Некоторые особенности алмазного торцового шлифования металлов
К.т.н. Иванова Т.Н., Долганов А.М., Люпа Д.С.
http://www.rusnauka.com/Article/Tehnica/6-9/26.html
ГОУ ВПО ИжГТУ, ОАО «Удмуртторф», бюро ДОАО «Ижевский инструментальный завод», г. Ижевск, Россия
Технологически торцовое шлифование представляет собой операцию окончательной обработки поверхностей деталей шлифовальными кругами. Задачи шлифования как метода механической обработки сводятся к повышению производительности при одновременном улучшении качества металла поверхностного слоя. Это достигается в процессе высокоскоростного микрорезания мельчайшими режущими кромками зерен абразивных материалов, закрепленных на рабочей поверхности круга.
Одной из особенностей процесса торцового шлифования является непрерывность работыабразивных зерен круга, т.е. каждое зерно все время работает в металле. Тогда как при всех остальных видах шлифования за один оборот круга зерно может нанести царапину один раз, так как оно только один раз заходит в контакт с деталью, причем несоизмеримо большую часть пути находится вне работы (в воздухе).
Шлифовальный круг в процессе обработки выполняет работу беспорядочно расположенными абразивными зернами неправильной геометрической формы. Все это приводит к тому, что резание ведется не сплошной кромкой, а отдельными режущими зернами, наиболее выступающими над связкой. В результате этого при шлифовании образуется большое количество мельчайших стружек, размеры которых изменяются от десятых долей микрометра до десятых долей миллиметра. Расположение вершин абразивных зерен, их форма влияют на размеры и форму стружек. Обычно в резании участвуют не более 20% режущих зерен, расположенных на рабочей поверхности круга. Обрабатываемая поверхность формируется не всеми участвующими в работе абразивными зернами. Чтобы отделить припуск от основной массы заготовки, абразивные зерна проходят в металле определенный путь, обеспечиваемый относительным движением инструмента и заготовки. Из числа контактирующих кромок абразивных зерен стружку снимают только те, которые имеют более благоприятную форму вершин и достаточную глубину внедрения в металл. Наличие в большинстве случаев у режущих абразивных зерен отрицательных передних углов резания приводит к длительному скольжению режущей кромки по дуге контакта и пластической деформации металла. Остальные контактирующие кромки абразивных зерен выполняют работу трения и упругопластической деформации без снятия стружки. Критерием перехода от пластической деформации к началу отделения стружки является предельное значение отношения глубины резания (толщины среза) аz к радиусу округления вершины режущей кромки ? (аz/?), которое изменяется в пределах 0,01-1,0. Анализ процесса резания единичным абразивным зерном и его геометрических соотношений в зоне стружкообразования показывает: при шлифовании стружка образуется всегда, если отношение аz/ ?>1; при аz/?<0,5 происходит упругопластическое оттеснение металла в зоне резания; при 0,5<аz/?<1,0 процесс образования стружки не стабилен, и шлифование протекает при больших затратах энергии на преодоление упругопластических деформаций и трения.
Таким образом, микрорезание отдельно взятым на рабочей поверхности круга абразивным зерном представляет собой сочетание внедрения и царапания. Скорость резания состоит из скорости внедрения (врезания) и скорости перемещения (царапания). Способность металла сопротивляться внедрению абразивного зерна характеризуется его твердостью, а сопротивление металла царапанию и срезу определяется его прочностью на сдвиг. В процессе шлифования возникают силы резания, необходимые для преодоления сопротивления металла внедрению зерна и его перемещению относительно обрабатываемой поверхности заготовки [1].
С увеличением ширины шлифуемой поверхности увеличивается как число одновременно работающих зерен, так и путь перемещения по обрабатываемой поверхности. Увеличение числа одновременно работающих зерен и динамическое воздействие каждого зерна на обрабатываемый поверхностный слой способствует возрастанию источников теплообразования, и, как следствие, повышению температуры обрабатываемой поверхности, а увеличение пути зерна в контакте с обрабатываемым металлом приводит к увеличению температуры и накоплению тепла в зерне и, соответственно, повышению износа. Высокие мгновенные температуры, развивающиеся в процессе шлифования, с одной стороны, повышают пластичность деформируемого металла и улучшают условия образования стружки абразивными зернами круга, а с другой – из-за обильного теплообразования вызывают структурные изменения металла в поверхностном слое и способствует появлению напряжений растяжения в этих слоях металла [2].
Абразивные зерна при шлифовании испытывают периодическое силовое, тепловое и химическое воздействие в момент контакта с обрабатываемой поверхностью заготовки. В результате такого воздействия возникает износ абразивных зерен, потеря их режущей способности. Поэтому основными требованиями к абразивному инструменту являются высокая твердость и теплостойкость материала абразивных зерен, обеспечивающие их работу без чрезмерного изнашивания; их хрупкость и регулируемая сила закрепления зерен связкой, способствующие требуемому операцией шлифования самозатачиванию (обновлению) рабочей поверхности круга.
Установлено [3], что торцовое шлифование алмазными зернами обеспечивает режим самозатачивания шлифовального круга, позволяет стабилизировать скорость съёма металла, обеспечить стабильные шероховатость поверхности и толщину снимаемого слоя металла за рабочий ход. Необходимость правки в процессе шлифования отпадает. Для того чтобы вызвать самозатачивание шлифовального круга необходимо при заданных режимах резания снизить силы связи между алмазным зерном и связкой, путём применения более мягкого круга или изменить режим резания так, чтобы увеличить силы резания. Это достигается увеличением продольной подачи, глубины и ширины шлифования, а также снижением скорости круга. Поэтому, эффективность алмазного торцового инструмента в значительной степени зависит от правильного выбора режимов резания.
Для сопоставления поведения круга в разных условиях, для оценки его режущей способности, а так же для разработки рекомендаций по повышению производительности торцового шлифования целесообразно в качестве условия обеспечения нормального процесса резания принять выражение Qпод = Qсрез, т.е. производительность процесса шлифования выражаемая объемом обрабатываемой поверхности в единицу времени (Qпод ) зависит от того, какой способностью обладает алмазный круг снимать режущими зернами определенное количество металла (Qсрез ).
Если Qпод<Qсрез работоспособность алмазных зерен будет использоваться не полностью и производительность шлифования снизится. Если Qпод>Qсрез будет наблюдаться или интенсивный износ или засаливание рабочей поверхности.
Поскольку процесс торцового шлифования есть процесс снятия с обрабатываемой поверхности мельчайших стружек алмазными зернами, установление закономерностей между параметрами обработки и толщиной срезаемого слоя является очень важным. Учитывая, что различные алмазные зерна в реальных условиях шлифования за время контакта с обрабатываемой поверхностью снимают различные по величине стружки, то средняя величина ожидаемой толщины среза при торцовом шлифовании выразится зависимостью:
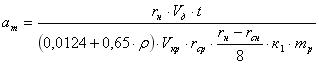
Проведенные расчеты и экспериментальные исследования показали, что при равных условиях глубина внедрения алмазного зерна в металл, а, следовательно, и величина среза при торцовом шлифовании меньше, чем при обычном шлифовании и имеется путь интенсификации процесса за счет увеличения подвода в зону резания объема снимаемого материала. Наибольшее влияние оказывает скорость обрабатываемой детали ?д, т.к. в совокупности с глубиной резания она предопределяет объем подводимого материала в зону обработки.
Полученная расчетная зависимость устанавливает степень влияния зернистости, концентрации и разновысотности алмазных зерен, геометрических параметров обрабатываемой детали и шлифовального круга на режимы обработки и толщину срезаемого слоя, снимаемого одним зерном, и через них на процесс шлифования в целом. Изменение характеристик круга и режимов обработки приводит к различной режущей способности инструмента.
Таким образом, проведенные исследования показали, что при алмазном торцовом шлифовании существует немало резервов повышения производительности, точности и качества обработки.<
Литература
1. Люпа Д.С., ИвановаТ.Н. Технологические возможности процесса торцового планетарного шлифования. / Информационные технологии в инновационных проектах: Тр. IV междунар. науч.-техн. конф. (Ижевск, 29-30 мая 2003 г.).- Ч. 3 – Изд-во ИжГТУ, 2003. С. 57-59.
2. Иванова Т.Н. Исследование остаточных напряжений, возникающих при шлифовании. Сб. ст. IX межд. науч.-техн. конф. «Современные тенденции развития транспортного машиностроения и материалов» 24-27 мая 2004г. – Пенза: Пензенский гос. ун-т, Приволжский дом знаний, 2004. С. 66-69.
3. Свитковский Ф.Ю., Иванова Т.Н. Исследование закономерностей и повышения эффективности процесса шлифования деталей из труднообрабатываемых материалов. / ж. Обработка металлов. № 1(22), 2004. Стр. 22-24.
|
|