Abstract
Content
- Introduction
- 1. Relevance of the topic
- 2. Purpose and objectives of the study, planned results
- 3. Scientific and theoretical foundations of enterprise cost management
- 3.1 The role of costs and costs in the operation of the enterprise
- 3.2 Classification of costs and types of costs
- 3.3 Features and need for cost management
- 4. Determination and regulation of costs in order to stabilize and reduce them
- Conclusion
- References
Introduction
In the modern socio-economic conditions of the functioning of any society and state, financial management turns into a central management mechanism, implemented through relatively independent tasks, the solution of which is aimed at providing all business entities with financial resources and achieving a synergistic effect from management actions.
Meanwhile, many enterprises, possessing large production capacities and highly qualified labor resources, operate ineffectively and are unable to withstand market competition. And also the heads of many enterprises do not have sufficient knowledge of modern methods of effective management of the formation and distribution of profits and profitability in the process of financial activities.
Traditional approaches to cost management, widely used in enterprises, do not meet the requirements of the current level of production development and increased competition, and management accounting systems often provide misleading information that is not suitable for decision-making. The value of the main types of resources spent on the production of products greatly affects the efficiency of production, the amount of profit and the level of profitability. Therefore, an enterprise using various types of resources: material, labor, technological, financial, etc., needs to effectively manage them in order to know how they relate to each other, what decisions to make to increase their return.
The efficiency of the enterprise depends on the rational use of all types of resources, which necessitates the transition to a unified cost management system. This management decision will ensure the competitiveness of products and services at the expense of lower costs; availability of high-quality and reliable information about the cost of certain types of products and their position on the market in comparison with competitors, the ability to assess the activities of each division in the enterprise and make effective and well-grounded decisions.
1. Relevance of the topic
The problem of cost management is investigated in the works of I.A. Goncharenko, S.A. Kotlyarova, Yu.B. Kravchuk, I.A. Blank, V.P. Savchuk, A.A. Turilo, F.F. Efimova, O.A. Moshkovsky, L.V. Napadovskaya, N.A. Skrypnik, A. Varchuk, A. N. Mukhin, N.G. Yatsenko, L.I. Abalkin, V.F. Paliy, N.G. Chumachenko et al. Each scientist explains his approach to cost management differently, taking into account his experience and the experience of other scientists.
However, most scientists consider cost management separately from enterprise development processes. Therefore, a complex, integrated cost management method has not found sufficient theoretical and practical justification.
Certain issues of increasing the efficiency of enterprise cost management have not been studied enough. In particular, there are different approaches to the factors influencing the costs of the enterprise, discrepancies in the methods of calculation, analysis, main indicators and complex assessment of the costs of the enterprise. The processes of developing specific search mechanisms and implementing internal reserves of cost savings for enterprises also require further development.
2. Purpose and objectives of the study, planned results
The purpose of the study is to further develop the theoretical foundations and develop guidelines for improving the cost management system at the enterprise in modern economic conditions.
The main objectives of the research:
- Explore the scientific and theoretical foundations of cost management at the enterprise.
- Determine the role of costs and costs in the functioning of the enterprise.
- Examine cost classification and cost types.
- Consider the specifics and need for cost management.
Research object: economic and business processes that are carried out at the enterprise.
Research subject: specifics of the formation and analysis of costs in the enterprise.
As part of the master's work, it is planned to obtain relevant scientific results in the following areas:
- Improvement of enterprise cost classification.
- Revealing tendencies of enterprise development.
- Development of guidelines for improving the cost management system at the enterprise in modern business conditions.
3. Scientific and theoretical foundations of enterprise cost management
The activity of any enterprise consists in the production of various products and their sale to end consumers. It is impossible to accomplish such a task without costs, since they are one of the main performance indicators. The essence of the enterprise economy consists in determining the costs and results of production and their comparison with each other. The results of the activity of an enterprise or organization are diverse and include, together with production and economic (financial) results, achievements in the field of technical and social development. Comparison of costs and benefits makes it possible to assess the efficiency of the enterprise. By itself, the concept of costs
is typical for the activities of any business entity, however, an analysis of literary sources and recent scientific publications indicates that today there is no consensus on its interpretation. In modern conditions, there are different approaches to the definition of the concept of costs
, which causes a lot of controversy and becomes difficult to manage.
3.1 The role of costs and costs in the functioning of the enterprise
Sytnik O.E. believes that costs are any payments for the use of resources of enterprises, entrepreneurs, private producers for the production, circulation, sale of products [24]. Dyachenko O.G. states that costs reflect the valuation of the resources used [10].
Other authors also give a similar definition to the concept of costs
: S.А. Kotlyarova, G.V. Nashkerskaya, Yu.B. Kravchuk, A.M. Turilo. In their opinion, costs are a value expression of the amount of resources used, aimed at achieving the production and economic goals and achieving the set goal of the enterprise.
V.P. Deriy defines costs as stocks, fixed assets and other resources of the enterprise that were used in the course of production and economic activities [8]. T.Yu. Druzhilovskaya believes that costs are neither assets, nor liabilities, nor capital, nor expenses, nor income of the organization. They represent the value of what forms the cost of the acquired asset. In other words, costs determine how accounting items are valued, such as work in progress, finished goods, etc.[9].
The concept of costs
should be understood as a monetary expression of the resources consumed, as well as the work and services performed for the enterprise.
Quite often, the authors identify such concepts as costs
, charges
and expenses
on the basis of a common base for the use of labor, material and financial resources.
S.S. Serzhuk believes that expenses reflect a decrease in means of payment or other property of the enterprise and are recorded in the accounting at the time of payment. O.E. Sytnik argues that the term charges
refers to the movement of funds in the course of economic activity, leading to a decrease in the organization's funds or an increase in its debt obligations.
The concept of charges
should be understood as a decrease in economic benefits as a result of the disposal of assets or the occurrence of liabilities, leading to a decrease in the capital of this organization.
According to S.S. Serzhuk, costs are the real or estimated costs of the enterprise's financial resources. It is no coincidence that the expressions material expenses
and labor expenses
are not accepted in practice - neither material resources nor labor belong to finance. Costs in the literal sense of the word represent the totality of transfers of funds and relate either to assets, if they are able to generate income in the future, or to liabilities, if this does not happen and the retained earnings of the enterprise for the reporting period decrease. The costs of missed opportunities act as a loss of income when choosing one of the methods of doing business [23]. Mironov M. G. defines costs as a monetary expression of the costs of production factors necessary for the enterprise to carry out its commercial and production activities "[16].
The concept of expenses
should be understood as a part of the costs determined for the corresponding year, which should be used during this period for the implementation of production and marketing activities. [20].
In the conditions of market relations, the success in the competitive struggle and the stable financial condition of the enterprise are largely due to the ability to ensure the level of costs not higher than the industry average (Fig. 1).
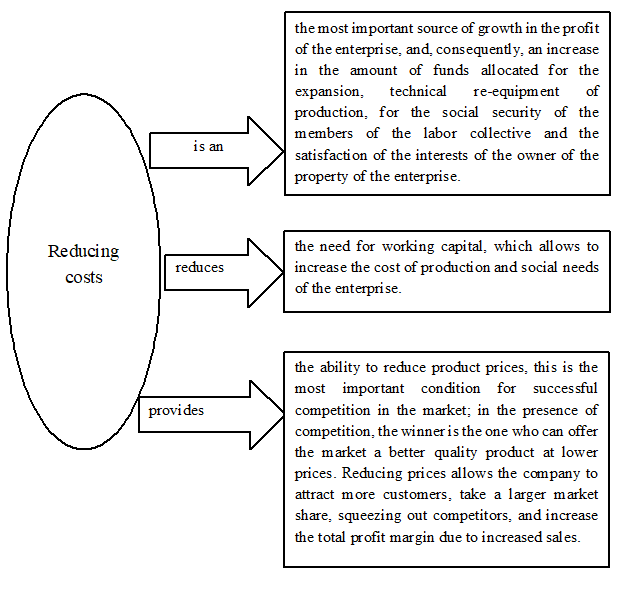
Figure 1 – Cost level value
In a business environment that is based on the principle of continuity and on an accrual basis, we cannot identify such concepts as costs
, charges
and expenses
, since their use assumes a long-term perspective of activity. The costs of the institution for operating activities, if it is probable that short-term or long-term benefits will be received, will be recognized as assets. We can use the term costs
only in the case of short-term activities, since they imply funds determined for the corresponding year and should be used during this period.
Thus, we can conclude that cost management makes it possible to determine the most capital-intensive elements in the overall cost structure, optimize the resources used and further rationing costs in the process of developing products and their manufacturing technology, as well as planning the costs necessary for justification of management decisions and determination of profit.
3.2 Classification of costs and types of costs
Any production activity always implies the presence of certain costs, their structure and size are important indicators of the functioning of the enterprise. Classification of costs allows you to identify costs according to the types of activities, simplify cost management, determine financial results of activities and calculate the cost of manufactured and sold products.
V.V. Sopko defines 10 areas of economic, legal and planning and accounting grouping of enterprise costs [18]:
- By economic elements (cost elements).
- By centers of origin - cost centers (enterprise, production, site, team, etc.).
- By types of products (products, works, services).
- Relative to the calendar period.
- By the way cost elements are included in the accounting object and the costing object.
- In relation to the cost of production.
- By cost items.
- By sphere of origin.
- By degree of plan coverage.
- By composition homogeneity.
According to V.F. Paliy it is necessary to classify the costs of the enterprise by: phases of circulation; relation to technology; influence on the cost price; the degree of generalization; the scope of planning and regulation; relation to the sale; integrity.
According to the methods of transferring value to products, costs can be divided into direct and indirect. Direct costs are costs that can be allocated directly to a specific cost object in an economically feasible way. Direct costs include costs associated with the production of a particular type of product that can be directly included in its cost (raw materials and supplies, purchased semi-finished products and components, other material costs, labor costs and other production costs).
Indirect costs are costs that cannot be directly attributed to a specific cost object in an economically feasible way.
It should be noted that the less methods of indirect distribution of costs are used between individual types of products (since this inevitably leads to distortions in the calculation of the cost of production), the more reliable and accurate the calculation of the cost of production is. If it is impossible to avoid indirect distribution methods, it is important to use those that allow the minimum redistribution and provide the greatest accuracy in calculating the cost of products [2].
Indirect costs include costs associated with the production of several types of products (general production), included in the production cost using special methods. Indirect costs form complex costing items (that is, they consist of costs that include several elements) that differ in their functional role in the production process.
According to the degree of influence of the volume of production on the level of expenses, costs are divided into variable and fixed. This type of classification is used to assess the utilization of production facilities and determine the amount of non-productive fixed costs and to determine the optimal production volumes and cost limits.
Variable costs include costs of raw materials and materials, purchased semi-finished products and components, process fuel and energy, wages to workers employed in the production of goods (works and services), net of social events, and other costs.
Constant are costs, the absolute value of which does not change significantly with an increase (decrease) in the volume of production. Fixed costs include the costs associated with the maintenance and management of the production activities of shops, as well as the costs of meeting the economic needs of production. The total variable costs are linear with respect to the volume of activity, and the variable costs per unit of output are constant for all levels of activity.
Depending on the percentage of changes in costs and changes in output, variable costs, in turn, are divided into proportional and disproportionate.
Proportional costs increase or decrease in proportion to the increase or decrease in production. Examples of proportional costs are direct costs, that is, costs of raw materials, basic materials, purchased semi-finished products, wages of production workers at piece rates, fuel and energy for technological purposes.
Disproportionate costs include progressive and depressive costs. Progressive costs have a higher growth rate than production volume. Such expenses, for example, include extra payments for after-hours, for work on holidays, payment of downtime. As a rule, they cause disturbances in the rhythm of production and are not typical for a normally functioning enterprise. Degressive costs are growing at a rate significantly lower than the volume of production (costs of maintenance, electricity, auxiliary materials for household needs, wages of auxiliary workers).
The total amount of fixed costs does not change with changes in the volume of activity, but the amount of fixed costs per unit of output decreases accordingly if the volume of activity increases and increases when it decreases.
Cost classification makes it possible:
- Determine the efficiency of production areas, processes.
- Predict the volume of production and the amount of costs based on the available production capacity.
- Timely intervene in the production process in the presence of significant deviations of actual data from the norm [6].
Production costs are divided by calendar periods into current, long-term and one-time. Current, or fixed, ordinary costs or costs in which the frequency is less than a month. Long-term - these are expenses associated with the implementation of a long-term agreement (contract), that is, a contract that is not planned to be completed earlier than nine months from the date of the first expenses or receipt of an advance (prepayment). One-time, that is, one-time costs, or costs that are carried out once (with a frequency of more than a month) and are directed to ensure the production process for a long time.
According to the expediency of spending, costs are divided into productive and unproductive. Productive - provided by technology and organization of production. Unproductive - not necessary, arising as a result of certain deficiencies in the organization of production, violation, technology, and the like.
According to the classification of costs by calculation items, the main items are the following [6]:
- Determine the efficiency of production areas, processes.
- Purchased semi-finished products and components.
- Fuel and energy for technological purposes.
- Recyclable waste.
- Basic salary of production workers.
- Additional wages for production workers.
- Contributions to social events.
- Expenses for the maintenance and operation of equipment (ESOE).
- Losses from marriage.
- General production costs (GPC).
- Related products.
The cost of production is the cost of production and sale, reflected in monetary terms. It consists of costs that are used in the production process of products, raw materials and materials, fuel, energy, fixed assets, labor resources and other costs for its production and sale.
Thus, the main task of cost classification is the formation of the cost of production. With the help of classification, costs are grouped by type and directly or indirectly related to the cost of production.
3.3 Features and need for cost management
The dynamism of the external environment, the consequences of transformational processes in the economy necessitate qualitatively new approaches to building the organizational structure of enterprise management. The effectiveness of the functioning of the strategic management of the enterprise is closely interconnected with the cost management process. An analysis of literary sources in the field of theory and practice made it possible to identify the problem of ambiguity in the interpretation of the term. The generalization of the definitions made it possible to conclude that none of them takes into account the strategic importance of cost management, but comes down to an accounting reflection of the company's existing expenses. The issue of cost management is brought to the fore because high-quality implementation of the cost management process directly affects the performance indicators of the enterprise.
Cost management is a component of the enterprise management system, which makes it possible to clearly track, analyze and control costs, covering almost all areas of financial and economic activities of the enterprise, to quickly receive information necessary to implement measures to improve production efficiency [14].
The purpose of cost management is to reduce or optimize the cost per unit of manufactured products, increase the profitability of business processes and the level of risk of business activities. Cost management is essential to improve the efficiency of the enterprise.
The enterprise cost management algorithm is shown in Figure 2.[2]
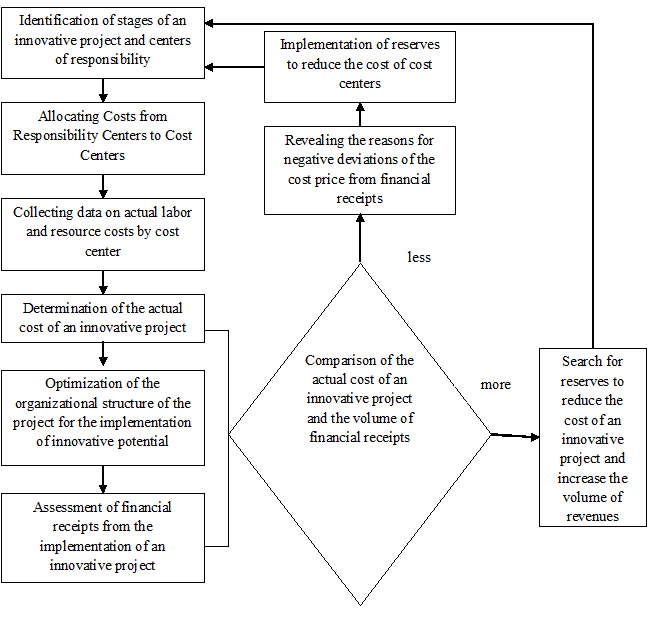
Figure 2 – Algorithm of cost management in the development of an innovative project
Cost management is a process of purposeful formation of costs by their types, place of origin and carriers, while constantly monitoring their level and stimulating a reduction.[2]
Developing a cost management policy has several aspects: functional, organizational, administrative and financial. Functional is a set of management functions used in the cost management process of a company. Organizational - consists in the differentiation of costs depending on the place of formation and the structure of their management bodies. The organizational aspect considers costs in terms of the internal needs of the company in planning, accounting and cost management in the context of economic activity. Financial - represents compliance with obligations to government organizations, banks, shareholders and other counterparties of the company.
The functional aspect includes [14]:
- Optimization of used resources and further regulation of costs in the process of product development and manufacturing technology, i.e. during the design and technological preparation of production.
- Cost planning required to justify management decisions and determine the expected results of work - profit.
- Cost accounting establishes their actual value after the planned work has been completed.
- Cost control and analysis required to clarify their rationality, the correspondence of actual costs to planned ones. The deviation is analyzed and measures are developed to maintain the economy.
- Promote rational use of resources. Development of projects, management decisions and other activities to rationalize resource consumption.
In the cost management system, it is important to determine their place of origin and organize controls for any type of costs incurred by the company. The cost of production of products (services) is the most important quality indicator, the management of which makes it possible to control all aspects of the company's business and analyze its results. The amount of costs depends on the quantity and quality of products, the use of working time, raw materials, materials, equipment, wage bill expenses, etc. Production costs are the basis for determining the prices of products, their reduction leads to an increase in profits and profitability. To achieve cost reduction, you need to know their composition, structure and dynamics.
The efficiency of a company's business depends, first of all, on the rational use of all types of resources, which requires a gradual transition to a unified cost management system. The introduction of such a system has the following advantages: ensuring the production of competitive products by reducing costs and prices; availability of reliable and high-quality information about the cost of certain types of products and their position on the market in comparison with products of other manufacturers, the possibility of using flexible prices; providing objective data for budgeting; the ability to assess the activities of each division of the enterprise from a financial point of view; making effective and well-grounded management decisions.
The level of costs determines the strategic position of the enterprise in the market, is the most important factor in the amount of profit and, therefore, the possibility of economic growth.
The cost management system is characterized by a balanced integrated approach, as a result of which the cost management system becomes closely linked to the strategic goals of the company, while various methods of cost management are used in the short and long term.
Thus, cost management is a system of measures that saves resources and maximizes the return on their use. The goal of cost management is to optimize costs (Figure 3).
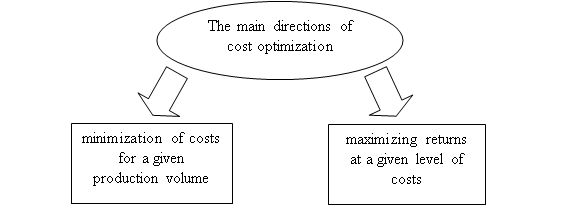
Figure 3 – The main directions of cost optimization
Generalization of the modern theory and practice of cost management at industrial enterprises made it possible to conclude that a modern cost management mechanism should include two relatively independent blocks - current and strategic cost management aimed at implementing tactical and strategic goals of industrial enterprises.
At the same time, current cost management is aimed at curbing cost growth, and strategic - at reducing costs throughout the production and consumption cycle.
The methodological component of the cost management mechanism should include modern methods of managing current and strategic costs that are adequate to the current state of the market economy.
Determination and regulation of costs in order to stabilize and reduce them
Determination of costs by stages of the economic life cycle of a product is an important and difficult task, the solution of which makes it possible to make a product economically competitive. The complexity of this task is due to the fact that the number of factors influencing the formation of costs is quite large. The main ones among them are the complexity of the product, the quality requirements, the nature of the production of the product, the requirements for the conditions of transportation, operation and disposal.
A wide variety of factors affecting the total costs leads to a variety of methods for calculating costs at different stages of the life cycle, as well as methods for determining individual elements of calculating costs.
The whole set of methods for calculating individual cost elements can be combined into four groups[4]:
- Heuristic methods. They are based on the use of expert opinion and include: the method of expert assessments (assigning weight characteristics, sequential comparisons, pairwise weighting), modeling method, preference method, prioritization method, scoring method.
- Mathematical and statistical methods. They are based on modeling one- and multi-factor dependencies between costs and technical (qualitative and quantitative) indicators based on actual statistical data on products and their constituent parts. The most widespread methods are correlation modeling, specific indicators, correcting coefficients, coefficient elements, estimates of detailed production costs, and reduced calculation.
- System methods. Their essence boils down to modeling the dependence of cost and technical and economic indicators on the basis of iterative approximation of the projected indicators to the normative and calculated ones established for standard or similar products (processes). As a rule, these are multivariate models that take into account the influence of factors that are not closely related to each other. This group includes methods of simulation modeling, dimensional factors, etc.
- Methods of technical regulation, calculation and analytical and calculation. They are based on the calculation of detailed (operational) norms and standards (standard ratios) for the consumption of raw materials and materials, purchased components, semi-finished products and other constituent material elements of products, norms and standards for labor intensity, energy consumption, and other types of costs.
Rationing of costs is carried out in accordance with the dimensional, weight and quality characteristics of the constituent elements and products in general. This takes into account the manufacturing technology of products, as well as the conditions of transportation, storage, operation and maintenance, disposal.
The norms and standards used for the most accurate calculation of resource costs are very diverse. These include [10]:
- Typical norms and standards for the production of various types of work.
- Enlarged norms and standards for parts and operations, typical technological processes.
- Mathematical relationships between weight, quality and dimensional parameters of a product and time spent.
- Separate transitions, techniques and movements of regulatory - calculation and planning - management works and procedures.
- Norms and standards of service and consumption.
- Standards of manageability.
- Comprehensive norms and standards for maintaining and ensuring the conditions for the normal course of the technological process, etc.
The scope of use of certain methods for calculating costs is limited by the degree of accuracy achieved with their help: if at the R&D stage methods of the 1st and 2nd groups are used, then at the production stage, where more stringent requirements are imposed on the accuracy of calculations and it depends on the type of production, methods of the 3rd and 4th groups are used.
There is a rule: the larger the volume of production and sales of products, the more carefully the costs of working time should be normalized and the more differentiated (by transitions, operations, parts, stages of the technological process, etc.) should be standards. Even small excess of the actual expenditure of working time against the normative ones causes a significant increase in the wages fund, an increase in prime cost and a decrease in the profitability of products. In mass, large-scale and serial production, the methods of technical labor regulation are used in the manufacture of products.[24]
The disadvantage that restrains the use of technical rationing of labor is the complexity and duration of the calculation of time rates. Therefore, in single and small-scale production, when fulfilling one-time orders, the technical rationing of labor is often inappropriate: while the rationing of work and adjusting the norms, taking into account the actual conditions of their implementation, the lead time may end. In single and small-scale production, as a rule, experimental statistical time norms are used. To speed up rationing and reduce its labor intensity, enlarged time norms are being developed - for individual parts, units and even for products. The accuracy of such standards is lower than technically justified, but they should also take into account as many specific factors and conditions for which they are calculated.
The accuracy of the experimental statistical time norms depends on the qualifications and experience of the developer. He must know well the technique, technology and organization of a particular production.
An indicator of the quality of the calculated time norms is their observance in practice. The establishment of overly tense norms of time leads not so much to an increase in labor intensity as to violations of technology and defects in the manufacture of products, staff turnover and other negative phenomena. On the other hand, relaxed norms are the reason for a decrease in labor discipline, ineffective use of working time and reserves for reducing production costs. In any case, compliance with established working hours should be constantly monitored and analyzed.
The need for better labor rationing increases when the share of labor costs in the cost estimate for economic elements is significant, especially if it exceeds 50%. This may occur during repair work, provision of services, in the service sector, etc.
At the implementation stage, where the calculation of costs is carried out in aggregate, for a batch of products (agreed delivery quantity), methods of the 2nd and 3rd groups are used.
During operation, the calculation of costs is complicated by the large uncertainty of indicators of reliability, maintainability, and preservation. It is difficult to calculate direct operating costs, which are calculated, as a rule, consolidated using the methods of the 4th group. Normative and reference materials on the norms of energy consumption per unit of time are widely used, as well as consolidated standards for the costs of performing work and rendering services to maintain and restore the operational characteristics of products, and standards for repairs.
Thus, the calculation and rationing at all stages of the product life cycle are necessary for cost management, their stabilization and systematic reduction. In the absence of calculation and rationing, costs are spontaneous, not manageable and tend to grow, which reduces the competitiveness of products. The regulatory framework is used in forecasting and planning costs, organizing and regulating the production process, wages and labor incentives, accounting and cost analysis. Constant comparison of actual costs with normative ones allows to reveal the reserves of their reduction.
Conclusions
The activity of any enterprise consists in the production of various products and their sale to end consumers. It is impossible to accomplish such a task without costs, since they are one of the main performance indicators. Their structure and size are important indicators of the functioning of the enterprise.
The efficiency of the enterprise depends on the rational use of all types of resources, which necessitates the transition to a unified cost management system. The main task of cost management is to achieve sustainable growth in production and profits based on comparing development goals with the available opportunities for this.
Cost management of an enterprise involves the performance of all functions inherent in the management of each object, i.e. development, adoption, implementation of decisions, their analysis and control over their implementation. Cost management functions are implemented through the elements of the management cycle: planning, forecasting and rationing, organization, regulation and incentives, accounting, calculation and analysis. Individual elements that are directly related to each other can be grouped and, thus, three subsystems of cost management can be distinguished: development and decision making, decision implementation, cost accounting and control.
In addition to the fact that the company must produce products and ensure their sales, it also aims to minimize the consumption of material resources. For this, it is necessary to determine the reserves for reducing costs. The most common are: a decrease in specialization and cooperation, an increase in labor productivity, an increase in output, compliance with the strictest economy at all stages of production, as well as in the field of administrative activities of the enterprise. The main condition for reducing the cost of raw materials and materials for the production of a unit of production is the improvement of the design of products and the improvement of production technology, the use of modernized equipment and the introduction of rationing the costs of material resources. It is also necessary to take measures to preserve the existing sales markets and conquer new ones.
When writing this essay, the master's work has not yet been completed. Final completion: June 2021. The full text of the work and materials on the topic can be obtained from the author or his manager after that date.
References
- Адамчук, В.В. Эргономика: учеб. пособие для вузов / В.В. Адамчук, Т.П. Варна, В.В. Воротникова [и др.]. - М.: Юнити-ДАНА, 2009. - 254 с.
- Артемова, М.М. Особенности планирования управления затратами в современных условиях / М.М. Артемова // Социально-экономические проблемы трансформационной экономики. Сборник материалов. – Тюмень, 2014. – Выпуск 2. – с.27 – 30.
- Белов, С. В. Охрана труда при производстве и эксплуатации подъемно-транспортных машин / С. В. Белов, А. Ф. Козьяков. — М. : Машиностроение, 2016. — 208 с.
- Бланк, И. А. Управление финансовыми ресурсами / И. А. Бланк М.: Издательство
Омега-Л
; ОООЭльга
, 2014. – 768 с. - Бутинец, Ф.Ф. Бухгалтерский финансовый учет Учебник под ред. Проф. Ф.Ф. Бутинца. — Житомир: ЖТИ, 2000 – с.429-431.
- Волков, О.И. Экономика предприятия: курс лекций. / О.И. Волков, В.К. Скляренко – М.: ИНФРА – М, 2014 – с. 340 – 348.
- Дементий, Л. В. Охрана труда в автоматизированном производстве. Обеспечение безопасности труда / Л. В. Дементий, А. Л. Юсина. — Краматорск: ДГМА, 2007. - 300 с. - ISBN 978-966-379-163-0.
- Дерий, В.П. Термин
затраты
и его трактовка для потребностей учета и контроля / В.П. Дерий // Галиц. экон. вестн. – 2013 – №1(26). – С.154 – 160. - Дружиловская, Т.Ю. Характеристика
расходов
изатрат
для бухгалтерского финансового учета // Международный бухгалтерский учет. – 2015. – №2 (344). – С. 31 – 45. - Дьяченко, О.Г. Понятийный аппарат
затраты
,издержки
,расходы
/ О.Г. Дьяченко, Т.А. Бородина // Вестник КрасГАУ. – 2013 – №11. – С.16 – 23. - Золотухина, А.Д. Методы учета затрат и калькулирования себестоимости продукции (работ, услуг) // Аудит и финансовый анализ, 2017, № 2. С. 1–9.
- Исхаков, А.Т. Практическое применение системы целевой себестоимости (
таргет-костинг
) икайзен-костинг
в сельском хозяйстве // Вестник № 1 Казанского государственного финансово-экономического института, 2009 – С. 48 – 51. - Костюковой, Е. И. Бухгалтерский управленческий учет / под ред. Е. И. Костюковой. – М.:КНОРУС, 2014.
- Кузьмин, О.Э. Управленние затратами на предприятиях : уч. пособие / О.Є. Кузьмин, О.Г. Мельник, У.И. Когут. – Львов: Издательство Львовской политехники, 2014. – С. 242 – 245.
- Милосердова, Н. Д.
Стандарт-кост
идирект-костинг
: преимущества и недостатки / Н. Д. Милосердова ; науч. рук. А. Л. Спесивцева // Экономика России в XXI веке: сборник научных трудов XI Международной научно-практической конференцииЭкономические науки и прикладные исследования: фундаментальные проблемы модернизации экономики России
, посвященной 110-летию экономического образования в Томском политехническом университете, г. Томск, 18-22 ноября 2014 г. : в 2 т. — Томск : Изд-во ТПУ, 2014. — Т. 2. — С. 87-90. - Миронов, М. Г. Экономика отрасли (машиностроение): учебник / М. Г. Миронов, С. В. Загородников. – М.: ФОРУМ: ИНФРА-М, 2015 – 320 с.
- Навакатикян, А. О. Охрана труда пользователей компьютерных видео-дисплейных терминалов / А. О. Навакатикян, В. В. Кальниш, С. Н. Стрюков. — К. : Охрана труда, 2007. — 400 с.
- Нападовська, Л.В. Управленческий учет: Монография. – Днепропетровск: Наука и обучение, 2010 – 450 с.
- Одноколов, С.М., Платов О.К. Затраты предприятия: теория, система управления, оптимизация. – Ярославль: Канцлер, 2017, 202 с.
- Пинчук, М.Е., Крапивницкая, С.Н. Особенности управления затратами на современном предприятии / Материалы научно-практической конференции
Ресурсосбережение. Эффективность. Развитие
. – Донецк: ДонНТУ, 2017. – С. 91 – 93. - Пинчук, М.Е., Крапивницкая, С.Н. Выбор метода калькулирования затрат в зависимости от фазы жизненного цикла товара / Материалы научно-практической конференции
Ресурсосбережение. Эффективность. Развитие
. – Донецк: ДонНТУ, 2018. - Просвирина, И.И., Проскурина, В.В. Кайзен-костинг как система управления затратами на современном предприятии // Научно-аналитический экономический журнал. 2016. № 5. С. 4 – 14.
- Сержук, С.С. Сравнительный анализ теоретических трактовок определения понятия затрат предприятия // Вестник Удмуртского университета. 2011 Вып.3. С.58 – 61.
- Сытник, О.Е., Леднева, Ю.А. Экономическая сущность категории
затраты
,расходы
,издержки
и их отраслевые особенности // Вестник Северо-Кавказского государственного технического университета. – 2015 – №4 – С.241–245. - Чая, В.Т., Золотухина, А.Д. Система методов управленческого учета // Аудит и финансовый анализ, 2013. – № 1.
- Шалаева, Л.В. Современные системы управления затратами как важнейший инструментарий стратегического управленческого учета // Международный бухгалтерский учет. 2012. № 21 (219). С. 7 – 21.