Т Е Х Н О Л О Г И Я
М А Ш И Н О С Т Р О Е Н И Я |
Васьковский Антон Николаевич
Тема выпускной работы:
Совершенствование структурного и технологического обеспечения процессов изготовления лопаток компрессора газотурбинного двигателя в условиях Снежнянского машиностроительного завода
Автореферат по теме выпускной работы
Содержание
Введение
Актуальность темы
Цель и задачи работы
Научная новизна работы
Основная часть
Компрессорные лопатки газотурбинного двигателя
Формирование поверхностного слоя на финишных операциях изготовления лопаток
Виброабразивная обработка лопаток
Заключение
Литература
Введение
Актуальность работы
Ресурс и надежность авиационных двигателей в основном определяются несущей способностью лопаток компрессора (рис. 1), являющихся наиболее ответственными и высоконагруженными деталями, испытывающими в процессе эксплуатации значительные знакопеременные и циклические нагрузки, которые воздействуют на них с большими частотами. Лопатки компрессора самая массовая, высоконагруженная и ответственная деталь авиационного двигателя.
Особенностью лопаток компрессора, имеющих тонкие входные и выходные кромки и изготовленных из титановых сплавов, весьма чувствительных к концентрации напряжений, является то, что они первыми встречаются с инородным телом (птица, град и др.), попавшим в тракт двигателя.
Риски, забоины, эрозионные повреждения и др. дефекты значительно увеличивают уровень локальных вибронапряжений, что резко снижает прочностные характеристики лопаток. Поэтому создание благоприятного сочетания свойств поверхностного слоя на финишных отделочно-упрочняющих операциях оказывает большое влияние на повышение несущей способности лопаток ГТД. Актуальной задачей является оценка влияния поверхностного деформационного упрочнения на ударную прочность лопаток при соударении с посторонними предметами.
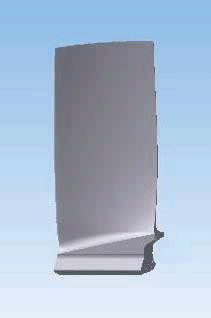
Рисунок 1 - Модель лопатки компрессора ГТД (10 кадров, 20 циклов)
В настоящее время при изготовлении лопаток компрессора широкое применение получили методы пластического деформирования и механической обработки, а также комплексные технологии на финишных операциях технологического процесса.
Виброабразивная обработка (ВО) на специальных установках нашла широкое применение в производстве лопаток компрессора из титановых сплавов. Положительное влияние на эффективность виброабразивной обработки оказывает применение вместе с абразивом химически активных жидкостей.
Ультразвуковая обработка шариками (УЗО) позволяет формировать благоприятное сочетание характеристик поверхностного слоя лопаток компрессора, имеющих малую жесткость, высокую точность изготовления, сложную конфигурацию и тонкие кромки.
Пневмодробеструйная обработка (ПДО) характерна скользящим соударением шариков с поверхностью пера лопатки, не допуская их перенаклепа. Установлено, что ПДО сопровождается уменьшением структурной неоднородности и придает структуре, распределению фаз и остаточным сжимающим напряжениям более однородный характер в поверхностном слое пера лопатки. Предлагаемый пневмодробеструйный метод отделочно-упрочняющей обработки эффективно нейтрализует технологические микродефекты поверхностного слоя, образованные на предыдущих стадиях технологического процесса, сопровождается значительным увеличением предела выносливости, снижением рассеяния долговечности и не требует последующей доводки тонких кромок ручным полированием [6].
Одним из перспективных методов отделочно-упрочняющей обработки является метод магнитно-абразивного полирования (МАП). Отличительная черта МАП заключается в возможности обрабатывать детали с различной конфигурацией и сочетать в одном процессе отделочные и упрочняющие операции.
Проблема эрозии лопаток газотурбинных двигателей является общепризнанной. Интенсивность и вид эрозии лопаток компрессора зависят не только от условий соударения частиц с поверхностью пера, но и от сочетания характеристик поверхностного слоя.
Для повышения износостойкости лопаток все более широкое применение получили различные виды комплексных технологий — нанесение плазменных покрытий в сочетании с различными отделочно-упрочняющими методами.
Разработка и внедрение в серийное производство двигателей в настоящее время сопровождается прогрессивными конструкторско-технологическими решениями, выражающимися в появлении новых деталей, применением принципиально новых конструкционных материалов, а также усовершенствованием технологий производства, сборки и испытания. Широко используются прогрессивные технологические процессы механической обработки, основанные на концепции высокоскоростного резания, усовершенствуются методы отделочно-упрочняющей и термической обработки.
Тесная взаимосвязь между конструкцией и технологией производства
двигателей предопределила ряд актуальных на сегодняшний день вопросов, связанных с повышением несущей способности сложнопрофильных деталей технологическими методами.
содержание
Цель и задачи работы
Цель работы — повышение долговечности и качества лопаток компрессора ГТД за счет совершенствования структурного и технологического обеспечения процессов изготовления лопаток компрессора ГТД.
Основные задачи работы:
1.) Провести анализ современного состояния структурного и технологического обеспечения процессов изготовления лопаток компрессора ГТД;
2.) Исследовать возможности повышения долговечности лопаток компрессора путем нанесения ионно-плазменных покрытий;
3.) Выполнить эксперименты по исследованию свойств износостойкого ионно-плазменного покрытия;
4.) Разработка рекомендаций по совершенствованию структурного и технологического обеспечения процессов изготовления лопаток компрессора ГТД.
содержание
Научная новизна работы
Научная новизна работы заключается в разработке рекомендаций по совершенствованию структурного и технологического обеспечения процессов изготовления лопаток компрессора ГТД и создании оптимальной структуры технологического процесса обработки лопаток компрессора ГТД. Также данная работа предусматривает решение проблемы долговечности и износостойкости лопаток компрессора ГТД.
содержание
Основная часть
Компрессорные лопатки газотурбинного двигателя
Лопатки ГТД работают в условиях высоких температур, достигающих для турбины свыше 1200°С, для компрессора свыше 600°С. Многократное изменение тепловых режимов работы двигателя - быстрый нагрев в момент запуска и быстрое охлаждение при остановке двигателя - вызывает циклическое изменение термических напряжений, характеризуемое как тепловая усталость (рис. 2). Кроме этого, профильная часть пера и хвостовик лопатки, помимо растяжения и изгиба от центробежных сил, изгиба и крутящего момента от скоростного газового потока, испытывают знакопеременные напряжения от вибрационных нагрузок, амплитуда и частота которых изменяются в широких пределах.
Рисунок 2 - Схема движения газовых потоков в ГТД (3 кадра)
Надежность работы рабочих лопаток компрессора и турбины зависит не только от их конструктивной прочности, сопротивления циклическим и длительным статическим нагрузкам, но и от технологии их изготовления, которая непосредственно влияет на качество поверхностного слоя хвостовика и пера лопаток. В поверхностном слое образуются конструктивные и технологические концентраторы напряжений, он испытывает влияние наклепа и внутренних остаточных напряжений от механической обработки. Кроме того, поверхностный слой подвергается воздействию внешних нагрузок при основных видах напряженного состояния (изгибе, растяжении, кручении) внешней среды. Эти негативные факторы могут привести к разрушению лопатки, и, следовательно, к выходу из строя газотурбинного двигателя.
Производство лопаток ГТД занимает особое место в авиадвигателестроении, что обуславливается рядом факторов, главными из которых являются:
• сложная геометрическая форма пера и хвостовика лопаток;
• высокая точность изготовления;
• применение дорогостоящих материалов, таких, как легированные стали и титановые сплавы;
• массовость производства лопаток;
• оснащенность технологического процесса дорогостоящим специализированным оборудованием;
• высокая трудоемкость изготовления.
Для производства лопаток ГТД на сегодняшний день характерны следующие виды механической обработки:
• протягивание;
• фрезерование;
• вальцевание;
• полирование;
• виброполирование или виброшлифование;
• термообработка [11].
содержание
Формирование поверхностного слоя на финишных операциях изготовления лопаток
При изготовлении лопаток ГТД на их поверхностях образуются микронеровности, риски, а в поверхностном слое происходят структурные и фазовые превращения. Кроме того, в поверхностном слое наблюдается повышение твердости металла и формирование остаточных напряжений.
В условиях эксплуатации поверхностный слой воспринимает наибольшие нагрузки и подвергается физико-химическому воздействию: механическому, тепловому, коррозионному и др.
В большинстве случаев у лопаток ГТД начинают ухудшаться служебные свойства поверхности из-за износа, эрозии, коррозии, зарождения усталостных трещин, что может привести к отказу.
После финишной обработки различают такие дефекты поверхности: риски, царапины, задиры, вмятины, поры, трещины, заусеницы и др.
Физико-механические свойства поверхностного слоя, созданные при изготовлении лопаток, во время эксплуатации существенно изменяются под действием силовых, температурных и других факторов.
Поверхность детали по сравнению с сердцевиной имеет ряд
особенностей. Атомы, которые находятся на поверхности, имеют
односторонние связи с металлом, поэтому находятся в неустойчивом состоянии и обладают избыточной энергией по сравнению с
атомами, находящимися внутри.
В результате диффузии, особенно при воздействии повышенных температур, в поверхностном слое возникают химические соединения основного металла с проникающими извне веществами. При повышенных температурах усиливается диффузионная подвижность атомов, приводящая к перераспределению концентрации легирующих элементов. Диффузия в поверхностном слое оказывает заметное влияние на свойства металлов. Это особенно характерно для такой операции, как шлифование, когда в зоне обработки наблюдается высокая температура.
Основными причинами возникновения макронапряжений при механической обработке является неоднородность пластической деформации и локальный нагрев металла поверхностного слоя, а также фазовые превращения.
Степень и глубина наклепа поверхностного слоя деталей обусловлены режимами механической обработки и непосредственно связаны с увеличением количества дислокаций, вакансий и др. дефектов кристаллической решетки металла.
Поверхностный слой деталей ГТД формируется в результате взаимосвязанных явлений, происходящих в очаге деформирования и прилегающих к нему зонах: многократных упруго-пластических деформаций, изменения пластических свойств металла, трения, изменения микро и макроструктуры и др.
При упрочнении в результате деформирования поверхностного
металла и работы трения выделяется теплота, которая
нагревает деталь. При интенсивных режимах обработки локальные
участки поверхностных слоев нагреваются, при выглаживании — до
600—700 °С, при ударных методах — до 800—1000 °С [1].
Такой нагрев приводит к снижению уровня остаточных сжимающих напряжений у поверхности, что может привести к уменьшению эффекта упрочнения. В некоторых случаях происходит превращение сжимающих напряжений в растягивающие.
Основной причиной упрочнения является повышение плотности дислокаций, скапливающихся вблизи линий сдвигов, и последующая их остановка перед различного рода препятствиями, образующимися в процессе деформирования или существовавшими до него. Дробление на блоки объемов металла, заключенных между плоскостями скольжения, поворот этих блоков, искривление плоскостей скольжения и накопление на них продуктов разрушения кристаллической решетки способствуют увеличению неровностей по плоскостям скольжения, а следовательно, и упрочнению.
При механической обработке деталей образование остаточных
напряжений связано с неравномерной пластической деформацией
поверхностных слоев, которая протекает при взаимодействии силового и теплового факторов.
Деформация сопровождается неравномерными по глубине и взаимосвязанными между собой процессами сдвига, переориентации, дробления, удлинения или укорочения составляющих структуры. В зависимости от характера деформаций наблюдается увеличение плотности материала детали.
При жестких режимах упрочнения может происходить перенаклеп, в результате которого в поверхностном слое появляются опасные микротрещины и намечается образование частичек отслаивающегося металла. Перенаклеп — необратимый процесс, при котором нагрев не восстанавливает исходную структуру металла и его механические свойства.
содержание
Виброабразивная обработка лопаток
Лопатки являются характерными массовыми деталями авиационных ГТД, работают в условиях высоких статических, динамических и термических нагрузок и во многом определяют ресурс и надежность работы двигателя в целом.
Для их изготовления используются высокопрочные титановые сплавы, нержавеющие стали, жаропрочные сплавы на основе никеля, а также композиционные материалы.
Трудоемкость изготовления лопаток в большинстве конструкций ГТД составляет 30—40 % общей трудоемкости двигателя. Эта особенность, наряду с условиями работы лопатки в двигателе, требует использования в производстве прогрессивных методов получения заготовок, современных технологий обработки, особенно на финишных операциях, механизации и автоматизации технологических процессов.
В эксплуатации авиационных ГТД из всех отказов по причинам прочностных разрушений деталей на лопатки приходится около 60%. Подавляющее большинство разрушений лопаток носит усталостный характер. Этому нередко способствуют повреждения лопаток, вызванные попаданием в тракт двигателя твердых частиц (камней при рулении на земле, птиц в полете и т.п.). Это вызывает потребность иметь достаточно высокий запас циклической прочности лопаток, а также принимать специальные технологические и конструктивные меры по повышению их живучести в случае получения повреждений (забоин).
В зависимости от условий работы в двигателе уровень переменных напряжений в лопатках обычно находится в пределах 40—160 МПа, а с учетом необходимого запаса прочности их предел выносливости требуется, как правило, в диапазоне 300—500 МПа. Сопротивление усталости лопатки зависит от материала, конструкции лопатки, технологии ее изготовления, но в любом случае на величину предела выносливости очень сильно влияет состояние поверхностного слоя. Основными факторами, влияющими на качество поверхностного слоя, являются:
- остаточные напряжения — их знак, величина, глубина залегания, характер распределения по сечению детали и др.;
- микрорельеф поверхности — величина и характер микронеровностей, наличие рисок;
- структура поверхностного слоя [1].
Актуальность задач по повышению сопротивления усталости лопаток привела к разработке и внедрению специальных методов обработки и внедрению в отрасли ряда специальных методов обработки их поверхности.
Место виброабразивной обработки в технологическом процессе механообработки лопаток, как правило, финишный процесс, выполняемый на завершающей стадии обработки. В зависимости от материала лопатки, вида предшествующей обработки, и исходной величины микронеровностей поверхности и некоторых других факторов назначаются режимы обработки — частота и величина амплитуды колебаний, характеристики рабочих тел (бой абразива, формованные вибротела, керамические, стеклянные или металлические шары, деревянные кубики и др.), соотношения масс и др. Это позволяет достигать желаемого результата в достаточно широком диапазоне исходных состояний поверхности. Так, для компрессорных лопаток малых и средних габаритов из стальных и титановых сплавов окончательной формообразующей операцией является холодное вальцевание с последующим скруглением кромок абразивным кругом. В этом случае шероховатость поверхности Rа=1,6 и выше, поэтому используются «мягкие» режимы виброобработки для выравнивания микронеровностей по поверхности и создания сжимающих напряжений в поверхностном слое. При этом применяется обработка «внавал», (без закрепления деталей) в торообразных вибромашинах. В ряде случаев технология обработки предусматривает на окончательных операциях абразивное шлифование с последующим полированием поверхности пера лопатки. Такие лопатки подвергаются более интенсивной виброабразивной обработке для снятия микронеровностей и обеспечения в поверхностном слое остаточных напряжений сжатия.
Реализовать эффективную виброобработку крупных лопаток турбомашин значительно сложнее. Большая масса таких деталей с учетом веса контейнера и рабочей среды делают проблематичным создание вибромашины с приемлемыми частотой и амплитудой колебаний в двух или трех координатах из-за резкого роста потребной мощности приводов и динамических перегрузок элементов машин. Кроме того, такие детали имеют худшее качество исходной поверхности, что снижает производительность обработки.
На предприятии «Мотор Січ» используется метод продольной однокоординатной виброобработки в замкнутом контейнере (ПОВО).
В традиционных отечественных и зарубежных виброабразивных машинах сыпучий наполнитель приводится в движение от колебательных движений днища контейнера, расположенного всегда снизу. При этом наполнитель возвращается обратно свободным падением. Эффективность такого метода недостаточно высока.
Процесс виброабразивной обработки деталей значительно активизируется и интенсифицируется внутри закрытого контейнера с двумя днищами, расположенными напротив друг друга, если сыпучий наполнитель активно колеблется между ними, получая кинетическую энергию толчка от каждого днища. Интенсивность соударений наполнителя с обрабатываемой деталью существенно возрастает. Боковые стенки контейнера выполняются наклонными (коническими), это создает дополнительное обжатие ими наполнителя во время его движения, что увеличивает силы динамического воздействия между абразивным наполнителем и стенками контейнера, внутри которого располагаются обрабатываемые детали ГТД в закрепленном или свободном состоянии.
При виброобработке указанным методом абразивными гранулами и стальными калеными шариками происходят более интенсивные, чем в традиционных вибромашинах, съем металла с поверхности и поверхностное микродеформирование деталей, что увеличивает величину и глубину залегания поверхностных сжимающих напряжений и повышает сопротивление усталости деталей.
На рисунке 3 представлены кривые изменения шероховатости поверхности лопаток из стали 14Х17Н2Ш от продолжительности обработки на виброустановке с U-образным контейнером.
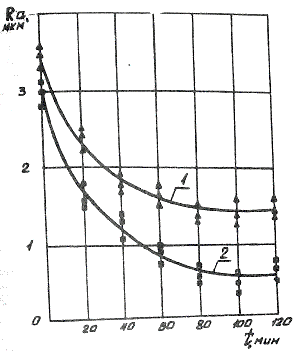
Рисунок 3 – Зависимость шероховатости от виброабразивной обработки
в U-образном контейнере (1) и методом ПОВО (2)
Достижение шероховатости Ra=1.5 мкм методом ПОВО, как следует из рис.3, происходит примерно за 30 мин, а обычной виброабразивной обработкой — 1,5 ч.
Исследование виброабразивной обработки турбинных и компрессорных лопаток показывает преимущества этого процесса по сравнению с полированием и глянцеванием вручную. Результаты исследования показали, что предел выносливости лопаток, подвергнутых виброшлифованию и виброполированию, составляет 410 МПа и удовлетворяет требованиям ТУ. Величина и характер остаточных напряжений исследуемых лопаток более благоприятны, чем на лопатках с полированием и глянцеванием вручную.
содержание
Заключение
Большое значение в решении проблемы обеспечения ресурса и надежности авиационных ГТД, а также создания двигателей новых поколений имеет разработка, совершенствование и создание новых технологических процессов, методов обработки деталей и оборудования, которые повышают не только производительность, но и качество изготовления.
Появление современных типов и модификаций авиационных двигателей непрерывно сопровождается новыми конструкторскими решениями, влекущими за собой технологические трудности. Для их своевременного преодоления и сокращения разрыва между «идеальной», с точки зрения конструкции, и «реальной», с точки зрения технологии изготовления детали, необходимо активно внедрять в производство прогрессивные методы механической и отделочно-упрочняющей обработки.
содержание
Литература
1. Богуслаев В. А., Яценко В.К., Притченко В.Ф. Технологическое обеспечение и прогнозирование несущей способности деталей
ГТД. -К.: Издательская фирма «Манускрипт», 1993. - 332 с.
2. Дриггс И. Г., Панкастер О. Е. Авиационные газовые турбины. Пер. с англ. Г.Г. Миронова. — М., Оборонгиз, 1957 — 265 с.
3. Жирицкий Г. С. Авиационные газовые турбины. —М., Оборонгиз, 1950 — 511 с.
4. Доронин Ю.В., Макаров В.Ф. Причины образования дефектов на профиле пера титановых лопаток при полировании.// Там же. – 1991. - №12. – С. 17- 19
5. Колощук Э.М., Шаботенко А.Г., Хазанович С.В. Объемная виброабразивная обработка деталей ГТД. // Авиац. прои-сть. – 1973. - №6. С7 13 -16
6. Богуслаев В.А., Яценко В.К., Жеманюк П.Д., Пухальская Г.В., Павленко Д.В., Бень В.П. Отделочно-упрочняющая обработка деталей ГТД – Запорожье, изд. ОАО «МоторСич», 2005 г. – 559 с.
7. Демин Ф. И., Проничев Н. Д., Шитарев И. Л. Технология изготовления основных деталей газотурбинных двигателей: Учеб. пособие. — М.: Машиностроение. 2002. — 328 с.; ил.
8. Сулима А.М., Шулов В.А., Ягодкин Ю.Д. Поверхностный слой и эксплуатационные свойства деталей машин. М.: МашиностроениеЮ, 1988.240с.
9. Скубачевский Г. С. Авиационные газотурбинные двигатели: Учебник для студентов авиационных вузов. М.: Машиностроение, 1969—544 с.
10. Маталин А. А. Технология машиностроения: Учебник для студентов вузов. М.: Машиностроение, 1985—512 с.
11. http://www.nfmz.ru/lopatki.htm
ОАО «Наро-Фоминский машиностроительный завод» Компрессорные лопатки ГТД
12. http://www.nfmz.ru/lopatki.htm
Д.т.н. Юрий Елисеев, генеральный директор ФНПЦ ММПП "Салют", Перспективные технологии производства лопаток ГТД
содержание
Важное замечание!
При написании данного автореферата магистерская работа еще не завершена. Окончательное завершение: декабрь 2009 г. Полный текст работы и материалы по теме могут быть получены у автора или его руководителя после указанной даты.
|