Abstract
Сontents
- Introduction
- 1. Theme urgency
- 2. Goal and tasks of the research
- 3. Comparison shearer and plow dredging coal technologies
- 4. Overview of treatment systems for the production of coal in longwall
- 5. Techno-economic analysis of modern powered supports
- Conclusion
- References
Introduction
One of the areas of the progressive development of underground coal is to improve manufacturability and completeness of mining coal reserves to ensure recovery of previously written off stocks in areas deemed inexpedient to recess long clearing faces and pillars in various applications. Implementation of scientific and technological developments in this area , namely the rational combination of technologies working out long and short clearing faces - will extend the life of the coal mines and the maximum recoverable reserves , including in difficult conditions both operating and closing mines . The main reason for the decline in coal production of thin layers was the lack of high technology for their mining and the application of mining shearer - extremely low load on the working face and the high volume of work.
The reasons for this are significant depreciation of fixed assets and lack of adaptability to the mines of underground coal due to excessive orientation industry mechanized coal mining (78.9% in 2006). In addition, the disposal capacity of coal mines exceeds their input 3-5 times, significantly increasing the volume of construction in progress.
1. Theme urgency
On the Donbass mines currently under testing of seams most convenient technological power, which was created and is commercially available from new high-performance equipment for sewage treatment works, tunneling and transport. Reserves are concentrated in thin layers and low-power, tend to remain in the ground and can not be removed. Currently, 70% of coal in the Donbass occur in thin and very thin layers.
Waiver of reservoir development of low power will increase the depth of mining operations , mining suite violation of the order , as well as the rapid depletion of more powerful layers , which are needed to fill the large investment funds for further exploration stocks , the construction of new enterprises , reconstruction or modernization. Please keep in mind that mineral resources have a characteristic - they are not recoverable . This leads to the fact that reserves are drying up in thick seams and possibly attack the moment when the coal begins to fade and then there is a need to develop measures aimed at increasing the life of the mines.
On this basis, the development of technical solutions for the preparation and mining of thin layers is a very important problem which is both very complicated, due to the specificity of the conditions of their development [1].
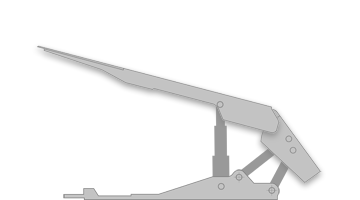
Figure 1 - Shielding mechanized system (animation: 9 frames, 5 cycles of repetition, 70.5 kilobytes).
2. Goal and tasks of the research
Prerequisite for successful concentration of sewage works yavlyaetsya software fold increase productivity purification equipment by improving the technical level of powered supports and complexes ( greater share of shield supports and their carrying capacity , increasing installation step , width and pitch shifting support units ) , the technical level of shearers ( increase in unit capacity and the installed capacity of electric drive , width , and feed rate of traction , improved feed mechanisms , the use of single-screw combines lava for short ) , the technical level of plows (increase basic parameters settings , their reliability, precision control of the plow at work on formations with unseasoned hypsometry ).
As of 1.01.12 , the Ukrainian mines operated 240 stopes , of which 166 - mechanized mining (ASM ) . The average load on the working face was 770 t / d to CMH - 1041 t / d . In thin flat and inclined seams less than 1.2 m working stopes 129 , of which 106 CMH . The average load on the working face in thin layers was 795 t / d to CMH - 940 tons / day . Two-thirds of stopes are operated in environments with highly volatile, low stability immediate roof . Therefore, a highly efficient purification technique for testing thin flat layers is of the highest priority tasks of the research and design organizations of Ukraine[2].
3. Comparison shearer and plow dredging coal technologies
There are different approaches to bring both technologies to a common denominator, and in most cases there was no comprehensive approach. Most often compared combines technical parameters and plows, sometimes considered technology, however, examples of holistic analysis is almost impossible to find in the literature. However, a comprehensive comparison of the two different technologies makes sense only if a comprehensive approach that takes into account all the important technical, operational and economic factors (Pic. 3)
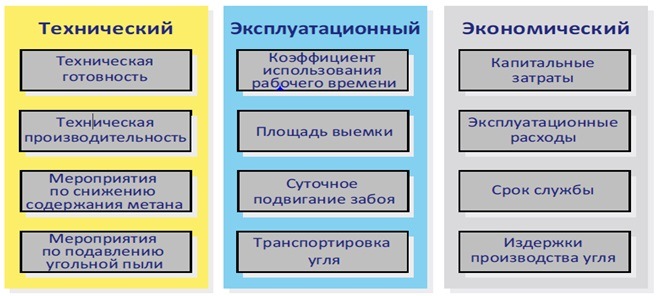
Figure 3. Levels comparison shearer and plow technology
Shearers are usually used on the seams from 1.5 to 6.0 m in the past there have been numerous attempts to effective use of harvesters seams at least 1.5 m Most of these attempts have failed, both from a technical and economic point of view . Relatively low installed power, the complexity of manipulation in a confined space and the low quality of loading a broken rock mass - are the main reasons . In many cases, the notch on the harvester is a height greater than net pay , capturing the roof rock or soil , resulting in an increase in carbon content of rocks and rising costs proizvodstva.olzovanie very powerful high harvesters (Fig. 2) involves the transition from the system power supply voltage of 660 V voltage at 1140 , 2300, 4160 (for example , combines a series of "Elektra ," the German company DBT) and subsequently 6-10 kV
Thus, depending on the size and configuration combines weight varies from 5.3 m (for thin layers) to 30-50 m - excavating coal seams of average power and up to 75-100t - for thick seams.
Modular design combines the modern and the presence of one major carrier frame to which are attached quick connect all units combine provide quick "assembly-disassembly" combine a rolling replacement during repairs, eliminating the need for repairs in the mining conditions, the ability to work with two or one driven cutting and feeding. All this leads to increased reliability of harvesting and reduce the cost of their maintenance and repair.
Shearers are equipped with a manual system of direct control (used for commissioning and testing regimes combines their work), radio remote control systems (with a wearable remote) software automated control at high speeds of the shearer, exceeding the average speed of the driver.
For working fine flat seams "Dongiprouglemash" developed a number of shearers for a wide range of geological conditions - UKD200-250 UKD200-400-500 UKD200, UKD400 and KA200.
Combine UKD200-250, designed for excavation seams 0.85-1.3 m, equipped with a centrally located along the face of the blade pieces engine power 200-250 kW. In 2009-2011. design documentation shearers UKD200-400-500 and UKD200. The new layout engine in these models allowed to increase power-harvesting, reduce their "hard" base and improve "vpisyvaemost" in hypsometry formation
Combine UKD200-500 for the first time in the history of domestic engineering features balanced gearboxes cutting part.
In 2011, completed the work on the creation of a shearer with electric supply system Chainless UKD400 allowing effectively seize a thin shallow and inclined seams 0.85-1.6 m operating speed of 10 m / min[3].
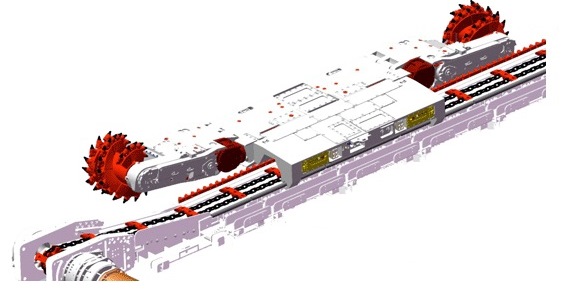
Harvester for cleaning thin seams UCD 400
Plow units are used for work on seams from 0.6 to 2.3 m, while in Germany, used a plow and seams to
up to 3 m on seams less than 1.0 m from the base used Struga podkonveyernoy stove, and seams more than 1.0 m - Struga sliding type. Despite the small own height, plow units provide a recess exactly hypsometry coal seam without having prisechki surrounding rocks. Layers with varying power not present any problems for plows, if the roof seam lies breed layers or top layer of coal can unleash using overlap lining.
It should be noted that at a high speed for efficient operation of the plow lava complex must have a considerable length of time to reduce the weighting for acceleration and deceleration of the plow at each chip groove . With these operations, the longwall 400 m long plow removes one chip for 3 min . The energy intensity of the recess in the tests was 0.72 kW ? H / t , and the project - from 0.5 kW ? H / t to 0.83 kW ? H / t , ie, calculations showed that when working in harsh environments even the most powerful modern plow complex provides a recess coal power consumption , higher than the shearer recess[4].
The most realistic way of solving the problem of high-performance thin seams development is to create the art, using the traditional method of mechanical destruction of the mineral, and especially front-plow units, allowing not only to implement a high-performance, in-line production of coal, but also to solve a major social and economic problem as the withdrawal of people from the working face[5].
4. Overview of treatment systems for the production of coal in longwall
Creation and implementation of OMC in the practice of underground coal mining has played a crucial role in modernization of the coal industry , served as a powerful stimulus to the development of mines led to an increase in the technical level of all parts of underground mining technology . Successful application of OMC in the coal industry contributed to the expansion of their application . Purification mechanized complexes were used for potash mines and the extraction of a number of other minerals mainly with reservoir structure occurrence.
In the transition to the comprehensive mechanization of clearing works were basically solved the problem of creating hydroficated mobile support units, mobile downhole scraper conveyors, uzkozahvatnyh harvesters, plows. Kinematic connections listed machinery and equipment provide consistent movement in cyclic operation of the whole complex machinery behind podviganiya stope as mining excavation column.
Plow OMC have an advantage over COMBINE complexes when mining thin seams without layers and consolidated rock solid inclusions. COMBINE complexes used for mechanization of cleaning operations in coal seams of medium-power and high-power, as well as thin layers with a complex structure and hypsometry occurrence, where the use of plows inappropriate.
Coordinated functioning of all machinery and equipment OMC in major and minor mode provides integrated power systems, lighting, signaling and control , hydraulic system , providing police support units moving conveyor and cutter machine , hydraulic dust suppression systems, air monitoring in mines , in particular quantitative content methane gas , telephone and public address systems . The main requirement for the listed equipment and systems to provide long-term sustainable high performance and safe for people of OMC in the changing geological conditions as mining excavation column. Using redundancy to improve reliability as a method of treatment in mechanized complexes is limited, so each of the elements included in the OMC should be trusted and explosion , intrinsically safe . The development, manufacture and operation of the OMC should be guided by artists applicable safety regulations in the coal mines ( shale mines , mines ) , safety regulations downhole machines and systems and a number of other industry regulations , procedures and instructions.
Efficiency of mechanized longwall faces evaluate system absolute and specific technical and techno-economic indicators , providing a comparative evaluation of both the equipment and the efficiency of its use . However, mining and geological , mining and processing conditions of effluent treatment mechanized complexes differ so much that performance indicators mechanized longwall faces , even when developing a post excavation , it is difficult to compare . The presence of weak and heavy , difficult to manage, prone to periodic block caving roofs, weak watered soils , undulating hypsometry , irregularities in the Seam , increased bearing capacity - this is not a complete list of geological factors complicating treatment operation of mechanized coal mining complexes treatment in long faces[6].
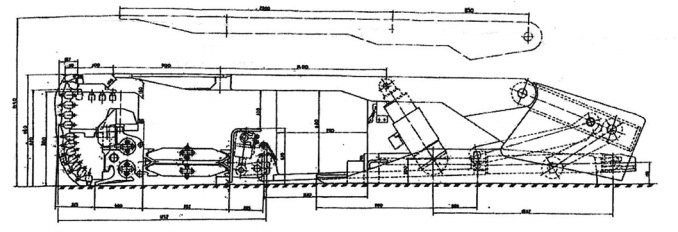
Complex KM 137 with plow type setting «Компактхобель»
5. Techno-economic analysis of modern powered supports
The main contribution to the scientific basis for interaction powered supports with side seams rocks have specialists VNIMI , IGD them . AA Skochinskiy " Giprouglemash " PNIUI , DonUGI and " Krangormasha ." It should be noted that the first phase of the development of domestic powered support for Donbass mines with virtually no evidence-based recommendations on the resistance , " Giprouglemash " involving VNIMI ( AA Orlov) in the 1950s laid the development unit for bolting resistance A2 700 remove kN/m2 at an average seam thickness of 1.0 m
The efficiency of the mechanized system resource affects her work. Domestic resource shoring type M138, M142, M144 was 8 thousand cycles shifting sections with six years of service and 10 thousand cycles at eight years of service, which is almost completely satisfy the requirements for their use in complex mechanized faces CMH in the mines of Russia until 2000-2002 years. Resource shoring companies in Germany amounted to 30 thousand cycles shifting sections with 12 years of service
Step Position support units also affects efficiency. Until recently secured with double-row sections mainly used step installation sections of 1.5 m When using a single row of supports sections under heavy roofs began to use step 1.75m to allow passage between the uprights..
Development " Giprouglemash " Modular M151 lining for extraction of thin layers with step installation sections 1.0, 2.0 and 3.0 m showed that increased installation step sections leads to an increase in its ME. talloemkosti 5 ... 7%, based on reducing the cost of system management section does not affect the original cost of the lining as a whole. These studies have shown that the transition to the lining block modular design step installation sections 2.0 and 3.0 m , respectively, when the module is equal to step install 1.0 and 1.5 m for the favorable conditions as wall rock formation justified[7].
Conclusion
In order to compare the efficiency of the shearer and plow lavas on coal seams average power required to consider the following technical, operational and economic factors.
A. Harvesters are characterized by a more efficient transfer of energy, but lower efficiency recess than Struga. However, the value of specific energy required for the extraction of coal per unit mass under the same conditions, is comparable for both types of machines.
B. In the power range up to the formation of 0.7 to 2.3 m modern plow systems have higher power density, i.e. installed capacity per unit height of lava than harvesters.
С. Production costs depend on performance in addition to lava from capital and operating costs. In general we can say that when developing layers ranging from 1.5 to 2.3 m capex for shearer lavas comparable capex plow lavas, but operating costs Plow lavas less than a combine. Consequently, production costs plow lavas less than shearer.
References
- Бурчаков А.С. Технология подземной разработки пластовых месторождений полезных ископаемых / А.С. Бурчаков, Н.К. Гринько, Д.В. Дорохов. - М.: Недра, 1983. - 487с.
- Козловчунас Е.Ф., Скрыль А.И., Шатиров С.В. Концентрация очистных работ как основа повышения Эффективности производства угольных шахт."Уголь",1998, 21с.
- Мышляев Б.К., Титов И.В Струг или комбайн для выемки тонких пластов //Уголь, 2011, №7, с. 24-26
- Матвеев В.А. Разработка научных основ управления кровлей в струговых очистных забоях с целью создания технологии струговой выемки угля с высоким уровнем механизации. : Дпс. докт.техн.наук. - М., 1974. - 388 с.
- Батин О.Б., Голод А.Б., Вихров О.Ф., Гозенко А.Д., Мендрух М.В. Струговая выемка тонких пластов и перспективы ее развития. - Технология и техника струговой выемки антрацитов: Тр. ШахтНШ, I97I, вып. II, с. 77-85.
- Габов В.В. Очистные механизированные комплексы для добычи угля в длинных забоях. М.: Недра, 1995. - 166с.
- Мышляев Б.К., Титов И.В. Технико-экономический анализ современных механизированных крепей // Горное оборудование и электромеханика, 2008 №12, с.20-25