Abstract on the topic of graduation work
Content
- Introduction
- 1. Status of the issue and research objectives
- 1.1 The relevance of additive technologies for the production of engineering products
- 1.2 Features and classification of additive technologies for the manufacture of engineering objects
- 1.3 Types of designs of devices for implementing additive technologies
- 1.4 Goals and objectives of the study
- Findings
- List of sources
Introduction
3D printing is a way to quickly obtain a product from a digital model by applying layers and then combining them with each other. Thanks to this, the 3D printer occupies an important position in the 21st century. The invention and development of the first three-dimensional printing (rapid prototyping system) was carried out by Dr. Hideo Kodama. His greatest creation of the present time was born in the 80s of the 20th century.
The existence of additive technologies began when Charles Hull in 1983 invented and constructed the world's first 3D printer with layering technology using ultraviolet radiation. Hull named this technology as stereolithography.
Quite a lot of time has passed since that moment, and this area received huge worldwide fame and appreciation only in the early 2010s, so nowadays, more than every second knows what 3D printing is. The main feature of 3D technology is, first of all, simplicity and accessibility, which attracts the attention of every interested user.
1. Status of the issue and research objectives
1.1 The relevance of additive technologies for the production of engineering products
3D printing technologies represent a completely different approach to creating products. In this process, there are no such methods of mechanical processing as:
1. turning;
2. Milling;
3. drilling;
4. etc.
Additive technologies have a lot of advantages over traditional production methods for obtaining products.
First is the speed of production. It takes months to manufacture a part of a complex design at the enterprise, when, in turn, 3D technologies allow expanding the possibilities and creating the same part in a certain number of hours.
Secondly, waste-free production. In production, there are a lot of risks and incorrect calculations, which is often the fault of the human factor, due to which, if the parts are incorrectly manufactured, they are defective.
Thirdly, the absence of seams and welded joints.
Additive technologies are a new look at design. There is a constant process of modernization and improvement of technologies, especially such important indicators as: speed, accuracy, quality, strength, durability of the product (fig. 1.1) [1].
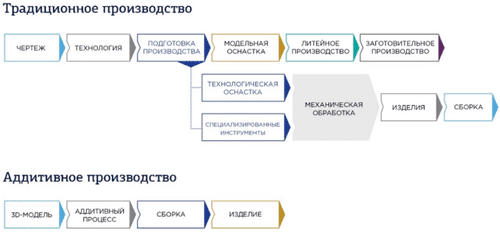
Figure 1 - Technological processes of traditional and additive manufacturing
In Russia, until recently, these 3D technologies did not have much popularity and application, but every day statistics show an increasing growth in this direction. Many enterprises have already begun to intensively apply additive technologies in various industries.
1.2 Features and classification of additive technologies for the manufacture of engineering objects
There are many 3D printing technologies that differ in the method of building a model and their modifications: extrusion, wire, powder, inkjet, laminated, polymerization, but we will focus on the most important and most common.
FDM technology (Fusion Deposition Modeling - in Russian as “layer-by-layer deposition modeling” was developed by Scott Crump and appeared in 1989, is the most common and popular technique for creating models on a 3D printer [2]. The design of the FDM printer includes such elements as: [3]
• extruder;
• nozzle;
• filament feed mechanisms (fig. 1.2);
• desktop (fig. 1.3);
• assembly elements of the table;
• guides;
• stepper motor.
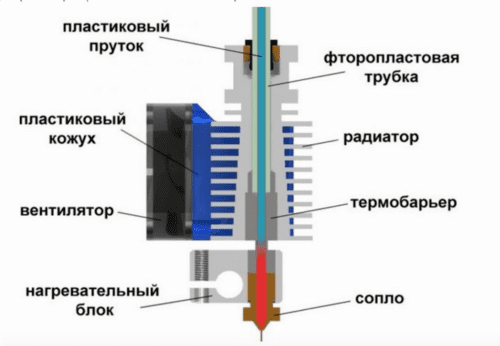
Figure 2 - Elements of the print head
There are modifications of printers that have several extruders in their arsenal, with the help of which it became possible to create several models of different colors at the same time. This method is applicable only for the manufacture of one model in mass production. [4].
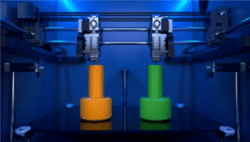
Figure 3 - Printer desktop
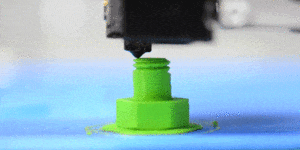
Figure 4 - An example of the operation of the FDM extruder
The printing material (filament) is fed into the extruder where it is heated, and later melted when certain temperature standards are reached for the specific material used from which the future model of the product is created, then it exits through the nozzle to the printer desktop.
The first molten layer of material is squeezed out by a thread and connected to the working surface of the table, after which it is fixed on it. Printing takes place on the principle of layers, starting from the bottom and gradually upwards, in the process of work, a new layer of heated plastic is sintered with the previous one and gradually hardens, this process is repeated layer by layer until the end of printing. To cool the extruder and accelerate the solidification of the filament, coolers are used (Fig. 1.5), which are attached to the extruder, which makes it possible to speed up the process of solidification of the layers of the product [5].
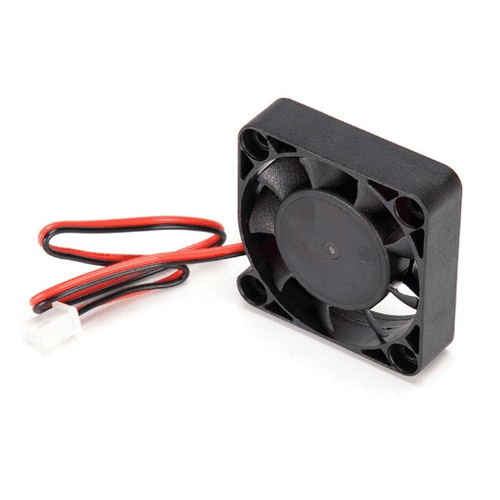
Picture 5 - Cooler cooling
The movement of the printing module of the extruder occurs in the directions of the (Cartesian) coordinate system X, Y, Z, that is, horizontally and vertically. Movement along the axes is carried out by stepper motors that set the movement of the print head and the desktop located on the guides along a given path to create a model [6].
The standard size of the working area of the printer is within 200x200x200 mm, while the industrial one has overall dimensions of 1000x1000x1000 mm. The most characteristic and well-known FDM defect is the deformation of the product, especially when printing with ABS plastic.
To create products with protrusions, it is necessary to resort to the use of supports [7].
FDM also has a wide range of materials to choose from. [8]:
• standard plastics - PLA and ABS,
• engineering - TPU and PETG,
• high strength - PEEK.
Consider the most important and widely used materials everywhere.
PLA (polylactide) is a natural product made from lactic acid found in corn, sugar cane, potatoes and other foods. It has a characteristic pleasant smell.
Tab. 1.1 - Advantages and disadvantages of PLA material
Advantages | Flaws |
The best option for high-speed prototyping; |
Low accuracy of model manufacturing; |
no shrinkage after printing; |
Post-processing required; |
Economical way of production; |
The impossibility of creating hinged structures, due to the lack of supports; |
Good print speed |
fragility; |
Wide range of materials; |
Low temperature resistance; |
It lends itself well to subsequent machining; |
Not durable (product service life 2 years); |
Not toxic; |
Subject to deformation under the influence of sunlight; |
ABS (acrylonitrile butadiene styrene) is a synthetic material and can be easily post-machined to create holes, sand surfaces, as well as chemically to clean the surface of residual plastic elements and smoothing to give the model a glossy look.
Having these advantages, ABS rather involves the use of functional and loaded products for printing. A part made of this filament is capable of operating in the temperature range from -40 to +80 degrees, in various conditions, and has the ability to withstand unfavorable chemical vapors and liquids.
ABS also has quite a few drawbacks, one of them is that it is a synthetic material and when melted, an unpleasant smell is released, which is not useful for the user of the printer.
To avoid problems and get around this problem, you must resort to using a printer with a closed working area. In this case, the part will cool much more slowly, and significant shrinkage will not be noticeable, but the design of such a printer is more complicated and its cost is higher.
Tab. 1.2 - Advantages and disadvantages of ABS material
Advantages | Flaws |
Strength; |
toxic; |
Durability; |
material shrinkage; |
heat resistance; |
Low resistance to sunlight; |
impact resistance; |
|
Not subject to chemical attack; |
|
Low cost; |
|
Nylon - polyamide is one of the most durable materials, but also the most expensive.
This material is best suited for machine-building parts such as: gears, joints, bushings, etc.
A feature of nylon is high heat resistance, impact resistance, excellent flexibility, and also partially restores its shape after unloading and deformation.
Nylon also has a number of disadvantages, it actively absorbs liquid and moisture from the air. The material needs to dry before each print, so this material is difficult to work with. There are a number of storage requirements.
PET-G (polyethylene terephthalate with glycol) is one of the newest plastics in the 3D printing industry. It has a smooth glossy surface, unlike PLA and HIPS. Quite dense, durable material, does not absorb moisture, so it is possible to manufacture parts that work in damp places. Has no impact to an ultraviolet, very durable, is not subject to decomposition. Easy to print.
Tab. 1.3 - Advantages and disadvantages of PET-G material
Advantages | Flaws |
Elastic; |
Deformed under load; |
Good resistance to bending and torsion; |
Requires detailed temperature setting when printing; |
High wear resistance; |
Low resistance to sunlight; |
Works well when mating surfaces; |
Difficult removal of supports; |
Not subject to chemical attack; |
Uncut due to toughness; |
Not toxic; |
|
Product durability; |
|
TPU, also referred to as FLEX, is a flexible, stretchable, rubbery, highly elastic material. Distinguished by its enormous strength, high wear resistance, chemical and thermal resistance and lack of toxicity, as well as excellent layer sintering; Used in engineering, mechanical engineering, medicine, etc. TPU has a number of disadvantages, it is almost impossible to paint, varnish, and printing accuracy is not the best.
PEEK is an organic polymer polyether ether ketone. Possesses excellent mechanical properties, has the chemical firmness which is not losing the qualities at high temperatures.
This polymer was supposed to be used mainly as a high temperature resistant and durable insulating material for cables, but over time it has shown its best combination of ease of processing and stability of mechanical properties when reaching high temperature thresholds.
Today, PEEK replaces metals in manufacturing, and it is used to solve various kinds of complex engineering problems. In gear systems, the use of PEEK gears reduces wear on gear parts, allowing you to work with less lubrication.
The disadvantages include high cost compared to other materials proposed by FDM technology, and also has special requirements for the printer, such as high extruder temperatures, printing platform, the need to print in a closed chamber [9].
SLA - stereolithography. Printers of this type by design have a significant difference from layer-by-layer fusing. This technology works with a light-sensitive photopolymer that changes its physical properties when exposed to light. In stereolithography, a laser is used, with the help of which the liquid resin solidifies and sets (Fig. 1.5). This process is called photopolymerization. In the process of printing with this technology, you can see a higher resolution of products. In addition to SLA, there are several other types of photopolymerization technology in the bath - these are DLP and LCD 3D resin printing. The only difference is the use of a different light source [10].
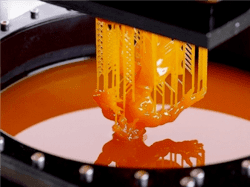
Figure 6 - The process of creating a product in SLA technology
Tab. 1.4 - Advantages and disadvantages of SLA technology
Advantages | Flaws |
High accuracy; |
The fragility of the product; |
Smooth surface of the product; |
Small print area; |
Ease of controls; |
Low resistance to sunlight; |
High print speed; |
Requires post-processing after applying supports; |
Large range of materials for printing; |
Uncut due to toughness; |
Materials used to create products [11]:
1. Standard resin (has a smooth surface, but the part is made quite fragile)
2. Transparent resin (transparent material, but requires post-processing)
3. Casting resin (used to make mold templates)
4. High temperature (heat resistance, used for injection molding, high cost)
The size of the print working area is 145x145x175 mm - for desktop printers and 1500x750x500 mm - for industrial ones, the total layer thickness is 25-100 microns, supports are always required [12].
Areas of use:
• Jewelry,
• healthcare,
• engineering,
• dentistry
• production of models for injection molding
SLS - (selective laser sintering) selective laser sintering. The printer with this technology has a tank (chamber) on which a leveling roller is installed, moving horizontally, levels the powder particles on the surface with a thin layer. The product is created in layers in the process of sintering the lower finished layer of the product with a new one. The platform moves down with each step of building a new layer of the product. Ultimately, the product is removed from the tank (Fig. 1.7) with unused powder and cleaned with a brush from the remaining non-sintered particles, which can be used for further printing after processing [13].
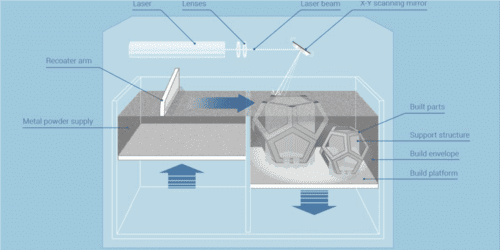
Figure 7 - The process of creating a product on an SLS printer
The advantages include [14]:
• Possibility of manufacturing ready assembly movable elements;
• Creation of products without supporting structures (supports). The powder in which the model is created serves as the very support.
• high accuracy;
• non-waste;
• high strength;
• excellent mechanical properties;
• Easy to operate;
• Perfect detail;
• great quality.
SLS is used only in manufacturing and industrial areas of activity, because. have a significantly high cost, have considerable overall dimensions, and also require a trained specialist to work with an SLS printer.
The main stages of creating products using additive technologies [15]:
• The creation of a digital model takes place in a 3D editor (Fusion 360, Kompas, SolidWorks, etc.);
• Export 3D model to STL format (most photopolymer 3D printers work with STL file format);
• Transfer of the STL file to the printer (correction of the size, position and orientation of the product is performed;
• Preparing the 3D printer for work (the table is calibrated, the layer thickness is selected, the print time is set);
• Printing a 3D object (the process is automatic).
• Finishing of the product (some parts may require additional post-processing);
1.3 Types of designs of devices for the implementation of additive technologies
The design of printers made using FDM technology is divided into [3]:
• Carthusian;
• Delta printers;
• Polar 3D printers;
• Robotic manipulators;
• Five axis printers;
There are such variations in the designs of Cartesian 3D printers [16]:
1. The platform (desktop) moves along one horizontal X or Y axis, the extruder moves along the second horizontal axis, as well as along the vertical Z axis.
2. The platform moves along two axes, horizontal and vertical Z-axis, the extruder along a different horizontal axis.
3. The platform has no movement, and the extruder, in turn, moves along all three axes.
4. The platform moves along the Z axis, up and down, the extruder moves along the X and Y axes, forward-backward, left-right.
5. The platform moves along two horizontal axes X and Y, the extruder moves only along the Z axis.
Delta 3D printer (Fig. 1.8). It has a significant difference from the Cartesian ones made in the Cartesian system, which is familiar to most users, where there are three dimensions and three working axes. In a delta printer, all 3 axes work simultaneously and are responsible for the position of the printing device in space.
The table of this printer is somewhat different from the Cartesian one in that it is absolutely motionless, almost always made in a round shape.
The print head should be as light as possible, have small overall dimensions and weight, because. the speed of model building and accuracy will depend on this.
The speed of the delta exceeds the performance of all currently known FDM printers.
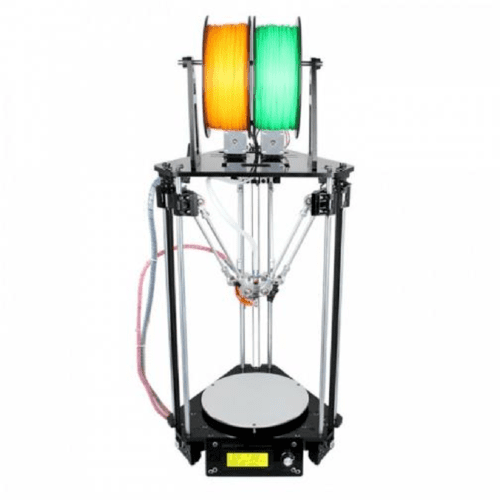
Figure 8 - Delta 3D printer
Advantages [9]:
• The highest speed of the press of models;
• Good quality, depends mainly on the rigidity of the structure itself;
Flaws:
• It is difficult to adjust and adjust the zero position;
• Complex design;
• On budget devices, print quality decreases from the center to the edges
Polar 3D printers (Fig. 1.9). The difference from Cartesian is that the table does not move in different directions, but rotates around its axis. The print quality decreases from the center of the table to the edges of the workpiece.
This printer is intended more for the production of parts such as bodies of revolution, various cylindrical, spherical surfaces;
The second version of the design of the polar printer. The printer is installed in the center of the circle where, in turn, the object is printed by rotating the extruder arm around its axis. This type of 3D printer design is mainly used in the construction industry. [16].
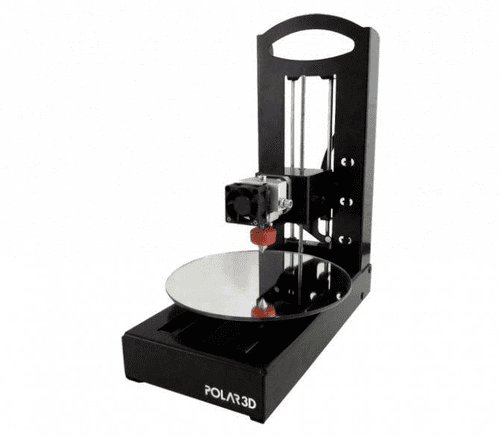
Figure 9 - Appearance of a 3D printer with a polar system
Robotic manipulators are industrial devices whose main task is to replace the actions of human manual work (Fig. 1.10). In the industry, these point-and-click printers are quite multifunctional, have a wide range of work, and achieve excellent printing accuracy.
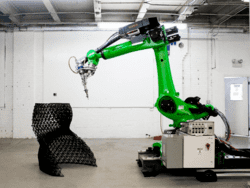
Figure 10 - Appearance of the robotic arm
These controls are divided into [17]:
1) Mobile (have the ability to move around the production shop and perform work at any point).
2) Stationary (used mainly for lifting work, have a fairly wide radius of action).
3) Horizontal (used to serve several sections at a time).
Five-axis printers (Fig. 1.11). Thanks to the new additional axes, it became possible to move the designed model during the printing process, which is a great advantage in the engineering industry.
This printer has the ability to print elements on the side of the part, by turning and tilting, which eliminates a huge number of supporting structures.[18].
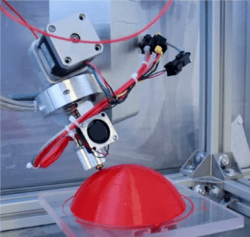
Figure 11 - Appearance of a five-axis printer
Unlike FDM technology, photopolymer SLA printers use UV radiation in their work. They always work in a closed environment, with a protective cover made of tinted glass that does not allow UV radiation to pass through.
SLA printing process [12]:
1) A platform is placed in a container with a liquid photopolymer, at a height level from the surface of the material.
2) The UV laser, according to the established program, cures the necessary sections of the photopolymer. The formation of the product occurs with the help of a laser beam, which is carried out with the help of a set of mirrors.
3) After the layer is completed, the platform moves to a safe distance where the resin inside the bath is mixed with the stirrer foot. This process continues until the finished product is obtained.
4) Then, at the end of the product creation process, additional post-processing with a UV lamp is necessary, because the part has not reached the desired curing. In this process, the part eventually acquires high mechanical and thermal properties.
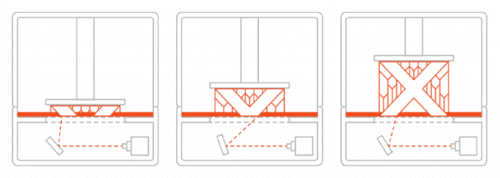
Figure 12 - SLA printing process
Printer design elements are shown in Fig. 1.13
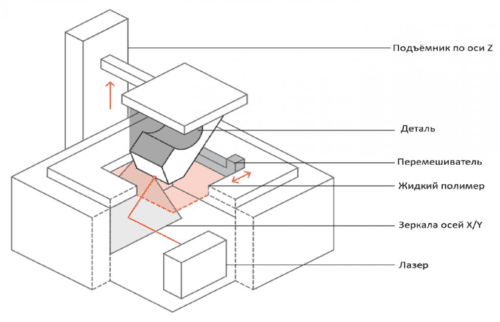
Figure 13 - Printer design elements
The height of the SLA print layer has a range of 25 to 100 microns.
For most products, a layer height of 100 µm is acceptable.
An important parameter is also the size of the platform. Mainly depends on the type of printer [12].
By design, SLA printers are divided into two types:
• top to bottom orientation;
• bottom-up orientation;
The top-down orientation is that the resin tank is below the platform and the work platform is above it (Figure 1.14)
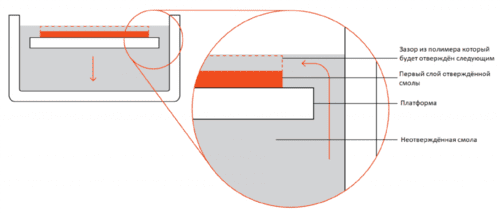
Figure 14 - Printer SLA diagram from top to bottom
Advantages:
• lower cost
• Wide market availability
Flaws:
• Small platform size
• Smaller range of materials
• Requires additional post-processing due to extensive use of supports
The bottom-up diagram looks like when the resin tank is placed above the light source, the part is built upside down (Fig. 1.15) [12].
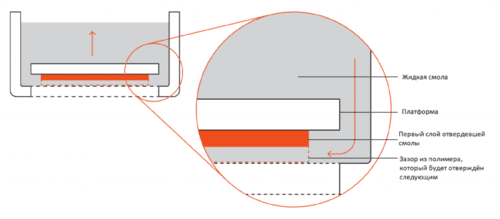
Figure 15 - Printer SLA diagram from bottom to top
Advantages:
1) Faster print time
2) Very large platform size
Flaws:
1) Changing the material involves emptying the entire tank
2) Qualified operator required
3) High cost
The manufacture of products by the SLS method is a process that looks like this (Fig. 1.16):
1) The chamber in which the powder is located is heated together with the entire print area and reaches temperature standards below the melting of the polymer. Then the blade or roller distributes the powder in a thin layer over the entire working area of the platform.
2) The laser performs the function of scanning the contour of the next layer, after which it selectively sinters the powder particles.
3) Upon completion of the sintering of the layers, the working platform moves down, and the blade, in turn, repeats the process of coating the surface with powder. This whole process occurs again, until the product is completed.
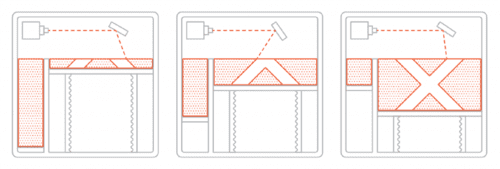
Figure 16 - The process of manufacturing products using the SLS method
At the end of printing, the product is located in an unaffected (not sintered) powder, so you need to let it cool before removing it from the camera [19].
The structural elements of the printer are shown in (Fig. 1.17)
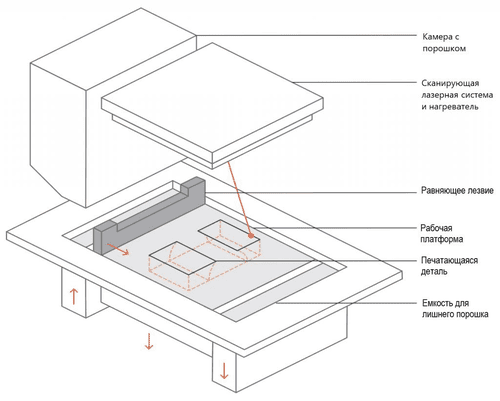
Figure 17 - Structural elements of the SLS printer
The layer height reaches 100-120 microns. There are also options for printers that allow you to produce products with a layer thickness ranging from 50 to 150 microns.
The most important and perhaps the most important advantage of this technology is that no support is required for the manufacture of the part; it is located in a tank filled with powder, which in turn serves as the very support. This allows you to print parts of any geometric shape.
With the use of SLS technology, the strength characteristics of the sintering of the layers reach excellent values [20].
Tab. 1.5 - Final Comparison of 3D Printing Technologies
Layered deposition (FDM) | Stereolithography (SLA) | Selective laser sintering (SLS) | |
Advantages |
High speed, cheap products and materials |
Excellent price, High precision, Smooth product surface |
Robust functional parts, Free design, No support structures required |
Flaws |
Poor accuracy, Low detail, Design limitations |
Limited modeling space, Sensitivity to long-term UV exposure |
Expensive equipment, Rough surface, Limited by material choice |
Usage |
Inexpensive, rapid prototyping |
Functional prototyping, Dental applications, Prototyping and jewelry molding Modeling |
Functional prototyping Short-term, intermediate, custom production |
Price |
Mid-range desktop printers - from $2,000, industrial systems - from $20,000 |
Professional desktop printers from $2000, large scale industrial systems from $80,000 |
Industrial printers - from $100,000 |
1.4 Goals and objectives of the study
The purpose of the master's thesis is to improve the accuracy of 3D printing of the Delta FDM printer by studying the parameters and synthesizing the design. To achieve this goal, the following tasks are supposed to be solved:
• Kinematic structure of the 3D printer design
• Types and features of kinematic structures of a 3D printer
• Classification of parallel structures of 3D printer design
• Selection and description of the block diagram of the 3-PUU parallel mechanism
• Solution of the direct kinematics problem for the 3-PUU structure
• Choosing a working body of a 3D printer
• Study of types and classification of working bodies of 3D printers
• Development of the design scheme of the working body
• Printer platform design
• Calculation for the accuracy and strength of the nodes of the working body
• Technological preparation for the production of a 3D printer
• Initial data for the development of manufacturing technology for the production object
• Selecting a Generic Part
• Development of a part manufacturing route
• Design of an operational technological process for manufacturing a part in CAD TP
findings
Studying the issue of additive technologies, we can conclude that 3D printing is rapidly gaining growth and these technologies, although having a huge number of advantages, also have a number of disadvantages that require detailed study and analysis to solve them. As for FDM, in this technology, for the most part, it is necessary to improve the print quality and achieve indicators that allow using this technology in engineering production.
List of sources
- Market of 3D printing technologies in Russia and in the world: prospects for introducing additive technologies into production [Ýëåêòðîííûé ðåñóðñ]. – Access mode: https://additiv-tech.ru/publications/rynok-tehnologiy-3d-pechati-v-rossii-i-mire-perspektivy-vnedreniya-additivnyh
- FDM printing (layer-by-layer deposition method) | FDM printer: 3d printing technology [Ýëåêòðîííûé ðåñóðñ]. - Access mode: https://vektorus.ru/blog/obzory/tehnologii-3d-pechati-fdm.html
- FDM Printer Design [Ýëåêòðîííûé ðåñóðñ]. - Access Mode: https://www.ixbt.com/printer/3d/3d_fdm.shtml
- Creality Ender 3 Dual Extruder - All Your Best Options (& Pro/V2) - 3D Industry [Ýëåêòðîííûé ðåñóðñ]. - Access Mode: https://3dindustry.ru/3d-printery/dvojnoj-ekstruder-creality-ender-3-vse-vashi-luchshie-varianty-pro-v2.html
- Plastic extruder for a 3D printer, principle of operation, device, varieties - 3Dradar [Ýëåêòðîííûé ðåñóðñ]. - Access mode: https://3dradar.ru/post/48016/
- The device of 3D printers, types of kinematics. The difference between a delta 3D printer and a Cartesian one - 3Dradar [Ýëåêòðîííûé ðåñóðñ]. - Access mode: https://3dradar.ru/post/47812/
- Optimal print area size [Ýëåêòðîííûé ðåñóðñ]. - Access mode: https://3dtoday.ru/questions/optimalnyy-razmer-oblasti-pechati
- FDM technology. How it works [Ýëåêòðîííûé ðåñóðñ]. - Access mode: https://3dtool.ru/stati/fdm-tekhnologiya-kak-eto-rabotaet/
- Overview Guide to FDM 3D Printing Materials [Ýëåêòðîííûé ðåñóðñ]. - Access Mode: https://cvetmir3d.ru/blog/3d-obzory/3d-svyazuyushchaya-nit-obzornyy-putevoditel-po-materialam-dlya-fdm-3d-pechati/
- 3D Printing DLP LCD SLA Resin - Stereolithography Guide [Ýëåêòðîííûé ðåñóðñ]. - Access Mode: https://3dpt.ru/blogs/support/sla
- Types of resins for photopolymer 3D printer, characteristics, application [Ýëåêòðîííûé ðåñóðñ]. - Access mode: https://cvetmir3d.ru/blog/3d-obzory/obzor-fotopolimernykh-smol-2021/
- SLA Technology. How SLA 3D Printing Works [Ýëåêòðîííûé ðåñóðñ]. - Access Mode: https://3dtool.ru/stati/sla-tekhnologiya-kak-rabotaet-3d-pechat-sla/
- SLS printing with polyamide | Selective Laser Sintering - SLS Printer Technology [Ýëåêòðîííûé ðåñóðñ]. - Access Mode: https://vektorus.ru/blog/tehnologija-sls.html
- Features and Benefits of SLS Technology [Ýëåêòðîííûé ðåñóðñ]. - Access Mode: https://blog.iqb.ru/sls-technology/
- Additive technology: what is it and where is it applied | RBC Trends [Ýëåêòðîííûé ðåñóðñ]. - Access mode: https://trends.rbc.ru/trends/futurology/6284222d9a79472c8b9a67bc
- 3d printer kinematics: best views, types of corexy mechanics [Ýëåêòðîííûé ðåñóðñ]. - Access mode: https://top3dshop.ru/blog/types-of-fdm-3d-printer.html
- Delta 3D Printers: Pros and Cons of Delta Bots in 3D Printing [Ýëåêòðîííûé ðåñóðñ]. - Access Mode: https://top3dshop.ru/blog/delta-3d-printery-plusy-i-minusy.html
- 5D Printing Technology [Ýëåêòðîííûé ðåñóðñ]. - Access Mode: https://rec3d.ru/rec-wiki/5d-printery-opisanie-vozmozhnosti-vidy/
- SLS 3d printing technology: selective laser sintering [Ýëåêòðîííûé ðåñóðñ]. - Access mode: https://top3dshop.ru/blog/sls-3d-printing.html
- 3D printing technologies: FDM, SLA, DLP(LCD), SLS, DMLS, SLM how 3D printers work - 3DRadar [Ýëåêòðîííûé ðåñóðñ]. - Access mode: https://3dradar.ru/post/45940/