Т Е Х Н О Л О Г І Я
М А Ш И Н О Б У Д У В А Н Н Я |
Васьковський Антон Миколайович
Тема выпускної роботи:
Вдосконалення структурного і технологічного забезпечення процесів виготовлення лопаток компресора газотурбінного двигуна в умовах Снежнянського машинобудівного заводу
Автореферат по темі випускної роботи
Зміст
Вступ
Актуальність теми
Мета і завдання роботи
Наукова новизна роботи
Основна частина
Компресорні лопатки газотурбінного двигуна
Формування поверхневого шару на фінішних операціях виготовлення лопаток
Віброабразивна обробка лопаток
Висновоки
Література
Вступ
Актуальність теми
Ресурс і надійність авіаційних двигунів в основному визначаються несучей здатністю лопаток компресора (рис. 1), що є найбільш відповідальними і високонавантаженими деталями, що випробовують в процесі експлуатації значні знакозмінні і циклічні навантаження, які впливають на них з великими частотами. Лопатки компресора наймасовіша, високонавантажена і відповідальна деталь авіаційного двигуна.
Особливістю лопаток компресора, що мають тонкі вхідні та вихідні кромки і виготовлених з титанових сплавів, досить чутливих до концентрації напружень, є те, що вони першіми зустрічаються з чужорідним тілом (птиця, град та ін.), яке потрапило в тракт двигуна.
Риски, забоїни, ерозійні пошкодження та ін. дефекти значно збільшують рівень локальних вібронапруг, що різко знижує прочностни характеристики лопаток. Тому створення сприятливого поєднання властивостей поверхневого шару на фінішних отделочно-зміцнюючих операціях робить великий вплив на підвищення несучої здатності лопаток ГТД. Актуальним завданням є оцінка впливу поверхневого деформаційного зміцнення на ударну міцність лопаток при зіткненні з сторонніми предметами.
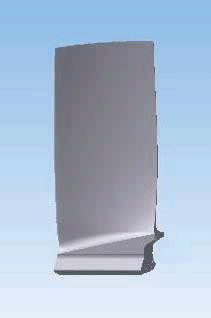
Рисунок 1 - Модель лопатки компресора ГТД (10 кадрів, 20 циклів)
В даний час при виготовленні лопаток компресора широке застосування отримали методи пластичної деформації та механічної обробки, а також комплексні технології на фінішних операціях технологічного процесу.
Віброабразивна обробка (ВО) на спеціальних установках знайшла широке застосування у виробництві лопаток компресора з титанових сплавів. Позитивний вплив на ефективність віброабразивної обробки надає вживання разом з абразивом хімічно активних рідин.
Ультразвукова обробка кульками (УЗО) дозволяє формувати сприятливе поєднання характеристик поверхневого шару лопаток компресора, що мають малу жорсткість, високу точність виготовлення, складну конфігурацію і тонкі кромки.
Пневмодробеструйна обробка (ПДО) характерна ковзаючим зіткненням кульок з поверхнею пера лопатки, не допускаючи їх перенаклепа. Встановлено, що ПДО супроводжується зменшенням структурної неоднорідності і додає структурі, розподілу фаз і залишковим стискуючим напругам більш однорідний характер в поверхневому шарі пера лопатки. Пропонований пневмодробеструйний метод отделочно-зміцнюючої обробки ефективно нейтралізує технологічні мікродефекти поверхневого шару, утворені на попередніх стадіях технологічного процесу, супроводжується значним збільшенням межі витривалості, зниженням розсіяння довговічності і не вимагає подальшої доробки тонких кромок ручним поліруванням [6].
Одним з перспективних методів отделочно-зміцнюючої обробки є метод магнітно-абразивного полірування (МАП). Відмінна риса МАП полягає в можливості обробляти деталі з різною конфігурацією і поєднувати в одному процесі обробні і зміцнюючі операції.
Проблема ерозії лопаток газотурбінних двигунів є загальновизнаною. Інтенсивність і вигляд ерозії лопаток компресора залежать не лише від умов зіткнення часток з поверхнею пера, але і від поєднання характеристик поверхневого шару.
Для підвищення зносостійкості лопаток усе більш широке вживання отримали різні види комплексних технологій — нанесення плазмових покриттів у поєднанні з різними отделочно-зміцнюючимі методами.
Розробка і впровадження в серійне виробництво двигунів на даний час супроводжується прогресивними конструкторсько-технологічними рішеннями, що виражаються в появі нових деталей, вживанням принципово нових конструкційних матеріалів, а також удосконаленням технологій виробництва, збірки та випробування. Широко використовуються прогресивні технологічні процеси механічної обробки, засновані на концепції високошвидкісного різання, удосконалюються методи отделочно-зміцнюючої і термічної обробки.
Тісний взаємозв'язок між конструкцією і технологією виробництва двигунів зумовив ряд актуальних на сьогоднішній день питань, пов'язаних з підвищенням несучої здатності сложнопрофільних деталей технологічними методами.
зміст
Мета і завдання роботи
Мета роботи — підвищення довговічності і якості лопаток компресора ГТД за рахунок вдосконалення структурного і технологічного забезпечення процесів виготовлення лопаток компресора ГТД.
Основні завдання роботи:
1.) Провести аналіз сучасного стану структурного і технологічного забезпечення процесів виготовлення лопаток компресора ГТД;
2.) Дослідити можливості підвищення довговічності лопаток компресора шляхом нанесення іонно-плазмових покриттів;
3.) Виконати експерименти по дослідженню властивостей зносостійкого іонно-плазмового покриття;
4.) Розробка рекомендацій щодо вдосконалення структурного й технологічного забезпечення процесів виготовлення лопаток компресора ГТД.
зміст
Наукова новизна роботи
Наукова новизна роботи полягає в розробці рекомендацій щодо вдосконалення структурного й технологічного забезпечення процесів виготовлення лопаток компресора ГТД та створення оптимальної структури технологічного процесу обробки лопаток компресора ГТД. Також ця робота передбачає вирішення проблеми довговічності і зносостійкості лопаток компресора ГТД.
зміст
Основна частина
Компресорні лопатки газотурбінного двигуна
Лопатки ГТД працюють в умовах високих температур, що досягають для турбіни понад 1200°С, для компресора понад 600°С. Багаторазова зміна теплових режимів роботи двигуна - швидкий нагрів у момент запуску і швидке охолоджування при зупинці двигуна - викликає циклічну зміну термічних напружень, що характеризується як теплова втома (рис. 2). Крім цього, профільна частина пера і хвостовик лопатки, окрім розтягування і вигину від відцентрових сил, вигину і обертального моменту від швидкісного газового потоку, зазнають знакозмінні напруги від вібраційних навантажень, амплітуда і частота яких змінюються в широких межах.
Рисунок 2 - Схема руху газових потоків в ГТД (3 кадра)
Надійність роботи робочих лопаток компресора і турбіни залежить не лише від їх конструктивної міцності, опору циклічним і тривалим статичним навантаженням, але і від технології їх виготовлення, яка безпосередньо впливає на якість поверхневого шару хвостовика і пера лопаток. У поверхневому шарі утворюються конструктивні і технологічні концентратори напруги, він випробовує вплив наклепа і внутрішніх залишкових залишкових напружень від механічної обробки. Крім того, поверхневий шар піддається дії зовнішніх навантажень при основних видах напруженого стану (вигині, розтягуванні, крученні) зовнішнього середовища. Ці негативні фактори можуть призвести до руйнування лопатки, і, отже, до виходу з ладу газотурбінного двигуна.
Виробництво лопаток ГТД займає особливе місце в авіадвигунобудівництве, що обумовлено рядом факторів, головними з яких є:
• складна геометрична форма пера і хвостовика лопаток;
• висока точність виготовлення;
• застосування дорогих матеріалів, таких, як леговані стали та титанові сплави;
• масовість виробництва лопаток;
• оснащеність технологічного процесу дорогим спеціалізованим обладнанням;
• висока трудоємність виготовлення.
Для виробництва лопаток ГТД на сьогоднішній день характерні наступні види механічної обробки:
• протягування;
• фрезерування;
• вальцювання;
• полірування;
• віброполірування або віброшліфування;
• термообробка [11].
зміст
Формування поверхневого шару на фінішних операціях виготовлення лопаток
При виготовленні лопаток ГТД на їх поверхнях утворюються мікронерівності, риски, а в поверхневому шарі відбуваються структурні та фазові перетворення. Крім того, в поверхневому шарі спостерігається підвищення твердості металу і формування залишкових напружень.
В умовах експлуатації поверхневий шар сприймає найбільші навантаження і піддається фізико-хімічному впливу: механічному, тепловому, корозійному та ін.
У більшості випадків у лопаток ГТД починають погіршуватися службові властивості поверхні із-за зносу, ерозії, корозії, зародження втомних тріщин, що може призвести до відмови.
Після фінішної обробки розрізняють такі дефекти поверхні: риски, подряпини, задіри, вм'ятини, пори, тріщини, задирки та ін.
Фізіко-механічні властивості поверхневого шару, створені при виготовленні лопаток, під час експлуатації істотно змінюються під дією силових, температурних та інших факторів.
Поверхня деталі в порівнянні з серцевиною має ряд особливостей. Атоми, які знаходяться на поверхні, мають односторонні зв'язки з металом, тому знаходяться в нестійкому стані і володіють надлишковою енергією в порівнянні з атомами, що знаходяться усередині.
В результаті дифузії, особливо при дії підвищених температур, в поверхневому шарі виникають хімічні сполуки основного металу з проникаючими ззовні речовинами. При підвищених температурах посилюється дифузійна рухливість атомів, що приводить до перерозподілу концентрації легуючих елементів. Дифузія в поверхневому шарі робить помітний вплив на властивості металів. Це особливо характерно для такої операції, як шліфування, коли в зоні обробки спостерігається висока температура.
Основними причинами виникнення макронапруг при механічній обробці є неоднорідність пластичної деформації і локальний нагрів металу поверхневого шару, а також фазові перетворення.
Ступінь і глибина наклепа поверхневого шару деталей обумовлені режимами механічної обробки і безпосередньо пов'язані із збільшенням кількості дислокацій, вакансій та ін. дефектів кристалічної решітки металу.
Поверхневий шар деталей ГТД формується в результаті взаємопов'язаних явищ, що відбуваються у вогнищі деформації і прилеглих до нього зонах: багаторазових пружно-пластичних деформацій, зміни пластичних властивостей металу, тертя, зміни мікро і макроструктури та ін.
При зміцненні в результаті деформації поверхневого металу і роботи тертя виділяється теплота, яка нагріває деталь. При інтенсивних режимах обробки локальні ділянки поверхневих шарів нагріваються, при вигладжуванні — до 600—700 °С, при ударних методах — до 800—1000 °С [1].
Такий нагрів призводить до зниження рівня залишкових стискаючих напружень у поверхні, що може призвести до зменшення ефекту зміцнення. У деяких випадках відбувається перетворення стискаючих напружень в розтягуючих.
Основною причиною зміцнення є підвищення щільності дислокацій, що скупчуються поблизу ліній зрушень , і подальша їх зупинка перед різного роду перешкодами, що утворюються в процесі деформації або існували до нього. Дроблення на блоки об'ємів металу, укладених між площинами ковзання, поворот цих блоків, викривлення площин ковзання і накопичення на них продуктів руйнування кристалічної решітки сприяють збільшенню нерівностей по площині ковзання, а отже, і зміцненню.
При механічній обробці деталей утворення залишкової напруги пов'язане з нерівномірною пластичною деформацією поверхневих шарів, яка протікає при взаємодії силового і теплового факторів.
Деформація супроводжується нерівномірними по глибині та взаємопов'язаними між собою процесами зсуву, переорієнтації, дроблення, подовження або вкорочення складових структури. Залежно від характеру деформацій спостерігається збільшення щільності матеріалу деталі.
При жорстких режимах зміцнення може відбуватися перенаклеп, в результаті якого в поверхневому шарі з'являються небезпечні мікротріщини і намічається утворення частинок металу, що відшаровується. Перенаклеп — незворотний процес, при якому нагрів не відновлює вихідну структуру металу і його механічні властивості.
зміст
Віброабразивна обробка лопаток
Лопатки є характерними масовими деталями авіаційних ГТД, працюють в умовах високих статичних, динамічних і термічних навантажень і багато в чому визначають ресурс і надійність роботи двигуна в цілому.
Для їх виготовлення використовуються високоміцні титанові сплави, неіржавіючі стали, жароміцні сплави на основі нікелю, а також композиційні матеріали.
Трудоємність виготовлення лопаток в більшості конструкцій ГТД складає 30—40 % загальної трудоємності двигуна. Ця особливість, поряд з умовами роботи лопатки в двигуні, вимагає використання у виробництві прогресивних методів отримання заготовок, сучасних технологій обробки, особливо на фінішних операціях, механізації і автоматизації технологічних процесів.
В експлуатації авіаційних ГТД з усіх відмов з причин міцнісних руйнувань деталей на лопатки припадає близько 60%. Переважна більшість руйнувань лопаток носить втомний характер. Цьому нерідко сприяють пошкодження лопаток, викликані попаданням в тракт двигуна твердих частинок (каменів при рулюванні на землі, птиць у польоті і тому подібне). Це викликає потребу мати досить високий запас циклічної міцності лопаток, а також приймати спеціальні технологічні і конструктивні заходи по підвищенню їх живучості в разі отримання пошкоджень (забоін).
Залежно від умов роботи в двигуні рівень змінних напруг в лопатках зазвичай знаходиться в межах 40—160 МПа, а з урахуванням необхідного запасу міцності їх межа витривалості потрібна, як правило, в діапазоні 300—500 МПа. Опір втоми лопатки залежить від матеріалу, конструкції лопатки, технології її виготовлення, але у будь-якому випадку на величину межі витривалості дуже сильно впливає стан поверхневого шару. Основними факторами, що впливають на якість поверхневого шару, є:
- залишкові напруги — їх знак, величина, глибина залягання, характер розподілу по перетину деталі та ін.;
- мікрорельєф поверхні — величина і характер мікронерівностей, наявність рісок;
- структура поверхневого шару [1].
Актуальність завдань по підвищенню опору втоми лопаток привела до розробки та впровадження спеціальних методів обробки та впровадження в галузі ряду спеціальних методів обробки їх поверхні.
Місце віброабразивної обробки в технологічному процесі механообробки лопаток, як правило, фінішний процес, що виконується на завершальній стадії обробки. В залежності від матеріалу лопатки, виду попередньої обробки, і вихідної величини мікронерівностей поверхні і деяких інших факторів призначаються режими обробки — частота і величина амплітуди коливань, характеристики робочих тіл (бій абразиву, формовані вібротіла, керамічні, скляні або металеві кулі, дерев'яні кубики та ін.), співвідношення мас та ін. Це дозволяє досягати бажаного результату в досить широкому діапазоні вихідних станів поверхні. Так, для компресорних лопаток малих і середніх габаритів із сталевих і титанових сплавів остаточної формотворной операцією є холодне вальцювання з наступним скругленням кромок абразивним кругом. У цьому випадку шорсткість поверхні Rа=1,6 і вище, тому використовуються «м'які» режими віброобробки для вирівнювання мікронерівностей по поверхні і створення стискуючої напруги в поверхневому шарі. При цьому застосовується обробка «внавал», (без закріплення деталей) в торообразних вібромашинах. У ряді випадків технологія обробки передбачає на остаточних операціях абразивне шліфування з подальшим поліруванням поверхні пера лопатки. Такі лопатки піддаються більш інтенсивної віброабразівной обробці для зняття мікронерівностей та забезпечення в поверхневому шарі залишкових напруг стиснення.
Реалізувати ефективну віброобробку крупних лопаток турбомашин значно складніше. Велика маса таких деталей з врахуванням ваги контейнера та робочого середовища роблять проблематичним створення вібромашини з прийнятними частотою і амплітудою коливань в двох або трьох координатах із-за різкого зростання потрібної потужності приводів і динамічних перевантажень елементів машин. Крім того, такі деталі мають гіршу якість вихідної поверхні, що знижує продуктивність обробки.
На підприємстві «Мотор Січ» використовується метод подовжньої однокоординатної віброобробки в замкнутому контейнері (ПОВО).
У традиційних вітчизняних і зарубіжних віброабразивних машинах сипкий наповнювач приводиться в рух від коливальних рухів днища контейнера, розташованого завжди знизу. При цьому наповнювач повертається назад вільним падінням. Ефективність такого методу недостатньо висока.
Процес віброабразивної обробки деталей значно активізується і інтенсифікується усередині закритого контейнера з двома днищами, розташованими напроти один одного, якщо сипкий наповнювач активно коливається між ними, отримуючи кінетичну енергію поштовху від кожного днища. Інтенсивність зіткнень наповнювача з оброблюваною деталлю істотно зростає. Бічні стінки контейнера виконуються похилими (конічними), це створює додаткове обтиснення ними наповнювача під час його руху, що збільшує сили динамічної дії між абразивним наповнювачем і стінками контейнера, усередині якого розташовуються оброблювані деталі ГТД в закріпленому або вільному стані.
При віброобробці вказаним методом абразивними гранулами і сталевими каленеми кульками відбуваються більш інтенсивні, ніж в традиційних вібромашинах, знімання металу з поверхні і поверхнева мікродеформація деталей, що збільшує величину і глибину залягання поверхневих стискаючих напруг і підвищує опір втоми деталей.
На рисунку 3 представлені криві зміни шорсткості поверхні лопаток із сталі 14Х17Н2Ш від тривалості обробки на віброустановці з U-образним контейнером.
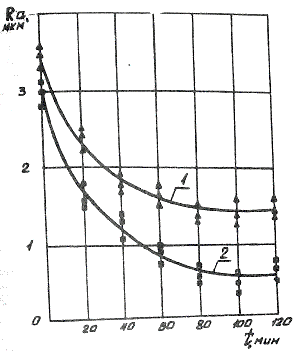
Рисунок 3 – Залежність шорсткості від віброабразивної обробки в U-образном контейнері (1) і методом ПОВО (2)
Досягнення шорсткості Ra=1.5 мкм методом ПОВО, як випливає з рис. 3, відбувається приблизно за 30 мін, а звичайною віброабразивною обробкою — 1,5 ч.
Дослідження віброабразивної обробки турбінних і компресорних лопаток показує переваги цього процесу в порівнянні з поліруванням і глянцеванням у
вручну. Результати дослідження показали, що межа витривалості лопаток, підданих віброшліфуванню і віброполіруванню, складає 410 МПа і задовольняє вимогам ТУ. Величина і характер залишкових напружень досліджуваних лопаток більш сприятливі, ніж на лопатках з поліруванням і глянцеванням вручну.
зміст
Висновоки
Велике значення у вирішенні проблеми забезпечення ресурсу і надійності авіаційних ГТД, а також створення двигунів нових поколінь має розробка, вдосконалення і створення нових технологічних процесів, методів обробки деталей і устаткування, які підвищують не лише продуктивність, але і якість виготовлення.
Поява сучасних типів і модифікацій авіаційних двигунів безперервно супроводиться новими конструкторськими рішеннями, що тягнуть за собою технологічні труднощі. Для їх своєчасного подолання і скорочення розриву між «ідеальною», з точки зору конструкції, і «реальною», з точки зору технології виготовлення деталі, необхідно активно упроваджувати у виробництво прогресивні методи механічної і отделочно-зміцнюючої обробки.
зміст
Література
1. Богуслаев В. А., Яценко В.К., Притченко В.Ф. Технологическое обеспечение и прогнозирование несущей способности деталей
ГТД. -К.: Издательская фирма «Манускрипт», 1993. - 332 с.
2. Дриггс И. Г., Панкастер О. Е. Авиационные газовые турбины. Пер. с англ. Г.Г. Миронова. — М., Оборонгиз, 1957 — 265 с.
3. Жирицкий Г. С. Авиационные газовые турбины. —М., Оборонгиз, 1950 — 511 с.
4. Доронин Ю.В., Макаров В.Ф. Причины образования дефектов на профиле пера титановых лопаток при полировании.// Там же. – 1991. - №12. – С. 17- 19
5. Колощук Э.М., Шаботенко А.Г., Хазанович С.В. Объемная виброабразивная обработка деталей ГТД. // Авиац. прои-сть. – 1973. - №6. С7 13 -16
6. Богуслаев В.А., Яценко В.К., Жеманюк П.Д., Пухальская Г.В., Павленко Д.В., Бень В.П. Отделочно-упрочняющая обработка деталей ГТД – Запорожье, изд. ОАО «МоторСич», 2005 г. – 559 с.
7. Демин Ф. И., Проничев Н. Д., Шитарев И. Л. Технология изготовления основных деталей газотурбинных двигателей: Учеб. пособие. — М.: Машиностроение. 2002. — 328 с.; ил.
8. Сулима А.М., Шулов В.А., Ягодкин Ю.Д. Поверхностный слой и эксплуатационные свойства деталей машин. М.: МашиностроениеЮ, 1988.240с.
9. Скубачевский Г. С. Авиационные газотурбинные двигатели: Учебник для студентов авиационных вузов. М.: Машиностроение, 1969—544 с.
10. Маталин А. А. Технология машиностроения: Учебник для студентов вузов. М.: Машиностроение, 1985—512 с.
11. http://www.nfmz.ru/lopatki.htm
ОАО «Наро-Фоминский машиностроительный завод» Компрессорные лопатки ГТД
12. http://www.nfmz.ru/lopatki.htm
Д.т.н. Юрий Елисеев, генеральный директор ФНПЦ ММПП "Салют", Перспективные технологии производства лопаток ГТД
зміст
Важливе зауваження!
При написанні даного автореферату магістерська робота ще не завершена. Остаточне завершення: грудень 2009 р. Повний текст роботи і матеріали по темі можуть бути отримані у автора або його керівника після вказаної дати.
|