Реферат по теме выпускной работы
Содержание
- Введение
- 1. Цель и задачи магистерской работы
- 2. Анализ эффективности применяющихся пусковых узлов ГБС
- 2.1. Схема ПБС с пусковыми узлами типа ВПУ-I и НПУ-I
- 2.2. Схема ПБС с пусковыми узлами типа ВПУ-II и НПУ-II
- 2.3. Схема ПБС с одноэлементным исполнением запорного устройства пусковых узлов
- 2.4. Схема ПБС с пусковыми узлами в виде составного запорного устройства
- 3. Задачи разработки новых пусковых узлов ГБС
- 4. Принципиальная схема предложенных пусковых узлов
- Выводы
- Список источников
Введение
Освоение минеральных ресурсов морских месторождений вызвано такими причинами как: нехватка руд, ограниченность, либо полное отсутствие каких-либо промышленных запасов полезных ископаемых на суше в пределах страны, а так же стремление к независимости от импорта необходимого сырья.
Для освоения морских месторождений необходимо пробурить большое количество поисково-разведочных и структурно-картировочных скважин на твёрдые полезные ископаемые и инженерно-геологических скважин для проектирования и строительства специальных сооружений на море. Такие скважины бурят на глубину до 50 м на небольших площадях акваторий. Важным условием при выполнении геологоразведочных задач является наиболее быстрое и рентабельное выполнение работ в сложных метеорологических и гидрологических условиях моря [1].
Решением этих задач является внедрение лёгких технических средств (ЛТС), максимально адаптированных к штатному оборудованию экономичных судов общетехнического назначения. Что предполагает развитие забортной бесколонной технологической схемы бурения скважин. А так же такая схема предусматривает полное исключение такого габаритного и энергоёмкого оборудования как: буровой станок, буровая вышка, станции для приготовления, хранения и очистки бурового раствора и т. д.
Для Украины важность развития отмеченной технологической схемы, определяется наличием достаточного количества неспециализированных судов (морских буксиров, спасательных судов и др.), эксплуатационно-технические возможности которых приемлемы для реализации забортной технологической схемы бурения, а также приоритетом в создании многофункциональных гидроударных буровых снарядов (ГБС), производительность которых значительно превосходит известные зарубежные аналоги [6]
По данным [2] использование ЛТС при бурении на шельфе обеспечивает высокий уровень сохранности геологического материала (по глинистым породам 90...100%, по остальным породам в т. ч. по пескам 88–95%), что является одним из важнейших показателей качества выполнения инжинерно-геологических исследований.
Технические средства, применяемые для обеспечения бурения скважин до 50 м для более полного использования резервов ГБС реализуют цикл бурения скважины, который состоит из последовательно повторяющихся на ее интервалах двух способов разрушения пород:
- C отбором керна, за счет частотно-ударного погружения бурового снаряда в донные осадки на заданную глубину;
- Без отбора керна, за счет размыва пород или ударно-гидромониторного их разрушения на ранее пройденном или заданном отрезке ствола скважины [1].
Такая схема позволяет не закреплять стенки скважины обсадными трубами и тем самым сократить время и затраты на проведение скважины.
На современном этапе актуальность технического обеспечения бурения скважин глубиной до 50 м
возросла и в значительной мере определяется производственными планами отечественных специализированных
предприятий ГАО Черноморнефтегаз
и ГГП Причерноморгеология
, для которых наметившаяся тенденция роста
объемов бурения обусловлена перспективой выполнения государственных программ, направленных на изучение
Украинского сектора шельфа Черного и акватории Азовского морей.
В соответствии с программой Освоение углеводородных ресурсов Украинского сектора Черного и Азовского морей
(1996 г.)
ГАО Черноморнефтегаз
предусмотрено продолжение геологоразведочных работ на перспективных участках углеводородных месторождений,
а также в районах открытых и действующих газовых месторождениях Азовского и Черного морей. Реализация намеченных проектов
предполагает проведение широкомасштабных работ по бурению сотен скважин глубиной 6–50 м,
с целью инженерного изучения морского дна для получения прочностных характеристик грунтов, слагающих основание для построек специальных морских сооружений [3, 4].
Исходя из вышеизложенного, техническое обеспечение для бурения скважин глубиной до 50 м, имеет высокую актуальность и его совершенствование имеет большое значение в освоении минеральных и углеводородных ресурсов морских месторождений полезных ископаемых.
1. Цель и задачи магистерской работы
Цель работы состоит в разработке гидравлической взаимосвязи и обосновании параметров пусковых узлов и гидродвигателя гидроударного бурового снаряда для повышения эффективности комбинированного разрушения пород в технологическом цикле процесса многорейсовой проходки скважин глубиной до 50 м.
Задачи исследований:
– обоснование схемы пусковых узлов как образующих элементов гидроударного бурового снаряда, обеспечивающих технологическую схему многорейсовой проходки скважин в условиях морских акваторий;
– разработка метода инженерного расчета и определение гидромеханических характеристик верхнего пускового узла, обеспечивающих устойчивое состояние его образующих элементов в режиме комбинированного разрушения пород на интервале бурения скважины без отбора керна;
– экспериментальные исследования нижнего пускового узла для выбора его параметров и режимов управления при блокировании и разблокировании каналов пропуска жидкости в керноприемную трубу;
– разработка чертежей на усовершенствованный вариант гидроударного бурового снаряда для многорейсового бурения скважин в условиях морских акваторий.
Объект исследований – технологические схемы и технические средства бурения скважин глубиной до 50 м в условиях морских акваторий.
Предмет исследований – параметры и рабочие процессы пусковых узлов, обеспечивающие комбинированный способ разрушения пород, при многорейсовой проходке скважин гидроударными буровыми снарядами.
2. Анализ эффективности применяющихся пусковых узлов ГБС
В соответствии с принципиальным назначением пусковые узлы в составе ГБС являются контуром питания гидроударной машины и одновременно выполняют функции переключателя, с перекрытием рабочих камер гидроударника и открытием каналов для свободного прохода жидкости на забой скважины в режиме гидромониторного разрушения осадков.
В соответствии с общепринятыми признаками классификации, запорные элементы пусковых узлов гидроударных буровых снарядов относятся: по назначению – к пусковым; по конструкции – к пружинным; по характеру работы: клапан – к нормально открытым; плунжерный золотник – к нормально закрытым; по источнику срабатывания – от давления набегающего потока жидкости [1].
В настоящее время обобщающим критерием разработки пусковых устройств ПБС, является характер фиксированного положения пусковых узлов в зависимости от расхода жидкости в гидросистеме (Q). С одной стороны, ВПУ обеспечивает поступление номинального количества воды (Qном) только в гидроударный механизм. При этом НПУ закрывает поступление воды в керноприемную трубу и одновременно пропускает отработанную в гидроударнике жидкость в затрубное пространство (работа в режиме отбора керна). С другой стороны (на фазе размыва) – ВПУ исключает доступ увеличенного количества воды (Q1) в рабочие камеры гидроударника и одновременно НПУ направляет весь поток жидкости (Q1>Qном) в керноприемную трубу, и далее через кернорватель–насадку на забой скважины [4].
В целом, по отмеченному признаку можно реализовать ряд комбинаций c различным обеспечением положений элементов запорного устройства пусковых узлов (табл. 1).
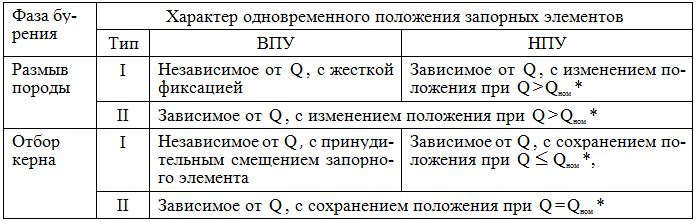
Таблица 1 – Комбинации обеспечения положений применяемых распределительных (запорных) элементов пусковых узлов ПБС.
2.1. Схема ПБС с пусковыми узлами типа ВПУ-I и НПУ-I
Исполнение пусковых узлов по первому варианту (ВПУ-I и НПУ-I) использовано в первых конструкциях установок УМБ-130 и УМБ-130М (рис. 1)
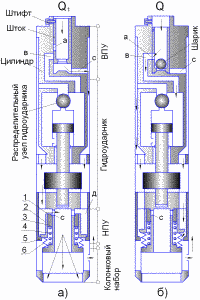
Рисунок 1 – Схема ПБС с пусковыми узлами типа ВПУ-I и НПУ-I.
НПУ-I соединяется с нижней наковальней посредством штока 1. Нижняя ступень штока является уплотнительной втулкой для внутренней (керноприемной) трубы колонкового набора. На штоке 1 концентрично установлены плунжерный золотник 3 с пружиной 4, и клапан 2, опирающийся на пружины 6. В корпусе НПУ-I выполнено седло 5.
В режиме бескерновой проходки ствола скважины в нагнетательный трубопровод подается заданный расход жидкости Q1, соответствующий условию размыва осадков. Элементы ВПУ-I сохраняют исходное положение (рис. 1, а). Жидкость через полый шток, канал (с) и межтрубному пространству гидроударника направляется в камеру (д) НПУ-I, что приводит к усилению нагрузки на клапан 2, который, преодолевая сопротивление пружин 6, смещается вниз. После посадки клапана 2 на седло 5, силой давления потока в камере (д) перемещается поршень–золотник 3 с открытием боковых окон (с) в штоке 1. В таком положении элементов НПУ-I жидкость поступает внутрь керноприемной трубы колонкового набора, и далее на забой скважины, обеспечивая размыв породы [1].
Для перехода ПБС в режиме отбора керна (рис. 1, б), в нагнетательную линию с помощью питателя сбрасывается пробка-шарик. После посадки шарика в седло штока в нагнетательном трубопроводе повышается давление, сила которого обеспечивает срез штифта. Шток опускается вниз, перекрывая канал (с). Одновременно совмещаются окно (в) и канал (а), через которые жидкость направляется в цилиндр гидроударника (рис. 2, б). Происходит запуск гидроударника с последующим выводом его на режим эффективной работы путем увеличения подачи жидкости до Qном [5].
Для хорошо размываемых интервалов скважины, где достаточным является разовое срабатывание
ВПУ при переходе от размыва пород на фазу пробоотбора, исполнение ВПУ-I вполне оправдано
с точки зрения обеспечения надежности блокирования гидроударника на фазе размыва. Одновременно ВПУ-I
обеспечивает гарантированное нерегулируемое перемещение и удержание штока в нижнем положении с
разделением рабочих камер гидроударника с затрубным пространством на фазе бурения с отбором керна
независимо от расхода жидкости. В то же время, бескерновая проходка интервалов, сложенных глинистыми
породами обусловливает необходимость перехода на нетехнологичный клюющий
способ бурения.
Вышеприведенная схема подразумевает усложнение конструкции нагнетательного шланга, для сброса шарика-пробки. Дополнительные трудности связаны с особенностями выполнения технологических операций перезарядки ВПУ-I. Возвращение элементов запорно-регулирующего устройства ВПУ-I в исходное положение (рис. 1, а), соответствующее режиму размыва осадков, возможно только после подъема установки с последующим демонтажем нагнетательного шланга и троса, отсоединением от ПБС грузового переходника, извлечением сброшенного шарика и размещением его в камере питателя, перемещением и шплинтовкой штока в исходном положении. По хронометражным данным, время на подготовку бурового снаряда к очередному спуску за счет увеличенной трудоемкости перезарядки ВПУ и питателя составляет более 20% в общем объеме подготовительно-заключительных операций [5].
Облегчение обвязки насоса путём исключения питателя для сброса шарика, а также, исключение потерь времени на перезарядку ВПУ принципиально решается при использовании комбинации пусковых узлов второго типа. Узлы ВПУ-II и НПУ-II структурно являются элементами гидравлической системы бурового снаряда и работают в автоматическом режиме взвода с дистанционным включением в нужный режим работы, за счет изменения подачи жидкости в нагнетательную линию.
2.2. Схема ПБС с пусковыми узлами типа ВПУ-I и НПУ-I
Схема варианта ПБС с комбинацией ВПУ и НПУ по типу II приведена на рис. 2. Впервые предложенная схема исполнения пусковых узлов применена в опытном варианте установки УМБ-130 [4].
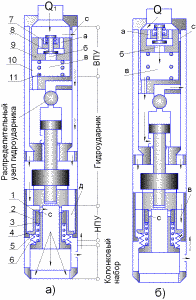
Рисунок 2 – Схема погружного бурового снаряда с пусковыми узлами типа ВПУ-II и НПУ-II.
При переходе на головную операцию (бурение с нормативным отбором керна), распределительные элементы пусковых узлов должны занять исходное положение, соответствующее рис. 2, б. Эта операция обеспечивается путем снижения расхода жидкости, следствием чего является уменьшение силы давления на элементы запорных устройств ВПУ-II и НПУ-II [1].
Для рассмотренных схем открытым остается вопрос, связанный с целесообразной необходимостью замены общего принципа обеспечения срабатывания и взаимодействия элементов пусковых узлов за счет разработки конструкций с уменьшенным количеством элементов и их настроечных параметров [1].
Особенностью технологии проходки скважины с отбором керна, в зависимости от геологического разреза, является то, что рабочие параметры гидроударника на интервале бурения либо форсируются, либо уменьшаются изменением подачи жидкости в нагнетательный трубопровод. Поэтому, учитывая наличие единой приводной линии для пусковых узлов и гидроударника, процесс подготовки ПБС к бурению обусловливает необходимость перенастройки, как ВПУ, так и НПУ на заданный расход жидкости. Для предотвращения непроизвольного изменения положений пусковых узлов в процессе пробоотбора, необходимо обеспечивать диапазон расходов Q...1,5Qном больше, чем Q1 [4]. Это соотношение справедливо как для комбинации с пусковыми узлами типа I, так и с пусковыми узлами типа II.
2.3. Схема ПБС с одноэлементным исполнением запорного устройства пусковых узлов
Для уменьшения количества элементов пусковых узлов, а так же уменьшения времени сборки и настройки ПБС обоснованным явился выбор принципиальной схемы пусковых узлов с одноэлементным запорным устройством (рис. 3).
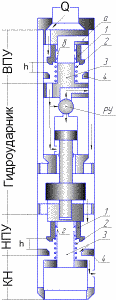
Рисунок 3 – Схема ПБС с одноэлементным исполнением запорного устройства пусковых узлов.
Как показали проведенные ДонНТУ лабораторные и опытно-промышленные исследования, применение одноэлементной конструкции существенно упростило настроечные операции пусковых узлов, с обеспечением возможности многократного изменения направления движения жидкости в зависимости от необходимого способа разрушения пород по интервалу скважины. В то же время, нерегулируемость высоты раскрытия щели (h), связанная с условием необходимого открытия окон штока, а также увеличенная результирующая площадь клапана (без возможности широкого интервала ее изменении из-за ограничений к сечению каналов штока, пропускающих через себя поток жидкости) обусловливали повышенные требования к силовым параметрам возвратных пружин. Отмеченный факт являлся также причиной повышенной трудности возврата клапана в исходное положение, вследствие значительной величины силы давления жидкости, формирующейся на его площади в направлении действия набегающего потока жидкости [1].
2.4. Схема ПБС с одноэлементным исполнением запорного устройства пусковых узлов
Отмеченный в пункте 2.3 недостаток явился причиной поиска решений, направленных на увеличение силы возврата запорно-регулирующей системы (ЗРС) пусковых узлов, прежде всего, на фазе оперативного разблокирования работы гидроударника. В результате, сохранив условие одноэлементной настройки, предложена принципиальная схема ЗРС в виде концентрично размещенных относительно друг друга клапана 5 и плунжерного золотника 1 (рис. 4).
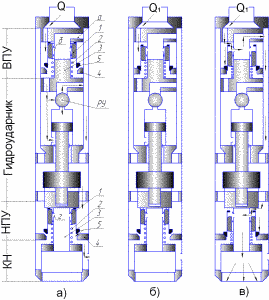
Рисунок 4 – Схема ПБС с пусковыми узлами в виде составного запорного устройства.
Исходное положение элементов пусковых узлов отмечено на рис. 4, а. Плунжерный золотник 1 и клапан 5 усилием пружины 2 удерживаются в верхнем положении. Через щель между клапаном 5 седлом 4 в рабочую камеру гидроударника обеспечивается подача жидкости, соответствующая номинальному значению Q для его запуска и эффективной работы. На этой фазе сила давления жидкости на площадь запорного устройства пусковых узлов компенсируется силой предварительного натяжения пружин 2.
Для блокирования гидроударника на фазе реализации размыва породы, расход жидкости в гидросистеме увеличивается до заданной величины, что приводит к смещению системы «клапан-плунжерный золотник» до посадки клапана 5 на седло 4 (рис. 5, б). В дальнейшем имеет место самостоятельное движение поршня-золотника с дополнительным сжатием пружины 2, до полного открытия окон (б), выполненных в штоке 3 (рис. 5, в) [1].
Для возвращения запорного устройства в начальное положение, расход жидкости уменьшается, что приводит к снижению усилия, действующего на поршень-золотник, который пружиной ускоренно переместится вверх. При контакте золотника с упорными выступами клапана 5, последний, воспринимая суммарное действие силы пружины и силы удара, совместно с плунжерным золотником вернется в верхнее исходное положение.
В таком исполнении пусковых узлов появилась возможность изменять высоту щели клапана независимо от процесса открытия окон штока. В цикле открытия окон участвует только подпружиненный поршень-золотник, площадь которого на этапе проектирования может варьироваться изменением внутреннего сечения клапана. За счет уменьшения рабочей площади золотника появляется возможность для снижения силы набегающего на него потока. Кроме того, при перемещении золотника вверх имеет место ударное взаимодействие золотника и клапана, что существенно повышает надежность выполнения условия возврата ЗРС в исходное положение [1].
Несмотря на достигнутую результативность установки УМБ-130М её потенциальные возможности не реализованы. Выявленные в процессе эксплуатации установки недостатки обусловлены нерешенными взаимосвязанными задачами технологического плана, а также инженерного и научного характера.
К технологическим можно отнести ряд задач, связанных с выполнением приемов работы непосредственно
на фазе разрушения пород, прежде всего при размыве прослоев и интервалов плотных песков и глинистых пород.
Так, при статическом положении ПБС на забое время размыва 1 м плотных пород составляло более 1 часа.
Увеличить скорость размыва удавалось только после перехода на клюющий
способ бурения,
сущность которого заключалась в периодических поднятиях и сбрасываниях ПБС на забой с высоты 0,5–1 м с
последующим вымыванием сформированного столбика керна из колонковой трубы.
Причем, при проходке плотных глинистых пород продуктивность клюющий
способа резко снижалась из-за
формировании на забое опорного потока жидкости, приводящего к снижению скорости падающего ПБС на забой скважины.
Кроме того, [1] способ проходки интервалов скважины наряду с не технологичностью выполнения работ
при запредельных нагрузках на грузоподъемную систему, нередко являлся причиной осложнений и аварийных
ситуаций в скважине. Подъем и сбрасывание ПБС неизбежно приводило к обрыву скоб, закрепляющих к тросу
нагнетательный шланг. Это в конечном итоге не только повышало трудоемкость извлечения шланга на палубу,
но и в ряде случаев, приводило к аварийному подъему донного основания на шланговом жгуте,
образовывающемуся ниже устья скважины. [1].
К технологическим недостаткам можно также отнести ухудшающиеся условия очистки ствола скважины над буровым снарядом на фазе пробоотбора. В процессе бурения с отбором керна в скважину направлялся поток жидкости, соответствующий номинальному расходу для работы гидроударного механизма, количественно значительно меньше необходимой для эффективного размыва и очистки ствола скважины. В этой ситуации над ПБС ствол скважины практически не формируется и насыщается разжиженным песком, который при кратковременном отключении насоса в период срыва керна быстро оседает. Поэтому процесс подъема ПБС, особенно при прохождении мощных участков песка, после окончания рейса с отбором керна осложняется повышенными усилиями извлечения, и сложными прихватами бурового снаряда [1].
В ходе испытаний УМБ-130М проводимых представителями ДонНТУ Существенные потери времени обусловливались и несовершенством конструкции гидродвигателя гидроударного механизма. Незащищенность гидродвигателя ПБС от попадания в него абразивных частиц шлама в период спуска в скважину и на фазе гидроразмыва пород в ряде случаев приводила к отказам запуска гидроударника, и, как следствие, к не санкционированному подъему ПБС из скважины. Кроме того, соотношение параметров гидродвигателя обеспечивало достаточные частотносиловые характеристики при расходах жидкости от 300 до 340 л/мин и давлении в системе 3,5–4 МПа, что нередко, при энергетической зависимости от ограниченного судового энергоисточника являлось не только предельно допустимым, но и невозможным [1].
Перечисленные выше технологические недостатки в общем случае устраняются принятием инженерных решений, в частности, модификацией пусковых узлов ГБС.
Одной из наиболее важных задач разработки новых пусковых узлов ГБМ, является в получение прогнозируемых режимов управления и положительных показателей надежности ВПУ-II и НПУ-II с упрощенной схемой их настройки на режим срабатывания ЗРС.
3. Задачи разработки новых пусковых узлов ГБС
По данным [1], при эксплуатации ПБС-127 в составе установок УМБ-130 и УМБ-130М с борта СО/ССН
Нефтегаз 68
на газовых месторождениях шельфа Черного моря при бурении скважин со сложным
геологическим разрезом возникали трудности, обусловленные нарушением условия синхронного срабатывания
ЗРС нижнего и верхнего пусковых узлов в диапазоне расходов жидкости Q...Q1.
При заложенных соотношениях параметров двигателя гидроударного механизма ПБС-127, значения энергии удара (E) и частоты ударов (n) для разрушения, прежде всего, встречающихся по разрезу ствола скважины твердых пород, обеспечиваются при увеличенных расходах жидкости.
В литературе [4] утверждается что, технологически благоприятным с надежным контро-лем состояния запорно-регулирующих систем ВПУ-II и НПУ-II является соблюдение соотношения Qср0,3Q. Для форсированных режимов работы с принятым исполнением гидродвигателя ПБС-127, рекомендуемая величина предполагает необходимость выполнения условия Qф>400 л/мин. Учитывая ограниченность судового энергообеспечения, применение такого уровня Qф, являющегося фактором увеличения мощности привода насоса, является затруднительной.
Поэтому сумма задач, связанных с разработкой ВПУ, была дополнена вопросами параметрической оптимизации гидроударного механизма, для адаптации его привода к характеристи-кам наиболее часто применяющихся буровых насосов, с соблюдением условий: Qср0,3 и Qф=300 л/мин.
Принципиальный характер имеют задачи, обусловленные необходимостью совершенствования кинематики и принятия выгодных конструкций системы «ВПУ-гидроударный механизм-ПУ». При этом гидроударный механизм, как наиболее изученный и отработанный в плане выбора схемы, кинематики и конструкции узел системы можно рассматривать как базу, для разработки структуры погружного бурового снаряда. Наименее изученными и неподготовленными к эксплуатации являются пусковые узлы бурового снаряда, которые функционально являются образующими элементами для обеспечения самой схемы многорейсового бурения скважин.
В работе [5], отмечена низкая надежность управления пусковыми узлами, обусловленная, прежде всего, несовершенством их конструкции и отсутствием обоснованных рекомендаций по выбору диапазона границ расхода жидкости, необходимого для оперативного управления процессом срабатывания узлов на фазах блокирования или разблокирования гидроударника. Как следствие, не исключались случаи неконтролируемого срабатывания, прежде всего, нижнего пускового узла на фазе отбора керна, особенно на участках проходки твердых грунтов, при повышении частотно-энергетических параметров гидроударника увеличением подачи насоса. Это приводило к открытию доступа жидкости в керноприемную трубу, что в свою очередь нарушало структуру керна, или полностью вымывало его из керноприемной трубы. Как следствие, инженерно-геологическая задача скважиной не решалась.
Поэтому задача расширения показателей назначения установок предполагает разработку новых технических предложений, направленных на более полную реализацию возможностей гидроударных буровых снарядов и обусловливают принципиальность научных и инженерных задач, связанных, прежде всего, с обеспечением повышенной надежности пусковых узлов, как элемента, определяющего саму возможность многорейсового бурения скважин.
Наиболее актуальной становится задача, связанная с созданием ВПУ и НПУ, исключающих необходимость применения «клюющего» способа проходки интервалов скважины, и структурно являющимися элементами бурового снаряда. В этом отношении перспективным можно считать направление, связанное с разработкой пусковых узлов с автоматическим режимом взвода при многократном дистанционном способе включения их в нужный режим работы. Срабатывание пусковых узлов на фазе отбора керна должно происходить на увеличенных расходах жидкости, при одновременном снижении нагрузки на гидродвигатель гидроударной машины без снижения подачи жидкости в скважину.
При достаточно высокой степени надежности разработанных пусковых узлов бурового снаряда ГБС-127 и относительной простоте получения обоснованных настроечных характеристик для их срабатывания при блокировании и разблокировании гидроударника, техническая реализация и технология бескернового бурения плотных пород не является совершенной. В перспективе, следует рассматривать разработки, требующие не только нового подхода к выбору конструкции и схемы управления ЗРС пусковых узлов в структуре ГБС, но и в корне изменить характер разрушения пород.
Анализ проведенных исследований и практические результаты выполненных разработок приведённых в [1] показали, что эффективной альтернативой бескерновой проходки интервалов скважины может служить способ, основанный на использовании гидромониторного эффекта в сочетании с непрерывными частотно-ударными нагрузками на забое, формирующимися гидроударным механизмом.
Эти моменты ставят задачу создания конструкции универсального пускового узла,
обеспечивающего постоянную работу гидроударника в течение всего цикла проходки скважины
с возможностью быстрого и эффективного разблокирования механизма на этапе отбора керна.
Первый опыт реализации задачи получен при проектировании бурового снаряда ГБС-108,
разработанного на основании технического задания ГГП Причерноморгеология
.
4. Принципиальная схема предложенных пусковых узлов
Разработанный снаряд ГБС-108 (рис. 5) выполнен с одинарным колонковым набором длиной 2,5–3 м и свободно размещенным внутри него пластиковым вкладышем 10, имеющим внутренний диаметр не более 88 мм.
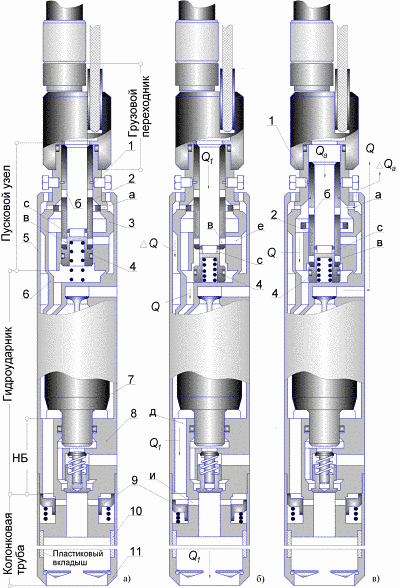
Рисунок 5 – Принципиальная схема гидроударного бурового снаряда ГБС-108.
Конструкция и параметры двигателя гидроударника соответствуют принятым для ГБС-127. Отличительной особенностью разработки является использование в структуре нового ГБС универсального пускового узла (УПУ), обеспечивающего постоянное разблокированное состояние гидроударника с технической возможностью бескерновой проходки ранее пройденного или заданного участка скважины за счет одновременно действующих гидромониторных и частотно-силовых нагрузок, формирующихся на забое скважины при работающей гидроударной машине.
УПУ размещается в цилиндре распределительного переходника 3 и структурно включает два взаимосвязанных элемента: патрубок 2, с разнесенными по его длине радиальными каналами (б) и (в), и подпружиненный плунжерный золотник 4 с калиброванными отверстиями (с).
В режиме бескернового разрушения осадков патрубок зафиксирован штифтами 1. Расход жидкости Qф устанавливается на уровне 300–320 л/мин. Набегающим потоком плунжерный золотник 4 смещается вниз (рис. 5, б). Через отверстия (с) в рабочие камеры гидроударника направляется часть жидкости Q, обеспечивая его запуск и работу. Одновременно, через освобожденные отверстия (в) и радиальные каналы (е), доля жидкости Qср=Q1–Q попадает в кольцевой зазор между корпусами 5 и 6, и далее, через каналы (д) нижней наковальни 8, направляется в полость подпружиненного обратного клапана 9. Гидравлическая сила набегающего потока перемещает клапан 9 вниз, открывая окна (и). Жидкость в количестве Q1 поступает в керноприемную трубу 10 и далее, через лепестки-насадки башмака 11, на забой скважины.
Для перехода на режим отбора керна подача жидкости в гидросистему увеличивается до Qа=380 – 400 л/мин для среза фиксирующих штифтов 1. Процесс сопровождается смещением патрубка 2 вниз с последующим блокированием канала (в) и отверстий (с), открытием делительных окон (а), через которые выполняется сброс части жидкости Qа.ср=Qа–Q в скважину.
С помощью регулировочного вентиля гидроударник выводится на режим эффективного погружения колонкового набора в породу при номинальном или форсированном расходе Q, с повышенной интенсивностью потока над ГБС, вследствие соблюдения условия Qа>Q.
Включение в состав ГБС-108 обратного клапана 9, исключает возможность всасывания жидкости из полости бойка 7 при работе насосного блока, и предотвращает попадание в полости гидроударного механизма песка и частиц шлама при спуске снаряда в скважину. Принцип работы устройства изображен на рисунке 6.

Рисунок 6 – Принцип работы устройства
Рисунок анимирован. Объем – 91 Кб.; количество кадров – 5; время задержки – 0,4 с.; количество повторений – бесконечно.
Выводы
Приведены и обоснованы схемы и параметры существующих пусковых узлов гидроударных буровых снарядов для бурения в морских акваториях.
В процессе выполнения магистерской работы разработана изменённая конструкция пусковых узлов, которые обеспечивают более быструю и рациональную проходку скважин и отбор проб.
Наибольшая выгода от нового решения достигнута вследствие исключения из цикла бурения клюющего
способа бескерновой проходки участков плотных и твердых пород при более рациональном
способе разрушении пород, в виде одновременно формирующихся на забое скважины гидромониторных и
частотно-силовых нагрузок, при работающем гидроударном механизме.
Кроме того, существенно повышена надежность контроля срабатывания пускового узла при полном разблокировании гидроударника на фазе отбора керна.
При написании данного реферата магистерская работа еще не завершена. Окончательное завершение: октябрь 2015 года. Полный текст работы и материалы по теме могут быть получены у автора или его руководителя после указанной даты.
Список источников
- Калиниченко О. И, Хохуля А. В., Зыбинский П. В., Каракозов А. А. Установки для бесколонного бурения скважин на морских акваториях. – Донецк: «Світ книги», 2013. – 163 с.
- Новые возможности и продуктивность легких гидроударных установок для бурения инженерно–геологических скважин на морских акваториях // Калиниченко О. И., Хохуля А. В., Комарь П. Л., Тельбиш М. Ю., Мартыненко И. И. // Сб. научн. трудов. – Вып. 15. – Киев: ИСМ им. В. Н. Бакуля НАН Украины, 2012. – с. 120–125.
- Возний В. Р., Голубков С. В. Освоєння шельфу – нафтогазове майбутнє України. // Науковий вісник Івано-Франківського технічного університету нафти і газу 2(11). 2005. – с. 56–58.
- Калиниченко О. И., Зыбинский П. В., Каракозов А. А. Гидроударные буровые снаряды и установки для бурения скважин на шельфе. – Донецк:
Вебер
(Донецкое отделение), 2007. – 276 с. - Калиниченко О. И., Хохуля А. В. Основные проблемы и пути совершенствования техники и технологи многорейсового бурения скважин на морских акваториях // Науковий вісник. №7, Національного гірничого університету. Науково технічний журнал. Дніпропетровськ, 2009. С. 45–50.
- Фальков И. М., Бабич В. А., Хамидуллин Р. Г., Лисагор О. И. Современное состояние техники и технологии морского инженерно-геологического бурения // Труды ВНИИморгео. Обзор. – Рига, 1986. – 152 с.
- Калиниченко О. И., Каракозов А. А., Зыбинский П. В. Разработка погружных гидроударных снарядов для бурения подводных разведочных скважин со специализированных плавсредств // Сб. научн. трудов. – Вып.8. – Киев: ИСМ им. В. Н. Бакуля НАН Украины, 2005. – 180 с.