Actuality of theme
With development of science and technique new tasks are put before modern mechanical engineering. One of them provides technical characteristics of constructions working in wide temperature range at complex combination of variable power and thermal influences in aggressive environments. The conditions of environment do not often allow to use metals efficiently. Different types of ceramics, including glass ceramics or сetalls are these materials. Cetalls posses certain operating characteristics such as hardness, high compression strength at a low specific density, heat-resistance, resistance (resistibility) to power tension and external hydrostatical pressure. These properties make fragile non-metal constructions most suitable for their application in the conditions of aggressive environments of ocean and space, in aircraft and rocket industry. Specific character of using there wares predetermines exactness and strength while making them which is determined by the roughness of the treated surface and minimization of superficial layer defects.

|
Review of existent researches
The technological ware treatment process includes multioperational treatment by polishing on machine-tools of the RT 66202 type, equipped by an aggregate polishing head and the system of the direct copying. Dynamic characteristics of the system MAID while polishing an outward detail surface are explored in this work. The chart is presented on the fig. 1.

Fig. 1 – Chart of an outward product machining
The features of ware treatment of the considered class from сetalls are largely conditioned by the following factors. Basic sizes of a good: length to 1,0 is m; maximal diameter 450...500 mm; thickness of wall of purveyance 20 mm at the thickness of the finished product 5 mm. Treatment of internal contour of good takes 18-20 hours of machine time; treatment of an outward contour takes 6-10 hours at the considerable stake of maximal labour applied in the operation of clean treatment of an outward type. Operating characteristics of wares need to keep accuracy and quality requirements of treatment, providing minimum defect depth in the superficial layer which determines subsequent operational duration of chemical etching and strengthening of mechanically treated surfaces [4].
Dynamic characteristics of gear-box of a machine-tool were determined to see autovibration reasons. They were computed to define rotation frequency of a spindle nд=80 rot/min. The computation method assumes step-by-step transformation of elements in a gear-box into a chart, which is presented on fig. 2. I1 и Iэ - equivalent inertia moments of a engine rotor and inertia moments of details in a gear-box; e э - turning equivalent pliability of elements in a gear-box.
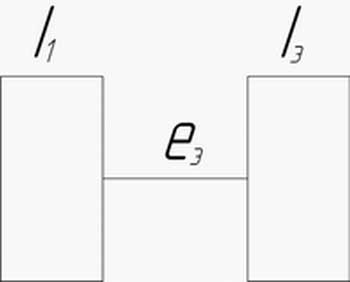
Fig. 2. Chart of a dynamic system of a gear rotation drive.
Equivalent inertia moment of a gear-box is calculated by a formula:

where I'i - is inertia moment of elements in a gear-box: gear-wheels, billows, pulleys of a strap transmission, adaptation.
Turning equivalent pliability can be calculated from [5]
eэ=1/Iэ(e'iI'i+(e'i)+...+enI'n)
where e'i - element pliability of a gear-box: electric motor, billows, strap transmission and spline connections etc.
Frequency of turning vibrations of a gear-box drive in tool-spline is determined. To define high frequency the formula is used:
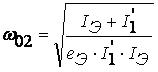
Computations show that . Thus turning frequency .
Lower frequency of turning vibrations is compared with indignation frequency (t.e. with frequency of rotation of purveyance).
For the accepted terms indignation frequency is determined from
fвоз=(nd/60)kф
where nd – rotation frequency of a detail (purveyances), nd = 80 rot/min;
kф - is purveyance form factor.
For real terms (purveyance material is сetalls, description of form, type, size of a purveyance, in combination with technological conditions) the section of a purveyance tends to the ellipse form. kф is accepted to be 2. Then revolting vibration frequency will be fвоз = 2,6 Hz.
The system is considered steady [5], if fвоз is found in ranges:
0,7fрас > fвоз; или fвоз > 1,3 fрас.
In this case the condition is executed fвоз > 1.3 f рас that is 2,6 > 1,625. Thus we consider that there are no turning vibrations in the subsystem «engine – gear-box – detail».
The possibility of bent vibrations in the resilient system MAID is shown in fig.3.
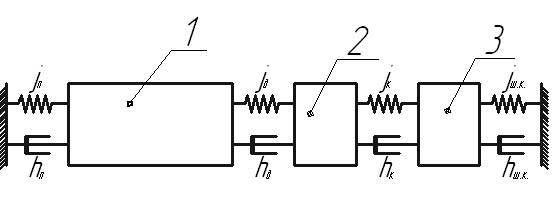
Fig. 3. Dynamic grinding model. 1 – spindle knot with adaptation; 2 – work-pieces; 3 – aggregate head with a grinding circle
Dynamic characteristics computation of a spindle of machine-tool is carried out by a special program in Mach CAD 2001 package. The method of initial parameters in accordance with the method described in [6] is used. Fig. 4 is a chart of a spindle knot with adaptation. Dynamic characteristics computation of a spindle is carried out taking into account adaptation necessary for setting of detail.
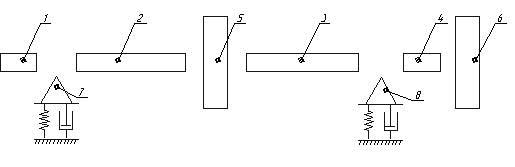
Fig. 4 - Chart of a spindle knot with adaptation
1, 2, 3, 4 – spindle knot areas; 5 – gear-wheel for spindle rotation; 6 – adaptation; 7, 8 – bearing supports.
The presented program allows to produce spindle frequency description (PFD) taking into account processes of cutting and drive influences. Fig. 5 shows PFD of a spindle knot when cutting.
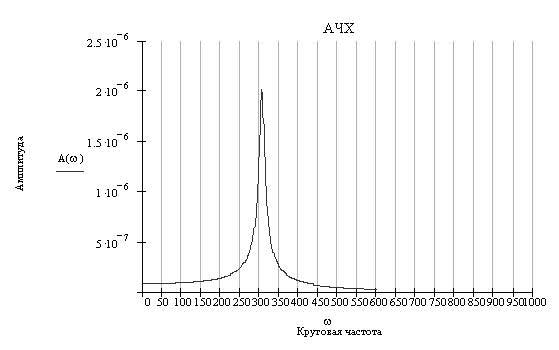
Fig. 5. PFD of a spindle knot when cutting
Low frequency of bend vibrations of a subsystem «spindle knot – adaptation – work-pieces» fс.ш. is 314 rad/sec or 50 Hz.
Further research will be carried out with two program packages: Solid Works, ANSYS.

|
References
1 Гусев В.В., Калафатова Л.П. Обеспечение эксплуатационных характеристик изделий из конструкционной керамики на стадии их производства // Сучасні технології у машинобудуванні: Збірник наукових статей / За заг. ред. А.І. Грабченка. – Том 2. – Харків: НТУ «ХПІ», 2006. – С. 334-346.
2 Гусєв В.В., Калафатова Л.П. Вплив стану робочої поверхні алмазного інструмента на процес шліфування крихких неметалевих матеріалів // Вісник Житомирського державного технічного університету.–№2 (26).– 2003.– С.49-54.
3 Гусев В.В. Силы резания и формирование дефектного слоя при алмазном шлифовании керамики // Надійність інструменту та оптимізація технологічних систем. Збірник наукових праць. – Краматорськ: ДДМА. – 2003.- Вип. №13. – С. 70-76
4 Калафатова Л.П. Прогнозирование качества поверхностного слоя при обработке изделий из технических ситаллов // Приложение №9 к журналу «Инженерный журнал. Справочник » Инженерия поверхности. – М.: Машиностроение. – 2002. – №9. – С.5-8.
5 Расчеты на прочность деталей машин: Справочник / Сост.: И.А. Биргер, Б.Ф. Шорр, Г.Б. Иосилевич. – М.: Машиностроение, 1979. – 702с.
6 Металлорежущие станки: Учебник для машиностроительных втузов/Под ред. В.Є. Пуша. – М.: Машиностроение, 1985. – 256 с.

|