Реферат по теме выпускной работы
Содержание
- Введение
- 1. Актуальность темы
- 2. Цель и задачи исследования, планируемые результаты
- 3. Основной раздел
- 3.1 Описание конструкции манипулятора
- 3.2 Обзор типов отсечных элементов для ввода в ванну кислородного конвертера
- 4. Анализ проведенных исследований по теме
- Выводы
- Список источников
Введение
При производстве стали в кислородном конвертере образуется слой шлака на поверхности зеркала металла, который при выпуске плавки попадает в сталеплавильный ковш. Наличие конвертерного шлака в сталеплавильном ковше значительно понижает качество производимой продукции. Основные негативные последствия попадания шлака из конвертера в сталеразливочный ковш это: повышение общего содержания кислорода в стали из–за высокого уровень FeO и МnО в шлаке; шлак образует толстый слой на поверхности металла, который мешает проведению операций по внепечной обработке металла в ковше; появляется необходимость в использовании машин для скачивания шлака из ковша; увеличение степени рефосфорации, повышенный угар ферросплавов; увеличение расхода на раскислители (алюминия, ферросилиция и пр.); снижение сроков службы футеровки ковшей [1].
В настоящее время на металлургических предприятиях используют такие системы удержания шлака как: газодинамическая система отсечки шлака; при помощи шиберного затвора; с использованием отсечных элементов поплавкового типа, вводимых в полость кислородного конвертера. В большинстве случаев обнаружение шлака в струе металла производится визуально оператором, контролирующим процесс. Так, например, при переливе металла из конвертера в сталеразливочный ковш оператор, управляющий сливом конвертера, наблюдает за струей металла и по изменению ее цвета, а также по изменению шума, создаваемого падающей струей, судит о вовлечении шлака и поворачивает конвертер в исходное вертикальное положение. Результат в данном случае сильно зависит от квалификации оператора, а условия процесса истечения не позволяют точно определить момент проникновения шлака даже опытному специалисту. По комплексу технико–экономических показателей, позволяющих оценить эффективность известных способов бесшлакового выпуска стали в условиях кислородно–конвертерного производства, считается наиболее перспективным тот, который предполагает осуществление запирания выпускного канала сталеплавильного агрегата специальным элементом поплавкового типа, вводимого в его ванну с помощью механического манипулятора для ввода отсечных элементов в ванну кислородного конвертера [2].
1. Актуальность темы исследования
Для получения качественной стали в кислородном конвертере необходимо минимизировать количество шлака, который попадает в сталеразливочный ковш при выпуске плавки. Это остается актуальной задачей в современном конвертерном сталеплавильном производстве. Одним из наиболее эффективных способов отсечки конечного конвертерного шлака считается применение отсечных элементов поплавкового типа, которые вводятся в ванну конвертера специальными механическими манипуляторами. Выявление наиболее рациональная форма отсечных элементов позволит увеличить процент не допущенного в сталеразливочный ковш шлака, этой проблеме собственно и посвящены исследования данной магистерской работы.
2. Цель и задачи исследования, планируемые результаты
Проанализировав существующие типы отсечных элементов, особенности их состава и применения, можно сделать вывод, что наиболее важной задачей дальнейших исследований является определение рациональной формы боковой поверхности отсечного элемента в форме стрелки
,
которая позволит получить высокую эффективность отсечки шлака, сократит расходы при вынужденном использовании «универсальных» элементов и позволит изготавливать отсечные элементы с использованием собственных производственных мощностей.
В результате исследований планируется определить наиболее рациональную форму боковой грани головной части отсечного элемента. Путем проведения моделирования процесса отсечки шлака на физических и виртуальных моделях кислородного конвертера.
Объект исследования – отсечка конечного шлака при выпуске стали из кислородного конвертера.
Предмет исследования – отсечной элемент поплавкового типа вводимого в ванну кислородного конвертера с помощью специального механического манипулятора.
3. Основной раздел
3.1 Описание конструкции манипулятора
Механические манипуляторы для ввода отсечных элементов в ванну кислородного конвертера по типу своего конструктивного исполнения могут быть, например такими как: подвесного, телескопического, бокового и осевого типов (рис.1).
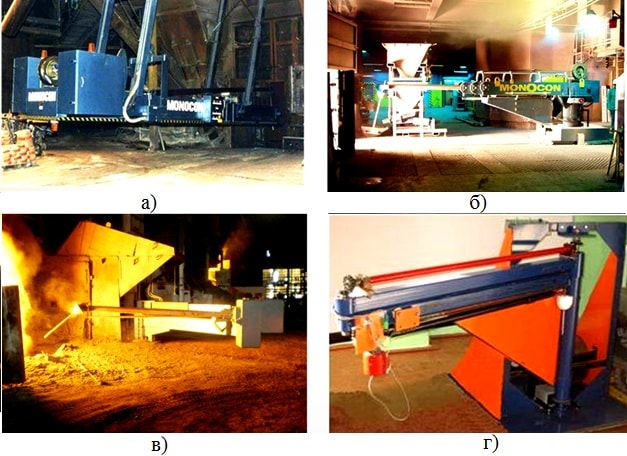
Рисунок 1 – Типы конструкции манипуляторов: а – подвесного типа; б – телескопического типа; в – бокового типа; г – осевого типа
Однако манипулятор осевого типа (рис.1,г) разработанный кафедрой МОЗЧМ Донецкого национального технического университета
и защищенный патентом [3], обладает рядом следующих преимуществ относительно других типов манипуляционных систем, такими как:
компактность и универсальность использования конструкции; высокая точность позиционирования отсечного элемента относительно сталевыпускного отверстия перед его сбросом в ванну кислородного конвертера; высокая надежность работы в экстремальных условиях запыленности и высоких температур на рабочей площадке.
Данный манипулятор располагается на специализированной рабочей площадке, со стороны сталевыпускного отверстия кислородного конвертера. В исходном положении, данный вид конструкции манипулятора не вторгается в рабочее пространство устройств для механического разрушения износившейся футеровки конвертера, а также и торкрет машин которые необходимы для ремонта футеровки. У манипулятора есть возможность изменения расстояния вылета штанги, для облегчения регулировки соосного позиционирования отсечного элемента с сталевыпускным каналом конвертера.
Конструкция манипулятор (рис.2) состоит из колонны 3 которая в свою очередь установлена на неподвижных подшипниковых опорах, верхней 5 и нижней 2. Поворот колонны осуществляется с помощью привода 1. Она соединена с консолью 4, на которой установлен подшипниковый узел с вертикальным валом 12, а на конце этого вала закреплен кронштейн 13, оборудованный двумя направляющими, на которой располагаются ролики каретки 14, которые обеспечивают ее передвижение по направляющим. Каретка 14 несет пустотелую штангу 15, на переднем конце которой с помощью пружинного фиксатора установлен отсечной элемент поплавкового типа 16. Поворот кронштейна 13 относительно основной консоли 4 производиться механизмом, состоящим из конической зубчатой пары 11, которая объединяет вертикальный вал 12 с задним концом горизонтального вала 9 установленного в подшипниковых опорах 8 и 10. На переднем конце горизонтального вала установлено коническое зубчатое колесо 7, которое имеет возможность обкатки по конической зубчатой шестерни 6, жестко закреплена на неподвижной верхней опоре 5 поворотной колонны 3
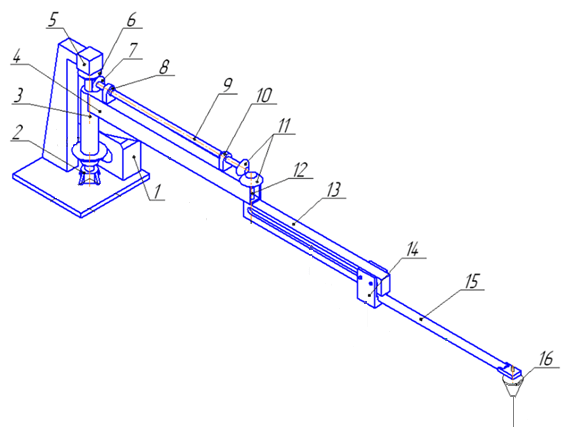
Рисунок 2– Конструкция манипулятора осевого типа: 1 – привод; 2,5 – нижняя и верхняя подшипниковые опоры; 3 – колонна; 4 – консоль; 6 –коническая зубчатая шестерня; 7 – коническое зубчатое колесо;8,10 – подшипниковые опоры; 9 – горизонтальный вал; 11 – коническая зубчатая пара;12 – вертикальный вал; 13 – кронштейн; 14–каретка; 15 – штанга; 16 – отсечной элемент
При такой конструкции манипулятора обеспечивается соотношение количества чисел зубьев конической неподвижной шестерни 6 и конического зубчатого колеса 7 равное 2:1. Что обеспечивает одновременный поворот колонны 3 с консолью 4 на необходимый угол из исходного положения относительный поворот кронштейна 13 на 180 градусов, в результате чего пустотелая штанга 15 расположится вдоль соосной оси симметрии для любого заданного варианта размещения технологического оборудования на рабочей площадке при базовой комплектации основных механизмов (рис. 3). Такое конструктивное решение обеспечивает повышение уровня универсальности конструкции манипулятора, приведение к единой норме его структурных узлов и уменьшить число приводов до одного.
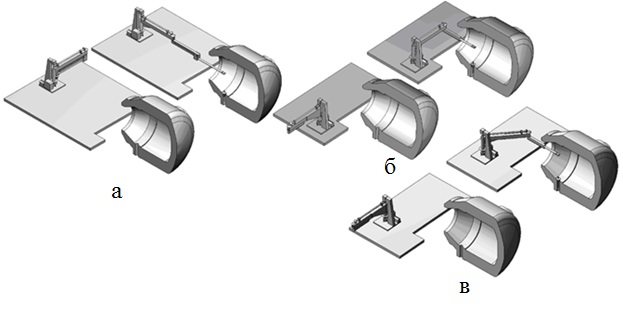
Рисунок 3 – Положение звеньев механической системы манипулятора в начальной и рабочей позициях при соосном (а), боковом (б) и диагональном расположении на площадке относительно конвертера (в)
3.2 Обзор типов отсечных элементов для ввода в ванну кислородного конвертера
Отсечной элемент вводится в ванну кислородного конвертера специальным механическим манипулятора после наклона конвертера в положения выпуска плавки в сталеразливочный ковш. После его ввода, для выполнения своей функции отсечной элемент должен иметь специальную форму и такую плотность материла, чтобы в ванне конвертера он находился на границе раздела жидкой стали и шлака. Во время завершения выпуска стали отсечной элемент должен застопорить отверстие для предотвращения попадания конечного конвертерного шлака в сталеразливочный ковш. Вышеописанный процесс отсечки шлака показан на (рис. 4).
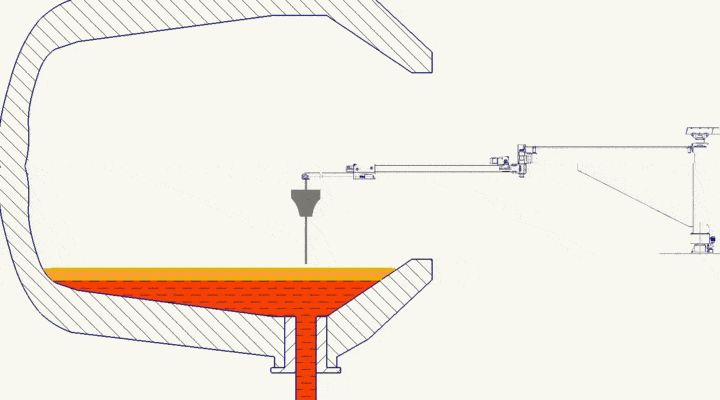
Рисунок 4 – Процесс отсечки шлака элементом поплавкового типа.(Рисунок анимирован. Количество кадров 8, размер 141кб.)
Отсечные элементы можно классифицировать по нескольким признакам: 1) по конструктивному исполнению могут быть в форме шара или стрелки
(рис.5); 2) по размеру в зависимости от объема конвертера; 3) по химическому составу; 4) по виду образующей боковой поверхности для элемента в виде стрелки
(рис.6).
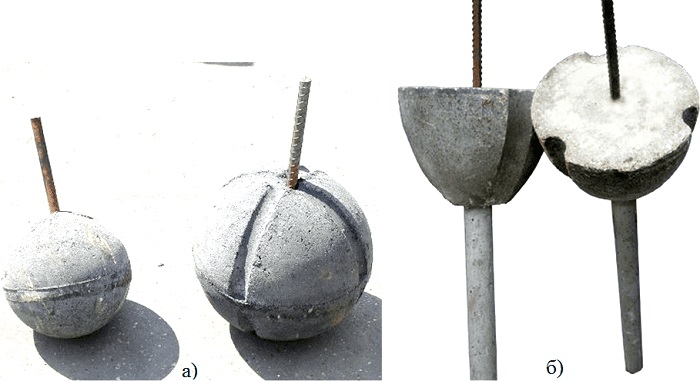
Рисунок 5 – Отсечные элементы: а) в форме шара; б) в форме стрелки
Производитель отсечных элементов – фирма Yuntian Metallurgy Technology Co., Ltd. приводит некоторые показатели их физического и химического состава (табл.1). Кроме указанных в (табл.1) химических соединений в состав материалов также могут входить Al2O3, SiO2, Fe2O3. Проманиторив рынок отсечных элементов можно сказать что стоимость одного отсечного элемента колеблется в пределах 15–30 долларов США, без учета доставки адресату.
Вместимость конвертера, т | Параметр отсечного элемента | Значение |
8–120 | содержание MgO | ≥70% |
плотность | ≥4–4,2 г/см3 | |
прочность на сжатие | 20 мпа | |
огнеупорность | ≥1790°с |
|
форма элемента | шар | |
30–150 | содержание MgO | ≥70% |
огнеупорность | ≥4–4,2 г/см3 | |
прочность на сжатие | 80 мпа | |
огнеупорность | ≥1790°с | |
форма элемента | стрелка |
|
160–300 | содержание MgO(Al2O3) | 60% |
плотность (стерженьсферическая часть) | ≥3,9/4,1 г/см3 | |
прочность на сжатие | 40–70 мпа | |
огнеупорность | 1790°с | |
форма элемента | стрелка |
Процесс изготовления отсечных элементов в форме стрелки
состоит из следующих этапов: получение необходимых составляющих материалов, дробление и перемешивание, нагрев и придание формы на специальном оборудовании, охлаждение, сборка сферической части и стержня.
Применение разных форм отсечных элементов обусловлено рядом факторов. Это прежде всего степень эффективности применения элемента той или иной формы. Эффективность отсечки шлака с помощью огнеупорного шара составляет менее 75%; отсечной элемент в форме стрелки
благодаря направляющему стержню обеспечивает эффективность отсечки 90–98%.
Следующим фактором применения является стоимость элементов. Несмотря на разницу по эффективности отсечки, шары до сих пор используются, что может быть объяснено их относительной дешевизной по сравнению со «стрелками», их стоимость отличается в два раза. Кроме того, значимым фактором являются физико–химические показатели отсечных элементов, а именно соотношение процентного содержания компонентов, входящих в их состав.
Это в свою очередь влияет на плотность материала элемента и расположение его в ванне кислородного конвертера на границе раздела сталь–шлак [4].
4. Анализ проведенных исследований по теме
Одним из факторов, оказывающим существенное влияние на эффективность отсечки элементом в форме стрелки
, имеет вид боковой поверхности (рис.6). Как показывают исследования [5], нерациональная форма отсечного элемента может приводить к преждевременному перекрытию сталевыпускного канала конвертера и кроме того к увеличению амплитуды собственных колебаний.
Анализ полученных результатов исследования [6], гласит что для исследованных отсечных элементов, имеющих близкие геометрические параметры, масса варьируется от 53,5 до 119 кг, приведенная плотность практически одинакова и составляет около 2830..2860 кг/м3, центр тяжести расположен на высоте около 0,9 м от начала координат, а глубина погружения в жидкую сталь имеет широкий диапазон изменения. Наименьшие значения глубины погружения имеют элементы типа IV (головная часть – ступенчатый цилиндр), I (гиперболоид) и III (эллипсоид), т.е. отсечные элементы с таким конструктивным исполнением дольше сохранят равновесие при уменьшении уровня жидкой стали в конвертере в процессе ее выпуска и, в конечном итоге, обеспечат более высокую степень отсечки шлака. Полученные результаты расчетов согласуются с данными исследований, проведенных на физических моделях [7] и установивших, что наиболее эффективными являются варианты элементов типа IV и III.
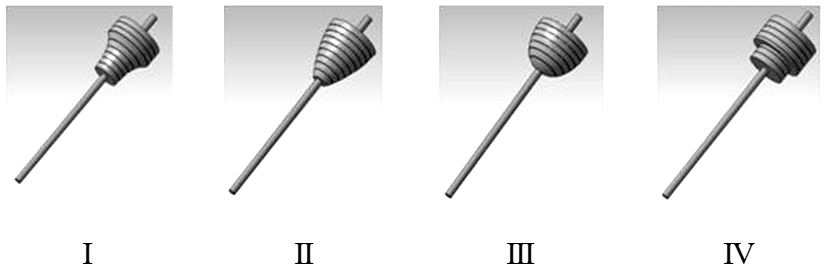
Рисунок 6 – Отсечные элементы с разной формой боковой поверхности
Выводы
В данном реферате была рассмотрена проблема отсечки конечного шлака в кислородно–конвертерном производстве стали.
Наиболее высокий процент отсечки шлака обеспечивается элементами поплавкового типа, которые вводятся в полость конвертера специальным механическим манипулятором.
Было определенно, что отсечной элемент в форме стрелки
по качеству отсечки шлака преобладает над элементом в форме шара, во многом благодаря направляющему стержню и формы боковой поверхности головной части отсечного элемента.
Из обзора проведенных исследование следует что дальнейшие исследования необходимо посвятить разработке наиболее оптимальной формы отсечного элемента в форме стрелки
. Этой актуальной задаче собственно и будет посвещена данная магистерская работа
При написании данного реферата магистерская работа еще не завершена. Окончательное завершение: июнь 2018 года. Полный текст работы и материалы по теме могут быть получены у автора или его руководителя после указанной даты.
Список источников
- А. Н. Смирнов,А. М. Зборщик.Внепечное рафинирование чугуна и стали: Учебное пособие. – Донецк: ГВУЗ «ДонНТУ», 2012. – 186 с.
- С. П. Еронько, А. Н. Смирнов, С. А. Бедарев и др.Новые устройства для реализации технологии бесшлакового выпуска стали из кислородного конвертера [Текст] / Процессы литья. – 2007. – № 4. – С. 16–21.
- Пат. 71681 UA, C21 C/46. Пристрій для відсічення шлаку при випуску сталі з конвертора/С.П.Єронько, О.М.Смірнов, О.Ю.Цупрун та інш.: Заяв. 20.04.2004; опубл. 15.12.2004, №12.
- С. П. Еронько, Е. В. Ошовская, С. А. Бедарев и др. Исследование на физической модели процесса отсечки конвертерного шлака элементами поплавкового типа [Текст]/ Известия высших учебных заведений. Черная металлургия. – 2009. – №7. – С.13 – 18.
- С. А. Бедарев. Определение массо–центровочных характеристик отсечных элементов поплавкового типа / С. А. Бедарев // Научные труды Донецького национального техничного университета. Сер. : Горно–електромеханическая. – 2013. – Вип. 1. – С. 14–21.
- Е. В. Ошовская, С. А. Бедарев, И. А. Брозянский.Задача поиска эффективной конструкции элементов поплавкового типа для отсечки конвертерного шлака / Материалы X Международной научно–технической студенческой конференции
Механика жидкости и газа
. – Донецк: ДонНТУ, 2011. – С. 90–94. - С. П. Еронько, Е. В. Ошовская, С. А. Бедарев, С. В. Мечик. Исследования на физической модели процесса взаимодействия отсечных элементов поплав–кового типа с потоками расплава в ванне конвертера /
Черметинформация
. БюллетеньЧерная металлургия
, 2009. – Вып.6. – С. 39–45.