Содержание
- 1. Тенденции в развитии металлургии
- 2. Описание среднесортного стана 390
- 3. Анализ конструкций ножниц для порезки проката
- 3.1 Классификация ножниц для порезки проката
- 3.2 Описание конструкции ножниц №55 для холодной порезки проката стана 390
- 4. Обзор методов виброметрии
- 4.1 Измерение вибрации
- 4.2 Средства измерения
- 4.3 Методы анализа вибрации
- 4.4 Измерение удара
- 5. Выбор направления дальнейших исследований
- Список источников
1. Тенденции в развитии металлургии
Металлургия – одно из наиболее древних и востребованных направлений деятельности человека. Изделия из металла нашли широкое применение во всех сферах деятельности общества благодаря своим механическим свойствам, не смотря на свою относительную дороговизну и сложность изготовления. Практически все фундаментальные каркасы машин, строительных сооружений, технологических конструкций и обычных бытовых приборов содержат металлические изделия, зачастую являющиеся тем неотъемлемым звеном, без которого принципиально невозможна нормальная работа конструкции.
Постоянно возрастающая востребованность металлических изделий значительно влияла на технологию получения металлических заготовок на всем протяжении развития металлургии. В условиях постоянно увеличивающихся объемов заказов качественного металла на нужды промышленности и строительства, перед руководством металлургических заводов появился ряд задач, связанных с усовершенствованием оборудования производственных цехов, а также с принятием новых, более совершенных и экономически целесообразных, методов производства качественного металла.
В настоящее время в мировой металлургической практике в укрупненном плане принято различать предприятия полного цикла (металлургические комбинаты) и металлургические мини-заводы [1]. Предприятия полного металлургического цикла предполагают выпуск готовой продукции после прохождения всех стадий получения металла, начиная с переработки железоуглеродистого сырья (получение агломерата), заканчивая получением жидкого передельного чугуна в доменных печах, производством стали (преимущественно в кислородных конвертерах), разливкой стали (как правило, на МНЛЗ или в слитки), а также системами прокатных станов для получения определенных видов металлопродукции. Основным отличием металлургических мини-заводов от предприятий с полным циклом является использование в качестве металлического сырья, главным образом, металлолома. При этом технологический процесс выплавки стали базируется на современных дуговых сталеплавильных печах.
В работах А.Н. Смирнова [1], А.А. Минаева [2] показаны основные тенденции в развитии современных металлургических заводов, освещены новые подходы к решению тех или иных задач производства металлических заготовок и готовой продукции. Применение литейно-прокатных модулей, представляющие собой совмещенные в один агрегат машины непрерывного литья заготовки и прокатного стана, различных комбинаций основного технологического оборудования – позволило выйти на новый уровень в развитии производства сравнительно недорогой готовой металлической продукции, такой, как профили, уголки, круги и т.п..
Помимо создания новых мини-заводов, непрерывно проводятся работы по реконструкции производственных мощностей металлургических заводов с полным циклом [1], которые имеют, не смотря на широкие возможности по получению готовой продукции, ряд недостатков. К последним относится низкая гибкость производства под изменения требований заказчика, значительные энергетические затраты, сложность в координации действий различных взаимосвязанных производственных цехов, необходимость в содержании многочисленного штата сотрудников, и, как следствие, значительное повышение стоимости готовой продукции. В связи с этим, для компенсации подобных недостатков, на заводах с полным циклом проводятся мероприятия по усовершенствованию установленного оборудования, либо по полной реконструкции существующих технологических цепочек. Целями подобных усовершенствований являются увеличение гибкости производства, уменьшение влияния человеческого фактора на технологические процессы, и, что немаловажно, подчеркивание своих положительных качеств, а именно: большой объем и высокое качество получаемой готовой продукции.
Технология получения чугуна и стали, отшлифованная годами практики, практически не дает возможностей для масштабных модернизаций, направленных на оптимизацию производства. Однако, выпуск цельнолитых заготовок (блюмов, слябов), отнюдь не является конечной целью в металлургии. Полученные отливки поступают для последующей обработки на прокатные станы, где уже и происходит производство конечной продукции – профилей круглого, квадратного сечения, листов, труб. Сама технология прокатки изначально предъявляет требования исключительно к свойствам самого металла до прокатки, во время, и после нее. Таким образом, возникает значительное пространство для появления новых идей по внедрению на производстве более совершенных и эффективных цепочек обработки цельнолитых заготовок.
Современный прокатный стан – это сложный комплекс разнообразных машин, расположенных непрерывными линиями протяженностью до 1000 м и более, в ряде случаев в трех и более пролетах здания (рис. 1.1, 1.2). Общая масса оборудования крупного прокатного стана превышает 40 тыс. т. Прокатное оборудование – это в основном машины с тяжеловесными станинами или рамами с крупными вращающимися деталями (валками, шпинделями, роликами, валами, шестернями), а также деталями, совершающими возвратно-поступательное и криволинейное движение по сложной траектории [3].
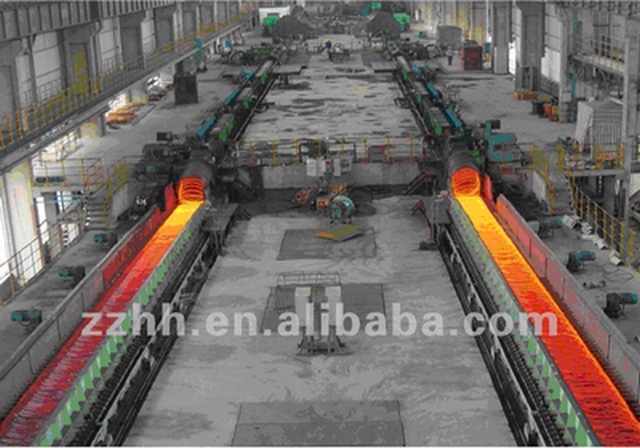
Рисунок 1.1 – Проволочный непрерывный стан
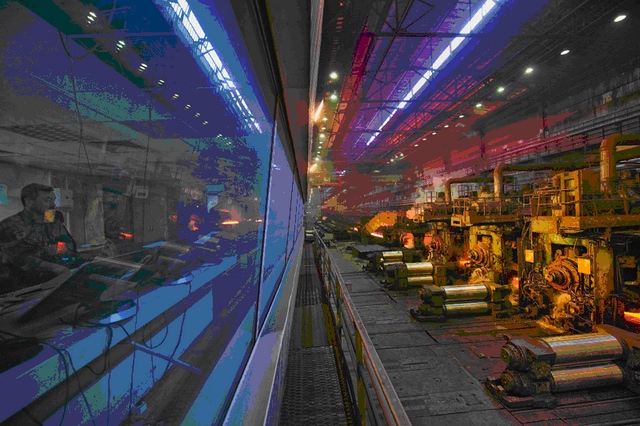
Рисунок 1.2 – Листопрокатный непрерывный стан
Основные фирмы-производители прокатных станов на сегодняшний день – Siemens-VAI, Danieli, Sket, SMS-Demag.
Одним из ярких примеров такого современного прокатного стана является стан 390 Макеевского филиала Енакиевского металлургического завода – один из самых передовых, по оснащенности и организации производства, станов в Украине.
2. Описание среднесортного стана 390
Сортопрокатный стан 390 Макеевского филиала Енакиевского металлургического завода предназначен для выпуска профилей различного типоразмера из исходных заготовок сечением 150х150 мм и 125х125 мм, имеющих длину до 12,0 м [4]. Общая длина стана составляет 500 м; он состоит из 18 рабочих клетей дуо с индивидуальным приводом, в том числе 8 горизонтальных, 4 вертикальных и 6 комбинированных клетей, а также ряда другого технологического оборудования. Максимальная скорость прокатки на стане – 18 м/с, расчетная рабочая скорость – от 2,3 до 17 м/с в зависимости от прокатываемого профилеразмера сортовой стали. Стан оснащен автоматизированными системами регулирования и управления режимами прокатки и работой технологических агрегатов, механизмов и устройств, а также промышленными телекамерами обзора невидимых оператору зон и участков, технологической линии, мониторы которых установлены на соответствующих постах управления.
Сортамент стана очень разнообразен: предусматривается выпуск круглого (диаметром 12..60 мм), квадратного (14..45 мм), шестигранного (с диаметрами вписанной окружности 14..48 мм) сечений, равнополочных (от 25х25х3...4 до 63х3х4…6) и неравнополочных (от 45х28х3...4 до 63х40х4...8) уголков, швеллеров (№ 5,0, № 6,5, № 8,0) и т.д. [4].
Высокий уровень автоматизации, а также использование передовых технологий позволяет выпускать в час до 120 т готовой продукции. Все технологические машины, установленные на стане, выполняют ровно свою незаменимую функцию, и являются звеньями одной большой цепи, имеющая свое начало на участке загрузки блюмов, где пратцен-краны грузят холодные заготовки на загрузочные решетки, и конец – на участках упаковки и погрузки готового проката.
Схема расположения оборудования стана 390 Макеевского филиала Енакиевского металлургического завода приведена на рисунке 2.1.
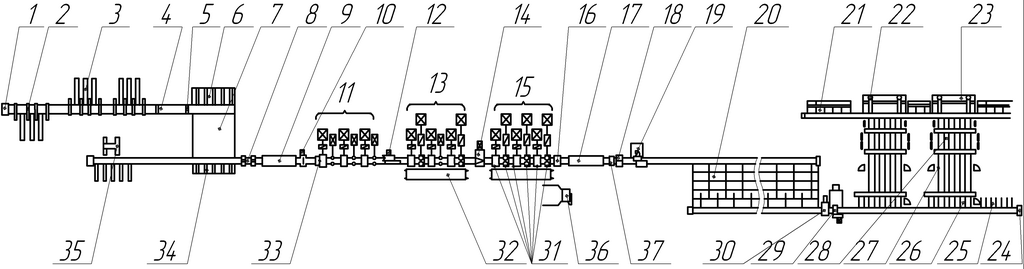
Рисунок 2.1 – Схема расположения оборудования стана 390 Макеевского филиала Енакиевского металлургического завода: 1 – неподвижный упор; 2 – стеллаж брака заготовок; 3 – загрузочная решетка; 4 – рольганговые весы; 5 – опускающийся упор; 6 – сталкиватель; 7 – нагревательная печь; 8 – устройство для гидросбива окалины; 9 – тоннель-термостат; 10 – трайбаппарат перед 1-й клетью; 11 – черновая группа клетей; 12 – кривошипно-рычажные ножницы; 13 – промежуточная группа клетей; 14 – кривошипно-рычажные ножницы; 15 – чистовая группа клетей; 16 – прибор для измерения геометрических размеров; 17 – участок ускоренного охлаждения; 18 – двухсистемные ножницы; 19 – кривошипный крошитель; 20 – реечный стеллаж; 21– мостовые весы; 22 – вязальная машина; 23 – поперечный транспортер; 24 – стационарный упор; 25 – накопитель немерных прутков; 26 – цепной транспортер 1; 27 – цепной транспортер 2; 28 – дозатор; 29 – летучие ножницы холодной резки; 30– правильная машина; 31 – петлерегуляторы; 32 – устройства для смены клетей; 33 – разрывные ножницы; 34 – машина съема заготовок; 35 – сталкиватель; 36 – бракомоталка; 37 – трайбаппарат
Заготовки, подготовленные для прокатки на стане, подаются пратцен-кранами (рис. 2.2) со склада заготовок, и укладываются в один слой на одну из двух загрузочных решеток 3, откуда кулачками реечного шлеппера транспортируются к перекладывающему устройству.
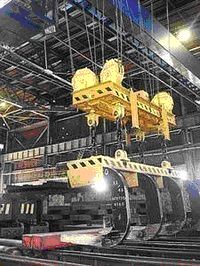
Рисунок 2.2 – Пратцен-кран
Перекладывающим устройством заготовки поштучно передаются на подводящий рольганг, которым транспортируются к нагревательной печи (рис. 2.3). На третьей секции подводящего рольганга заготовки взвешиваются на рольганговых весах 4; фиксированное положение заготовки на участке весов обеспечивается опускающимся упором 5.
Бракованные заготовки подводящим рольгангом подаются в противоположную от печи сторону к стационарному упору 1 и сталкивателем передаются на решетку-стеллаж 2.
Нагрев заготовок до температуры прокатки производится в методической комбинированной печи 7 с водоохлаждаемыми балками; подача и разгрузка заготовок осуществляется с помощью внутрипечных роликов. Печь выполнена по принципу шагающей; нагрев заготовок происходит посредством сгорания газа.
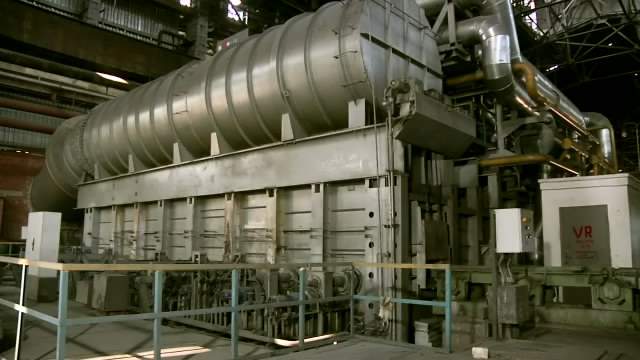
Рисунок 2.3 – Нагревательная печь с шагающими балками
При аварийной ситуации на стане, связанной с прекращением процесса прокатки, или в случае необходимости разгрузки печи, нагретые заготовки с рольганга выгрузки 34 транспортируются по отводящему рольгангу в противоположную от стана сторону к стационарному упору и сталкивателем 35 передаются на стеллаж, откуда после охлаждения убираются пратцен-краном.
Горячая же заготовка, при попадании на основную технологическую линию, поступает в тоннель-термостат 9 (обеспечивающий минимальное падение и выравнивание температуры заготовки перед первой клетью), откуда трайбаппаратом 10 подается в первую клеть.
Перед первой клетью установлены разрывные ножницы маятникового типа 33, которые при производственной необходимости или в аварийных ситуациях выполняют делительный рез и предотвращают дальнейшую подачу заготовки в черновую группу. При этом перемещение верхнего и нижнего ножей из исходного положения до контакта с гранями заготовки осуществляется пневмоприводом, а дальнейшее их внедрение в металл – за счет тянущего усилия первой клети.
Прокатка сортовых профилей на стане осуществляется в трех группах клетей (рис. 2.4):
- черновой 11, состоящей из одной горизонтальной и одной вертикальной клетей 600, двух горизонтальных, и двух вертикальных клетей 440, с чередованием горизонтальных и вертикальных клетей в группе;
- промежуточной 13, состоящей из трех горизонтальных и двух комбинированных клетей 390, и одной вертикальной клети 390; горизонтальные клети чередуются с комбинированными и вертикальной клетями;
- чистовой 15, состоящей из двух горизонтальных и четырех комбинированных клетей 390; горизонтальные клети чередуются с комбинированными.
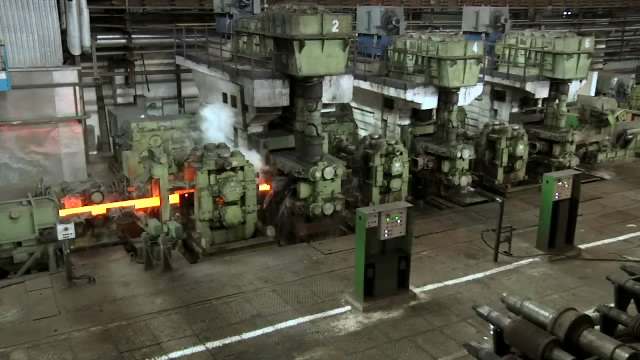
Рисунок 2.4 – Участок клетей
В черновой и промежуточной группах прокатка ведется без кантовки раската с минимальным натяжением его между клетями, которое автоматически поддерживается системой регулирования минимального натяжения.
На кривошипно-рычажных ножницах 12 и 14 (рис. 2.5) после черновой и промежуточной групп производится обрезка передних, и, при необходимости, задних концов раската, а также аварийная порезка на мерные части.
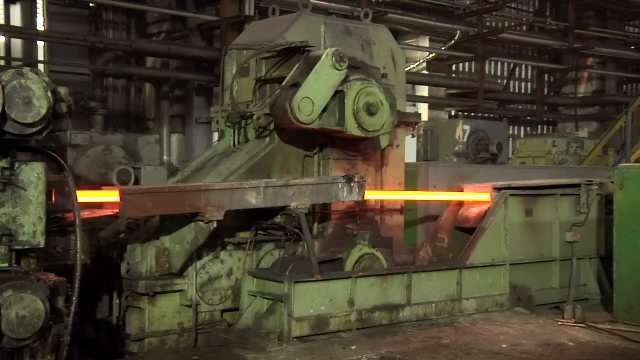
Рисунок 2.5 – Кривошипно-рычажные ножницы
В чистовой группе прокатка осуществляется с использованием системы петлерегулирования. Величина петли поддерживается автоматически петлерегуляторами 31 (рис. 2.6), использующие при работе импульсы от фотоэлектрических датчиков положения петли.
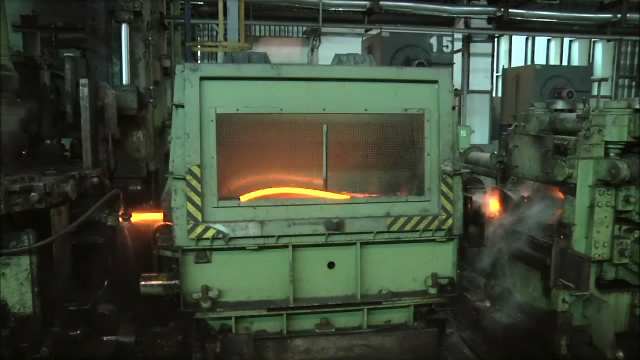
Рисунок 2.6 – Петлерегулятор
Рабочие клети, неиспользуемые в процессе прокатки, удаляются из потока стана, а на их место устанавливаются специальные желоба.
Готовый прокат, после контроля геометрических размеров, транспортируется в установку ускоренного охлаждения 17, обеспечивающая снижение повышение прочностных свойств металла.
При производстве профилей, не подвергающихся ускоренному охлаждению, вместо секций охлаждающих труб в линию стана вводятся соответствующие секции рольганга.
Термоупрочненный или горячекатаный прокат подается трайбаппаратом к двухсистемным стоп-стартовым ножницам 18, на которых производится раскрой его на штанги заданной длины, транспортируемые на холодильник подводящим рольгангом.
Торможение полос готового проката осуществляется на приемном рольганге холодильника системой двойных подъемных клапанов (разделительных перегородок и клапанов).
Сам холодильник представляет собой систему из шагающих реек 20, перекладывающих охлаждаемый прокат в поперченном направлении по мере поступления заготовок (рис. 2.7).
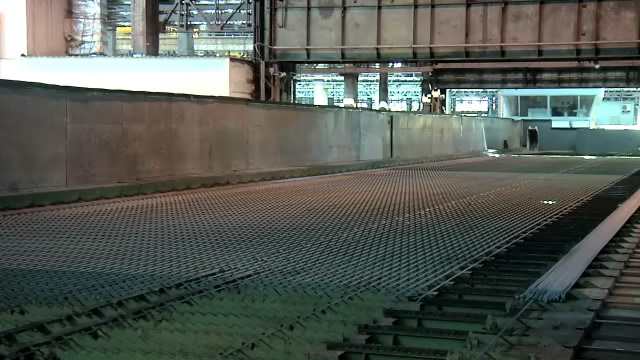
Рисунок 2.7 – Холодильник с шагающими балками
Прокат после реечного стеллажа поступает на передаточное устройство, на собирательных цепях которого формируются слои проката с определенным количеством штанг и шагом раскладки, которые передаются затем на отводящий рольганг холодильника.
На отводящем рольганге слой фасонного проката торцуется по передним концам с помощью опускающегося упора и подается к многоручьевой правильной машине 30. Затем, головная часть слоя проката, после правильной машины, поступает по рольгангу к летучим ножницам холодной резки 29 (рис. 2.8), на которых производится обрезка передних концов прутков проката на готовые длины. При этом правильная машина и летучие ножницы холодной резки работают в синхронном скоростном режиме.
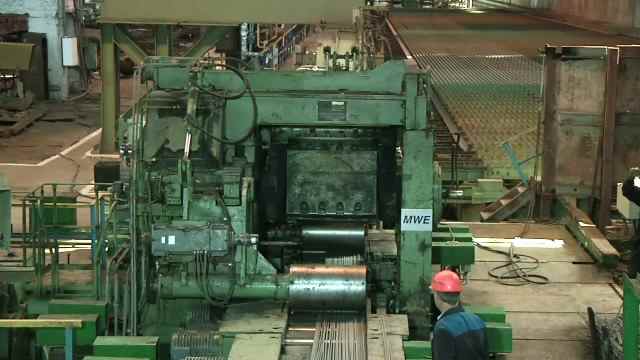
Рисунок 2.8 – Ножницы №55 холодной порезки проката
При производстве простых профилей, не требующих правки, правильная машина выводится из потока и на ее место вводится секция рольганга. В этом случае слой проката с отводящего рольганга подается непосредственно к летучим ножницам холодной резки. Обрезка концов слоя проката и раскрой на ножницах холодной резки проката производится в автоматическом режиме.
Слои прутков готовой длины после порезки на летучих ножницах холодной резки транспортируются на участок отделки.
Затем, в зависимости от профиля и требований заказчика, прокат транспортируется по транспортерам 26 и 27 в зону упаковки, где может быть собран в связки или штабеля при помощи вязальных машин 22 (рис. 2.9).
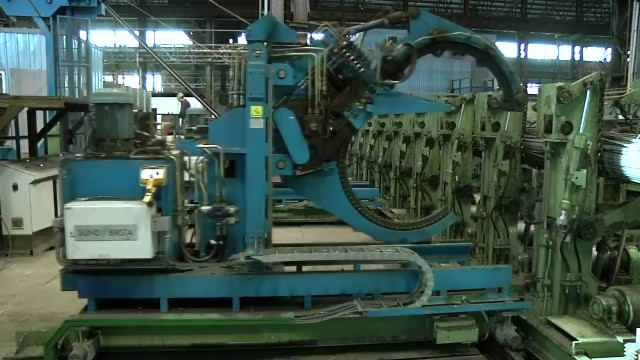
Рисунок 2.9 – Вязальная машина
Пакет или штабель готового проката со сборной решетки передается цеховым краном на склад готовой продукции или на погрузку в вагон.
Все оборудование стана – уникальное, полностью идентичных машин не выпускается, что является одним из характерных признаков металлургического производства. Аварийный выход из строя даже одной из машин влечет за собой аварийную остановку всего технологического комплекса, что, учитывая специфику производства, создает серьезную проблему как экономического, так и практического характера, т.к. температура нагретого металла достигает 1400 °С. При проектировке стана стараются учесть возможность аварийной остановки и предусмотреть различные варианты быстрого выхода из подобных ситуаций. К примеру, при отказе одной из клетей сортопрокатного стана, можно перейти на другой сортамент, и продолжить прокатку, исключив из работы вышедшую из строя клеть.
Но, не смотря на это, в технологической линии прокатных станов есть машины, функции которых заменить невозможно. К такому оборудованию можно отнести нагревательную печь, холодильник, а также ножницы холодной порезки проката.
При отказе одной из машин, находящихся в технологической цепочке, наиболее серьезную проблему создает горячий прокат, находящийся в это время на линии. И, если в случае отказа, к примеру, привода нагревательной печи, заготовки, успевшие попасть на подводящие рольганги, продолжают следовать далее по установленной технологами программе, не создавая опасности для персонала, то в случае отказа ножниц холодной порезки, либо холодильника, находящиеся в конце линии, весь горячий металл остается на рольгангах и в клетях. Существуют методы аварийной разгрузки основной нити прокатного стана, однако и они не позволяют эффективно избежать последствий чрезвычайных ситуаций.
В связи с этим большое внимание уделяется надежности оборудования, путем введения резервных машин и дублирующих приводов, как на холодильнике стана 390. Однако, в случае с ножницами холодной порезки проката, дублирование и резервирование невозможно – механизм синхронизирован с правильной машиной и расположен на строго определенном расстоянии от последней – для обеспечения точного контроля длины проката и качества реза. Любое изменение взаимного расположения ножниц и правильной машины, даже при условии сохранения синхронизации, приведет к ухудшению качества реза, что недопустимо. Установленные в конце производственной линии, они работают в режиме частых пусков-остановов, а также испытывают регулярные ударные нагрузки, при резе остывших заготовок. В отличие от прокатных клетей, нагрузки на которые достаточно хорошо известны и практически не меняются [5], ножницы холодной прокатки – гораздо более неизученный элемент технологической цепи, потому что на каждом стане процесс порезки проката реализован по-разному, и, в соответствии с этим, информация о загруженности несущих элементов ножниц, установленных на одном стане, не может быть применима для аналогичной конструкции, установленной в другой производственной линии.
В связи с этим, обеспечение и контроль работоспособного состояния ножниц холодной прокатки – одна из наиболее важных задач, стоящих перед персоналом прокатного стана.
3. Анализ конструкций ножниц для порезки проката
3.1 Классификация ножниц для порезки проката
Порезка проката на мерные длины – достаточно сложная и ответственная задача. При порезке металла происходит разделение его сдвигом в плоскости реза ножа. Нож имеет переднюю и боковые рабочие грани с углом заострения и режущую кромку. В зависимости от геометрии режущего инструмента и взаимного расположения передних граней ножей, ножницы делят на четыре типа [5].
1 группа – ножницы с параллельными ножами – поперечная резка горячего проката квадратного, прямоугольного и круглого сечения на блюмингах, слябингах, заготовочных и сортовых станах.
2 группа – гильотинные ножницы с наклонными ножами. Используются для горячей и холодной резки листов мелкого профиля пачками.
3 группа – дисковые ножницы – имеют форму дисков и предназначены для поперечного (рельсы, балки) и продольного (листы) резания.
4 группа – ножницы летучие – разрезают полосу по ходу при ее движении в горячем и холодном состоянии.
Каждая из групп ножниц имеет множество вариантов исполнения, в зависимости от поставленных задач. К примеру, летучие ножницы могут иметь конструкцию не только кривошипных, но и барабанных ножниц, на которых ножи устанавливаются на специальных вращающихся барабанах.
3.2 Описание конструкции ножниц №55 для холодной порезки проката стана 390
Ножницы холодной порезки проката, установленные на стане 390 Макеевского филиала Енакиевского металлургического завода, по типу геометрии режущего инструмента и взаимного расположения передних граней ножей, относятся к четвертой группе – летучие ножницы. В зависимости от заданной длины прокатываемого профиля и скорости прокатки, рез происходит каждые 10-20 секунд.
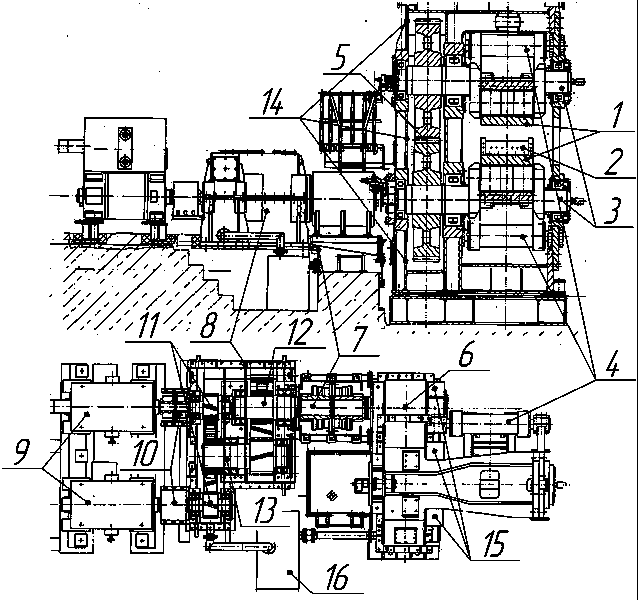
Рисунок 3.1 – Принципиальная схема ножниц холодной порезки проката
На рисунке 3.1 приведена схема ножниц. Рез происходит благодаря плоскопараллельному движению суппортов 1, в каждом из которых закреплен нож 2. Ножи, в зависимости от сортамента проката, имеют различный вид режущей кромки, и могут заменяться при необходимости. Суппорты крепятся в коленях трехопорных коленчатых валах 3, и имеют возможность свободно вращаться на них, благодаря посадке с зазором. Плоскопараллельное движение ножа обеспечивается системой рычагов балансира 4, соединяющегося с ножевым суппортом.
Механическая синхронизация валов осуществляется посредством зубчатой передачи 5, с передаточным отношением 1:1. Зубчатое колесо нижнего коленчатого вала, кроме того, входит в зацепление с приводной шестерней 6. Вал последней посредством муфты 7 соединен с двухступенчатым редуктором 8.
Механизм приводится в движение двумя синхронизированными, и, по необходимости, дублирующими друг друга, двигателями постоянного тока 9 мощностью 620 кВт каждый. Двигатели, через муфты 10, соединяются с редуктором, имеющий два входящих вала-шестерни 11 и один выходной вал 12. Входные валы приводят в движение промежуточный вал 13, имеющего зацепление с зубчатым колесом выходного вала. Все зубчатые передачи выполнены как косозубые. Общее передаточное отношение от двигателя к коленчатым ножам составляет 14,07.
Корпус ножниц представляет собой трехкомпонентную структуру станин 14, на стыках которых расположены коленчатые валы и вал-шестерня. Станины соединяются между собой стяжными болтами М90 15.
Смазывание узлов трения осуществляется при помощи маслостанции 16.
Все компоненты ножниц постоянно подвергаются значительным ударным нагрузкам, поэтому требования к качеству исполнения всех составляющих очень высоки. При наличии в механизме каких либо конструктивных недостатков, или погрешностей при монтаже, кратковременное воздействие динамических сил провоцирует развитие серьезных дефектов фундаментальных и дорогостоящих элементов.
Физически, в момент реза, происходит полное перераспределение сил в механизме, за счет размыкания зазоров зубчатых передач и подшипниковых опор, что создает предпосылки для дополнительных динамических ударов. Такие процессы негативно сказываются на состоянии конструктивных элементов, и требуют дополнительных исследований, для контроля технического состояния ножниц.
Разборные методы контроля технического состояния являются экономически невыгодными, потому что требуют полной остановки работы ножниц, и как следствие, всего стана, что недопустимо в условиях непрерывного производства. Однако, для получения информации о состоянии элементов механизмов, существуют методы неразрушающего контроля. Наиболее оптимальным и информативным методом из них, на данный период времени, является виброметрия [6].
4. Обзор методов виброметрии
4.1 Измерение вибрации
Для механизмов роторного типа (электродвигатели, насосы, вентиляторы, турбины, генераторы и т.д.) широкое распространение во всём мире получили методы контроля, базирующиеся на измерении параметров вибрации. Обусловлено это тем, что вибрация является следствием действия каких-либо сил в самом механизме, и соответственно сигнал вибрации несет в себе информацию о состоянии механизма, его кинематических связей и отдельных узлов. При этом теория и практика анализа вибросигналов к настоящему времени столь отработана, что можно получить достоверную информацию практически по любому дефекту монтажа, изготовления или износу [8].
Трехкомпонентная модель распространения механоакустического сигнала по механизму, принятая за основу в теоретическом контексте методов виброметрии, описана в работах Ю.И. Иориша [8], А.С. Гольдина [9], А.Б. Капрановой [10]. В соответствии с ней, объект, к которому прикладывается внешняя сила, обладает массой, коэффициентом демпфирования и коэффициентом жесткости, в зависимости от значения которых происходит та или иная степень затухания механических колебаний в материале механизма.
Измерение вибрации в машинах роторного типа регламентируется нормативно-технической документацией [11, 12]. В указанных стандартах описываются методы измерения вибрационного сигнала, приводятся требования к измерительной аппаратуре, регламентируются места установки датчиков и указывается границы зон технического состояния для типового роторного оборудования.
Однако, применимость государственных стандартов ограничена для ряда оборудования, в том числе, к машинам, работающим в условиях металлургического производства, что освещено в работе [13]: Данные рекомендации неприменимы к тяжелонагруженным низкоскоростным машинам большой массы, металлорежущим станкам, оборудованию, установленному на податливом основании. Нормативы для такого оборудования могут быть определены экспериментально либо расчетным путем при моделировании неисправных состояний
.
В работах [14, 15, 16, 17] приведены возможные решения распознавания технического состояния механических систем, работающих в длительном режиме. Универсальность методов виброметрии позволяет решать разнообразные задачи, применительно к большому перечню оборудования.
Исследование [18] указывает на тесную взаимосвязь колебательных процессов, вибрации, скоростных режимов с параметрами электроприводов механического оборудования. Параметры двигателя могут являться одним из ключевых диагностических признаков определения технического состояния системы.
Среди многообразия решений вопросов обеспечения надежности оборудования, однако, практически отсутствуют методики оценки состояния машин, работающих в режимах переходных процессов [13]. При этом оборудование прокатных станов, имеющее напряженный циклический режим работы, динамичный и близкий к ударному режим работы, относится именно к такой категории машин [19].
Вопросы динамики прокатных станов неоднократно поднимались в процессе развития металлургии. На рисунке 4.1 представлен график появления работ, касающихся анализа динамических процессов на прокатных станах, начиная с 1960 года.
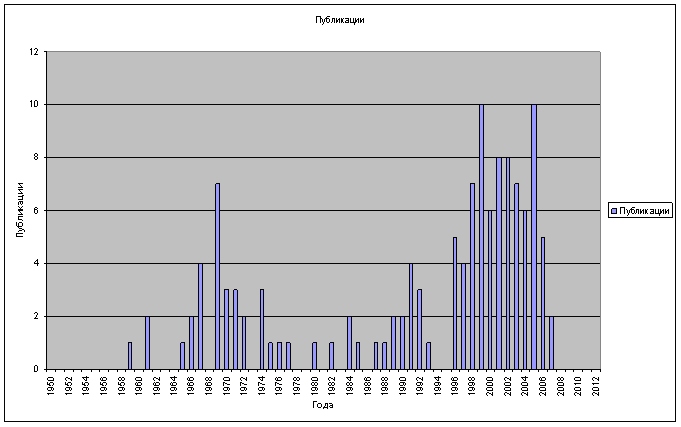
Рисунок 4.1 – График интенсивности появления публикаций материалов на тему динамики прокатных станов
Наибольший скачок в исследовании динамических процессов на прокатном стане прошел в 1998-2004 годах. Данный период характеризуется скачком в количестве прокатных станов, когда вопрос об экономии финансовых ресурсов встал наиболее остро. Остальные периоды всплесков публикаций в этом направлении связаны, прежде всего, с появлением новых достижений научно-технического прогресса, которые позволили начать проводить дополнительные исследования, и, как следствие, привели к появлению литературных изданий.
Срок службы многих станов исчисляется десятками лет. Их следует отнести к тем сложным техническим объектам, когда, по словам Б.Е. Патона, техническое освидетельствование их работоспособности уже не может дать реальную картину состояния конструкции, так как нормативные параметры ее работоспособности могут не совпадать с реальными
[20].
Проблема оценки технического состояния оборудования прокатного производства освещена в работе В.В. Веренева Диагностика и динамика прокатных станов
[21]: Поддержание работоспособности оборудования прокатных станов обеспечивается проведением планово-предупредительных ремонтов, которые являются устоявшейся, однако, устаревшей практикой технического обслуживания. Она позволяет продолжать эксплуатацию прокатных станов, неся при этом большие затраты на ремонты. Современные экономические условия приводят к необходимости внедрения новой стратегии технического обслуживания
.по фактическому состоянию
. Наряду с этим требуются новые решения по определению технического состояния узлов и деталей оборудования прокатных станов
Однако, не смотря на прогресс в рассмотрении вопросов надежности и безотказности машин прокатных цехов, практических подходов к измерению вибрационных параметров ударных процессов до настоящего времени нет [13].
4.2 Средства измерения
Требования к виброизмерительной аппаратуре изложены в нормативно-технической документации: ГОСТ 30265-95 [22], ГОСТ 25275-82 [23], ГОСТ 4.304-85 [24]. Следует отметить, что материалы, изложенные в ГОСТ 25275-82 в значительной части устарели [6].
Номенклатура основных показателей внброизмерительной аппаратуры (включая вибропреобразователи): полоса частот, диапазон измерений, коэффициент преобразования вибропреобразователя, неравномерность АЧХ, относительный коэффициент поперечного преобразования вибропреобразователя, нелинейность АХ, число измеряемых параметров, коэффициент влияния, габаритные размеры, масса, потребляемая мощность сопротивление изоляции [6].
Более подробная классификация виброизмерительных средств приведена в работе Иориша Ю.И. [8]. Разработка подобных средств имела начало еще в середине 20 века, что освещено в ряде работ [25, 26, 27, 28, 29].
Среди средств технического диагностирования, используемых для диагностирования механического оборудования, по уровню решаемых задач и приборной реализации можно выделить: портативные, анализаторы и встроенные системы контроля [13].
Портативные – простые показывающие приборы для определения общего уровня вибрации оборудования (по СКЗ виброскорости), не имеющий памяти и интерфейса [30].
Виброанализаторы (сборщики-спектроанализаторы) – многофункциональные приборы с возможностями определения амплитудно-частоных спектров колебаний, с реализацией различных методов получения информации о состоянии оборудования по виброакустическим сигналам, сбора и анализа диагностических данных, балансировки роторов [30].
Стационарные системы – многоканальные измерительные комплексы, предназначенные для измерения, регистрации и анализа вибрации контролируемого стационарного оборудования [30].
Различные конструкции и типы датчиков для фиксации вибропараметров рассмотрены в работах В.А. Сидорова [13], Б.Л. Герике [30], Г.Ш. Розенберга [6]. В настоящее время, для измерения параметров вибрации, используется 3 типа датчиков: акселерометры – для измерения виброускорения; велосиметры – для измерения виброскорости; проксиметры – для измерения виброперемещений
.
На данный момент наиболее распространенные производители анализаторов вибрации – это ДИАМЕХ, ВиКонт, Оргтехдиагностика, SKF, МЕРА, ВАСТ, ТСТ, Вибро-Центр, ИНКОТЕС.
4.3 Методы анализа вибрации
В настоящее время существует три основных метода анализа вибропараметров: анализ временных реализаций сигнала, анализ общего уровня вибрации и спектральный анализ [13].
Временная форма (рис. 4.2) является базовой для остальных методов и включает в себя запись определенного диапазона частот параметра вибрации во временном разрезе [8]. Основные настроечные параметры для фиксации временной формы – длительность записи, диапазон измерения и период фиксации значений [13].
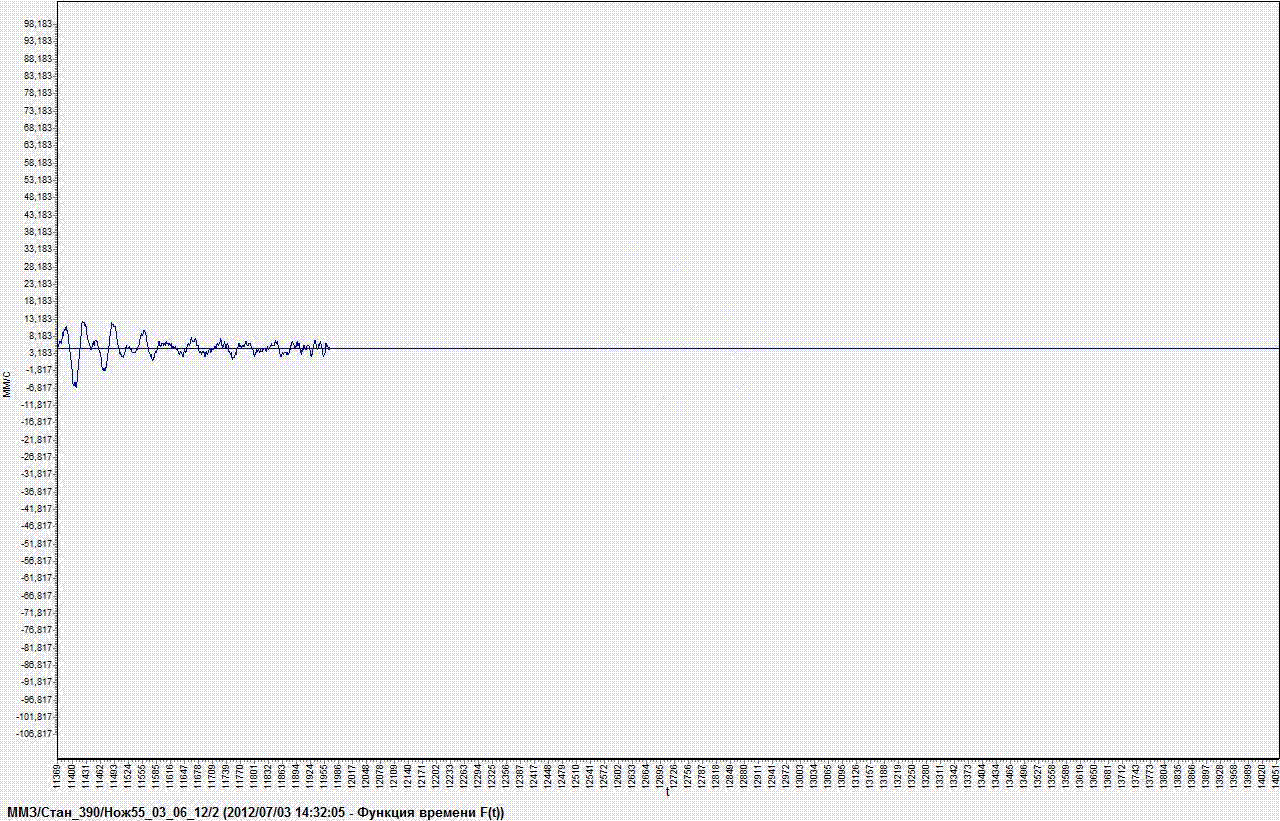
Рисунок 4.1 – Анимированный пример временной реализации сигнала – переходный процесс (сделано в mp_gif_animator, 111 кБ, 5 кадров, 0,7 сек задержки между кадрами, 4 цикла повторения)
В работе В.А. Сидорова [13] приведены диагностические параметры при анализе временной реализации вибрационного сигнала для оценки технического состояния механизма, работающего с ударными нагрузками.
- Стабильность, повторяемость процесса. Повреждения в механической системе приводят к возникновению случайных колебаний, отражающихся на конкретных временных реализациях.
- Симметричность сигнала.
- Увеличение параметров вибрации во время наиболее нагруженной работы механизма по сравнению с работой на холостом ходу.
- Характерные параметры процесса затухания колебаний механической системы после снятия нагрузки.
- Изменение временной картины при изменении направления вращения отражает параметры технического состояния механизма.
Метод анализа общего уровня вибрации является одним из наиболее широкоиспользуемых методов благодаря своей информативности и низкой требовательности к виброизмерительной аппаратуре. При определении значений общего уровня вибрации обычно подразумевают измерение среднеквадратичного значения виброскорости в частотном диапазоне от 10 до 1000 Гц. Это соответствует требованиям стандарта ИСО 10816-97-1 [11]. Для оценки состояния подшипников качения эффективным является измерение пикового и среднеквадратичного значений виброускорения в более высоких частотных диапазонах [13]. Стоит отметить, что для измерения общего уровня вибрации требуется некоторое усреднение выборок из временного сигнала.
При определении причины вибрации необходимо учитывать направление измерения. Регламентируется проведение измерений вибрации корпусов подшипников в трех взаимно перпендикулярных направлениях: вертикальном, горизонтальном и осевом (рис. 4.3). Измерение общего уровня вибрации в вертикальном направлении проводится в наивысшей точке корпуса. Горизонтальная и осевая составляющие измеряются на уровне разъема крышки подшипника или горизонтальной плоскости оси вращения. Измерения, проведенные на защитных кожухах, металлоконструкциях не позволяют определить техническое состояние механизма из-за нелинейности свойств данных элементов [11].
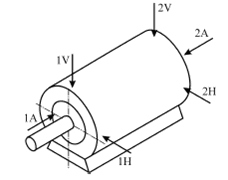
Рисунок 4.3 – Направления измерения общего уровня вибрации
В ряде работ приведены методики анализа результатов общего уровня вибрации [7-10].
Спектральный анализ – это метод обработки, позволяющий выявить частотный состав вибрационного сигнала. Выявление повышенных амплитуд вибрации на частотах, совпадающих с частотами возможных повреждений элементов, резонансных частотах деталей, на частотах протекания рабочего процесса помогает обнаружить и идентифицировать неисправность на ранних стадиях зарождения и развития [13].
Существует два способа описания сигнала вибрации – во временной области и в частотной (рис. 4.4). Измерение на определённой частоте даёт информацию о неисправности раньше, чем измерение общего уровня вибрации. При спектральном анализе используются ряд последовательных фильтров или перемещаемый полосовой фильтр [16].
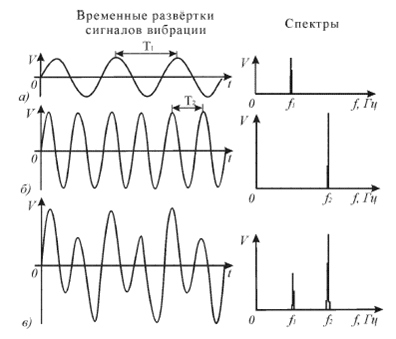
Рисунок 4.4 – Временные сигналы вибрации и их спектры: а) гармонические колебания с периодом Т1; б) гармонические колебания с периодом Т2; в) полигармонический сигнал
Решение задач спектрального анализа возможно при использовании быстрого преобразования Фурье, позволяющего определить вклад отдельных составляющих спектра вибрации в общую картину вибрации [33]. Использование математических методов интегрирования и дифференцирования параметров вибрационного сигнала значительно повысило требования к вычислительному аппарату виброанализаторов.
Вопросами анализа результатов измерений вибрации спектральными методами занимался ряд авторов [6, 7, 9, 14, 15, 16, 17, 18].
4.4 Измерение удара
Сложность оценки состояния машин, работающих в повторно-кратковременном и ударном режимах, заключается в отсутствии достаточно длительных по времени промежутков равномерной работы, что значительно ограничивает применимость большинства методов, используемых в виброметрии.
Анализ общего уровня вибрации, спектральный анализ – оказывается неприменим для таких машин, т.к. эти методы контроля основываются на усреднении и обработке временных промежутков вибрационного сигнала. При этом информативность переходных процессов известна, потому что именно в них проявляются все скрытые дефекты и зарождающиеся повреждения машины [13, 14, 35].
Процесс удара сопровождается изменением частотных составляющих сигнала, зависящих от изменения воздействия внешней силы, жесткостей соединений, демпфирующих свойств каждой из деталей. Одним из характерных факторов ударного процесса в механических системах является дребезжание [8]. Дребезжание возникает главным образом из-за люфтов во вращающихся деталях. При этом наравне с пиками, следующими хаотически один за другим, удается все же обнаружить и некоторые элементы периодичности, связанные с числом оборотов вращающихся деталей. Однако часто дребезжание происходит совершенно независимо от вращения. Например, оно может быть вызвано соударением гаек и шайб, отвинтившихся во время работы машины из-за плохой сборки. В записи такой хаотической вибрации никакой упорядоченности пиков обычно не бывает
.
В ряде работ было исследована возможность использования сверхбыстрого преобразования Фурье [36, 37], позволяющего формировать спектрограмму при быстротекущих процессах, используя минимальное усреднение временного сигнала.
Однако, наиболее эффективным методом анализа состояния механизмов, работающих во время переходных процессов, по мнению ряда авторов, является анализ временных реализаций вибрационного сигнала [13, 38]. Временная реализация вибрационного сигнала механизма кратковременного режима работы может быть охарактеризована двумя факторами – текущими положительными и отрицательными значениями амплитуды колебаний A, –A и соответствующими периодами колебаний T
(рис. 4.5).
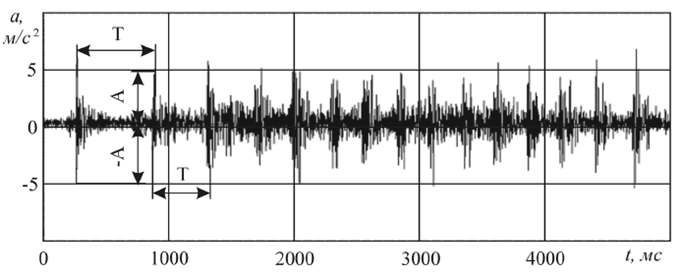
Рисунок 4.5 – Пример временной реализации временного сигнала
Результаты исследований переходных процессов в электро-гидро-механических системах металлургических машин, включая прокатные станы, обобщены в монографии коллектива авторов [39].
Данные аспекты, как базис, использовала фирма Инкотес
для своего программного обеспечения Старт/Стоп
[40], при помощи чего появилась возможность фиксировать на ограниченном промежутке времени различные параметры, имеющих определенную информативность на переходных процессах. Программа позволяет обрабатывать сигнал длительностью до 16 секунд, с интенсивностью до 32768 точек за 16 секунд, с частотным диапазоном от 0 до 16000 Гц, и возможностью снятия до 500 спектров за период измерения. Среди измеряемых параметров присутствуют диаграммы Боде, Найквиста, текущая траектория движения поверхности, вэйвлет анализ.
Не смотря на все свои достоинства, информация, полученная при помощи программы фирмы Инкотес
, на данный момент не может быть ключевой при оценке технического состояния оборудования на переходных процессах, потому что отсутствует достаточная экспериментальная и теоретическая база применимости используемых методов. В том числе, отсутствует универсальная методика обработки временных реализаций вибрационного сигнала, что делает создание нормативов для оценки параметров вспомогательных методов измерения переходных процессов неэффективным.
5. Выбор направления дальнейших исследований
Виброметрия, как один из методов неразрушающего контроля – наиболее развитый и информационно емкий для оценки технического состояния роторных машин любого типа, в том числе и ножниц холодной порезки проката №55. Однако, данный механизм работает в режиме частых остановов и пусков, и, к тому же, испытывает сильные ударные нагрузки.
Использование методик оценки общего уровня вибрации и спектральный анализ не допустимо в таких условий, т.к. в обоих случаях временной сигнал перед обработкой усредняется, и поэтому эти методы не способны предоставить информацию о техническом состоянии. При этом, быстротекущие динамические процессы являются ключом для решения этой задачи – ведь именно в эти периоды механизм испытывает пиковые напряжения, максимально проявляя все свои недостатки и дефекты в конструкции.
Использование вэйвлет анализа, информации о траекториях движения во время пусков-выбегов также не эффективно, потому что на данный момент отсутствует подходящая теоретико-практическая база для оценки технического состояния машин этими методами.
Для развития данных направлений вибродиагностики, на данный период времени, есть необходимость формализовать временные выборки вибрационного сигнала.
В связи с этим, целью данной работы является составление методики и критериев оценки технического состояния машин, работающих в режиме частых переходных процессов, методом анализа вибрационного временного сигнала.
Задачи, которые необходимо решить в данной работе:
- Проанализировать существующие дефекты на ножницах, и сопоставить их с измеренными на машине временными вибрационными выборками.
- Вывести математическую зависимость распространения механических колебаний при переходных процессов, при наличии и отсутствия зазоров в механизме.
- Постановка и проведение эксперимента, который включает фиксацию ударного процесса, и изменение его параметров при разных начальных условиях.
- Анализ и систематизация полученных данных, составление выводов.
При написании данного реферата магистерская работа еще не завершена. Окончательное завершение: декабрь 2013 года. Полный текст работы и материалы по теме могут быть получены у автора или его руководителя после указанной даты.
Список источников
- Металлургические мини-заводы: Монография / М 54 Смирнов А.Н., Сафонов В.М., Дорохова Л.В., Цупрун А.Ю. – Донецк: Норд-Пресс, 2005. – 469 с.
- Минаев А.А. Совмещенные металлургические процессы: Монография – Донецк: Технопарк ДонГТУ УНИТЕХ, 2008. – 552 с.
- Торопов А.С. и др. Охрана труда при монтаже технологического оборудования. М. Стройиздат, 1987 г. – 286 с.
- Стан 390. Техническая документация
- A. И. Целиков, П. И. Полухин, В. М. Гребеник и др. Машины и агрегаты металлургических заводов. В 3-х томах. Том 3. Машины и агрегаты для производства и отделки проката. Учебник для вузов. – 2-е изд., перераб. и доп. – М.: Металлургия, 1988. – 680 с.
- Розенберг Г.Ш., Мадорский Е.З. и др. Вибродиагностика Монография. / СПб.: ПЭИПК, 2003. – 284 с.
- Кравченко В.М. Техническое обслуживание и диагностика промышленного оборудования. – Донецк: ООО
Юго-Восток, Лтд
, 2004. – 504 с. - Иориш Ю.И. Виброметрия М.: Государственное научно-техническое издательство машиностроительной литературы, 1963. – 756 с.
- Гольдин А.С. Вибрация роторных машин: – 2-е изд. исправл. – М.:Машиностроение, 2000 – 344 с.
- Основы теории механических колебаний, Капранова А.Б., Зайцев А.И. – Ярославский государственный технический университет, 1999. – 112 с.
- ГОСТ 20815-93
Машины электрические вращающиеся. Механическая вибрация некоторых видов машин с высотой оси вращения 56 мм и более. Измерение, оценка и допустимые значения
. - ГОСТ ИСО 10816-1-97
Вибрация. Контроль состояния машин по результатам измерений вибрации на невращающихся частях. Часть 1. Общие требования
. - Кравченко В.М., Сидоров В.А., Седуш В.Я. Техническое диагностирование механического оборудования: Учебник. – Донецк: ООО "Юго-Восток, Лтд", 2009. – 459 с.
- Биргер И. А. Техническая диагностика. – М.: Машиностроение, 1978. – 240 с.
- Артоболевский И. И., Бобровницкий Ю. Н., Генкин М. Д. Введение в акустическую диагностику машин. – М.: Наука, 1979. – 296 с.
- Голуб Е. С., Мадорский Е. З., Розенберг Г.Ш. Диагностирование судовых технических средств: Справочник. – М.: Транспорт, 1993. – 150 с.
- Коллакот Р. А. Диагностирование механического оборудования. – Л.: Судостроение, 1980. – 281 с.
- Борисенко В. Ф., Сидоров В. А., Мельник А. А. Подходы к оценке состояния электромеханических систем / Наукові праці Донецького національного технічного університету. Серія:
Електротехника і енергетика
, випуск 79. – Донецьк: ДонНТУ, 2004. – С. 23–26. - Ловчиновский Э. В., Вагин В. С. Эксплуатационные свойства металлургических машин. – М.: Металлургия, 1986. – 160 с.
- Патон Б.Е., О состоянии работ в Украине по технической диагностике промышленного оборудования, конструкций и сооружений. Доклад на 3-м расширенном заседании Технического комитета по технической диагностике и неразрушающему контролю (ТК-78) 27 мая 1999 г. Направление
Техническая диагностика
//Техническая диагностика и неразрушающий контроль
, 1999, №3. – С. 66-68. - В.В. Веренев, В.И. Большаков, А.Ю. Путноки, А.А. Корень, С.В. Мацко. Диагностика и динамика прокатных станов. Монография. Днепропетровск: IMA-пресс. – 2007. – 144 с.
- ГОСТ 30265-95
Варисторы. Метод испытания импульсной электрической нагрузки
. - ГОСТ 25275-82
Система стандартов по вибрации. Приборы для измерения вибрации вращающихся машин. Общие технические требования
. - ГОСТ 4.304-85
Система показателей качества продукции. Аппаратура и приборы для измерения вибрации. Номенклатура показателей
. - Дрейпер Ч. C., Маккей В., Лис С. Измерительные системы, Машгиз, 1960. – 784 с.
- Ушаков А. А. Виброизмерительная аппаратура, Изд. ВВА им. Н. Е. Жуковского, 1948. – 288 с.
- Кlotter К. – Messung mechanischer Schwingungen, Berlin, 1943.
- Messung mechanischer Schwingungen,
Richtlinien VDI
, 205—210, 1956. - Steuding H. Messung niechanischer Schwingungen, Berlin 1928.
- Герике Б.Л., Абрамов И.Л., Герике П.Б. Вибродиагностика горных машин и оборудования. Учебное пособие / Кузбасский государственный технический университет 2007. – 168 с.
- Седуш В. Я., Сидоров В. А., Ошовская Е. В. Контроль технического состояния металлургических машин по виброакустическим параметрам. Сб. научн. трудов. – Алчевск: ДГМИ, 2000. – Вып. 12. – С. 213–218.
- Сидоров В. А., Куватов А. В., Куришева Е. П. Анализ временных реализаций вибрационного сигнала / Научно-технический и производственный сборник статей
Вибрация машин: измерение, снижение, защита
. – 2005. – № 2. – С. 10–14. - Основы анализа данных и поиска неисправностей. By Glenn D. White, DLI Engineering Corporation. Пер. с англ. – Шейняк И. Р. / под ред. Смирнова В. А. Vibrashion.ru\Основы анализа.htm
- Преобразование Фурье и классический цифровой спектральный анализ. Медведев С.Ю., к.ф., м.н. [Электронный ресурс]. – Режим доступа: http://www.vibration.ru/preobraz....
- Электромеханические системы автоматизации стационарных установок (под общ. редакцией проф. Борисенко В.Ф.). – Донецк: ДонНТУ, НПФ
МИДИЭЛ
, – 2005. – 459 с. - Вэйвлеты в вибрационной динамике машин. А.И. Прыгунов [Электронный ресурс]. – Режим доступа: http://www.vibration.ru/wavelet....
- Добеши И. Десять лекций по вэйвлетам. Ижевск: НИЦ
Регулярная и хаотическая динамика
, 2001. – 464 с. - Диагностические параметры переходных процессов при оценке технического состояния электромеханических систем. Лытаев А.В., Сидоров В.А. // Автоматизація технологічних об'єктів та процесів / Матеріали ХIІ Міжнародної науково-технічної конференції аспірантів і студентів. – Донецьк, ДонНТУ – 2012, с. 441-443.
- Переходные процессы в электро-гидро-механических системах металлургических машин. Монография / Большаков В.И., Злобинский В.Е., Харлан Б.А., Цехнович Л.И., Яхно О.М. Днепропетровск: 2002. – 324 с.
Старт/Стоп
– измерение и анализ вибрации на переходных режимах, ОООИнкотес
[Электронный ресурс]. – Режим доступа: http://encotes.ru/....