Abstract on the topic of graduation work
Content
- Introduction
- 1. Purpose of work
- 2. Main Research Objectives
- 3. Requirements for gears
- 4. Signs of reduced gear performance
- 5. The main provisions of the master's work
- 6. Scientific novelty of the obtained results
- 7. Practical implications
- List of sources
Introduction
Increasing the productivity and accuracy of manufacturing both individual parts and machines as a whole, while ensuring their minimum cost under given production conditions, are the main tasks of mechanical engineering technology. Product designs become more complex, operational requirements for them increase, which entails the need to improve the processes of shaping individual surfaces of parts, expand the technological capabilities of the technological equipment used and improve the designs of cutting tools [8]. The processes of designing and manufacturing gear elements of various types, including cylindrical gears, are no exception.
The development of engineering and technology leads to the need to increase the reliability, durability, load capacity of cylindrical gears, while maintaining or reducing their overall dimensions [3]. The performance characteristics of gears are increased by increasing the accuracy of manufacturing their individual elements [2], including gear rims, which is not always economically feasible, or by changing their design, modifying the side surface of the teeth.
The performance of products with gear rims depends on the type and magnitude of errors in the manufacture and installation of gear rims [2], as well as deformations of gear elements and parts with gear rims. The presence of errors and deformations leads to a change in the nature of the contact of the teeth in the mesh and, as a consequence, to an increase in contact and bending stresses on the teeth.
The spatial nature of the contact of the teeth in engagement implies the introduction of a spatial modification of the lateral surface of the teeth [4] of at least one of the links of the gear pair. Accounting for errors and deformations of gear elements in the synthesis of new tooth geometries leads to the creation of a new element base and, as a result, to the need to improve the technology for manufacturing gear rims, which determines the relevance of the presented work.
1. The purpose of the work
Improving the accuracy of the process of shaping the spatially modified teeth of cylindrical wheels by copying with a finger modular cutter due to the analytical determination of the parameters of the linear spatial trajectory of the cutting tool during the shaping process.

Figure 1 - The process of creating a gear wheel with a finger cutter
2. Main research objectives:
1. Perform an analysis of operational factors affecting the bending endurance of spur gear teeth, consider known design methods for increasing the bending endurance of spur gears and justify the need to improve the design of spur gears with spatially modified teeth and technological methods for their manufacture.
2. To develop design support for the shaping of spatially modified teeth of cylindrical wheels by copying with a finger modular cutter.
3. To develop a method for determining the parameters of the trajectory of movement of a finger modular cutter in the process of shaping a spatially modified gear rim and to study the accuracy of shaping of spatially modified gear rims by copying with a finger modular cutter [1].
4. To develop technological support for the formation of spatially modified teeth of cylindrical wheels with a finger modular cutter when it moves along a linear spatial trajectory.
5. To develop measures for labor protection in the manufacture of gear elements.
6. Perform an assessment of the economic efficiency of the proposed technological solutions.
The object of study - the elements of the process of shaping spatially modified gear rims of cylindrical wheels by copying [10] with a finger modular cutter. The subject of research - the parameters of the process of shaping spatially modified teeth with a finger modular cutter.
3. Requirements for gears
In modern machines, gears with involute gearing are predominantly used.
Depending on the conditions of the work performed and the purpose of the gears, the following requirements are imposed [5,11]:
1) high wear resistance of the working surfaces of the teeth, achieved through the use of high-quality alloy steels, thermal and chemical-thermal treatment, mechanical hardening of the PPD, surface finishing;
2) quietness and smoothness of work, accuracy of transmission of movements, achieved by the accuracy of manufacturing the profile of the teeth, their finishing and the elimination of the eccentricity of the gear rims;
3) sufficient efficiency;
4) high fatigue strength of the teeth, achieved by their careful processing, thermal, mechanical, thermomechanical hardening, finishing.
The listed requirements are explained by high circumferential speeds, contact pressures, bending cyclic loads.
During operation, the teeth are subjected to bending loads that cause the tooth root to break; The surface of the teeth is subjected to relatively high contact pressures and abrasion, leading to chipping (pitting) and wear.
To improve the performance properties, the working surfaces of the teeth in most cases should have high surface hardness (HRC 58-62) and surface roughness (Ra = 2.5-1.25 microns) with a relatively viscous and plastic core, which provides increased strength at cyclic and shock loads.
In some cases, gears operate in less severe and difficult conditions, as a result of which the requirements for their manufacture are also lower.
The accuracy of gears is characterized by the following indicators [5]:
1. The kinematic accuracy of the transmission of rotation from a given wheel to a conjugate one. Violation of kinematic accuracy is manifested in the inconsistency of the turns of the transmission wheels for each revolution.
2. The smoothness of the transmission. Violation of it causes repeatedly repeated fluctuations in the speed of rotation, accompanied by vibration and noise.
3. The contact patch of the side surfaces of the teeth. Its decrease leads to an increase in the load concentration on small areas of the tooth surface.
4. Lateral clearance between non-working tooth profiles.
5. The roughness of the working (side) surfaces of the teeth.
According to GOST 1643-81, machined wheels and gears are divided into 12 degrees of accuracy according to manufacturing accuracy: 1st, 2nd, 3rd, 12th (in descending order of accuracy). Each degree combines wheels and gears that have similar methods for forming gear elements, that is, the same degree of perfection in manufacturing technology. The most widely used are the 6th, 7th, 8th, 9th degrees of accuracy.
The roughness of working surfaces, depending on the requirements, can be from Ra \u003d 2.5-1.25 microns.
Various working conditions of gears explain the difference in technological requirements and, accordingly, the difference in methods of processing teeth.
4. Signs of reduced gear performance
Passing through the engagement zone, during the operation of the transmission, the teeth are subjected to cyclic loading. In this case, the force Fn normal to them and the friction force act on the contact surfaces of the teeth [6]. For each tooth, the stresses change with time in a discontinuous zero cycle.
Repetitively variable loads cause fatigue failure of teeth - their breakage or chipping of working surfaces. Slip and frictional forces in engagement cause wear and seizing of the teeth.
1. Gear tooth failure
This is the most dangerous type of destruction, as it results in a sudden and complete failure of the transmission. Breakage is a consequence of fatigue of the material of the teeth from acting repetitively variable bending stresses or from shock overload [7].
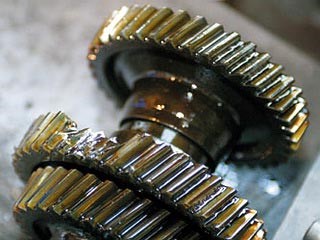
Figure 2 - Broken teeth
This happens, for example, when a foreign object gets between the teeth or a sharp gearshift of the gearbox.
Fatigue cracks form at the base of the tooth on the side where the greatest tensile stresses arise from bending. Straight short teeth break out completely along the section at the base of the tooth. In case of fatigue failure, a concave surface remains on the wheel body after a fracture, and in case of breakage due to overload, a convex surface remains.
The teeth of herringbone and wide helical gears break out along an inclined section.
To increase the strength of the tooth is facilitated by: an increase in the engagement modulus, a decrease in the stress concentration at the base of the teeth, the use of modifications, an increase in the strength of the material of the wheels, an increase in the accuracy of manufacturing and mounting of the transmission.
To prevent fatigue breakage of the teeth, a strength calculation is carried out using bending stresses.
2. Fatigue chipping of the working surfaces of the teeth
This is the main type of tooth decay for most enclosed, well-lubricated gears. It is a consequence of the action of repetitively alternating contact stresses. The destruction begins at the root of the tooth near the pole line, where the greatest load (single-pair engagement zone) and the highest friction force (near the pole, the minimum sliding speeds) act, which contributes to the formation of microcracks on the surface of the teeth.
The development of cracks is facilitated by the wedging effect of the lubricant that has fallen into the cracks of the teeth.
The development of cracks leads to chipping of material particles from the surface, the formation of small pits, which then turn into larger shells on the entire surface of the teeth.
When chipping, the conditions for the formation of a continuous oil film are violated (the oil is squeezed into the pits), which leads to rapid wear and scuffing of the teeth. Dynamic loads, noise, vibration increase, temperature rises.
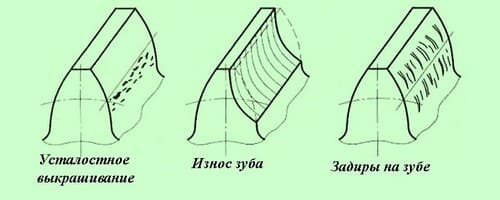
Figure 3 - Types of Wear
Chipping may be limited or progressive. Limited chipping is observed in areas with stress concentration. In wheels made of well-running-in materials, such chipping stops after running-in, without affecting the operation of the transmission. Dangerously progressive chipping, gradually affecting the entire working surface of the tooth roots.
The prevention of chipping is facilitated by increasing the hardness of the tooth surface, reducing the roughness of working surfaces, modifying the profile, and choosing the right type of oil.
To prevent fatigue chipping of the teeth, a strength calculation is carried out using contact stresses.
3. Tooth wear
Wear is the main type of destruction of the teeth of open gears. As the tooth wears out, it becomes thinner, its root weakens, and gaps in engagement increase, which leads to a loss of kinematic accuracy and, ultimately, to tooth breakage [5].
The destruction of the teeth is preceded by the occurrence of increased noise during the operation of the transmission. Wear can be reduced by protecting against abrasive particles, increasing the hardness and reducing the roughness of the working surfaces of the teeth, and reducing tooth slip by modification.
4. Jamming of teeth
Tooth seizing consists in welding particles of the material of one tooth to another (microwelding) as a result of the destruction of the lubricating film and local heating, due to high pressures and sliding speeds in the contact zone. The detached outgrowths on the teeth lift up the working surfaces of the mating teeth, furrowing them in the direction of sliding.
Tooth seizing is prevented by increasing hardness, reducing the roughness of the working surfaces of the teeth, using modifications, selecting extreme pressure oils, and artificially cooling the gear.
Seizure is the most dangerous type of failure in heavily loaded gears.
5. The main provisions of the master's work:
• synthesis of gear teeth, taking into account errors and deformations of gear elements, allows creating a spatial engagement of spur gears, which provides high performance properties due to two-pair contact in all phases of engagement and has increased bending endurance;
• moving the cutting tool along a linear spatial trajectory, allows you to cut a gear rim with a geometry close to the specified spatial one on existing serial equipment by copying with a finger modular cutter;
analytical determination of the relationship between the geometry of the lateral surface of spatially modified teeth, the geometry of the cutting edge of the finger modular cutter with the parameters of the linear spatial trajectory of its movement allows to increase the accuracy of the process of shaping the gear rim.
6. The scientific novelty of the results obtained is:
• the technique for synthesizing spatially modified teeth of spur gears of the middle module with external gearing of the teeth has been further developed, and the gears created on its basis are able to compensate for errors and deformations of gear elements;
• for the first time, a method has been proposed for gear milling of spatially modified teeth of cylindrical wheels by copying with a finger modular cutter, characterized by moving the cutting tool along a linear spatial trajectory;
• received further development of the method of analytical determination of the coordinates of the points of the linear spatial trajectory of the cutting tool working according to the copying method, depending on the geometry of the side surface of the teeth and the geometry of the cutting edge of the tool
7. The practical significance of the results obtained is:
• recommendations have been developed on the synthesis of spatially modified gear teeth, gearing, on the basis of which they are able to compensate for manufacturing errors and deformation of gear elements under the action of work loads;
• design and technological support for cutting gear rims with spatially modified teeth has been developed;
• approximation of the coordinates of the contact points of the lateral surface of the teeth by Bezier [12] splines allows to reduce the time required for the stages of design and technological preparation for the production of gear rims;
• recommendations for the development of technological support presented in the work allow designing technological processes for manufacturing products with spatially modified gear rims of middle modules using existing serial equipment.
List of sources
- Tsukanov, O.N. On the development of the theory of synthesis of non-involute gears on the basis of a cylindrical initial link in generalizing coordinates / O.N. Tsukanov // Bulletin of SUSU. Series "Engineering". - 2013. - Volume 13, No. 1. - P. 119 - 122.
- Ayrapetov, E.L. Gear couplings [Text] / E.L. Airapetov, O.I. Kosarev. — M.: Nauka, 1982. — 128 p.
- Genkin, M.D. Improving the reliability of heavily loaded gears [Text] / M. D. Genkin, M. A. Ryzhov, N. M. Ryzhov. - M.: Mashinostroenie, 1981. - 232c.
- Grubka, R.M. Constructive ways to improve the performance of cylindrical gears [Text] / R.M. Grubka// Progressive technologies and engineering systems: International coll. scientific works. - Donetsk: Donets. nat. tech. un-t, 2019. - Issue. 1(64). - S. 17 - 22.
- About metalworking - [Электронный ресурс]. — Режим доступа: Gears and their assembly
- EAM Association - [Электронный ресурс]. — Режим доступа: Basic requirements, materials and design of gears
- Metal forum - [Электронный ресурс]. — Режим доступа: Classification of gear damage
- Loskutov, V.V. Gear cutting machines [Text] / V.V. Loskutov - M: Mashinostroenie, 1972.-125 p.
- Finger, M. L. Cylindrical gears: Theory and practice of manufacturing [Text] / M. L. Finger. - M: Scientific book, 2005. - 368 p.
- Grubka, R. M. Classification of movements in multi-coordinate gear milling of spatially modified teeth of cylindrical gears by copying [Text] / R. M. Grubka, A. N. Mikhailov, I. A. Petryaeva// Progressive technologies and systems Engineering: International Sat. scientific works. - Donetsk: Donets. nat. tech. un-t, 2019. - Issue 3 (66). - S. 16 - 21.
- Production technology and quality assurance methods for gears and gears [Text]: textbook. allowance / V. E. Antonyuk [and others]; ed. V. E. Starzhinsky and M. M. Kanne. - Minsk: Technoprint, 2003. - 766 p.
- Grubka, R. M. Trajectory of movement of a standard tool during multi-coordinate machining of spatially modified teeth of cylindrical wheels by copying [Text] / R. M. Grubka, M. V. Dolmatova, Yu. V. Sazonenko // Progressive technologies and engineering systems: International coll. scientific works. - Donetsk: Donets. nat. tech. un-t, 2022. - Issue 3(77). - S. 10 - 17.