Реферат по теме выпускной работы
Содержание
- Вступ
- 1. Актуальність теми
- 2. Мета і завдання дослідження
- 3. Аналіз умов експлуатації і можливих відмов
- 4 Пропоновані типові рішення
- 4.1 Двигун
- 4.2 Редуктор
- 4.3 Металоконструкції крана
- 5 Склад стаціонарної системи
- Висновки
- Список джерел
Вступ
В умовах сучасних вимог до безперервності технологічних процесів і безвідмовності механічного обладнання необхідні зміни в підходах до забезпечення експлуатаційної надійності механічного обладнання, в тому числі і для металургійних ливарних кранів. В даному випадку необхідність безвідмовної роботи комплексу металургійних машин, не може бути вирішена традиційними методами періодичних оглядів та діагностування. Необхідно використання стаціонарних систем діагностування при використанні комплексу параметрів діагностики. Оцінка технічного стану металургійних кранів, що працює при невизначеному нестационарном навантаженні, не може проводитися методами використовуваних для роторних машин, що працюють в тривалому режимі.
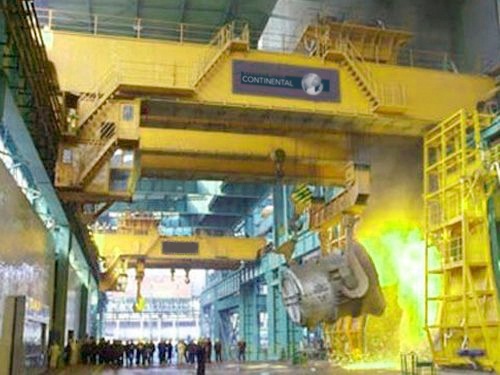
1. Актуальність теми
У складі металургійного крана слід виділити три основні об'єкта контролю: механізм пересування, механізм головного підйому, металоконструкції. Різні режими і діапазони вимірювань в даному випадку об'єднуються непериодическими навантаженнями, що діють в різних часових інтервалах. Це дозволяє рекомендувати в якості діагностичних параметрів: вібраційні коливання, струмові характеристики і частоти обертання приводних двигунів.
Типова конструкція механізму головного підйому розливного крана приведена на малюнку 2. Механізм складається з двох однакових механізмів, пов'язаних між собою зубчастими вінцями 9 барабанів 7, що забезпечує їх рівні кутові швидкості обертання. Кожен механізм приводиться в обертання електродвигуном 1 і складається з двоступеневого редуктора 4 і зубчастої пари 8-9, має два колодкових гальма 2, 5, встановлених з двох сторін редуктора 4. Вал двигуна з'єднаний з швидкохідним валом редуктора за допомогою зубчастої муфти 3. До складу механізму входить силовий поліспаст 6.
В основі побудови системи контролю пропонується використовувати блоковий принцип, що відрізняється налаштованим параметрами визначення технічного стану. Необхідним є наявність об'єднуючого блоку контролю. Повинні бути передбачені можливості розширення точок контролю і функцій аналізу. Це дозволить уніфікувати функції обслуговування, налагодження, експлуатації, використання інформації та вдосконалення стаціонарної системи.
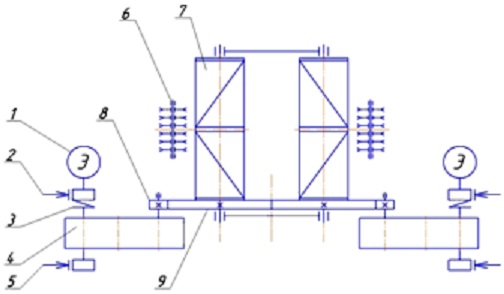
2. Мета і завдання дослідження
Метою розроблюваної системи є підвищення довговічності і безвідмовності, що експлуатується металургійних кранів за рахунок своєчасного виявлення механізмів, що мають підвищену вібрацію, визначення та усунення (шляхом проведення ремонтів) причин викликали вібрацію.
Система повинна забезпечити поточний контроль і діагностування технічного стану механізмів прокатних станів для запобігання раптових відмов і забезпечення цілісності базових і корпусних деталей та вузлів механізмів. Результати контролю повинні використовуватися для прийняття рішення про аварійну зупинку і про необхідність поведінки ремонту механізмів.[7]
Основні завдання дослідження:
контроль і сигналізація про перевищення заданих значень: параметрами вібрації;
використання для контролю технічного стану струмових характеристик і частоти обертання валів приводних двигунів;
аналіз поточних значень вібраційних параметрів, розпізнавання спектрального складу вібраційного сигналу, характеру можливих пошкоджень і визначення трендів розвитку пошкоджень;
аналіз тимчасової реалізації вібраційного сигналу і визначення ступеня накопичення пошкоджень при ударних процесах;
оцінка технічного стану контрольованих механізмів, визначення часу і обсягів ремонтних впливів;
накопичення і аналіз інформації про зміст проведених ремонтів, ефективності дій, періодичності замін елементів;
діагностування правильності функціонування стаціонарної системи і попередження про можливі несправності.
У складі стаціонарної системи повинен бути присутнім блок стиковки результатів діагностування за допомогою переносних приладів і контролю параметрів вібрації стаціонарними датчиками. Можливе виконання в вигляді автоматизованої інформаційно-діагностичної системи ремонту обладнання.
Необхідно передбачити підготовку фахівців безпосередньо працюють з системою, що використовують отриману інформацію і фахівців з обслуговування системи.
3. Аналіз умов експлуатації і можливих відмов.
Металургійний кран працює в умовах змінних і непостійних навантажень при різній частоті обертання і різному моменті двигуна. Температурні умови - постійні, є сезонні зміни. Підвищена запиленість, всередині корпусу редуктора - вплив теплого мінерального масла.
Можливі відмови пов'язані з ослабленням різьбових з'єднань, порушенням взаємного розташування деталей, появою зазорів в з'єднаннях і виникненням металевого контакту між елементами підшипників, зубчастих передач. Зафіксовані відмови пов'язані з зносом осей, ушкодженнями підшипників, зубчастих передач, ослабленням і руйнуванням різьбових з'єднань, порушенням режиму змащення.
4 Пропоновані типові рішення
4.1 Двигун
Основний вид пошкодження механічної частини двигуна - поступові пошкодження підшипників в результаті осповідного викришування або порушення режиму змащування. Час розвитку пошкоджень 1 ... 2 місяці, дозволяють використовувати зміни трендів для розпізнавання появи несправностей. Порушення центрування, своєчасна заміна роторів, що мають пошкодження, виявлення пошкоджень електричної частини двигунів повинно здійснюватися ремонтної службою цеху під час проведення поточних ремонтів.[1]
Поступове накопичення пошкоджень при експлуатації електродвигуна дозволяє використовувати для контролю поточного стану значення загального рівня вібрації: середньоквадратичного значення віброшвидкості в частотному діапазоні 2 ... 400 Гц; середньоквадратичне і пікове значення віброприскорення в частотному діапазоні 10 ... 5000 Гц. Частотні діапазони необхідно уточнити після проведення вібраційних досліджень підшипникових вузлів двигунів.[5]
.Прийняті рішення: додаткове змазування, затягнути нарізні сполучення, замінити підшипник. Підстава для прийняття рішення - перевищення значень вібрації допустимого значення, стабільне збільшення значень вібрації, відсутність зниження вібрації після проведення ремонтних робот.
Можливе застосування вирішальних правил, наведених в ГОСТ 25364-97[2]:
допустиме значення після ремонту - 2,8 мм / с; експлуатація без обмежень - 4,5 мм / с; експлуатація в обмеженому часовому інтервалі (до 7-ми днів) - 7,1 мм / с; експлуатація не допускається при значеннях виброскорости перевищує 7,1 мм / с.При одночасному збільшенні вібрації двох опор на 1,0 мм / с при стабілізації частоти обертання повинні бути прийняті оперативні заходи для з'ясування причин зміни. Зростання вібрації підшипникової опори двигуна на 2,0 мм / с за період до 3-х діб, або збільшення на 3,0 мм / с незалежно від тривалості зростання повинно служити підставою для прийняття оперативних заходів по виявленню причин, для чого може здійснюватися зупинка двигуна .
Точки контролю розташовуються у вертикальному напрямку, в нижній частині підшипникових вузлів електродвигуна.
Додаткові діагностичні параметри для прийняття рішення про зупинку двигуна: збільшення струму холостого ходу; нестабільність частоти обертання.
4.2 Редуктор
Для своєчасного виявлення поступових і раптових пошкоджень пропонується використовувати для контролю поточного стану значення загального рівня вібрації і зміни спектральної картини вібрації. Контрольовані параметри при вимірюванні загального рівня вібрації: середньоквадратичного значення віброшвидкості в частотному діапазоні 2 ... 400 Гц; середньоквадратичне і пікове значення віброприскорення в частотному діапазоні 10 ... 5000 Гц.
Контроль спектральної картини вібрації здійснюється за 3-м максимальних значень складових виброскорости і віброприскорення при роботі на заданій частоті обертання. Ознака зміни спектральної картини - зміна амплітуд складових вібрації більш, ніж в 2,6 рази, зміна частотних характеристик максимальних значень.
Зміна частоти обертання може призводити до зміни спектральної картини, але це не є ознакою пошкодження. Зміна навантаження на редуктор також змінює вид спектрограми. У механічному обладнанні поряд з детермінованими процесами присутні і стохастичні. Стабільність імовірнісних характеристик останніх визначається технічним станом системи. Амплітуда складових виброскорости і стабільність значень віброприскорення, може бути пов'язано зі зміною швидкісного режиму або технічного стану редуктора. Однак, дані значення повинні залишатися практично незмінними при стабільних зовнішніх впливах і мати однотипне зміна при зміні частоти обертання.
Частоти можливих пошкоджень елементів механізму необхідно пов'язати з фактичної частотою обертання валу двигуна.
Прийняті рішення: зупинка механізму, огляд механізму, затягування різьбових з'єднань, заміна елементів. Підстава для прийняття рішення - перевищення значень вібрації допустимого значення, стабільне збільшення значень вібрації, відсутність зниження вібрації після проведення ремонтних робот, різка зміна спектральної картини в порівнянні з попередніми реалізаціями при незмінному характері навантаження. Зміна спектральної картини віброприскорення - підстава для проведення додаткового огляду механізму. Зміна спектральної картини виброскорости вимагає термінового прийняття рішення по ремонтним впливів по відновленню працездатного стану механізму - затягуванні різьбових з'єднань, заміні елементів. Уточнення змісту ремонту необхідно здійснити після проведення візуального огляду механізму.
Для вибору контрольних точок установки датчиків слід визначити сектора дії сил і запаси міцності по основних елементів - валів, зубчастих передач, підшипників. Напрямок установки датчиків вимагає досліджень по визначенню інформативності різних напрямків для умов редуктора. Визначити інформативні частоти можливих пошкоджень. Так як частоти пов'язані з елементами, можна знайти деяку мінімальну кількість контрольних точок для діагностування всіх елементів редуктора. Слід виконати контурну діаграму вібрацій і пошук по зовнішнім підшипників.
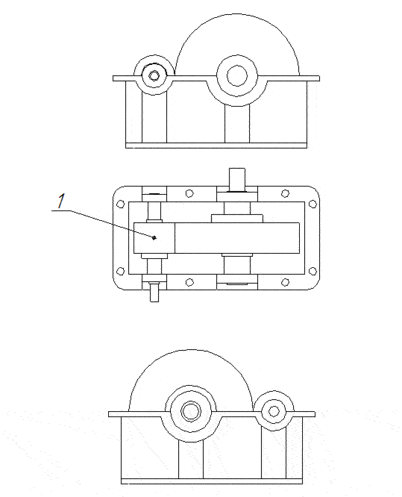
Малюнок 3 - Місця і порядок установки датчиків
(анімація: 13 кадрів, 4 циклу повторення, 134 кілобайти)
Точки контролю редуктора повинні включати підшипники вхідного вала, проміжних валів і вихідного валу. Обов'язково передбачити контроль вібрації в осьовому напрямку. Використання низькочастотного і среднечастотного діапазону дозволяє зменшити кількість точок контролю, так як дані коливання легко поширюються по корпусним деталям. Крім того контрольовані елементи можна розпізнати по частотах можливих пошкоджень.
Пропоноване розташування контрольних точок: 1 - радіальний напрямок підшипник вхідного вала; 2 - осьовий напрямок підшипник вхідного вала; 3 - радіальний напрямок підшипник проміжного вала; 4-радіальний напрямок підшипник вихідного вала. Конкретне розташування необхідно вибирати з урахуванням зон навантаження і конструкції редуктора.
В даному випадку для оцінки технічного стану кращим є метод відносного порівняння виміряних значень в часі експлуатації. Додаткові діагностичні параметри для прийняття рішення про зупинення редуктора: збільшення струму холостого ходу; нестабільність частоти обертання.
Періодичність опитування 1 раз в хвилину, тривалість опитування 10 секунд, період між вимірами 100 мкс. Для побудови трендів використовується повсякчасне значення, для архіву вибирається щозмінне значення, щотижневе значення. Вибір значень здійснюється оператором стаціонарної системи.
4.3 Металоконструкції крана
Стан металоконструкцій багато в чому визначають зовнішні впливи на механізми приводу. Найбільш інформативним в даному випадку є контроль тимчасової форми вібраційного сигналу в момент захоплення підйому і початку руху. Це дозволить контролювати цілісність балок, рівномірність руху крана, наявність зазорів в елементах металоконструкції, ослаблення кріплень.
Тимчасова форма є найбільш інформативним параметром при оцінці технічного стану механізмів короткочасного і повторно короткочасного режимів роботи. Бистропротекающие процеси зі змінними прискореннями важко діагностувати, т. К. Процес вимірювання вимагає певного проміжку часу, протягом якого вимірюється параметр не залишається постійним. У цьому випадку доцільно проводити спільну реєстрацію не середніх, а миттєвих значень вібрації і отримувати для аналізу їх тимчасову розгортку.[4]
Розташування контрольних точок - два Однокоординатний датчика, встановлених у вертикальному напрямку посередині головних балок і чотири трикоординатних датчика по периметру металоконструкцій. Необхідно передбачити швидкознімний роз'єм і механічний захист від пошкоджень кабелю та датчика. Робота датчика відбувається в умовах агресивного середовища: змінного впливу температурних полів, дрібнодисперсного пилу. Це вимагає використання нержавіючих матеріалів, пило-та вологозахищених роз'ємів. Для кріплення датчиків можуть бути використані проміжні елементи. Необхідно навчання фахівців питань установки, обслуговування, заміни та відновлення елементів вимірювальної частини системи.
Для контролю стану механізму пересування, зокрема підшипників коліс, пропонується використовувати систему контролю струмових параметрів двигунів.
5 Склад стаціонарної системи
У складі стаціонарної системи слід виділити наступні елементи:
- вимірювальна частина, включає датчики вібрації, необхідно забезпечити отримання інформації про частоту обертання двигунів і струмових характеристиках;
- коммутирующая частина - кабелі, попередні підсилювачі і погоджують пристрої;
- блоки контролю трьох типів: контроль загального рівня вібрації, контроль загального рівня вібрації і спектральних складових, контроль тимчасових реалізацій вібраційного сигналу з функцією контролю ударних процесів;
- блоки візуалізації і сигналізації стану;
- загальний блок контролю технічного стану і діагностування;
- блок самодіагностики стану системи;
- блок стиковки результатів діагностування за допомогою переносних приладів - автоматизована інформаційно-діагностична система ремонту обладнання для обліку проведених ремонтів і характерних ушкоджень.
Досить ефективним доповненням може бути апаратура (стаціонарна або переносна) для візуального огляду внутрішніх елементів механізму дозволяючи виконати уточнення характеру пошкоджень під час поточних ремонтів і профілактик, підтвердивши правильність поставленого діагнозу. Ефективність функціонування системи визначається ступенем використання інформації про технічний стан. Повідомлення про поточний стан повинні стати постійною інформацією для експлуатаційного персоналу.[3]
Висновки
При написанні даного реферату магістерська робота ще не завершена. Остаточне завершення: травень-червень 2018 року. Повний текст роботи і матеріали по темі можуть бути отримані у автора або його керівника після зазначеної дати.
Список джерел
1. Обоснование необходимости проведения ремонтов механического оборудования металлургических предприятий,В.А. Сидоров, Донецкий национальный технический университет (Донецк, Украина), http://www.mayster.info/index.php?lang_id=1&menu_id=167
2. ГОСТ 25364-97http://wiki-numbers.ru/gost_pdf/gost-25364-97
3. Информационные основы виброметрии, В.А. Сидоров,Вестник СевГТУ. – Севастополь: Изд-во СевНТУ, 2011. – Вып. 117: Машиноприборостроение и транспорт. – С.157-165http://masters.donntu.ru/2013/fimm/lytaev/library/article8.htm
4. Практика реализации стационарной системы вибродиагностики прокатного оборудования на примере комплекса «КОРУНД» http://patonpublishinghouse.com/tdnk/pdf/2014/pdfarticles/02/11.pdf
5. Механическое оборудование: техническое обслуживание и ремонт / В.И. Бобровицкий, В.А. Сидоров. — Донецк: Юго-Восток, 2011. — 238 с.http://eam.su/2-3-vibraciya-mexanizmov.html
6. Механическое оборудование металлургических заводов/ Магнитогорский государственный технический университет им. Г.И. Носова, 2014г., Стр. 87-94https://elibrary.ru/item.asp?id=22828041
7. О работе подвесок литейных кранов, Щеглов О.М., Сагиров Ю.Г., Суглобов Р.В. - Мариуполь, 25.11.2010г.http://eir.pstu.edu/bitstream/handle/123456789/1396/захист%2013_22.pdf?sequence=1