Реферат по теме выпускной работы
Содержание
1. Введение
Современная подъемная установка – одно из важнейших сооружений шахтного комплекса. Это сложный электромеханический механизм, состоящий из отдельных элементов, выполняющих различные функции. От нормальной работы этой установки зависит бесперебойная и продуктивная работа всей шахты, потому, что подъемная установка – основной связующий элемент между поверхностной и подземной частью шахты. В случае выхода подъема из строя останавливается работа всего предприятия.
Один из факторов, влияющий на работу установки – тепловой баланс подшипниковых узлов.
На большинстве шахт температура подшипниковых узлов не контролируется, или контролируется аппаратурой, выполненной на устаревшей элементной базе и не соответствует современному уровню и нормам. Это приводит к увеличению количества простоев установки и к дополнительным убыткам. Поэтому разработка аппаратуры контроля подшипниковых узлов шахтной подъемной установки, которая будет уменьшать количество простоев установки, актуальна.
2. Цель работы
Таким образом, целью работы является повышение эффективности работы шахтной подъемной установки путем совершенствования аппаратуры контроля температура подшипниковых узлов.
3. Объект автоматизации и его особенности
Главный скиповой подъем – основное связующее звено между подземной частью шахты и ее поверхностью. Он предназначен для спускаподъема оборудования, материалов, полезных ископаемых и породы. Согласно рисунка 1, скорость движения сосуда контролируется тахогенератором BV1 и BV2. Тахогенератор BV1 получает вращение от подъемных двигателей 1, а BV2 – от ретардирующего устройства. От тахогенераторов э.д.с. поступает на соответствующие реле ограничения скорости К1 или К2.
С помощью магнитоупругих индуктивных датчиков 2 и 4, которые установлены под корпусами подшипников копровых шкивов 3, осуществляется контроль зависания скипа в стволе.
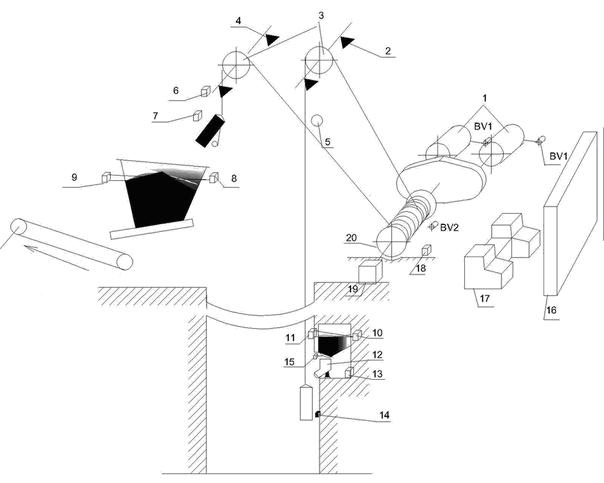
Рисунок 1 – Технологическая схема автоматизированной скиповой подъемной установки
Защита от переподъема скипа осуществляется бесконтактными индуктивными датчиками 5 и 6 на копре и концевыми выключателями на пульте управления 17 в блоке указателя глубины.
Подход скипа к месту разгрузки на копре и места загрузки в стволе контролируется взрывобезопасными магнитными выключателями 7 (разгрузки) и 14 (загрузки).
Уровень нижнего и верхнего бункеров контролируется рудничными взрыва–защитными гамма–реле. Поток гамма–квантов от источников 8 (верхний бункер) и 10 (нижний бункер) проходит через контролируемую среду и регистрируется датчиками 9 и 11.
При дозировке скипа с помощью веса доза угля взвешивается силоизмерительным датчиком 12 (магнитоупругим или тензометрическим), сигнал с которых принимается электронным блоком 13. 15 – исполнительный механизм загрузочного устройства, 16 – схема управления подъемной машиной, 20 – датчики контроля температуры подшипников.
Режимы работы скиповой подъемной установки
На главном скиповом подъеме предусмотрена возможность осуществления двух режимов работы: с полной скоростью и пониженной.
Режим работы с полной скоростью осуществляется при спуске–подъеме оборудования, выдачи груза с горизонтов.
Режим работы с пониженной скоростью осуществляется при ревизии ствола, спуска взрывоопасных веществ и других вспомогательных операций.
Способ управления установкой – автоматический. При таком способе цикл подъема осуществляется по заданной тахограмме без вмешательства человека. Пульт дистанционного управления расположен на приемном участке в надшахтном здании.
На рисунке 2 приведена тахограмма движения скипов подъемной установки. Тахограма шестипериодная с прямолинейным изменением скорости в неустановленные периоды.
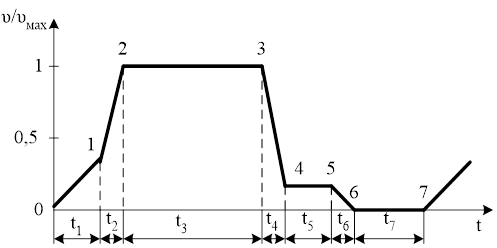
Рисунок 2 – Тахограмма движения скипов подъемной установки
В период дотягивания сосуда к месту разгрузки требуется двигательное усилие на ободе барабана в течение всего периода. При спуске диаграмма имеет значение движущихся усилий ниже нуля.
Согласно рисунку 2 на участке 0–1 осуществляется движение подъемного сосуда в разгрузочных кривых.
дъемного сосуда в разгрузочных кривых. На участке 1–2 машина движется с ускорением после выхода скипа с разгрузочных кривых.
На участке 2–3 подъемные сосуды движутся с максимальной скоростью. Участок 4–5 соответствует движению скипа в разгрузочных кривых. На участке 5–6 происходит процесс конечного останова. Участок 6–7 соответствует паузе между двумя периодами подъема.
На рисунке 3: t0 – период ускорения при перемещении скипа в кривых, t1 – период нормального ускорения после выхода скипа из кривых, t2 – период движения с максимальной скоростью, t3 – период нормального замедления, tп – период движения скипа со скоростью дотягивания, tс – время стопорения машины.
Цель проектирования – повышение эффективности работы шахтной подъемной установки путем разработки блока автоматической защиты подшипников от перегрева.
Требование к системе автоматизации подъемной установки:
- контроль работы погрузочно–разгрузочных устройств по состоянию технологического оборудования установки;
- обеспечение программного выполнения тахограммы независимо от изменения нагрузки в заданных пределах;
- обеспечение безопасности работы установки и сигнализации о режимах работы, и причины отклонения от заданного режима;
- наличие защит и блокировок для контроля исправностей отдельных элементов оборудования;
- наличие связи с оператором и возможность задания уставок и осуществления визуального контроля за работой;
- контроль температуры подшипниковых узлов на установке.
Задачи, которые решаются:
- разработать новую аппаратуру контроля температуры подшипников;
- расширить функции новой аппаратуры по сравнению со старой.
Технические требования к аппаратуре контроля температуры:
- контролируемая температура – 70 ° С;
- допустимое отклонение температуры срабатывания от контролируемой – 5 °С;
- инерционность – не более 20 с;количество контролируемых узлов – не менее 6; номинальное сопротивление при 0 ° C = 100 Ом;
- пределы преобразования – 0 до 90 ° С
Перегрузки в системе и неисправность подшипникового узла могут привести к остановке подъема на значительный промежуток времени, что в свою очередь приведет к остановке работы всей шахты и дополнительным убыткам.
Для оценки динамических свойств объекта контроля разработана математическая модель нагрева подшипников на основе уравнения теплового баланса. Основными параметрами уравнений модели являются коэффициент охлаждения и масса подшипника, конструкция, теплоемкость, коэффициент трения.
Температура подшипника в установившемся режиме зависит от нагрузки, частоты вращения и характеристик теплопроводности машины. Дифференциальное уравнение, описывающее изменение температуры подшипника в функции времени имеет вид:
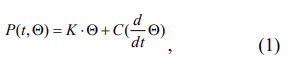
где К – коэффициент охлаждения, Вт/°С; θ – температура нагрева подшипника, °С; С – теплоемкость подшипника, (Вт*ч/кг*град); t – время моделирования, с.
Запись дифференциального уравнения в форме Коши имеет вид:

где P(t) – изменение мощности трения в подшипнике в функции времени. При нормальном режиме процесс нагрева подшипника инерционный и не претерпевает резких температурных изменений, что видно по рис.1. График изменения момента трения (рис.1) определяется выражением:

где η – коэффициент трения; Fd (t) – изменение диаметральной нагрузки на подшипнике в функции времени, Н; d – диаметр подшипника, м.
Разработаем модель процесса нагрева подшипников подъемной установки на основе использования физических законов, которые описывают поведения и состояние объекта. Тепловой баланс в подшипнике устанавливается по моменту трения М (Н*м), мощности трения ΔРтр (Вт), которая зависит от силы трения, обуславливая нагрев всего подшипника, и теплоты, которая выделилась при этом, W (Дж), потому что возникновение значительного перепада температур является следствием усиления трения в подшипнике.
Мощность трения зависит от нагрузки на подшипник, а именно от частоты вращения подшипника и радиальной нагрузки. Также на тепловой баланс подшипника значительное влияние имеет его конструкция, а именно его диаметр, высота и ширина корпуса, которые составляют внешнюю охлаждающую поверхность, через которую осуществляется теплообмен между подшипником и внешней средой. Нельзя не учитывать теплоемкость материала, из которого изготовлен подшипник. Теплоемкость зависит от вида стали подшипника и его массы. рассматривается стандартный подшипник для скиповой подъемной установки 2Ц–5*2,4 типа 3003752. В результате моделирования перегрева подшипникового узла были получены следующие зависимости (Рис. 3–5).
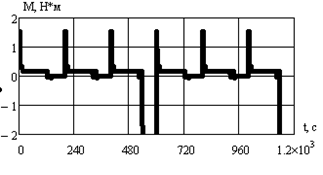
Рисунок 3 – График зависимости момента трения в подшипнике от времени работы подъемной установки
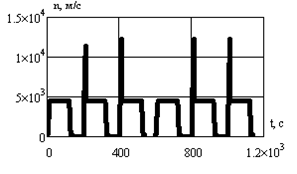
Рисунок 4 – График зависимости скорости вращения подшипника от времени работы подъема
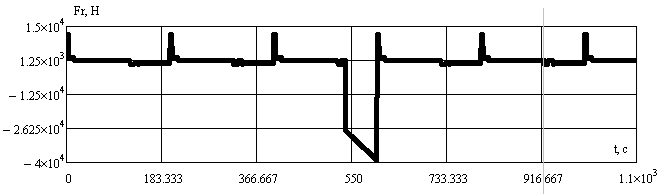
Рисунок 5 – График зависимости радиальной нагрузки на подшипник от времени работы подъема
В случае, если смазки недостаточно, температура резко возрастает, что видно на рисунке 6.
Согласно результатам математического моделирования процесса нагрева подшипника скиповой подъемной установки, можно сделать следующие выводы. При нормальной работе подъемной установки (без перегрузки и при исправном подшипнике) температура подшипника колеблется в пределах 35– 40 °С, что отвечает ПБ при работе подъема. Однако, перегрузка в системе и неисправимость в подшипнике (механические повреждения, загрязнения смазки, и тому подобное) вызывают повышение температуры подшипника и невозможность последующего его использования, пока температура снова не установится в пределах нормы.

Рисунок 6 – График процесса нагрева в функции времени
Таким образом, полученные результаты показывают необходимость контроля температуры подшипников подъемной установки, так как, когда подшипник окончательно выйдет из строя, работа подъема остановится на большой отрезок времени, а это приведет к прекращению работы всей шахты и к дополнительным убыткам (увеличение простоев, затраты, на замену старого подшипника на новый). Контроль температуры подшипников позволит избежать замены подшипников, то есть сократить время простоев и уменьшить расходы.
Разработанная модель позволяет оценивать скорость изменения температуры подшипника и определять уставки для прогноза перегрева. Анализ литературных источников [1] показывает, что для автоматизации скиповой подъемной установки наиболее подходящей является система ЗДКР.
К достоинствам можно отнести: универсальность системы – постоянный мониторинг ситуации и обеспечение условий для своевременного проведения предупредительных мероприятий по обеспечению безопасной работы (регистрация, хранение, автоматизированное воспроизведение исторической информации о работе установки за необходимый временной интервал).
К недостаткам следует отнести высокую стоимость комплектующих системы.
Целью настоящей работы является модернизация и внедрение разрабатываемого блока автоматического контроля температуры подшипникового узла скиповой подъемной установки в данную аппаратуру. Структурная схема разрабатываемого устройства показана на рисунке 7. Работа структурной схемы заключается в следующем. Сигналы от датчиков температуры ТД 1..6 подаются на мостовую схему, проходят сквозь операционный усилитель, блок согласования и поступают на вход микроконтроллера. Если температура превысит 70°С – микроконтроллер выдаст команду на остановку подъемной установки. При этом включаются звуковая сигнализация и устройство индикации. В случае постепенного нарастания температуры и превышения порога в 60°С микроконтроллер выдаст предупредительный сигнал оператору ЭВМ и включит устройство соответствующей индикации.
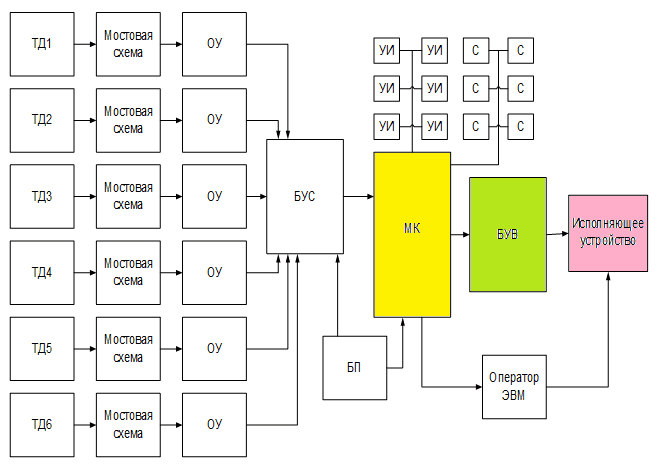
Рисунок 7 – Структурная схема устройства контроля теплового режима (анимация: 3 кадра, задержка 150 мс, 35.5 килобайт)
Приведенная структурная схема состоит из следующих блоков: ТД1..ТД6 – температурные датчики; ОУ – операционный усилитель; БУС – блок согласования; МК – микроконтроллер; БП – блок питания; УИ – устройство индикации; С – светодиоды; БУВ – блок согласования выходных сигналов.
Выводы
В результате выполненной работы повышен уровень автоматизации и надежности скиповой подъемной установки.
К достоинствам разработки следует отнести:
- возможность контроля градиента температуры подшипниковых узлов установки;
- возможность настройки порога срабатывания аппаратуры контроля;
- применение современной элементной базы;
- невысокие затраты на установку и обслуживание устройства.
Данный блок, являясь составной частью крупной системы может использоваться как отдельно, так и в составе аппаратуры управления скиповой подъемной установкой.
На момент написания данного реферата магистерская работа еще не завершена. Окончательное завершение: июнь 2019 года. Полный текст работы и материалы по теме могут быть получены у автора или его руководителя после указанной даты.
Список источников
- Бежок В. Р., Дворников В. И., Манец И. Г., Пристром В. А. Шахтный подъем: Научно–производственное издание / В. Р. Бежок и другие. Шахтный подъем: Научно–производственное издание. – Донецк:ООО «Юго–Восток,Лтд», 2007. – 624 с.
- Батицкий В. А., Куроедов В. И., Рыжков А. А. Автоматизация производственных процессов в АСУП в горной промышленности: учебник для техникумов. / В. А. Батицкий и другие. Автоматизация производственных процессов в АСУП в горной промышленности: учебник для техникумов – М.:Недра,1981.– 320 с.
- Дворников В. И., Къерцелин Е. Р., Трибухин В. А., Савенко Э. С. Динамические жесткости канатов шахтных подъемных установок / В. И. Дворников, Е. Р. Къерцелин, В. А. Трибухин, Э. С. Савенко // Стальные канаты. – Одесса, 2003. – Вып. 3.
- Шахтный подъем: Научно–производственное издание / В. Р. Бежок, В. И. Дворников, И. Г. Манец, В. А. Пристром; общ. ред. Б. А. Грядущий, В. А. Корсун. – Донецк : ООО «Юго-Восток Лтд», 2007. – 624 с.
- Степанов А. Г. Динамика шахтных подъёмных установок / Анатолий Григорьевич Степанов. – Пермь : УрО РАН, 1994. – 263 с.
- Степанов А. Г. Динамика машин / А. Г. Степанов. – Екатеринбург: Российская академия наук, 1999. – 392 с.
- Степанов А. Г., Корняков М. В. Динамика машин : монография. 2–е изд., испр. и доп. / А. Г. Степанов, М. В. Корняков. – Иркутск : Изд-во ИрГТУ, 2014. – 412 с.
- Степанов А. Г. Динамические процессы при скольжении канатов по футеровке барабана многоканатной подъемной установки / А. Г. Степанов // Горное оборудование и электромеханика. № 6, 2010. – C. 24-35.
- Колосов Л. В., Потураев В. Н., Червоненко А. Г., Безпалько В. В., Завозин Л. Ф. Вертикальный транспорт на горных предприятиях / Л. В. Колосов, В. Н. Потураев , А. Г. Червоненко, В. В. Безпалько, Л. Ф. Завозин. – М.: Недра, 1975. – 350с.