Реферат за темою випускної роботи
Зміст
- Вступ
- 1. Актуальність теми
- 2. Мета і задачі дослідження
- 3. Аналіз робіт по темі
- 4. Заплановані практичні результати
- Перелік посилань
Вступ
Розвиток промисловості ДНР вимагає збільшення обсягу будівельних робіт, в тому числі і дорожнього будівництва. Обсяги та темпи будівництва значною мірою визначаються рівнем механізації робіт. Тому вимоги до дорожніх і будівельних машин, а також до їх обслуговування, постійно посилюються. Причому має місце не тільки кількісний, але і якісне зростання парку: з'являються нові види техніки, ускладнюється конструкція. Забезпечення працездатності такого мінливого парку машин вимагає постійного вдосконалення системи технічної експлуатації. Її значимість характеризує відомий факт, що в процесі експлуатації витрати на підтримку і відновлення працездатності машин в 6...10 разів перевищують вартість їх виготовлення. За даними дослідників близько 80% ефективності використання дорожніх і будівельних машин забезпечується засобами їх технічної експлуатації.
Довговічність деталей машин – один з головних елементів, що визначають надійність машин в цілому. Збільшення довговічності деталей дозволяє скоротити число, обсяг і тривалість ремонтів, зменшити витрату запасних частин і збільшити строки служби машин. Підвищення довговічності деталей, а, отже, і підвищення надійності машин є важливою народногосподарською проблемою, що вирішується на всіх стадіях виготовлення, монтажу, експлуатації та ремонту машин.
Типовою деталлю дорожніх і будівельних машин є кулачковий механізм.
Кулачковий механізм – це механізм з вищої кінематичною парою, володіє можливістю забезпечення законів руху вихідної ланки, а структура містить хоча б одну ланку з робочою поверхнею змінної кривизни. Кулачкові механізми призначені для перетворення руху провідної ланки в необхідний вид руху вихідної ланки відповідно до заданого закону. Ці механізми знайшли широке застосування в транспортних, технологічних та інших машинах.
На малюнку 1 показаний принцип роботи кулачкового механізму, в якому обертальний рух перетворюється в поступальний рух штовхача.
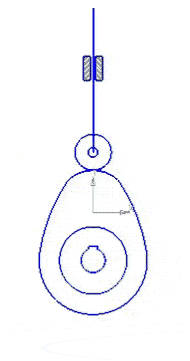
Малюнок 1 - Принцип работи кулачкового механізму
Надійність кулачкових механізмів переважно визначається довговічністю кулачків, робоча поверхня яких втрачає працездатність внаслідок контактно-втомного зносу в процесі експлуатації. У відповідність з експлуатаційним призначенням, кулачок має складну геометричну форму в торцевому перерізі і, з метою підвищення технологічності, просту-в осьовому перерізі. Апріорі передбачається наявність лінійного контакту в сполученні деталей кулачкового механізму, що має забезпечувати високу навантажувальну здатність.
Відомо, що підвищення довговічності будь-якої деталі найбільш ефективно технологічними методами, які забезпечують необхідну якість поверхневого шару. Розроблено велику кількість різних технологічних методів, які дозволяють підвищити зносостійкість поверхонь тертя, як при виготовленні, так і при ремонті. Однак, проблема обґрунтованого вибору найбільш ефективної зміцнюючої технології, пошук режимів зміцнення для конкретної деталі в даний час продовжує залишатися актуальним.
Отже, пошук, дослідження та застосування технологічних методів, що дозволяють забезпечити формування модифікованого профілю осьового перерізу кулачків, зміцнення робочої поверхні і підвищення довговічності кулачкових механізмів, є актуальною задачею.1. Актуальність теми
Найбільш ефективним і економічним способом збільшення діючого парку дорожніх, будівельних машин є підвищення їх довговічності. Одним з основних процесів, що ушкоджують, що знижують потенціал працездатності дорожньо-будівельних машин і устаткування, є інтенсивне зношування елементів машин. Відмови машин внаслідок зносу досягають 70-80% всіх відмов, що виникають в процесі експлуатації машин. У зв'язку з цим питанням зносу деталей, підвищенню довговічності приділяється більша увага.Забезпечення надійності будівельних і дорожніх машин досягається при комплексному підході до вирішення цієї задачі на всіх етапах: конструкторському, технологічному та експлуатаційному.
Довговічність відповідальних деталей машин закладена в якості їх поверхневого шару робочих поверхонь, у зв'язку з чим на етапі виготовлення технологічного забезпечення надійності закладається шляхом формування заданих експлуатаційних властивостей деталей оздоблювально-зміцнюючої обробки.
Аналіз робіт в області забезпечення довговічності деталей машин показує необхідність розробки методології підвищення зносостійкості на основі «високих» технологій.
2. Мета і задачі дослідження
Метою даної роботи є розробка підходів до синтезу комбінованих функціонально-орієнтованих технологій оздоблювально-зміцнюючої обробки забезпечують задану довговічність відповідальних деталей дорожніх, будівельних, машин. .
Для досягнення поставленої мети необхідно вирішити наступні задачі:
- Виконати дослідження умов експлуатації відповідальних деталей пар тертя дорожніх, будівельних машин.
- Дослідити і розробити принципи підвищення зносостійкості швидкозношуваних деталей з нерівномірно-розподіленим навантаженням.
- Розробити рекомендації на основі проведених досліджень.
3. Аналіз робіт по темі.
Функціональність і термін служби транспортно-технологічних машин значно залежить від надійності деталей пар тертя.
Зношування деталей дорожньо-будівельних машин обумовлено різними за своєю природою факторами:
- конструктивні – характер навантаження; вид тертя робочих поверхонь; поєднання матеріалів деталей спряження; наявність захисних покриттів;
- технологічні – методи обробки робочих поверхонь; якість складання сполучень; наявність технологічних забруднень; структура поверхневого шару металу; мікрогеометричні показники поверхонь тертя;
- експлуатаційні – характер проведених робіт та режими використання машини; кліматичні умови роботи; стан мастильних матеріалів; види і періодичність технічних обслуговувань і ремонтів [9].
Зносостійкість поверхні тертя в основному визначається значеннями стану поверхневого шару, що формуються в процесі виготовлення різними технологічними методами [2, 3]. Для підвищення довговічності деталей широке застосування отримали обробно-зміцнююча обробка ППД і нанесення зносостійких покриттів [3]. При ОЗО ППД в промисловості досить успішно застосовуються обкатка деталей роликами і кульками, Дробоструминна обробка, обробка ударними інструментами, гідроструминна і гідроабразивна обробки і т. д. [4]. На етапі виготовлення технологічного забезпечення надійності закладається шляхом правильного і точного виготовлення вузлів та агрегатів, що також важливо підвищення зносостійкості, статичної і циклічної міцності деталей термічною обробкою; зміцнення деталей хіміко-термічною обробкою: зміцнення деталей поверхневим пластичним деформуванням; нанесення на робочі поверхні деталей машин зносостійких покриттів; і т. д.
Роботи В.Ф. Без'язичного, В.І. Бутенко, А.А. Маталіна, А.Н. Михайлова, А.В. Орлова, А.Г. Суслова, В.П. Федорова, Ю.Г. Шнейдера та ін. переконливо свідчать про можливість підвищення зносостійкості як за рахунок технології обробки так і за рахунок оптимізації профілю сполучених поверхонь.
Довговічність і експлуатаційна надійність машин і обладнання в значній мірі залежить від стану і фізико-механічних властивостей поверхневого шару деталей, де зароджуються та розвиваються процеси зносу і втомного руйнування. Значного підвищення зносостійкості деталей можна добитися оптимальним поєднанням властивостей структури матеріалів і зміцнюючої обробки.
У машинобудуванні все більш широке застосування отримують деталі з робочими поверхнями, що функціонують в екстремальних умовах нерівномірно-розподіленого навантаження. Застосування звичайних технологій обробно-зміцнюючої обробки, що забезпечують рівномірний розподіл експлуатаційних властивостей по поверхні не забезпечують оптимальний ресурс для таких деталей. Методи технологічного впливу вибираються на основі особливих принципів орієнтації технологічного впливу та забезпечення заданих експлуатаційних властивостей робочих поверхонь і їх окремих функціональних елементів. При сучасних методах оздоблювально-зміцнюючої обробки в основному створюються деталі з однаковими показниками якості по всій функціональної поверхні незалежно від реальних змін умов зовнішнього навантаження в окремих зонах і навіть точках. Це змушує зміцнювати всю поверхню, виходячи з максимально діючих факторів навантаження (тиску, температури і т. д.) у визначеній зоні, що підвищує собівартість деталі, також призводить до зниження ресурсу всього вузла тертя. Вивчення характеру зносу поверхонь показує, що практично неможливо знайти поверхня тертя, в межах якої всі зовнішні фактори навантаження мали б стабільні параметри. Практично всі поверхні тертя в різних точках зношуються нерівномірно.
Особливістю роботи деталей дорожніх, будівельних машин є нерівномірність розподілу нормального навантаження і швидкостей ковзання по робочим поверхням, що призводить до нерівномірного зносу і, отже, до зменшення довговічності пар тертя в цілому. Нерівномірність зносу призводить до порушення макрогеометрії поверхні і, як наслідок, до заміни всієї поверхні [1].
В статті [10] представлена енергота ресурсозберігаюча, імпортозаміщуюча, екологічно чиста нанотехнологія поверхневого зміцнення інтенсивно зношуються деталей, що дозволяє зміцнювати великогабаритні деталі з ординарних сталей в промислових масштабах з отриманням структур нанорозмірного діапазону.
До деталей з нерівномірно розподіленим навантаженням відносяться деталі кулачкових і кулісних механізмів, кульових шарнірів, зубчастих передач, підшипники ковзання.
Довговічність кулачкових механізмів визначається нерівномірністю зносу робочої поверхні кулачків, яка супроводжується зміною прискорення штовхача. Ефективним технологічним способом підвищення довговічності кулачків кулачкових механізмів є створення великого радіуса кривизни осьового профілю робочої поверхні обробкою нескінченними еластичними алмазними стрічками з перекриттям, що дозволяє підвищити їх несучу здатність і зносостійкість порівняно з традиційними технологіями в 2 рази [5].
Ряд деталей гальмівних механізмів потребує підвищення ресурсу за характеристиками міцності і зносостійким характеристикам. До числа таких деталей відносяться корпусні деталі Гальма, в яких підвищеному зношуванню в процесі експлуатації схильні упори проміжних дисків гальмівних механізмів [6].
Сферичні шарнірні з'єднання підвищують функціональність машини і стійкість до деформацій. До сферичних шарнірних з'єднань відносяться підшипники ковзання, широко застосовуються в транспортних машинах [14-16]. В результаті досліджень [17] визначено, що довговічність кульових шарнірів в основному визначається зносостійкість контактуючих поверхонь його деталей і залежить від конструктивних, технологічних і експлуатаційних факторів. Найважливішою і трудомісткою частиною технологічного циклу при виготовленні кульового пальця є чорнова і чистова обробка неповної сферичної головки. Заготовки кульових пальців, що застосовуються в кульових шарнірах передньої підвіски, виготовляються, головним чином, холодною висадкою, або поперечно-клиновою прокаткою, фрезерування, холодного листового штампування корпусів кульових пальців [18, 19]. В якості операції чистової розмірно-зміцнюючої обробки неповної сфери кульового пальця набула поширення ротаційна (планетарна) обкатка кульками, обробно-зміцнюючої бессепаратор Ної обкатці обробно-зміцнююче обкатування [18, 21, 22].
Вибір способу технологічного впливу на робочу поверхню деталей обумовлюється функціональним призначенням цих поверхонь і їх елементів. Умови експлуатації, технологічні впливи та експлуатаційні властивості деталі взаємопов'язані між собою [1]. Схема аналізу деталі при виборі способу обробно-зміцнюючої обробки представлена на малюнку 2. Згідно структурно-логічної схеми, забезпечення функціональних параметрів виробу при формуванні поверхневого шару, характеризується експлуатаційними зв'язками. Ці характеристики залежать від параметрів якості й експлуатаційних факторів, що виникають в процесі експлуатації виробу.
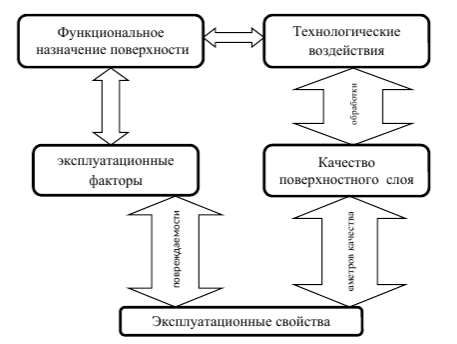
Малюнок 2 - Структурно-логічна схема
При виборі способу оздоблювально-зміцнюючої обробки необхідно враховувати функціональне призначення деталі, її міру корисності, закон розподілу по робочій поверхні і умови впливу експлуатаційних факторів.
Для підвищення функціональних властивостей виробів машинобудування необхідна розробка наукоємних технологій, ознаками яких є: формування якісно нової сукупності властивостей, як наслідок реалізація якісно нової міри корисності виробів, а також ефективність виробництва деталей машинобудування, досягається мінімізацією матеріальних, енергетичних, трудових витрат. Формування функціональних властивостей і забезпечення надійності деталі в цілому, визначаються відповідно якістю їх функціональних поверхонь, ґрунтується на принципах корисності, подібності технологічних систем і критеріальної оцінки. Метою виготовлення будь-якого виробу є забезпечення заданих експлуатаційних властивостей і заданого рівня корисності. Для цього синтез інноваційних методів обробки виробів повинен базуватися на єдності технології виготовлення та експлуатації. Розробка наукоємних напрямків забезпечення заданої міри корисності виробів є актуальним завданням машинобудування.
4. Заплановані практичні результат
В результаті виконання магістерської роботи повинні бути розроблені технології, що дозволяють підвищити довговічність дорожніх, будівельних машин.
У технологічній частині магістерської роботи планується розробка "високих" технологій комбінованої обробно-зміцнюючої обробки забезпечують задану міру корисності виробів, що виготовляються.
У дослідницькій частині планується визначити умови експлуатації деталей машин, визначити технологічні методи підвищення довговічності і розробити рекомендації на основі проведених досліджень.
Перелік посилань
- Разработка классификатора поверхностей деталей для обеспечения синтеза функционально ориентированных технологий отделочно-упрочняющей обработки / Михайлов А.Н., Лукичев А.В., Матвиенко С.А., Стрельник Ю.Н., Пичко А.П. // Прогрессивные технологии и системы машиностроения. – 2017. – №4(59). – С.31–36.
- Суслов, А.Г. Качество поверхностного слоя деталей машин. – М.: Машиностроение, 2000. – 320 с.
- Суслов, А.Г., Федоров, В.П., Горленко, О.А. и др. Технологическое обеспечение и повышение эксплуатационных свойств деталей и их соединений / под общ. ред. А.Г. Суслова. – М.: Машиностроение, 2006. – 448 с.
- Технология и инструменты отделочно-упрочняющей обработки деталей поверхностным пластическим деформированием: справочник. В 2-х томах. Т.1. /под общ. ред. А.Г. Суслова.– М.: Машиностроение, 2014. – 480 с.
- Шоев, А.Н. Технологическое повышение долговечности кулачковых механизмов / А.Н. Шоев // Справочник. Инженерный журнал. – 2010. – № 6. – С. 10–12.
- Кобяков, О.С Повышение износостойкости и ресурса работы многодисковых тормозных механизмов трактора «Беларус» лазерным термоупрочнением быстроизнашивающихся деталей / О.С. Кобяков, Спиридонов Н.В., Баркун А.А. // Вестник БНТУ – 2008. – №5. – С.10–17.
- Густов, Ю.И. Триботехника строительных машин и оборудования: монография. – М.: МГСУ, 2011. – 197 с.
- Гребенникова, Н.Н. Оптимальная стратегия эксплуатации машин / Н.Н. Гребенникова // Вестник развития науки и образования. – 2014. – № 3. – С. 25–29.
- Мухаметшина, Р.М. Трибологические отказы дорожно-строительных машин. /Известия Самарского научного центра Российской академии наук, том 18, №1(2), 2016. – С. 252–255.
- Загорский, Я.В. Повышение долговечности интенсивно изнашивающихся деталей дорожно-строительных машин / Я.В. Загорский Я. В., В.К. Загорский, И.В. Кусова. Электронный научный журнал «Нефтегазовое дело». 2016. №1 http://ogbus.ru.
- Польченко, В.В., Богуславский, В.А. Способы повышения долговечности зубчатых муфт.[Электронный ресурс] – Режим доступа http://ea.donntu.ru/bitstream/123456789/9316/1/В.В.%20Польченко.pdf.
- Мухаметшина, Р.М. Отказы дорожно-строительных машин по параметрам коррозии / Мухаметшина, Р.М.// Известия КГАСУ, 2013, №4(26). – С. 403–408.
- Старостина, Ж.А. Создание комплекса условий развития отечественного производства строительно-дорожной техники. // European Research: Innovation in Science, Education and Technology Сб. ст. по мат.: VIII межд. науч.-практ. конф. М., 2015. – C. 5–8.
- Железков, О.С. Усовершенствованный шаровый шарнир передней подвески легковых автомобилей / О.С. Железков, У.В. Михайлова // Автомобильная промышленность. – 2010. – № 3. – С. 14–15.
- Математическое моделирование технического состояния шарового шарнира в условияхстендовых испытаний / А.Н. Новиков, В.И. Чернышов, В.А. Гордон, А.А. Катунин, М.Д. Тебекин // Мир транспорта и технологических машин. – 2014. – № 4. – С. 39–46.
- Новиков, А.Н. Проблемы эксплуатации шаровых опор легковых автомобилей / Новиков А.Н., Катунин А.А., Тебекин М.Д. // Мир транспорта и технологических машин. – 2010. – № 3. – С. 42–45.
- Родионов, Ю.В. Повышение износостойкости и долговечности шаровых опор автомобилей / Ю.В. Родионов, А.А. Войнов, А.А. Шмелев // Успехи современной науки и образования. – 2017. – Том 4, №4. – С 84–86.
- Гун, И.Г. Совершенствование технологии изготовления шаровых пальцев автомобилей / И.Г. Гун, О.С. Железков, И.А Михайловский. и др. // Бюл. ин-та "Черметинформация". – 2000. – №11-12 (1211-1212). – С. 60–62.
- Катунин, А.А. Комбинированный способ отделочно-упрочняющей обработки головок шаровых пальцев / А.А. Катунин, А.В. Катунин, Н.Н. Самойлов // Мир транспорта и технологических машин. – 2010. – № 1(28). – С. 22–26.
- Катунин, А.А. Формирование шероховатости поверхности неполной сферы при обкатке бессепараторным инструментом / А.А. Катунин // Известия ОрелГТУ. – 2009. – № 3/275(561). – С. 70–75.
- Исследование кинематических параметров процесса обкатки неполной сферической головки шарового пальца / Ю.С. Степанов, А.М. Гаврилин, А.В. Катунин, А.А. Катунин // Известия ОрелГТУ. – 2009. – № 2/274(560). – С.52-56.
- Автореферат магистерской работы Назарчук В.К.Исследование долговечности и разработка предложения увеличения срока службы механизма передвижения мостового крана. [Электронный ресурс] – Режим доступа http://masters.donntu.ru/2007/fema/nazarchuk/diss/index.htm.
- Бобырь, Н. А. Повышение качества поверхностного слоя деталей машин при отделочной обработке [Электронный ресурс] – Режим доступа http://masters.donntu.ru/2003/mech/bobyr/diss/index.html.
- Автореферат магистерской работы Дубоделовой О.С. на тему: «Повышение качества обработки деталей машин с использованием методов поверхностно-пластического деформирования». [Электронный ресурс] – Режим доступа http://masters.donntu.ru/2005/mech/dubodelova/diss/index.htm.