями.
В даний час майже всі конвеєрні лінії на шахтах автоматизовані. Розвиток автоматизації шахтних конвеєрних ліній протягом тривалого періоду визначався необхідністю зниження трудомісткості управління та підвищення безпеки експлуатації конвеєрного транспорту. У зв'язку з цим широкого поширення набуло автоматизоване управління конвеєрної лінією, технічна сутність якого полягає в централізації управління процесами пуску-зупинки конвеєрів, а також у забезпеченні автоматичного захисту від розвитку аварії при виникненні аварійних ситуацій [10].
3.2 Критичний огляд відомих технічних рішень з автоматизації процесу конвеєрного транспорту
У гірничій промисловості існує досить велика кількість способів автоматизації конвеєрів і конвеєрних ліній. Основні способи автоматизації наведені нижче:
Апаратура САУКЛ [6] призначена для автоматизації шахтного та рудникового конвеєрного транспорту. Багаторічний досвід експлуатації підтвердив високу надійність, зручність в експлуатації, функціональну повноту і відповідність всім вимогам безпеки експлуатації гірничошахтного обладнання, в тому числі на шахтах і рудниках небезпечних по газу і пилу.
Система автоматизованого управління конвеєрними лініями (САУКЛ) призначена для:
- централізованого автоматизованого управління і контролю роботи розгалуженими і нерозгалуженими конвеєрними лініями, що складаються зі стрічкових конвеєрів, призначених для транспортування вантажу і перевезення людей, з числом конвеєрів керованих через один комплект АПУ і АЛС до 60 одиниць, і необмеженим числом маршрутів;
- централізованого або місцевого автоматизованого управління і контролю роботи окремими конвеєрами, що входять або не входять до складу конвеєрної лінії;
- телеуправління та контролю стану супутнім допоміжним обладнанням;
- автоматичної реєстрації та збереження інформації про роботу конвеєрів і супутнього обладнання, командах управління та налаштуваннях, захисних відключеннях і блокіровках.
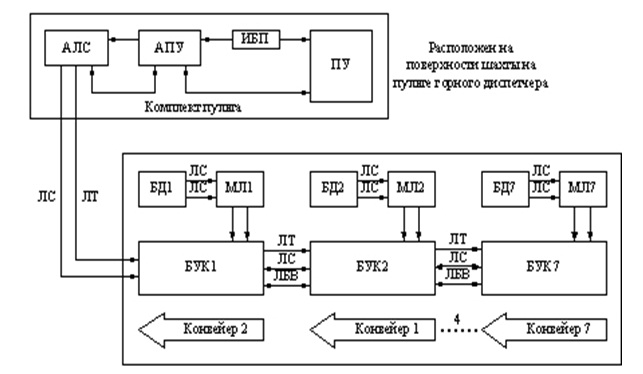
Рисунок 3 - Структурна схема системи САУКЛ
Система САУКЛ складається з комплекту пульта управління, який розташовується в диспетчерській шахти, і комплектів апаратних засобів, які встановлюються на конвеєрах.
Система автоматики APD1 [7] (Чехія) призначена для програмного регулювання, управління та моніторингу ходу конвеєрної лінії, в тому числі дробарки і струга, або ж інших машин на шахті і на поверхні.
Вона дає можливість передачі даних і розмови з шахти на поверхню, візуалізації процесу відпрацювання, гучного розмовного зв'язку, сигналізації та передачі попереджувального тону при розгоні машин в забої або на штреках. Систему APD1 можна використовувати у всіх шахтних просторах небезпечних вибухом метану і вугільного пилу, за винятком просторів з високою небезпекою вибуху метану.
Виріб виконує технічні вимоги до обладнання, призначеного для використання в середовищі, небезпечному вибухом відповідно до Директиви 94/9/ЄС (NV 176/1997 Зводу).
Система автоматики APD1 являє собою мікропроцесорну систему управління, призначену для управління забоєм, або ж конвеєрними лініями в шахтах або на поверхні. Вся система мається в іскробезпечному виконанні. Вона виконує технічні вимоги до обладнання, призначеного для використання в середовищі, небезпечному вибухом. Виріб можна використовувати у вугільних шахтах небезпечних по газу (метану) і вугільному пилу, згідно з Технічним описом та інструкцією по експлуатації та Правилами безпеки у вугільних шахтах РД 05-94-95.
Основні функції системи:
- програмне управління, параметризація і керування конвеєрними лініями;
- аварійний останов (блокування) машин;
- розмовний зв'язок уздовж ліній;
- сигналізація, включаючи передачу застережливого сигналу до розгону;
- моніторинг ходу конвеєрних ліній;
- візуалізація всього процесу розробки;
- нескладна діагностика всієї системи і локалізація відмови з поста управління на поверхні або в шахті;
- доступ з Ithernet і Internet.
Моніторинг ходу конвеєрної лінії
Всі відомості про хід конвеєра (стан датчиків, стан виводів, відомості про місце блокування і її причини і т.п.) є доступними на кожній Станції конвеєра SD1. У діагностичному режимі можна на 2-строковому буквено-цифровому LCD дисплеї Станції конвеєра зобразити всі важливі напруги датчиків, батарейного джерела, проводів лінії і т.п. Однаковим чином можна отримати інформацію про стани інших станцій конвеєрів, включених в лінії.
Між Станцією центральної та Станцією конвеєрів проходить постійна передача відомостей, і відомості, таким чином, є доступними також на керуючому комп'ютері Станції центральної (звичайний комп'ютер стандарту IBM ПК 486 і вище). Якщо комп'ютер підключений в заводську мережу, то ці дані є доступними для всіх інших учасників мережі. Всі робочі зміни зберігаються у файлі, так що вони доступні для пізнішої оцінки.
Структурна схема системи автоматизації APD1 представлена на рисунку 4.
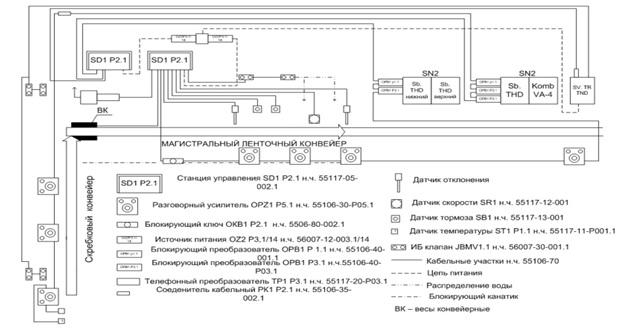
Рисунок 4 - Структурна схема системи автоматизації APD1
Комплекс автоматизованого управління конвеєрами АУК.2М [8] призначений для автоматизованого управління і контролю роботи стаціонарних і напівстаціонарних нерозгалужених конвеєрних ліній з числом конвеєрів до 10, а також для місцевого управління окремими конвеєрами, що входять і не входять до складу лінії. Комплекс призначений для експлуатації в шахтах, у тому числі небезпечних по газу або пилу, при температурі навколишнього повітря від мінус 10 до 40 ° С з відносною вологістю до 100% при температурі 35 ° С.
Комплекс забезпечує виконання наступних функції управління:
- автоматичний послідовний запуск конвеєрів, включених в лінію, в порядку, зворотному напрямку руху вантажопотоку;
- автоматизоване управління конвеєрної лінією з кнопок пульта управління;
- автоматизоване управління конвеєрної лінією з кнопок приладу-покажчика;
- автоматизоване управління конвеєрної лінією за сигналами телемеханіки;
- запуск частини конвеєрної лінії;
- запуск конвеєрної лінії без зупинки працюючих конвеєрів;
- автоматичне керування конвеєрною лінією за сигналами технологічних датчиків приймальних пристроїв без застосування додаткових апаратів контролю;
- припинення запуску конвеєрної лінії з будь-якого блоку управління;
- можливість роботи конвеєрної лінії в режимі автоматичного відключення її за відсутності вантажопотоку;
- управління будь-яким конвеєром в лінії при відсутності живлення на пульті управління;
- управління будь-яким конвеєром лінії з кнопок блоку керування в ремонтно-налагоджувальному режимі;
- управління будь-яким конвеєром лінії з виносного кнопкового поста в ремонтно-налагоджувальному режимі;
- управління кінцевим (підлавний) конвеєром під лави;
- управління одиночним конвеєром без застосування пульта управління;
- управління двухприводним конвеєром з такими програмами роботи пускачів: управління одним пускачем; робота з вибору одного з двох пускачів; управління двома пускачами з їх одночасним включенням і відключенням; робота двох пускачів, включення яких зрушено за часом, а відключення - одночасне;
- дозапуск лінії відгалуження з пульта управління магістральної конвеєрної лінії;
- видача команди на управління допоміжними механізмами без застосування додаткових апаратів.
З перерахованих способів автоматизації за основоположну ми вибрали апаратуру САУКЛ, тому що дана апаратура найкращим чином підходить для автоматизації досліджуваного об'єкта.
3.3 Обґрунтування та розробка системи автоматизації розгалуженої конвеєрної лінії
Розглянутий об'єкт автоматизації являє собою розгалужену конвеєрну лінію (дільничні та магістральну) з акумулюючими проміжними бункерами-живильниками. Кожна дільнична конвеєрна лінія складається з одного стрічкового конвеєра типу 1Л-80 з довжиною 300 м і шириною стрічки 800 мм. Дільнична конвеєрна лінія призначена для транспортування породи, що надходить від видобувної дільниці, безпосередньо в акумулюючий бункер-живильник. Бункер-живильник, у свою чергу, застосовується типу ШМ-50 об'ємом 50 м3. Магістральна конвеєрна лінія складається з одного стрічкового конвеєра типу 1Л-100 з довжиною 700 м і шириною стрічки 1000 мм. Магістральна конвеєрна лінія призначена для транспортування породи, що надходить з бункера-живильника, безпосередньо до навантажувального пункту.
На рисунку 5 наведена технологічна схема стабілізації вантажопотоку розгалуженої конвеєрної лінії за допомогою проміжних ємностей бункерів-живильників.
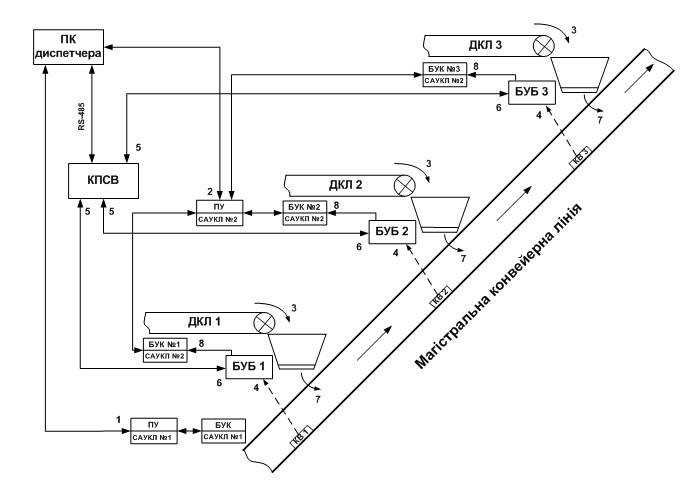
Рисунок 5 - Технологічна схема стабілізації вантажопотоку розгалуженої конвеєрної лінії за допомогою проміжних ємностей бункерів-живильників
На рисунку 5 прийняті наступні позначення:
КПСВ – Координуючий пристрій стабілізації вантажопотоку; ДКЛ – Дільнична конвеєрна лінія; САУКЛ – Система автоматизованого управління конвеєрними лініями; ПУ – Пульт управління; БУК – Блок управління конвеєром; БУБ – Блок управління бункером; КВ – Конвеєрні ваги.
Принцип роботи автоматизованої системи полягає в наступному: з ПК диспетчера шахти подається сигнал 1 на пульт управління (ПУ) системи САУКЛ № 1 на включення магістральної конвеєрної лінії. Потім аналогічним чином подається сигнал 2 на ПУ системи САУКЛ № 2 на включення дільничної конвеєрної лінії. Потім гірнича маса 3, яка надходить від видобувної дільниці, за допомогою дільничної конвеєрної лінії транспортується в акумулюючий бункер-живильник. Під опорами бункера-живильника БЖ встановлюють тензометричні перетворювачі ВДР, які перетворять силу тяжіння бункера з заповнюючим його матеріалом в електричний сигнал. Цей сигнал (інформація про стан завантаження бункера) надходить на блок управління бункером, де даний сигнал аналізується, а також аналізується сигнал 4, який надходить з конвеєрних ваг забункерного магістрального конвеєра про стан завантаження стрічки; потім інформація від кожного блоку управління бункером 5 надходить на координуючий пристрій стабілізації вантажопотоку, де аналізується і потім з КПСВ видається команда 6 на блок управління відповідним бункером на відкриття / закриття шибера Ш цього бункера. Далі стабілізований вантажопотік 7 за допомогою магістральної конвеєрної лінії транспортується до навантажувального пункту. Слід зазначити, що у разі, якщо рівень вугілля в бункері досяг аварійного, а шибер бункера повністю відкритий, то з блоку управління цього бункера надходить сигнал 8 на блок управління БУК відповідного дільничного конвеєра на відключення дільничної конвеєрної лінії з подальшим сповіщенням диспетчера шахти про аварію.
На рисунку 6 наведена анімація, завдяки якій можна спостерігати процес стабілізації вантажопотоку конвеєрної лінії в дії.
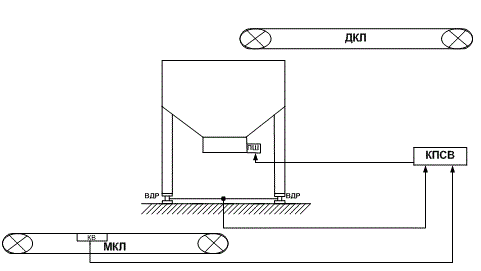
Рисунок 6 - Процес стабілізації вантажопотоку конвеєрної лінії
(анімація: 10 кадрів, 7 циклів повторення, 51 кілобайт)
На рисунку 6 прийняті наступні позначення:
КПСВ – Координуюча пристрій стабілізації вантажопотоку; ДКЛ – Дільнична конвеєрна лінія; МКЛ – Магістральна конвеєрна лінія; ВДР – Вагові датчики рівня бункера; ПШ – Привід шибера бункера; КВ – Конвеєрні ваги.
На рисунку 7 наведена структурна схема автоматизації об'єкта, яка відображає взаємозв'язок самого координуючого пристрою стабілізації вантажопотоку і блоків управління бункерами.
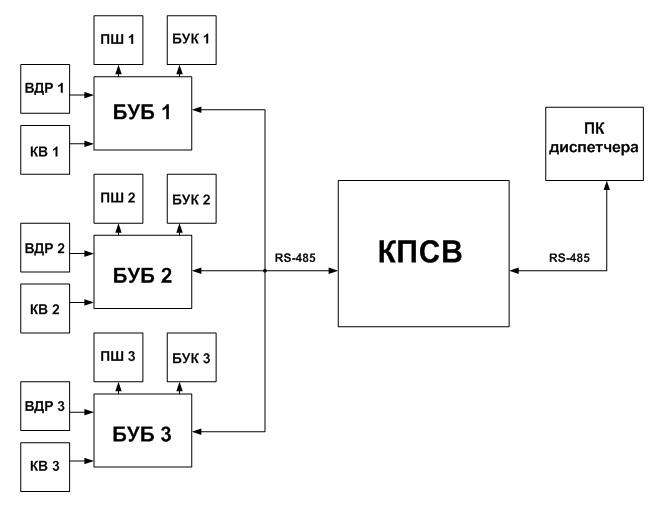
Рисунок 7 - Структурна схема автоматизації об'єкта
На рисунку 7 прийняті наступні позначення:
КПСВ – Координуючий пристрій стабілізації вантажопотоку; ПК диспетчера – Персональний комп'ютер диспетчера шахти; БУБ – Блок управління бункером; БУК – Блок управління конвеєром; ПШ – Привід шибера бункера; ВДР – Вагові датчики рівня бункера; КВ – Конвеєрні ваги; RS-485 – Інтерфейс.
Висновки
У результаті дослідження проведен аналіз технологічного процесу конвеєрного транспорту як об'єкта автоматизації, сформульована мета і задачі дослідження. Зроблено критичний огляд відомих технічних рішень з автоматизації процесу конвеєрного транспорту, обґрунтовано подальший напрямок автоматизації досліджуваного процесу. Вироблено обґрунтування та розробка системи автоматизації розгалуженої конвеєрної лінії, а саме: розроблена технологічна схема стабілізації вантажопотоку розгалуженої конвеєрної лінії за допомогою проміжних ємностей бункерів-живильників, розроблена структурна схема автоматизації об'єкта, яка відображає взаємозв'язок самого координуючого пристрою стабілізації вантажопотоку і блоків управління бункерами.
Так як з точки зору підвищення енергоефективності в шахті доцільно регулювати не продуктивність конвеєра, а вантажопотік, який надходить на нього, наближаючи його до номінального значення, тим самим запобігаючи режим холостого ходу і збільшуючи ККД конвеєрної установки, застосовуються акумулюючі бункери (бункери-живильники), обсяг, і продуктивність яких визначають, і вирівнюють вантажопотік на забункерной конвеєрної лінії. І, у зв'язку з цим, розробивши даний координуючий пристрій стабілізації вантажопотоку, ми найкращим чином зможемо домогтися підвищення вищевказаної енергоефективності.
Таким чином, за рахунок застосування розроблюваного пристрою, можна досягти не тільки високого економічного ефекту, але й істотно поліпшити умови праці робітників, підвищити безпеку, а найголовніше – підвищуються техніко-економічні показники підприємства в цілому, що призводить до підвищення рівня життя працівників цього підприємства.
При написанні даного реферату магістерська робота ще не завершена. Остаточне завершення: грудень 2013 року. Повний текст роботи та матеріали по темі можуть бути отримані у автора або його керівника після зазначеної дати.
Перелік посилань
- Конвейер ленточный [Электронный ресурс]. – Режим доступа: http://emmkursk.ru/transportnoe-oborudovanie/konvejer-lentochnyj.
- Малиновский А.К. Автоматизированный электропривод машин и установок шахт и рудников / А.К. Малиновский. – М.: Недра, 1987. – 280 с.
- Толпежников Л.И. Автоматическое управление процессами шахт и рудников / Л.И. Толпежников. – М.: Недра, 1985. – 352 с.
- Гаврилов П.Д., Гимельштейн Л.Я., Медведев А.Е. Автоматизация производственных процессов: Учебник для ВУЗов / П.Д. Гаврилов, Л.Я. Гимельштейн, А.Е. Медведев. – М.: Недра, 1985. – 216 c.
- Батицкий В.А., Куроедов В.И., Рыжков А.А. Автоматизация производственных процессов и АСУ ТП в горной промышленности: Учебник для техникумов / В.А. Батицкий, В.И. Куроедов, А.А. Рыжков. – 2-е изд., перераб. и доп. – М.: Недра, 1991. – 303 c.
- Кузнецов Б.А., Ренгевич А.А., Шорин В.Г. Транспорт на горных предприятиях / Б.А. Кузнецов, А.А. Ренгевич, В.Г. Шорин. – 2-е изд., перераб. и доп. – М.: Недра, 1976. – 552 c.
- Мельникова А.П. Исследование и разработка системы автоматического управления разветвленной конвейерной линией / А.П. Мельникова // Автореф. магистерской работы [Электронный ресурс]. – Режим доступа: Портал магистров ДонНТУ, Факультет ФЭМА, 2009 г.
- Авласенко Ю.Г., Ковалевский М.М. Автоматизация шахтных установок / Ю.Г. Авласенко, М.М. Ковалевский // Государственное издательство технической литературы УССР. – Киев, 1958. – 296 c.
- Рачков Е.В. Совершенствование системы пуска ленточного конвейера с грузом / Е.В. Рачков // Речной транспорт. – 2011. – № 5 (53). – С. 63.
- Гливанский А.А. Методы управления шахтным подземным конвейерным транспортом / А.А. Гливанский, И.П. Коновалова, В.М. Ротенберг, Е.К. Травкин // Средства и аппаратура горной автоматики для угольных предприятий, Труды института № 29. – Москва, 1978. – С. 77-95.