Содержание
- Введение
- 1. Процесс 3D-печати
- 2. Методы 3D-печати
- 3. Кинематика 3D-принтеров
- 3.1 Конструкция 3D-принтера разработанная Джозефом Прюши
- 3.2 Конструкция кинематики 3D-принтеров от компании Felix printers
- 3.3 Delta кинематика
- 3.4 Кинематика от компании Ultimaker
- 4. Разработка аппаратной части 3D-принтера
- Выводы
- Список источников
Введение
3D-печать – это инструмент, позволяющий переходить от концепции (3D-модели) к непосредственной материализации объекта, независимо от формы объекта, сокращая время между концептуальным дизайном и изготовлением продукта. Один из наиболее доступных методов печати, является расплавление нити пластика (FFF – Fused Filament Fabrication), которая при помощи экструдера подается на рабочую поверхность, создавая слои и наплавляя их друг на друга. При помощи этого метода, возможно создавать объекты, которые не могли быть созданы традиционным процессом изготовления или для их изготовления необходимо потратить больше времени и стоимость процесса была бы гораздо выше.
3D-технологии открыли уникальные возможности создания сложных пространственных форм, объектов и инженерных конструкций.
В работе [2] было отмечено: экономическая эффективность 3D-технологии в ее качественной безальтернативности,
безотходности и значительном снижении себестоимости при серийном и массовом производстве
Аддитивные технологии (от английского Additive Fabrication) – обобщенное название данной технологи, предполагает изготовление изделия по данным цифровой модели (или CAD-модели) методом послойного добавления.
Суть Additive Fabrication (AF) может быть проиллюстрирована простым примером: CAD-модель → AF-машина → деталь (рис. 1)[1].
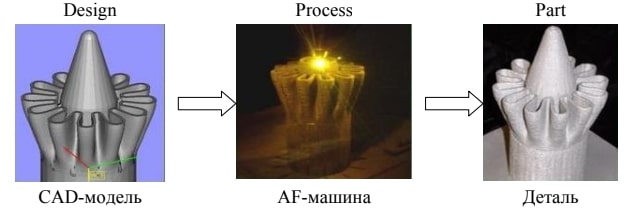
Рисунок 1 – Процесс Additive Fabrication
С каждым годом AF-технологии открывают новые возможности по созданию уникальных изделий и новые области применения, об этом говорится и в выступлении на
6-м Международном инструменте саммите, посвященном актуальной теме – Современные технологии и оборудование быстрого прототипирования и производства
[3].
Многие специалисты считают Additive Fabrication революционной технологией, некоторые утверждают, что производство перестанет существовать в таком виде, в котором мы его знаем сегодня, если дальше развивать аддитивные технологии [4].
1. Процесс 3D печати
Трехмерная печать заключается в последовательном добавлении материала по слоям, позволяя создавать трехмерные объекты со сложными геометрическими формами первоначально которые находились в цифровом формате. Специализированное программное обеспечение преобразует трехмерную фигуру в многочисленные горизонтальные срезы, которые могут интерпретироваться принтером. Принтер считывает каждый из этих фрагментов как 2D-изображение и начинает откладывать материал, воссоздавая каждый фрагмент на печатной платформе.
2. Методы 3D печати
Существует много типов 3D-принтеров, основанных на различных технологиях, различных методах печати и с использованием различных материалов. Из наиболее распространенных технологий 3D-печати являются:
1. Стереолитография (SLA или SL) – технология аддитивного производства моделей, прототипов и готовых изделий из жидких фотополимерных смол. Процесс создания готового изделия происходит за счет отвердения смолы облученной ультрафиолетовым лазером или другим схожим источником энергии. Полимеризация материала происходит в точках соприкосновения с лучом. После создания желаемого объекта, платформа погружается в бак с жидкой смолой на дистанцию, равную толщине одного слоя – как правило, от 0.05 мм до 0.15 мм. После выравнивания поверхности жидкого материала начинается процесс построения следующего слоя. Цикл повторяется до построения полной модели. После завершения печати, готовое изделие промывается для удаления остаточного материала [5].
2. Технология 3DP – струйная трехмерная печать. Также является аддитивной технологией, которая была разработана одной из первых в Массачусетском технологическом институте в 1993 году.
Данная технология подразумевает послойное построение физических объектов на основе цифровой трехмерной модели. В качестве материалов изготовления использую всевозможные порошки, которые наносятся последовательными тонкими слоями. Чаще всего использовали гипс, но по мере улучшения технологии, стали распространены самые разнообразные материалы, включая пластики, песчаные смеси и даже металлы. Данная технология способна создавать трехмерные модели из любого порошкового материала, также есть возможность добавление красителей, что позволяет осуществить цветную печать[6].
3. Технология многоструйного моделирования (MJM) – метод, который был запатентованной компанией 3D Systems. Данная технология используется в линейке профессиональных принтеров ProJet.
Технология MJM сочетает в себе черты следующих методов 3D-печати, таких как: струйная трехмерная печать (3DP), моделирование методом послойного наплавления (FDM/FFF) и стереолитография (SLA). Построение слоев производится при помощи специальной печатающей головки, которая оснащённая массивами сопел. Количество сопел может варьироваться от 96 до 448.
Изготовление желаемого объекта производится термопластиками, восками и фотополимерными смолами. Для первых двух случаев материалы затвердевают за счет постепенного охлаждения. В случае печати фотополимерами, каждый слой обрабатывается ультрафиолетовым излучением.
Данная технология позволяет добиться высоких показателей точности, а минимальная толщина наносимого слоя может составлять 16 микрон[7].
4. Выборочное тепловое спекание (SHS) – метод аддитивного производства. Технология основана на плавке слоев термопластического или металлического порошка с помощью теплового излучателя.
При создании желаемого объекта, происходит формирование слоя, после чего рабочая платформа передвигается вниз на дистанцию, соответствующую толщине одного слоя, новый слой порошка наносится с помощью автоматизированного ролика, а затем производиться спекание нового слоя по контурам, заданным цифровой трехмерной моделью.
Технология выборочного теплового спекания (SHS) похожа на технологию с выборочным лазерным спекание (SLS), единственное существенное различием между ними заключается в использовании тепловой печатающей головки вместо лазерной[8].
5. Электро-лучевая плавка («Electron Beam Melting» или EBM) – метод аддитивного производства. В данной технологии в качестве используемой энергии для плавки используются электронные излучатели. В основе технологии лежит использование электронных пучков высокой мощности для сплавки металлического порошка в вакуумной камере с образованием последовательных слоев, повторяющих контуры цифровой модели. В отличии от технологий спекания, электронно лучевая плавка позволяет создавать детали особо высокой плотности и прочности[9].
6. Моделирование методом послойного наплавления (Fused deposition modeling FDM) – технология аддитивного производства, которая нашла свое применение при создании моделей, прототипировании и промышленном производстве. Технология FDM создает трехмерные объекты за счет нанесения последовательных слоев материала, повторяющих контуры цифровой модели.
Принцип работы данного метода заключается в том, что экструзионное сопло нагревается и снабжается пластиковой нитью, происходит процесс плавление нити, после чего она осаждается на поверхность платформы, создавая твердое тело модели. Метод послойного наплавления начинается с подготовки компьютерной трехмерной модели. Соответствующее программное обеспечение загружает модель в формате stl и далее анализирует ее во всех сечениях и рассчитывает алгоритм наплавления. Относительное перемещение между экструзионным соплом или головкой экструдера и платформой в пространстве по трем координатам создается благодаря микроконтроллеру[10].

Рисунок 2 – моделирование технологии Fused deposition modeling FDM
3. Кинематика 3D-принтеров
Рассмотрим 4 самых популярных конструкций 3D-принтеров.
3.1 Конструкция 3D-принтера разработанная Джозефом Прюши
Кинематика данного 3D-принтера построена на перемещении печатающей головки по оси Z (вверх-вниз) и оси X(влево-вправо) при помощи двух шаговых двигателей и двух винтов с трапецеидальной резьбой. Платформа перемещается по оси Y.
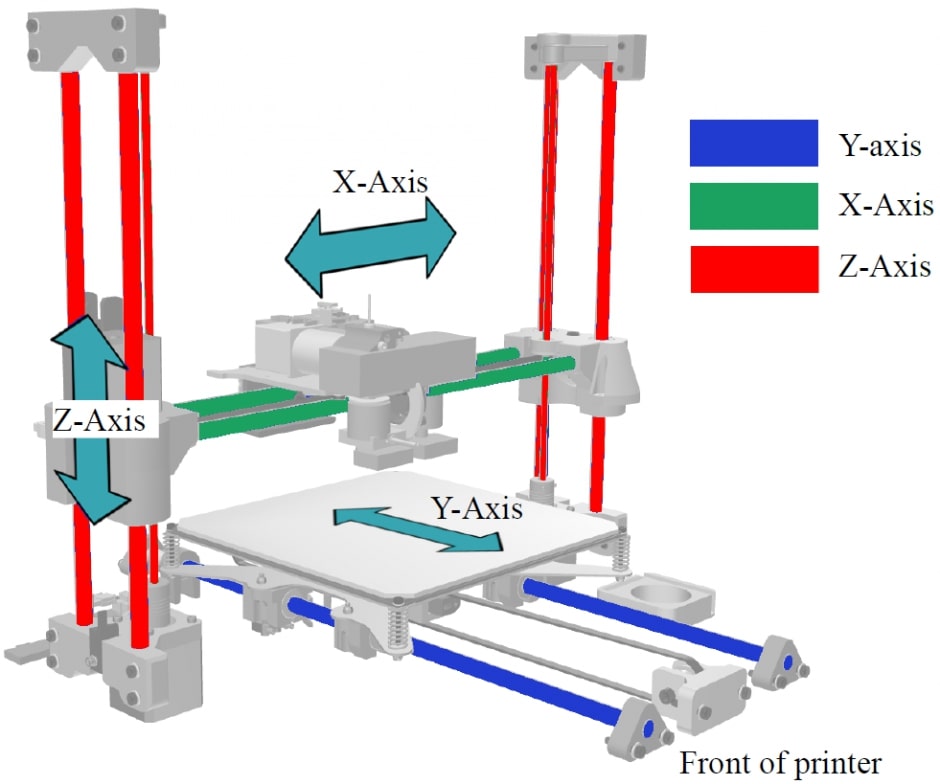
Рисунок 3 – Конструкция 3D-принтера разработанная Джозефом Прюши
Достоинствами данной кинематики является
- Перемещение каждой из осей независимое, поэтому если возникают дефекты при печати из-за пропускания шагов, легко определить из-за какой оси это происходит. В связи с этим данная кинематика очень распространённая у фрезерных ЧПУ станков.
- Простота данной кинематики.
- Размеры данного принтера могут быть самыми разнообразными, экструдер так же может подлежать модернизации поскольку он не мешает движению других частей из-за того что он выступает вперед. В связи с этим многие ставят второй экструдер.
Достоинствами данной кинематики является
- Одним из основных недостатков, является сложность в калибровки.
- Качественной печати можно добиться только при небольшой скорости печати из-за невысокой жесткости конструкции.
- Еще одним из недостатков является так называемая деламинация. Происходит это из-за открытого типа корпуса, при перемещении платформы горячий воздух нестабилен, если использовать дополнительное охлаждение, увеличивается просадка печатающих материалов, а она и без того достаточно большая.
3.2 Конструкция кинематики 3D-принтеров от компании Felix printers
Конструкция данного типа 3D-принтеров похожа на предыдущую, однако платформа теперь перемещается не вдоль одной оси Y, а вдоль двух осей Z, Y.
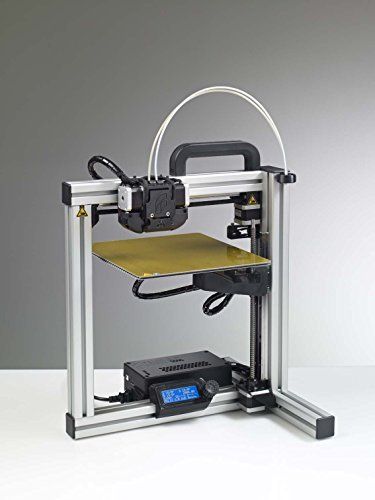
Рисунок 4 – Конструкция кинематики 3D-принтеров от компании Felix printers
Принтеров такого типа изготавливают несколько компаний, однако популярности данный принтер среди потребителей так и не нашел.
Из достоинств данной кинематики можно выделить:
- Ось Z перемещается только при помощи одного двигателя. Поэтому в данной конструкции просто физически не может быть воблинга, потому что есть два вала и один винт.
- Есть возможность установки необходимого экструдера.
- По сравнению с кинематикой предыдущего 3D принтера, есть возможность сделать жесткую раму.
Недостатки:
- Большие вибрации из-за перемещении платформы по двум осям.
- Нет возможности сделать данному 3D-принтеру термокамеру, в связи с тем же перемещением стола сразу по двум осям.
3.3 Delta кинематика
Данная кинематика основывается на движении дельта-роботов. Только вместо звена схвата устанавливается хотенд.
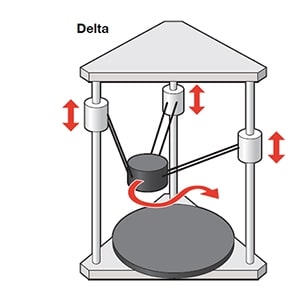
Рисунок 5 – Delta кинематика
Достоинства данной кинематики:
- Легко поддается увеличению рабочей области печати.
- Чаще всего данный 3D-принтер гораздо больше в высоту чем в ширины, за счет этого он занимает меньше места.
- Есть возможность закрыть корпус из-за отсутствующих выступающих частей.
Недостатки:
- Тяжело сделать прочную раму, что бы не было вибраций при перемещении кареток.
- Сложность в установки директ-экструдера.
- Если есть несоосности или неровности хотя бы на одной оси, они буду сильно влиять на качество печати.
- Необходимо ставить 32-битные платы.
3.4 Кинематика 3D-принтера от компании Ultimaker
Кинематика данного 3D-принтера полностью построена на валах, они выполняют роль одновременно как и направляющих, так и шкивов.
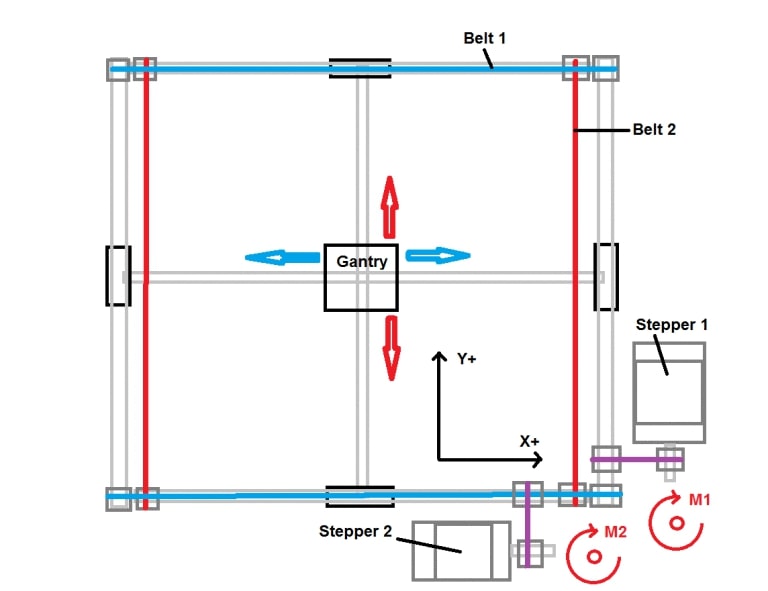
Рисунок 6 – Кинематика 3D-принтера от компании Ultimaker
Плюсы данной кинематики:
- Перемещение платформы осуществляется только по одной оси Z (вертикально). В связи с эти градиент температур никак не изменятся, поэтому просадка пластика при печати будет меньше чем у других типов принтеров.
- На первый взгляд сложная конструкция, в реализации достаточно проста, и перемещение по каждой оси осуществляется при помощи отдельного двигателя.
- Закрытый корпус, который обеспечивает поддержание стабильной температуры.
- Очень простая калибровка платформи.
Минусы кинематики:
- Оборудование для изготовление такого 3D-принтера должно быть качественно изготовлено.
- Поскольку кинематика данного принтера полностью построена на валах, их необходимо правильно выставить, а это порой оказывается достаточно сложной задачей.
- Нельзя увеличить область печати небольшими изменениями.
4. Разработка аппаратной части 3D-принтера
Кинематика разрабатываемого 3D-принтера была выбрана такая же как и у компании Ultimaker, из-за ее надежности, простоты, также она одна из самых распространённых в мире.
Перемещение рабочего органа (экструдера) осуществляется по двум горизонтальным осям (X, Y) при помощи направляющих валов, зубчатых ремней и двух двигателей Nema17HS4401. Данные двигателя являются гибридными с углом шага 1,8°, они в себе сочетают лучшие черты двигателей с переменным магнитным сопротивлением и двигателей с постоянными магнитами, а именно, имеют меньшую величину шага, большой момент и большую скорость.
Шаговые двигатели Nema17HS4401, нашли свое применение в робототехнических конструкциях, небольших станках с ЧПУ и других оборудованиях которые требуют точного позиционирования рабочего органа.
Таблица 1.1 – паспортные характеристики шагового двигателя Nema 17HS4401[11].
Модель | 17HS4401 |
Номинальный ток | 1.7 А |
Сопротивление обмотки | 1.5 Ом |
Индуктивность обмотки | 2.8 мГн |
Момент удержания | 4 кг/см |
Угол поворота на 1 шаг | 1.8° |
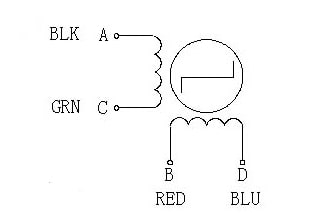
Рисунок 7 – Схема подключения шагового двигателя 17HS4401
Управление двигателями происходит с помощью драйверов DRV8825, которые позволяют ограничить ток, защитить двигатель от перегрузок и перегрева.
Обратной связью системы выступает три механических концевых датчика, при помощи которых есть возможность осуществить начальную калибровку осей, а также они исполняют роль аварийной остановки, при возникновении сбоев в работе.
Перемещение платформы с алюминиевым основанием и двумя линейными направляющими, роль которых выполняют 12 мм валы, осуществляется по вертикальной оси Z при помощи трапецеидального винта и двигателя Nema 17HS4401.
Устройством управления в разрабатываемом 3D-принтере, служит микроконтроллер ATmega 2560 на базе платы Arduino. В его состав входит все необходимое для удобной работы с микроконтроллером:
- 54 цифровых входа/выхода (из которых 15 могут использоваться в качестве ШИМ-выходов).
- 16 аналоговых входов.
- 4 UART (аппаратных приемопередатчика для реализации последовательных интерфейсов)
- Кварцевый резонатор на 16 МГц
- Разъем USB
- Разъем питания
- Разъем ICSP для внутрисхемного программирования
- Кнопка сброса
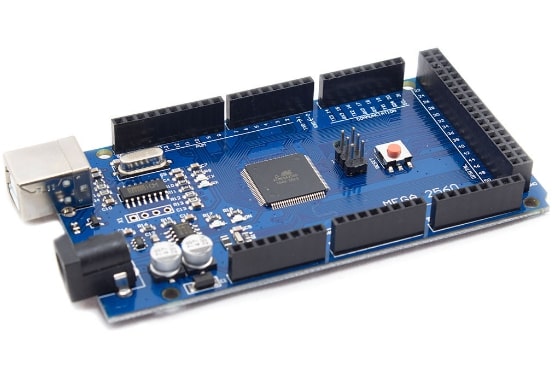
Рисунок 8 – Микроконтроллер ATmega 2560 на базе платы Arduino
Связующим звеном между микроконтроллером и другим оборудованием, выступает плата расширения RAMPS, которая кроме драйверов двигателей, также включает в себя силовые ключи, при помощи которых подается напряжение на нагреватель, экструдер и платформу.
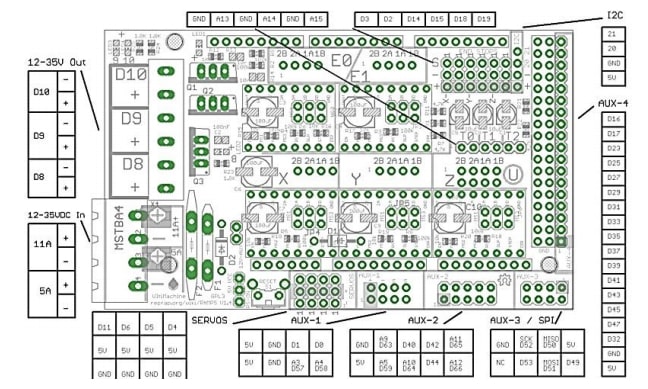
Рисунок 9 – Схема RAMPS
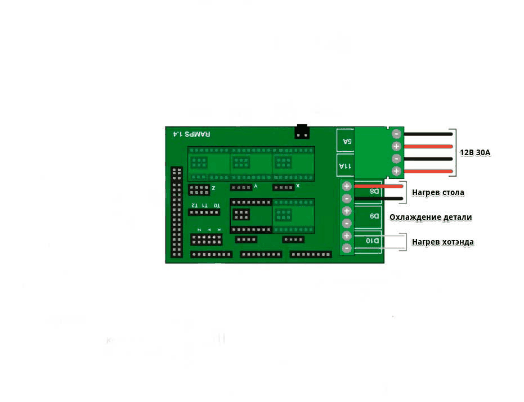
Рисунок 10 – Подключение электроники к Ramps
(анимация: 8 кадров, 8 циклов повторения, 327 килобайт)
Рабочим органом конструкции выступает боуден-экструдер, при помощи которого осуществляется послойное наплавление расплавленного пластика. Отличие такого экструдера от экструдеров с прямой подачей пластика, в том что блок подачи филамента и сопло находятся в разных местах, cold-end закрепляется на раме 3D-принтера, а hot-end устанавливается на подвижной печатающей головки. Филамент подается при помощи тефлоновой трубке. Конструкция экструдера представлена на рисунке.
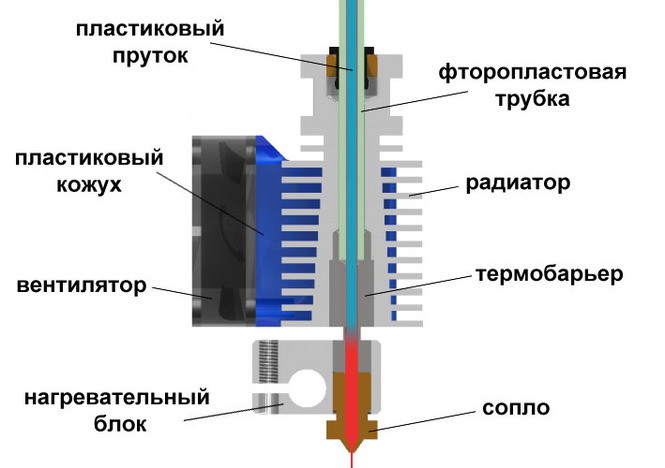
Рисунок 11 – Конструкция экструдера
Радиатор установлен для обеспечения качественного прохождения пластика, он рассеивает тепло, что бы пластик не расплавлялся внутри экструдера и не засорял проход. Вентилятор обдувает радиатор для улучшения охлаждения.
Выводы
3D-печать по-прежнему является разрабатываемой технологией и имеет аспекты, которые не были полностью проанализированы; неудачи во время процесса печати очень распространены и вызывают потерю времени и материала. Эти аспекты 3D-печати, создают отличную возможность для улучшения состояния печатающих частей, помогающих усовершенствовать создаваемые объекты.
Список источников
- М. А Зленко, А. А. Попович, И. Н. Мутылина Аддитивные технологии в машиностроении.
- Александрова В. В., Зайцева А. А. 3D-технологии и когнетивное программирование // Информационно-измерительные и управляющие системы. – 2012 -№5
- Добринский Е. С. Быстрое прототипирование: идеи, технологии, изделия // Полимерные материала. – 2011. – №9.
- Гибсон Я., Розен Д., Стакер Б. Технология аддитивного производства. Трехмерная печать, быстрое прототипирование и прямое цифровое производство.
- Мишинов С. В., Ступак В. В., Мамуладзе Т. З., Копорушко Н. А., Мамонова Н. В., Панченко А. А., Красовский И. Б., Рабинович С. С., Ларькин В. И., Долженко Д. А., Новокшонов А. В. Использование трехмерного моделирования и трехмерной печати в обучении нейрохирургов. [Электронный ресурс]. – Режим доступа: applied-research.ru.
- Научно-технический журнал вектор высоких технологий№6(11) 2014г. Реализация производства по индивидуальным заказам с помощью промышленных 3D принтеров [Электронный ресурс]. – Режим доступа: ostec-3d.ru.
- 54-я научная конференция аспирантов, магистров и студентов БГУИР, 2018 г [Электронный ресурс]. – Режим доступа: libeldoc.bsuir.by.
- Е. Б. Романова, Т. И. Веселова. Применение PR-технологий при прототипировании электронных средств
- [Электронный ресурс]. – Режим доступа: 3dtoday.ru.
- [Электронный ресурс]. – Режим доступа: 3dprofy.ru.
- Паспортные характеристики шагового двигателя Nema 17HS4401 [Электронный ресурс]. – Режим доступа: svaltera.ua.