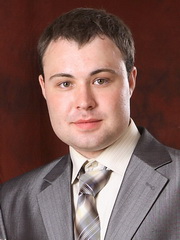
Speciality "Chemical technology of high molecular connections"
Research of influence of structure and the solvent maintenance in a paint on quality flexography
Scientific adviser: Manzhos Uriy
Contents
Relevance:
Important role in attracting consumers and capturing the market of goods is packaging of the goods. It is no secret that the beautiful products will interest more people, and the package with logo or stylistic organization will be an effective promotional swing. And this possibility is provided by the use of flexographic printing. A large variety of materials requires a wide variety of printing inks. So in flexography for each material can be used only a certain kind of paint.
At the moment, more and more attention is paid to the quality of the prints. Quality, in turn, depends on the correctness of the process and the quality of materials used. The solvent plays a leading role in the process of applying the paint coating on the film. It is important to know its performance and behavior under different temperature conditions.Thus the correct selection of the characteristics of the solvent ensure quality prints of any complexity.
Objectives — to examine the physical and chemical basis of the process of paint, the composition of flexographic inks and basic properties of used solvents.
Tasks — improve the quality of flexo printing
—to examine the physical and chemical basis of the process of paint;
—to examine the composition of flexographic inks and basic properties of used solvents;
—to carry out studies to determine the drying time of paint coatings with different solvent content in it.
Volatility is one of the most important properties of solvents. From this index depends not only on the duration of drying paint material and the ability to bear one method or another, but also some properties of the coating. Excessively high volatility can lead to coating defects, and low volatility contributes to retention of large amounts of solvent, which greatly affects the performance properties of the coating.[1] Therefore, the development and application of paints and varnishes must take into account the volatility of solvents, the effect on it of various factors, as well as methods for its determination.
The process of evaporation of volatile substances is described by the Langmuir—Knudsen:
where W — the rate of evaporation;
m — mass of liquid that evaporates;
τ — duration of evaporation;
s — surface evaporation;
p1 — vapor pressure of liquid;
М — molecular mass;
Т — the surface temperature of evaporation;
k — correction factor.
Due to the heat of evaporation cools the surface of the liquid that introduces an error in the determination of the rate of evaporation. Lowering the surface temperature of evaporation depends on the volatility of the solvent (Figure 1.1): the higher the volatility of the solvent, the greater the reduction in surface temperature.
Figure 1.1 — lowering the surface temperature of the evaporation of solvents.
1 — butyl, 2 — toluene, 3 — isopropyl alcohol, 4 — hexane, 5 — acetone
The experimental determination of volatile solvents to consider the transfer of heat from the air and from the substrate. With this in mind lowering the temperature of the evaporating surface can be expressed as formula:
Where h — heat transfer coefficient;
k — thermal conductivity;
cη — experimental coefficient taking into account the heat transfer from the substrate (can be calculated on the basis of experimental results);
ΔHeva — heat of evaporation;
ρi0 — vapor pressure solvent.
The calculated results have good agreement with experimental data. Thus, the evaporation of water at 25°С, the surface was cool down to 15,6°С. In this case, the vapor pressure is reduced from 3.20 kPa (24 mmHg) to 1.73 kPa (13 mmHg). If the surrounding air has a humidity of 50%, which corresponds to the water vapor pressure 1.60 kPa (12 mmHg), the driving force of evaporation is equal to the difference of vapor pressures in the absence of surface cooling at 25°С amounted to 3.20 — 1,60 = 1.60 kPa (12 mmHg. cent.), and when there is a cooling surface, the driving force is significantly reduced: 1.73 — 1.60 = 0.13 kPa (1 mm Hg .). Consequently, the evaporation rate is reduced by 12 times.
The diffusion of the solvent from the liquid layer to the molecules must diffuse through: a) a liquid phase to the surface, and b) the surface layer of liquid, and c) laminar boundary layer of air. After that, hitting a turbulent layer flowing air solvent vapors are carried away. From the standpoint of diffusion, evaporation of the liquid is described by Gardner:
Where a — constant;
D — diffusion coefficient of liquid molecules in the air;
P — atmospheric pressure;
x — effective thickness of the laminar air layer above the surface evaporation.
If the equation of Langmuir—Knudsen is valid only for solvent evaporation in a vacuum, then the equation of Gardner can be applied in the case of evaporation in the air, but it also contains a constant whose value is determined by the conditions of the experiment. In addition to appearing in the equation Gardner parameters for evaporation is significantly affected as the air velocity over the surface of evaporation. Effective thickness of the laminar layer over the surface of x depends on the speed of the air and on the shape of the vessel, which are being identified. These parameters, as well as the length of the evaporation surface in contact with the air flow, takes into account the following equation:
Where n — vapor concentration at the surface;
H — distance from the evaporation surface to the wall;
l — length of surface evaporation;
ν — linear velocity of air;
D — diffusion coefficient of solvent molecules in the air;
ζ — aerodynamic coefficient of displacement (the coefficient of capture).
Formulas can express the absolute rate of evaporation. The relative volatility of W rel is determined by the duration of a certain amount of evaporation of the solvent in comparison with the reference solvent such as diethyl ether, butyl acetate or xylene:
Where τВА90% — time of the evaporation of butyl acetate 90%;
τ90% — time of the evaporation of the solvent 90%.
To determine the relative volatility of solvents have developed various methods and their modifications. The basis of these methods are based on the definition of the kinetics of solvent evaporation from thin films, because the evaporation of large masses of solvent does not represent the nature of the volatilization of solvent from the paint. To study the kinetics of evaporation of a small amount of solvent applied to various substrates like porous (Whatman paper, filter paper) and smooth (glass, aluminum). To the substrate during the experiment is uniformly wetted, the surface, such as aluminum disks treated with alkali solution. Another difficulty is to eliminate uneven layer due to capillary effect. Depending on the size and shape of the disk on which the solvent is applied, the liquid can either go up on his bumper, or meet in the middle of the disc.
Consider the role of solvents in the process of film formation from solutions. Currently accepted that the process of film formation, determined by the evaporation of the solvent occurs in two stages. At the first stage of the process rate depends mainly on the vapor pressure of solvent over the film-forming solution. Since the solute lowers the vapor pressure of the solvent evaporation rate due to this may be reduced. On lowering the vapor pressure affects the degree of thermodynamic affinity of the solvent to the film former dissolved in it. To account for this was offered to enter into the equation of Langmuir —Knudsen excess chemical potential of solvent in the solutionΔμ1:
Where ρ01 — vapor pressure of pure solvent.
After substitution of values ρ1 from this expression in eq Langmuir— Knudsen latter takes the following form:
Where φ1 — volume fraction of solvent.
The excess chemical potential estimated excluding the entropy factor can be calculated using the parameters of the solubility of the polymer δ1 and solvent δ2:
Where φ2 — volume fraction of polymer;
V1 — molar volume of solvent.
Must take into account that the reduction of the vapor pressure of solvent over the polymer solution affects only at relatively high concentrations. So at the beginning of film formation rate of evaporation of the solvent can be calculated without taking into account the interaction of solvent and polymer.
Until the concentration of film former increases slightly, the first stage of film formation on the evaporation rate than the volatility and speed of the surrounding gas is strongly influenced by other factors. The concentration of solvent vapors in the surrounding area allows you to adjust the duration of the first stage of film formation and, consequently, filling and draining of paint material from the surface that is used in coating technology.
Are also important thermal phenomena which accompany the flow of the first stage of film formation. In addition to ambient temperature and the substrate, as well as the amount of heat and speed of its submission to the rate of evaporation of the solvent affects the effect of lowering the temperature overhnosti formed film that is associated with the heat of evaporation of the solvent. Heat transfer, depending on the temperature gradient in the formation of the films can be directed to both the surface and the substrate through the film formed by the surrounding space. Terms and direction of heat transfer depend on the thermophysical properties of the system. There are two extreme cases:
— substrate is a good conductor of heat and has a large mass, and the film is very thin and thermal conductivity;
— and the substrate and the film have a low thermal conductivity.
In the first case, the surface temperature equal to ambient temperature, and evaporation takes place under isothermal conditions. In the second case the heat flow is directed from the environment to the formed film and the surface temperature below ambient temperature.
Proposed to describe the process of drying equations of mass&ndash and heat&ndashtransfer. You can also describe the processes of mass and heat transfer using the similarity criteria, and thanks to the analogy between heat and mass transfer can be used the same experimental data.
When the concentration of film-forming at the surface and, consequently, the density of the surface layer begins to show the convective mixing of the solution, aimed at equalizing the density of the solution over the thickness of the formed film. Viscosity of the system gradually increases and decreases the rate of convective mixing. The system loses fluidity, first at the surface and then deeper, there is a concentration gradient. This point can be considered the beginning of the second stage of film formation, which is called the period of the incident velocity. Fig. 1.2 we can see that the transition from the first stage to the second is relatively smooth. Reduce the rate of evaporation of the solvent increases the concentration of film-forming at the surface up to the transition of the polymer in the glassy state. A so-called surface crust.
Fig. 1.2 — Kinetics of evaporation of heptane from tsiklokauchuka (1) and butyl rubber (2).
The duration of the first stage under the same conditions of film formation depends on the nature of the polymer. The lower glass transition temperature of the polymer, the lower the concentration at which the polymer goes when you remove the solvent in the glassy state. This is well illustrated by Fig. 1.2, which compares the rate of evaporation of the solvent from a rigid polymer (tsiklokauchuka) and elastomers (butyl rubber).
Flexography - this is the most flexible way, which is used today in the industrial sector - mainly in the packaging industry. This technology can be used for all kinds of zapechaiyvaemyh materials [3].
In simplified form, flexo printing machine includes four major elements: duktorny shaft, metering or anilox roller, plate cylinder, impression cylinder. Duktorny shaft rotates in the ink trough, and capture the paint. [2] He then rolls the paint on the anilox roller, it is also sometimes called rolling, dosing, with embossed, engraved, applicator, kraskoperedayuschim.
The methodology of the work:
For this experiment, one must have the following components:
— polypropylene film;
— pigment;
— Technolak for polypropylene film;
— solyufleks (as solvent) or other solvent;
— hollow cylinder.
Pre-treated by corona discharge film is cut into small pieces, about 5x5 cm active side to mount the film is placed on a flat surface of a table or stand. It is also necessary to prepare containers for paint to conduct an experiment under normal conditions.
The experiment
Proceed to prepare the paint. To mix Technolak with pigment in a proportion of 60% Technolak 40% pigment to grab sample of pigment and Technolak 35 grams 55 grams. To spend inserting on technical scale. Selected portions of pigment and Technolak mixed in a glass volume of more than 100 ml for 2 minutes. Next one need to include heat chamber at temperatures of 55°С. Pre-prepared pieces of film are laid on a flat surface of a table or stand. At the film is applied coat of paint approximately 1 ml on the active side of the film, by applying a single drop, with the help of sticks, and further drops of ink rubbing the back of a hollow cylinder. This ensures uniformity of the paint film on the film. After that measured time to complete drying of the paint film. Experience is conducted several times with increase of solvent in the paint. The solvent is added to the paint consistently over 0.5 ml. Adding a solvent using a pipette or other dimensional device. The experiment was conducted for normal conditions, 55°С and 65°С. Then a graph of the drying time of solvent. Graph are handled by least squares. We conclude with respect to temperature change and its effect on the rate of drying.
Table 1 — Dependence of the drying layer of paint on the content of the solvent at temperature 20°С
The content of solvent, ml | 0 | 0,5 | 1,0 | 1,5 | 2,0 | 2,5 | 3,0 |
Drying time, sec | 35 | 36 | 38 | 44 | 50 | 54 | 61 |
Table 2 — Dependence of the drying layer of paint on the content of the solvent at temperature 55°С
The content of solvent, ml | 0 | 0,5 | 1,0 | 1,5 | 2,0 | 2,5 | 3,0 |
Drying time, sec | 25 | 27,5 | 32,6 | 34 | 35,5 | 39 | 47 |
Table 3 — Dependence of the drying layer of paint on the content of the solvent at temperature 65°С
The content of solvent, ml | 0 | 0,5 | 1,0 | 1,5 | 2,0 | 2,5 | 3,0 |
Drying time, sec | 21 | 25 | 27 | 27,8 | 29 | 32 | 40 |
According to the data tables were constructed plots, which are presented in Figure 1.3, as well as the overall plots in Figure 1.4
Fig 1.3 — 3 frames, 20,3 kb, 1,5sec
Fig 1.3 — Dependence of the drying layer of paint on the content of the solvent at temperature 20°С, 55°С, 65°С
Fig 1.4 — Depending on the drying time of the paint film on the content of the solvent at temperatures 20°С, 55°С, 65°С
The experiment revealed the following results. Application of solvent to the paint increases while it dries. This is due to the fact that a large amount of solvent should evaporate. Thus adding to the original paint various solvents can adjust the speed of drying.
ПWith increasing temperature, drying rate increases drying paint layer. Under normal conditions, the drying time is 38sec, at 55°С 32sec and at 65°С 27sec.
Dependence of drying is not linear, and has two inflection at high temperature and one under normal conditions. This is due to go to the next stage of film formation. This transition occurs rather slowly and smoothly.