Реферат по теме выпускной работы
Содержание
- Введение
- 1. Актуальность темы
- 2. Цель и задачи исследования
- 3. Основные задачи исследования
- 3.1 Анализ процесса конвейерного транспорта как объекта автоматизации.
- 3.2 Критический обзор известных технических решений по автоматизации процесса конвейерного транспорта.
- 3.3 Обоснование и разработка системы автоматизации разветвленной конвейерной линии.
- Выводы
- Список источников
Введение
Основным средством доставки грузов на современных горнодобывающих предприятиях является конвейерный транспорт. Ленточные конвейеры (ЛК) эффективно заменяют локомотивную и канатную откатку, что обусловлено такими их преимуществами, как непрерывность, широкие возможности для автоматизации, возможность транспортирования грузов в наклонных выработках, простота наращивания и разветвления линии, относительная безопасность.
К его основным достоинствам относятся: экономичность, высокая производительность, обусловленная непрерывностью процесса транспортирования; надежность (коэффициент готовности достигает для ленточных конвейеров 0,999, для пластинчатых – 0,987); технологическая приспособленность к работе с системой автоматизированного управления и вследствие этого низкая трудоемкость обслуживания (1–4 чел./смену в сутки на один конвейер); способность транспортирования груза как по горизонтальным, так и по наклонным горным выработкам; простота и удобство сопряжения с оборудованием очистных и подготовительных забоев.
1. Актуальность темы
Магистерская работа посвящена актуальной в настоящее время на шахтах Украины проблеме повышения надежности конвейерного транспорта. За счет снижения нагрузки на электропривод ленточного конвейера. Большая нагрузка вызвана высокой неравномерностью грузопотоков, поступающих на транспортные установки, так как конвейерная линия по своему технологическому назначению является транспортным объектом, обслуживающим очистной забой. Технологические паузы в работе выемочных комбайнов, в том числе при аварийной остановке лавы, и периодическое изменение их скорости перемещения вдоль линии очистного забоя являются причиной неравномерности или отсутствия грузопотоков, которые также отражаются на загрузке конвейера. При этом характерна значительная недогрузка магистральных конвейеров; продолжительная работа в режиме холостого хода. Это отрицательно сказывается на технико-экономических показателях использования средств транспорта, т.к. они большую часть времени своей работы имеют существенную (в 2–4 раза) недозагрузку, приводят к повышению удельных расходов электроэнергии. В настоящее время на угольных предприятиях для повышение эффективности конвейерного транспорта применяются угольные аккумулирующие бункеры и предлагается регулирование скорости движения конвейерной ленты с использованием частотно-регулируемого привода (ЧРП). Стремление к удешевлению и повышению надежности ЛК обусловило широкое применение в них нерегулируемого привода на основе асинхронных электродвигателей с короткозамкнутым ротором (АД). Однако, как показывает анализ факторов, определяющих режим работы ЛК, нерегулируемый привод не обладает достаточной эффективностью. Одним из важнейших параметров, влияющих на надежность и экономичность конвейерной установки, является скорость движения ленты. Регулирование этого параметра может достигаться применением специальных приводов и системы автоматического регулирования скоростью [1].
2. Цель и задачи исследования, планируемые результаты
Целью работы является исследование и разработка устройства автоматического контроля и стабилизации нагрузки электропривода шахтного ленточного конвейера. объект автоматизации представляет собой разветвленную конвейерную линию.
3. Основные задачи исследования
3.1 Анализ процесса конвейерного транспорта как объекта автоматизации.
Процесс конвейерного транспорта шахты – это технологический процесс перемещения горной массы, материалов, а в некоторых случаях и людей с помощью конвейеров по горным выработкам. На шахтах для конвейерного транспорта в основном применяются ленточные конвейера. Ленточный конвейер – транспортирующее устройство непрерывного действия с объединённым грузонесущим и тяговым органом в виде замкнутой гибкой ленты. Лента приводится в движение силой трения между ней и приводным барабаном; опирается по всей длине на стационарные роликоопоры. Для перемещения груза на большие расстояния используются конвейерные линии, состоящие из двух и более конвейеров.
Современные подземные конвейерные линии характеризуются значительной протяженностью (десятки километров) и разветвленность транспортных магистралей, изменяющих современем свои параметры: длину, топологию и т.п. В условиях шахт конвейерная линия может быть не разветвленной и разветвленной. Под неразветвленной конвейерной линией понимают однопоточную линию, в которой груз на каждый конвейер поступает только с одного предыдущего конвейера, а под разветвленной – многопоточную линию, состоящую из ответвлений и сборной части. Для разветвленных конвейерных линий требуется согласование режимов работы основных – магистральных конвейеров с участковыми. Ленточные конвейеры могут быть оборудованы одним приводным электродвигателем или несколькими мощными электродвигателями. Суммарная мощность электродвигателей участковых конвейеров составляет 300-500 кВт, а магистральных – несколько тысяч киловатт, поэтому подземная транспортная система современной угольной шахты наравне с подъёмными, водоотливными и вентиляторными установками является основным потребителем электроэнергии. Доля энергопотребления конвейерного транспорта шахты составляет порядка 20% общешахтного потребления электроэнергии. Поэтому требуется обеспечение работы конвейерных установок в энергосберегающих режимах. Ленточный конвейер в общем виде состоит из гибкой, замкнутой, предварительно натянутой ленты 1, являющейся одновременно грузонесущим и тяговым органом; привода 2, состоящего из приводного барабана, редуктора 3, двигателя 4 и соединительных муфт; натяжного устройства 8 с натяжным барабаном 7; роликоопор 5 и 11 для поддержания соответственно рабочей и холостой ветвей ленты; опорной металлоконструкции (станины) 6; загрузочного 9 и разгрузочного устройств; очистного устройства 10 (в случае необходимости).
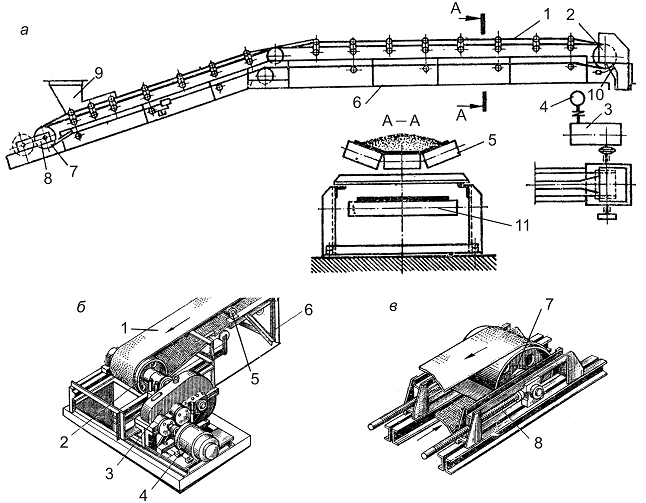
Рисунок 1 – технологическая схема
Лента приводится в движение силой трения, возникающей при вращении приводного барабана 2. Предварительное натяжение создается с помощью натяжного устройства 8, которое устанавливается на концевом барабане или на холостой ветви ленты (вертикальное натяжное устройство). В настоящее время почти все конвейерные линии на шахтах автоматизированы. Развитие автоматизации шахтных конвейерных линий на протяжении длительного периода определялось необходимостью снижения трудоемкости управления и повышения безопасности эксплуатации конвейерного транспорта. В связи с этим широкое распространение получило автоматизированное управление конвейерной линией, техническая сущность которого заключается в централизации управления процессами пуска и остановка конвейеров, а также в обеспечении автоматической защиты от развития аварии при возникновении аварийных ситуаций [2].
3.2 Критический обзор известных технических решений по автоматизации процесса конвейерного транспорта
Система автоматизированного управления конвейерными линиями типа САУКЛ.
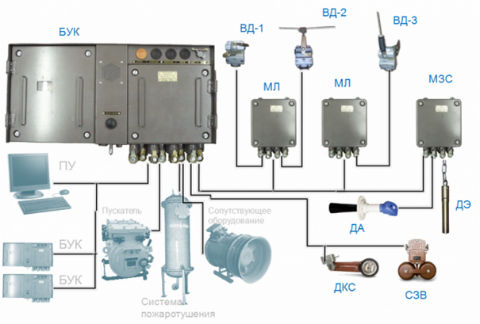
Рисунок 2 – Система автоматического управления типа САУКЛ
Аппаратура САУКЛ разработана для автоматизации шахтного и рудничного конвейерного транспорта, состоит из комплекта аппаратуры пульта управления, включающего пульт управления (ПУ), адаптер пульта управления (АПУ), адаптер линии связи (АЛС) и комплекта аппаратуры управления конвейером, включающего блок управления конвейером (БУК), модули линейные (МЛ), модуль заштыбовки и сирены (МЗС), датчик акустический (ДА) и источник питания (ИП).
Аппаратуры САУКЛ предназначена для:
шибер,
перегружатель,
питатель);
Система САУКЛ предназначена для работы в
шахтах, в том числе опасных по газу или пыли и внезапным выбросам угля
или газа, а также рудников, где возможно образование взрывоопасных
смесей категории I, отнесенных по воспламеняемости к группе Т1 по ГОСТ
12.1.011, в условиях умеренного и холодного климата, температура
окружающего воздуха от -10 до +40° С, относительная влажность
до 100% при температуре +35° С. Область и условия применения в
шахтах в соответствии с Едиными правилами безопасности при разработке
рудных, нерудных и россыпных месторождений подземным способом
и
Правилами безопасности в угольных шахтах
.
Комплекс АУК-1М автоматизированного управления конвейерами, предназначен для управления разветвленными конвейерными линиями.
Аппаратура АУК-1М выполняет следующие основные функции:
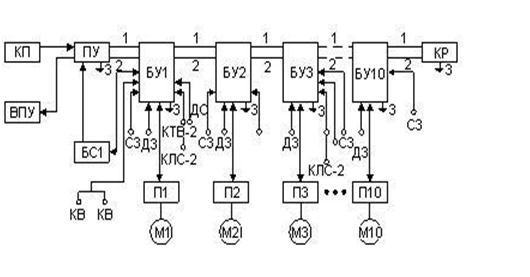
Рисунок 3 –Структурная схема аппаратуры АУК-1М
На рисунке обозначено: ПУ – пульт управления, ВПУ –выносной прибор – указатель, БУ – блоки управления, БКР – блок концевого реле, ДС – датчик скорости, КСЛ – 2 – датчик контроля схода ленты, КТВ – 2 – кабель – тросовые выключатели, ДЗ – датчик заштыбовки.
Взрывобезопасное исполнение аппаратуры и искробезопасные параметры цепей управления позволяют осуществлять управление, сигнализацию, контроль работы конвейерной линии и телефонную связь по двум изолированным друг от друга голым проводам и общешахтному контуру земля или с помощью трёх жил контрольного кабеля. Пуск конвейерной линии осуществляется путём подачи в линиюуправления (провода 1 и 2 пусковой полярности (на проводе 1, на проводе 2). После окончания пускового процесса производится переключение пусковой полярности на рабочую (на проводе 2 на проводе 1), при этом реле управления БУ второго конвейера питается через контакты реле скорости БУ первого конвейера. Таким образом, осуществляется электромеханическая блокировка работы последующего конвейера в зависимости от работы предыдущего конвейера. Отключение конвейерной линии может производиться оператором, путём нажатия кнопок «Стоп» пульта ПУ или любого блока БУ.
3.3 Обоснование и разработка системы автоматизации разветвленной конвейерной линии
Из-за неравномерной работы магистральные ленточные конвейеры, эксплуатируемые на шахтах, часто не используются на проектную мощность, а доля холостых, или близких к ним режимов, составляет значительную часть рабочего времени. Стремление к удешевлению и повышению надежности ЛК обусловило широкое применение в них нерегулируемого привода на основе асинхронных электродвигателей с короткозамкнутым ротором (АД). Однако, как показывает анализ факторов, определяющих режим работы ЛК, нерегулируемый привод не обладает достаточной эффективностью. Причиной тому является, во-первых, переменная интенсивность грузопотока, поступающего на конвейер, а во-вторых, высокая жесткость механической характеристики приводного АД. Колебания интенсивности поступления груза приводят к соответствующему изменению нагрузки на привод, которая может варьироваться в довольно широких пределах.
Основные задачи, решаемые в ходе проводимых исследований, могут быть сформулированы следующим образом:
1) Применение средств регулирования грузопотока за счет использования накопительных систем (промежуточные бункеры, конвейеры), что обеспечивает адаптацию интенсивности поступления груза к условиям нерегулируемого привода конвейера.
2) Применение средств регулирования скорости в составе привода ЛК, обеспечивающих адаптацию конвейера под условия изменяющегося грузопотока (частотно-регулируемый электропривод, регулируемые муфты, каскадные схемы управления АД с фазным ротором).
Экономичная и надежная работа конвейера, обусловлена стабильностью его статической нагрузки F. Последняя, в свою очередь, может быть обеспечена за счет поддержания на заданном уровне соотношения между интенсивностью поступающего грузопотока Q и скоростью ленты V. При отсутствии бункерных накопителей, что характерно для участковых, а также неразветвленных участков магистральных конвейерных линий, грузопоток рассматривается как независимое возмущающее воздействие. Единственным фактором, посредством которого можно влиять на нагрузку привода (стабилизируемая выходная величина), остается скорость (управляющее воздействие) [3].
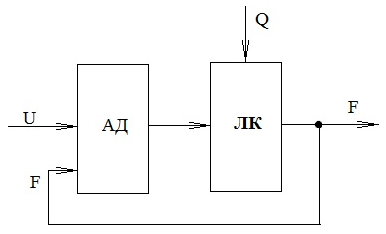
Рисунок 4 – Расчетная схема идентифицируемого объекта
В зависимости от объёма грузопотока значение тягового усилия при постоянной скорости изменяется в несколько раз, тем самым меняется нагрузка двигателя и, как следствие, его скольжение. Поскольку оптимальное скольжение соответствует максимуму коэффициента мощности и КПД, необходимо регулирование скорости движения ленты для достижения оптимальной работы ЭП.
При отсутствии регулирования скорости, статический момент сопротивления электродвигателя, в зависимости от грузопотока, значительно варьируется, что негативно сказывается на надёжности двигателя и рациональности его энергопотребления. Если же регулировать скорость в зависимости от грузопотока можно добиться оптимальных значений энергетических показателей электропривода ленточного конвейера, а также увеличить срок службы грузонесущего органа. Отсюда следует, что применение плавного регулирования линейной скорости ленты, например, с помощью частотно-регулируемого электропривода, позволяет снизить энергопотребление по сравнению с нерегулируемым электроприводом.
В качестве аппаратуры автоматизации принята аппаратура типа САУКЛ. Аппаратура САУКЛ была выбрана так как выполнена на современной микропроцессорной основе, а так же имеет современные средства и стандарты связи. Искробезопасность в САУКЛ обеспечивается гальванической развязкой электрических цепей пульта управления, линии связи, линии телефона, линии модулей линейных, линии взаимоблокировки, цепи питания датчика электродного и цепей питания электронных схем, а также применением схем, обеспечивающих ограничение мощности возможной искры, за счет ограничения тока короткого замыкания [4].
Функциональности аппаратуры САУКЛ и решения проблемы с перегрузкой привода конвейера и нецелесообразным экономическим использованием разрабатывается устройство на микропроцессорной основе, которое будет выполнять функцию регулирования скорости конвейерной линии в зависимости от поступающего грузопотока на ленту. Структурная схема приведена на рисунке 5.
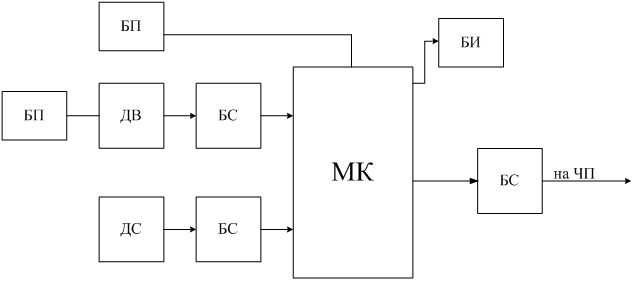
Рисунок 5 – Структурная схема устройства регулирования и формирования заданной скорости
На рисунке 5 показаны:
БП – блок питания; БС – блок согласования; ДВ
– датчик веса;
ДС – датчик скорости; МК – микроконтроллер; БИ
– блок индикации;
Устройство формирования заданной скорости (УФС) состоит из блока датчиков, микропроцессора и блока сигнализации включающего в себя LCD дисплей. Основой устройства является микроконтроллер. Датчик веса располагается на предыдущем конвейере, это дает возможность быстрее реагировать на изменения грузопотока. Используется тензорезистивный датчик веса, они рекомендованы к использованию в условиях шахты. Сигналы от датчика скорости (через гальваническую развязку) и датчика веса (через интерфейс токовая петля) предаются на аналоговый вход микроконтроллера. Модуль АЦП, который входит в его состав преобразует данную информацию в двоичный код с целью дальнейшей обработки. Происходит вычисление фактического грузопотока на ленте и сравнение его с заданным. В зависимости от разности этих значений вырабатывается сигнал управления, который через интерфейс RS-485 достигает конечного адресата – преобразователя частоты, к которому подключен электродвигатель привода конвейера. Согласование сформированного сигнала с RS-485 происходит через преобразователь интерфейсов. Для контроля работы устройства в блоке присутствует жидкокристаллический индикатор, на который выводится информация о скорости и производительности конвейера. Количество угля на ленте, т.е. масса поступающего груза, является изменяющимся параметром, а скорость – регулируемым [6].
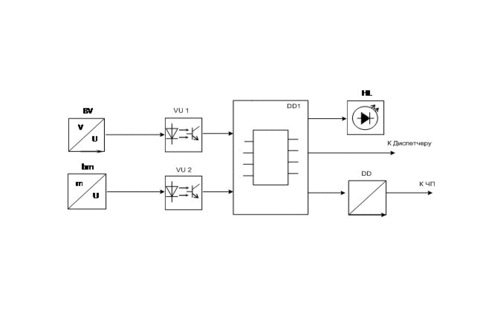
Рисунок 6 – Функциональная схема устройства формирования заданной скорости(анимация: 7 кадров, итервал: 55 мс, размер: 112 кбайт)
Диапазон регулировки скорости конвейера устанавливается в пределах от 0,1V до 1,0V, где V – номинальная скорость. Регулирование скорости производится по сигналу УФС. При нулевой загрузке ленты скорость ее не превышает 0,1 от номинальной. При нарастании грузопотока и достижении уровня груза выше установленной величины выдается сигнал на увеличение скорости ленты. Скорость ленты будет увеличиваться до тех пор пока уровень груза не станет ниже установленной величины. За счет обратной связи УФС – преобразователь производится автоматическое поддержание уровня груза на заданном уровне. УФС совместно с преобразователем частоты должен поддерживать постоянство коэффициента отношения грузопоток/скорость.
Выводы
Был рассмотрен процесс автоматизации конвейерной линии, состоящей из трех участковых и одного магистрального конвейера. Было разработано устройство формирования заданной скорости ленточного конвейера, которое обеспечивает плавное регулирования скорости ленты конвейера, путем изменения частоты вращения электропривода конвейера, в зависимости от поступающего на ленту конвейера грузопотока.Выведены зависимости входящего грузопотока и оптимальной для его количества скорости с целью обеспечения оптимальной нагрузки на привод конвейера и достижения более эффективных энергетических и экономических показателей. Была обоснована целесообразность данного исследования, сконструирована структурная, функциональная и принципиальная электрическая схема УФС, проведено математическое моделирование. Разработаны методы по безопасной и безаварийной эксплуатации УФС. Обоснованны факторы технико-экономической целесообразности принятых технических решений. Что доказало целесообразность разработанного устройства.
При написании данного реферата магистерская работа еще не завершена. Окончательное завершение: декабрь 2014 года. Полный текст работы и материалы по теме могут быть получены у автора или его руководителя после указанной даты.
Список источников
- Малиновский А. К. Автоматизированный электропривод машин и установок шахт и рудников: учебник для вузов / А. К. Малиновский. – М.: Недра, 1987. – 277 с.
- Шахмейстер Л. Г. Динамика грузопотоков и регулирование скорости ленточных конвейеров / Л. Г. Шахмейстер, В. Г. Дмитриев, А. К. Лобочева. – М.: Машиностроение, 1972. – 160 с.
- Полунин В. Т. Эффективность регулирования скорости шахтных конвейеров / В. Т. Полунин / Научные труды МГИ. – 1968. – № 53. – С. 87 – 95.
- Дмитриева В. В. Разработка и исследование системы автоматической стабилизации погонной нагрузки магистрального конвейера: дис. кандидата техн. наук: 05.13.06 / Дмитриева В. В. – М., 2005. – 162 c.
- Лукас В. А. Теория автоматического управления: учебник для вузов / В. А. Лукас. – М.: Недра, 1990. – 416 с.
- Справочник по автоматизации шахтного конвейерного транспорта / Н. И. Стадник В. Г. Ильюшенко С. И. Егоров и др. – К.: Техника, 1992. – 438 с.