Содержание
- Введение
- 1. Актуальность проблемы и ее связь с научными и практическими задачами
- 2. Анализ существующих технологий и средств механизации выемки маломощных пластов
- 2.1. Комбайновая выемка
- 2.2. Струговая выемка (и различные модификации струга)
- 2.3. Комплексная и агрегатная выемка
- 2.4. Бурошнековая выемка
- 2.5. Комбинированная, не традиционная выемка и др
- Выводы и направления дальнейших исследований
- Заключение
- Список источников
Введение
С момента своего появления и по сегодняшний день горная промышленность непрерывно и интенсивно развивается. К основным этапам ее развития можно отнести следующие [1]:
- безмашинная добыча угля с применением простейших инструментов и приспособлений (начальный этап до 1920 гг.);
- механизированная подрубка пласта врубовыми машинами (1920-1940);
- механизированное разрушение и погрузка угля комбайнами (1940-1960) и стругами (1950-2000);
- полная механизация внутрилавных процессов (1960-2000);
- переход к «безлюдной» автоматизированной технология добычи угля (первые предложения с 1960 -70-х гг. и по настоящее время);
Однако, несмотря на бурное, главным образом, экстенсивное развитие технологии и техники по добыче угля, по сравнению с начальным периодом своего развития (период ручной выемки) современные интегральные показатели работы промышленности не улучшились. Если в начале прошлого века добыча угля на одного трудящегося была 1-2 т/сут, то таковой она осталась и доныне, проявляя явную тенденцию к понижению.
Это объясняется тем, что в настоящее время количество шахт функцио-нирующих на Украине составляет несколько сотен. И на каждой шахте присутствует полный штат необходимых для нормальной работы сотрудников. В то же время средняя добыча с одной лавы редко превышает рубеж в 1000 тонн в сутки. Если на лаве работает три очистных забоя, суммарная производительность шахты составит всего 3000 т/сут. Еще несколько десятилетий назад цифра в 600 т/сут. с лавы считалась рекордной, но сегодня при постоянно возрастающей стоимости на оборудование и необходимые для добычи энергоресурсы, в условиях жесткой конкуренции,
Также на эффективность угледобычи существующих шахт влияют сле-дующие технические проблемы горной отрасли:
1. Основные запасы углей в Донецком бассейне находятся в высокогазоносных пластах с самыми разнообразными горно-геологическими условиями, По основным свойствам углей и вмещающих пород (газоносность, запыл?нность, взрываемость пыли, силикозоопасность, обводн?нность) Донецкий бассейн следует отнести к весьма сложным по разработке.
2. Существующая техника и технология добычи угля на тонких пластах, – комбайновые комплексы с широким и узким захватом, струги, скреперо-струги и др., - во многом исчерпали свои технические возможности, и при существующих условиях не в состоянии обеспечить достаточную производительность.
3. Техногенная и экологическая опасность угледобычи, которая усугубляется с увеличением глубины разработок, неприемлема для современного цивилизованного общества (выбросы угля, породы и газа, взрывы газа и угольной пыли, пожароопасность, обрушения пород, высокие проявления горного давления и горные удары и др.) [2].
Украинской угольной промышленности необходимы серьезные инженерно-технические разработки и предложения по модернизации и созданию новых средств интенсивной выемки тонких пластов. При этом центральное место в технолого-конструкторских разработках должна занимать техника и технология выемки тонких и весьма тонких пластов до (1,0м). Для тонких пластов угля следует искать возможности создания выемочной техники нового технического уровня, стабильно работающей в сложных и изменяющихся горно-геологических условиях с нагрузками из одной лавы не менее 3000-5000 т угля в сутки при обеспечении полной безопасности ведения работ.
Данная задача может быть решена с применением машин и комплексов оборудования с мехатронными системами управления, диагностики и кон-троля.
1. Актуальность проблемы и ее связь с научными и практическими задачами
Основной сырьевой и энергетической базой всех отраслей хозяйства яв-ляется горнодобывающая промышленность. Более 70 % запасов угля в Ук-раине сосредоточены на пластах мощностью до 1,0 метра. Общие запасы, сосредоточенные преимущественно (96,0 %) в Донецком бассейне, оцениваются в 110 млрд. тонн, промышленные - 7,13 млрд. При этом, если в диапазоне мощности от 0,85 м до 1,0 м можно, с большим трудом, найти лаву с удовлетворительными экономическими параметрами работы, то в диапазоне менее 0,85 м их не существует. Если шахта отрабатывает такой пласт, то неминуема попутная добыча породы, так как современное оборудование не в состоянии эффективно работать на пластах 0,6–0,85 м. Некоторые страны не работают на весьма тонких пластах, но для Украины такой подход не приемлем. Поэтому обоснование структуры выемочной машины для интенсивной выемки тонких пластов, является актуальной научной и практической задачей. Эта задача на сегодняшний день частично решена применением струговой выемки.
В настоящее время в угольной промышленности наметилась тенденция снижения добычи угля комбайновым способом из-за исчерпания запасов залежей мощных угольных пластов. По расчетам специалистов, пласты мощностью более 1,2 м будут отработаны в течение 15 лет, 0,8-1,2 м – за 45 лет, а менее 0,8 м – за 110 лет. Поэтому в перспективе придется отрабатывать тонкие (менее 0,8 м) и весьма тонкие (от 0,4 м) пласты, балансовые запасы которых составляют свыше 220 млрд. т до глубины 1800 м, т.е. более двух третей от общих балансовых запасов. Это обуславливает актуальность проведения исследований по данной теме.
2. Анализ существующих технологий и средств механизации выемки маломощных пластов
Под добычей полезных ископаемых понимают извлечение их из недр в результате разработки месторождения. Различают два способа добычи: без изменения и с изменением агрегатного состояния полезного ископаемого. К первому относят добычу твердых полезных ископаемых подземным, открытым и подводным способами; ко второму — подземную газификацию угля[3].
Подземная газификация заключается в том, что каменный или бурый уголь под воздействием химически активных компонентов — кислорода, паров воды и диоксида углерода превращаются на месте залегания в энергетический или технологический газ.
Идея подземной газификации угля, высказанная Д. И. Менделеевым, впервые была реализована в нашей стране, найдены и проверены в разнообразных природных условиях технические решения основ ее практического осуществления. Сейчас этот способ в промышленности не применяется, однако его можно рассматривать как перспективный для отработки забалансовых весьма тонких пластов (мощностью 0,2 м и ниже).
Подземный и открытый способы являются традиционными, освоенными и широко применяемыми. Уголь при таком способе добычи отделяется от массива за счет силового взаимодействия его с исполнительным органом выемочной машины, или иной приложенной к пласту энергии – например гидравлическая добыча; воздействие на пласт резким перепадом температур, или заморозка пласта и др.
Современные способы добычи угля механическим способом с применением выемочных машин непосредственно контактирующих с массивом подразделяется на следующие категории (рис. 2.1):
2.1. Комбайновая выемка; (a,c)
2.2. Струговая выемка (и различные модификации струга); (b)
2.3. Комплексная и агрегатная выемка;(d,e)
2.4. Бурошнековая выемка; (f)
2.5. Комбинированная, не традиционная выемка и др.
2.1. Комбайновая выемка;
Очистной комбайн предназначен для одновременного выполнения двух операций технологического процесса добычи полезного ископаемого: отделение его от массива и дробление на транспортабельные куски, погрузка на забойный конвейер или другое доставочное средство [4].
Требования, предъявляемые к современному очистному комбайну, определяются, с одной стороны, требованиями, предъявляемыми к его отдельным узлам и механизмам, а с другой - требованиями, обусловленными совместной работой комбайна с другими машинами очистного забоя - конвейером, крепью и др.
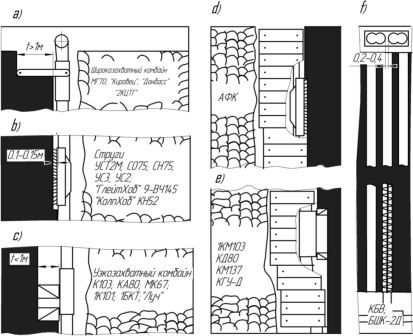
Рисунок 2.1 – Схематическое изображение основных существующих средств механизации очистного забоя при традиционной технологии выемки угля двумя штреками по простиранию.
В настоящее время нет единой классификации очистных комбайнов. Многообразие их конструкций предопределило и многообразие частных классификационных признаков (например, тип исполнительного органа, тип механизма подачи, вид применяемой энергии и т.д.)
Принципиально отличается технология работы комбайна с разной шириной захвата. По ширине захвата комбайны подразделяют на узкозахватные (с захватом до 1м) и – широкозахватные (с захватом более 1 м).
2.1.1. Широкозахватная комбайновая выемка
Врубовые машины
Предшественниками широкозахватных комбайнов являлись врубовые машины (рис. 2.2).
Они использовались для подрубки угля и сланца в сложных горно-геологических условиях [5].Основными недостатками машин такого типа является – минимальная автоматизация очистных работ; - большая доля ручного труда; - переизмельчение угля и работа машины в крайне тяжелых условиях, за счет работы резцов в условиях блокированного реза.
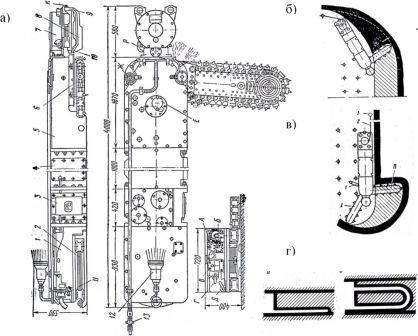
Рисунок 2.2 – Пример работы врубовой машины. а) Врубовая машина «Урал-33»; б), в) виды выполняемых технологических операций; г) основные типы врубов.
В настоящее время машины данного типа на украинских шахтах не применяются.
Широкозахватные комбайны
Приоритет в создании и промышленном применении угледобывающих комбайнов для длинных забоев (лав) принадлежит Советскому Союзу [5].
Первые испытания комбайнов производились в Донбассе уже в 30-е годы ХХ столетия. А в 50-х годах – этот вид выемки получил широкое развитие за счет применения его в составе комплекса и механизации кроме отбойки так же погрузку и транспортирование угля.
Основными широкозахватными комбайнами в свое время являлись:
+ Комбайн МГ-70 (УКМГ-3М) для мощности 0,4-0,6 м;
+ Комбайн «Кировец» для мощности 0,55-0,8 м;
+ Комбайн 2КЦТГ для мощности 0,55-0,75 м;
+ Комбайн «Донбасс» для мощности 0,8-1,6 м.
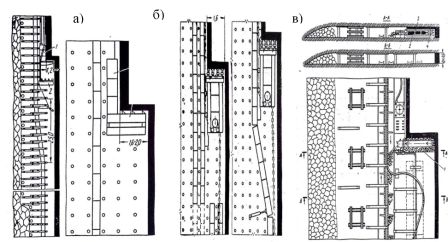
Рисунок 2.3 – Технологические схемы работы широкозахватных комбайнов а) «Донбасс»; б) 2КЦТГ; в) МГ-70.
Основные недостатки машин данного типа: - минимальное использование явления отжима; - большая площадь обнаженного пространства после прохода комбайна и необходимость вручную его крепить; - невозможность управления горным давлением.
Данный тип машин, в настоящее время, так же в Донбассе не применяется.
2.1.2. Узкозахватная комбайновая выемка
Создание и широкое применение начиная с шестидесятых годов узкоза-хватных комплексов очистного оборудования позволило решить задачу управления горным давлением. Внедрение очистных комплексов с узкоза-хватными комбайнами для пологих пластов мощностью от 0,7 до 4,5 м по-зволяло комплексно механизировать почти 3/4 всей подземной добычи угля из очистных работ, увеличить нагрузку на лаву и производительность труда[6].
Современный комбайн имеет ряд достоинств: простую и надежную кон-струкцию; высокую производительность и эффективность, интенсификацию очистных работ; обеспечивает выемку на всю мощность пласта; имеет минимальное измельчение угля и пылеобразование, не высокие удельные энергозатраты; самозарубывается в массив угля и может осуществлять выемку угля на концевых участках лавы без ниш; имеет автоматическое бесступенчатое регулирование скорости, надежную защиту от перегрузок широкую область применения.
Узкозахватные комбайны могут быть:
А) Со шнековым ИО;
Б) С барабанным ИО;
В) С ИО типа бур.
Основными узкозахватными комбайнами для пластов <1м являются:
+ Комбайн К103 для мощности 0,7-1,1 м; (шнек)
+ Комбайн КА80 для мощности 0,8-1,1 м; (барабан)
+ Комбайн МК67М для мощности 0,7-1,0 м; (барабан)
+ Комбайн 1К101 для мощности 0,75-1,2 м; (шнек)
+ Комбайн «Луч» для мощности 0,6-0,8 м; (барабан)
+ Комбайн «1БКТ» для мощности 0,6-0,8 м; (бур)
+ Комбайн УКД300 для мощности 0,85-1,5 м. (шнек)
Существенными недостатками комбайнов на малой мощности являются: - недостаточная погрузочная способность комбайна, из-за невозможности конструктивно обеспечить требуемое сечение окна выгрузки, что приводит к перемалыванию угля как в мясорубке; - меньшая степень механизации, чем при струговой выемке; более сложная конструкция и меньший ресурс; не возможность фактически определить распределение приводной мощности на резание и погрузку; комбайны обладают достаточной длиной, что может вызвать проблемы по вписываемости их в гипсометрию пласта при боковых породах склонных к взбучиванию.
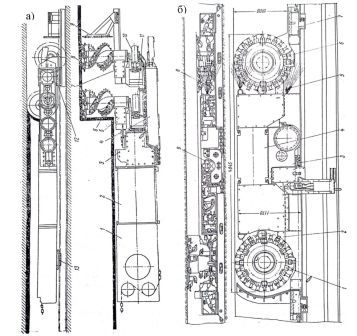
Рисунок 2.4 – Принципиальные схемы узкозахватных комбайнов а)шнекового; б) барабанного.
2.2. Струговая выемка (и различные модификации струга)
Струговая выемка — один из наиболее прогрессивных способов добычи угля. Ее преимуществами являются возможность эффективной механизации выемки из тонких пластов, простота конструкции, хорошая сортность добываемого угля. Наибольшее применение в Украине и за рубежом получили быстроходные зубчатые струговые установки статического действия. Режущий инструмент (резцы) этих установок в результате постоянного прижатия к забою и натяжения тяговой цепи находятся при работе в постоянном (статическом) контакте с разрушаемым массивом угля, снимая стружку угля толщиной 50—150 мм. 0днако область применения таких стругов ограничена [6].
Применение струговой выемки целесообразно при следующих горно-геологических условиях: тонкие и средней мощности (не более 2 м) пласты с крепостью угля не выше средней с ясно выраженным кливажем под углом 5—40° к линии забоя и эффективным отжимом угля под влиянием горного давления; залегание пласта спокойное; кровля не ниже средней устойчивости; почва достаточно плотная, не разрушающаяся при работе струга.
Применение струговой выемки осложняется и даже становится невозможным при наличии в пласте крупных крепких включений колчедана, кварцита, породных прослойков или у кровли пласта крепкого слоя угля, для разрушения которого необходимо предварительное проведение буровзрывных работ, что осложняет организацию работ в очистном забое. Наличие в нижней части пласта крепкого слоя угля (земника) и слабая неровная почва также препятствуют применению струговой выемки.
По сравнению с выемкой комбайнами при струговой выемке лучше сортность угля, ниже удельные энергозатраты и меньше пылеобразование, так как разрушение угля осуществляется крупным срезом (сколом) и ведется в зоне максимального отжима угля;
более безопасные условия для отработки пластов, опасных по газу и пыли и особенно по внезапным выбросам угля и газа;
возможность эффективной выемки весьма тонких пластов мощностью 0,4—0,7 м;
проще схема организации работ по длине лавы; менее сложные средства комплексной механизации и автоматизации производственных процессов в очистном забое.
Кроме того, струговые установки более просты по конструкции и не имеют передачи электроэнергии по силовому гибкому кабелю к движущейся машине.
Учитывая вес эти преимущества, следует во всех случаях, когда позволяют горно-геологические и технические условия, применять струговую выемку угля.
По законам развития техники струговая установка непрерывно развива-лась и модернизировалась. По компоновке и назначению различают следующие виды стругового оборудования:
скреперо-струго-таранные установки в комплекте с индивидуальной крепью для механизации выемки и доставки угля из весьма тонких и тонких пластов мощностью 0,3—0,8 м с углом падения до 900 и некрепкими утлями при боковых породах не ниже средней устойчивости (УС2У и др.);
струговые установки в комплекте с индивидуальной крепью для механизации выемки и доставки угля из тонких и средней мощности пластов (0,6—2,0 м) с углом падения до 35 , с углями не выше средней крепости при боковых породах не ниже средней устойчивости (УСТ2М, С075, СН75, УСБ67М и др.);
струговые очистные комплексы с механизироваными крепями для ком-плексной механизации процессов выемки и доставки угля, крепления и управления я горным давлением из тонких и средней мощности пластов (0,6—2,0 м) с углом падения до 35°, с углями не выше средней крепости, боковыми породами не ниже средней устойчивости (комплексы 1КМС97, 1КМС98, К1МКС и др.). Струговые комплексы — это, по существу, струговые установки с конструктивно привязанными к ним механизированными передвижными крепями;
стругoвые агрегаты, обычно фронтального типа, предназначенные для комплексной механизации очистных работ из тонких и средней мощности пластов с разными углами падения, углями средней крепости, боковыми породами не ниже средней устойчивости (АКЗ, 1АЩМ, 1АНЩ п др.). Агрегат представляет собой комплекс машин, связанных между собой технологически и кинематически, конструктивно соединенных базовыми элементами в единую систему.
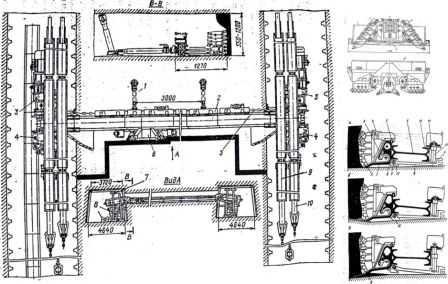
Рисунок 2.5 – Принципиальная технологическая схема работы струговой установки
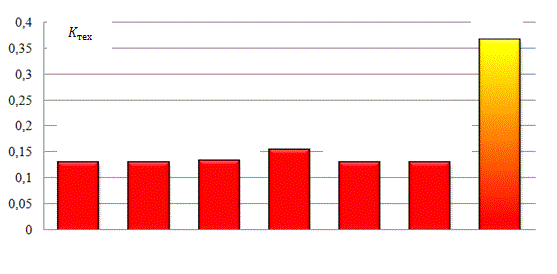
Анимац.1 – Диаграмма значений коэффициента технически возможной неравномерности работы струга при нулевых затратах времени на отдельные операции.
2.3. Комплексная и агрегатная выемка
Очистные комплексы и агрегаты позволяют механизировать и совмещать во времени все основные операции технологического процесса в очистном забое: выемку угля, его доставку, крепление и управление кровлей. Комплексы и агрегаты в зависимости от условий их эксплуатации классифицируют по углу падения пласта, а так же по мощности пластов в соответствии с общепринятой классификацией последних [4].
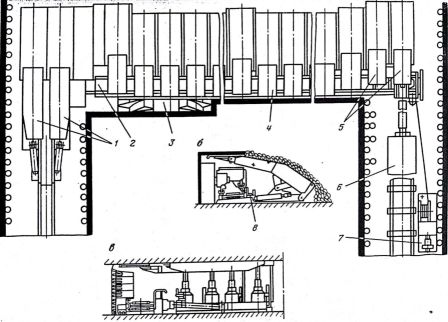
2.6 – Компоновочная схема механизированного комплекса
В состав очистных комбайновых и струговых комплексов (рис 2.6) в за-висимости от типа выемочной машины входят: выемочная машина - очист-ной комбайн 3; доставочная машина - забойный скребковый конвейер 2 (либо при струговом варианте вместо комбайна и конвейера используется струговая установка); механизированная крепь 4; крепи сопряжения забоя с конвейерным (откаточным) / и вентиляционным 5 штреками; насосные станции 6 типа СНУ или СНТ; типовая оросительная система с оросительной установкой 2УЦНС13 и энергопоезд. При работе комплекса по прости- ранию на пластах с углами Падения 9° и выше на вентиляционном штреке устанавливается предохранительная лебедка 7 типа ЗЛП или 1ЛГКН. Все современные комплексы имеют в своем составе кабелеукладчики 8 тракового (КЦН) или барабанного (КБК2) типов. Области применения современных механизированных комплексов определяется областью применения соответствующей крепи и выемочных машин.
В качестве доставочных машин комплексов применяются исключительно забойные скребковые конвейеры, которые выполняют следующие дополнительные функции. Во-первых, став конвейера выполняет функцию общей базы механизированного комплекса, связывающей через домкраты секции крепи и являющейся опорой при их передвижении. Во-вторых, став является направляющей балкой, по которойх перемещается или на которую опирается (на тонких пластах выемочная машина).
Компоновочные схемы агрегатов. Очистные комплексы, обеспечивая механизацию и совмещение во времени операции технологического процесса, не способны работать без маневровых и концевых операций. Технология выемки угля при их применении многооперационна, циклична и требует постоянного присутствия людей в очистном забое. Создание и использование угледобывающих агрегатов позволяет перейти к поточной технологии добычи угля, выемке угля без постоянного присутствия людей в забое.
Для пластов мощностью до метра был разработан модернизированный вариант агрегата (АК-2), и А-2 для отработки пологих пластов мощностью 0,85-1,35 м. Промышленные испытания первых образцов агрегатов на шахтах Кузнецкого и Донецкого бассейнов доказали их работоспособность и правильность новых решений. Дальнейшее развитие структура очистного агрегата получила в конструкции стругового агрегата СА. Решающую роль в развитии агрегатостроения сыграл агрегат А-3. разработанный Гипроуглемашем. В конструкции агрегата впервые был применен многоструговый отбойно-доставочный кольцевой исполнительный орган, замкнутый в вертикальной плоскости.
Недостатки конструкции агрегатов: не достаточная управляемость, низкой эффективность транспортирования отбитого угля вдоль забоя, переизмельчению угля и, как следствие - высокой энергоемкости.
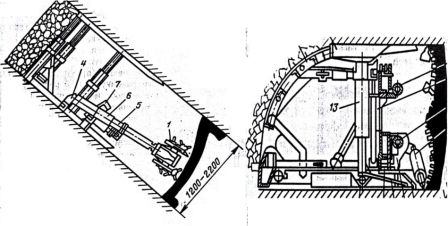
Рисунок 2.7 – Принципиальные схемы некоторых агрегатов
2.4. Бурошнековая выемка
Бурошнековый способ выемки заключается в последовательном бурении скважин диаметром, несколько меньшим мощности пласта, отделенных одна от другой целиками шириной 0,25—0,3 м, без крепления или с закладкой выработанного пространства.
Рабочим агрегатом является двухшпиндельная установка БШУ (рис. 2,8), которая предназначена для выемки угля с сопротивлением резанию до 250 кН/м из пластов мощностью 0,6—0,85 м, залегающих под углом до 15° и имеющих неустойчивые вмещающие породы, где неэффективно применение других средств комплексной механизации очистных работ.
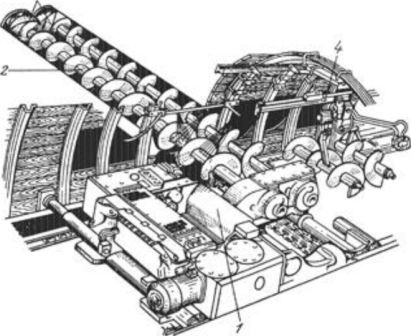
Рисунок 2.8 – Установка БШУ
В штреке может находиться одна или две машины. В первом случае установка бурит скважины как по восстанию, так и по падению пласта.
Одна из возможных технологических схем разработки пласта при панельной подготовке шахтного поля, возвратно-поточном проветривании и последовательной работе двух установок БШУ на один штрек представлена на рис. 2,8.
Размер крыла панели по простиранию порядка 800—1000 м; расстояние между смежными штреками 70—100 м и определяется длиной скважин, на которую способна бурить установка с достаточной степенью надежности (35—50 м).
Для поддержания кровли между скважинами оставляют целики угля шириной 0,25—0,3 м, которые по мере подвигания фронта очистных работ разрушаются. При этом достигается плавное опускание пород кровли.
Основные недостатки бурошнековой выемки: - относительно малая длина буримых скважин, что обусловлено техническим несовершенством установок БШУ; - высокие потери угля в недрах, достигающие 50%; - сложность проветривания и опасность взрыва метана в скважинах.
Дальнейшее совершенствование бурошнековой технологии выемки угля (бурошнековых установок, схем транспортирования с учетом невысокой нагрузки на выемочную выработку, вентиляционных схем и др.) может обеспечить значительный эффект на шахтах с небольшой производственной мощностью при выемке весьма тонких пластов, а именно: высокую производительность труда, низкую фондоемкость производства, ритмичную работу шахты.
2.5. Комбинированная, не традиционная выемка и др.
Были рассмотрены некоторые инновационные предложения д.т.н. проф. Семенченко А.К., д.т.н. проф. Гуляева В.Г. [7] и д.т.н. Литвинского Г.Г. [8], однако анализ предложенных технологических схем не проводился. Схемы могут быть проанализированы в дальнейшей работе.
Выводы и направления дальнейших исследований:
В результате анализа струговых выемочных комплексов на Украине и за рубежом было установлено:
1. При существующих параметрах и обстоятельствах работы стругового комплекса техническая производительность струговых комплексов работающих на Украине составляет всего 10-20% от теоретической;
2. Основными факторами ограничивающими производительность стругового комплекса являются: время на выравнивание искривленной линии очистного забоя; время на передвижку крепи и приводных головок струга и конвейера; перерывы для рабочих, время на пересменку и. др.
3. Расчетным путем было доказано, что сокращение указанных затрат времени позволит в несколько раз увеличить фактическую производительность и вывести ее на уровень 70-80% от теоретической;
4. Потери времени должны быть сокращены за счет максимальной сте-пени параллельности выполнения действий и передачи основных функциональных операций, а так же поддержание прямолинейности забоя, мехатронизированным и мехатронным системам. Должно быть обеспечено отсутствие человека в лаве;
5. Как показывает опыт эксплуатации на пластах от 1м до 1,5м струговые установки реально обеспечивали: 3200 т\сут (ш. «Красноармейская западная», Донбасс), 6200 т/сут (ш. Абашевская Кузбасс), 18 000 т\сут (ш. Проспер-Ханиэль, Германия).
Заключение
Рассмотрены имеющиеся технологии и средства механизации маломощных пластов. Традиционная технология добычи угля не в состоянии обеспечить прибыльную, или хотя бы самодостаточную работу шахт работающих на маломощных пластах.
Были сформулированы следующие требования к выемочной машине:
1. Работа без ниш; (обеспечивается малой длиной комбайна, требуется для его выезда на штрек);
2. Малые затраты мощности на погрузку;
3. Расположение корпуса и ЭД со стороны забоя;(для обеспечения возможности подхвата кровли малым рештаком)
4. Вынесенная система подачи;(снижает длину комбайна и увеличивает мощность резания)
5. Простота конструкции и надежность;
Было показано, что наиболее перспективными средствами выемки тонких пластов является струговая выемка, способная обеспечить интенсивную добычу малых пластов даже при отсутствии человека в очистном забое.
Направлением дальнейших исследований будет разработка математической модели системы механизированная «крепь – кровля – угольный массив» с целью обеспечения мехатронного управления и контроля передвижки крепи. Так же будет исследоваться влияние отжима на угольный пласт, и будет произведена попытка регулировать отжим, изменяя тем самым сопротивляемость угля резанию.
Список источников
- Garry G. Litvinsky. Problem eksploatacji cienkich pokladow w ukrains-kich kopalniach wengla kamiennogo Zaglebja Donieckiego/ Proceeding of the School of Underground Mining- 2002: International Mining Forum, Polish Academy of Science. – Krakow: Nauka-Technika, 2002. – pp. 347-363.
- Грищенко А.Н. Проблемы эргономики при организации и ведении работ на тонких пластах угля. - Уголь Украины, 2000, № 1. С. 32-34.
- Килячков А.П. Технология горного производства: Учеб. для вузов. – 4е изд., перераб. и доп. – М.: Недра, 1992. 415 с.: ил.
- Сафохин М.С. Горные машины и оборудование.
- Яцких В.Г., Имас А.Д. – Горные машины и комплексы.
- Яцких В.Г., Спектр . – Горные машины и комплексы.
- Г.В. Малеев, Ф.В. Костюкевич, В.Г. Гуляев. Фронтальная выемка угля широкими полосами по восстанию и падению // Уголь Украины. – июнь, 1999. – с. 13 – 14.
- Литвинский Г.Г. Агрегат для безлюдной выемки тонких пластов угля // Уголь Украины. – 2006. - № 3. С. 16 – 19.
- Лаврик Г.В., Дюпин А.Ю., Ногих С.Р., Дурнин М.К. Результаты шахтного эксперимента по применению технологии струговой выемки угля в глубоких шахтах Кузбасса // Уголь. – 2006. - №5. С. 26 – 28.
- Фосс Х. –В., Биттнер М. Средства механизации выемкиугля, применяемые в Германии при разработке пластов малой и средней мощности // Глюкауф. – 2003. - № 3. – С. 14 – 19.
- Методика расчета оптимальных параметров струговой установки. Шахты: МУП СССР, 1975. 20 с.