Реферат з теми випускної роботи
Зміст
- Вступ
- 1. Актуальність теми
- 2. Мета і задачі дослідження
- 3. Основні завдання дослідження
- 3.1 Аналіз процесу конвеєрного транспорту як об'єкта автоматизації.
- 3.2 Критичний огляд відомих технічних рішень з автоматизації процесу конвеєрного транспорту.
- 3.3 Обгрунтування та розробка системи автоматизації розгалуженої конвеєрної лінії.
- Висновки
- Список джерел
Вступ
Основним засобом доставки вантажів на сучасних гірничодобувних підприємствах є конвеєрний транспорт. Стрічкові конвеєри (CК) ефективно замінюють локомотивну і канатну відкатку, що обумовлено такими їх перевагами, як безперервність, широкі можливості для автоматизації, можливість транспортування вантажів у похилих виробках, простота нарощування та розгалуження лінії, відносна безпека.
До його основних достоїнств відносяться: економічність, висока продуктивність, обумовлена безперервністю процесу транспортування; надійність (коефіцієнт готовності досягає для стрічкових конвеєрів 0,999, для пластинчастих–0,987); технологічна пристосованість до роботи з системою автоматизованого управління і внаслідок цього низька трудомісткість обслуговування (1–4 люд. / зміну на добу на один конвеєр); здатність транспортування вантажу як по горизонтальних, так і на похилих гірничих виробках; простота і зручність сполучення з обладнанням очисних і підготовчих вибоїв.
1. Актуальність теми
Магістерська робота присвячена актуальній нині на шахтах України проблемі підвищення надійності конвеєрного транспорту. За рахунок зниження навантаження на електропривід стрічкового конвеєра. Велике навантаження викликана високою нерівномірністю вантажопотоків, що надходять на транспортні установки, так як конвеєрна лінія по своїм технологічним призначенням є транспортним об'єктом, обслуговуючим очисний забій. Технологічні паузи в роботі виїмкових комбайнів, у тому числі при аварійній зупинці лави, і періодична зміна їх швидкості переміщення уздовж лінії очисного вибою є причиною нерівномірності або відсутності вантажопотоків, які також відображаються на завантаженні конвеєра. При цьому характерна значна недовантаження магістральних конвеєрів; тривала робота в режимі холостого ходу. Це негативно позначається на техніко-економічних показниках використання коштів транспорту, т.к. вони більшу частину часу своєї роботи мають істотну (в 2–4 рази) недозавантаження, призводять до підвищення питомих витрат електроенергії. В даний час на вугільних підприємствах для підвищення ефективності конвеєрного транспорту застосовуються вугільні акумулюючі бункери і пропонується регулювання швидкості руху конвеєрної стрічки з використанням частотно-регульованого приводу (ЧРП). Прагнення до здешевлення та підвищення надійності ЛК зумовило широке застосування в них нерегульованого приводу на основі асинхронних електродвигунів з короткозамкненим ротором (АД). Однак, як показує аналіз чинників, що визначають режим роботи ЛК, нерегульований привід не володіє достатньою ефективністю. Одним з найважливіших параметрів, які впливають на надійність і економічність конвеєрної установки, є швидкість руху стрічки. Регулювання цього параметра може досягатися застосуванням спеціальних приводів і системи автоматичного регулювання швидкістю [1].
2. Мета і завдання дослідження, плановані результати
Метою роботи є дослідження та розробка пристрою автоматичного контролю та стабілізації навантаження електроприводу шахтного стрічкового конвеєра. об'єкт автоматизації являє собою розгалужену конвеєрну лінію.
3. Основні задачі дослідження
3.1 Аналіз процесу конвеєрного транспорту як об'єкта автоматизації.
Процес конвеєрного транспорту шахти – це технологічний процес переміщення гірської маси, матеріалів, а в деяких випадках і людей за допомогою конвеєрів по гірничих виробках. На шахтах для конвеєрного транспорту в основному застосовуються стрічкові конвеєра. Стрічковий конвеєр – транспортує пристрій безперервної дії з об'єднаним грузонесущим і тяговим органом у вигляді замкнутої гнучкої стрічки. Стрічка приводиться в рух силою тертя між нею і приводним барабаном; спирається по всій довжині на стаціонарні ролікоопори. Для переміщення вантажу на великі відстані використовуються конвеєрні лінії, що складаються з двох і більше конвеєрів.
Сучасні підземні конвеєрні лінії характеризуються значною протяжністю (десятки кілометрів) і розгалуженість транспортних магістралей, змінюваному свої параметри: довжину, топологію і т.п. В умовах шахт конвеєрна лінія може бути не розгалуженої і розгалуженою. Під неразветвленной конвеєрної лінією розуміють однопоточні лінію, в якій вантаж на кожен конвеєр надходить тільки з одного попереднього конвеєра, а під розгалуженої–багатопоточну лінію, що складається з відгалужень і збірної частини. Для розгалужених конвеєрних ліній потрібне узгодження режимів роботи основних–магістральних конвеєрів з дільничними. Стрічкові конвеєри можуть бути обладнані одним приводним електродвигуном або кількома потужними електродвигунами. Сумарна потужність електродвигунів дільничних конвеєрів становить 300-500 кВт, а магістральних – кілька тисяч кіловат, тому підземна транспортна система сучасної вугільної шахти нарівні з підйомними, водовідливними і вентиляторними установками є основним споживачем електроенергії. Частка енергоспоживання конвеєрного транспорту шахти становить порядку 20% загальношахтного споживання електроенергії. Тому потрібно забезпечення роботи конвеєрних установок в енергозберігаючих режимах. Стрічковий конвеєр в загальному вигляді складається з гнучкої, замкнутої, попередньо натягнутою стрічки 1, що є одночасно грузонесущим і тяговим органом; привода 2, що складається з приводного барабана, редуктора 3, двигуна 4 і з'єднувальних муфт; натягача 8 з натяжним барабаном 7; роликоопор 5 і 11 для підтримки відповідно робочої і холостої гілок стрічки; опорної металоконструкції (станини) 6; завантажувального 9 і розвантажувального пристроїв; очисного пристрою 10 (у разі необхідності).
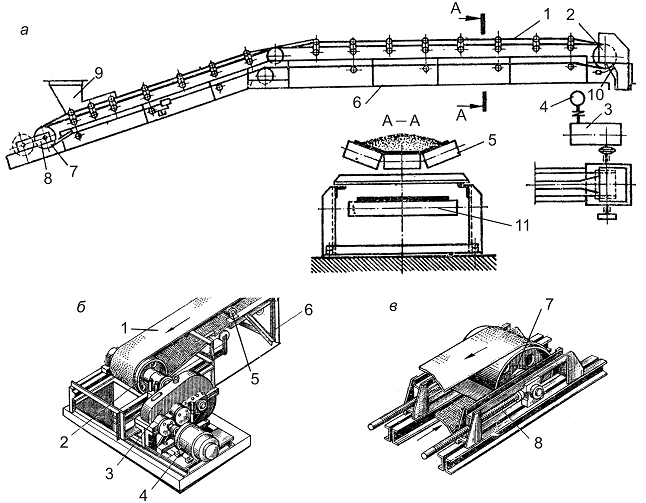
Рисунок 1 – Технологічна схема конвеєра
Стрічка приводиться в рух силою тертя, що виникає при обертанні приводного барабана 2. Попереднє натяг створюється за допомогою натяжного пристрою 8, яке встановлюється на концевом барабані або на холостий гілки стрічки (вертикальне натягач). В даний час майже всі конвеєрні лінії на шахтах автоматизовані. Розвиток автоматизації шахтних конвеєрних ліній протягом тривалого періоду визначалося необхідністю зниження трудомісткості управління та підвищення безпеки експлуатації конвеєрного транспорту. У зв'язку з цим широке поширення набуло автоматизоване управління конвеєрною лінією, технічна сутність якого полягає в централізації управління процесами пуску-зупинки конвеєрів, а також у забезпеченні автоматичного захисту від розвитку аварії при виникненні аварійних ситуацій [2].
3.2 Критичний огляд відомих технічних рішень з автоматизації процесу конвеєрного транспорту
Система автоматизованого управління конвеєрними лініями типу САУКЛ.
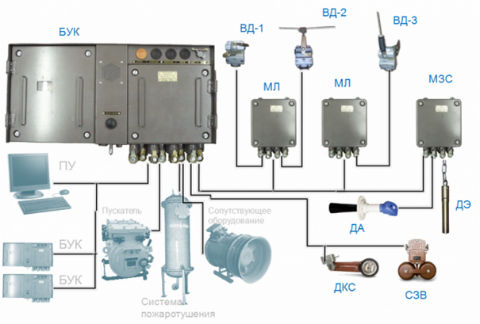
Рисунок 2 – Система автоматичного управління типу САУКЛ
Апаратура САУКЛ розроблена для автоматизації шахтного та рудничного конвеєрного транспорту, складається з комплекту апаратури пульта управління, що включає пульт управління (ПУ), адаптер пульта управління (АПУ), адаптер лінії зв'язку (АЛС) і комплекту апаратури управління конвеєром, що включає блок управління конвеєром (БУК ), модулі лінійні (МЛ), модуль заштибовки і сирени (МЗС), датчик акустичний (ДА) і джерело живлення (ІП).
Апаратури САУКЛ призначена для:
шибер,
перевантажувач,
живильник);
Система САУКЛ призначена для роботи в шахтах, у
тому числі небезпечних по газу або пилу і раптовими викидами вугілля
або газу, а також рудників, де можливе утворення вибухонебезпечних
сумішей категорії I, віднесених за займистості до групи Т1 за ГОСТ 12.1.011, в умовах помірного і холодного клімату, температура
навколишнього повітря від -10 до +40 ° С, відносна вологість до
100% при температурі +35 ° С. Область та умови застосування в
шахтах відповідно до Єдиними правилами безпеки при розробці рудних,
нерудних і розсипних родовищ підземним способом i правилами безпеки у
вугільних шахтах
.
Комплекс АУК-1М автоматизованого управління конвеєрами, призначений для управління розгалуженими конвеєрними лініями.
Апаратура АУК-1М виконує наступні основні функції:
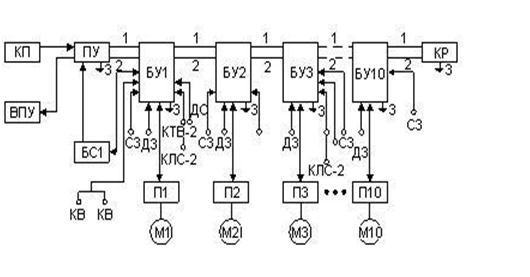
Рисунок 3 – Структурна схема апаратури АУК-1М
На малюнку позначено: ПУ – пульт управління, ВПУ – виносний прилад – вказівник, БО – блоки управління, БКР – блок кінцевого реле, ДС – датчик швидкості, КСЛ-2 – датчик контролю сходу стрічки, КТВ-2 – кабель – тросові вимикачі, ДЗ – датчик заштибовки.
Вибухобезпечне виконання
апаратури і іскробезпечні параметри
ланцюгів управління дозволяють здійснювати управління, сигналізацію,
контроль роботи конвеєрної лінії і телефонний зв'язок по двох
ізольованим один від одного голим проводам і загальношахтного контуру
земля
або за допомогою трьох жив контрольного
кабелю.
Пуск конвеєрної лінії здійснюється шляхом подачі в лініюуправленія
(проводу 1 і 2) пусковий
полярності
(на дроті 1,
на дроті
2). Після закінчення пускового процесу
проводиться
перемикання пускової полярності на робочу (на
дроті
2 на дроті
1), при цьому
реле управління БУ другого конвеєра живиться через контакти реле
швидкості БУ першого конвеєра. Таким чином, здійснюється
електромеханічна блокування роботи наступного конвеєра залежно від
роботи попереднього конвеєра. Відключення конвеєрної лінії може
проводитися оператором, шляхом натискання кнопок
Стоп
пульта ПУ або будь-якого блоку БУ.
3.3 Обгрунтування та розробка системи автоматизації розгалуженої конвеєрної лінії
Через нерівномірне роботи магістральні стрічкові конвеєри, експлуатовані на шахтах, часто не використовуються на проектну потужність, а частка неодружених, або близьких до них режимів, становить значну частину робочого часу. Прагнення до здешевлення та підвищення надійності ЛК зумовило широке застосування в них нерегульованого приводу на основі асинхронних електродвигунів з короткозамкненим ротором (АД). Однак, як показує аналіз чинників, що визначають режим роботи ЛК, нерегульований привід не володіє достатньою ефективністю. Причиною тому є, по-перше, змінна інтенсивність вантажопотоку, що надходить на конвеєр, а по-друге, висока жорсткість механічної характеристики приводного АД. Коливання інтенсивності надходження вантажу призводять до відповідної зміни навантаження на привід, яка може варіюватися в досить широких межах.
Основні завдання, які вирішуються в ході проведених досліджень, можуть бути сформульовані наступним чином:
1) Застосування засобів регулювання вантажопотоку за рахунок використання накопичувальних систем (проміжні бункери, конвеєри), що забезпечує адаптацію інтенсивності надходження вантажу до умов нерегульованого приводу конвеєра.
2) Застосування засобів регулювання швидкості в складі приводу ЛК, що забезпечують адаптацію конвеєра під умови мінливого вантажопотоку (частотно-регульований електропривод, регульовані муфти, каскадні схеми керування АД з фазним ротором).
Економічна і надійна робота конвеєра, обумовлена стабільністю його статичного навантаження F. Остання, в свою чергу, може бути забезпечена за рахунок підтримки на заданому рівні співвідношення між інтенсивністю надходить вантажопотоку Q і швидкістю стрічки V. При відсутності бункерних накопичувачів, що характерно для дільничних, а також нерозгалужених ділянок магістральних конвеєрних ліній, вантажопотік розглядається як незалежна рівноваги вплив. Єдиним фактором, за допомогою якого можна впливати на навантаження приводу (стабілізуєма вихідна величина), залишається швидкість (керуючий вплив) [3].
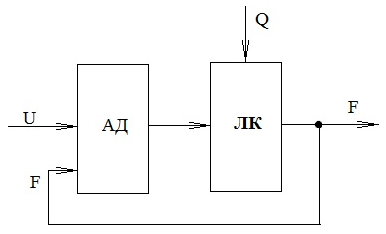
Рисунок 4 – Розрахункова схема ідентифікуємого об'єкта
Залежно від обсягу вантажопотоку значення тягового зусилля при постійній швидкості змінюється в кілька разів, тим самим змінюється навантаження двигуна і, як наслідок, його ковзання. Оскільки оптимальне ковзання відповідає максимуму коефіцієнта потужності і ККД, необхідно регулювання швидкості руху стрічки для досягнення оптимальної роботи ЕП.
При відсутності регулювання швидкості, статичний момент опору електродвигуна, залежно від вантажопотоку, значно варіюється, що негативно позначається на надійності двигуна і раціональності його енергоспоживання. Якщо ж регулювати швидкість залежно від вантажопотоку можна домогтися оптимальних значень енергетичних показників електропривода стрічкового конвеєра, а також збільшити термін служби грузонесущего органу. Звідси випливає, що застосування плавного регулювання лінійної швидкості стрічки, наприклад, за допомогою частотно-регульованого електроприводу, дозволяє знизити енергоспоживання в порівнянні з нерегульованим електроприводом.
В якості апаратури автоматизації прийнята апаратура типу САУКЛ. Апаратура САУКЛ була обрана оскільки виконана на сучасній мікропроцесорній основі, а так само має сучасні засоби та стандарти зв'язку. Іскробезпека в САУКЛ забезпечується гальванічною розв'язкою електричних ланцюгів пульта управління, лінії зв'язку, лінії телефону, лінії модулів лінійних, лінії взаимоблокировки, ланцюга живлення датчика електродного і ланцюгів живлення електронних схем, а також застосуванням схем, що забезпечують обмеження потужності можливої іскри, за рахунок обмеження струму короткого замикання [4].
Для розширення функціональності апаратури САУКЛ та вирішення проблеми з перевантаженням приводу конвеєра і недоцільним економічним використанням розробляється пристрій на мікропроцесорній основі, яке буде виконувати функцію регулювання швидкості конвеєрної лінії в залежності від вступника вантажопотоку на стрічку. Структурна схема приведена на рисунку 5.
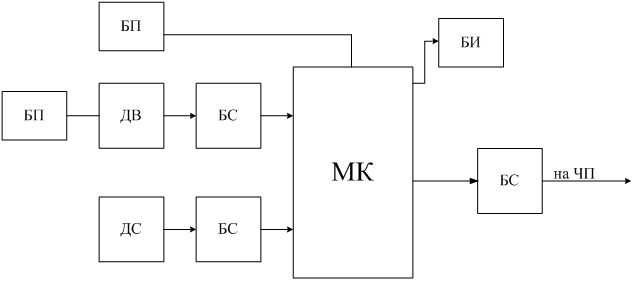
Рисунок 5 – Структурна схема пристрою регулювання і формування заданої швидкості
На рисунке 5 показані:
БП – блок живлення; БС – блок узгодження; ДВ
– датчик ваги;
ДС – датчик швидкості; МК – мікроконтролер; БИ
– блок індикації;
Пристрій формування заданої швидкості (УФС) складається з блоку датчиків, мікропроцесора і блоку сигналізації включає в себе LCD дисплей. Основою пристрою є мікроконтролер. Датчик ваги розташовується на попередньому конвеєрі, це дає можливість швидше реагувати на зміни вантажопотоку. Використовується тензорезистивного датчик ваги, вони рекомендовані до використання в умовах шахти. Сигнали від датчика швидкості (через гальванічну розв'язку) і датчика ваги (через інтерфейс струмова петля) віддаються на аналоговий вхід мікроконтролера. Модуль АЦП, який входить до його складу перетворює дану інформацію в двійковий код з метою подальшої обробки. Відбувається обчислення фактичного вантажопотоку на стрічці і порівняння його з заданим. Залежно від різниці цих значень виробляється сигнал управління, який через інтерфейс RS-485 досягає кінцевого адресата – перетворювача частоти, до якого підключений електродвигун приводу конвеєра. Узгодження сформованого сигналу з RS-485 відбувається через перетворювач інтерфейсів. Для контролю роботи пристрою в блоці присутній рідкокристалічний індикатор, на який виводиться інформація про швидкість і продуктивності конвеєра. Кількість вугілля на стрічці, тобто маса надходить вантажу, є мінливих параметром, а швидкість – регульованим [6].
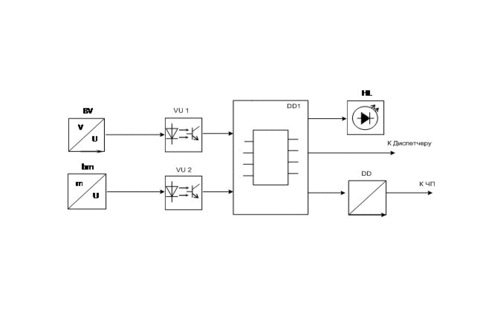
Рисунок 6 - Функціональна схема пристрою формування заданої швидкості (анімація: 7 кадрів, ітервал: 55 мс, розмір: 112 кбайт)
Діапазон регулювання швидкості конвеєра встановлюється в межах від 0,1 V до 1,0 V, де V – номінальна швидкість. Регулювання швидкості проводиться за сигналом УФС. При нульовій завантаженні стрічки швидкість її не перевищує 0,1 від номінальної. При наростанні вантажопотоку і досягненні рівня вантажу вище встановленої величини видається сигнал на збільшення швидкості стрічки. Швидкість стрічки буде збільшуватися до тих пір поки рівень вантажу не стане нижче встановленої величини. За рахунок зворотного зв'язку УФС – перетворювач проводиться автоматичне підтримання рівня вантажу на заданому рівні. УФС спільно з перетворювачем частоти повинен підтримувати сталість коефіцієнта відносини вантажопотік / швидкість.
Висновки
Було розглянуто процес автоматизації конвеєрної лінії, що складається з трьох дільничних і одного магістрального конвеєра. Було розроблено пристрій формування заданої швидкості стрічкового конвеєра, яке забезпечує плавне регулювання швидкості стрічки конвеєра, шляхом зміни частоти обертання електроприводу конвеєра, залежно від вступника на стрічку конвеєра грузопотока.Виведени залежності вхідного вантажопотоку та оптимальної для його кількості швидкості з метою забезпечення оптимального навантаження на привід конвеєра і досягнення більш ефективних енергетичних та економічних показників. Було обгрунтовано доцільність даного дослідження, сконструйована структурна, функціональна і принципова електрична схема УФС, проведено математичне моделювання. Розроблено методи з безпечної та безаварійної експлуатації УФС. Чи обгрунтовані фактори техніко-економічної доцільності прийнятих технічних рішень. Що довело доцільність розробленого пристрою.
При написанні даного реферату магістерська робота ще не завершена. Остаточне завершення: грудень 2014 року. Повний текст роботи та матеріали по темі можуть бути отримані у автора або його керівника після зазначеної дати.
Список источников
- Малиновский А. К. Автоматизированный электропривод машин и установок шахт и рудников: учебник для вузов / А. К. Малиновский. – М.: Недра, 1987. – 277 с.
- Шахмейстер Л. Г. Динамика грузопотоков и регулирование скорости ленточных конвейеров / Л. Г. Шахмейстер, В. Г. Дмитриев, А. К. Лобочева. – М.: Машиностроение, 1972. – 160 с.
- Полунин В. Т. Эффективность регулирования скорости шахтных конвейеров / В. Т. Полунин / Научные труды МГИ. – 1968. – № 53. – С. 87 – 95.
- Дмитриева В. В. Разработка и исследование системы автоматической стабилизации погонной нагрузки магистрального конвейера: дис. кандидата техн. наук: 05.13.06 / Дмитриева В. В. – М., 2005. – 162 c.
- Лукас В. А. Теория автоматического управления: учебник для вузов / В. А. Лукас. – М.: Недра, 1990. – 416 с.
- Справочник по автоматизации шахтного конвейерного транспорта / Н. И. Стадник В. Г. Ильюшенко С. И. Егоров и др. – К.: Техника, 1992. – 438 с.