Реферат по теме выпускной работы
Содержание
- 1. Технологическая схема системы дегазации шахтных выработок
- 2. Состав и принцип работы системы дегазации шахтных выработок
- 3. Функциональная схема системы контроля и управления
- Список источников
1. Технологическая схема системы дегазации шахтных выработок
Относительное количество шахт, на которых происходят газодинамические явления с каждым годом увеличивается. В угледобывающих странах наблюдается тенденция к уменьшению количества шахт, лав и к росту нагрузки на забой. Газодинамические явления сдерживают дальнейшее увеличение добычи в высоко нагруженных лавах, скоростную проходку подготовительных выработок. Организация добычи метана с шахтных пластов позволит существенно расширить энергетическую базу страны, повысить безопасность добычи угля и экологическую безопасность окружающей среды. Поэтому в настоящее время являются актуальными разработка и внедрение дегазационных систем, позволяющих извлекать метан из угольных пластов и использовать его.
Одновременно с разработкой технологических схем дегазации, выбором и созданием нового оборудования разрабатывают системы контроля и автоматизации управления.
Источниками метановыделений на выемочном участке являются: разрабатываемый пласт, смежные пласты-спутники и вмещающие породы. Увеличение глубины разработки и повышение нагрузок на очистные забои приводит к возрастанию абсолютного метановыделения на выемочных участках. Возможности вентиляции по разбавлению метана свежим воздухом до допустимой Правилами безопасности концентрации ограничены из-за недопустимости превышения средней скорости движения воздуха в призабойных пространствах лав выше 6м/с. В связи с этим на высокогазообильных выемочных участках газовый фактор может ограничивать величину нагрузки на очистные забои.
При этом Количество воздуха, которое необходимо подавать на выемочный участок зависит от метановыделения и определяется по формуле
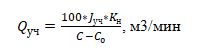
Кн - коэффициент неравномерности метановыделения;
С – допустимая ПБ концентрация метана в исходящей струе участка, %;
С0 - концентрация метана в струе воздуха, поступающего на участок.
Однако, во многих случаях подача необходимого количества воздуха на выемочные участки и в очистные забои невозможна. Это может быть по следующим причинам:
- Фактическое аэродинамическое сопротивление вентиляционной сети превышает проектное, а, следовательно, выбранный вентилятор не может обеспечить шахту и участки необходимым количеством воздуха.
- Подача воздуха в очистной забой и на выемочный участок ограничена скоростью движения воздуха в забое, которая согласно ПБ должна быть не более 4 м/с.
Одним из весьма эффективных способов обеспечения безопасных атмосферных условий на высокогазообильных выемочных участках и снятия ограничений газового фактора на нагрузку очистных забоев является дегазация источников метановыделения.
Согласно действующему нормативному документу [4] дегазация источников метановыделения на выемочных участках в угольных шахтах должна осуществляться, если средствами вентиляции невозможно обеспечить содержание метана в воздухе участковых выработок с учётом установленного ПБ значения и если не выполняется условие
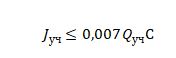
где, Jуч – среднее абсолютное метановыделение на выемочном участке, м 3 /мин; Qуч – фактический или планируемый расход воздуха, подаваемого на выемочный участок, м3 /мин; С – максимально допустимая концентрация метана в исходящей струе (ПБ), %
Типовая структура дегазационной системы горной выработки изображена на рисунке 1. Дегазационная система состоит из распределенных в пространстве дегазационных скважин, газоотсасывающего трубопровода (рис.2), проложенного по горным выработкам, стволу и на поверхности шахты, вакуум-насосной станции на поверхности. Скважины присоединяются к газоотсасывательному трубопроводу. Каждая скважина оборудуется заслоном, водоотделителем, патрубками для измерения вакуума, дебита скважины и концентрации метана переносными приборами и для установки стационарных датчиков.
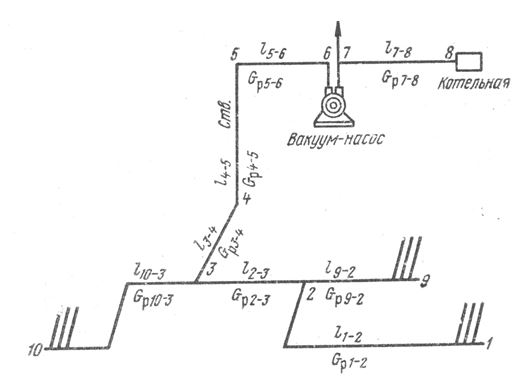
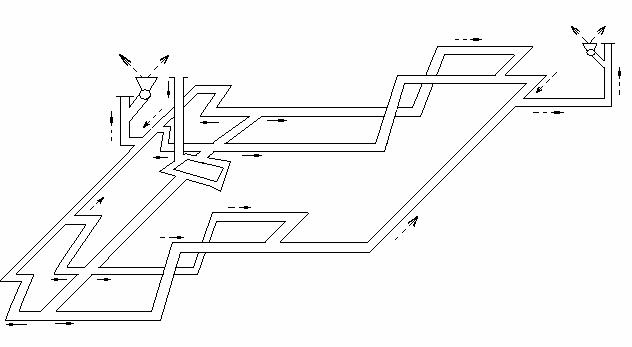
Каждая скважина имеет ограниченный срок службы, обусловленный предельно допустимыми минимальным дебитом скважины и концентрацией метана в метановоздушной смеси.
По окончании срока службы скважины оборудования демонтируется и переносится на новую скважину. На отработанных скважинах устанавливаются заглушки, а устье скважин заливаются цементным раствором.
Всасывающий газопровод, проложенный на поверхности от ствола шахты, присоединяется к вакуум-насоса. По нагнетательному трубопроводу газ подается в котельную. Вакуум-насосная станция оснащена стационарными приборами для контроля, измерения параметров и защиты дегазационной системы.
2. Состав и принцип работы системы дегазации шахтных выработок
Основной задачей системы дегазации шахтных выработок является поддержание требуемой концентрации метана, а так же иных аэрологических параметров в выработке, тем самым обеспечивая безопасное проведение рабочих процессов внутри шахты.
Приборы для контроля и измерения параметров находятся на территории самой шахтной выработки. Они относятся к системе аэрогазового контроля (АГК). В систему АГК входят датчики контроля состава и параметров шахтной атмосферы, аппаратура автоматического контроля расхода воздуха, аппаратура автоматического контроля работы и управления вентиляторами местного проветривания (ВМП), устройства звукового оповещения и (или) световой сигнализации в подземных выработках об аварийной ситуации на контролируемом объекте, взрывозащищенные источники питания.
Система АГК должна обеспечивать: непрерывное централизованное слежение за параметрами рудничной атмосферы (концентрация газов, скорость движения воздуха, температура, давление, влажность) в целях текущего (оперативного) обнаружения природных и техногенных опасностей, влияющих прямо или косвенно на состояние рудничной атмосферы; принятие своевременных мер по обеспечению безопасности труда путем нормализации параметров рудничной атмосферы или прекращения горных работ; хранение информации и последующее ее использование при разработке комплексных общешахтных мероприятий по технике безопасности, при расчетах количества воздуха, подаваемого в горные выработки, а также для установления категории шахты по газопроявлениям.
Подсистема автоматического управления вентиляторами ВМП предназначена для управления вентиляторами местного проветривания ВМП и отключения электроснабжения электропотребителей, как возможного источника инициирования взрыва метано-воздушной среды, при отклонении от заданного режима проветривания подготовительной выработки. Требования к подсистемы автоматического управления вентиляторами ВМП:
- Обеспечить включение рабочего или резервного ВМП при плавном заполнение вентиляционного трубопровода воздухом;
- Обеспечить автоматическое включение резервного ВМП при отключении рабочего ВМП, тем самым обеспечить непрерывность подачи воздуха в тупиковую выработку;
- Обеспечить выдержку времени на подачу напряжения к электроприемникам тупикового забоя после включения вентилятора ВМП с момента выдачи датчиком скорости воздуха сигнала о нормальном проветривании выработки;
- Отключение электроэнергии от электроприемников тупиковой выработке при нарушении процесса проветривания или отключении вентилятора ВМП;
- Обеспечить управление вентилятором ВМП с диспетчерского пункта шахты;
- Обеспечить местную световую сигнализацию и информацией диспетчера шахты о работе вентилятора ВМП, о снижении скорости воздуха, подаваемого к забою, до величины, меньшей заданной уставки, наличии напряжения в резервной сети, снятии блокировки на включении группового аппарата;
- Обеспечить защиту исполнительного реле от самовыключения при кратковременном (в течение 3-5 с) повышении питающего напряжения до 1,5 Uном и сохранность его во включенном состоянии при снижении напряжения питающей сети;
- При необходимости обеспечить автоматическое разгазирование горной выработки;
- Автоматическое регулирование режима работы вентилятора ВМП.
Все вышеперечисленные системы входят в состав системы контроля и управления технологическими процессами шахты, которая выглядит следующим образом (рис. 3):
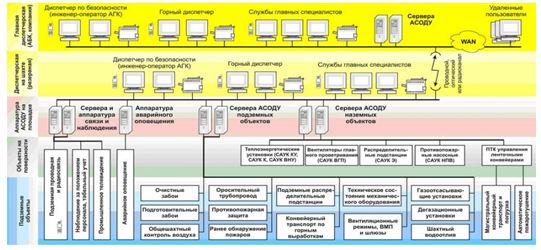
На рисунке 1.2 показана типовая структура автоматизированной системы оперативно-диспетчерского управления (АСОДУ) с указанием типовых контролируемых и управляемых процессов. АСОДУ с такой типовой структурой реализуются на многих горных предприятиях с комбинированием программно-технических комплексов различных производителей. АСОДУ реализует функции диспетчерского и автоматического управления объектами, при этом алгоритмы технологического управления объектами реализуются программно-техническими средствами, входящими в состав локальных подсистем автоматизации: на местном уровне реализуются «малые» циклы технологического и противоаварийного управления, обеспечивая высокую надежность и оперативность выработки управляющих воздействий. Сбор информации о контролируемых объектах в единую информационную систему обеспечивает диспетчеризацию горно-технологических объектов, оптимизацию технологических и производственных процессов.
3. Функциональная схема системы контроля и управления
Техническое обеспечение системы контроля и управления процессом дегазации представляет собой совокупность используемых технических средств.
Основными компонентами системы являются:
- вычислительный блок (далее ВБ);
- повторитель сигналов;
- барьер искробезопасности (также работает как повторитель);
- источник питания;
- датчики;
- линии связи;
- блок управления вмп.
- вычислительный блок;
- датчики;
- источник питания;
- блок управления вмп (только для ИС, расположенных в выработке).
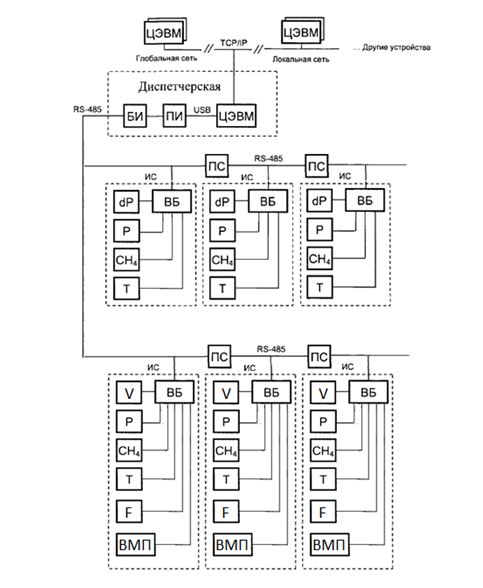
ПИ – преобразователь интерфейсов;
БИ – барьер искрозащиты;
ПС – повторитель сигналов;
ВБ – вычислительный блок;
dP – датчик дифференциального давления;
P – датчик абсолютного давления;
〖CH〗_4 – датчик концентрации метана;
Т – датчик температуры;
F – датчик влажности;
V – датчик скорости потока воздуха;
ИС – измерительная станция;
ВМП – блок управления вентилятором местного проветривания.
Работу системы в общем виде можно представить следующим образом: вычислительный блок, входящий в состав измерительной станции, опрашивает датчики метана, абсолютного и дифференциального давления и температуры, считывает состояния дискретных входов. На основании полученных данных рассчитывает значения дебита метана и расхода метановоздушной смеси. ВБ проверяет данные на выход за границы допустимых значений и выставляет необходимые статусы, используя всю полученную информацию, производит управление блоком ВМП.
Вычислительный блок (ВБ) представляет собой устройство сбора, обработки, отображения и передачи информации от датчиков. Другими словами, ВБ можно назвать контроллером, в состав которого входит процессорный модуль и периферия.
ИС, которые представляют собой программно-аппаратные комплексы, устанавливаются в местах, где необходимо контролировать параметры метановоздушной смеси. Все ИС объединяются в единую сеть, в которой они работают как подчиненные устройства. Ведущее устройство, представляющее собой ПК с установленным на нем сервером (Диспетчерская), опрашивает поочередно ИС и предоставляет полученную информацию для клиентских систем. В свою очередь ПК может быть включен в сеть более высокого уровня.
ВБ может работать в двух режимах:
- режим измерения, в котором проводятся измерения сигналов с датчиков, обработка и запись (передача) данных, отображение измеренных значений и просмотр текущей конфигурации;
- режим конфигурирования ВБ, который предназначен для ввода настроечных параметров: диапазонов измерения датчиков, порогов срабатывания световой сигнализации, корректировки внутренних часов ВБ, номера станции и скорости по modbus.
Повторитель сигналов служит для удлинения линии передачи данных стандарта RS-485.
Барьер искробезопасности предназначен для неповреждаемого гальванического разделения искробезопасных сегментов линии RS-485 от искроопасных сетей переменного тока во взрывобезопасных зонах. Также он может выполнять функции повторителя.
Блок управления ВМП производит управление приводом вентилятора местного проветривания. Общая структура блока показана на рисунке 5.
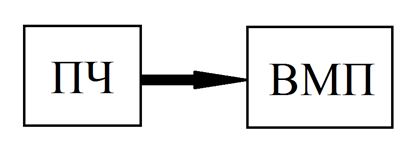
За счет изменения потока воздуха Qвх на входе ВМП посредством регулиро-вания частоты f подводимого к двигателю напряжения по заданию f* для ПЧ поток Qвихподдерживается на заданном уровне Q*вих. Величина Qвих определяется косвенно по скорости выходного потока Vвих, регулирование осуществляется по отклонению с применением ПИД-регулирования.
Список источников
- Звягильский Е.Л., Бокий Б.В. Пути совершенствования технологических схем дегазации // Уголь. – 2007. – №12.
- Карпов Е. Ф., Рязанов А. В. Автоматизация и контроль дегазационных систем. – М.: Недра, 1983, – 190 с.
- Колл.авт. Инструкция по дегазации угольных шахт. – М.: Закрытое акционерное общество «Научно-технический центр по безопасности в промышленности», 2012. – 250 с.
- Абдрахманов М.И. Задачи автоматизации дегазационной установки // Материалы Уральской горнопромышленной декады, г. Екатеринбург, 14-23 апреля 2008 г. – Екатеринбург, 2008.
- РЭ АПТВ.М.КП по ст. 1999 г., г. Прокопьевск 2010.
- ГОСТ 6625-85 Вентиляторы шахтные местного проветривания.
- Забурдяев B.C., Бухны Д.И. Особенности проектирования дегазационных систем на протяженных шахтных полях // Безопасность труда в промышленности. – 2012. – № 7.
- Васенин И.М. Математическое моделирование нестационарных процессов вентиляции сети выработок угольной шахты / И.М. Васенин, Э.Р. Шрагер, А.Ю. Крайнов, Д.Ю. Палеев, О.Ю. Лукашов, В.Н. Костеренко // Компьютерные исследования и моделирование. – 2011. – № 2. – С 155 – 163.
- Забурдяев B.C. Дегазация угольных шахт – эффективный способ обеспечения безопасности горных работ в метанообильных шахтах / B.C. Забурдяев, Ю.Ф. Руденко, В.Н. Костеренко, Е.П. Ютяев, Е.В.Мазаник // Безопасность труда в промышленности. – 2010. – №11.