Abstract
This abstract is used as an example, with the permission of Evgeniy Tatolov.
Original: http://masters.donntu.ru/2011/fknt/tatolov/diss/indexe.htm
Content
- Introduction
- 1. The relevance of the topic
- 2. Methods of manufacture,material for implants
- 2.1 Cobalt - chromium alloys in prosthetics
- 2.2 Titanium alloys
- Findings
- source List
Introduction
When we begin to think about the need prosthetics? Do I need to enlist the help of a dentist? First of all, very often you can say in front of the severely damaged teeth when it is not possible to save the tooth restorative materials then the tooth must be restored with a tab, followed by restoration with a crown.In addition, after removal of the tooth immediately raises the question of the prosthetic tooth for tooth extraction due to masticatory forces bend and neighboring nominated antagonists (the teeth of the other jaw opposite the remote) which leads to malocclusion and their closure, as well as to contribute to the development of side diseases. The best way out of this situation – prosthetics.
1. The relevance of the topic
Since the emergence of the first prosthesis was not enough time. During this period and changed the design and materials of manufacture. Today, there are two types of dentures: removable and fixed. But increasingly, patients prefer more modern mind – implantation. Modern dentures are different from the usual in our understanding dentures. They are invisible and have beautiful appearance. Dentures are an inexpensive and effective way to restore the dentition. Fixed dental prostheses include crowns and bridges. Such structures are made of different materials and varies their price. Apply with small loss the number of teeth.
2. Methods of manufacture,material for implants
According to the method of manufacturing the implants can be divided in two groups:
- factory production (standard);
- laboratory production (standard and individual);
the First group of implants can be purchased through a medical supply system and the second is made in the conditions a dental laboratory is additionally equipped with appropriate equipment" tools and materials.
depending on the material from which made implantaty can be used by various technologies: casting (CJC, cerebrals palladium alloys, titanium and its alloys, etc.), sintering (ceramics, cermet) mechanical or electro-spark machining (titanium, Nickel titanium, sapphire carbon and others), methods of powder metallurgy and self-propagating high temperature synthesis (SHS) of titanium, Nickel-titanium). Developed four of a method of manufacturing intraosseous implant tov from titanium and alloys based on titanium nickelide.
First method: standard or bespoke sizes by casting or machining are made of non-porous Foundation the implant, which is then applied to the porous coating by powder metallurgy or the SAF(Fig.1).
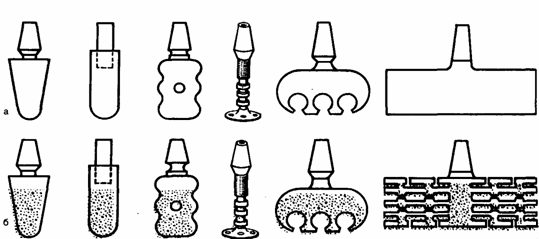
figure 1 – General view of the implants, manufactured by the first method. a — prior to application of the porous coating; b — after application.
the Second method: powder metallurgy or SAF is produced from titanium or niti porous cylindrical billet, plate tubular shape. From this workpiece is made the implant of any design method of mechanical or electric spark machining (Fig. 2).
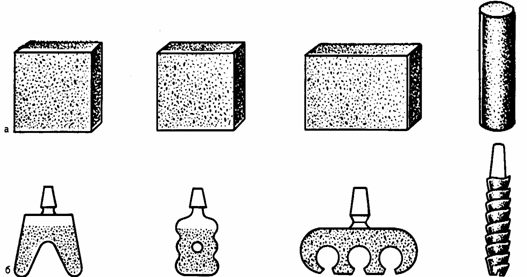
figure 1 – General view of the implants made by the second method. a — billet; b — implants made of theseblanks.
the Third way: using powder metallurgy or SAF immediately, eliminating the machining stage, get an implant according to standard or individual molds (Fig.3).
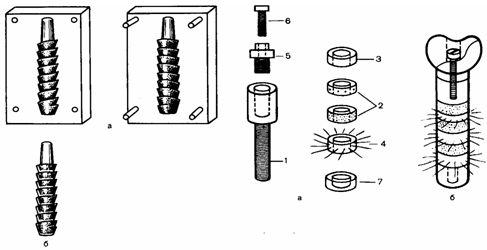
figure 1 – General view of the implants, manufactured by the third method. a-mold;b-implant.
the Fourth way is elementwise graft production of non-porous core, a porous root rings, cervical rings, rings with simulators of periodontal ligaments of wire with shape memory.
2.1 Cobalt - chromium alloys in prosthodontics
C — CR alloys for the first time in dental practice began to be used in the 30-ies, and from this time they successfully replaced gold alloys type IV in the manufacture of frames for partial dentures, primarily due to their relatively low cost is a significant factor in the manufacture of large castings.
Alloy contains cobalt (55-65%) and chromium (up to 30%). Other major alloying elements (molybdenum (4-5%) and less titanium (5%). Cobalt and chromium form a solid solution with chromium content up to 30%, the solubility limit of chromium in cobalt; chromium excess forming a second brittle phase.
In General, the higher the chromium content, the more resistant the alloy to corrosion. Therefore, manufacturers try to maximize the number of chromium, avoiding the formation of fragile second phase. Molybdenum is introduced for the formation of fine-grained structure of the material by creating a greater number of nucleation sites during the curing process. This has the added advantage, since molybdenum together with iron give a substantial strengthening of the solid solution. However, the grains are large enough, although their boundaries it is very difficult to determine because of the coarse dendritic structure of the alloy.
Carbon present only in small amounts, is an extremely important component of the alloy, because a slight changes in the quantitative content can significantly alter the strength, hardness and ductility of the alloy. Carbon can be combined with any other alloying element with the formation of carbides. A thin layer of carbides in the structure can significantly improve the strength and hardness of the alloy. However, too many carbides may cause excessive brittleness of the alloy. It is the problem for the dental technician, who needs to ensure that during the melting and casting the alloy are not absorbed an excessive amount carbon. The distribution of carbides depends on the casting temperature and the degree of cooling,since single crystals of carbides on the boundaries grains are better than their continuous layer around the grain. For a dental technician to work with these alloys are harder than gold alloys, because before casting, they must be heated to very high temperatures. Casting temperature of these alloys in the range of 1500-1550°C, and the associated with her casting shrinkage of approximately 2%. This problem was largely solved with the advent of equipment for induction casting and refractory molding materials for phosphate based. Precision casting suffers at such high temperatures, significantly limiting the use of these alloys, mainly for the manufacture of partial dentures.
hard Alloys conventional mechanical polishing method because of their high hardness. For internal surfaces of prostheses, directly adjacent to the oral tissues, the method of electrolytic polishing so as not to reduce the quality of the fit the prosthesis, but the outer surface has to be polished mechanically. The advantage of this method is that pure polished the surface is maintained over a long period of time, which is a significant advantage for removable dentures.
Lack of plasticity, coupled with inclusions of carbon, represents a particular challenge, particularly because these alloys prone to the formation of pores in the casting. When connecting these flaws can lead to breakage clasps of removable dentures. However, there are several properties of these alloys that make them almost ideal for the manufacture of frames for partial dentures. The modulus of elasticity Co — CR alloy is usually equal to 250 HPa, while for other alloys, this figure is in the range 70 to 100 GPA. Such a high modulus of elasticity has the advantage that the prosthesis, and particularly the shoulders clasp, can be made of the thinner cross-section, while maintaining necessary rigidity.
the Combination of this high rate of elastic modulus to density, which is about half lower than in gold alloys, significantly lighten the weight of the castings. This is undoubtedly a great benefit for patient comfort. The addition of chromium provides reception of corrosion-resistant alloys, which are used for the manufacture of many implants, including hip and knee joints. Therefore, it is safe to say that these alloys possess a high degree of biocompatibility. Some alloys also contain Nickel, which manufacturers add upon receipt of the alloy increased viscosity and reduced hardness. However, Nickel is known to the allergen, and its use may cause allergic reactions of the oral mucosa.
2.2 Titanium alloys
the Interest in titanium from the point of view of its use in the manufacture of fixed and removable dentures appeared simultaneously with the introduction of titanium dental implants. Titanium has a number of unique properties, including high tensile low density and biocompatibility. In addition, it was assumed that, if for the manufacture of crowns and bridges based on titanium implants, the use of a different metal, not titanium, it can lead to galvanic effect.
the opening of the element titanium is associated with the name Reverend William Gregor in 1790, but the first sample of pure titanium was obtained only in 1910. Pure titanium is produced from titanium ores (such as rutile) in the presence of carbon or chlorine. Obtained by heating TiCl4 recovering molten sodium with the formation of titanium sponge, which is then melted in a vacuum or in argon to get the billet (ingot) of metal. In the clinical aspect of most interest are the two forms of titanium. It is technically clean shape of titanium and titanium alloy—aluminum 6%and 4% vanadium.
Titanium— metal, tends to allotropic or polymorphic transformation from a hexagonal close-Packed structure (a) at low the temperature and structure of the BCC (N) at temperatures above 882°C. Pure titanium is actually an alloy of titanium with oxygen (0.5%). Oxygen is in solution, so that metal is the only crystalline phase. Elements such as oxygen, nitrogen and carbon have greater solubility in a hexagonal close-Packed structure and phase than in the cubic structure 3-phase. These elements form intermediate solid solutions with titanium and contribute to the stabilization of a-phase. Elements such as molybdenum, niobium and vanadium, act as R-stabilizers.
When added to titanium, aluminum and vanadium in small quantities, the strength of the alloy becomes higher than pure titanium Ti. It is believed that aluminum is a stabilizer and vanadium acts In stabilizer. When they are added to the titanium the temperature at which the transition occurs GC—G, decreases so that both forms can exist at room temperature. Thus, Ti—6% Al—4% V is a two-phase structure of the grains.
Pure titanium is a shiny white metal with low density, high strength and corrosion resistance. It is plastic and is an alloying element for many other metals. Titanium alloys are widely used in aviation industry and in the military field due to the high tensile strength (-500 MPa) and the ability to withstand the high temperatures. The modulus of elasticity of pure titanium including those. Those equal IN HPa, i.e. twice lower than the elastic modulus of stainless steel and cobalt-chrome alloy.
tensile Properties of pure titanium Tex.h.Ti largely depend on the oxygen content, and although the ultimate strength in tension, the constant strain rate and hardness increased with increasing oxygen concentration, all of this happens by reducing plasticity of the metal.
By doping titanium aluminum and vanadium may receive a wide range of mechanical properties of the alloy, exceeding properties of commercially pure titanium including those Those. Such alloys titanium is a mixture of a— and P-phases, where the OS phase is relatively soft and plastic, and R-phase harder and harder, although it has some plasticity. Thus, by varying the relative proportions of phases can get a wide variety of mechanical properties.
For the alloy Ti—6% Al—4% V can achieve higher tensile strength (-1030 MPa) than for pure titanium, which expands the scope of the alloy, including when exposed to heavy loads, for example, in the manufacture of partial dentures.
an Important property of titanium alloys is their fatigue strength. How pure titanium including those Those and the alloy Ti—6% Al—4%V have clearly certain limit fatigue S—N curve (stress—number of cycles), after levelling 10-10 cycles of the alternating voltage, the value of which is set at 40-50% below the ultimate tensile strength. Thus, teh. h. Ti should not be used in cases requiring fatigue strength above 175 MPa. On the contrary, for the alloy Ti—6% Al—4%, the average is about 450 MPa.
As is known, metal corrosion is the main cause of the destruction of the prosthesis and the occurrence of allergic reactions in patients under the influence of secreted toxic components. Titanium has become widely used because it is one of the most resistant corrosion of metals. Fully these qualities can be attributed to its alloys. Titanium is highly reactive that in this case, its strength, because the oxide formed on the surface (TiO2), extremely stable, and it provides passivation effect on the rest of the metal. High corrosion resistance of titanium in biological applications is well studied confirmed by many studies.
Casting of titanium alloys is a serious technological problem. Titanium has a high melting point (~1670°C), what makes it difficult to compensate for the shrinkage of the casting during cooling. Due to the high reactivity of metal casting, you must perform in vacuum or in an inert environment, which requires the use of special equipment. Another problem is the melt has a tendency to react with the mold of a refractory mold material, forming a layer of scale on the casting surface, which reduces the quality of the fit of the prosthesis. When designing dentures based on implants, you should to withstand a very tight tolerance to obtain a good fit to the implant. Otherwise you can break the retention of the implant in bones. In titanium castings is also often possible to observe internal porosity. Therefore, we use other technology to manufacture of dental prostheses made of titanium, such as CAD/CAM technology in combination with rolling and spark erosion method.
Conclusions
Treatment of teeth with technology of the 21st century allows you to save the native teeth in the long term. However, regular preventive dental visits is essential to dental health. If worse comes to worst, and to save the tooth failed, your dentist can offer You several different options for prosthetics. An outsider will never be able to see the denture in your mouth, even if You smile a broad smile. An experienced dentist will give You detailed advice regarding what method of prosthesis is most suitable for You and Your teeth. - Your task is not to make the wrong choice specialist.
Source List
- Руководство по ортопедической стоматологии/Под Р85 ред. В. Н. Копейкина. М.: Медицина, 1993. 496с.
- Гожников Г.И., Логинов В.А., Асташина Н.Б., Щербаков А.С., Конюхова С.Г. Реставрация твердых тканей зубов вкладками. М.: Медицина.-2002.-420с.
- Лачев Б.А., Ливанов В.А, Елагин В.И. Металловеденье и термическая обработка цветных металлов и сплавов.М.:-1981.-365с.
- Лудев С.Е. Металлы и сплавы, применяемые в ортопедической стоматологии.-Екатеринбург.-1995.-500с. .