Зміст
- 1. Тенденції у розвитку металургії
- 2. Опис середньосортного стану 390
- 3. Аналіз конструкцій ножиць для різання прокату
- 3.1 Класифікація ножиць для різання прокату
- 3.2 Опис конструкції ножиць № 55 для холодної різки прокату табору 390
- 4. Огляд методів віброметрії
- 4.1 Вимірювання вібрації
- 4.2 Засоби вимірювання
- 4.3 Методи аналізу вібрації
- 4.4 Вимірювання удару
- 5. Вибір напрямку подальших досліджень
- Перелік посилань
1. Тенденції у розвитку металургії
Металургія – одна з найбільш древніх і затребуваних напрямів діяльності людини. Вироби з металу знайшли широке застосування у всіх сферах діяльності суспільства завдяки своїм механічним властивостям, не дивлячись на свою відносну дорожнечу і складність виготовлення. Практично усі фундаментальні каркаси машин, будівельних споруд, технологічних конструкцій і звичайних побутових приладів містять металеві вироби, найчастіше є тією невід'ємним ланкою, без якого принципово неможлива нормальна робота конструкції.
Постійно зростаюча затребуваність металевих виробів значно впливала на технологію одержання металевих заготовок на всьому протязі розвитку металургії. В умовах постійно зростаючих обсягів замовлень якісного металу на потреби промисловості й будівництва, перед керівництвом металургійних заводів з'явився ряд завдань, пов'язаних з удосконаленням обладнання виробничих цехів, а також з прийняттям нових, більш досконалих і економічно доцільних, методів виробництва якісного металу.
В даний час у світовій металургійній практиці в укрупненому плані прийнято розрізняти підприємства повного циклу (металургійні комбінати) і металургійні міні-заводи [1]. Підприємства повного металургійного циклу припускають випуск готової продукції після проходження всіх стадій отримання металу, починаючи з переробки залізовуглецевих сировини (отримання агломерату), закінчуючи отриманням рідкого передільного чавуну в доменних печах, виробництвом сталі (переважно в кисневих конвертерах), розливанням сталі (як правило, на МБЛЗ або в злитки), а також системами прокатних станів для отримання певних видів металопродукції. Основною відмінністю металургійних міні-заводів від підприємств з повним циклом є використання в якості металевого сировини, головним чином, металобрухту. При цьому технологічний процес виплавки сталі базується на сучасних дугових сталеплавильних печах.
У роботах А.Н. Смирнова [1], А.А. Мінаева [2] показані основні тенденції в розвитку сучасних металургійних заводів, освітлені нові підходи до вирішення тих чи інших завдань виробництва металевих заготовок і готової продукції. Застосування ливарно-прокатних модулів, що представляють собою сполучені в один агрегат машини безперервного лиття заготовки та прокатного стану, різних комбінацій основного технологічного устаткування – дозволило вийти на новий рівень у розвитку виробництва порівняно недорогий готової металевої продукції, такої, як профілі, кути, круги і т . п..
Крім створення нових міні-заводів, безперервно проводяться роботи з реконструкції виробничих потужностей металургійних заводів з повним циклом [1], які мають, не дивлячись на широкі можливості по отриманню готової продукції, ряд недоліків. До останніх відноситься низька гнучкість виробництва під зміни вимог замовника, значні енергетичні витрати, складність в координації дій різних взаємозв'язаних виробничих цехів, необхідність в утриманні численного штату співробітників, і, як наслідок, значне підвищення вартості готової продукції. У зв'язку з цим, для компенсації подібних недоліків, на заводах з повним циклом проводяться заходи по удосконаленню встановленого обладнання, або за повної реконструкції існуючих технологічних ланцюжків. Цілями подібних удосконалень є збільшення гнучкості виробництва, зменшення впливу людського фактору на технологічні процеси, і, що важливо, підкреслення своїх позитивних якостей, а саме: великий обсяг і високу якість отримуваної готової продукції.
Технологія одержання чавуну і сталі, відшліфована роками практики, практично не дає можливостей для масштабних модернізацій, спрямованих на оптимізацію виробництва. Однак, випуск суцільнолитих заготовок (блюмів, слябів), аж ніяк не є кінцевою метою в металургії. Отримані виливки надходять для подальшої обробки на прокатні стани, де вже і відбувається виробництво кінцевої продукції – профілів круглого, квадратного перетину, аркушів, труб. Сама технологія прокатки спочатку висуває вимоги виключно до властивостей самого металу до плющення, під час, і після неї. Таким чином, виникає значний простір для появи нових ідей щодо впровадження на виробництві більш досконалих і ефективних ланцюжків обробки суцільнолитих заготовок.
Сучасний прокатний стан – це складний комплекс різноманітних машин, розташованих безперервними лініями довжиною до 1000 м і більше, в ряді випадків у трьох і більше прогонах будівлі (рис. 1.1, 1.2). Загальна маса обладнання крупного прокатного стану перевищує 40 тис. т. Прокатне обладнання – це в основному машини з великоваговими станинами або рамами з великими обертовими деталями (валками, шпинделями, роликами, валами, шестернями), а також деталями, що здійснюють зворотно-поступальний і криволінійний рух по складній траєкторії [3].
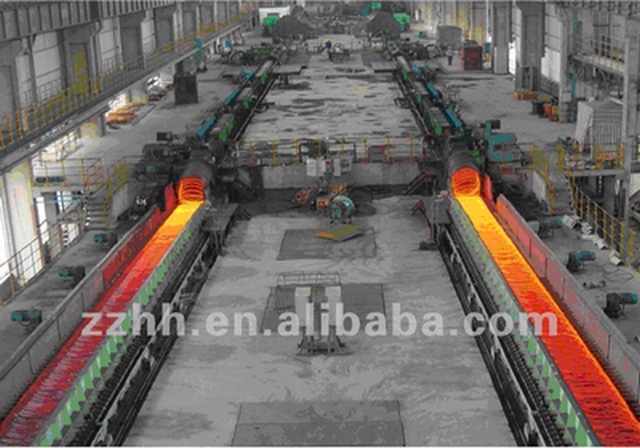
Рисунок 1.1 – Дротяний безперервний стан
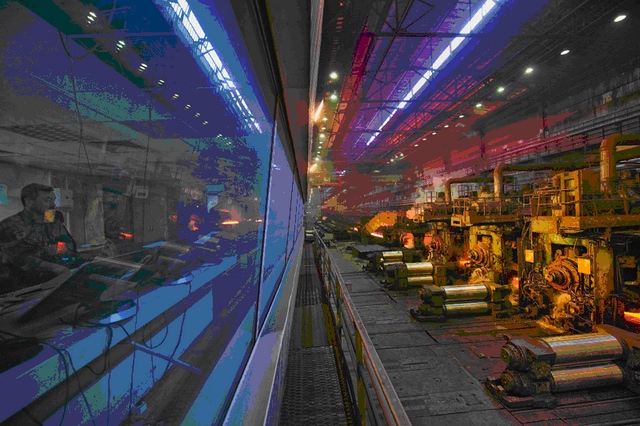
Рисунок 1.2 – Листопрокатний безперервний стан
Основні фірми-виробники прокатних станів на сьогоднішній день – Siemens-VAI, Danieli, Sket, SMS-Demag.
Одним із яскравих прикладів такого сучасного прокатного стану є стан 390 Макіївського філіалу Єнакіївського металургійного заводу – один з самих передових, по оснащеності та організації виробництва, станів в Україні.
2. Опис середньосортного стану 390
Сортопрокатного стан 390 Макіївського філіалу Єнакіївського металургійного заводу призначений для випуску профілів різного типорозміру з вихідних заготовок перерізом 150х150 мм і 125х125 мм, що мають довжину до 12,0 м [4]. Загальна довжина табору становить 500 м, він складається з 18 робочих клітей дуо з індивідуальним приводом, у тому числі 8 горизонтальних, 4 вертикальних і 6 комбінованих клітей, а також ряду іншого технологічного обладнання. Максимальна швидкість прокатки на стані – 18 м / с, розрахункова робоча швидкість – від 2,3 до 17 м / с в залежності від прокочується профілерозмірів сортової сталі. Стан оснащений автоматизованими системами регулювання та управління режимами прокатки і роботою технологічних агрегатів, механізмів і пристроїв, а також промисловими телекамерами огляду невидимих оператору зон і ділянок, технологічної лінії, монітори яких встановлені на відповідних постах управління.
Сортамент стану дуже різноманітний: передбачається випуск круглого (діаметром 12..60 мм), квадратного (14..45 мм), шестигранного (з діаметрами вписаного кола 14 .. 48 мм) перетинів, рівнополочні (від 25х25х3...4 до 63х3х4...6) і полками (від 45х28х3...4 до 63х40х4...8) куточків, швелерів (№ 5,0, № 6,5, № 8,0) і т.д. [4].
Високий рівень автоматизації, а також використання передових технологій дозволяє випускати на годину до 120 т готової продукції. Всі технологічні машини, встановлені на таборі, виконують рівно свою незамінну функцію, і є ланками одного великого ланцюга, що має свій початок на ділянці завантаження блюмів, де пратцен-крани вантажать холодні заготовки на завантажувальні решітки, і кінець – на ділянках упаковки і вантаження готового прокату.
Схема розташування устаткування стану 390 Макіївського філіалу Єнакіївського металургійного заводу наведена на малюнку 2.1.
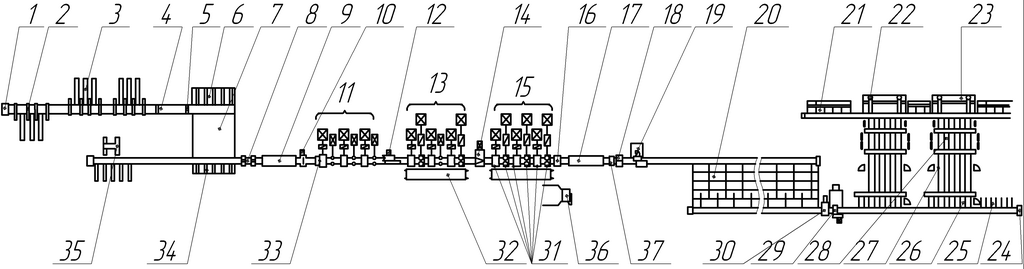
Рисунок 2.1 – 1 – нерухомий упор; 2 – стелаж шлюбу заготовок; 3 – завантажувальна грати; 4 – рольгангові ваги; 5 – опускающийся упор; 6 – зштовхувачі; 7 – нагрівальна піч; 8 – пристрій для гідрозбиву окалини; 9 – тунель-термостат; 10 – трайбаппарат перед 1-й кліттю; 11 – чорнова група клітей; 12 – кривошипно -важільні ножиці; 13 – проміжна група клітей; 14 – кривошипно-важільні ножиці; 15 – чистова група клітей; 16 – прилад для вимірювання геометричних розмірів; 17 – ділянка прискореного охолодження; 18 – двосистемні ножиці; 19 – кривошипний крошітель; 20 – рейковий стелаж; 21 – мостові ваги; 22 – в'язальна машина; 23 – поперечний транспортер; 24 – стаціонарний упор; 25 – накопичувач немірних прутків; 26 – ланцюговий транспортер 1; 27 – ланцюговий транспортер 2; 28 – дозатор; 29 – летючі ножиці холодної різання ; 30 – правильна машина; 31 – петлерегулятори; 32 – пристрої для зміни клітей; 33 – розривні ножиці; 34 – машина знімання заготовок; 35 – зштовхувачі; 36 – бракомоталка; 37 – трайбапарат
Заготовки, підготовлені для прокатки на стані, подаються пратцен-кранами (рис. 2.2) зі складу заготовок, і укладаються в один шар на одну з двох завантажувальних решіток 3, звідки кулачками рейкового шлеппера транспортуються до перекладати пристрою.
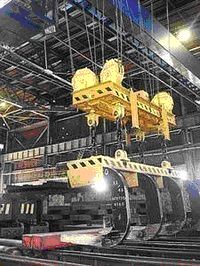
Рисунок 2.2 – Пратцен-кран
Перекладаємо пристроєм заготовки поштучно передаються на підвідний рольганг, якими транспортуються до нагрівальної печі (рис. 2.3). На третій секції підводить рольгангу заготовки зважуються на рольгангові вагах 4; фіксоване положення заготовки на ділянці ваг забезпечується опускається упором 5.
Браковані заготовки подводящим рольгангом подаються в протилежну від печі сторону до стаціонарного упору 1 і зштовхувачі передаються на решітку-стелаж 2.
Нагрівання заготовок до температури прокатки проводиться в методичній комбінованої печі 7 з водоохолоджуваними балками; подача і розвантаження заготовок здійснюється за допомогою внутріпечних роликів. Піч виконана за принципом крокуючої; нагрів заготовок відбувається за допомогою згоряння газу.
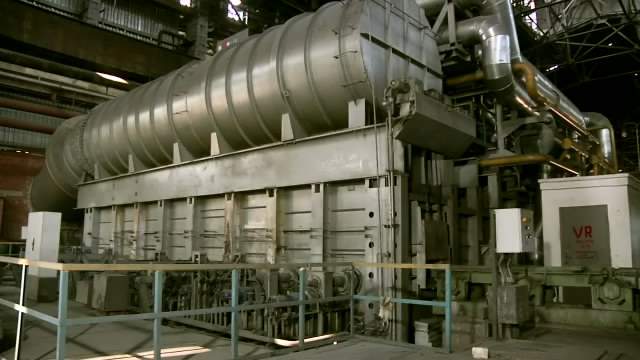
Рисунок 2.3 – Нагрівальна піч з крокуючими балками
При аварійній ситуації на таборі, пов'язаної з припиненням процесу прокатки, або в разі необхідності розвантаження печі, нагріті заготовки з рольганга вивантаження 34 транспортуються по відвідного рольганга в протилежну від табору сторону до стаціонарного упору і Штовхувачі 35 передаються на стелаж, звідки після охолодження прибираються пратцен- краном.
Гаряча ж заготовка, при попаданні на основну технологічну лінію, надходить у тунель-термостат 9 (забезпечує мінімальне падіння і вирівнювання температури заготовки перед першою кліттю), звідки трайбаппаратом 10 подається в першу кліть.
Перед першою кліттю встановлені розривні ножиці маятникового типу 33, які при виробничої необхідності або в аварійних ситуаціях виконують ділильний різ і запобігають подальшу подачу заготовки в чорнову групу. При цьому переміщення верхнього і нижнього ножів з вихідного положення до контакту з гранями заготовки здійснюється пневмоприводом, а подальше їх впровадження в метал – за рахунок тягнучого зусилля першої клеті.
Прокатка сортових профілів на стані здійснюється в трьох групах клітей (рис. 2.4):
- чорнової 11, що складається з однієї горизонтальної й однієї вертикальної клітей 600, двох горизонтальних, і двох вертикальних клітей 440, з чергуванням горизонтальних і вертикальних клітей в групі;
- проміжної 13, що складається з трьох горизонтальних і двох комбінованих клітей 390, і одній вертикальній кліті 390; горизонтальні кліті чергуються з комбінованими і вертикальної клітями;
- чистової 15, що складається з двох горизонтальних і чотирьох комбінованих клітей 390; горизонтальні кліті чергуються з комбінованими.
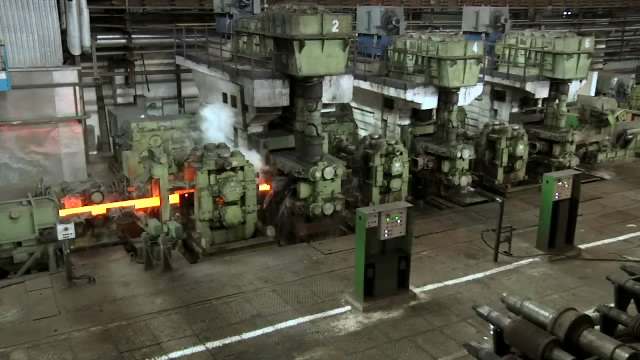
Рисунок 2.4 – Участок клетей
У чорнової і проміжної групах прокатка ведеться без кантування розкату з мінімальним натягом його між клітями, яке автоматично підтримується системою регулювання мінімального натягу.
На кривошипно-важільних ножицях 12 і 14 (рис. 2.5) після чорнової та проміжної груп проводиться обрізка передніх, і, при необхідності, задніх кінців розкату, а також аварійна порізка на мірні частини.
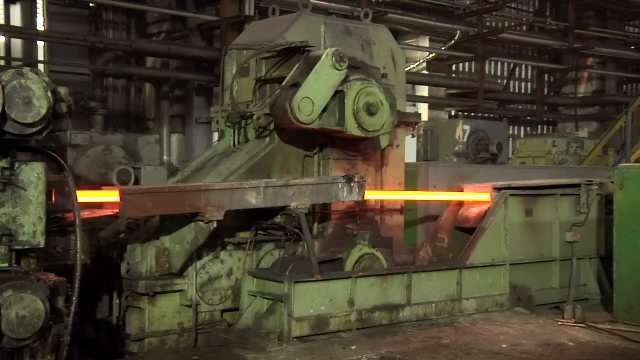
Рисунок 2.5 – Кривошипно-важільні ножиці
В чистовій групі прокатка здійснюється з використанням системи петлерегулірованія. Величина петлі підтримується автоматично петлерегуляторамі 31 (рис. 2.6), що використовують при роботі імпульси від фотоелектричних датчиків положення петлі.
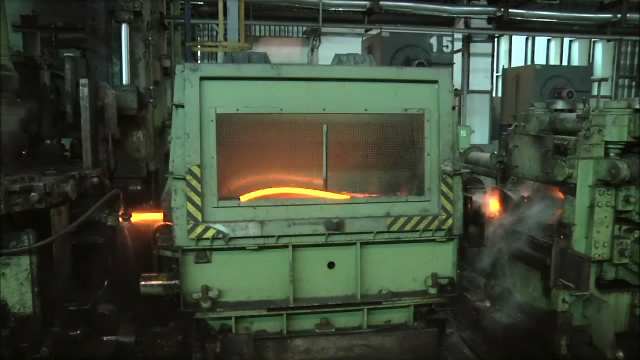
Рисунок 2.6 – Петлерегулятор
Робочі кліті, невживані в процесі прокатки, видаляються з потоку табором, а на їх місце встановлюються спеціальні жолоби.
Готовий прокат, після контролю геометричних розмірів, транспортується в установку прискореного охолодження 17, що забезпечує зниження підвищення міцнісних властивостей металу.
При виробництві профілів, не піддаються прискореному охолоджуванню, замість секцій охолоджуючих труб в лінію табору вводяться відповідні секції рольганга.
Термозміцнення або гарячекатаний прокат подається трайбаппаратом до двосистемних стоп-стартовим ножицям 18, на яких виробляється розкрій його на штанги заданої довжини, які транспортуються на холодильник подводящим рольгангом.
Гальмування смуг готового прокату здійснюється на приймальному рольгангу холодильника системою подвійних підйомних клапанів (розділових перегородок і клапанів).
Сам холодильник являє собою систему з крокуючих рейок 20, перекладають охолоджуваний прокат в поперченного напрямку по мірі надходження заготовок (рис. 2.7).
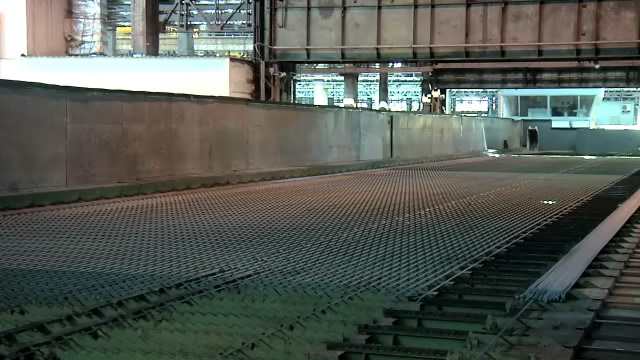
Рисунок 2.7 – Холодильник з крокуючими балками
Прокат після рейкового стелажа надходить на передавальне пристрій, на збірних ланцюгах якого формуються шари прокату з певною кількістю штанг і кроком розкладки, які передаються потім на відвідний рольганг холодильника.
На відвідному рольганге шар фасонного прокату торцюється по переднім кінцях за допомогою опускається упору і подається до многоручьевим правильній машині 30. Потім, головна частина шару прокату, після правильної машини, надходить по рольгангу до летючим ножиць холодного різання 29 (рис. 2.8), на яких виробляється обрізка передніх кінців прутків прокату на готові довжини. При цьому правильна машина і летючі ножиці холодної різання працюють у синхронному швидкісному режимі.
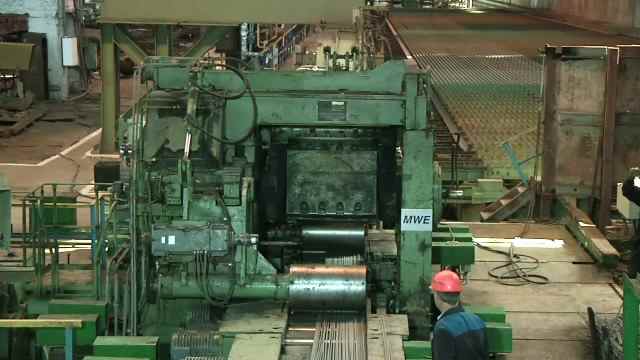
Рисунок 2.8 – Ножиці № 55 холодною порізки прокату
При виробництві простих профілів, які не потребують редагування, правильна машина виводиться з потоку і на її місце вводиться секція рольганга. У цьому випадку шар прокату з відвідного рольганга подається безпосередньо до летючим ножиць холодного різання. Обрізка кінців шару прокату і розкрій на ножицях холодної різання прокату проводиться в автоматичному режимі.
Шари прутків готової довжини після порізки на летючих ножицях холодної різання транспортуються на ділянку обробки.
Потім, залежно від профілю та вимог замовника, прокат транспортується по транспортерах 26 і 27 в зону упаковки, де може бути зібраний в зв'язки або штабеля за допомогою в'язальних машин 22 (рис. 2.9).
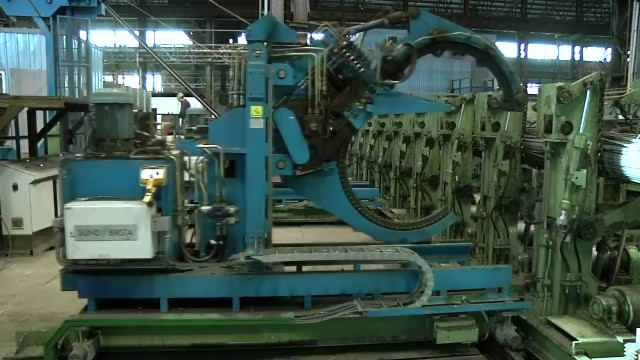
Рисунок 2.9 – В'язальна машина
Пакет або штабель готового прокату зі збірною решітки передається цеховим краном на склад готової продукції або на завантаження в вагон.
Все обладнання табору – унікальне, повністю ідентичних машин не випускається, що є однією з характерних ознак металургійного виробництва. Аварійний вихід з ладу навіть однієї з машин тягне за собою аварійну зупинку всього технологічного комплексу, що, враховуючи специфіку виробництва, створює серйозну проблему як економічного, так і практичного характеру, оскільки температура нагрітого металу досягає 1400 ° С. При проектуванні табору намагаються врахувати можливість аварійної зупинки і передбачити різні варіанти швидкого виходу з подібних ситуацій. Наприклад, при відмові одного з клітей сортопрокатного стана, можна перейти на інший сортамент, і продовжити прокатку, виключивши з роботи вийшла з ладу кліть.
Але, не дивлячись на це, в технологічній лінії прокатних станів є машини, функції яких замінити неможливо. До такого обладнання можна віднести нагрівальну піч, холодильник, а також ножиці холодної різання прокату.
При відмові однієї з машин, що знаходяться в технологічному ланцюжку, найбільш серйозну проблему створює гарячий прокат, знаходиться в цей час на лінії. І, якщо в разі відмови, приміром, привода нагрівальної печі, заготовки, які встигли потрапити на підвідні рольганги, продовжують слідувати далі за встановленою технологами програмі, не створюючи небезпеки для персоналу, то в разі відмови ножиць холодної порізки, або холодильника, що знаходяться в кінці лінії, весь гарячий метал залишається на рольгангах і в клітях. Існують методи аварійної розвантаження основної нитки прокатного стану, однак і вони не дозволяють ефективно уникнути наслідків надзвичайних ситуацій.
У зв'язку з цим велика увага приділяється надійності обладнання, шляхом введення резервних машин і дублюючих приводів, як на холодильнику табору 390. Однак, у випадку з ножицями холодної порізки прокату, дублювання і резервування неможливо – механізм синхронізований з правильною машиною і розташований на строго певній відстані від останньої – для забезпечення точного контролю довжини прокату і якості різу. Будь-яка зміна взаємного розташування ножиць і правильної машини, навіть за умови збереження синхронізації, призведе до погіршення якості реза, що неприпустимо. Встановлені в кінці виробничої лінії, вони працюють в режимі частих пусків-зупинок, а також відчувають регулярні ударні навантаження, при резе остившіх заготовок. На відміну від прокатних клітей, навантаження на які досить добре відомі і практично не змінюються [5], ножиці холодної прокатки – набагато більш невивчений елемент технологічного ланцюга, тому що на кожному таборі процес порізки прокату реалізований по-різному, і, відповідно до цього , інформація про завантаженість несучих елементів ножиць, встановлених на одному таборі, не може бути застосовна для аналогічної конструкції, встановленої в іншої виробничої лінії.
У зв'язку з цим, забезпечення і контроль працездатного стану ножиць холодного плющення – одна з найбільш важливих завдань, що стоять перед персоналом прокатного стану.
3. Аналіз конструкцій ножиць для різання прокату
3.1 Класифікація ножиць для різання прокату
Порізка прокату на мірні довжини – достатньо складна і відповідальна задача. При різанні металу відбувається поділ його зрушенням в площині реза ножа. Ніж має передню і бічні робочі грані з кутом загострення і ріжучу кромку. В залежності від геометрії ріжучого інструменту і взаємного розташування передніх граней ножів, ножиці ділять на чотири типи [5].
1 група – ножиці з паралельними ножами – поперечна різка гарячого прокату квадратного, прямокутного і круглого перерізу на блюмінгах, слябінг, заготовочних і сортових станах.
2 група – гільйотинні ножиці з похилими ножами. Використовуються для гарячої та холодної різання листів дрібного профілю пачками.
3 група – дискові ножиці – мають форму дисків і призначені для поперечного (рейки, балки) і поздовжнього (листи) різання.
4 група – ножиці летючі – розрізають смугу по ходу при її русі в гарячому і холодному стані.
Кожна з груп ножиць має безліч варіантів виконання, в залежності від поставлених завдань. Приміром, летючі ножиці можуть мати конструкцію не тільки кривошипних, але і барабанних ножиць, на яких ножі встановлюються на спеціальних обертових барабанах.
3.2 Опис конструкції ножиць № 55 для холодної різки прокату табору 390
Ножиці холодної порізки прокату, встановлені на стані 390 Макіївського філіалу Єнакіївського металургійного заводу, за типом геометрії різального інструменту і взаємного розташування передніх граней ножів, відносяться до четвертої групи – летючі ножиці. Залежно від заданої довжини прокатуваного профілю і швидкості прокатки, рез відбувається кожні 10-20 секунд.
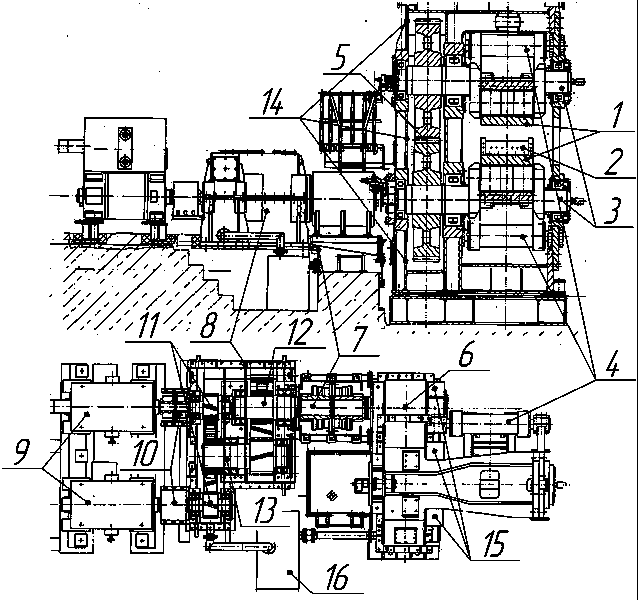
Рисунок 3.1 – Принципова схема ножиць холодної порізки прокату
На малюнку 3.1 приведена схема ножиць. Рез відбувається завдяки плоскопараллельной руху супортів 1, в кожному з яких закріплений нож 2. Ножі, в залежності від сортаменту прокату, мають різний вид різальної крайки, і можуть замінюватися при необхідності. Супорти кріпляться в колінах трехопорное колінчастих валах 3, і мають можливість вільно обертатися на них, завдяки посадці з зазором. Плоскопараллельное рух ножа забезпечується системою важелів балансира 4, з'єднується з ножовим супортом.
Механічна синхронізація валів здійснюється за допомогою зубчастої передачі 5, з передавальним відношенням 1:1. Зубчасте колесо нижнього колінчастого вала, крім того, входить в зачеплення з приводний шестернею 6. Вал останньої допомогою муфти 7 з'єднаний з двоступінчастим редуктором 8.
Механизм приводится в движение двумя синхронизированными, и, по необходимости, дублирующими друг друга, двигателями постоянного тока 9 мощностью 620 кВт каждый. Двигатели, через муфты 10, соединяются с редуктором, имеющий два входящих вала-шестерни 11 и один выходной вал 12. Входные валы приводят в движение промежуточный вал 13, имеющего зацепление с зубчатым колесом выходного вала. Все зубчатые передачи выполнены как косозубые. Общее передаточное отношение от двигателя к коленчатым ножам составляет 14,07.
Механізм приводиться в рух двома синхронізованими, і, за необхідності, дублюючими один одного, двигунами постійного струму 9 потужністю 620 кВт кожний. Двигуни, через муфти 10, з'єднуються з редуктором, що має два вхідних вала-шестерні 11 і один вихідний вал 12. Вхідні вали приводять в рух проміжний вал 13, що має зачеплення із зубчастим колесом вихідного валу. Всі зубчасті передачі виконані як косозубі. Загальне передавальне відношення від двигуна до колінчастим ножам становить 14,07. Корпус ножиць являє собою трикомпонентну структуру станин 14, на стиках яких розташовані колінчаті вали і вал-шестерня. Станини з'єднуються між собою стяжними болтами М90 15.
Змащення вузлів тертя здійснюється за допомогою маслостанції 16.
Всі компоненти ножиць постійно піддаються значним ударним навантаженням, тому вимоги до якості виконання всіх складових дуже високі. При наявності в механізмі яких або конструктивних недоліків, або похибок при монтажі, короткочасний вплив динамічних сил провокує розвиток серйозних дефектів фундаментальних і дорогих елементів.
Фізично, в момент різу, відбувається повний перерозподіл сил в механізмі, за рахунок розмикання зазорів зубчастих передач і підшипникових опор, що створює передумови для додаткових динамічних ударів. Такі процеси негативно позначаються на стані конструктивних елементів, і потребують додаткових досліджень, для контролю технічного стану ножиць.
Розбірні методи контролю технічного стану є економічно невигідними, тому що вимагають повної зупинки роботи ножиць, і як наслідок, всього табору, що неприпустимо в умовах безперервного виробництва. Проте, для отримання інформації про стан елементів механізмів, існують методи неруйнівного контролю. Найбільш оптимальним і інформативним методом з них, на даний період часу, є віброметрія [6].
4. Огляд методів віброметрії
4.1 Вимірювання вібрації
Для механізмів роторного типу (електродвигуни, насоси, вентилятори, турбіни, генератори і т.д.) широке поширення в усьому світі отримали методи контролю, що базуються на вимірюванні параметрів вібрації. Обумовлено це тим, що вібрація є наслідком дії яких-небудь сил в самому механізмі, і відповідно сигнал вібрації несе в собі інформацію про стан механізму, його кінематичних зв'язків і окремих вузлів. При цьому теорія і практика аналізу вібросигналів до теперішнього часу настільки відпрацьована, що можна отримати достовірну інформацію практично з будь-якого дефекту монтажу, виготовлення або зносу [8].
Трьохкомпонентна модель розповсюдження механоакустіческого сигналу за механізмом, прийнята за основу в теоретичному контексті методів віброметрії, описана в роботах Ю.І. Іоріша [8], А.С. Гольдіна [9], А.Б. Капранової [10]. Відповідно до неї, об'єкт, до якого прикладається зовнішня сила, володіє масою, коефіцієнтом демпфування і коефіцієнтом жорсткості, в залежності від значення яких відбувається та чи інша ступінь загасання механічних коливань в матеріалі механізму.
Вимірювання вібрації в машинах роторного типу регламентується нормативно-технічною документацією [11, 12]. У зазначених стандартах описуються методи вимірювання вібраційного сигналу, наводяться вимоги до вимірювальної апаратури, регламентуються місця установки датчиків і вказується межі зон технічного стану для типового роторного устаткування.
Однак, застосовність державних стандартів обмежена для ряду обладнання, в тому числі, до машин, що працюють в умовах металургійного виробництва, що освітлено в роботі [13]: Дані рекомендації незастосовні до важконавантажених низькошвидкісних машинам великої маси, металорізальних верстатів, обладнання, установленого на податливому підставі. Нормативи для такого обладнання можуть бути визначені експериментально або розрахунковим шляхом при моделюванні несправних станів
.
У роботах [14, 15, 16, 17] наведено можливі рішення розпізнавання технічного стану механічних систем, що працюють в тривалому режимі. Універсальність методів віброметрії дозволяє вирішувати різноманітні завдання, стосовно до великого переліку обладнання.
Дослідження [18] вказує на тісний взаємозв'язок коливальних процесів, вібрації, швидкісних режимів з параметрами електроприводів механічного обладнання. Параметри двигуна можуть бути одним із ключових діагностичних ознак визначення технічного стану системи.
Серед різноманіття рішень питань забезпечення надійності устаткування, проте, практично відсутні методики оцінки стану машин, що працюють в режимах перехідних процесів [13]. При цьому обладнання прокатних станів, що має напружений циклічний режим роботи, динамічний і близький до ударному режим роботи, відноситься саме до такої категорії машин [19].
Питання динаміки прокатних станів неодноразово піднімалися в процесі розвитку металургії. На малюнку 4.1 представлений графік появи робіт, що стосуються аналізу динамічних процесів на прокатних станах, починаючи з 1960 року.
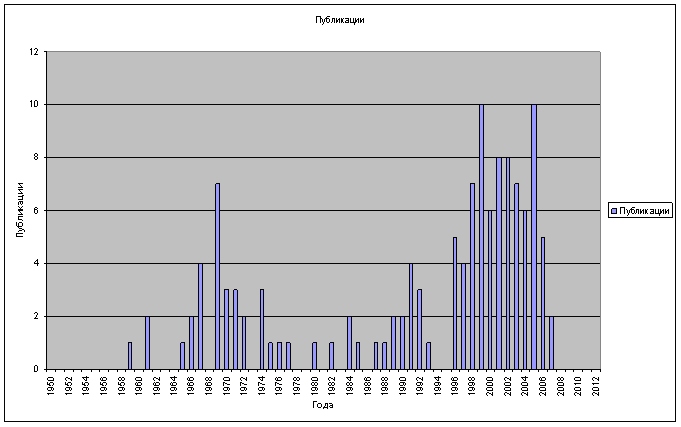
Рисунок 4.1 – Графік інтенсивності появи публікацій матеріалів на тему динаміки прокатних станів
Найбільший стрибок у дослідженні динамічних процесів на прокатному стані пройшов в 1998-2004 роках. Даний період характеризується переходом промислових підприємств на режим ринкової економіки, коли питання про економію фінансових ресурсів встав найбільш гостро. Решта періоди сплесків публікацій в цьому напрямку пов'язані, насамперед, з появою нових досягнень науково-технічного прогресу, які дозволили розпочати проводити додаткові дослідження, і, як наслідок, призвели до появи літературних видань.
Термін служби багатьох станів обчислюється десятками років. Їх слід віднести до тих складним технічним об'єктам, коли, за словами Б.Є. Патона, технічний огляд їх працездатності вже не може дати реальну картину стану конструкції, так як нормативні параметри її працездатності можуть не збігатися з реальними
[20].
Проблема оцінки технічного стану обладнання прокатного виробництва висвітлена в роботі В.В. Веренева Діагностика та динаміка прокатних станів
[21]: Підтримання працездатності обладнання прокатних станів забезпечується проведенням планово-попереджувальних ремонтів, які є усталеною, однак, застарілої практикою технічного обслуговування. Вона дозволяє продовжувати експлуатацію прокатних станів, несучи при цьому великі витрати на ремонти. Сучасні економічні умови призводять до необхідності впровадження нової стратегії технічного обслуговування
.по фактичному стану
. Поряд з цим потрібні нові рішення щодо визначення технічного стану вузлів і деталей устаткування прокатних станів
Однак, не дивлячись на прогрес в розгляді питань надійності і безвідмовності машин прокатних цехів, практичних підходів до вимірювання вібраційних параметрів ударних процесів до теперішнього часу немає [13].
4.2 Засоби вимірювання
Вимоги до вібровимірювальною апаратурі викладені в нормативно-технічної документації: ГОСТ 30265-95 [22], ГОСТ 25275-82 [23], ГОСТ 4.304-85 [24]. Слід зазначити, що матеріали, викладені в ГОСТ 25275-82 в значній частині застаріли [6].
Номенклатура основних показників внброізмерітельной апаратури (включаючи віброперетворювачі): смуга частот, діапазон вимірювань, коефіцієнт перетворення віброперетворювача, нерівномірність АЧХ, відносний коефіцієнт поперечного перетворення вібропреобразника, нелінійність АХ, число вимірюваних параметрів, коефіцієнт впливу, габаритні розміри, маса, споживана потужність опір ізоляції [6].
Більш докладна класифікація вібровимірювальною засобів наведена в роботі Іоріша Ю.І. [8]. Розробка подібних засобів мала початок ще в середині 20 століття, що висвітлено в ряді робіт [25, 26, 27, 28, 29].
Серед засобів технічного діагностування, використовуваних для діагностування механічного обладнання, за рівнем розв'язуваних завдань і приладової реалізації можна виділити: портативні, аналізатори і вбудовані системи контролю[13].
Портативні – прості показують прилади для визначення загального рівня вібрації обладнання (по СКЗ віброшвидкості), що не має пам'яті і інтерфейсу [30].
Віброаналізатори (збирачі-спектроаналізатори) – багатофункціональні прилади з можливостями визначення амплітудно-частоних спектрів коливань, з реалізацією різних методів отримання інформації про стан устаткування по віброакустіческім сигналам, збору та аналізу діагностичних даних, балансування роторів [30].
Стаціонарні системи – багатоканальні вимірювальні комплекси, призначені для вимірювання, реєстрації та аналізу вібрації контрольованого стаціонарного обладнання [30].
Різні конструкції і типи датчиків для фіксації вібропараметров розглянуті в роботах В.А. Сидорова [13], Б.Л. Геріке [30], Г.Ш. Розенберга [6]. В даний час, для вимірювання параметрів вібрації, використовується 3 типи датчиків: акселерометри – для вимірювання віброприскорення; велосіметри – для вимірювання віброшвидкості; проксіметри – для вимірювання вібропереміщень
.
На даний момент найбільш поширені виробники аналізаторів вібрації – це ДІАМЕХ, віконт, Оргтехдіагностіка, SKF, МІРА, ВАСТ, Вібро-Центр, ІНКОТЕС.
4.3 Методи аналізу вібрації
В даний час існує три основні методи аналізу вібропараметров: аналіз часових реалізацій сигналу, аналіз загального рівня вібрації і спектральний аналіз [13].
Тимчасова форма (рис. 4.2) є базовою для решти методів і включає в себе запис певного діапазону частот параметра вібрації в тимчасовому розрізі [8]. Основні параметри настройки для фіксації тимчасової форми – тривалість запису, діапазон вимірювання та період фіксації значень [13].
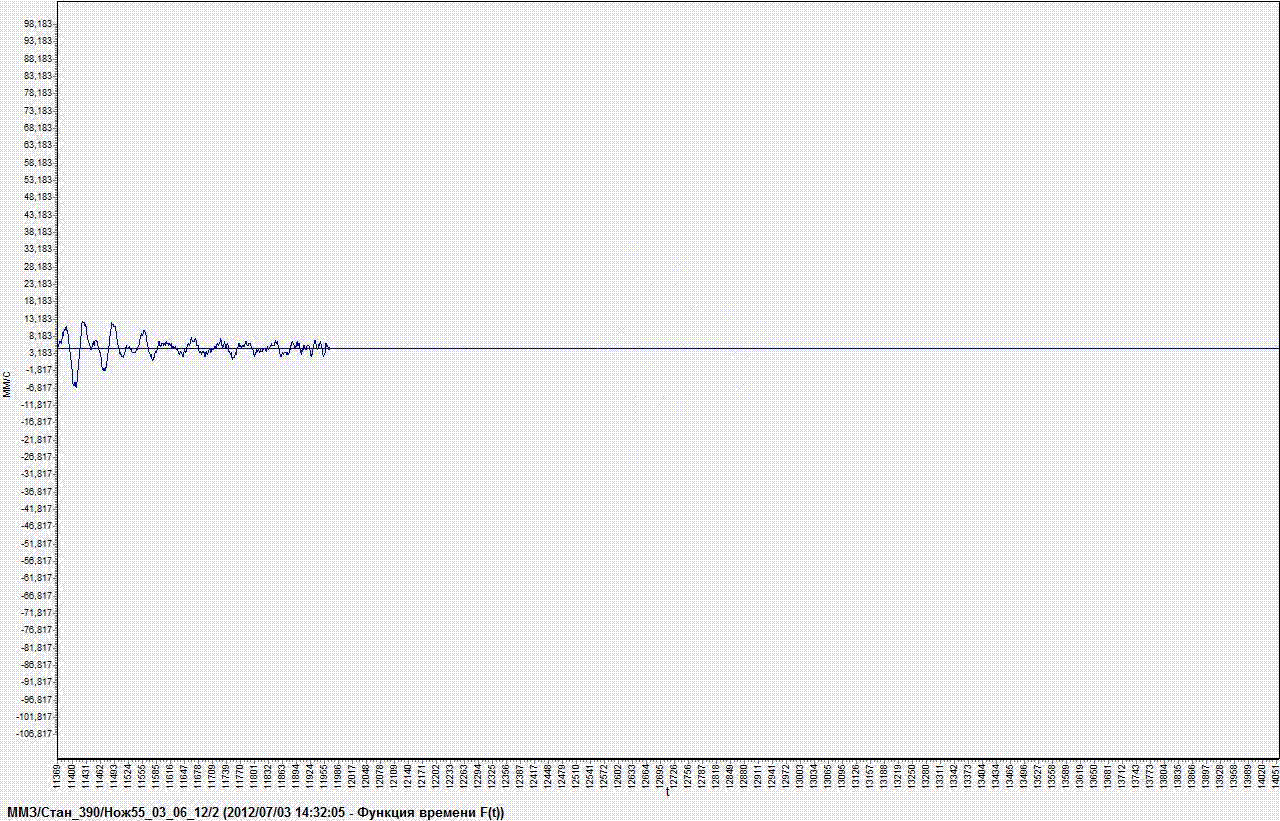
Рисунок 4.1 – Анімований приклад тимчасової реалізації сигналу – ударний процес (зроблено в mp_gif_animator, 111 кБ, 5 кадрів, 0,7 сек затримки між кадрами, 4 цикла повторення)
У роботі В.А. Сидорова [13] наведені діагностичні параметри при аналізі тимчасової реалізації вібраційного сигналу для оцінки технічного стану механізму, що працює з ударними навантаженнями.
- Стабільність, повторюваність процесу. Пошкодження в механічній системі призводять до виникнення випадкових коливань, що відбиваються на конкретних часових реалізаціях.
- Симетричність сигналу.
- Збільшення параметрів вібрації під час найбільш навантаженої роботи механізму в порівнянні з роботою на холостому ходу.
- Характерні параметри процесу загасання коливань механічної системи після зняття навантаження.
- Зміна тимчасової картини при зміні напрямку обертання відображає параметри технічного стану механізму.
Метод аналізу загального рівня вібрації є одним з найбільш шірокоіспользуемих методів завдяки своїй інформативності та низької вимогливості до вібровимірювальною апаратурі. При визначенні значень загального рівня вібрації зазвичай розуміють вимір середньоквадратичного значення віброшвидкості в частотному діапазоні від 10 до 1000 Гц. Це відповідає вимогам стандарту ІСО 10816-97-1 [11]. Для оцінки стану підшипників кочення ефективним є вимірювання пікового і середньоквадратичного значень віброприскорення в більш високих частотних діапазонах [13]. Варто відзначити, що для вимірювання загального рівня вібрації потрібен якийсь усереднення вибірок з тимчасового сигналу.
При визначенні причини вібрації необхідно враховувати напрям вимірювання. Регламентується проведення вимірювань вібрації корпусів підшипників в трьох взаємно перпендикулярних напрямках: вертикальному, горизонтальному й осьовому (рис. 4.3). Вимірювання загального рівня вібрації у вертикальному напрямку проводиться в найвищій точці корпусу. Горизонтальна і осьова складові вимірюються на рівні роз'єму кришки підшипника або горизонтальній площині осі обертання. Вимірювання, проведені на захисних кожухах, металоконструкціях не дозволяють визначити технічний стан механізму через нелінійності властивостей даних елементів [11].
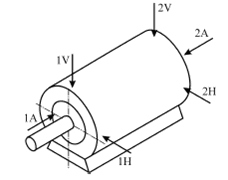
Рисунок 4.3 – Напрямки виміру загального рівня вібрації
У ряді робіт приведені методики аналізу результатів загального рівня вібрації [7-10].
Спектральний аналіз – це метод обробки, що дозволяє виявити частотний склад вібраційного сигналу. Виявлення підвищених амплітуд вібрації на частотах, що збігаються з частотами можливих пошкоджень елементів, резонансних частотах деталей, на частотах протікання робочого процесу допомагає виявити і ідентифікувати несправність на ранніх стадіях зародження і розвитку [13].
Існує два способи опису сигналу вібрації – в тимчасовій області і в частотній (рис. 4.4). Вимірювання на певній частоті дає інформацію про несправність раніше, ніж вимір загального рівня вібрації. При спектральному аналізі використовуються ряд послідовних фільтрів або переміщуваний смуговий фільтр [16].
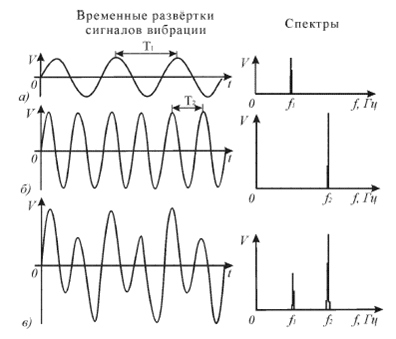
Рисунок 4.4 – Часові сигнали вібрації та їх спектри: а) гармонійні коливання з періодом Т1; б) гармонійні коливання з періодом Т2; в) полігармонічного сигнал
Рішення задач спектрального аналізу можливо при використанні швидкого перетворення Фур'є, що дозволяє визначити значення амплітуд окремих складових спектра вібрації в загальну картину вібрації [33]. Використання математичних методів інтегрування і диференціювання параметрів вібраційного сигналу значно підвищило вимоги до обчислювальному апарату виброаналізатори.
Питаннями аналізу результатів вимірювань вібрації спектральними методами займався ряд авторів [6, 7, 9, 14, 15, 16, 17, 18].
4.4 Вимірювання удару
Складність оцінки стану машин, що працюють в повторно-короткочасному і ударному режимах, полягає у відсутності досить тривалих за часом проміжків рівномірної роботи, що значно обмежує застосовність більшості методів, використовуваних в віброметрії.
Аналіз загального рівня вібрації, спектральний аналіз – виявляється непридатний для таких машин, тому ці методи контролю грунтуються на усередненні і обробці тимчасових проміжків вібраційного сигналу. При цьому інформативність перехідних процесів відома, тому що саме в них проявляються всі приховані дефекти і зароджуються пошкодження машини [13, 14, 35].
Процес удару супроводжується зміною частотних складових сигналу, що залежать від зміни впливу зовнішньої сили, жорсткостей з'єднань, демпфуючих властивостей кожної з деталей. Одним з характерних факторів ударного процесу в механічних системах є деренчання [8]. Деренчання виникає головним чином через люфтів в обертових деталях. При цьому нарівні з піками, наступними хаотично один за іншим, вдається все ж виявити і деякі елементи періодичності, пов'язані з числом оборотів обертових деталей. Однак часто деренчання відбувається абсолютно незалежно від обертання. Наприклад, воно може бути викликане зіткненням гайок і шайб, відгвинтити під час роботи машини через погану зборки. У записі такої хаотичної вібрації ніякої впорядкованості піків зазвичай не буває
.
У ряді робіт було досліджено можливість використання надшвидкого перетворення Фур'є [36, 37], що дозволяє формувати спектрограму при швидкоплинних процесах, використовуючи мінімальну усереднення тимчасового сигналу.
Однак, найбільш ефективним методом аналізу стану механізмів, що працюють під час перехідних процесів, на думку ряду авторів, є аналіз тимчасових реалізацій вібраційного сигналу [13, 38]. Тимчасова реалізація вібраційного сигналу механізму короткочасного режиму роботи може бути охарактеризована двома факторами – поточними позитивними і негативними значеннями амплітуди коливань A,-A і відповідними періодами коливань T
(рис. 4.5).
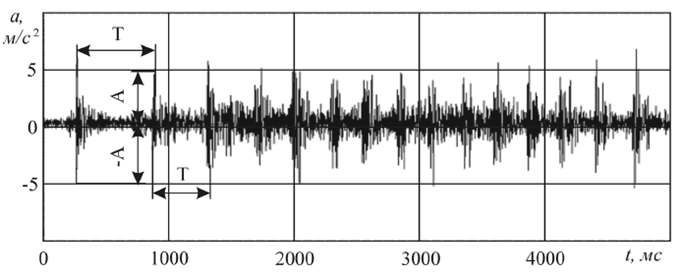
Рисунок 4.5 – Приклад часової реалізації тимчасового сигналу
Результати досліджень перехідних процесів в електро-гідро-механічних системах металургійних машин, включаючи прокатні стани, узагальнені в монографії колективу авторів [39].
Дані аспекти, як базис, використовувала фірма Інкотес
для свого програмного забезпечення Старт / Стоп
[40], за допомогою чого з'явилася можливість фіксувати на обмеженому проміжку часу різні параметри, що мають певну інформативність на перехідних процесах. Програма дозволяє обробляти сигнал тривалістю до 16 секунд, з інтенсивністю до 32768 точок за 16 секунд, з частотним діапазоном від 0 до 16000 Гц, і можливістю зняття до 500 спектрів за період вимірювання. Серед вимірюваних параметрів присутні діаграми Боде, Найквіста, поточна траєкторія руху поверхні, вейвлет аналіз.
Не дивлячись на всі свої достоїнства, інформація, отримана за допомогою програми фірми Інкотес
, на даний момент не може бути ключовою при оцінці технічного стану обладнання на перехідних процесах, тому що відсутня достатня експериментальна і теоретична база застосовності використовуваних методів. У тому числі відсутня універсальна методика обробки часових реалізацій вібраційного сигналу, що робить створення нормативів для оцінки параметрів допоміжних методів вимірювання перехідних процесів неефективним.
5. Вибір напрямку подальших досліджень
Віброметри, як один з методів неруйнівного контролю – найбільш розвинений і інформаційно ємкий для оцінки технічного стану роторних машин будь-якого типу, в тому числі і ножиць холодної порізки прокату № 55. Однак, даний механізм працює в режимі частих зупинок і пусків, і, до того ж, відчуває сильні ударні навантаження.
Використання методик оцінки загального рівня вібрації і спектральний аналіз не допустимо в таких умов, тому в обох випадках тимчасової сигнал перед обробкою усереднюється, і тому ці методи не здатні надати інформацію про технічний стан. При цьому, швидкоплинні динамічні процеси є ключем для вирішення цього завдання – адже саме в ці періоди механізм відчуває пікові напруги, максимально виявляючи всі свої недоліки і дефекти в конструкції.
Використання вейвлет аналізу, інформації про траєкторії руху під час пусків-вибіг також не ефективно, тому що на даний момент відсутня підходяща теоретико-практична база для оцінки технічного стану машин цими методами.
Для розвитку даних напрямків вібродіагностики, на даний період часу, є необхідність формалізувати тимчасові вибірки вібраційного сигналу.
У зв'язку з цим, метою даної роботи є складання методики та критеріїв оцінки технічного стану машин, що працюють в режимі частих перехідних процесів, методом аналізу вібраційного тимчасового сигналу.
Задачі, які необхідно вирішити в даній роботі:
- Проаналізувати існуючі дефекти на ножицях, і зіставити їх з виміряними на машині тимчасовими вібраційними вибірками.
- Вивести математичну залежність поширення механічних коливань при перехідних процесів, при наявності і відсутності зазорів в механізмі.
- Постановка та проведення експерименту, який включає фіксацію ударного процесу, і зміна його параметрів при різних початкових умовах.
- Аналіз і систематизація отриманих даних, складання висновків.
При написанні даного реферату магістерська робота ще не завершена. Остаточне завершення: грудень 2013 року. Повний текст роботи та матеріали по темі можуть бути отримані у автора або його керівника після зазначеної дати.
Перелік посилань
- Металлургические мини-заводы: Монография / М 54 Смирнов А.Н., Сафонов В.М., Дорохова Л.В., Цупрун А.Ю. – Донецк: Норд-Пресс, 2005. – 469 с.
- Минаев А.А. Совмещенные металлургические процессы: Монография – Донецк: Технопарк ДонГТУ УНИТЕХ, 2008. – 552 с.
- Торопов А.С. и др. Охрана труда при монтаже технологического оборудования. М. Стройиздат, 1987 г. – 286 с.
- Стан 390. Техническая документация
- A. И. Целиков, П. И. Полухин, В. М. Гребеник и др. Машины и агрегаты металлургических заводов. В 3-х томах. Том 3. Машины и агрегаты для производства и отделки проката. Учебник для вузов. – 2-е изд., перераб. и доп. – М.: Металлургия, 1988. – 680 с.
- Розенберг Г.Ш., Мадорский Е.З. и др. Вибродиагностика Монография. / СПб.: ПЭИПК, 2003. – 284 с.
- Кравченко В.М. Техническое обслуживание и диагностика промышленного оборудования. – Донецк: ООО
Юго-Восток, Лтд
, 2004. – 504 с. - Иориш Ю.И. Виброметрия М.: Государственное научно-техническое издательство машиностроительной литературы, 1963. – 756 с.
- Гольдин А.С. Вибрация роторных машин: – 2-е изд. исправл. – М.:Машиностроение, 2000 – 344 с.
- Основы теории механических колебаний, Капранова А.Б., Зайцев А.И. – Ярославский государственный технический университет, 1999. – 112 с.
- ГОСТ 20815-93
Машины электрические вращающиеся. Механическая вибрация некоторых видов машин с высотой оси вращения 56 мм и более. Измерение, оценка и допустимые значения
. - ГОСТ ИСО 10816-1-97
Вибрация. Контроль состояния машин по результатам измерений вибрации на невращающихся частях. Часть 1. Общие требования
. - Кравченко В.М., Сидоров В.А., Седуш В.Я. Техническое диагностирование механического оборудования: Учебник. – Донецк: ООО "Юго-Восток, Лтд", 2009. – 459 с.
- Биргер И. А. Техническая диагностика. – М.: Машиностроение, 1978. – 240 с.
- Артоболевский И. И., Бобровницкий Ю. Н., Генкин М. Д. Введение в акустическую диагностику машин. – М.: Наука, 1979. – 296 с.
- Голуб Е. С., Мадорский Е. З., Розенберг Г.Ш. Диагностирование судовых технических средств: Справочник. – М.: Транспорт, 1993. – 150 с.
- Коллакот Р. А. Диагностирование механического оборудования. – Л.: Судостроение, 1980. – 281 с.
- Борисенко В. Ф., Сидоров В. А., Мельник А. А. Подходы к оценке состояния электромеханических систем / Наукові праці Донецького національного технічного університету. Серія:
Електротехника і енергетика
, випуск 79. – Донецьк: ДонНТУ, 2004. – С. 23–26. - Ловчиновский Э. В., Вагин В. С. Эксплуатационные свойства металлургических машин. – М.: Металлургия, 1986. – 160 с.
- Патон Б.Е., О состоянии работ в Украине по технической диагностике промышленного оборудования, конструкций и сооружений. Доклад на 3-м расширенном заседании Технического комитета по технической диагностике и неразрушающему контролю (ТК-78) 27 мая 1999 г. Направление
Техническая диагностика
//Техническая диагностика и неразрушающий контроль
, 1999, №3. – С. 66-68. - В.В. Веренев, В.И. Большаков, А.Ю. Путноки, А.А. Корень, С.В. Мацко. Диагностика и динамика прокатных станов. Монография. Днепропетровск: IMA-пресс. – 2007. – 144 с.
- ГОСТ 30265-95
Варисторы. Метод испытания импульсной электрической нагрузки
. - ГОСТ 25275-82
Система стандартов по вибрации. Приборы для измерения вибрации вращающихся машин. Общие технические требования
. - ГОСТ 4.304-85
Система показателей качества продукции. Аппаратура и приборы для измерения вибрации. Номенклатура показателей
. - Дрейпер Ч. C., Маккей В., Лис С. Измерительные системы, Машгиз, 1960. – 784 с.
- Ушаков А. А. Виброизмерительная аппаратура, Изд. ВВА им. Н. Е. Жуковского, 1948. – 288 с.
- Кlotter К. – Messung mechanischer Schwingungen, Berlin, 1943.
- Messung mechanischer Schwingungen,
Richtlinien VDI
, 205—210, 1956. - Steuding H. Messung niechanischer Schwingungen, Berlin 1928.
- Герике Б.Л., Абрамов И.Л., Герике П.Б. Вибродиагностика горных машин и оборудования. Учебное пособие / Кузбасский государственный технический университет 2007. – 168 с.
- Седуш В. Я., Сидоров В. А., Ошовская Е. В. Контроль технического состояния металлургических машин по виброакустическим параметрам. Сб. научн. трудов. – Алчевск: ДГМИ, 2000. – Вып. 12. – С. 213–218.
- Сидоров В. А., Куватов А. В., Куришева Е. П. Анализ временных реализаций вибрационного сигнала / Научно-технический и производственный сборник статей
Вибрация машин: измерение, снижение, защита
. – 2005. – № 2. – С. 10–14. - Основы анализа данных и поиска неисправностей. By Glenn D. White, DLI Engineering Corporation. Пер. с англ. – Шейняк И. Р. / под ред. Смирнова В. А. Vibrashion.ru\Основы анализа.htm
- Преобразование Фурье и классический цифровой спектральный анализ. Медведев С.Ю., к.ф., м.н. [Электронный ресурс]. – Режим доступа: http://www.vibration.ru/preobraz....
- Электромеханические системы автоматизации стационарных установок (под общ. редакцией проф. Борисенко В.Ф.). – Донецк: ДонНТУ, НПФ
МИДИЭЛ
, – 2005. – 459 с. - Вэйвлеты в вибрационной динамике машин. А.И. Прыгунов [Электронный ресурс]. – Режим доступа: http://www.vibration.ru/wavelet....
- Добеши И. Десять лекций по вэйвлетам. Ижевск: НИЦ
Регулярная и хаотическая динамика
, 2001. – 464 с. - Диагностические параметры переходных процессов при оценке технического состояния электромеханических систем. Лытаев А.В., Сидоров В.А. // Автоматизація технологічних об'єктів та процесів / Матеріали ХIІ Міжнародної науково-технічної конференції аспірантів і студентів. – Донецьк, ДонНТУ – 2012, с. 441-443.
- Переходные процессы в электро-гидро-механических системах металлургических машин. Монография / Большаков В.И., Злобинский В.Е., Харлан Б.А., Цехнович Л.И., Яхно О.М. Днепропетровск: 2002. – 324 с.
Старт/Стоп
– измерение и анализ вибрации на переходных режимах, ОООИнкотес
[Электронный ресурс]. – Режим доступа: http://encotes.ru/....