Реферат по теме выпускной работы
Содержание
- Введение
- 1. Актуальность темы
- 2. Цель и задачи исследований
- 3. Сравнение струговой и комбайновой технологий выемки угля
- 4. Обзор очистных комплексов для добычи угля в длинных забоях
- Выводы
- Список источников
Введение
Одним из направлений прогрессивного развития подземной угледобычи является повышение технологичности и полноты отработки запасов угля, обеспечивающих извлечение ранее списанных запасов как в участках, признанных нецелесообразными к выемке длинными очистными забоями, так и в целиках различного назначения. Реализация научно-технических разработок в этом направлении, а именно рациональное сочетание технологий отработки длинными и короткими очистными забоями - позволит продлить срок эксплуатации угольных шахт и максимально извлекать запасы, в том числе в сложных условиях как действующих, так и закрывающихся шахт. Основной причиной сокращения объемов добычи угля из тонких пластов стало отсутствие высокопроизводительной техники для их отработки, а при применении комбайновой отработки - крайне низкие нагрузки на очистной забой и высокая трудоемкость работ.
Причинами такого положения являются значительный износ основных фондов шахт и недостаточная технологичность подземной угледобычи, обусловленные чрезмерной ориентацией отрасли на комплексно-механизированную добычу угля (78,9% в 2006 г). Кроме того, выбытие мощностей угольных шахт превышает их ввод в 3-5 раз, значительно растет объем незавершенного строительства.
1. Актуальность темы
На шахтах Донбасса в настоящее время ведется отработка пластов наиболее удобной технологической мощности, для которых создана и серийно выпускается новая высокопроизводительная техника для очистных работ, проходки, транспорта. Запасы, сосредоточенные в тонких и маломощных пластах, как правило, остаются в недрах и не вынимаются. В настоящее время 70% запасов угля в Донбассе залегают в тонких и весьма тонких пластах.
Отказ от разработки пластов малой мощности приводит к увеличению глубины горных работ, нарушению порядка отработки свиты, а также быстрому истощению запасов более мощных пластов, для восполнения которых необходимы вложения больших средств для доразведки запасов, строительства новых предприятий, реконструкции или их технического перевооружения. При этом необходимо учитывать, что минеральные ресурсы имеют характерную особенность - они не восстанавливаются. Это приводит к тому, что запасы в мощных пластах иссякают и возможно наступление того момента, когда добыча угля начнет затухать и тогда возникает необходимость разработки мероприятий, целью которых является увеличение срока службы шахт.
Исходя из этого, разработка технических решений по подготовке и отработке тонких пластов является весьма актуальной проблемой, которая одновременно и весьма сложна, ввиду специфичности условий их разработки [1].
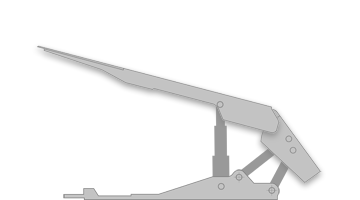
Рисунок 1 – Щитовая механизированная крепь (анимация: 9 кадров, 5 циклов повторения, 70,5 килобайт).
2. Цель и задачи исследований
Необходимой предпосылкой успешного проведения концентрации очистных работ являеться обеспечение кратного роста производительности очистного оборудования на основе повышения технического уровня механизированных крепей и комплексов(повышение удельного веса щитовых крепей и их несущей способности, увеличение шага установки, ширины и шага передвижки секций крепи), технического уровня очистных комбайнов(увеличение единичной мощности электродвигателей и установленной мощности привода, ширины захвата, скорости подачи и тяговых усилий, совершенствование механизмов подачи, применение одношнековых комбайнов для коротких лав), технического уровня струговых установок(повышение основных параметров установок, их надежности, точности регулирования струга при работе на пластах с невыдержанной гипсометрией).
По состоянию на 1.01.12 г. на шахтах Украины эксплуатировались 240 очистных забоев, из которых 166 – комплексно-механизированных (КМЗ). Средняя нагрузка на очистной забой составила 770 т/сут, на КМЗ – 1041 т/сут. В тонких пологих и наклонных пластах мощностью менее 1.2 м работали 129 очистных забоев, из которых 106 КМЗ. Средняя нагрузка на очистной забой в тонких пластах составила 795 т/сут, на КМЗ – 940 т/сут. Две трети очистных забоев эксплуатируются в условиях с весьма неустойчивыми и малоустойчивыми непосредственными кровлями. Поэтому создание высокоэффективной очистной техники для отработки тонких пологих пластов является самой приоритетной из задач, стоящих перед научно-исследовательскими и проектными организациями Украины[2].
3. Сравнение струговой и комбайновой технологий выемки угля
Существовали различные подходы приведения обеих технологий к общему знаменателю, при этом в большинстве случаев отсутствовал комплексный подход. Чаще всего сопоставлялись технические параметры комбайнов и стругов, иногда рассматривалась технология, однако, примеры целостного анализа практически невозможно найти в литературе. Тем не менее, всестороннее сопоставление двух различных технологий имеет смысл только при условии комплексного подхода, учитывающего все важнейшие технические, эксплуатационные и экономические факторы (рис. 3)
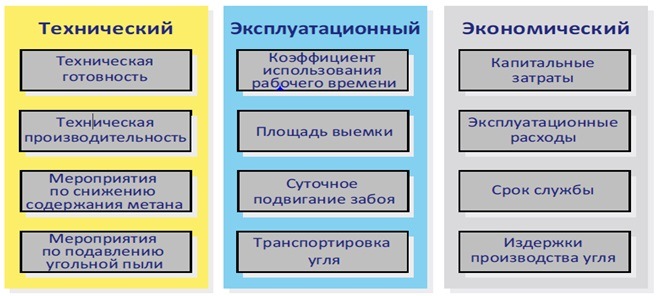
Рисунок 3. Уровни сравнения комбайновой и струговой технологий
Очистные комбайны применяются, как правило, на пластах мощностью от 1,5 до 6,0 м. В прошлом были многочисленные попытки эффективного использования комбайнов на пластах мощностью менее 1,5 м. Большая часть таких попыток окончилась неудачно, как с технической, так и экономической точки зрения. Относительно низкая установленная мощность, сложность манипулирования в тесном пространстве и низкое качество погрузки отбитой горной массы – вот основные причины. Во многих случаях комбайн ведет выемку на высоту, превышающую мощность пласта, захватывая породы кровли или почвы, в результате чего увеличивается содержание породы в угле и повышаются издержки производства.ользование особо мощных высокопроизводительных комбайнов (рис. 2) предполагает переход с системы электроснабжения напряжением 660 В на напряжение 1140, 2300, 4160 В (например, комбайны серии "Электра", немецкой фирмы DBT) и в дальнейшем на 6-10 кВ.
При этом в зависимости от типоразмера и комплектации вес комбайнов изменяется от 3–5 т (для тонких пластов) до 30–50 т - для выемки угля из пластов средней мощности и до 75-100т - для мощных пластов.
Модульная компоновка современных комбайнов и наличие одной основной несущей рамы, к которой быстроразъемными соединениями крепятся все блоки комбайна, обеспечивают быструю "сборку-разборку" комбайна, поузловую замену при ремонтах, исключение необходимости ремонта в шахтных условиях, возможность работы с двумя или с одним приводом резания и подачи. Все это приводит к повышению надежности работы комбайнов и снижению расходов на их обслуживание и ремонт.
Очистные комбайны оснащаются системами ручного непосредственного управления (используются при наладке комбайнов и тестировании режимов их работы), системами дистанционного радиоуправления (с носимого пульта), программного автоматизированного управления при больших скоростях подачи комбайна, превышающих среднюю скорость перемещения машиниста.
Для отработки тонких пологих пластов «Донгипроуглемаш» разработал ряд очистных комбайнов для широкого диапазона горно-геологических условий - УКД200–250, УКД200-400, УКД200-500, УКД400 и КА200.
Комбайн УКД200-250, предназначенный для выемки пластов мощностью 0.85-1.3 м, оснащен центрально расположенным вдоль забоя двигателем режущих частей мощностью 200–250 кВт. В 2009-2011 гг. разработана конструкторская документация очистных комбайнов УКД200-400 и УКД200-500. Новая компоновка двигателей в этих моделях позволила значительно повысить энерговооруженность комбайнов, уменьшить их "жесткую" базу и улучшить "вписываемость" в гипсометрию пласта.
Комбайн УКД200-500 впервые в истории отечественного машиностроения оснащен симметричными редукторами режущей части.
В 2011 г. завершена работа по созданию очистного комбайна с бесцепной электрической системой подачи УКД400, позволяющего эффективно производить выемку в тонких пологих и наклонных пластах мощностью 0.85-1.6 м с рабочей скоростью до 10 м/мин[3].
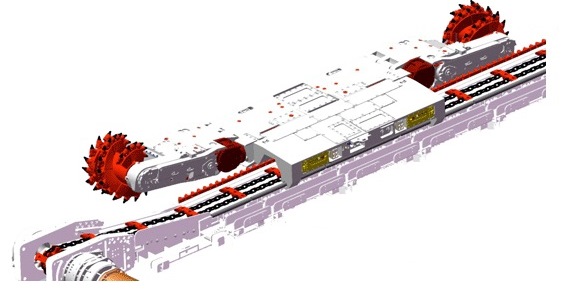
Комбайн очистной для тонких пластов УКД 400
Струговые установки применяются для работы на пластах мощностью от 0,6 до 2,3 м, хотя в Германии струговые установки используются и на пластах мощностью до
3 м. На пластах мощностью менее 1,0 м применяются струги с опорной подконвейерной плитой, а на пластах мощностью более 1,0 м – струги скользящего типа. Несмотря на небольшую собственную высоту, струговые установки обеспечивают выемку угля точно по гипсометрии пласта без необходимости присечки прилегающих пород. Пласты с изменяющейся мощностью не представляют каких-либо проблем для струговых установок, если в кровле пласта залегает породный прослоек или верхний слой угля можно обрушить при помощи перекрытия крепи.
Необходимо отметить, что при высокой скорости движения струга для эффективной работы комплекса лава должна иметь значительную длину для сокращения весомости времени на разгон и торможение струга при выемке каждой стружки. С учетом этих операций в лаве длиной 400 м струг снимает одну стружку в течение 3 минут. Энергоемкость выемки при испытаниях составляла 0,72 кВт?ч/т, а проектная – от 0,5 кВт?ч/т до 0,83 кВт?ч/т, т. е. расчеты показали, что при работе в сложных условиях эксплуатации даже наиболее современный мощный струговый комплекс обеспечивает выемку угля с энергозатратами, более высокими, чем при комбайновой выемке.[4].
Наиболее реальным путем решения задачи высокоэффективной разработки тонких пластов является создание совершенной техники, использующей традиционный механический способ разрушения полезного ископаемого, и в первую очередь – фронтальных струговых агрегатов, позволяющих не только осуществить высокопроизводительную, поточную добычу угля, но и решить такую важнейшую социально-экономическую задачу, как вывод людей из очистного забоя[5].
4. Обзор очистных комплексов для добычи угля в длинных забоях
Создание и внедрение ОМК в практику подземной добычи угля сыграло исключительную роль в техническом перевооружении угольной промышленности, послужило мощным стимулом развития шахт, привело к повышению технического уровня всех звеньев технологии подземной добычи. Успешное применение ОМК в угольной промышленности способствовало расширению области их применения. Очистные механизированные комплексы стали использоваться на калийных рудниках и при добыче целого ряда других полезных ископаемых преимущественно с пластовой структурой залегания.
При переходе на комплексную механизацию очистных работ в принципе были решены проблемы создания гидрофицированных передвижных секций крепи, забойных передвижных скребковых конвейеров, узкозахватных комбайнов, стругов. Кинематические связи перечисленных механизмов и оборудования обеспечивают согласованное перемещение в циклическом режиме всего комплекса машин и оборудования вслед за подвиганием очистного забоя по мере отработки выемочного столба.
Струговые ОМК имеют преимущество перед комбайновыми комплексами при отработке тонких пластов без прослоев породы и консолидированных твердых включений. Комбайновые комплексы применяются для механизации очистных работ при добыче угля из пластов средней мощности и мощных, а также из тонких пластов со сложной структурой и гипсометрией залегания, где использование стругов нецелесообразно.
Согласованное функционирование всех механизмов и оборудования ОМК в основных и вспомогательных режимах обеспечивается интегрированными системами электроснабжения, освещения, сигнализации и управления, гидросистемой, обеспечивающей силовые перемещения секций крепи и конвейера с выемочной машиной, гидросистемой пылеподавления, системами контроля состояния воздуха в выработках, в частности количественного содержания газа метана, телефонной и громкоговорящей связи. Основным требованием к перечисленным оборудованию и системам является обеспечение длительной устойчивой высокопроизводительной и безопасной для людей работы ОМК в изменяющихся горно-геологических условиях по мере отработки выемочного столба. Использование резервирования как метода повышения надежности в очистных механизированных комплексах ограничено, поэтому каждый из элементов, входящих в ОМК, должен быть высоконадежным и взрыво-, искробезопасным. При разработке, изготовлении и эксплуатации ОМК исполнители должны руководствоваться действующими правилами безопасности в угольных шахтах (сланцевых шахтах, рудниках), нормативами по безопасности забойных машин и комплексов и рядом других отраслевых нормативных документов, методик и указаний.
Эффективность работы комплексно-механизированных очистных забоев оценивают системой абсолютных и удельных технических и технико-экономических показателей, обеспечивающих сравнительную оценку как самого оборудования, так и эффективность его использования. Однако горно-геологические и горно-технологические условия эксплуатации очистных механизированных комплексов различаются столь значительно, что показатели эффективности работы комплексно-механизированных очистных забоев, даже при отработке одного выемочного столба, трудно сравнивать. Наличие слабых, а также тяжелых, трудно управляемых, склонных к периодическим блоковым обрушениям кровель, слабых обводненных почв, волнистой гипсометрии, нарушений в залегании пластов, повышенной газоносности – вот далеко не полный перечень горно-геологических факторов, усложняющих эксплуатацию очистных механизированных комплексов при добыче угля в длинных очистных забоях[6].
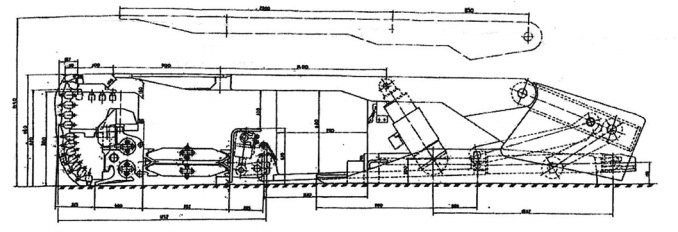
Комплекс КМ 137 со струговой установкой типа «Компактхобель»
5. Технико-экономический анализ современных механизированных крепей
Основной вклад в создание научных основ взаимодействия механизированных крепей с боковыми
породами пластов внесли специалисты ВНИМИ,
ИГД им. А.А. Скочинского, "Гипроуглемаша",
ПНИУИ, ДонУГИ и "Крангормаша".
Следует отметить, что на первом этапе создания
отечественных механизированных крепей для шахт
Донбасса при практически полном отсутствии обоснованных рекомендаций по сопротивлению, "Гипроуглемаш" с участием ВНИМИ (А.А. Орлов) в
1950-е годы заложил при разработке крепи для агрегата А2 сопротивление 700 кН/м2 при средней вынимаемой мощности пласта 1,0 м.
На эффективность работы механизированной крепи влияет ресурс ее работы. Ресурс отечественных крепей типа М138, М142, М144 составлял 8 тыс. циклов передвижки секций при шести годах службы и 10 тыс. циклов при восьми годах службы, что практически полностью удовлетворяло требования по их применению в комплексно механизированных забоях КМЗ на шахтах РФ до 2000–2002 гг.
Ресурс крепей фирм Германии составлял до 30 тыс. циклов передвижки секций при 12 годах службы.
Шаг установки секций крепи также влияет на эффективность работы. До последнего времени в крепях с двухрядными секциями преимущественно использовали шаг установки секций 1,5 м. При применении крепей с однорядными секциями в условиях тяжелых кровель стали использовать шаг 1,75 м для обеспечения прохода между стойками.
Разработка "Гипроуглемашем" блочно модульной крепи М151 для выемки тонких пластов с шагом установки секций 1,0, 2,0 и 3,0 м показала, что увеличение шага установки секций приводит к увеличению ее ме. таллоемкости на 5…7 %, что с учетом снижения затрат на систему управления секцией практически не влияет на первоначальную стоимость крепи в целом. Эти работы показали, что переход на крепи блочно модульной конструкции с шагом установки секций 2,0 и 3,0 м при модуле соответственно равном по шагу установке 1,0 и 1,5 м для благоприятных условий по состоянию боковых пород пласта обоснован[7].
Выводы
Для того чтобы сравнить эффективность работы комбайновой и струговой лав на угольных пластах средней мощности, потребовалось проанализировать следующие технические, эксплуатационные и экономические факторы.
A. Комбайны характеризуются более эффективной передачей энергии, но более низкой эффективностью выемки, чем струги. Вместе с тем величина удельной энергии, необходимой для выемки единицы массы угля в аналогичных условиях, сопоставима для обоих типов машин.
B. В диапазоне мощности пласта от 0,7 до 2,3 м современные струговые системы обладают более высокой удельной мощностью, т.е. установленной мощностью на единицу высоты лавы, чем комбайны.
С. Издержки производства зависят помимо производительности лавы от капитальных и текущих затрат. В целом можно утверждать, что при отработке пластов мощностью от 1,5 до 2,3 м капитальные затраты для комбайновых лав сопоставимы с капитальными затратами струговых лав, но эксплуатационные расходы по струговым лавам меньше, чем по комбайновым. Следовательно, издержки производства в струговых лавах меньше, чем в комбайновых.
Список источников
- Бурчаков А.С. Технология подземной разработки пластовых месторождений полезных ископаемых / А.С. Бурчаков, Н.К. Гринько, Д.В. Дорохов. - М.: Недра, 1983. - 487с.
- Козловчунас Е.Ф., Скрыль А.И., Шатиров С.В. Концентрация очистных работ как основа повышения Эффективности производства угольных шахт."Уголь",1998, 21с.
- Мышляев Б.К., Титов И.В Струг или комбайн для выемки тонких пластов //Уголь, 2011, №7, с. 24-26
- Матвеев В.А. Разработка научных основ управления кровлей в струговых очистных забоях с целью создания технологии струговой выемки угля с высоким уровнем механизации. : Дпс. докт.техн.наук. - М., 1974. - 388 с.
- Батин О.Б., Голод А.Б., Вихров О.Ф., Гозенко А.Д., Мендрух М.В. Струговая выемка тонких пластов и перспективы ее развития. - Технология и техника струговой выемки антрацитов: Тр. ШахтНШ, I97I, вып. II, с. 77-85.
- Габов В.В. Очистные механизированные комплексы для добычи угля в длинных забоях. М.: Недра, 1995. - 166с.
- Мышляев Б.К., Титов И.В. Технико-экономический анализ современных механизированных крепей // Горное оборудование и электромеханика, 2008 №12, с.20-25